Engines are the heart of countless machines that power industries, transport goods, and support critical infrastructure.
While many engines are built to perform under ideal conditions, only a select few can withstand the harsh realities of operating with substandard fuel.
In many parts of the world, particularly in developing regions and remote areas, fuel quality is often inconsistent, contaminated, or improperly stored.
Water intrusion, sediment buildup, and low-grade fuel blends can wreak havoc on engines, causing breakdowns, clogging injectors, and damaging internal components.
Yet, there are engines renowned for their exceptional ability to keep running even when fed fuel that would cripple lesser machines.
For decades, engineers and manufacturers have worked tirelessly to design engines that not only deliver power and efficiency but also resilience.
These engines feature advanced filtration systems, robust fuel injection technologies, and heavy-duty components that help them survive and thrive on poor-quality fuel.
Their reputation for durability has made them a top choice in regions where clean, high-grade fuel is a luxury rather than a guarantee.
The ability to handle bad fuel isn’t just a technical triumph—it’s a lifeline for businesses, farmers, aid workers, and industries that rely on continuous operation in challenging environments.
From rugged diesel generators in Africa to agricultural machinery in Southeast Asia, these engines prove their worth every day by providing reliable service no matter the fuel quality.
In this article, we will explore what makes these engines virtually indestructible, go into the engineering innovations that set them apart, and highlight some of the most trusted models and brands that have earned a legendary reputation for reliability in the toughest conditions.
Also Read: You Can Still Buy This 1980s Engine Brand New From the Factory
These Engines Can Run on Bad Fuel — and They Still Won’t Die.
The Challenge of Poor-Quality Fuel
In an ideal world, engines would always run on clean, high-quality fuel. However, in reality, many operators face the daily struggle of dealing with contaminated or degraded fuel.
Poor-quality fuel can result from various issues: improper storage, water contamination, microbial growth, the presence of dirt and debris, and substandard refining processes.
Diesel fuel, in particular, is prone to developing sludge or being mixed with kerosene or other diluents in some regions, further degrading its quality.
The consequences of using bad fuel are severe. It can clog fuel filters, damage injectors, cause uneven combustion, and lead to carbon buildup in the engine. Over time, this not only reduces engine efficiency but can cause complete engine failure.
For operations in remote areas—whether it’s mining in Africa, farming in rural India, or humanitarian aid in conflict zones—engine failure is not an option. This is where engines designed to tolerate poor fuel quality become invaluable.
Engineering Innovations Behind Fuel-Tolerant Engines
What allows some engines to withstand bad fuel when others fail? The answer lies in several key engineering innovations:
-
Advanced Filtration Systems:
Fuel-tolerant engines come equipped with multi-stage fuel filtration systems designed to capture water, dirt, and other contaminants before they reach sensitive engine components. These filters often feature water-separating capabilities and are built to be durable and easy to replace in the field. -
Robust Fuel Injection Systems:
Engines that excel in bad-fuel environments often use mechanical fuel injection systems instead of sensitive electronic ones. Mechanical systems are generally more forgiving of contaminants and can continue to operate even when small particles pass through the filters. -
Heavy-Duty Components:
Internal engine components such as pistons, cylinders, and valves are made from hardened materials and precision-engineered to withstand abrasive particles and chemical impurities. This ensures long-lasting durability even under tough conditions. -
Flexible Combustion Tolerances:
Some engines are designed with broader combustion tolerance ranges, allowing them to run efficiently even when the fuel-air mixture is less than optimal due to poor fuel quality. -
Automatic Air Purge Systems:
To address water contamination, some engines feature automatic air purge or water drainage systems that expel unwanted moisture before it can cause significant harm.
Trusted Engine Brands and Models Known for Fuel Tolerance
Over the years, certain engine brands and models have become legendary for their ability to run on poor-quality fuel. Here are some of the top performers:
-
Perkins 1100 Series:
The Perkins 1100 Series engines are widely known for their ruggedness and adaptability. Used in generators, tractors, and construction machinery, these engines are equipped with top-tier filtration systems and mechanical injectors, making them a favorite in Africa and Southeast Asia where fuel quality can be inconsistent. -
Cummins B Series (6BT):
The Cummins 6BT, part of the B Series, has earned a global reputation as one of the toughest diesel engines around. Its mechanical fuel system, robust design, and exceptional durability make it a go-to choice for trucks, buses, and industrial machines operating in harsh environments with unreliable fuel supplies. -
Kubota V2203:
Kubota’s V2203 engine, commonly found in tractors and compact construction equipment, is celebrated for its reliability and ease of maintenance. Its simple design, mechanical injection system, and high-tolerance components make it particularly resilient when running on low-quality fuel. -
Yanmar TNV Series:
Yanmar engines, especially the TNV Series, are famous for their long life and ability to perform in challenging conditions. Their precision engineering and strong filtration systems have made them popular in agricultural and marine applications. -
Deutz Air-Cooled Engines:
Deutz is known for its air-cooled engines, which not only excel in high-heat environments but also boast strong resistance to bad fuel. Their simplicity and mechanical design make them favorites in mining and remote construction sites.
Real-World Success Stories
The best testament to these engines’ capabilities comes from those who rely on them daily. In rural Kenya, for example, smallholder farmers use Perkins-powered irrigation pumps that run smoothly despite the local diesel often being contaminated with water and particulates.
A farmer reported using the same engine for over 15 years, requiring only basic maintenance and filter replacements.
In India, where adulterated diesel is a common issue, many truckers prefer Cummins-powered vehicles. A trucking company owner shared that his fleet of Cummins 6BT engines regularly travels long distances with minimal breakdowns, even when forced to buy fuel from unreliable roadside vendors.
In Southeast Asia, rice farmers praise the durability of Kubota engines, which often operate in muddy, wet conditions that compromise fuel purity. These engines keep their fields irrigated and their harvests on track, year after year.
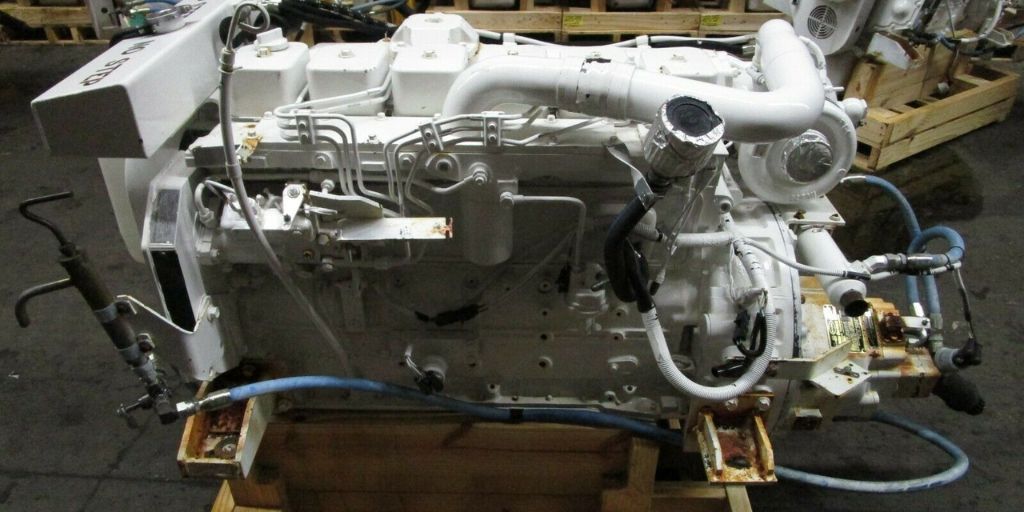
Humanitarian organizations operating in crisis zones, such as refugee camps in the Middle East, rely on Yanmar and Deutz-powered generators to provide consistent electricity despite the challenges of contaminated fuel supplies.
These engines have become trusted lifelines, ensuring that essential services like medical care and communications continue uninterrupted.
Maintenance Best Practices for Using Poor-Quality Fuel
While these engines are built to endure bad fuel, regular maintenance is still crucial to prolonging their lifespan. Here are some best practices farmers, operators, and technicians follow:
-
Frequent Filter Changes: Regular replacement of fuel filters is essential, especially in areas known for contaminated fuel. Some operators change filters every 100–200 operating hours.
-
Water Drainage: Checking and draining water separators helps prevent water-related damage.
-
Fuel Additives: Using fuel additives designed to clean injectors and improve combustion can mitigate some effects of poor fuel.
-
Proper Storage: Whenever possible, storing fuel in clean, sealed containers reduces the risk of contamination before it even enters the engine.
-
Routine Inspections: Regularly checking fuel lines, tanks, and injectors for signs of wear or blockages ensures early detection of potential problems.
The Future of Fuel-Tolerant Engines
As fuel quality remains an ongoing issue in many parts of the world, engine manufacturers continue to innovate. We are seeing the development of:
-
Self-Cleaning Filters: Some next-generation engines are being equipped with self-cleaning fuel filters that reduce manual intervention and extend service intervals.
-
Hybrid Fuel Systems: Advances in hybrid fuel systems that combine diesel with alternative fuels like biodiesel or synthetic fuels are providing more flexibility and cleaner operation, even when traditional fuel is subpar.
-
Smart Monitoring: Remote monitoring systems that alert operators to fuel quality issues in real-time are becoming more common, helping to prevent damage before it occurs.
These advances promise to make the next generation of engines even more robust and fuel-tolerant, ensuring that they continue to deliver in the harshest environments.
The Economic Impact of Reliable Engines
One often overlooked aspect of these resilient engines is their significant economic impact, particularly in regions where both resources and infrastructure are limited.
When engines break down due to fuel-related issues, the cost of repairs, lost productivity, and downtime can be devastating. In agriculture, a broken-down irrigation pump during the peak of the dry season can mean the loss of an entire crop.
In construction, delays caused by engine failures can push back project timelines, inflate costs, and damage business reputations.
Engines that are designed to withstand poor-quality fuel reduce these risks dramatically. Their reliability means less frequent repairs, lower maintenance costs, and minimal operational disruptions.
This has a multiplier effect: farmers can cultivate more land with confidence, businesses can expand their operations, and humanitarian organizations can provide consistent aid services.
For smallholder farmers and local entrepreneurs, these engines are not just machines—they are investments in economic stability.
The long service life and low maintenance demands of robust engines allow owners to allocate their limited financial resources more effectively, fostering growth and resilience in communities that need it most.
Training and Knowledge Sharing
Another key factor in the success of fuel-tolerant engines is the emphasis on training and knowledge sharing.
Many manufacturers and NGOs provide hands-on training for local mechanics and operators, teaching them how to maintain and repair these engines effectively, even in the most basic workshop settings.
This ensures that even in remote areas, the skills and expertise necessary to keep engines running are readily available.
In regions like sub-Saharan Africa and rural Southeast Asia, communities have built informal networks of skilled technicians who specialize in specific engine brands.
These local experts become invaluable resources, helping others troubleshoot issues, replace parts, and keep vital equipment operational, regardless of fuel quality.
Environmental Considerations
While these engines excel at running on bad fuel, there’s growing awareness of their environmental impact. Poor-quality fuel tends to produce higher emissions and can contribute to air pollution.
To address this, many manufacturers are investing in cleaner technologies that balance ruggedness with reduced environmental footprints.
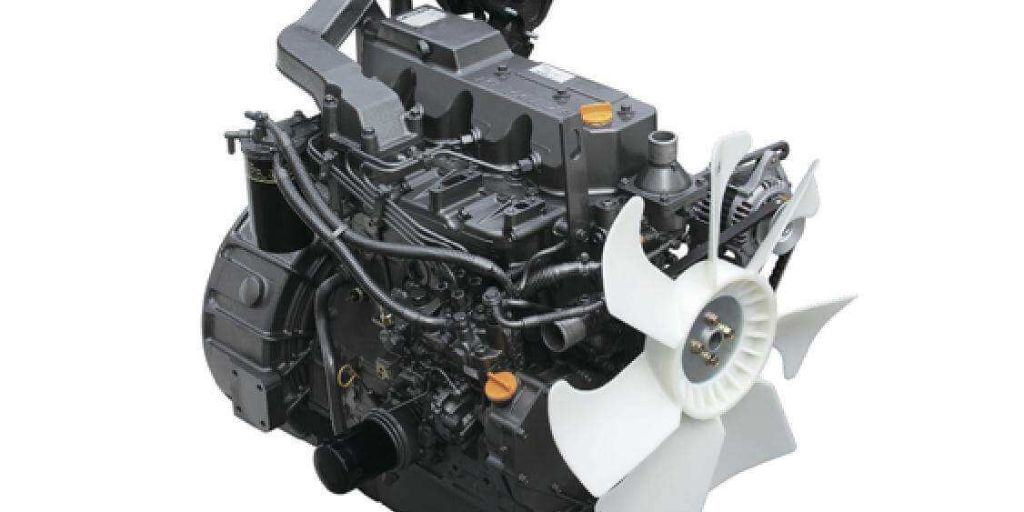
Low-emission models and the introduction of biofuels compatible with existing engines are helping to mitigate the environmental effects, ensuring that reliability doesn’t come at the cost of sustainability.
The story of engines that can withstand bad fuel is one of remarkable engineering and human ingenuity. In parts of the world where fuel quality is unpredictable and environmental challenges are relentless, these engines stand as symbols of resilience and reliability.
Their ability to operate on contaminated, low-grade, or adulterated fuel not only ensures uninterrupted work but also provides a lifeline to countless communities that rely on machinery for their livelihoods and essential services.
Brands like Perkins, Cummins, Kubota, Yanmar, and Deutz have become trusted names in this space, earning their reputations through years of dependable performance in some of the toughest conditions imaginable.
Farmers, truckers, humanitarian workers, and industrial operators all share stories of how these engines have kept their operations running when everything else seemed to falter.
Looking to the future, innovations such as self-cleaning filters, hybrid fuel systems, and smart monitoring technologies promise to enhance these engines’ capabilities even further.
Yet, at their core, the most trusted engines will continue to be those that prioritize durability, simplicity, and ruggedness—qualities that have always mattered most in the field.
In a world where fuel quality cannot always be guaranteed, these engines offer peace of mind and security.
Their steadfast performance, even on bad fuel, is a testament to engineering excellence—and a reason why, no matter the challenges ahead, they remain irreplaceable allies in the global drive for progress and productivity.
Also Read: 5 Cars That Easily Pass 250K Miles and 5 That Rarely Get Close