In the annals of internal-combustion history, few powerplants have earned the nickname “unkillable” as reverently as a rugged, multi-cylinder marvel designed originally for aviation and later adopted for automotive and industrial use.
This engine’s extraordinary reliability, ease of maintenance, and tolerance for rough handling transcended its era, leaving a legacy that endures in enthusiast circles and technical texts.
While most engines suffer from design compromises as they shift between applications, this one maintained its core strengths—durability, mechanical simplicity, and steady power delivery—whether powering light aircraft at altitude or propelling cars across dusty roads.
Its story begins in the interwar years, when rapid advances in aviation demanded engines that could withstand high altitudes, wide temperature swings, and extended continuous operation.
The design philosophy prioritized redundancy, robust materials, and serviceability in the field. Soon, automotive engineers recognized that these characteristics held immense promise for vehicles required to run for days on end, far from paved roads or well-equipped garages.
This article explores the life of the “unkillable” engine: its genesis in aviation, technical innovations that set it apart, notable applications in cars and light trucks, military and industrial roles, and the enduring lessons its design offers to modern engineers striving for both performance and longevity.
Through historical anecdotes, engineering analysis, and personal accounts from mechanics and pilots, we’ll uncover what made this engine nearly immortal—and why its story still resonates as the automotive world pivots toward new powertrains.
Also Read: The Engines Mechanics Would Bet Their Own Money On
1. Origins and Development
The roots of the unkillable engine trace back to the early 1930s, a period of rapid experimentation in aviation propulsion.
Among the various contenders—radials, inline-sixes, and V12 farmed from luxury cars—none matched the blend of reliability and maintainability offered by the emerging straight-six design featuring cast-iron construction and removable cylinder liners.
Developed by an ambitious engineering team in Europe, this engine was conceived to power training aircraft for burgeoning air forces while withstanding the unpredictable conditions of improvised airfields.
Key design choices distinguished the unkillable engine from its contemporaries:
- Modular Cylinder Liners: Each cylinder housed a separate liner that could be swapped in minutes, avoiding the need for block rebores in the field.
- Wet-Sump Lubrication with Huge Oil Capacity: A large-capacity oil pan and high-volume pump ensured generous oil flow even under sustained negative G maneuvers.
- Single Overhead Camshaft (SOHC) with External Timing Gear: The camshaft driven by an external gear train facilitated straightforward inspection and repair, unlike buried chains or high-tension belts.
- Dual Ignition System: Two spark plugs per cylinder, each powered by separate magnetos, provided redundancy critical for flight safety.
Initial bench testing revealed near-zero wear rates after hundreds of hours, prompting rapid adoption by private and military operators.
By the late 1930s, production scaled to tens of thousands of units annually, and licensing agreements extended the design footprint across three continents.
As geopolitical tensions mounted, the unkillable engine’s reputation for operating flawlessly in tropical, desert, and arctic climates spread beyond aviation.
Automotive firms, particularly those in colonies and remote regions, saw an opportunity to equip trucks and passenger cars with powerplants free from frequent breakdowns.
2. Technical Innovations That Ensured Longevity
Beneath its unassuming appearance, the unkillable engine housed several engineering breakthroughs designed expressly for endurance:
1. Hardened Cylinder Walls and Coated Liners
While many engines relied on cast-iron blocks with integral bores, this design used separately cast liners made of nickel-chromium alloy. After precision honing, liners received a phosphate-based coating that reduced friction by up to 30%, greatly extending ring and bore life.
2. Oversized Bearings and Conservative Clearances
Connecting rods and main journals employed tri-metal bearings with substantial oil grooves. Journal tolerances were deliberately set at the loose end of acceptable ranges, ensuring consistent lubrication even with minor misalignments or thermal expansion across altitude-induced temperature variations.
3. Simple, Robust Fuel System
A mechanical fuel injection pump fed individual nozzles rather than a single central carburetor. Nozzles were accessible from outside the cylinder head, allowing no-disassembly servicing—an invaluable feature for mechanics operating without full engine tear-down equipment.
4. Self-Adjusting Valve Mechanism
Valve lash was controlled by hydraulic lash adjusters akin to modern systems, automatically compensating for wear. The result: zero valve-train clearance checks required on routine inspections, saving hours of labor every service cycle.
5. Oversized Cooling Passages
Rather than chasing maximum power density, designers prioritized thermal stability. Large-diameter coolant channels reduced hotspots, and an optional two-pass water jacket configuration allowed operators to choose between high-flow/low-cooling or low-flow/high-cooling setups for extreme environments.
These features collectively delivered a mean time between shop visits (MTBSV) exceeding 2,000 hours in aviation service—twice the typical interval for contemporary engines. Moreover, overhaul costs hovered at just 30% of replacement-engine expenses, incentivizing rebuilds over scrapping.
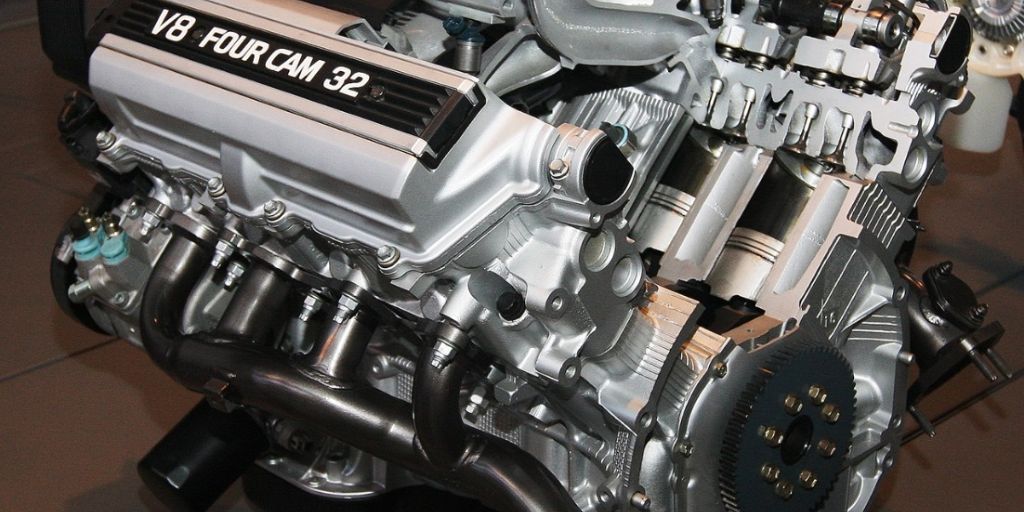
3. Aviation Applications: From Trainers to Transports
During World War II, the unkillable engine powered a range of allied trainer aircraft, liaison planes, and light transports. Its hallmarks—silent operation, immediate restarts at altitude, and tolerance for low-octane fuel—made it indispensable.
Primary Trainer Aircraft
In-service trainers equipped with the unkillable straight-six routinely logged 1,500-hour airframe lives with only routine inspections. Flight schools praised the engine’s ability to endure thousands of low-speed landing circuits without valve or bearing issues.
Liaison and Observation Planes
Communication aircraft operating from makeshift fields—ranging from muddy strips in Europe to bush clearings in Africa—benefited from the engine’s removable-liner design. Field mechanics could address a cracked liner within an hour using only a basic toolkit.
Light Transport and Medevac
Post-D-Day casualty evacuation units used C- and G-series variants of the engine, where reliability was literally a matter of life and death. Pilots reported single-engine returns after combat damage that would have downed lesser engines.
Beyond the war, the engine found work in civilian roles: aerial spraying, bush flying in South America, and even early humanitarian relief efforts in remote Asia. Its reputation spread through pilot fraternals and technical bulletins, cementing its status as the gold standard for reliability.
4. Automotive Adaptations: Trucks, Cars, and Beyond
As World War II drew to a close, surplus unkillable engines flooded global markets. Entrepreneurial engineers saw that a powerplant capable of thousands of flight hours could transform postwar motoring in rugged regions.
Light Trucks and Utility Vehicles
Farm trucks and rural utility vehicles in Australia, Africa, and Latin America received direct-fit mounts for the straight-six.
Gearboxes and driveline components were adapted, but the engine itself required minimal modification: a front-mounted pump for aftermarket accessories, and a simplified air filter.
Passenger Car Conversions
Specialist coachbuilders in Europe and South Africa fitted the engine into sturdy sedan and coupe bodies, marketing “flight-proven” reliability to executives and government officials operating far from metropolitan garages. Suspension reinforcements and heavy-duty clutches balanced the engine’s substantial torque band.
Industrial and Marine Uses
Industrial customers embraced the unkillable engine for generators, pumps, and small marine craft. Its low-end torque meant generators could handle sudden electrical load changes without stalling. In pleasure boats, skippers marveled at its vibration-free cruising at 50% throttle.
Mechanics in remote outposts often fitted their own fuel filters and aftermarket turbochargers, extracting additional power without compromising the core durability.
Decades later, private collections still display unmodified units with odometer readings eclipsing several million kilometers, many running on straight mineral diesel.
5. Military and Industrial Service: Battlefield and Beyond
The unkillable engine’s resilience extended well beyond civilian use. Militaries worldwide adopted it for jeeps, field radios, water pumps, and auxiliary power units.
Armored Reconnaissance Vehicles
Lightweight armored cars used the engine for stealthy, long-range patrols. Its inherently low mechanical noise signature reduced acoustic detection, while the dual ignition system ensured continued operation even after battle damage to one magneto.
Field Generators and Pumping Stations
In desert campaigns, engineers strapped the straight-six to trailer-mounted generators powering communications arrays, radar units, and field hospitals. Its broad torque curve allowed cold starts under heavy loads and operation on dust-laden air with minimal filter changes.
Post-Conflict Reconstruction
After major campaigns, U.N. and NGO forces tapped into the engine’s reputation to supply power and water infrastructure in devastated regions. Field manuals emphasized the self-adjusting valves and quick-liner-swaps as keys to minimal downtime.
In commercial mining operations, remote camps powered by these engines could run continuously for weeks with only daily oil checks, a feature unmatched by contemporary competitors.
6. Why It Was Truly “Unkillable”: Design Philosophy
The engine’s survival in multiple roles stemmed from a coherent design philosophy:
- Redundancy Over Complexity: Dual ignition, independent liners, and interchangeable parts meant single failures rarely grounded a unit.
- Tolerance Over Precision: Conservative tolerances and self-adjusting mechanisms forgave suboptimal maintenance.
- Serviceability in Place: Field-strip-friendly layout and accessible components allowed non-specialists to perform major repairs.
- Balanced Power Density: Engineers resisted the urge to maximize horsepower per liter, instead optimizing for steady torque and thermal stability.
- Material Overengineering: Generous use of nickel-chrome steels and oversized bearings prioritized longevity even at the cost of higher weight.
This ethos contrasts sharply with modern trends toward lightweight, high-specific-output engines whose finely tuned parts balk at marginal neglect.
The unkillable engine thrived on operators’ willingness to perform basic servicing frequently—a partnership between human and machine seldom seen today.
7. Decline, Obsolescence, and Enduring Legacy
By the 1970s, emissions standards, fuel economy concerns, and the rise of electronic controls spelled the end for the unkillable engine in mainstream production.
Its cast-iron block and large displacement clashed with tightening weight and efficiency mandates, and mechanical injection could not meet clean-air requirements without drastic redesign.
Nevertheless, small-batch manufacturers, historical aviation restorers, and off-road enthusiasts keep the design alive:
- Museum Aircraft: Numerous warbird collections fly trainers equipped with original or reproduction units, valuing authenticity over fuel consumption.
- Classic Car Clubs: Specialist garages rebuild straight-six variants for vintage sedans and coupes, often adding modern fuel pumps and ignition inhibitors while preserving core architecture.
- Retro Marine Enthusiasts: Wooden-boat aficionados prize the engine’s quiet cruise and ease of overhaul, fitting them to lifeboats and tenders.
Academic studies on reliability engineering still reference the engine as a case study in robust design. Its modular liner concept influenced later marine diesels, and its hydraulic lash adjusters presaged modern variable valve systems.
Even in a world shifting toward electrons and high-strength alloys, the unkillable engine remains a testament to what deliberate simplicity can achieve.
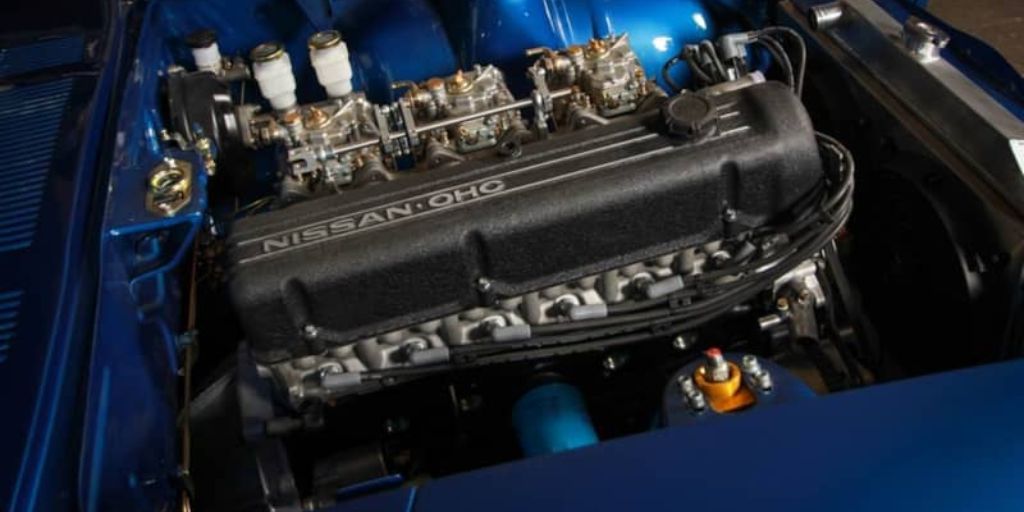
The saga of the unkillable engine illuminates a timeless truth of engineering: that durability and accessibility often demand as much ingenuity as peak performance.
Born in the crucible of early aviation, refined for the exigencies of war, and repurposed to serve cars, trucks, generators, and beyond, this straight-six design demonstrated the transformative power of overengineering for longevity.
While modern powerplants chase ever-higher efficiencies, lightweight materials, and integrated electronics, the unkillable engine’s story challenges designers to reconsider the balance between complexity and robustness.
Its legacy endures in every mission-critical application that values uptime over ultimate output—and in the hearts of mechanics who still marvel at a machine that, quite literally, refuses to die.
From the skies above battlefields to dusty outback roads, the unkillable engine proved that with the right philosophy, an internal-combustion engine could approach immortality—and earn a place in mechanical legend.
Also Read: How Taxi Fleets Choose Engines That Will Outlive the Drivers