Diesel powertrains have long been celebrated for their fuel efficiency, torque delivery, and longevity.
Yet, in real‐world practice, a diesel engine of identical make and model can exhibit remarkably different service lives depending on whether it plies the highways of Nairobi or the interstates of Chicago.
In many African markets—particularly sub‐Saharan regions—well‐maintained diesel engines routinely surpass 800,000 to over 1,200,000 kilometers before a full rebuild becomes necessary. Meanwhile, in the United States, comparable engines often reach “economic end of life” around 500,000 to 600,000 kilometers.
What underlies this disparity? While metallurgy, manufacturing quality, and design play important roles, the primary drivers of diesel engine longevity lie in the broader operating context: regulatory and emissions requirements, fuel characteristics, maintenance philosophies, duty cycles, climate effects, economic realities, and the availability (or absence) of parts and specialized service.
In Africa, the convergence of simpler engine architectures, robust local service cultures, moderate driving demands, warm climates, and powerful economic incentives to maintain rather than replace powerplants creates conditions under which diesels can soldier on far beyond the mileage deemed “excessive” in the U.S.
This article delves into each of these factors in depth, examining how far‐reaching policy choices, local practices, and environmental contexts shape a diesel engine’s real‐world lifespan—and why the same engine that might be condemned as worn out in North America can still be going strong after a million kilometers in East Africa.
Also Read: The Engines Mechanics Would Bet Their Own Money On
1. Emissions Regulations and Engine Complexity
Since the mid‐2000s, U.S. diesel engines—light‐duty pickups, heavy‐duty trucks, buses—have been subject to increasingly stringent federal emissions standards.
Key milestones include the 2007 heavy‐duty particulate‐matter limits, 2010 requirements for on‐board urea‐fed selective catalytic reduction (SCR) to cut NOₓ emissions, and successive reductions in permissible soot and nitrogen oxide output.
Meeting these mandates has forced manufacturers to integrate complex aftertreatment hardware—diesel particulate filters (DPFs), SCR catalysts, exhaust gas recirculation (EGR) valves, differential pressure sensors, NOₓ probes—and to rely on ultra‐precise common‐rail fuel injection systems with closed‐loop electronic controls.
Each of these components can malfunction, clog, or degrade over time: DPFs require periodic high‐temperature regenerations (or professional cleaning); SCR injectors and urea dosing modules can freeze in cold weather; EGR valves foul with soot; high‐pressure pumps and piezoelectric injectors demand immaculate fuel and specialized diagnostic tools.
In practice, the sheer complexity of U.S. diesel systems creates more potential failure points, each carrying significant repair costs and downtime.
Lighter‐Touch African Regulatory Environment
In contrast, most African countries—outside of South Africa and a handful of urban centers—impose minimal in‐use emissions requirements and allow older, less refined diesel technologies to remain on the road.
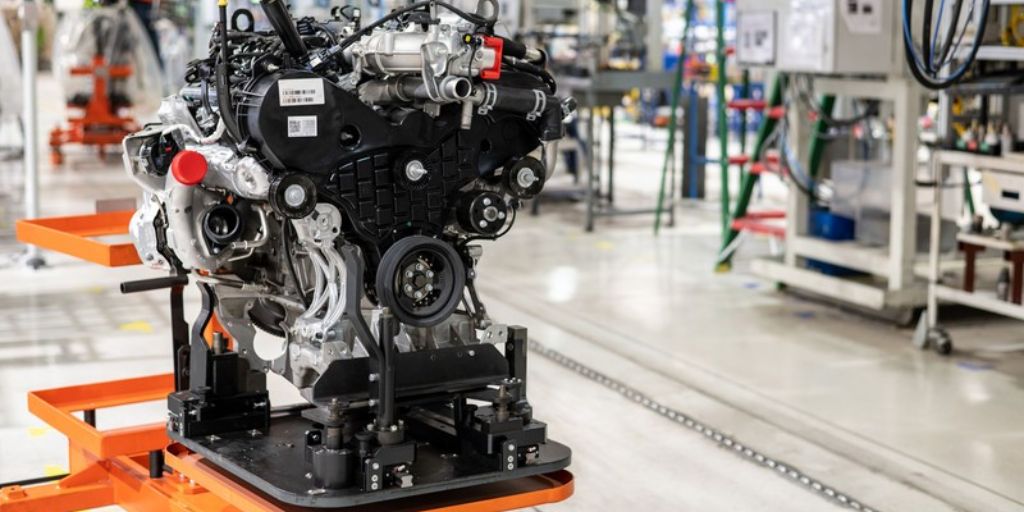
Engines built before the advent of DPFs and SCR systems continue in service, often with only basic mechanical fuel injection and simple exhaust plumbing.
Without the need to accommodate bulky aftertreatment hardware or high‐pressure injection electronics, these engines retain robust cast‐iron blocks, straightforward injector pumps, and minimal sensor arrays—an architecture proven over decades to be extraordinarily durable and easy to repair in resource‐constrained settings.
2. Fuel Quality: “Dirty” Versus Ultra‐Clean
Diesel fuel sold in many African markets commonly contains sulfur levels ranging from 50 to 500 parts per million, and in some regions, batches with over 1,000 ppm still circulate.
Local distribution infrastructure, regulatory oversight, and the economics of global fuel trading mean that so‐called “off‐spec” cargoes—viable for heavy equipment and tractors—often supply urban filling stations.
Older diesel engines, designed with looser internal clearances and mechanical injection pumps lubricated by the fuel itself, tolerate higher levels of particulate contamination and sulfur without catastrophic failure.
U.S. Ultra‐Low Sulfur Diesel and Biodiesel Blends
By law, U.S. diesel must contain no more than 15 ppm sulfur (ULSD), and many fleets also use biodiesel blends (B5, B20) or detergent additives.
While ULSD and biodiesel improve aftertreatment longevity and reduce certain emissions, they place greater demand on high‐precision common‐rail injectors and on seals and hoses—some of which can degrade prematurely when exposed to bio‐solvents.
Trace water in fuel can wreak havoc on high‐pressure systems, leading to injector failures that are expensive and time‐consuming to diagnose and replace.
3. Maintenance Culture: Preventive Preservation
In many African communities, diesel vehicles—ranging from small buses and lorries to agricultural tractors—represent irreplaceable income generators. Their owners and operators adopt a proactive maintenance regimen:
-
Frequent Oil and Filter Changes: Every 5,000–10,000 kilometers, often aligned with load factors and seasonal conditions.
-
Regular Fuel and Air‐Filter Swaps: To keep abrasive dust and water out of the combustion chamber and injectors.
-
Routine Inspections and Mechanical Overhauls: Local workshops rebore cylinders, regrind crankshafts, replace liners, and fabricate gaskets and seals on site.
-
Cottage‐Industry Rebuilding: Village and town machinists perform compression checks, valve adjustments, and injector calibrations without proprietary diagnostic tools.
This hands‐on approach—often led by owner‐mechanics who personally rely on each vehicle for livelihood—ensures that minor wear is caught early and addressed immediately. Engines are periodically “freshened up” long before wear accumulates to a critical threshold.
U.S. Extended‐Service Intervals and Dealer Dependence
Conversely, many U.S. fleets leverage manufacturer‐backed extended‐service intervals—stretching oil changes to 15,000–25,000 miles under warranty guidelines.
While superficially efficient, longer intervals allow soot, metal particulates, and combustion byproducts to concentrate, accelerating wear on piston rings, cylinder walls, and bearings.
Simultaneously, the complexity of modern diesel systems often mandates dealer‐only service, and proprietary software locks out independent mechanics.
High parts and labor costs discourage mid‐life rebuilds, leading many owners to defer maintenance until failure becomes imminent.
4. Operational Profiles: Duty Cycles and Load Patterns
On many African routes—where paved roads are limited and speed limits conservative—diesel engines operate predominantly at low to mid RPMs (1,200–2,000 rpm), hauling moderate loads across uneven terrain. This steady‐state, torque‐focused operation minimizes:
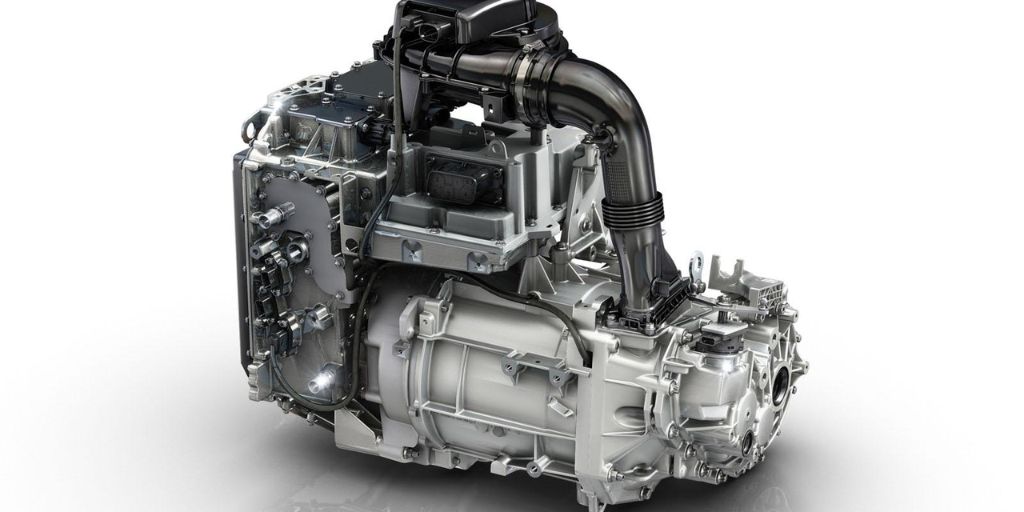
-
Thermal spikes that can warp cylinder heads or crack pistons.
-
Rapid turbocharger on/off cycling that fatigues turbine blades and seals.
-
The high‐speed wear on bearing surfaces and valvetrain components.
The result is a more uniform wear pattern and reduced peak stress on internal parts.
Highway Speeds and Heavy Loads in the U.S.
In North America, long‐haul trucks cruise at 60–75 mph (2,200–2,800 rpm) fully laden up to 80,000 pounds gross vehicle weight.
Frequent idling at weigh stations or urban delivery points, combined with aggressive throttle inputs to maintain highway speeds, subjects engines to cyclical thermal and mechanical stresses.
High oil temperatures and sustained bearing loads accelerate fatigue, and repeated cold‐start cycles amplify abrasive wear.
5. Climate Effects: Temperature and Condensation
Most of sub‐Saharan Africa enjoys ambient temperatures well above 15 °C (60 °F) year‐round. Engines warm up quickly, spending minimal time in the critical “boundary lubrication” phase—when metal surfaces rub with only a thin oil film, causing elevated wear.
Warm conditions also reduce water condensation in crankcases and fuel systems, lowering the risk of corrosion, acid formation, and microbial growth in stored fuel.
Cold Climates and Moisture Challenges
In many U.S. regions, winter temperatures regularly dip below freezing, leading to numerous cold starts—each inflicting disproportionate wear on pistons, rings, and cylinder walls. Studies estimate that 30–40% of total engine wear can occur during cold‐start events.
Humid climates further exacerbate moisture accumulation, where water marries with combustion byproducts to form corrosive acids that attack aluminum components, bearings, and hard‐chrome cylinder liners.
6. Economic Incentives: Rebuild Rather Than Replace
Import duties, shipping, and taxation on new diesel vehicles or engines can exceed 30–40% of an engine’s purchase price.
Consequently, a local rebuild kit—covering pistons, liners, bearings, gaskets, and injector nozzles for roughly $2,000–$5,000—is far more economical than replacing an entire powerplant or vehicle.
This cost differential incentivizes meticulous mid‐life overhauls, often multiple times over an engine’s service life, cumulatively extending mileage into the high six or even seven figures.
Scrap‐Value Dynamics in the U.S.
In North America, a worn heavy‐duty truck engine core may fetch only 10–25 cents per pound at salvage yards, translating to a few hundred dollars.
A factory remanufactured long block can cost $25,000–$35,000, making a rebuild financially unjustifiable once a truck surpasses certain mileage thresholds.
Many owners elect to retire or replace the entire vehicle rather than invest in a high‐hour rebuild.
7. Aftermarket and Parts Ecosystems
Local Fabrication and Adaptation
Across Africa, the aftermarket thrives on local ingenuity:
-
Injector Pump Overhauls: Ultrasonic cleaning and manual recalibration in regional workshops.
-
Custom Gasket and Seal Production: Sheet‐metal shops cut and shape replacements when OEM parts are unavailable.
-
Cylinder Reboring and Liner Services: Found in most district capitals, enabling block reuse indefinitely.
These services are priced for local economies, scheduled flexibly, and executed without waiting for manufacturer approvals.
Proprietary U.S. Assemblies
Modern U.S. diesels use torque‐to‐yield head bolts, integrated cylinder heads with pressed‐in valve seats, sealed electronic modules, and software‐locked injectors. Any attempt at in‐field repair voids warranties and can trigger fault codes that leave a truck in “limp mode.”
Parts availability is limited to dealership networks or franchised remanufacturers, with significant markups and lead times that discourage smaller shops from even attempting repairs.
8. The Role of Fleet Practices
In Africa, a single truck might be owned by a small entrepreneur or cooperative, with profits directly tied to uptime. This fosters a personal stake in preventive maintenance and rapid repairs.
By contrast, larger U.S. fleets may centralize maintenance decisions, strictly follow warranty‐driven service protocols, and retire vehicles on fixed schedules regardless of individual engine condition—sometimes scrapping engines that might still be serviceable under a more flexible maintenance regime.
The remarkable longevity of diesel engines in many African markets compared to the U.S. is not a matter of mystical metallurgy or clandestine factory settings—it is the product of deliberate regulatory choices, local adaptations, and economic incentives that together prioritize mechanical simplicity, proactive maintenance, and rebuild culture over replacement.
-
Regulatory Environment: Minimal aftertreatment permits simple, robust engine designs.
-
Fuel Realities: High‐sulfur, lower‐refinement diesel suits older injection systems.
-
Maintenance Philosophy: Hands‐on, frequent overhauls catch wear before it snowballs.
-
Operating Conditions: Moderate speeds, steady loads, and warm climates reduce stress.
-
Economic Pressures: High replacement costs drive multiple rebuilds; scrap economics favor retiring U.S. engines sooner.
-
Aftermarket Support: Local fabrication and broad parts interchange keep engines running indefinitely.
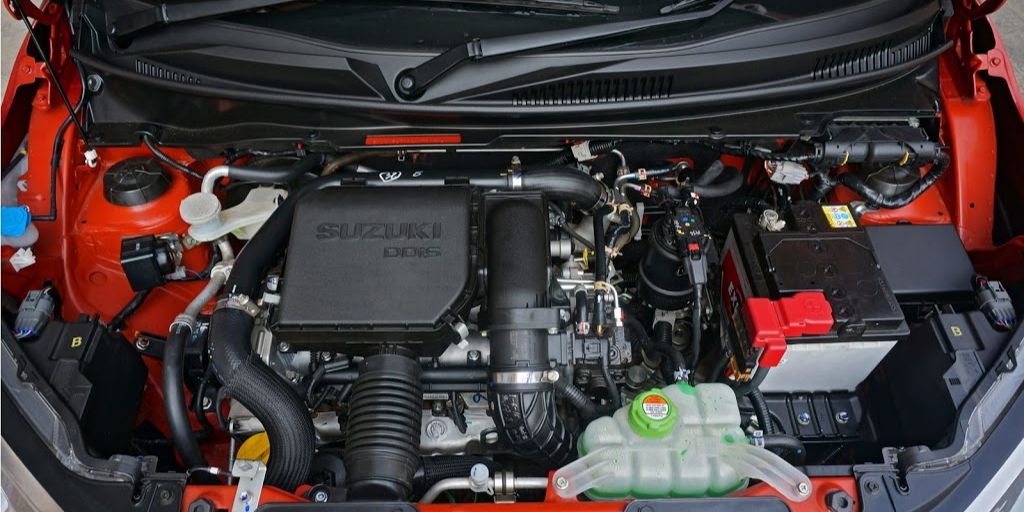
In an era of tightening emissions standards and increasingly sophisticated powertrains, the African diesel paradigm serves as a powerful reminder: sometimes the greatest engine longevity is not found in the most complex technology, but in the simplest, most repairable design—backed by a culture that values maintenance over replacement.
Understanding these dynamics offers valuable lessons for operators, policymakers, and manufacturers alike, challenging assumptions about “modern” versus “traditional” technology and underscoring the vital role of context in engineering resilience.
Whether cruising through the Rift Valley or idling in Lagos traffic, the African diesel’s capacity to eclipse the mileage of its American counterpart speaks to a broader truth: longevity is earned through alignment of design, environment, economics, and human ingenuity—far more than through any single technical specification.
Also Read: 5 Legendary V6 Engines That Refuse To Die and 5 That Self-Destruct