In the far-flung corners of the world, where paved roads give way to rugged paths and power grids remain distant dreams, the humble engine becomes more than just machinery; it becomes a lifeline.
Remote village mechanics face unique challenges that their urban counterparts rarely encounter: limited access to spare parts, inconsistent fuel quality, extreme climate conditions, and a critical need for reliability that can’t be compromised.
These circumstances have created a fascinating phenomenon, the emergence of specific engine types that have become legendary in remote communities for their dependability and serviceability.
These are not necessarily the newest or most technologically advanced power plants, but rather designs that have proven themselves through decades of practical application in challenging environments.
Through necessity and experience, village mechanics have developed deep relationships with certain engines that perfectly balance simplicity, durability, and repairability.
This exploration reveals which engines have earned the trust of these skilled practitioners and why these particular power sources continue to thrive in environments where mechanical failure is not just an inconvenience but can represent a genuine threat to livelihood and sometimes even survival.
The Single-Cylinder Diesel Workhorse
The single-cylinder diesel engine stands as perhaps the most revered power plant among mechanics in remote villages worldwide. These robust engines typified by models like the Lister-Petter, Yanmar YDG, and Lombardini have achieved near-mythical status in isolated communities from the Himalayan foothills to Amazonian settlements.
Their dominance in these environments stems from an unparalleled combination of mechanical virtues perfectly suited to regions where infrastructure is minimal and resources scarce.
At the core of their appeal is an almost architectural simplicity. With fewer moving parts than multi-cylinder alternatives, these engines present a mechanical transparency that enables even modestly trained technicians to understand their complete operation.
The single-cylinder design eliminates complex timing systems between multiple pistons, reducing potential failure points dramatically. This simplicity translates directly into repairability a critical factor when the nearest parts supplier might be hundreds of miles away.
The robust construction of these engines further cements their status. Most feature thick cast iron blocks and overbuilt components designed with considerable safety margins.
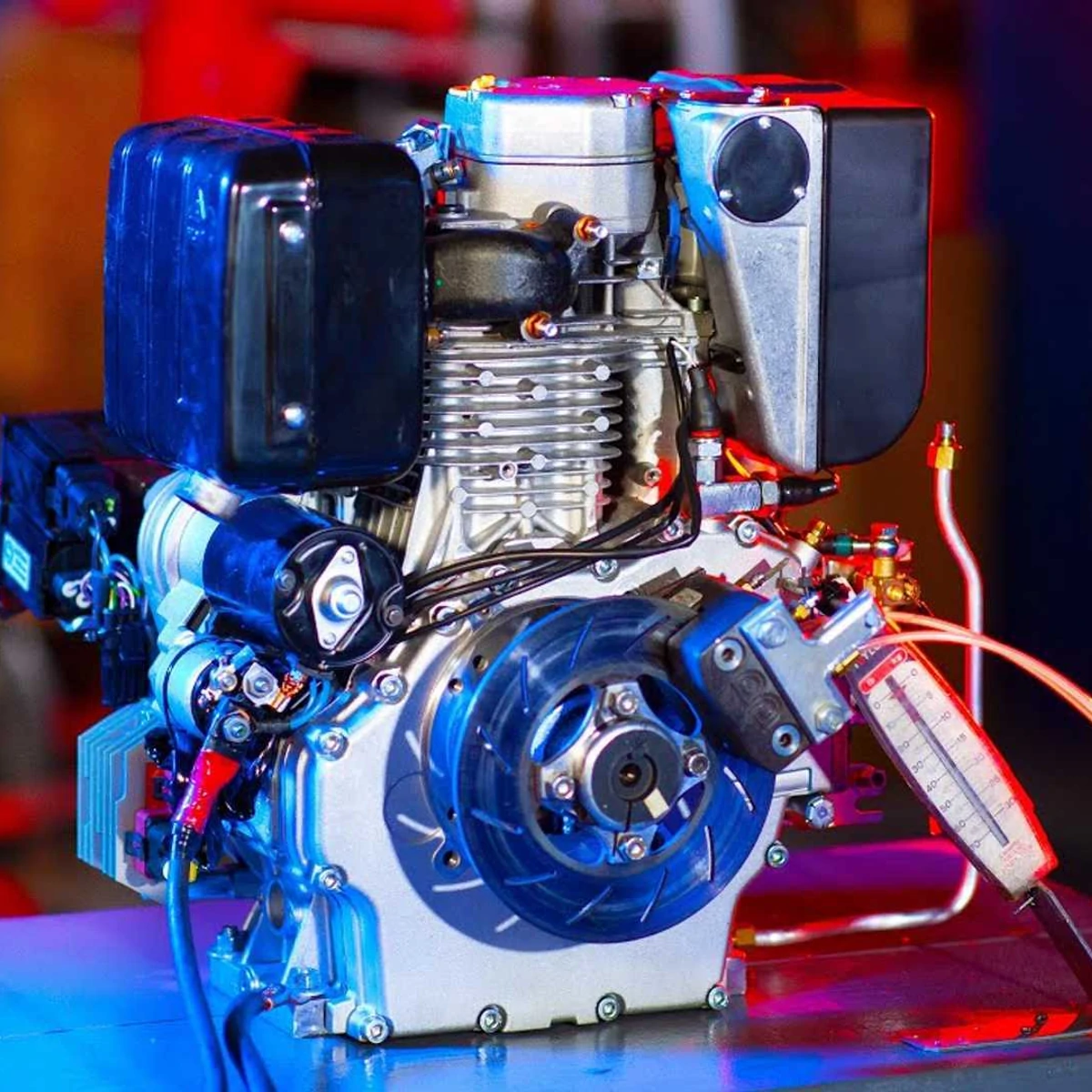
This inherent durability means they can withstand punishment that would destroy more refined engines including contaminated fuels, infrequent maintenance, and operation in extreme temperature conditions.
Many units continue functioning reliably after decades of service, with some villages treasuring engines that have powered communities for over half a century.
Fuel flexibility represents another crucial advantage. While designed primarily for diesel operation, many of these engines can be adapted to run on locally available alternatives including vegetable oils, kerosene blends, and even some biofuels with minimal modification.
This adaptability provides energy security in regions where conventional fuel supplies may be irregular or prohibitively expensive. Perhaps most significantly, these engines require minimal specialized tools for maintenance and repair. A basic set of wrenches, screwdrivers, and perhaps a hammer are often sufficient for most interventions.
When parts do fail, local fabrication becomes possible village blacksmiths and metalworkers can often manufacture replacement components from available materials, a virtually impossible feat with sophisticated modern engines dependent on precision-engineered parts and electronic systems.
The low rotational speed of these engines typically 650-1800 RPM contributes to their longevity and reduced wear. While this sacrifices power density compared to high-revving alternatives, it results in engines that can run continuously for years with only basic maintenance, making them ideal for consistent electricity generation or water pumping applications where reliability trumps efficiency or power-to-weight ratios.
The Toyota 22R Series: An Automotive Legend
In remote villages across developing nations where vehicles serve as critical infrastructure, one engine has achieved legendary status among local mechanics the Toyota 22R series.
First introduced in 1981 and produced with minimal changes until 1995, this 2.4-liter inline-four gasoline engine has become the preferred power plant in challenging environments from the dust-swept roads of sub-Saharan Africa to the mountain passes of Central Asia, earning a reputation that borders on reverence among village mechanics.
The 22R’s dominance in these settings begins with its fundamental design philosophy a deliberate emphasis on reliability over performance. Its relatively low compression ratio (around 9:1) reduces internal stresses, while its chain-driven overhead camshaft design eliminated the frequent maintenance requirements of belt-driven systems.
The engine’s mechanical fuel injection system on early models, or simple carburetors on others, avoided the complexity and diagnostic challenges of electronic fuel injection systems that require specialized equipment to troubleshoot equipment rarely available in remote settings.
Village mechanics particularly value the 22R’s exceptional tolerance for substandard fuel quality. In regions where gasoline may contain contaminants or varying octane ratings, the engine’s conservative timing and robust bottom end prevent the catastrophic failures that plague more highly-tuned engines.
The thick-walled cast iron block provides remarkable structural integrity, while the engine’s relatively large cooling passages help prevent overheating in tropical climates where cooling system maintenance might be irregular.
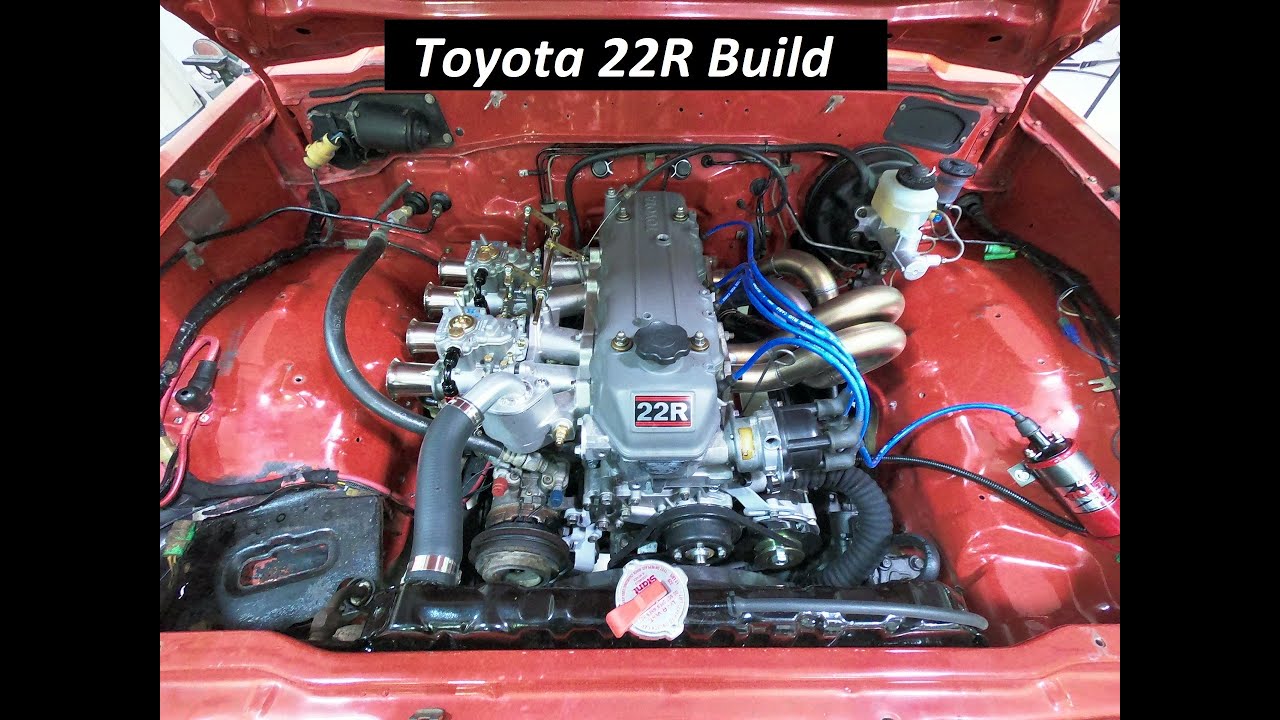
Perhaps most critically, the 22R established itself through an unparalleled parts ecosystem. The engine’s widespread global deployment in Toyota’s popular pickup trucks and 4×4 vehicles ensured that components spread throughout even the most remote regions.
Local mechanics developed deep familiarity with its architecture, passing knowledge through apprenticeship networks and developing innovative repair techniques using locally available materials.
Many village workshops maintain collections of salvaged 22R components, creating informal parts libraries that can keep these engines running indefinitely through component exchange and creative reuse.
The 22R also benefits from an extraordinary tolerance for improvised repairs. Its relatively generous clearances and robust design allow it to continue functioning even after repairs that might be considered substandard in more developed regions.
Village mechanics regularly perform remarkable feats of ingenuity with these engines from manufacturing replacement gaskets from local materials to adapting alternative parts when originals are unavailable.
There are documented cases of 22R engines continuing to run despite cracked cylinder heads (sealed with epoxy compounds), improvised bearing materials, and hand-fabricated valve components.
This engine’s consistent design over its production lifespan meant that techniques learned on early models remained relevant for later versions, allowing mechanical knowledge to accumulate within communities rather than requiring constant retraining.
For remote villages where a functioning vehicle can mean access to markets, medical care, and economic opportunity, the 22R’s combination of repairability, durability, and familiarity has made it an irreplaceable resource whose value extends far beyond mere transportation.
The Briggs & Stratton Small Engine: Ubiquitous Utility
Throughout remote villages spanning six continents, the distinctive sound of Briggs & Stratton small engines has become as familiar as the rooster’s crow at dawn.
These compact single-cylinder engines typically ranging from 3 to 25 horsepower have penetrated the most isolated communities on earth, powering everything from water pumps and grain mills to generators and agricultural equipment.
Their ubiquity in these settings is no accident but rather the result of specific design characteristics that make them uniquely suited to environments where technical support is limited and operational continuity is essential.
The fundamental appeal of Briggs & Stratton engines to village mechanics lies in their exceptional standardization and modular design. Unlike many competitors who constantly revise their engines, Briggs maintained remarkable consistency across decades of production.
This standardization means that knowledge acquired servicing one engine translates directly to others, allowing mechanics to develop deep expertise applicable across multiple equipment types.
The engines’ logical layout, with clearly defined subsystems (carburetion, ignition, valve train, etc.), creates natural troubleshooting pathways that don’t require sophisticated diagnostic equipment.
These engines achieve remarkable durability through intentionally conservative engineering. Rather than pushing metallurgical limits for maximum power, Briggs designs typically operate well below their theoretical stress thresholds, creating substantial safety margins that accommodate variable maintenance regimens.
The cast iron cylinder sleeves in many models prevent the rapid wear that all-aluminum designs might suffer when operating in dusty environments or with moderately contaminated fuels.
This robustness translates directly into forgiveness an essential quality in settings where preventive maintenance might be delayed by necessity.
Perhaps most crucially for remote applications, Briggs engines feature remarkable part interchangeability across generations and models. This compatibility creates a “mix-and-match” repair ecosystem where components from damaged engines can be harvested to keep others running indefinitely.
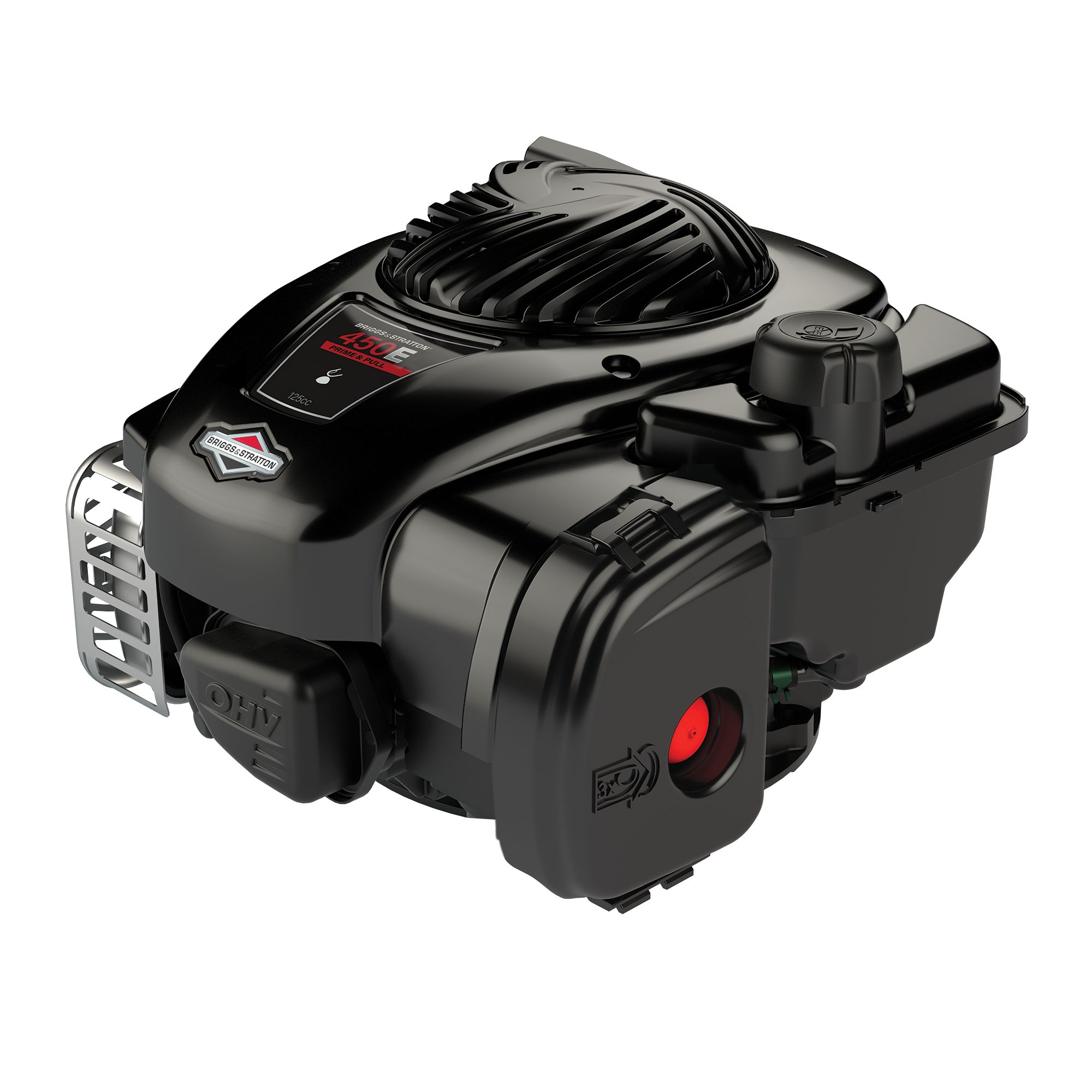
Village mechanics often maintain collections of salvaged Briggs parts accumulated over decades, creating resilience against supply chain disruptions.
When new components are required, their standardized design and widespread distribution mean that even in relatively isolated markets, basic parts like spark plugs, carburetors, and ignition coils can often be sourced locally.
The air-cooled design of most Briggs engines eliminates the complexity and failure points associated with water cooling systems—no radiators to leak, no water pumps to fail, no coolant to maintain.
This simplicity is particularly valuable in regions with limited access to specialized coolants or where freezing temperatures might damage water-cooled systems. The engines’ gravity-fed carburetion systems similarly avoid the complexity of fuel pumps while providing adequate fuel delivery for most applications.
Briggs engines also demonstrate remarkable adaptability to local conditions. Village mechanics have developed techniques to modify these engines for alternative fuels including natural gas, propane, and even biogas when gasoline is unavailable or prohibitively expensive.
Their relatively large combustion chambers and modest compression ratios tolerate fuel variations that would cause performance issues or damage in more highly-stressed engine designs.
The company’s century-long production history has created an unintended advantage: the emergence of community knowledge repositories where repair techniques are preserved and transmitted through generations.
In many villages, working on Briggs engines forms part of informal mechanical apprenticeships, creating continuity of expertise that helps maintain these power plants decades after their initial deployment.
This established knowledge base represents an invaluable resource that no newer engine design, regardless of its technical merits, can readily replace.
The Perkins 4.236: Commercial Diesel Excellence
In the challenging environments of remote villages where heavy equipment and larger power generation needs must be met, the Perkins 4.236 diesel engine has achieved a status approaching mechanical sainthood among local mechanics.
This 3.9-liter four-cylinder workhorse, first introduced in 1964 and produced with only incremental changes until 1996, represents the ideal intersection of industrial capacity and maintainability for regions where technical support infrastructure is limited but power demands exceed what smaller engines can provide.
The fundamental characteristic that establishes the Perkins 4.236 as indispensable in remote settings is its architectural simplicity relative to its power output.
Producing approximately 65 horsepower and 128 lb-ft of torque in its standard configuration, it delivers substantial capability through straightforward mechanical systems.
Unlike modern diesel engines encumbered with complex emissions equipment and electronic controls, the 4.236 relies entirely on mechanical fuel delivery via its reliable direct injection system, eliminating the diagnostic challenges posed by electronic control units and sensors that can be impossible to service in isolated locations.
Village mechanics particularly value the 4.236’s exceptional tolerance for fuel variability a critical attribute in regions where diesel quality can be inconsistent or contaminated.
The engine’s robust injection pump design and relatively modest pressure requirements allow it to function with fuels that would rapidly damage more sophisticated common-rail injection systems.
Many mechanics in developing nations have developed filtration techniques and fuel pre-treatment methods specifically calibrated to the Perkins’ requirements, enabling these engines to operate reliably even when supplied with problematic local fuels.
The engine’s remarkable thermal stability represents another crucial advantage. The substantial water capacity of its cooling system combined with generous oil volumes creates significant thermal inertia, preventing the rapid temperature fluctuations that can damage more highly-stressed designs.

This characteristic is particularly valuable in extreme climates where ambient temperatures vary dramatically within a single operating cycle.
Village mechanics often modify these cooling systems further, creating locally-adapted solutions for specific environmental challenges from additional cooling capacity for tropical deployments to innovative cold-weather starting systems in mountainous regions.
Perhaps most significantly, the 4.236 has generated an extraordinary global ecosystem of knowledge and parts. Its widespread deployment in agricultural equipment, generators, pumping stations, and commercial vehicles created a critical mass of installations that supported the development of parts supply networks reaching even relatively isolated regions.
Local repair shops in market towns often stock essential components, while the engine’s design consistency means that parts from decommissioned units can be salvaged to keep others operational.
This parts interchangeability creates mechanical resilience that newer, constantly-evolving designs cannot match. The engine’s serviceability extends beyond simple parts availability to encompass repair methodologies suited to limited resources.
Its wet-liner cylinder design allows for in-field rebuilds without specialized equipment, while its mechanically-operated valvetrain can be adjusted with basic tools.
Village mechanics have developed remarkable techniques for extending these engines’ lives from hand-lapping valves using locally-sourced compounds to reconditioning injectors using improvised test equipment.
Many 4.236 engines in remote settings continue operating decades beyond their intended service life through these innovative maintenance approaches.
The Perkins’ consistent, predictable power delivery ideally matches the requirements of village infrastructure applications. Its ability to maintain stable output under varying load conditions makes it particularly valuable for electricity generation, where inconsistent supply can damage connected equipment.
For communities where reliable power enables essential services including medical facilities, water purification, and communications, the 4.236’s dependability translates directly into improved quality of life and economic opportunity.
The Honda GX Series: Perfect Portable Power
In the furthest reaches of rural villages across developing nations, the distinctive red engine covers of Honda’s GX series stand as testaments to mechanical excellence adapted perfectly to challenging environments.
These small four-stroke engines ranging from 98cc to 690cc and producing between 3 and 24 horsepower have achieved unprecedented market penetration in remote communities, where they power everything from water pumps and small generators to agricultural equipment and transportation.
For village mechanics, the GX series represents the gold standard in portable power, combining remarkable reliability with a design philosophy that anticipates the maintenance challenges of isolated settings.
The foundation of the GX series’ success in remote environments begins with Honda’s unwavering commitment to construction quality even in their smallest engines.
Unlike many competitors who reduce manufacturing standards for smaller power plants, the GX engines feature the same precise engineering found in Honda’s larger applications.
This manifests in exceptional component tolerances, high-quality materials in critical wear surfaces, and carefully designed lubrication pathways that ensure consistent oil delivery even when operated at challenging angles a common scenario in multipurpose rural applications.
For village mechanics accustomed to frequent failures with other small engines, the GX’s ability to withstand irregular maintenance schedules while continuing to perform reliably creates almost evangelical loyalty to the brand.
These engines demonstrate remarkable fuel efficiency and adaptability to variable fuel quality critical factors in regions where gasoline may be expensive, difficult to obtain, or of inconsistent purity.
The GX’s overhead valve design and precision carburetion system extract maximum energy from each fuel measure while tolerating the occasional contaminated supply that might disable more sensitive engines.
Many village mechanics have developed specialized filtration systems and carburetor modifications that allow these engines to operate on locally available fuels that fall well outside manufacturer specifications, extending their utility in fuel-scarce environments.
Perhaps the GX series’ most significant advantage lies in its exceptional cold-starting capability. Honda’s design innovations, including optimized compression ratios and efficient combustion chamber geometry, enable reliable starting even in challenging conditions without requiring sophisticated battery systems or external power sources.
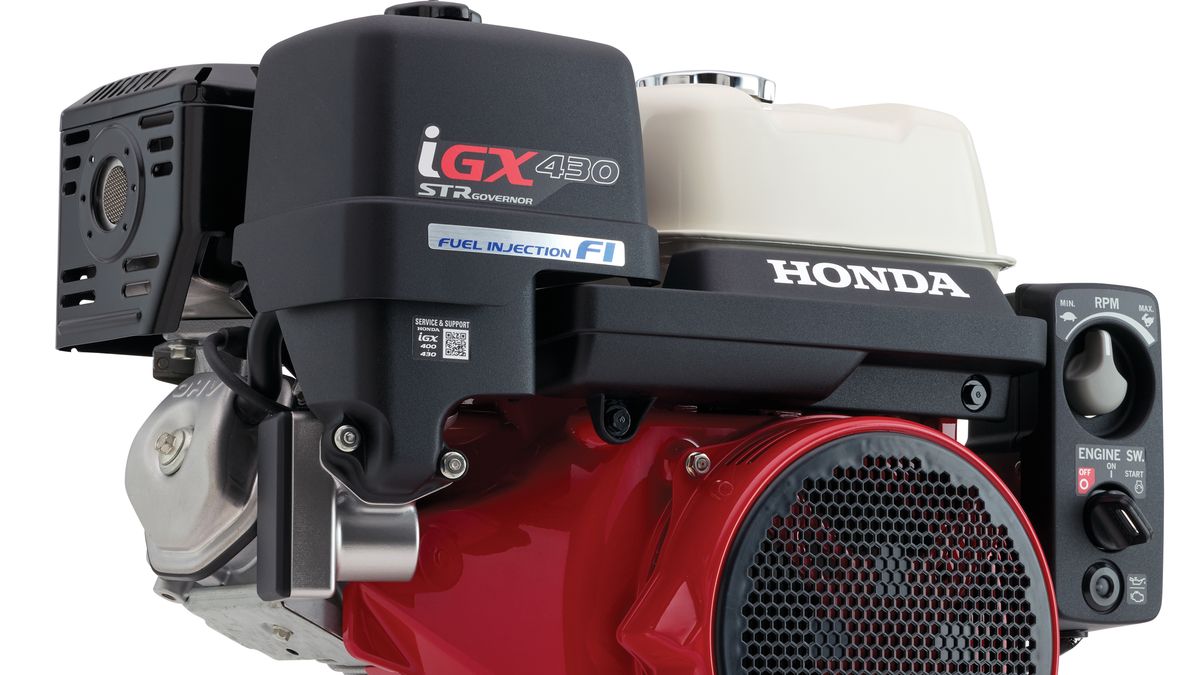
This self-sufficiency is invaluable in remote locations where electric infrastructure is limited or nonexistent. Village mechanics frequently comment on how GX engines will reliably start after multiple pulls even following extended storage periods a critical attribute in seasonal applications like irrigation pumping or emergency power generation.
The standardization of maintenance procedures across the entire GX lineup creates significant knowledge economies for rural mechanics. Techniques learned servicing one model apply directly to others, allowing technical expertise to build incrementally within communities.
This consistency extends to parts compatibility many components, including carburetors, air filters, and ignition systems, maintain common designs across multiple displacements, creating opportunities for creative parts sourcing when supply chains are disrupted.
Some village workshops maintain “donor engines” specifically to harvest components for keeping working units operational during parts shortages.
Honda’s design philosophy prioritizes accessibility for key maintenance points, with spark plugs, air filters, and oil drain locations positioned for easy service without specialized tools.
This attention to serviceability becomes particularly valuable in remote settings where performing routine maintenance must be simple enough to ensure it actually occurs.
The engines’ relatively generous internal clearances also provide forgiveness for maintenance that might be somewhat delayed by circumstance or necessity.
The GX series further distinguishes itself through exceptional vibration management a characteristic that significantly reduces wear on both the engine itself and the equipment it powers.
The engines’ well-balanced design and effective isolation systems prevent the gradual loosening of fasteners and component fatigue that plague less refined alternatives.
For village applications where equipment might operate continuously for days or weeks during critical periods like harvest or flood season, this vibration control translates directly into extended service life and reduced maintenance requirements.
Despite their relatively premium initial cost compared to less expensive alternatives, the GX engines’ extraordinary longevity creates compelling economics for remote communities.
Their exceptional durability means they often remain operational for decades rather than years, spreading the initial investment across a much longer service life than cheaper but shorter-lived competitors.
For village economies where capital for replacement equipment may be scarce, this extended service life represents not just mechanical advantage but genuine economic development opportunity.
Also Read: 5 Cars That Hold Alignment Perfectly and 5 That Constantly Drift