Additive manufacturing, often referred to as “3D printing,” is widely used in prototyping, enabling the creation of parts without the need for costly tooling or skilled machining.
Automakers utilize this technology for design and occasionally even for producing parts, with companies like Czinger leveraging it to fabricate significant structural elements in lightweight sports cars.
While some hot rod shops have embraced 3D printing, it wasn’t until we saw Jay Leno speak at a networking event organized by Aria Group—a manufacturing firm collaborating with 3D printing company Stratasys—that we fully grasped how beneficial additive manufacturing can be for collectors and restoration enthusiasts.
During the event, Leno and his chief engineer, Jim Hall, presented examples of how 3D printing has helped maintain Leno’s extensive collection of rare automobiles.
Later, we had the opportunity to visit Leno’s garage to observe some of these parts and see his Stratasys Fortus 450mc 3D printer firsthand.
Various 3D printing methods are available, tailored to specific materials and intended applications.
For instance, Czinger uses a powder-based printing process to produce metal parts that are ready for production.
Leno’s machine, however, employs fused deposition modeling (FDM), which uses reels of plastic to produce prototype parts for casting, sample parts for testing fit, or custom components.
One of the first projects Hall shared with us involved a 1913 Packard. The engine, a large straight-six with L-head design and cylinders cast in pairs, had hydrolocked, destroying one cylinder.
Hall initially tried traditional repair avenues, searching for new-old-stock and spare parts from restoration suppliers and salvage yards.
As expected, he found that locating 1913 car parts locally was nearly impossible, requiring a creative solution.
Using a laser scanner, they captured data from both the damaged cylinder and intact ones.
With this data input into a CAD program, Hall recreated the cylinder pair in plastic, creating a model that could be sent to the foundry for a new casting.
This approach not only surpassed casting from broken parts but also allowed Hall to experiment with a slightly thicker cylinder design.
“I don’t know how they did it at Packard,” he remarked. “The foundry couldn’t reproduce the piece that thin, but we were able to print it with additional material on the exterior and test fit it before sending it off to be cast.”
“We had four of them made,” added Leno. The CAD model data remains available, so if another Packard owner encounters a similar issue, they can use the model to produce their own engine blocks.
That’s not the only vintage car in Leno’s collection benefiting from 3D printing. His 1907 White steam car, which is now one of fewer than 100 survivors out of over 10,000 originally made, relies on 3D-printed parts for repairs.
The White, like many others of its kind, was cannibalized for aluminum scrap during World War I. When it requires repairs, Leno scans the aluminum parts and prints a casting pattern in ABS plastic.
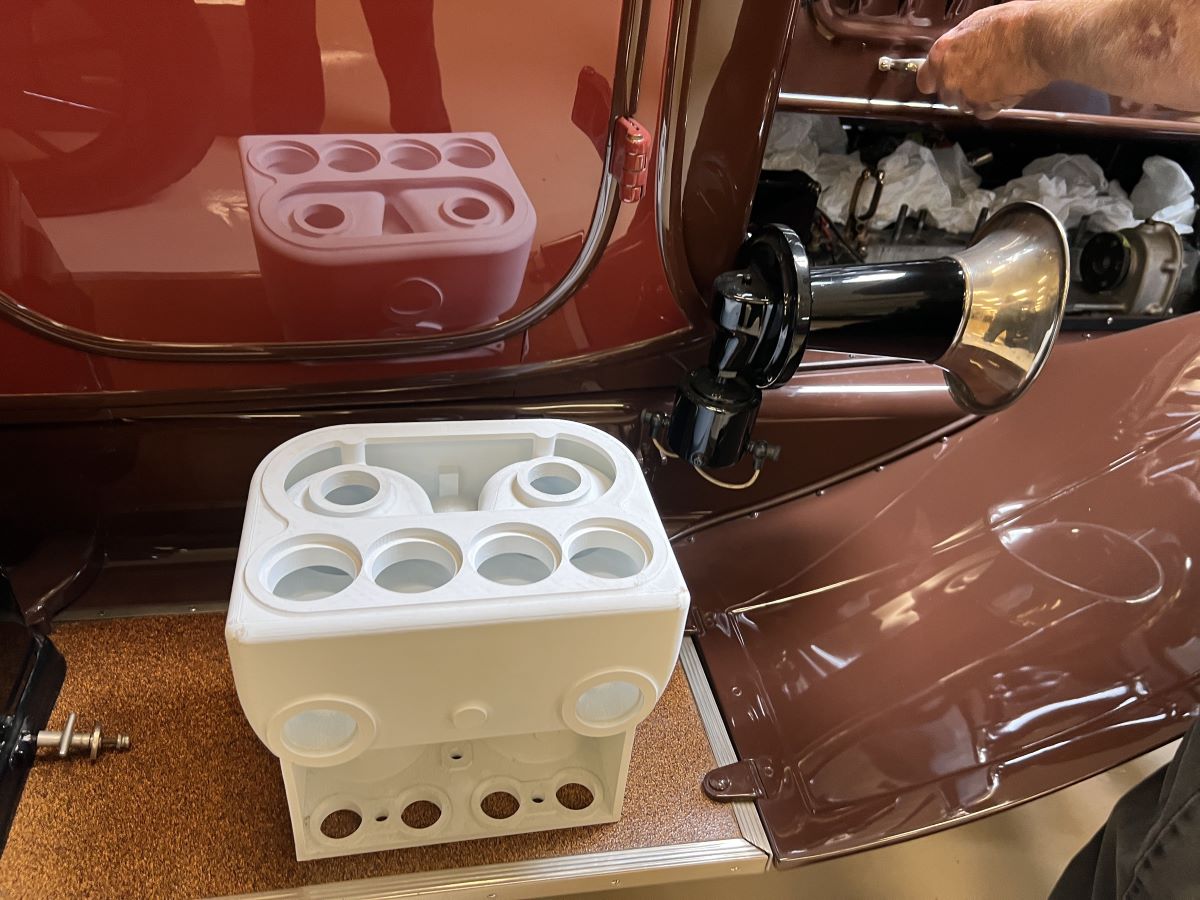
Fast-forward about 50 years from that steam car, and you have the Pontiac Firebird Sprint.
Intended as an affordable American counterpart to sleek European sports cars, the Sprint boasted an advanced overhead-cam inline-six engine that delivered a powerful 215 horsepower.
However, convincing muscle-car enthusiasts to choose an expensive, high-tech six-cylinder over a V-8 was a tough sell.
Consequently, the Sprint was rare even when new and is almost unobtainable today. Naturally, Leno owns a 1968 model and needs parts to keep it in peak condition.
While finding parts for many muscle cars is straightforward thanks to shared part numbers and extensive documentation, obtaining parts for the Sprint is far more challenging.
Body parts and trim pieces are scarce, and whole parts cars are nearly impossible to find. Leno’s Firebird engine cover, for example, was produced on his 3D printer, polished to achieve a factory-like finish.
“We have been able to fix things that were unfixable because in my business, when I first got started dealing with cars, you’d go to a junkyard and find stuff,” Leno said.
“Those parts don’t exist anymore . . . And now you have the technology to make the parts that you want. It’s just unbelievable.”
Additive manufacturing isn’t restricted to rare or antique automobiles. The Aria Group uses Stratasys 3D printers for building concept cars, prototypes, and specialty parts in limited runs.
In Aria’s production facility, we saw an early prototype of the Nilu hypercar, along with an Everatti-converted Porsche 911 EV and a Scarbo Designs SVRover trophy truck.
While Aria didn’t specify which of their 3D-printed parts made it into these vehicles, representatives did confirm that these parts were structural and crucial to vehicle function, not simply for aesthetic purposes.
Even large manufacturers like Toyota utilize 3D printing, with Stratasys printers making parts for the GR86 Cup Car.
During a visit to Toyota’s GR Garage in Charlotte, North Carolina, we learned that each GR86 Cup Car begins as a standard model before it’s stripped down and rebuilt with high-performance, lightweight materials.
Stratasys contributes components such as interior door panels, hood vents, and aerodynamic aids.Leno’s 3D printer can handle multiple materials, enabling him to print parts suited to various needs.
For instance, when he wanted an airbox for the Roush V-8 in his ’66 Galaxie, he printed it in a high-temperature-resistant material, ideal for use in the engine bay.
Similarly, carburetor spacers for a Rolls-Royce needed to be fuel-stable, requiring another specific material. Leno’s printer uses cartridges that monitor material usage and can be swapped out easily.
This versatility lets Hall print temporary signal mounts to test designs on a Detroit Electric before switching materials to create carburetor spacers or tooling that can be dissolved away for mold making.
Though most of us don’t have a chief engineer or a 3D printer in our garages, if you’re ever stuck on a restoration project, it may be worth finding a shop nearby that offers 3D printing.
Stratasys even has a program for on-demand printing at both large and small scales. Who knows? Perhaps Jay Leno’s team has already created a blueprint for the part you need.