Diesel engines have earned their reputation as the workhorses of the industrial and transportation worlds through unmatched durability and reliability.
These powerplants are engineered to withstand punishing conditions, from the frigid Arctic to scorching deserts, while delivering consistent performance over hundreds of thousands sometimes millions of miles.
The best diesel engines combine robust construction with simple, effective designs that minimize failure points.
Heavy-duty components, efficient cooling systems, and meticulous engineering create machines that can operate continuously under extreme loads for decades.
What sets legendary diesel engines apart is their ability to maintain performance through harsh environments, constant use, and minimal maintenance.
These engines often outlast the vehicles or machinery they power, sometimes being rebuilt multiple times while maintaining their core structure.
From commercial trucking to agriculture, maritime applications to military vehicles, these ten diesel engines represent the pinnacle of longevity and toughness, setting the standard for what’s possible when reliability is the primary design goal.
1. Cummins 5.9L 6BT (12-Valve)
The Cummins 5.9L 6BT, commonly known as the “12-valve Cummins,” has achieved legendary status among diesel enthusiasts for its nearly indestructible construction and mechanical simplicity.
Produced from 1989 to 1998, this inline-six engine revolutionized the pickup truck market when it appeared in Dodge Ram trucks, offering farm equipment reliability in a consumer vehicle.
What makes the 12-valve Cummins exceptional is its straightforward mechanical design. With a cast-iron block and head, forged-steel connecting rods, and a gear-driven camshaft, the 6BT minimizes potential failure points.
Its direct mechanical fuel injection system operates without complex electronics, allowing it to function reliably even in environments where electrical systems might fail.
The robust Bosch P7100 injection pump is particularly renowned for its durability and tuning potential.
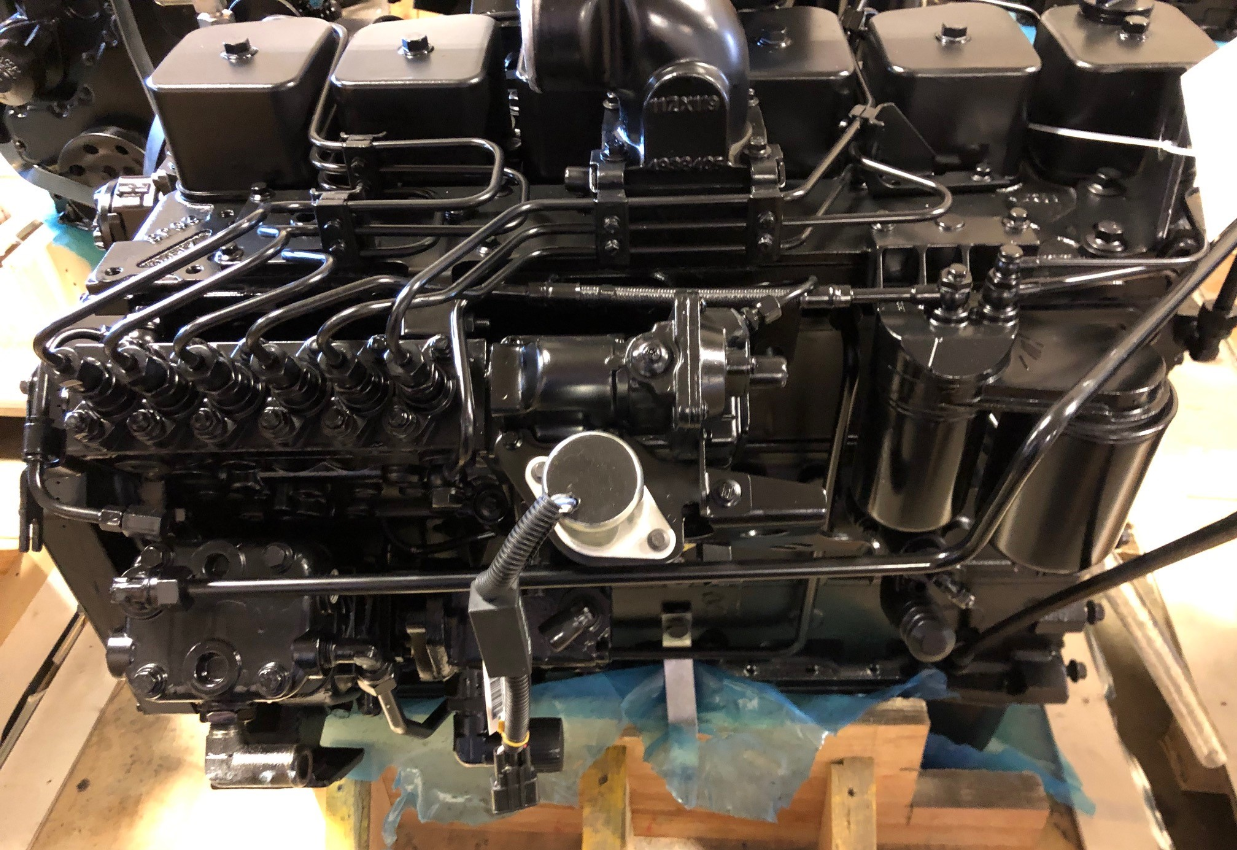
The overbuilt nature of this engine becomes apparent in its performance characteristics. While factory rated at a modest 160-215 horsepower (depending on the year), many 12-valve Cummins engines have been pushed to double or triple those numbers with basic modifications, highlighting the significant engineering margins built into the design.
The massive torque output—peaking at 440 lb-ft in later models enables these engines to pull tremendous loads without strain.
Perhaps most impressive is the 12-valve’s longevity. Many examples have surpassed 500,000 miles without internal repairs, and million-mile examples exist with basic maintenance.
The engine’s tolerance for less-than-ideal maintenance practices, low-quality fuel, and extreme temperature ranges makes it particularly suited for remote operations where service facilities might be limited.
These characteristics have made the 12-valve Cummins a preferred power source not just for trucks but for agricultural equipment, generators, and marine applications worldwide, cementing its status as one of the most durable diesel engines ever produced.
2. Detroit Diesel Series 71
The Detroit Diesel Series 71 represents a watershed moment in diesel engine design, setting new standards for reliability in the most demanding applications since its introduction in 1938.
Developed by GM’s Detroit Diesel division under the direction of Charles F. Kettering, this two-stroke diesel engine family has powered everything from military vehicles and locomotives to marine vessels and stationary generators.
What distinguishes the Series 71 is its unique two-stroke design with unit injectors and a roots-type blower, giving it exceptional power density for its era.
Available in configurations from single-cylinder to 24-cylinder arrangements (V24), the versatility of this engine platform is unmatched.
The inline variants (particularly the 6-71) became workhorses in buses, trucks, and construction equipment, while the larger V configurations found homes in marine, railroad, and power generation applications.
These engines exhibit remarkable durability through several key design elements. The block and heads are constructed from high-grade cast iron, providing excellent thermal stability and wear resistance.
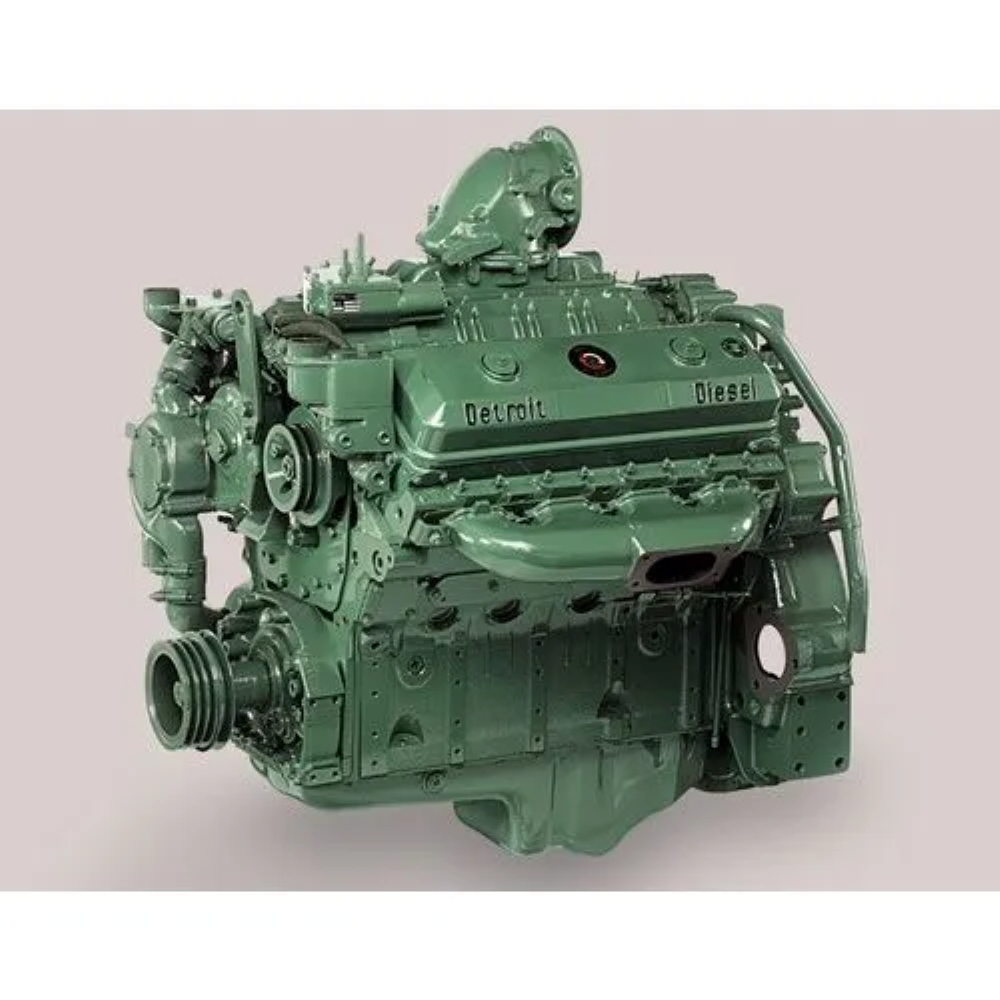
The unit injector system combining the injection pump and injector in one component eliminates high-pressure external fuel lines, a common failure point in other diesel designs.
The engine’s simplicity also contributes to its longevity maintenance can be performed with basic tools, even in field conditions.
The Series 71’s reputation was cemented during World War II when it powered landing craft, tanks, and generators in every theater of the war.
Under the harshest battlefield conditions from Arctic cold to desert heat and tropical humidity these engines kept running when failure meant disaster.
This military heritage translated to commercial success in the post-war period, where operators discovered that these engines could run continuously for tens of thousands of hours before requiring major service.
Even today, decades after production ended for many variants, Series 71 engines continue to operate around the world, with some examples logging over 100,000 hours of operation equivalent to running continuously for more than 11 years.
This extraordinary longevity explains why these engines, though no longer in production, remain highly sought-after and actively rebuilt.
3. Caterpillar 3406E
The Caterpillar 3406E stands as a testament to heavy-duty diesel engineering excellence, having established itself as one of the most reliable power plants in commercial transportation and industrial applications since its introduction in 1993.
This 14.6-liter inline-six diesel represents the culmination of Caterpillar’s mechanical engine development before the transition to fully electronic designs.
What makes the 3406E exceptional is its ideal balance between robust mechanical components and useful electronic controls.
The massive iron block features wet cylinder liners for superior cooling, while the engine’s internal components from the forged steel crankshaft to the heavy-duty connecting rods are dimensioned far beyond minimum requirements.
This overbuilt approach gives the 3406E significant tolerance for stress and operating conditions that would destroy lesser engines.
The 3406E’s cooling system deserves special mention for its contribution to the engine’s longevity.
Designed to maintain optimal operating temperatures even under extreme loads, the system effectively manages heat rejection through intelligent water flow paths and an oil cooler that prevents oil degradation during sustained high-output operation.
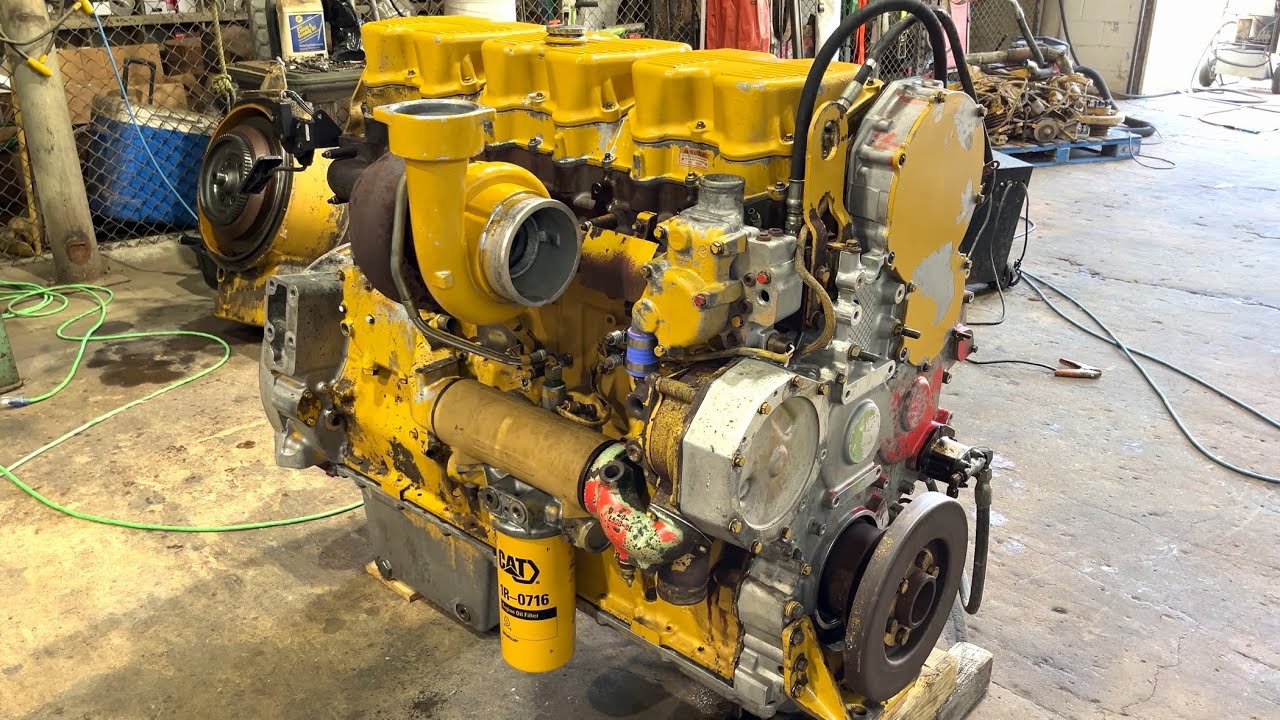
This thermal management capability allows the engine to perform reliably in environments ranging from sub-zero temperatures to desert heat.
In long-haul trucking applications, the 3406E repeatedly demonstrates its exceptional durability, with many engines exceeding one million miles before requiring rebuilding.
Even more impressive, the engine’s block and major components typically remain serviceable through multiple rebuilds, with some engines effectively serving for several million miles through proper maintenance and periodic refreshing of worn components.
Beyond its physical durability, the 3406E earned its legendary status through consistent, predictable performance.
Rated between 350 and 550 horsepower depending on specific configuration, these engines deliver tremendous torque across a wide RPM band, making them ideal for hauling heavy loads across varying terrain.
The mechanical simplicity of critical systems means that even when minor issues arise, they can typically be addressed without specialized electronic diagnostic equipment a significant advantage for operators working in remote areas.
The Caterpillar 3406E’s combination of brute strength, serviceability, and consistent performance explains why these engines remain highly valued in the secondary market, often commanding premium prices even decades after manufacture.
4. Mercedes-Benz OM617
The Mercedes-Benz OM617 five-cylinder diesel engine stands as one of the most celebrated mechanical achievements in automotive history, earning its reputation for extraordinary longevity and resilience in the harshest operating conditions.
Produced from 1974 to 1991, this inline-five turbodiesel powered numerous Mercedes models including the legendary W123 series, which established new benchmarks for vehicle longevity.
What sets the OM617 apart begins with its fundamental architecture. The engine block is cast from a high-silicon aluminum alloy with cast-iron cylinder liners, providing exceptional rigidity while managing thermal expansion.
The five-cylinder design offers natural balance while delivering smooth power delivery and minimal vibration.
The forged steel crankshaft rotates in seven main bearings an overspecified design that ensures durability even under sustained high loads.
The OM617’s pre-chamber indirect injection system, while not as efficient as modern direct injection, contributes significantly to the engine’s reliability by reducing combustion shock loads on internal components.
The precisely engineered Bosch injection pump delivers consistent fuel metering decade after decade, with many units requiring minimal service even after hundreds of thousands of miles.
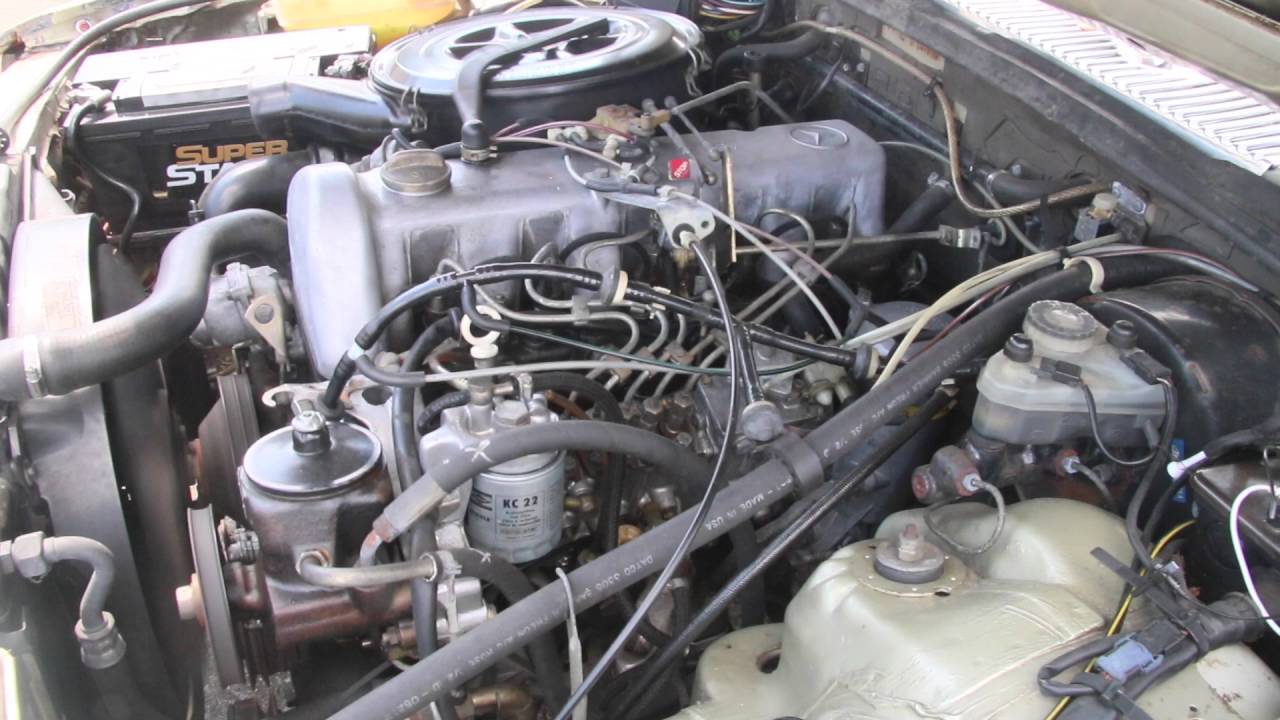
Temperature management critical to diesel longevity is handled through an exceptionally efficient cooling system that prevents hot spots and maintains consistent operating temperatures.
The oil system features generous oil capacity and excellent filtration, protecting bearing surfaces even when oil change intervals are extended beyond recommendations.
The OM617’s reputation was cemented when Mercedes-Benz used it to set multiple endurance records, including a 100,000-kilometer test at the Nardò Ring in Italy, where W123 sedans averaged speeds over 150 km/h for weeks without stopping except for fuel, oil, and driver changes.
In real-world applications, these engines routinely surpass 500,000 miles without internal repairs, with many documented cases exceeding one million miles on original components.
Perhaps most impressively, the OM617 achieves this longevity while maintaining exceptional tolerance for fuel quality variations a crucial factor in developing regions where diesel fuel standards vary widely.
From the Arctic Circle to the Sahara Desert, from European highways to unpaved tracks in Africa and South America, the OM617 has demonstrated its ability to operate reliably where other engines fail, making it one of the most trusted power plants for remote and challenging environments.
Also Read: 10 Forgotten Automakers That Deserve a Comeback
5. Isuzu 4BD1T/4BD2T
The Isuzu 4BD1T and its evolution, the 4BD2T, represent Japanese engineering excellence in the medium-duty diesel engine sector, having earned worldwide respect for exceptional reliability in commercial applications since their introduction in the 1980s.
These 3.9-liter four-cylinder turbodiesel engines have powered everything from delivery trucks and light buses to generators and construction equipment across the globe.
The foundation of these engines’ durability begins with their structural design. The block is constructed from dense, high-grade cast iron with thick walls that resist warping even after decades of thermal cycling.
The crankshaft a massive, forged-steel component supported by five main bearings provides exceptional resistance to torsional stress.
Unlike many competitors who reduced material to save costs, Isuzu dimensioned these engines conservatively, providing significant safety margins in critical components.
Cooling system efficiency plays a crucial role in the 4BD series’ longevity. The engines feature a high-capacity water pump, strategically positioned coolant passages, and an oil cooler that effectively manages operating temperatures even under sustained high loads in hot environments.
This thermal stability prevents the accelerated wear that plagues less sophisticated designs when operating near their thermal limits.
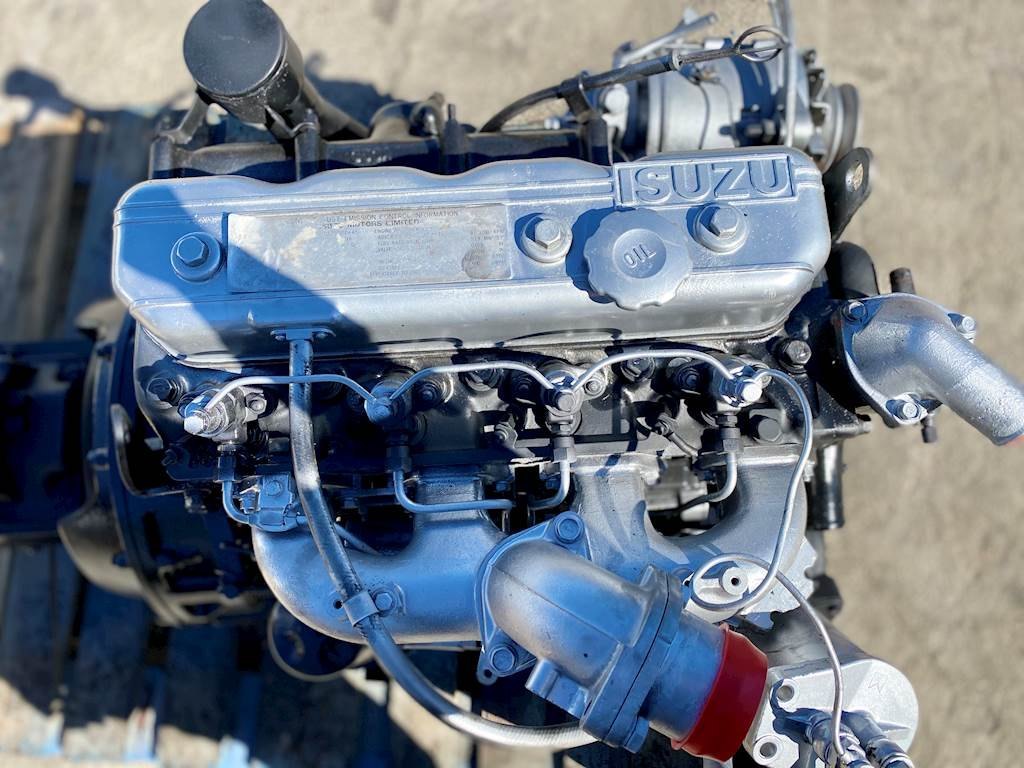
The fuel injection system demonstrates equal attention to durability concerns. The mechanical inline injection pump is renowned for its simplicity and reliability, continuing to provide precise fueling even after hundreds of thousands of miles.
The injectors themselves are designed to withstand the contamination often found in regions with variable fuel quality, making these engines particularly well-suited for developing markets.
What truly distinguishes the 4BD series is their tolerance for less-than-ideal operating conditions and maintenance.
While designed for regular service intervals, these engines frequently demonstrate remarkable forgiveness when maintenance is delayed or performed with limited resources.
This characteristic has made them particularly popular in regions where specialized service facilities may be limited or inaccessible.
The practical result of this engineering approach is evident in the field performance: 4BD-powered vehicles routinely accumulate 500,000+ miles in commercial service before requiring significant attention to the engine internals.
Even after rebuilding, the core components often remain serviceable for another complete service cycle, effectively providing decades of reliable operation.
This exceptional lifespan, combined with straightforward serviceability and widely available parts, explains why these engines continue to be sought after for applications where failure is not an option, from emergency service vehicles to remote mining operations.
6. International Harvester DT466
The International Harvester/Navistar DT466 has earned its place in diesel engine history as one of the most dependable medium-duty power plants ever developed, serving as the backbone of countless commercial and municipal fleets since its introduction in 1971.
This 7.6-liter inline-six engine represents a perfect balance of robust construction, straightforward engineering, and practical serviceability.
The DT466’s remarkable durability begins with its wet-sleeve cylinder design a feature that provides superior cooling and allows for complete cylinder rebuild without block machining.
The engine block itself is cast from high-strength gray iron with exceptional rigidity that maintains precise alignment of critical components even after decades of service.
The crankshaft rotates in seven main bearings, providing extraordinary support that minimizes deflection even under maximum load conditions.
Particularly noteworthy is the DT466’s head design, which incorporates robust components that resist the cracking that plagues many competitors’ engines.
The valve train often a point of failure in high-hour engines features hardened components and generous oil delivery that ensures lubrication even under less-than-ideal conditions.
This attention to the upper engine’s durability contributes significantly to the DT466’s reputation for running virtually indefinitely with proper maintenance.
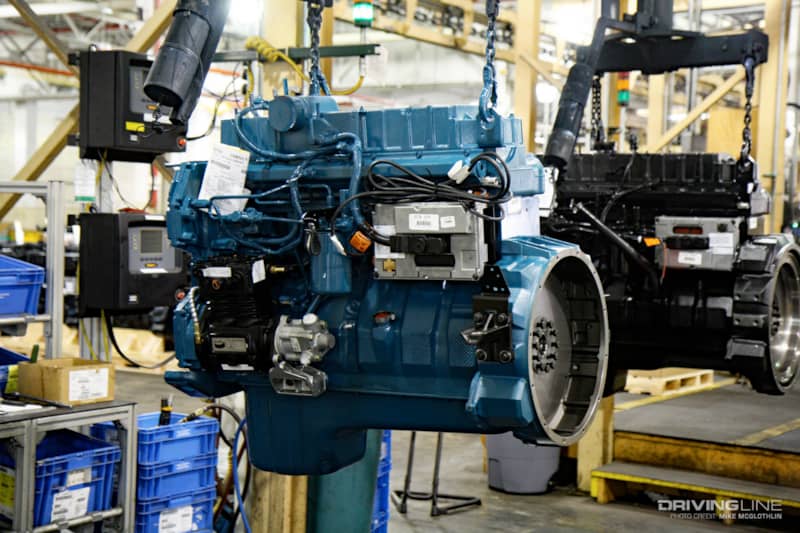
The evolution of the DT466 from mechanical (pre-1994) to electronic versions maintained its core reliability while improving emissions and efficiency.
Even the transition to high-pressure electronic fuel injection preserved the engine’s fundamental durability advantages.
This successful evolution across decades of regulatory changes highlights the inherent soundness of the original design.
In practical applications, the DT466 has proven its mettle in some of the most demanding scenarios.
School buses subjected to the constant stop-and-go operation snowplows working in sub-zero temperatures, and delivery trucks operating in scorching desert heat all demonstrate the engine’s exceptional environmental tolerance.
Municipal fleets particularly value these engines for their predictable service needs and remarkable longevity, with many examples exceeding 20,000 operational hours without internal repairs.
Perhaps most telling is the engine’s rebuilding potential. Unlike many modern designs, the DT466 was engineered from the outset for multiple service lives.
With proper maintenance, these engines can be rebuilt multiple times, with the block and major components often remaining serviceable through several cycles.
This gives the DT466 an effective service life measured in decades rather than years, explaining why these engines even older variants command premium prices in the secondary market for operators who prioritize long-term reliability over momentary acquisition costs.
7. Duramax 6.6L LB7
The Duramax 6.6L LB7, introduced in 2001 as a joint venture between General Motors and Isuzu, revolutionized the light-duty diesel truck market by combining exceptional durability with refinement previously unknown in the segment.
While later Duramax variants addressed early issues, the fundamental architecture established with the LB7 created one of the most robust diesel platforms in automotive history.
The LB7’s block is constructed from high-strength cast iron with deep skirts and six-bolt main bearing caps that provide extraordinary rigidity under load.
Unlike competitors who economized with four-bolt mains, this six-bolt design dramatically reduces crankshaft flex and bearing wear during high-torque operations.
The cylinder heads made from cast aluminum to reduce weight feature premium materials and generous cooling passages that prevent the cracking issues common in high-output diesel engines.
What truly distinguished the LB7 was its advanced common-rail fuel injection system, operating at pressures up to 23,000 psi revolutionary for its time.
While early injectors proved problematic and were covered by an extended warranty, the underlying injection architecture provided precise fuel delivery that optimized combustion efficiency while minimizing internal component stress.
Once addressed, this system contributed significantly to the engine’s longevity by reducing combustion shock and thermal loading.
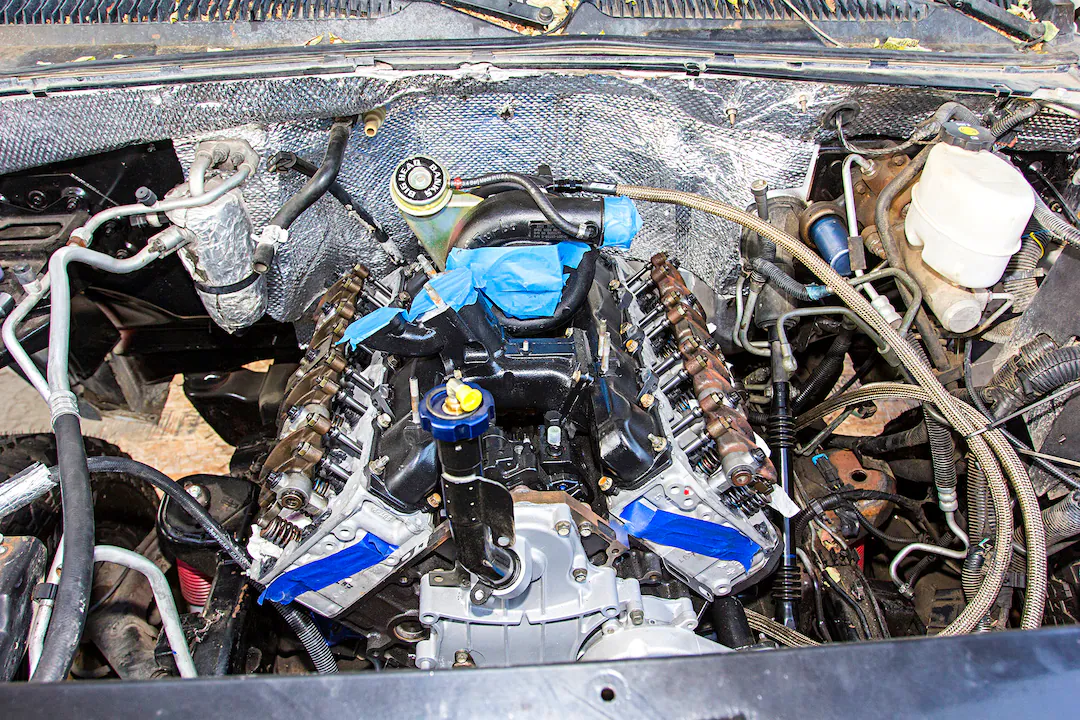
The bottom end of the LB7 deserves special attention for its durability features. The crankshaft forged from hardened steel rides in massive main bearings capable of handling far more power than the factory ratings.
Similarly, the connecting rods feature a virtually indestructible design that has proven capable of handling double the factory horsepower with minimal modification.
This overbuilt approach explains why even highly modified LB7 engines often maintain exceptional reliability.
Cooling system efficiency critical for turbocharged diesel was addressed through a high-capacity water pump, strategically placed coolant passages, and an oil cooler that effectively manages operating temperatures even under sustained high loads.
This thermal management prevents the accelerated wear that affects less sophisticated designs during demanding operations such as towing in mountainous terrain.
In real-world applications, properly maintained LB7 engines routinely exceed 300,000 miles without internal repairs, with many documented cases surpassing 500,000 miles.
Professional users in industries like construction, agriculture, and emergency services particularly value the LB7’s combination of power density and durability, often keeping these vehicles in service far beyond normal fleet replacement cycles.
The engine’s tolerance for extreme environmental conditions from sub-zero temperatures to desert heat further enhances its reputation for reliability in the most demanding circumstances.
8. John Deere PowerTech 4.5L/6.8L
The John Deere PowerTech engine family, particularly the 4.5L four-cylinder and 6.8L six-cylinder variants, stands as a testament to agricultural-grade durability adapted for a wide range of demanding applications.
Introduced in the mid-1990s and constantly refined, these engines have become legendary for their ability to operate reliably under punishing conditions from farmlands to construction sites, forestry operations to marine environments.
The foundation of the PowerTech’s durability begins with its block architecture a deep-skirt, wet-sleeve design cast from high-grade iron with exceptional rigidity.
The wet-sleeve configuration not only provides superior cooling but also allows for complete cylinder rebuilding without block machining, effectively extending the engine’s useful life through multiple service cycles.
The crankshaft a massive, forged-steel component rotates in generously sized bearings that distribute loads evenly even during peak torque production.
Thermal management is critically important for constant-load applications that receive special attention in the PowerTech design.
The cooling system features precisely controlled coolant flow that maintains consistent temperatures across the entire engine, preventing the hot spots that accelerate wear in less sophisticated designs.
An integrated oil cooler ensures lubricant stability even during extended high-output operation in extreme ambient temperatures.
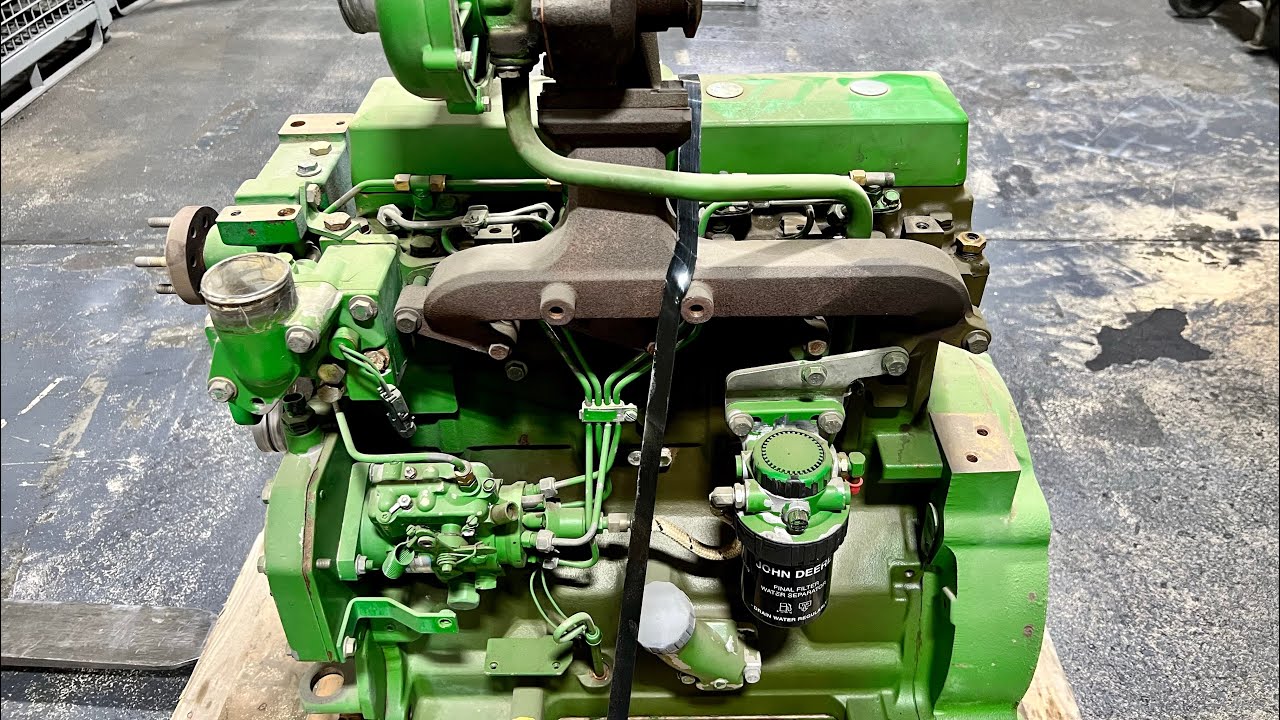
The PowerTech’s fuel system evolved from mechanical injection to advanced common-rail electronic systems without compromising reliability.
Regardless of generation, these engines demonstrate remarkable tolerance for fuel quality variations a crucial attribute for equipment operating in remote locations where premium diesel may be unavailable.
This fuel flexibility, combined with the engine’s inherent durability, makes PowerTech engines particularly well-suited for operations in developing regions with limited infrastructure.
What truly distinguishes the PowerTech series is its constant-load endurance. Unlike automotive applications with variable duty cycles, agricultural and industrial equipment often operates at near-maximum output for extended periods.
The PowerTech engines are specifically engineered for this operating profile, with generous oil capacity, efficient filtration systems, and precision-balanced rotating assemblies that minimize internal stress during sustained high-output operation.
In practical applications, PowerTech engines routinely accumulate 15,000-20,000 hours of operation before requiring significant service equivalent to nearly one million miles in highway use.
More impressively, these engines frequently maintain consistent performance parameters throughout their service life, with minimal power loss or efficiency reduction even at high hours.
This performance stability is particularly valued in applications like irrigation pumps or generators, where consistent output is essential.
PowerTech’s reputation for extreme environmental tolerance further enhances its standing among operators in challenging regions.
From Arctic logging operations to equatorial mining sites, these engines continue to perform reliably in temperature extremes that would sideline less robust designs, cementing their reputation as truly all-condition power plants.
9. Ford Power Stroke 7.3L
The Ford Power Stroke 7.3L diesel, produced from 1994 to 2003 and developed in partnership with International Navistar, has achieved legendary status among diesel enthusiasts and commercial operators for its exceptional reliability and longevity.
This 444-cubic-inch V8 turbodiesel powered Ford’s heavy-duty pickup trucks and established new standards for durability in the consumer diesel market. The 7.3L Power Stroke’s remarkable toughness begins with its fundamental architecture.
The engine block cast from high-strength gray iron features extraordinary wall thickness and rigid main bearing supports that maintain the perfect alignment of rotating components even after hundreds of thousands of miles.
The crankshaft is forged from high-grade steel and supported by massive main bearings capable of handling far more torque than factory specifications.
Similarly, the connecting rods and pistons are dimensioned with significant safety margins, explaining why even heavily modified 7.3L engines rarely experience bottom-end failures.
The hydraulically actuated, electronically controlled unit injector (HEUI) fuel system represents an engineering breakthrough that contributed significantly to the engine’s durability.
By eliminating the traditional high-pressure mechanical injection pump often a failure point in diesel engines the HEUI system distributes stress more evenly throughout the engine.
While complex in principle, this system proved remarkably reliable in practice, with many injectors exceeding 200,000 miles before requiring service.
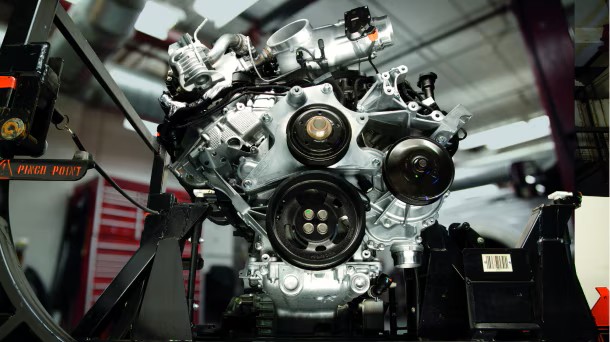
Cooling system efficiency, critically important for turbocharged engines, receives special attention in the 7.3L design.
The engine features precisely controlled coolant flow that maintains consistent temperatures across both cylinder banks, preventing the hot spots that accelerate wear in less sophisticated designs.
An efficient oil cooler ensures lubricant stability even during extended towing in extreme ambient temperatures.
In real-world applications, the 7.3L Power Stroke demonstrates extraordinary endurance. Commercial fleet vehicles frequently exceed 500,000 miles on original internal components with proper maintenance, with many documented cases surpassing 750,000 miles.
Even more impressive is the engine’s tolerance for less-than-ideal maintenance while regular service maximizes longevity, these engines frequently survive maintenance lapses that would destroy less robust designs.
Perhaps most telling is the 7.3L’s performance in extreme duty applications. From snowplows operating in sub-zero temperatures to utility trucks in desert environments, from high-altitude work in mountain regions to coastal operations in high-humidity conditions, the 7.3L consistently delivers reliable performance across environmental extremes.
This universal capability explains why these engines, though no longer in production for nearly two decades, remain highly sought after by operators who prioritize reliability above all other factors.
10. Toyota 1HD-FTE
The Toyota 1HD-FTE 4.2-liter inline-six turbodiesel engine represents the pinnacle of Japanese diesel engineering focused on ultimate reliability in the most challenging environments.
Featured primarily in the Land Cruiser 100 Series and various industrial applications between 1998 and 2007, this powerplant has earned legendary status among expedition travelers, military users, aid organizations, and others who operate in remote regions where engine failure could have catastrophic consequences.
The 1HD-FTE’s extraordinary durability begins with its block construction a deep-skirt design cast from high-grade iron with exceptional wall thickness and seven main bearings supporting the crankshaft.
This overbuilt foundation ensures perfect alignment of rotating components even after decades of use on punishing terrain.
The cylinder head also constructed from cast iron rather than the more common aluminum resists warping even under extreme thermal conditions, maintaining perfect sealing regardless of the operating environment.
Fuel system reliability, critically important in regions with variable fuel quality, was addressed through a conservative high-pressure common-rail design that balanced performance with durability.
The injectors and high-pressure pumps were engineered with significant safety margins, allowing them to function reliably even with diesel fuel containing higher levels of contaminants or water than would be acceptable to more highly-strung designs.
This fuel tolerance makes the 1HD-FTE particularly valuable in developing regions where fuel filtration may be compromised.
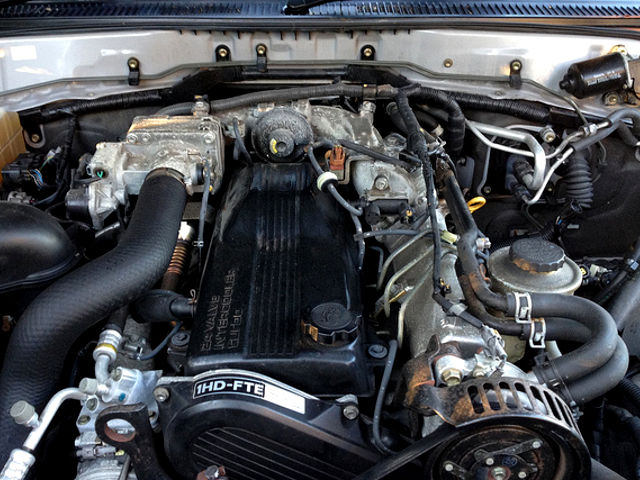
The cooling system deserves special mention for its contribution to the engine’s extreme-condition capability.
Designed specifically for operation in ambient temperatures ranging from -40°C to +50°C, the system maintains optimal operating temperatures regardless of external conditions or load factor.
This thermal stability prevents the accelerated wear that affects engines operating near their thermal limits in challenging environments.
What truly distinguishes the 1HD-FTE is its documented reliability record in the demanding regions.
From the Australian Outback to the Sahara Desert, from the Siberian tundra to the Amazonian rainforest, these engines routinely deliver 500,000+ kilometers of service in environments where maintenance facilities may be thousands of kilometers away.
This real-world performance has made the 1HD-FTE the preferred power plant for organizations operating in conflict zones, disaster areas, and other critical missions where engine failure is not an option.
The engine’s reputation is further enhanced by its exceptional tolerance for extended service intervals when necessary.
While Toyota specifies conventional maintenance schedules, 1HD-FTE engines have repeatedly demonstrated the ability to maintain operation far beyond recommended service intervals when circumstances prevent routine maintenance a crucial attribute for expedition and remote industrial applications.
This combination of fundamental durability and operational flexibility explains why vehicles powered by the 1HD-FTE often command premium prices even decades after manufacture, particularly for use in regions where absolute reliability trumps all other considerations.
Also Read: 12 Legendary Cars That Defined a Generation of Automaking