When we think of most internal combustion engines (ICE), we immediately imagine the need for cooling systems to prevent overheating. Water-based cooling has been the standard for many years, providing a way to regulate engine temperature and keep it running efficiently.
However, not all engines rely on water cooling to function optimally. There are types of engines, particularly in specialized fields, that operate without the need for conventional water-based cooling systems.
These engines may use alternative methods such as air cooling, oil cooling, or even new-age technologies like thermoelectric cooling.
This article explores the science behind engines that don’t rely on traditional water cooling, understanding their design, principles, and applications.
Also Read: The Engines Mechanics Would Bet Their Own Money On
1. Traditional Water Cooling Systems: A Quick Recap
Before diving into engines that don’t need water cooling, it’s essential to briefly review why water cooling is so ubiquitous in traditional engines.
In most internal combustion engines, water cooling is used to maintain the temperature of engine components, preventing them from overheating. The process typically works as follows:
-
Coolant (water mixed with antifreeze) is circulated through channels in the engine, absorbing heat from the engine block and cylinder head.
-
The coolant is then pumped into a radiator where the heat is dissipated by airflow.
-
The cooled coolant then returns to the engine, where it continues to absorb heat.
Water cooling is highly effective because water has a high specific heat capacity, meaning it can absorb and retain a lot of heat before its temperature rises significantly.
This makes water an ideal medium for cooling engine components, which are exposed to extreme temperatures during operation.
However, while water cooling is efficient and well-established, there are certain circumstances and engine types where it’s not required, or even desired.
2. Air-Cooled Engines: A Classic Alternative
Air-cooled engines are one of the oldest and most common alternatives to water-cooled designs. Instead of using liquid coolant, these engines rely on air flowing over the engine components to dissipate heat.
A. How Air-Cooled Engines Work
Air-cooled engines typically have a series of fins attached to the engine block and cylinder heads. These fins increase the surface area of the engine, allowing more air to contact the metal surfaces and carry away heat.
The engine relies on the movement of air (either from the vehicle’s motion or a fan) to keep the temperature within safe limits.
-
Fins: The engine components, particularly the cylinder heads, have finned structures to improve heat dissipation. The more surface area exposed to the air, the more heat can be carried away.
-
Fan: Many air-cooled engines use a fan to help move air over the engine. The fan increases airflow, ensuring that the engine remains cool even when the vehicle is stationary or moving at low speeds.
B. Benefits of Air-Cooled Engines
-
Simplicity: Air-cooled engines do not require the complex plumbing of radiators, hoses, and water pumps. This reduces the likelihood of failure associated with water cooling systems.
-
Weight: Without the need for a water cooling system, air-cooled engines are typically lighter, which is especially advantageous in applications where every ounce counts, such as in motorcycles or small aircraft.
-
Durability: Air-cooled engines tend to have fewer parts, meaning there are fewer components that can wear out over time.
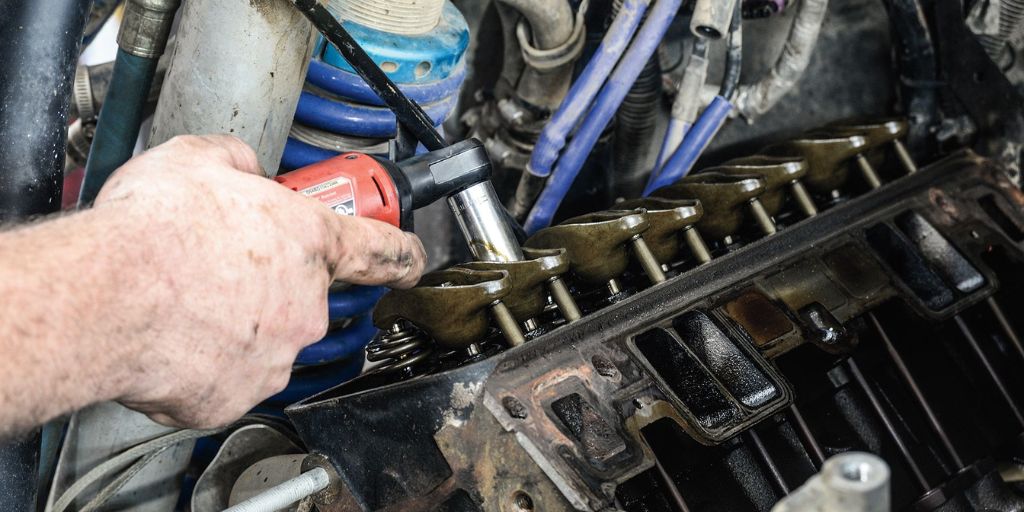
C. Drawbacks of Air-Cooled Engines
-
Less Efficient Cooling: While air is readily available, it is less efficient at absorbing heat than water. Air-cooled engines must be larger or operate at lower temperatures to avoid overheating.
-
Limited Power: Since air-cooled engines cannot handle the same high levels of heat as water-cooled engines, they are typically limited in power output, which is why air-cooling is often found in smaller, lower-power engines.
D. Applications of Air-Cooled Engines
Air-cooled engines are commonly found in motorcycles, small aircraft, lawnmowers, and certain automotive applications like the iconic Volkswagen Beetle. Their simplicity and reliability make them ideal for these situations.
3. Oil-Cooled Engines: Another Approach to Heat Management
While air-cooled engines rely on the movement of air to dissipate heat, oil-cooled engines use engine oil to manage temperature. The oil, which circulates through the engine, not only lubricates the components but also absorbs and carries away heat from critical areas.
A. How Oil-Cooled Engines Work
In oil-cooled engines, the oil is pumped through a series of passages in the engine block, cylinder head, and other parts.
The oil absorbs heat from these components and is then pumped through an external oil cooler, often located near the radiator, where it dissipates the heat. The cooled oil is then returned to the engine to continue the cycle.
-
Oil Cooler: Similar to a radiator in a water-cooled engine, the oil cooler dissipates heat from the engine oil. It works by circulating oil through a heat exchanger that allows heat to escape.
-
Thermal Management: Oil is much better at maintaining a stable operating temperature over a wide range of conditions. It also helps to prevent the engine from developing hot spots that could lead to catastrophic failure.
B. Benefits of Oil-Cooled Engines
-
More Efficient Than Air Cooling: Oil absorbs and dissipates heat more effectively than air, which allows oil-cooled engines to maintain lower temperatures while operating at higher power levels.
-
Compact Design: Oil cooling systems are more compact than water cooling systems, making them ideal for vehicles with limited space.
-
Reduced Maintenance: Since oil-cooled engines don’t require the frequent maintenance associated with water-cooling systems (like replacing coolant, fixing leaks, or maintaining a radiator), they can be more reliable and less maintenance-intensive.
C. Drawbacks of Oil-Cooled Engines
-
Oil Breakdown: Over time, engine oil can degrade, especially at high temperatures. This means that the oil must be changed regularly, or it can lose its effectiveness at both lubricating and cooling.
-
Complexity: While simpler than water cooling systems, oil-cooling systems still require additional components such as oil coolers, pumps, and more intricate oil passages.
D. Applications of Oil-Cooled Engines
Oil-cooled engines are commonly found in high-performance motorcycles, sports cars, and certain industrial machinery. Vehicles like BMW motorcycles and some Porsche engines use oil cooling systems to handle the extra heat generated by their performance engines.
4. Solid-State Cooling: The Future of Engine Cooling?
As technology continues to advance, traditional cooling methods are being complemented by solid-state cooling techniques, which use thermoelectric materials to directly transfer heat without requiring fluids.
A. Thermoelectric Cooling
Thermoelectric cooling relies on the Peltier effect, a phenomenon where heat is transferred from one side of a material to another when an electrical current is applied.
This can be used to cool engine components by directly transferring heat away from the hot parts and into the surrounding environment.
-
Peltier Modules: These solid-state devices are used to absorb heat from the engine components and expel it on the other side. The Peltier effect is reversible, so it can also be used for heating applications.
-
No Fluids Required: One of the primary advantages of thermoelectric cooling is that it doesn’t rely on fluids like water or oil, reducing the complexity of the cooling system.
B. Benefits of Solid-State Cooling
-
No Moving Parts: Unlike traditional cooling systems that rely on pumps, fans, and radiators, thermoelectric coolers have no moving parts, making them less prone to mechanical failure.
-
Compact and Lightweight: The absence of pumps and pipes makes thermoelectric cooling systems incredibly compact, which is particularly useful in automotive or aerospace applications where space and weight are critical.
-
Energy Efficiency: Solid-state cooling can be more energy-efficient in some cases, as it can operate without requiring a significant amount of power.
C. Drawbacks of Solid-State Cooling
-
Heat Dissipation Challenges: While thermoelectric materials can absorb heat effectively, they often struggle to expel it efficiently, which can limit their use in high-heat environments such as large engines.
-
Cost and Scalability: Thermoelectric coolers are still relatively expensive to produce, and scaling up the technology to handle larger engines is a significant challenge.
D. Applications of Solid-State Cooling
Solid-state cooling is still in the experimental stage for automotive and industrial applications. However, it has been used in niche applications such as cooling electronic components, small devices, and even some experimental aircraft designs.
5. Hybrid Cooling Systems: Combining Techniques for Maximum Efficiency
In some modern engine designs, manufacturers opt for hybrid cooling systems that combine several methods to achieve optimal thermal management. These systems might use a combination of air cooling, oil cooling, and even water cooling, all in one engine.
A. How Hybrid Cooling Works
In a hybrid system, the engine may rely on air cooling for the majority of the cooling process, but when higher temperatures are reached, oil cooling or even water cooling might be activated to prevent overheating.
This approach ensures that the engine can maintain high performance while also reducing weight and complexity.
-
Smart Systems: Hybrid systems often use sensors to monitor engine temperature and adjust the cooling process in real-time. This adaptability ensures the engine is always operating within the optimal temperature range.
-
Cost vs. Efficiency: Hybrid systems can be more expensive due to the additional components involved but can offer a significant increase in efficiency and reliability for certain high-performance or specialized engines.
B. Benefits of Hybrid Cooling Systems
-
Adaptable to Different Conditions: Hybrid systems can adjust cooling methods depending on the engine’s load and operating conditions, ensuring optimal efficiency and temperature management.
-
Optimized Performance: By using multiple cooling methods, these systems ensure the engine operates at the highest levels of performance without overheating or underperforming.
C. Applications of Hybrid Cooling Systems
Hybrid cooling systems are often used in high-performance cars, aircraft, and racing engines, where both weight and thermal efficiency are critical factors.
7. Emerging Technologies and the Future of Engine Cooling
As we look to the future, innovations in engine cooling technologies are expected to make significant strides, especially as the automotive and industrial sectors transition to more sustainable and efficient solutions.
The continuous demand for higher performance, lower emissions, and better fuel efficiency will drive the development of advanced cooling systems that go beyond traditional methods.
A. Heat Pipes and Loop Heat Pipes (LHPs)
One promising development in engine cooling is the use of heat pipes and loop heat pipes (LHPs). These systems are already used in electronics and space applications but are now being considered for use in automotive engines.
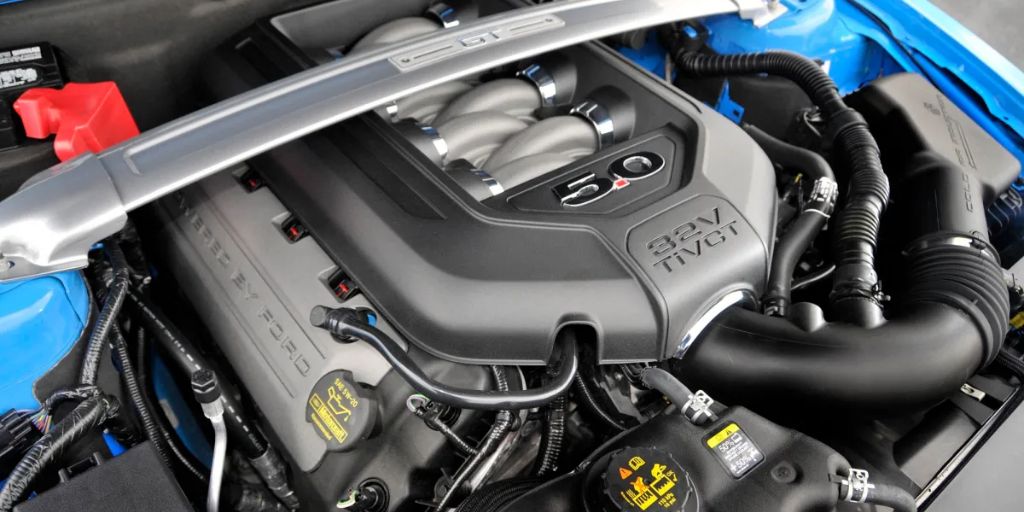
Heat pipes work by utilizing a liquid that evaporates to absorb heat and then condenses to release the heat in another location. This cycle allows for efficient heat transfer without the need for external cooling fluids like water or oil.
These systems are incredibly compact and lightweight, making them ideal for engines where space and weight are at a premium.
B. Phase Change Materials (PCMs)
Another emerging technology involves the use of phase change materials (PCMs). These materials absorb or release heat as they change from solid to liquid or vice versa.
By integrating PCMs into engine designs, manufacturers could create systems that passively absorb heat during high-performance periods and release it as needed.
This would allow for more consistent temperature regulation without relying on traditional fluid-based systems.
C. Future Hybrid Engines
As hybrid electric vehicles (HEVs) and fully electric vehicles (EVs) gain popularity, cooling technology will continue to evolve.
Electric motors typically don’t require the same cooling systems as ICE engines, but high-performance electric motors and batteries still need to be managed thermally.
Future hybrid engines could combine advanced cooling systems from both electric and combustion technologies, leading to more efficient, lightweight, and sustainable solutions.
Engines that don’t rely on traditional water cooling represent an intriguing evolution in automotive and industrial engineering.
Air-cooled engines, oil-cooled engines, and emerging solid-state cooling technologies each offer unique advantages in terms of simplicity, weight, and performance.
While water cooling remains the most common and efficient method for maintaining engine temperatures, these alternatives provide valuable options for specific applications.
As technology advances, it’s likely that new cooling methods will continue to emerge, pushing the boundaries of how we think about engine design and performance.
Whether through improved materials, smarter systems, or solid-state cooling, the future of engines without water cooling looks promising — offering efficient, durable, and lightweight solutions for a range of applications.
Also Read: What Makes the Toyota 1HZ the Most Respected Off-Road Engine?