In an age when robotic arms choreograph complex dances of precision and computer-driven assembly lines can produce thousands of identical units every day, the notion of building engines by hand can seem almost antiquated.
Yet, in the world’s most prestigious performance houses, racing workshops, and bespoke automotive ateliers, skilled technicians still assemble powerplants by hand. They inspect, fit, and adjust each component with human senses—often signing their name on a plaque once the process is complete.
This enduring practice is not rooted in nostalgia alone but in tangible benefits: uncompromising precision, bespoke customization, personal accountability, and the intangible craftsmanship.
In this article, we’ll explore why, even in 2025, hand-assembled engines remain a vital part of the automotive landscape.
We’ll trace the historical evolution of engine building, delve into the technical and human factors that make manual assembly indispensable for certain applications, examine real-world examples from hypercars to heritage restorations, consider the economic and logistical trade-offs, and look ahead to how this tradition will evolve as the industry accelerates its shift to electrification.
Also Read: 5 Legendary V6 Engines That Refuse To Die and 5 That Self-Destruct
A Historical Perspective: From Forge to Factory
The Birth of Engine Craftsmanship
At the dawn of the automotive era—late nineteenth to early twentieth century—every component of an internal combustion engine was crafted by hand. Blocks were cast and finished with files and scrapers; pistons were hand-fitted; carburetors were tuned by ear.
Engine builders developed an intuitive “feel” for metal, recognizing acceptable clearances and temperature-induced expansion through touch and sound rather than relying on digital measurement. Apprentices learned through close mentorship, absorbing techniques passed down over generations.
The Rise of Mass Production
Henry Ford’s introduction of the moving assembly line in 1913 marked a seismic shift. Engines were redesigned for interchangeability, prioritizing output volume and cost efficiency. Precision jigging, mechanized presses, and eventually computer-controlled machining centers replaced much of the hand-work.
By mid-century, most mainstream manufacturers had fully mechanized—or even automated—engine assembly, leaving artisanship to the fringes of racing and luxury coachbuilding.
The Parallel Track of Performance and Luxury
Even as mass production dominated, elite racing teams and bespoke coachbuilders retained the hand-assembly ethos. In 1950s Formula 1 garages, engines were blueprinted—balanced, measured, and adjusted by hand to extract every ounce of power.
Meanwhile, luxury coachbuilders in Europe hand-fitted overhead camshafts and superchargers for wealthy clientele. Thus, two paradigms emerged: one of industrial efficiency, the other of uncompromising exclusivity.
Today, they coexist, with automation delivering volume cars and artisans delivering the pinnacle of performance and prestige.
Technical Imperatives for Hand Assembly
Ultra-Fine Tolerances and Sensory Feedback
Modern CNC machines routinely hold tolerances within tenths of a millimeter, but high-performance engines often demand single-micron precision. Human assemblers bring irreplaceable sensory input:
-
Touch: Feeling the slight drag as engine bearings approach ideal clearance.
-
Hearing: Distinguishing a crisp “click” as piston rings seat perfectly in the cylinder.
-
Vision: Spotting microscopic tool marks or discoloration that hint at heat stress.
Automated systems excel at uniform repetition but lack the instantaneous judgment to adapt when alloy castings exhibit minute variances in grain structure or when ambient humidity affects material expansion.
Blueprinting and Real-Time Adjustments
Blueprinting transcends following factory specs. It entails:
-
Balancing rotating assemblies: Matching piston-and-rod assemblies to within one gram and polishing crank journals to sub-micron surface finishes.
-
Valve-train optimization: Hand-selecting shims for exact valve lift and ensuring parallel valve faces through meticulous measurement.
-
Compression ratio tweaking: Interchanging head gaskets and piston domes to achieve a precise compression figure suited to fuel quality or altitude.
A robot can torque bolts according to a program, but it cannot decide, mid-assembly, to swap in an alternate shim thickness or to lap valve seats by hand for a perfect seal.
The Benefits of Hand Assembly
Uncompromising Quality Control
Each hand-assembled engine receives continuous human inspection. Technicians log critical measurements—bore diameters, journal clearances, torque values—and re-check fits at every stage. Small deviations are corrected immediately, preventing minor anomalies from compounding into catastrophic failures under extreme loads.
Bespoke Customization
Hand assembly unlocks one-off modifications:
-
Performance mapping: Custom cam profiles and intake port flows tailored to a customer’s track, street, or altitude requirements.
-
Aesthetic enhancements: Anodized hardware, laser-etched valve covers, and personalized builder plaques.
-
Owner documentation: Detailed build journals documenting every torque setting, clearance check, and test-bench result, creating heirloom-quality records.
![The Bugatti W16 Engine for the Bugatti Chiron [1304 × 627] Bugatti W16 engine](https://daxstreet.com/wp-content/uploads/2024/02/The-Bugatti-W16-Engine-for-the-Bugatti-Chiron-1304-×-627.jpg)
Such flexibility is impossible on a production line geared toward maximum throughput and interchangeability.
Emotional and Marketing Value
For supercar buyers, an engine builder’s signature is more than a flourish—it represents a personal guarantee of quality and craftsmanship.
The narrative of “One Man, One Engine” or “Built by Takumi Artisan” adds emotional resonance, reinforcing exclusivity and justifying premium pricing.
It resonates in marketing campaigns, dealership visits, and social-media content, building brand mystique and dealer showroom appeal.
Domains Where Hand Assembly Persists
Supercars and Hypercars
-
Bugatti Chiron W16: Featuring over 3,700 individual parts, each W16 engine is assembled by hand over six days, followed by extensive dyno and leak testing.
-
Koenigsegg Jesko 5.0L V8: Built in Ängelholm, Sweden, by hand-assembled sub-teams focusing on lightweight components and record-setting durability.
Performance Sub-Brands of Mass-Market OEMs
-
Mercedes-AMG: The “One Man, One Engine” philosophy ensures each AMG powerplant is assembled start-to-finish by a single technician, who affixes a plaque bearing their signature.
-
BMW M Division: High-revving M engines receive hand-finished moving parts and final assembly by M Craft specialists.
Motorsport and Racing
-
Formula 1: Engines are hand-assembled in limited batches, with full rebuilds between races. Each unit is disassembled, inspected, and reassembled by a small team of specialists to maintain peak performance.
-
Endurance Racing (e.g., Le Mans prototypes): Hybrid powertrains combine hand-built ICE components with electric motor modules, requiring manual integration to meet reliability under 24-hour race demands.
Heritage and Continuation Programs
-
Jaguar Lightweight E-Type Continuations: Recreated in Browns Lane, UK, these models use original 1963 blueprints and hand-assembled straight-six engines to preserve period-correct construction.
-
Ferrari 250 GTO Continuations: Limited-run replicas built on original tooling, with hand-assembly techniques ensuring authenticity and collector appeal.
Deep Dive: Extended Case Studies
Rolls-Royce Phantom Twin-Turbo V12
While Phantom engine blocks and heads are CNC-machined, final assembly remains largely manual:
-
Hand-lapping valve seats to achieve ultra-tight seals.
-
Manual cam alignment using feeler gauges to precise lash specifications.
-
Bolt preload verification via ultrasonic stretch testing.
-
Acoustic calibration to deliver the Phantom’s signature whisper-quiet NVH characteristics.
This labor-intensive process is critical to delivering the “magic carpet” ride and silence Phantom owners expect.
Lexus LFA’s 4.8L Naturally Aspirated V10
Motomachi, Japan, hosts the limited-run LFA production line. Each V10 is hand-assembled in small batches, featuring:
-
Hand-finished intake trumpets tuned for optimal airflow.
-
Precision throttle linkage calibration for immediate response.
-
Dedicated dyno break-in cycle monitored by technicians to ensure consistent power output and reliability.
Yamaha’s musical instrument division even contributed to the LFA’s unique intake sound, further emphasizing the artisanal nature of the build.
Pagani Huayra Tricolore’s AMG-Derived V12
With fewer than ten units built, the Huayra Tricolore’s 6.0L V12 receives:
-
Master-technician assembly under engineers’ supervision.
-
Acoustic profiling in anechoic chambers.
-
Custom dyno mapping to match individual exhaust configurations and deliver a bespoke driving experience.
Training the Modern Engine Artisan
Becoming a certified engine builder—whether a “Takumi” at Nissan or an AMG technician—demands years of rigorous training:
-
Metrology and Blueprint Reading: Mastering micrometers, dial indicators, profilometers, and interpreting engineering drawings down to surface-finish symbols.
-
Material Science Seminars: Understanding how temperature, humidity, and alloy composition affect clearances and fatigue life.
-
Hands-On Clinics: Live builds under mentor supervision, with detailed audits at each stage—crank assembly, piston ring seating, head torquing, and more.
-
Quality Assurance Audits: Periodic re-qualification ensures builders remain proficient with evolving materials and processes.
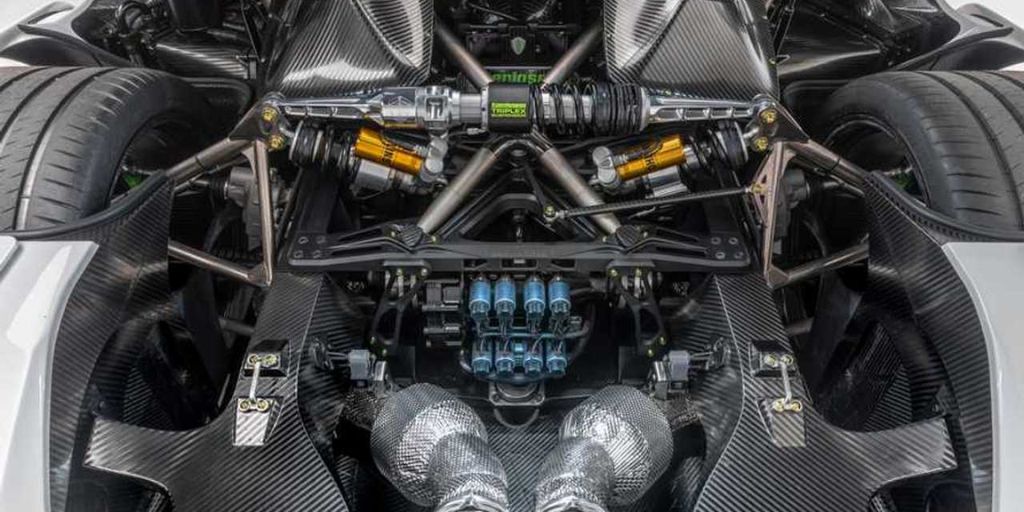
These programs often span three to five years, culminating in a certification that allows the technician to sign their work. Even after certification, continual assessments and refresher courses maintain standards across evolving technologies.
Economic and Logistical Trade-Offs
While hand assembly offers unparalleled quality and exclusivity, it carries significant costs and constraints:
Labor and Time
-
Hourly rates: Highly skilled technicians command wages 3–5× higher than general assembly workers.
-
Cycle time: Automated lines can complete an engine in 30–45 minutes; a hand-assembled V8 or V12 may require 6–12 hours of labor.
Skill Bottlenecks
Training master builders takes years, limiting rapid scale-up. A plant with ten certified technicians cannot instantly boost output without diluting expertise.
Inventory Management
Parts awaiting hand-fitment tie up capital in inventory. Manufacturers must balance just-in-time delivery for sub-assemblies with enough lead time to accommodate manual processes.
Consistency
Even among expert builders, slight variances in technique can introduce microscopic differences. Rigorous multi-stage quality checks—often combining machine inspections with final human sign-off—are essential to ensuring uniform performance across all units.
For these reasons, hand assembly is reserved for low-volume, high-value applications where the premium price paid by customers more than offsets these additional costs.
The Future of Hand Assembly in an Electrified World
As the automotive industry pivots toward electrification, the internal combustion engine’s role will diminish—but the principles of hand assembly will endure and migrate to new domains:
Artisan Electric Motor Builds
-
Custom stator windings and rotor laminations balanced to sub-gram precision for hyper-focused track EVs.
-
Manual bearing preload setups to eliminate unwanted vibration and noise in performance electric drivetrains.
Battery Pack Craftsmanship
In limited-run flagship EVs, technicians may:
-
Hand-select cells for capacity and internal resistance matching.
-
Apply thermal interface materials manually for optimized heat transfer and safety.
-
Perform bespoke welding of busbars and tabs under strict quality oversight.
Hybrid Powertrain Integration
Combining ICE units with electric motors demands:
-
Manual integration of control electronics and cooling systems.
-
Hand-tuned software maps to ensure seamless torque blending and regenerative braking characteristics.
Restomod and Continuation Builds
Classic car restorations and continuation series will continue to drive demand for engine artisans:
-
Vintage engine rebuilds requiring knowledge of period-correct processes and materials.
-
Custom powertrain swaps blending modern ICE or electric units into classic chassis, demanding hand-assembled adaptor plates, mounts, and harnesses.
Cultural and Psychological Drivers
Hand-assembly resonates with broader trends favoring artisanal, human-made products:
-
The maker movement: from bespoke furniture to craft spirits, consumers increasingly value tangible proof of human skill.
-
Heritage and authenticity: in a world of algorithmic optimization, a human-built engine provides a visceral connection to automotive history.
-
Storytelling and identity: a signed engine plate tells a story—one that evokes exclusivity, passion, and the pursuit of perfection.
These psychological factors amplify the appeal of hand-built engines, driving collector demand and fostering brand loyalty.
Hand-assembled engines are far more than a quaint throwback—they stand at the intersection of engineering excellence, human craftsmanship, and brand heritage.
From the thunderous W16 of a Bugatti Chiron to the whisper-smooth V12 of a Rolls-Royce Phantom, and into the burgeoning realm of hand-tuned electric motors and battery packs, the artisan’s touch remains irreplaceable where performance, exclusivity, and emotional resonance matter most.
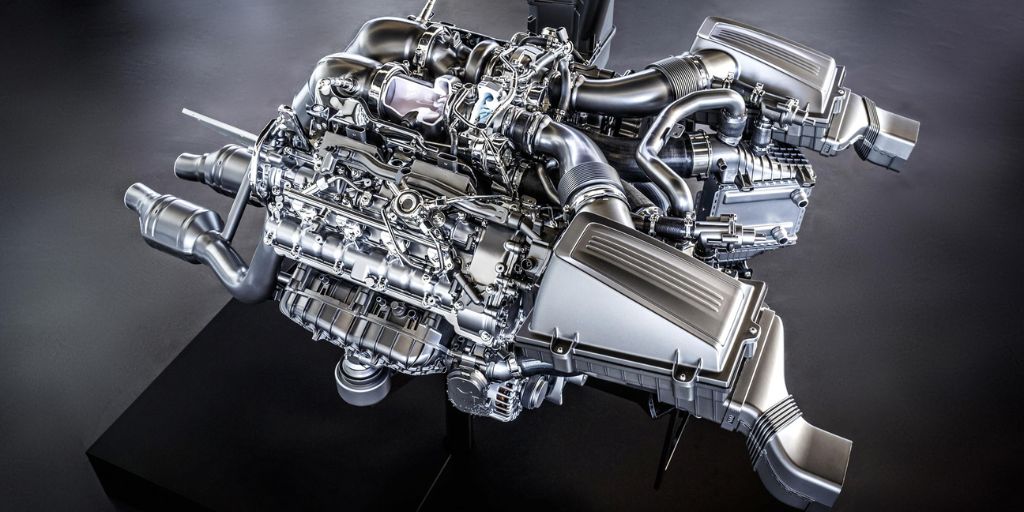
As the automotive world continues its electrification journey, the spirit of hand assembly will persist—evolving to new powertrain technologies and ensuring that the legacy of human mastery endures.
For enthusiasts, collectors, and drivers seeking the extraordinary, the hand-built engine—or its electric equivalent—will remain a powerful symbol of what human hands, guided by experience, passion, and precision, can achieve.
Also Read: You Can Still Buy This 1980s Engine Brand New From the Factory