In the harshest environments on Earth from Arctic oil fields to remote mining operations in scorching deserts, equipment reliability isn’t just about convenience; it’s about survival and operational viability.
Field-serviceability, once a cornerstone of mechanical design philosophy, has seen renewed interest as industries push into increasingly remote and hostile environments. This resurgence represents a fascinating countertrend to the sealed, modular designs that dominated recent decades.
Field-serviceable engines are specifically designed to be maintained, repaired, and even rebuilt with minimal specialized tools and facilities.
Their architecture prioritizes accessibility, component standardization, and repair-focused design characteristics that prove invaluable when the nearest service center might be hundreds or thousands of miles away.
In extreme conditions, where equipment failure can mean not just lost productivity but genuine danger to personnel, the ability to perform meaningful repairs on-site becomes a critical capability.
This examination explores what defines true field-serviceability in modern engines, the contexts where this attribute proves most valuable, the engineering principles that enable it, and why, after years of manufacturers moving toward sealed systems we’re witnessing a notable return to designs that prioritize in-field maintenance and repair.
The Core Elements of Field-Serviceability
True field-serviceability in an engine goes far beyond mere accessibility. It represents a comprehensive engineering philosophy that permeates every aspect of design.
At its foundation are several key principles that differentiate genuinely field-serviceable engines from those merely marketed as “maintainable.” First is the concept of strategic component placement.
Critical wear items and common failure points must be positioned where they can be accessed without extensive disassembly. This means thoughtful arrangement of components based not just on functional efficiency but on maintenance logistics.
Simple examples include placing oil filters, fuel pumps, and belt systems where they can be serviced without removing other components.
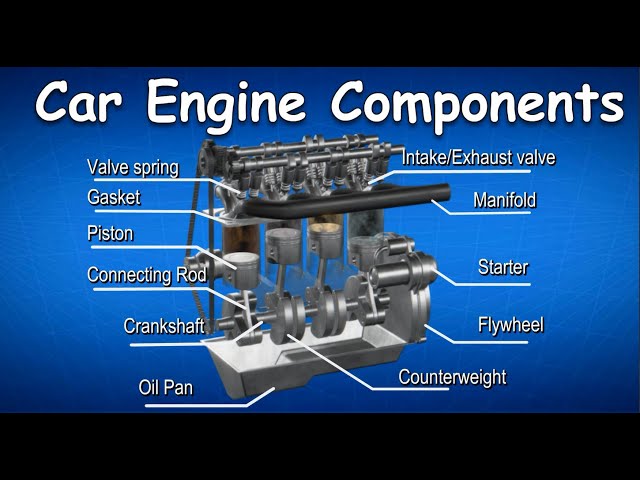
Second is the standardization of fasteners and connection points. Field-serviceable engines minimize the variety of specialized tools required, often designing components to be removable with basic tool sets that can reasonably be carried into remote locations.
This standardization extends to connection types using common bolt patterns and standardized fittings wherever possible. Third is modularity with purpose.
Unlike sealed-unit modularity that simply replaces entire assemblies, field-serviceable modularity means creating logical subsystems that can be individually repaired.
A properly designed cooling system, for instance, allows replacement of a water pump or thermostat without disturbing the entire cooling circuit.
Environmental Challenges That Demand Field-Serviceability
Field-serviceability becomes particularly valuable in environments where extreme conditions create both increased equipment stress and significant barriers to conventional service options.
In Arctic operations, where temperatures can plunge below -40°F, the combination of thermal stress on materials and the impossibility of transporting large equipment during winter months makes on-site repair capability essential.
Similarly, in desert environments, heat and abrasive dust accelerate component wear while remote locations may be hundreds of miles from the nearest service facility.
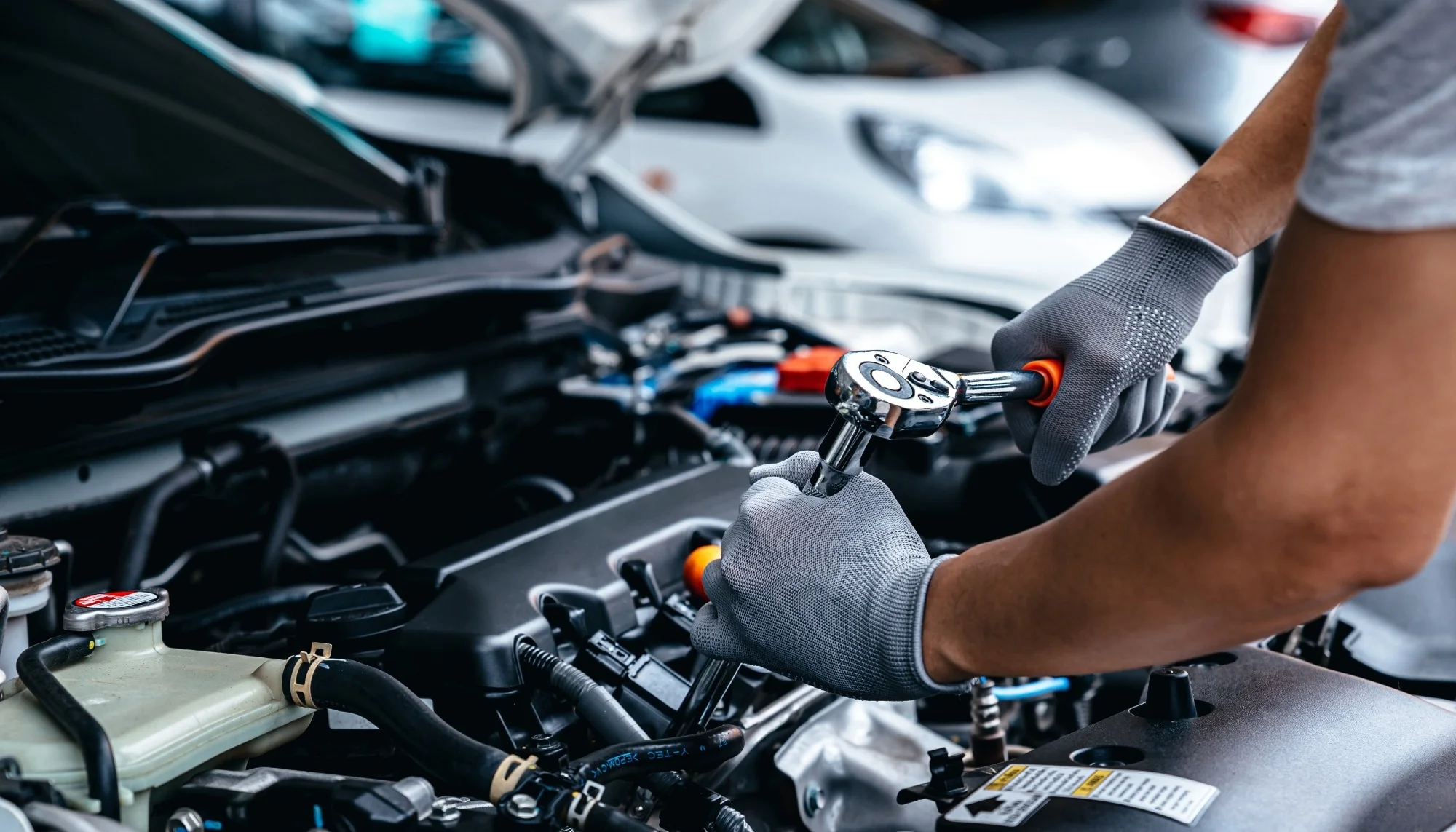
Maritime applications represent another critical context. Vessels operating in international waters cannot simply call for a service truck, and even minor engine issues can become catastrophic if they cannot be addressed while underway.
Mining operations in developing regions face similar challenges, where local infrastructure may be insufficient to support complex maintenance operations, and transportation of heavy equipment becomes logistically problematic and prohibitively expensive.
In military and disaster response applications, field-serviceability isn’t just about convenience or cost it directly impacts mission success and sometimes survival
Equipment that requires minimal specialized support infrastructure provides tactical advantages in rapidly changing situations where supply chains may be compromised.
Engineering Principles That Enable Field Maintenance
Creating truly field-serviceable engines requires adherence to specific engineering principles throughout the design process. Perhaps most fundamental is the concept of “designed disassembly paths,” ensuring that components can be removed in a logical sequence without requiring specialized extraction tools or complex procedures.
This means careful consideration of how components fit together and the clearances necessary for tool access. Material selection plays a crucial role as well.
Field-serviceable engines often employ more robust materials at key wear points, accepting minor weight penalties in exchange for extended service life and repairability.
This might include thicker cylinder walls that can be rebored in the field, or replaceable wear surfaces on components that would otherwise require complete replacement.
Diagnostic accessibility represents another critical factor. Field-serviceable engines typically incorporate easily accessible test points for measuring pressures, temperatures, and electrical values without extensive disassembly.
This allows troubleshooting to be performed efficiently with portable diagnostic equipment, avoiding the “guess and replace” approach that wastes both time and components.
Finally, effective field-serviceability requires comprehensive documentation, not just service manuals, but detailed troubleshooting guides, parts diagrams, and repair procedures specifically written for field conditions. This documentation becomes part of the engine’s design, not an afterthought.
Also Read: Top Engines That Can Survive Without a Working Cooling Fan
The Historical Evolution of Serviceability
The concept of field-serviceability has undergone fascinating evolution throughout mechanical history. Early industrial engines were inherently field-serviceable out of necessity, specialized service facilities simply didn’t exist in many areas.
These engines featured generous clearances, accessible components, and relatively simple systems that could be maintained with basic tools and mechanical knowledge.
As transportation networks improved and manufacturing became more sophisticated, a gradual shift occurred toward factory service models. Engines became more complex, tolerances tightened, and the specialized knowledge required for service increased.
By the late 20th century, many manufacturers had embraced “sealed unit” design philosophies, where entire components or subsystems were replaced rather than repaired, a model that presumed ready access to replacement parts and service facilities.
This trend reached its apex with computerized engine management systems and increasingly integrated designs that prioritized initial cost reduction and manufacturing efficiency over repairability.
Components that previously might have been straightforward to rebuild, such as alternators or water pumps, became sealed units with limited or no serviceability.
The Contemporary Revival of Field-Serviceability
Several converging factors have driven the recent revival of interest in field-serviceable engine designs. Economic considerations play a significant role, particularly in industries operating in remote locations where equipment downtime costs can exceed tens of thousands of dollars per hour.
In these contexts, the ability to perform effective repairs on-site dramatically reduces both downtime duration and the logistical costs associated with component shipping or equipment transportation.
Sustainability concerns have also influenced this trend. Field-serviceable designs typically support longer equipment lifespans through ongoing maintenance and component rebuilding, rather than the wholesale replacement of sealed units.
This aligns with growing corporate sustainability initiatives and regulatory pressures to reduce resource consumption.
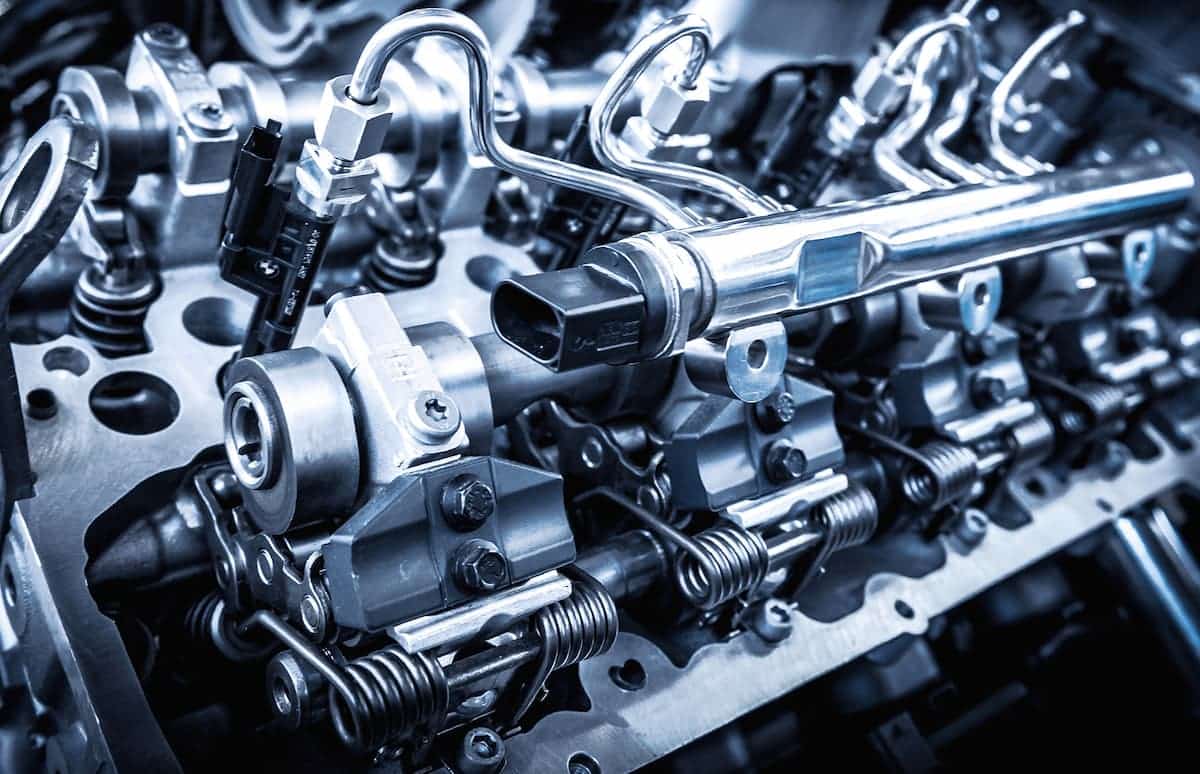
Technological advances have made field-serviceability more achievable even in sophisticated modern engines. Improved sealing technologies allow for easier repeated disassembly, while modular electronic systems can incorporate diagnostics that pinpoint specific failed components rather than requiring replacement of entire systems.
Perhaps most interestingly, customer demand has driven manufacturers to reconsider serviceability. Equipment operators in remote regions have increasingly selected machines specifically based on their maintainability characteristics, creating market pressure that has influenced design priorities.
Case Studies in Extreme Field-Serviceability
Several manufacturers have embraced field-serviceability as a key differentiator in their engine designs. Cummins’ QSK series engines, widely used in mining applications, feature individually replaceable cylinder heads, accessible fuel system components, and modular subsystems specifically designed for field maintenance with minimal specialized tools.
These engines include design features like replaceable cylinder liners and articulated pistons with replaceable skirts that can be serviced without removing the entire engine.
In Arctic applications, Caterpillar’s C18 industrial engines have been successfully field-serviced at temperatures approaching -40°F through design features including accessible heating elements, simplified winterization components, and cold-weather specific repair procedures.
Their block design allows critical repairs like connecting rod replacement to be performed without removing the engine from its installation. Marine diesel manufacturer Wärtsilä has pioneered modular engine designs that allow major components to be replaced at sea, even on vessels with limited workspace.
Their approach includes features like segmented engine frames that can be disassembled within the confined spaces of an engine room and cylinder units that can be individually accessed for service.
Best Practices in Modern Field-Serviceable Design
Leading manufacturers have established several key best practices for contemporary field-serviceable designs. Prioritizing the accessibility of critical wear components without requiring major disassembly represents a fundamental principle.
This might include positioning fuel filters, oil filters, and belt systems where they can be reached without removing other components. Standardization of fasteners and connection points simplifies the tool requirements for field service.
Using common bolt patterns and limiting the variety of specialized tools required enables effective field repairs with portable tool kits.
Similarly, employing robust, reusable sealing systems rather than single-use gaskets or adhesives supports field maintenance without requiring extensive parts inventories.
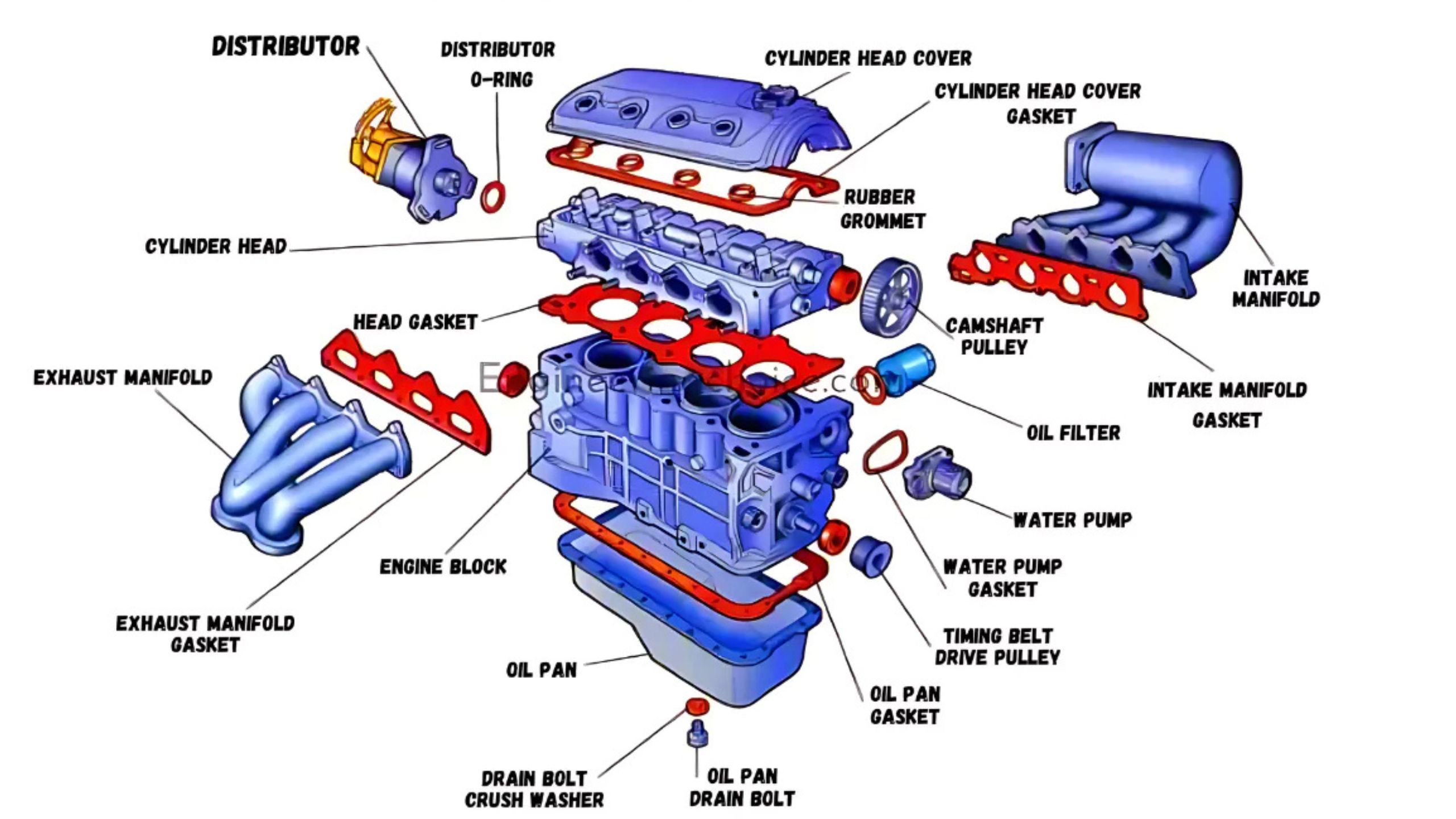
Progressive manufacturers also design with diagnostic access in mind, incorporating test points that allow pressure, temperature, and electrical measurements without extensive disassembly.
This enables accurate troubleshooting under field conditions and avoids unnecessary component replacement. Perhaps most importantly, comprehensive documentation specifically written for field conditions proves essential.
This includes not just traditional service information but detailed troubleshooting guides, parts diagrams with disassembly sequences, and repair procedures specifically written for field conditions.
Balancing Modern Performance with Serviceability
One of the most significant challenges in contemporary engine design is balancing the demands of modern performance standards with field-serviceability.
Emissions regulations, fuel efficiency requirements, and power density expectations have driven manufacturers toward increasingly sophisticated systems that can conflict with straightforward serviceability.
Successful designs manage this balance through careful system architecture that isolates complexity rather than distributing it throughout the engine.
For example, keeping sophisticated emissions components in distinct subsystems that can be bypassed temporarily during emergency field repairs, rather than integrating them throughout the engine’s core systems.
Material technology plays a crucial role in this balance as well. Advanced materials that maintain performance while requiring less precise tolerances can support field repairability.
Similarly, employing selective use of robust materials at key wear points, even at minor weight penalties, can dramatically improve service life and field repairability.
The Future of Field-Serviceability
The future of field-serviceable engine design points toward fascinating developments that merge traditional mechanical repairability with advanced technological support.
Augmented reality systems are already being deployed that overlay repair instructions and component identification directly onto the technician’s field of view, dramatically improving the effectiveness of field repairs even by less experienced personnel.
Improved diagnostic systems using machine learning can identify developing issues before catastrophic failure, allowing planned field service rather than emergency repairs. These predictive systems can dramatically improve the success rate of field repairs by identifying specific components requiring attention.
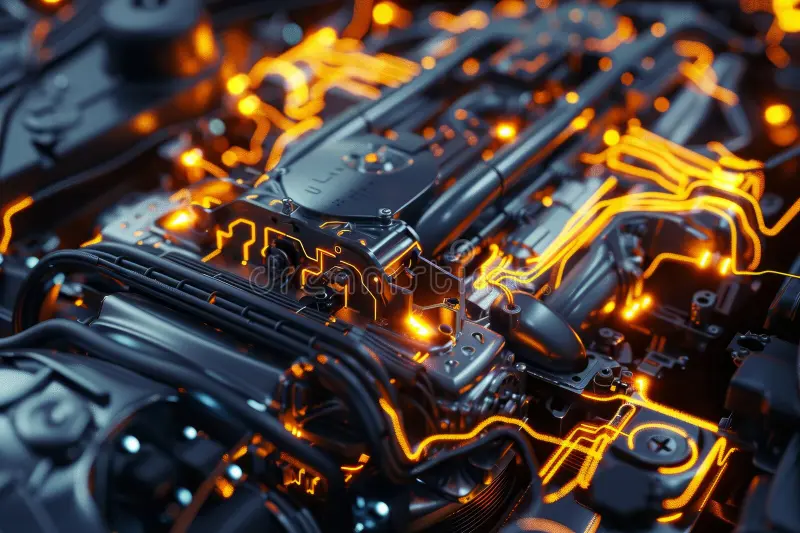
Material science advances are creating components with longer service life under extreme conditions, reducing the frequency of required field maintenance. Ceramic coatings, advanced alloys, and composite materials are extending component lifespans even in the harshest environments.
Perhaps most intriguing is the development of modularity concepts that maintain field-serviceability while addressing the complexity of modern engine systems.
These designs isolate sophisticated control and emissions systems in ways that allow them to be bypassed temporarily during emergency field repairs, then restored to full functionality once comprehensive service is available.
The Enduring Value of Field-Serviceability
The revival of interest in field-serviceable engine design represents more than just a nostalgic return to earlier mechanical philosophies it reflects a pragmatic recognition that as operations expand into increasingly remote and challenging environments, the ability to perform meaningful maintenance and repairs on-site becomes a critical operational capability.
This renewed focus on serviceability doesn’t reject modern advances in performance, efficiency, or emissions control. Rather, it represents a sophisticated integration of these requirements with practical maintainability considerations.
The most successful contemporary designs maintain compliance with stringent regulatory requirements while still enabling effective field service under extreme conditions.
As industries continue to expand operations into more remote and challenging environments, from Arctic exploration to deep desert mining, the value of genuine field-serviceability will likely continue to grow.
Manufacturers who successfully balance modern performance requirements with thoughtful serviceability design will find themselves with significant competitive advantages in these demanding markets.
Also Read: 5 Engines That Perform Better After 200,000 Miles Than Brand New