Turbocharged engines have transformed from performance-focused novelties to mainstream powerplants found in everything from economy cars to luxury flagships.
While forced induction once carried a reputation for fragility and high maintenance, modern engineering has created turbocharged engines capable of extraordinary longevity when properly maintained.
These engines balance power density with durability through advances in metallurgy, thermal management, lubrication systems, and electronic controls.
The key to their longevity lies in the relationship between engineering and maintenance even the most robustly designed turbocharged engine requires attentive care to reach its maximum potential lifespan.
Proper warm-up and cool-down periods, regular oil changes with appropriate lubricants, and respecting break-in periods all contribute significantly to long-term durability.
This list highlights ten turbocharged engines that have demonstrated exceptional reliability across hundreds of thousands of miles when given proper care.
From time-tested designs with decades of real-world validation to newer powerplants incorporating cutting-edge durability features, these engines represent the pinnacle of forced induction longevity.
Each has earned its reputation through a combination of overengineered components, conservative factory tuning, and design philosophies that prioritize longevity alongside performance.
1. Mercedes-Benz OM617 3.0L Turbodiesel
The Mercedes-Benz OM617 3.0L turbodiesel engine stands as perhaps the most legendary turbocharged engine ever created from a longevity perspective.
Produced from 1974 to 1991, this inline-five cylinder diesel has rightfully earned its reputation as “million-mile capable” with numerous documented examples exceeding 750,000 miles on original internal components.
What makes the OM617 exceptional is its overengineered nature and conservative design philosophy.
Featuring a cast-iron block with seven main bearings (unusual for a five-cylinder design), forged steel crankshaft, and robust connecting rods, the engine was built with significant safety margins.
The pre-combustion chamber design allowed for efficient combustion while maintaining relatively low cylinder pressures compared to modern direct-injection systems, significantly reducing long-term strain on components.
The turbocharging system itself is refreshingly simple by modern standards. A modest Garrett turbocharger provides approximately 8-10 psi of boost, operating well within its design parameters and rarely encountering the heat-related issues that plague more aggressively tuned systems.
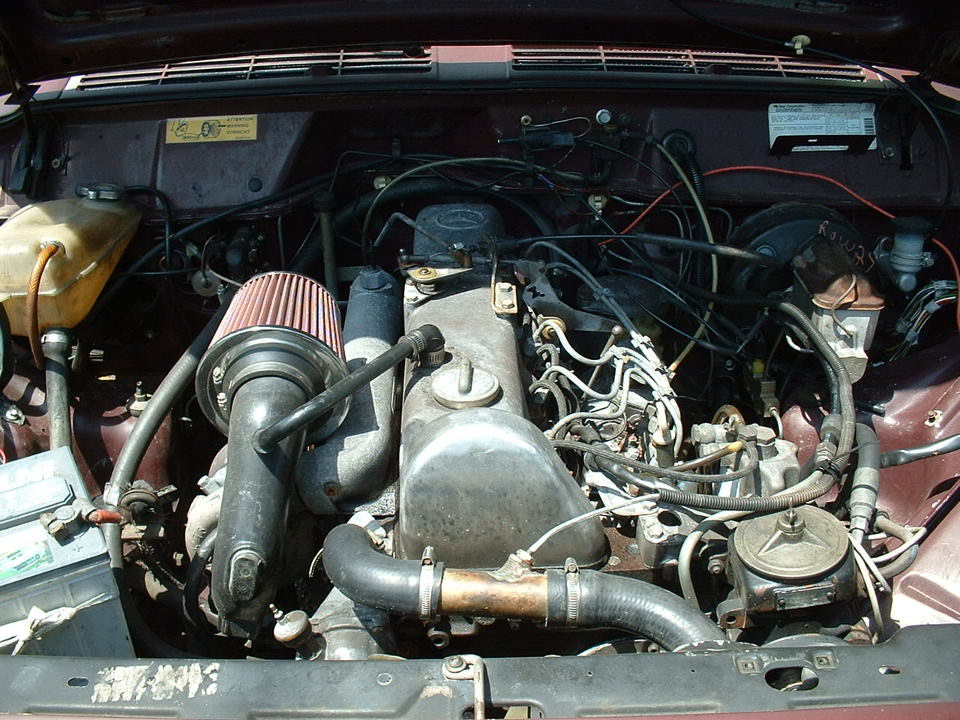
The wastegate and control systems are mechanical rather than electronic, eliminating potential points of electronic failure over decades of operation.
Oil circulation was another area where Mercedes-Benz prioritized longevity. The engine features a large-capacity oil system with excellent filtration and generous oil passages that resist clogging even after hundreds of thousands of miles.
With strict adherence to 3,000-mile oil change intervals using high-quality diesel-specific oils, these engines maintain excellent lubrication even into extreme mileage territory.
The injection pump, traditionally a worn item on diesel engines, is a robust Bosch inline design built to industrial standards.
When properly maintained with regular fuel filter changes and quality diesel fuel, these pumps routinely outlast the vehicles they power.
The indirect injection system also proves more tolerant of varying fuel quality than modern direct injection designs.
The OM617’s reputation for durability is not contingent on babying the engine these powerplants deliver their longevity while enduring real-world driving conditions.
The key to their exceptional lifespan lies in adhering to Mercedes’ prescribed maintenance schedule and addressing minor issues before they escalate into major problems.
With proper care, the OM617 remains the benchmark against which all other turbocharged engines are measured for longevity.
2. Volvo Redblock B230FT/B234F 2.3L Turbo
The Volvo Redblock turbocharged engines, particularly the B230FT and later B234F variants produced from 1985 through the mid-1990s, have earned legendary status for their exceptional durability when properly maintained.
These 2.3-liter four-cylinder engines combine robust engineering with moderate boost levels to create powerplants capable of extraordinary service lives.
The foundation of the Redblock’s longevity begins with its heavy-duty cast iron block featuring siamesed cylinder walls for exceptional strength.
Volvo’s engineering team designed these engines with significantly thicker deck surfaces, main bearing caps, and cylinder walls than contemporary turbocharged engines.
The crankshaft is forged steel, supported by five main bearings with a generous surface area that distributes load effectively even after hundreds of thousands of miles of operation.
The oiling system represents another area where Volvo prioritized longevity over cost-cutting. These engines feature a high-capacity oil pump, large oil passages that resist clogging, and an efficient oil cooler system that maintains proper lubricant temperature even under sustained high-load operation.
When maintained with synthetic oil changed at 5,000-mile intervals, these engines routinely reach 300,000 miles without internal repairs.
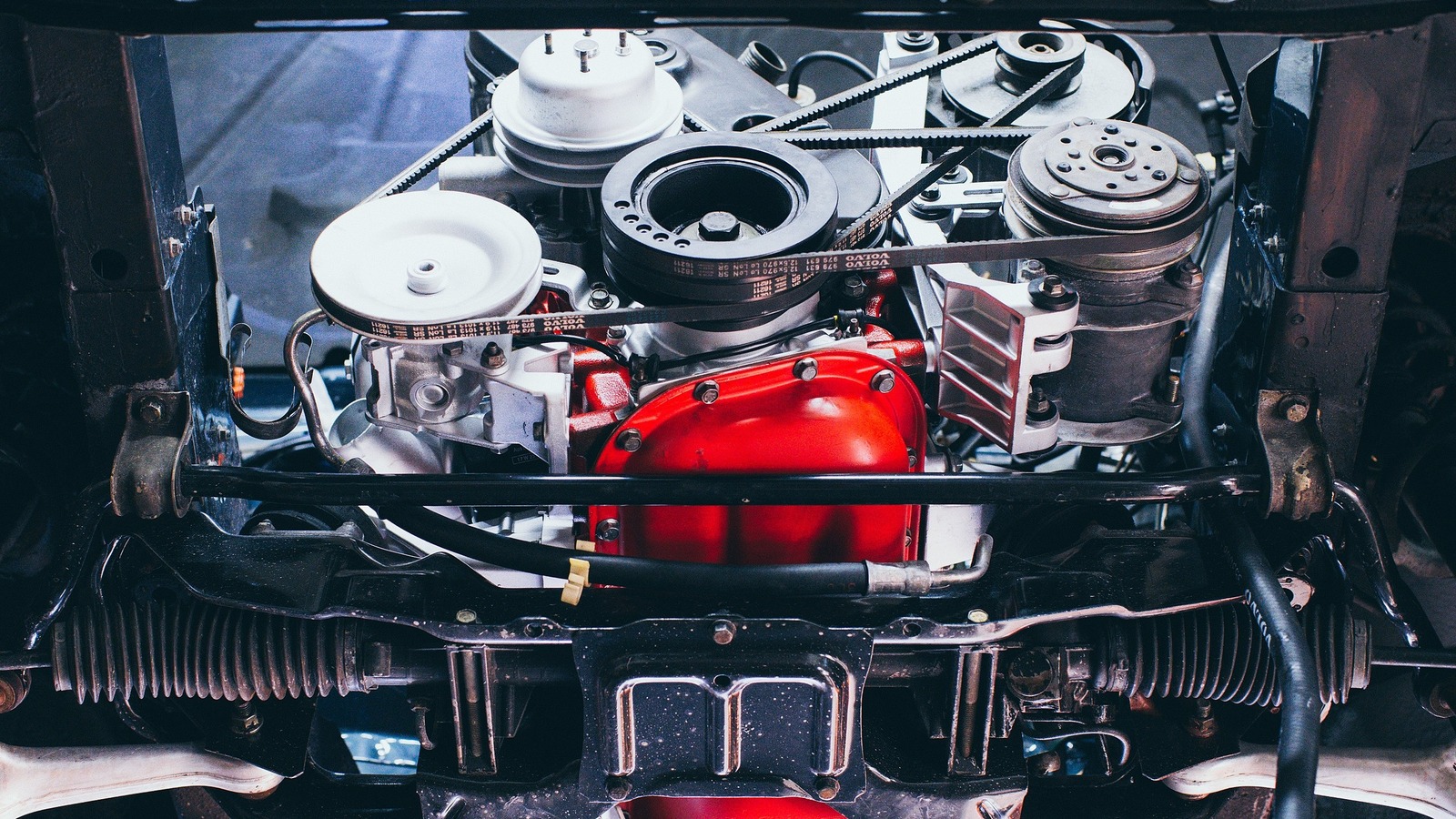
Volvo took a conservative approach to turbocharging, using a modest-sized Garrett or Mitsubishi turbocharger operating at relatively low boost levels (around 7-9 psi in stock form).
This approach minimizes thermal stress on engine components while still delivering satisfying performance gains over naturally aspirated variants.
The intercooling system is effectively sized to maintain consistent intake temperatures, preventing the detonation issues that often compromise longevity in turbocharged engines.
Perhaps most important to the Redblock’s durability is its cooling system design. With a high-capacity radiator, thermostatically controlled oil cooling, and excellent water jacket design around the cylinders and exhaust ports, these engines maintain consistent operating temperatures that prevent the thermal cycling that accelerates wear in many turbocharged engines.
Owners who achieve maximum longevity from these engines typically follow a disciplined warm-up procedure, allowing oil to reach operating temperature before applying heavy loads.
Similarly, a proper cool-down period after hard driving allows the turbocharger to reduce its rotational speed while still receiving oil flow, significantly extending turbocharger bearing life.
With documented examples exceeding 500,000 miles on original bottom ends, the Volvo Redblock turbo engines demonstrate that forced induction and exceptional longevity can coexist when engineering priorities and maintenance practices align properly.
3. BMW M57 3.0L Turbodiesel
The BMW M57 3.0L turbodiesel engine, produced from 1998 through 2008 across multiple iterations, represents one of the most durable forced-induction designs to emerge from Germany.
This inline-six cylinder engine has proven itself capable of extraordinary service life while delivering the performance expected from a BMW powerplant.
The M57’s foundation is its exceptionally rigid cast iron block paired with an aluminum cylinder head.
The block features a closed-deck design with substantial strengthening webbing that minimizes distortion even after hundreds of thousands of miles.
The crankshaft is forged steel, precisely balanced, and supported by seven main bearings that distribute the load evenly across the engine’s length. Connecting rods are fracture-split for perfect alignment and exceptional strength.
BMW’s engineering team addressed many typical diesel durability concerns through thoughtful design.
The common-rail direct injection system operates at lower pressures (around 23,000 psi) than later designs, reducing stress on components while still delivering excellent combustion efficiency.
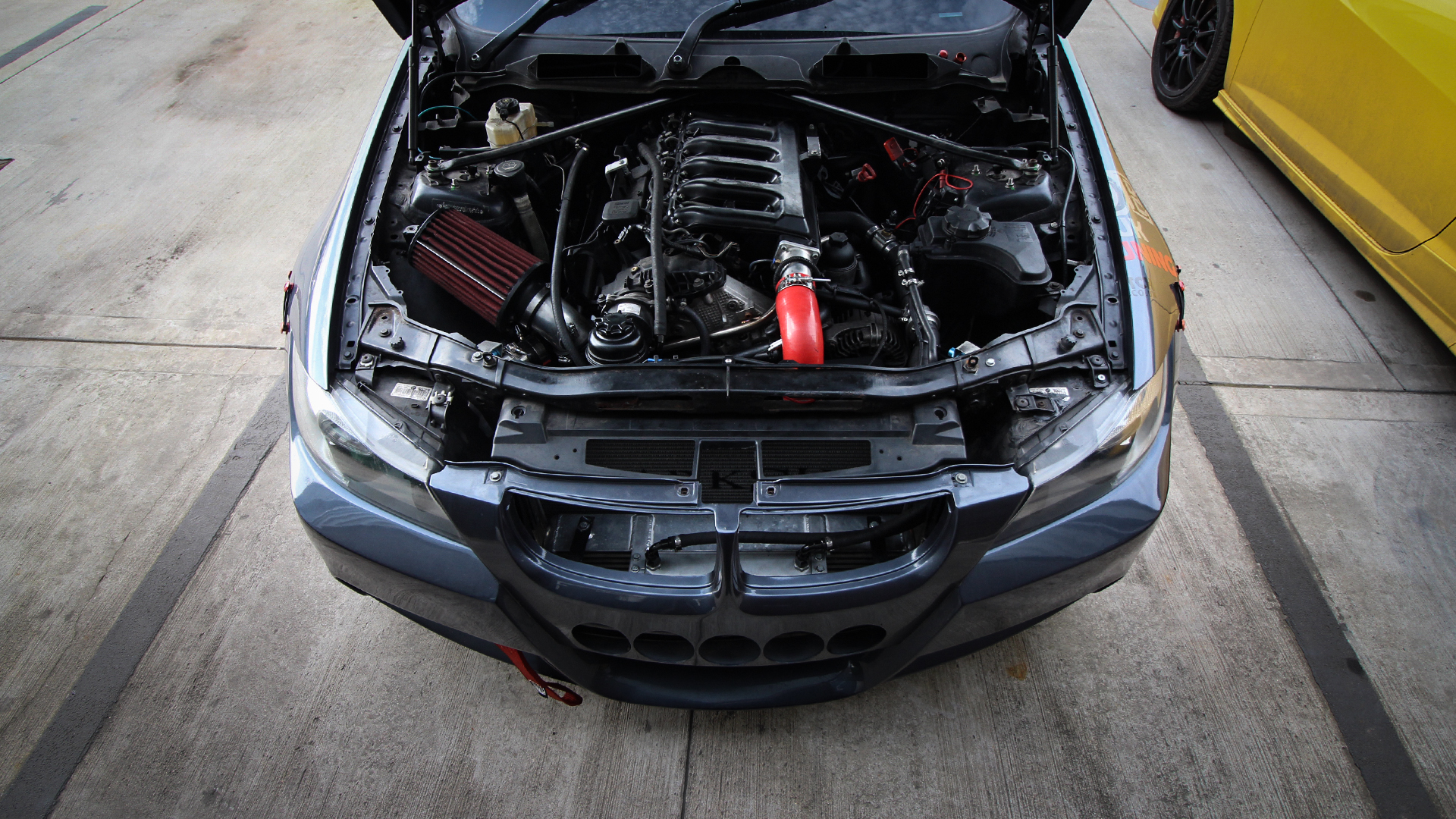
The injectors, typically worn items on diesel engines, are protected by sophisticated electronic control that prevents excessive heat buildup and coking.
The turbocharging system evolved throughout production, with later models featuring variable geometry turbochargers.
These units are sized conservatively, operating well within their design parameters rather than being pushed to maximum output.
The resulting lower turbine temperatures and reduced shaft speeds contribute significantly to longevity. The intercooling system is generously sized, maintaining consistent intake temperatures that prevent thermal shock to engine components.
Oil circulation received particular attention during design. The M57 features a high-pressure, high-volume oil pump that ensures adequate lubrication to critical components even as clearances increase with age.
The oil cooler system effectively manages oil temperatures during extended high-load operation, preventing the oil degradation that often compromises turbodiesel longevity.
Particular to this engine’s durability is its effective emissions control design. Unlike many diesels that suffer from exhaust gas recirculation (EGR) system failures, the M57’s system is more robustly engineered and less prone to clogging when properly maintained.
This prevents the common cascade of failures that often reduce diesel engine lifespan. Owners who achieve maximum longevity typically maintain strict 7,500-mile oil change intervals using BMW-approved synthetic oils, replace fuel filters at recommended intervals, and address minor issues promptly before they cascade into major problems.
With this maintenance approach, M57-equipped vehicles routinely exceed 300,000 miles without major engine work, with many documented examples surpassing 400,000 miles on original internal components.
4. Toyota 2JZ-GTE 3.0L Twin-Turbo
The Toyota 2JZ-GTE 3.0L twin-turbocharged inline-six, most famously featured in the 1993-2002 Toyota Supra, has achieved legendary status not only for its performance potential but also for its remarkable durability when properly maintained.
Unlike many high-performance engines that sacrifice longevity for power, the 2JZ-GTE was engineered from the outset to deliver both.
The engine’s foundation is its closed-deck, cast-iron block with seven main bearings supporting a forged steel crankshaft.
The block features extra-thick cylinder walls and substantial reinforcement around high-stress areas, creating an exceptionally rigid structure that resists flexing even under significant boost pressure.
This rigidity maintains precise bearing alignment and cylinder roundness throughout the engine’s lifespan, minimizing wear patterns that typically accelerate with age in less robust designs.
Toyota’s engineering team employed a sequential twin-turbocharger system that balances response with reliability.
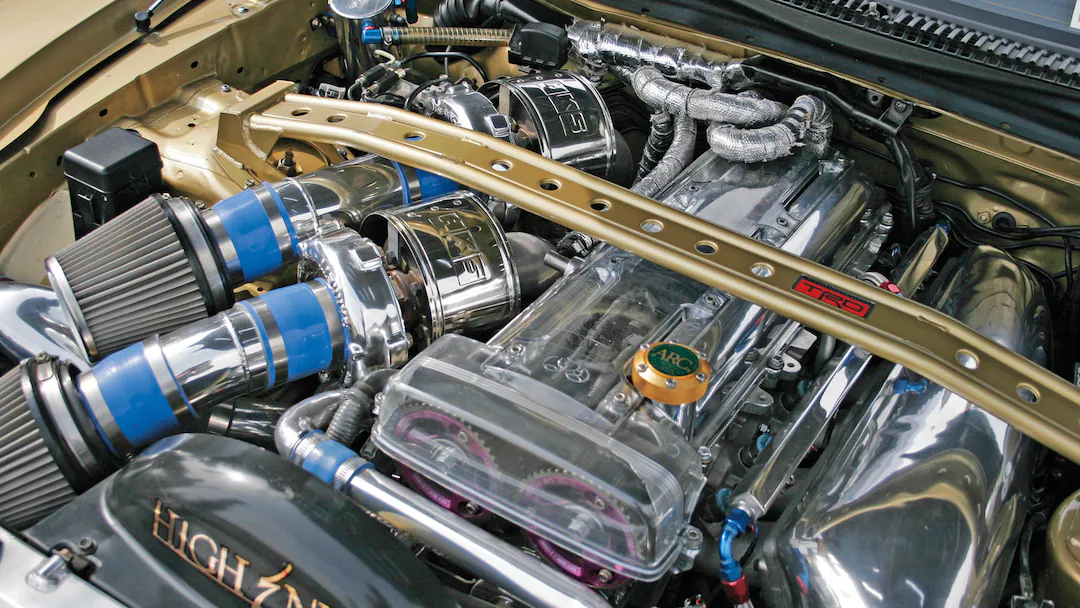
Rather than pushing single turbochargers to their limits, the sequential setup allows each turbocharger to operate well within its efficiency range, reducing thermal stress and extending turbine life.
The factory-specified ceramic turbine wheels have proven exceptionally durable, with many original units still functioning properly after 200,000+ miles when properly maintained.
The oiling system represents another area where Toyota prioritized longevity. The engine features a high-capacity oil pump, large oil galleries, and an efficient oil cooler that maintains proper lubricant temperature even during sustained high-performance driving.
The six-bolt main caps secure the crankshaft firmly, preventing the bearing walk and crankshaft deflection that often leads to premature failure in highly stressed engines.
Cooling system design further contributes to the 2JZ-GTE’s longevity. With a large-capacity radiator, effective water jackets, and excellent flow characteristics, the engine maintains consistent operating temperatures that prevent the thermal cycling that accelerates wear in many turbocharged engines.
The head gasket design, traditionally a failure point in forced-induction engines, has proven remarkably robust, with failure rare even in engines producing significantly more than factory power.
Owners who achieve maximum longevity from these engines typically follow a disciplined approach to maintenance, including warming the engine thoroughly before applying heavy load, allowing proper cool-down after spirited driving, and maintaining 3,000-5,000 mile oil change intervals with high-quality synthetic lubricants.
The fuel system components, including the in-tank pump and injectors, require consistent maintenance to prevent cascade failures that can damage engine internals.
With documented examples exceeding 300,000 miles on original internals some while producing substantially more than factory power the 2JZ-GTE stands as evidence that with proper engineering and maintenance, turbocharged performance and exceptional longevity need not be mutually exclusive.
Also Read: 10 Trucks With the Lowest Depreciation Rates After 5 Years
5. Cummins 5.9L 24-Valve ISB Turbodiesel
The Cummins 5.9L 24-valve ISB turbodiesel engine, particularly in its 2003-2007 “common rail” iteration (often referred to as the 5.9L CR), represents one of the most durable turbocharged engines ever installed in a consumer vehicle.
Found primarily in Dodge Ram heavy-duty pickups, this inline-six turbodiesel has established a reputation for extreme longevity when properly maintained.
The foundation of the 5.9L’s durability is its robust iron block with deep skirts and seven main bearings supporting a forged steel crankshaft.
The block features extra material in critical stress areas and cylinder walls that are significantly thicker than required a design philosophy that priortizes longevity over weight savings.
This substantial bottom end has proven capable of handling significantly more than the factory power output without compromising reliability.
Cummins’ approach to the valve train contributes significantly to longevity. The 24-valve design (four valves per cylinder) allows for optimal breathing without requiring extreme valve lift or aggressive cam profiles that accelerate wear.
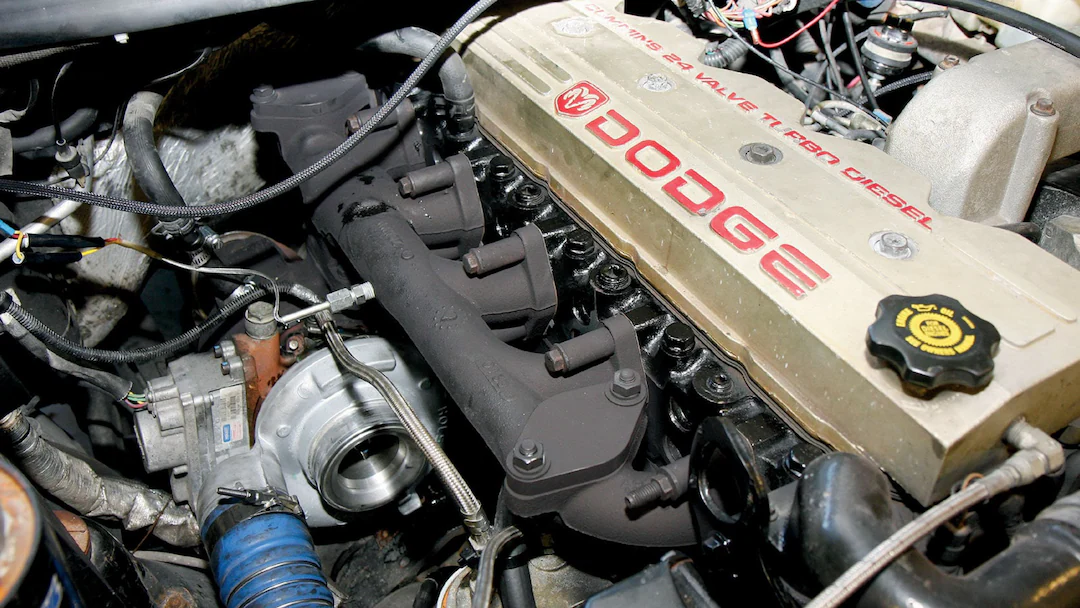
The solid lifter design eliminates the hydraulic lifter failures common in many engines, while hardened valve seats and stellite-faced exhaust valves withstand the extreme temperatures associated with diesel combustion.
The common rail fuel injection system, manufactured by Bosch, represents a significant reliability improvement over the earlier mechanical injection designs.
Operating at approximately 23,000 psi (significantly lower than later diesel engines), the system balances efficient combustion with component longevity.
The injectors, while still wearing items, typically achieve 200,000+ miles before requiring replacement far longer than many comparable diesels.
The turbocharging system employs a fixed-geometry Holset HY35W turbocharger that emphasizes reliability over cutting-edge performance.
With conservative sizing and relatively moderate boost levels (around 22-25 psi), the turbocharger operates well within its design parameters, preventing the overspin and excessive heat generation that often lead to premature turbocharger failure.
The wastegate and control systems are robustly engineered for commercial duty cycles. Oil circulation received particular attention during design.
The engine employs a gerotor oil pump that maintains consistent pressure even as clearances increase with age.
The oil filtration system features a large-capacity filter that provides excellent protection against contaminants.
When maintained with 7,500-mile oil change intervals using high-quality diesel-specific synthetic oils, these engines routinely reach 350,000+ miles without internal repairs.
Cooling system design further contributes to longevity, with a high-flow water pump, efficient radiator, and well-designed water jackets that prevent localized hot spots.
Unlike many modern diesels plagued by emissions equipment failures, the relatively simple emissions systems on these engines (before the addition of particulate filters in later models) have proven remarkably trouble-free.
With numerous documented examples exceeding 500,000 miles on original internals, the 5.9L Cummins stands as compelling evidence that with proper design and maintenance, turbocharged engines can deliver both substantial power and extraordinary service life.
6. Porsche M96/M97 Turbo 3.6-3.8L Flat-Six
The Porsche M96/M97 turbocharged flat-six engines, particularly in their 2001-2012 iterations found in the 996 and 997 generation 911 Turbo models, represent a remarkable achievement in combining performance with longevity.
Unlike the naturally aspirated variants that experienced well-documented issues with intermediate shaft bearings, the turbocharged versions received substantial engineering upgrades that have resulted in exceptional durability when properly maintained.
The foundation of these engines is a closed-deck aluminum block with Nikasil-coated cylinders that resist wear even after hundreds of thousands of miles.
The flat-six configuration inherently balances primary forces, reducing vibration that can accelerate wear on bearings and other components.
Porsche engineers specified larger, more robust main bearings in the turbocharged variants, addressing a potential weakness in earlier designs.
The crankshaft is forged steel, precisely balanced, and designed with conservative journal sizes that maintain oil film thickness even under high loads.
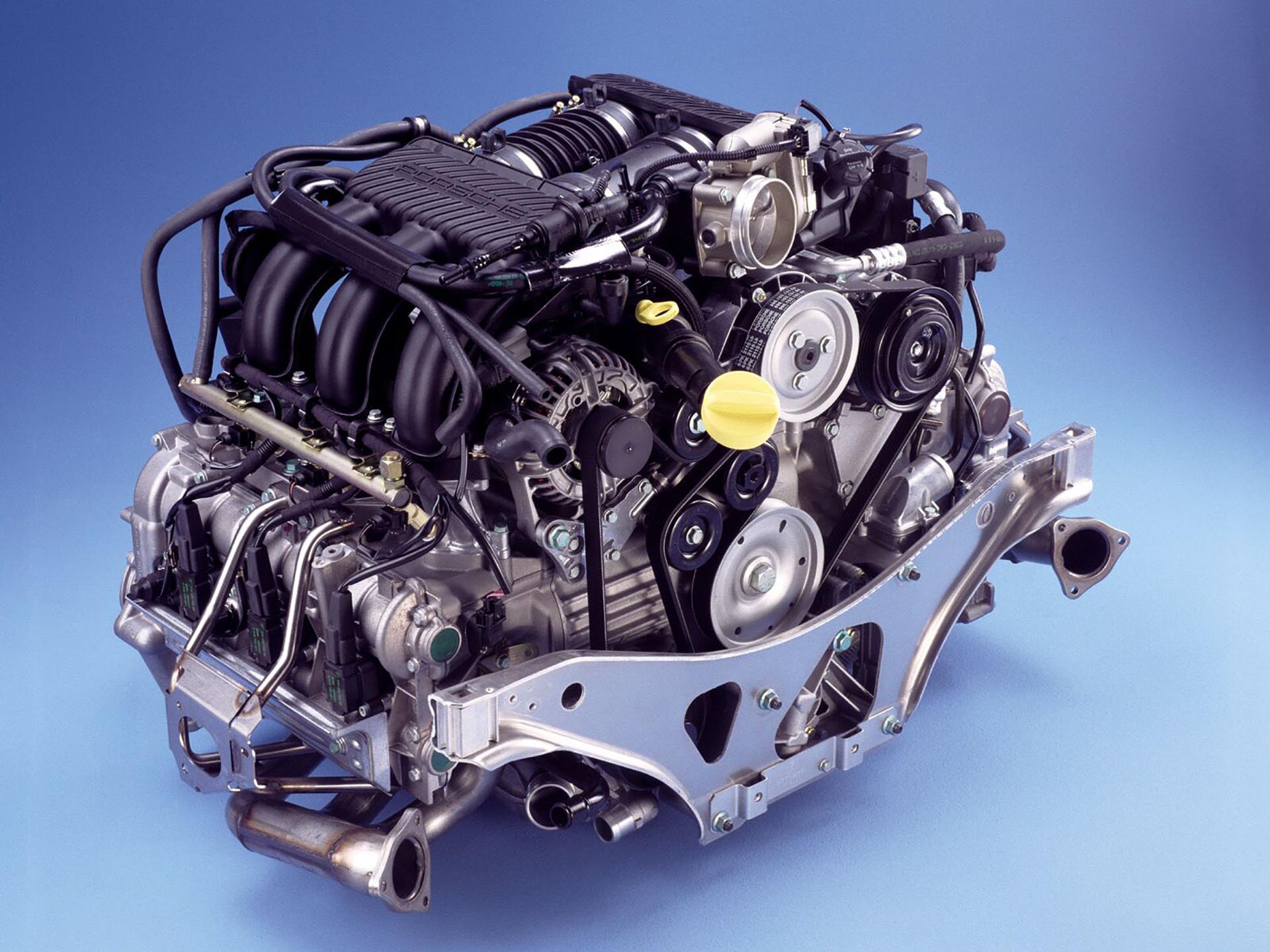
The water-cooled architecture represents a significant advancement over the air-cooled predecessors, allowing more precise temperature control throughout the engine.
The cooling system features multiple circuits with thermostatic control, preventing the localized hot spots that often compromise longevity in high-performance engines.
Temperature sensors throughout the engine allow the management system to adjust operation parameters to protect components when necessary.
Porsche’s approach to turbocharging emphasizes durability alongside performance. The twin turbochargers are conservatively sized and operate at moderate boost levels relative to their flow capacity, preventing the turbine overspin and excessive exhaust temperatures that often lead to premature failure.
The intercooling system is generously sized, maintaining consistent intake temperatures that prevent detonation a primary enemy of engine longevity.
Oil circulation received particular attention during design. The dry-sump lubrication system ensures consistent oil pressure during high-lateral-G cornering, preventing the momentary oil starvation that can destroy bearings in conventional wet-sump designs.
The multiple oil pumps maintain circulation even during extreme driving conditions, while the large oil capacity provides thermal stability that prevents oil degradation during track use.
The variable valve timing system (VarioCam) is hydraulically actuated rather than electronically controlled, resulting in a simpler, more robust design that requires minimal maintenance over the engine’s lifespan.
The timing chain drive to the camshafts, rather than a belt, eliminates a common maintenance item and potential point of failure.
Owners who achieve maximum longevity from these engines typically adhere to strict 5,000-mile oil change intervals using Porsche-approved synthetic lubricants, allow proper warm-up before applying heavy loads, and permit adequate cool-down after spirited driving.
With this maintenance approach, these engines routinely exceed 150,000 miles without major repair, with documented examples surpassing 200,000 miles on original internals exceptional longevity for high-performance turbocharged engines producing over 400 horsepower.
7. Ford EcoBoost 3.5L V6
The Ford 3.5L EcoBoost V6 engine, introduced in 2010 and continually refined through its current production, represents a significant achievement in turbocharged engine longevity.
Initially met with skepticism from Ford’s traditional V8 customers, this twin-turbocharged V6 has proven itself capable of exceptional durability in applications ranging from luxury sedans to hard-working F-150 pickups and commercial vehicles.
The foundation of the 3.5L EcoBoost’s longevity begins with its deep-skirt aluminum block featuring structural webbing that maintains rigidity throughout the engine’s life.
The crankshaft is forged steel supported by four main bearings with enlarged bearing surfaces that distribute load effectively.
The connecting rods are powder-forged metal with cracked caps that provide perfect alignment and exceptional strength, while the pistons feature low-friction coatings and optimized ring packs that maintain cylinder sealing even after hundreds of thousands of miles.
Ford engineers addressed many traditional turbocharged engine durability concerns through thoughtful design choices.
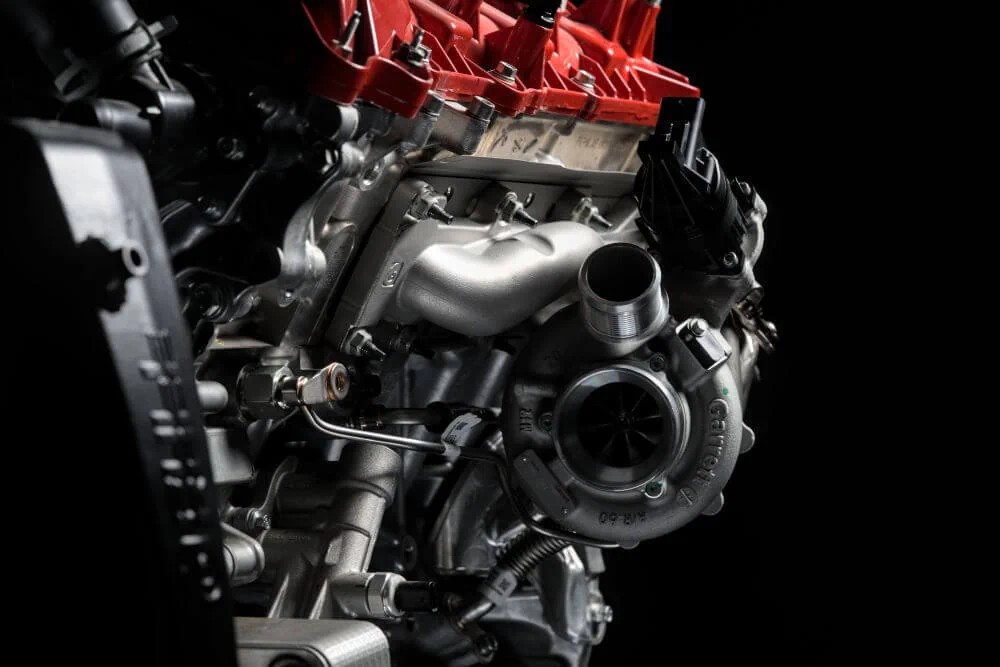
The twin turbochargers are relatively small and operate at moderate boost levels (approximately 12-15 psi), preventing the excessive heat generation that often compromises turbocharger longevity.
The turbos are mounted directly to the exhaust manifolds, reducing heat soak after shutdown and associated coking of oil in turbo bearings a common cause of premature turbocharger failure.
The direct fuel injection system operates at over 2,000 psi, delivering precisely controlled fuel directly into the combustion chamber.
This approach allows for excellent atomization and combustion efficiency while minimizing carbon buildup on intake valves a concern with early direct-injection engines.
On 2017+ models, a supplemental port injection system was added, virtually eliminating intake valve deposits and associated performance degradation over time.
Cooling system design contributes significantly to longevity. The engine features a split cooling system that allows for targeted temperature control of critical components.
The water pump is designed for extended service life, while the coolant formulation is specified for 100,000-mile change intervals.
The oil cooler effectively manages oil temperatures during extended high-load operation, preventing oil degradation that can accelerate engine wear.
Perhaps most important to the EcoBoost’s durability is its advanced electronic control system. The powertrain control module continuously monitors dozens of parameters, adjusting operation to protect engine components when necessary.
This includes thermal management, knock control, and turbocharger wastegate operation that prevents overboost conditions that could damage internal components.
Owners who achieve maximum longevity typically follow Ford’s recommended 5,000-7,500 mile oil change intervals using synthetic oil meeting Ford’s specifications, replace air filters at recommended intervals, and address minor issues promptly before they cascade into major problems.
With this maintenance approach, these engines routinely exceed 200,000 miles without major repair, with fleet examples surpassing 300,000 miles in commercial service compelling evidence that modern turbocharged engines can deliver exceptional longevity when properly engineered and maintained.
8. Subaru EJ255/EJ257 2.5L Turbo
The Subaru EJ255/EJ257 2.5L turbocharged flat-four engines, featured in various WRX, WRX STI, and Forester XT models from 2004 through 2021, have earned a reputation for exceptional longevity when properly maintained despite their high-performance nature.
While these engines have faced criticism for specific failure modes, those issues are typically associated with modification, abuse, or maintenance neglect rather than inherent design flaws.
The foundation of these engines is a semi-closed deck aluminum block with robust main bearing supports and reinforced crankcase.
The boxer configuration provides a natural balance that reduces vibration-induced wear on bearings and other components.
The crankshaft is forged steel with five main bearings, providing substantial support for an engine that produces significant torque at low RPM.
The connecting rods, particularly in the EJ257 STI variant, are engineered for strength rather than weight reduction, providing a significant safety margin when operated within factory parameters.
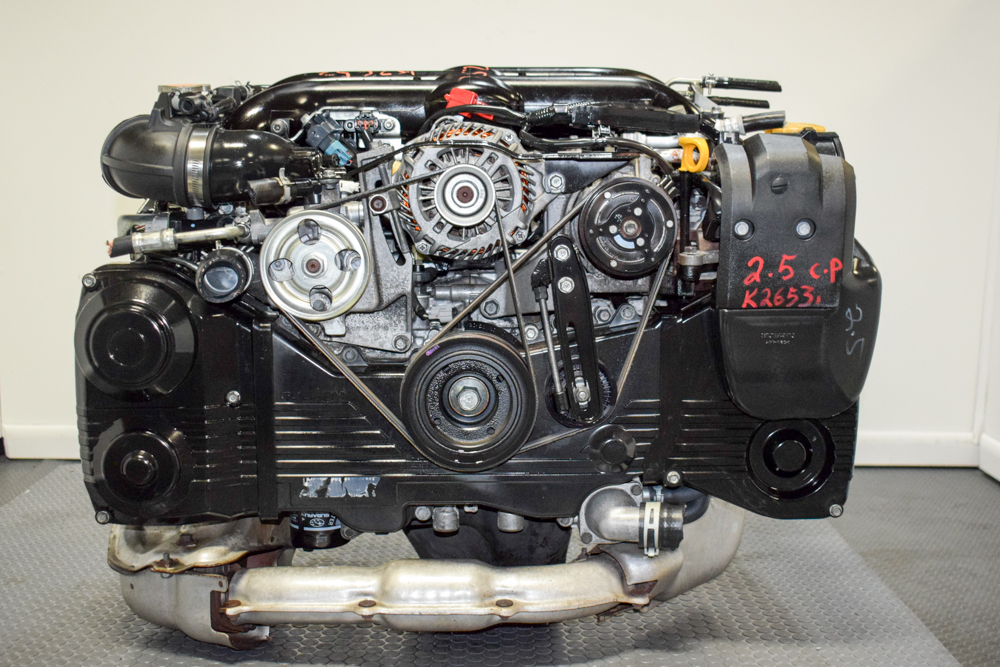
Subaru’s approach to the valvetrain contributes significantly to longevity. The four valve per cylinder design with solid lifters eliminates the hydraulic lifter failures common in many engines.
The dual overhead camshafts operate in aluminum heads with generous cooling passages that maintain consistent temperatures around valve seats and guides, preventing the thermal distortion that often leads to valve sealing issues in turbocharged engines.
The single turbocharger design (TD04 in most applications) represents a balanced approach to performance and durability. While not the most advanced turbocharging system, its simplicity contributes to longevity, with fewer components that can potentially fail.
The wastegate and control systems are robustly engineered for long-term reliability, preventing overboost conditions that can damage internal components.
The intercooling system is effectively sized to maintain consistent intake temperatures, preventing detonation that could compromise engine longevity.
Oil circulation received particular attention during design. The engine features a high-pressure, high-volume oil pump that ensures adequate lubrication to critical components even under high lateral G-forces experienced during performance driving.
The oil pickup design is less susceptible to starvation than many competitors, preventing the momentary loss of oil pressure that can destroy bearings during aggressive driving.
Cooling system design further contributes to longevity, with a high-flow water pump, efficient radiator, and well-designed water jackets that prevent localized hot spots.
The thermostat is designed to open at relatively low temperatures, helping the engine reach and maintain optimal operating temperature quickly, which reduces wear during cold operation.
Owners who achieve maximum longevity from these engines typically follow a disciplined approach to maintenance, including strict 3,000-5,000 mile oil change intervals with high-quality synthetic lubricants, allowing proper warm-up before applying heavy load, maintaining consistent oil levels, and avoiding abrupt shutdown after high-power operation.
The factory tune is conservative, with a significant safety margin built in those who resist the temptation to modify for more power typically experience far fewer reliability issues.
With documented examples exceeding 250,000 miles on original internals when maintained according to these principles, the EJ255/EJ257 engines demonstrate that Subaru’s approach to turbocharged performance can deliver exceptional longevity when paired with appropriate maintenance practices.
9. Mercedes-Benz M278 4.7L Twin-Turbo V8
The Mercedes-Benz M278 4.7L twin-turbocharged V8, produced from 2010 to 2020 and featured in numerous E-Class, S-Class, CLS, and GL models, represents a remarkable achievement in combining luxury performance with exceptional durability.
Unlike some previous Mercedes forced-induction engines that developed specific reliability issues, the M278 has established itself as a powerplant capable of extraordinary service life when properly maintained.
The foundation of the M278’s longevity is its closed-deck aluminum block with cast-in iron cylinder liners.
The block features substantial reinforcement around high-stress areas, creating an exceptionally rigid structure that maintains precise bearing alignment throughout the engine’s lifespan.
The crankshaft is forged steel, supported by five main bearings with cross-bolted main caps that prevent bearing caps walk under high loads.
The connecting rods are forged steel with cracked caps for perfect alignment, while the pistons feature advanced coatings that reduce friction and maintain cylinder sealing even after hundreds of thousands of miles.
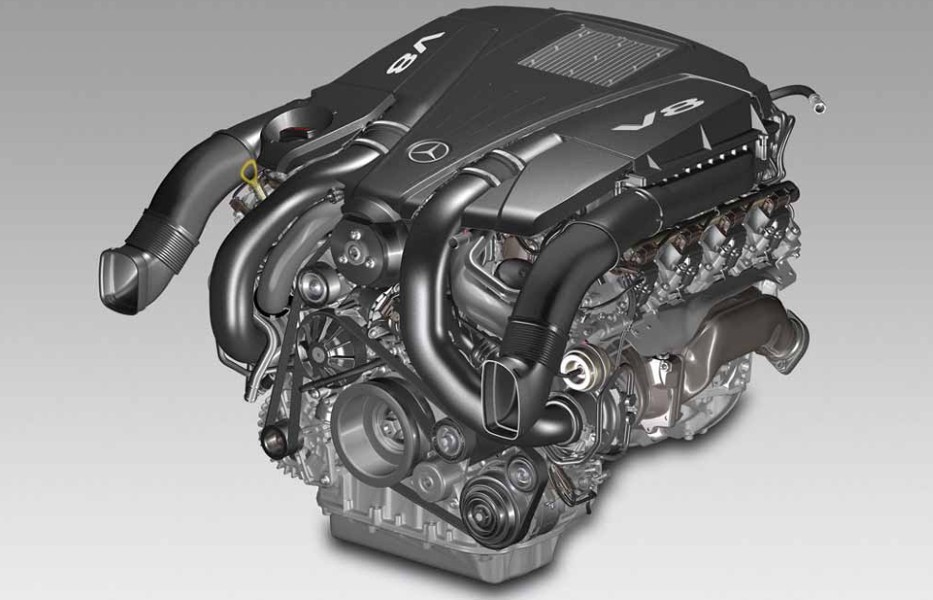
Mercedes engineers addressed many traditional turbocharged engine durability concerns through thoughtful design choices.
The twin turbochargers are mounted in the valley of the V8 (“hot V” configuration), which shortens exhaust paths and improves throttle response while also placing the turbos in a position where they benefit from the engine’s cooling system.
Operating at relatively moderate boost levels (around 12-14 psi), these turbochargers stay well within their design parameters, preventing the excessive heat generation that often compromises turbocharger longevity.
The direct injection system operates at over 2,900 psi, delivering precisely controlled fuel directly into the combustion chamber.
This approach allows for excellent atomization and combustion efficiency while reducing carbon buildup through precise spray patterns.
The injectors are positioned to minimize cylinder wall wetting, reducing oil dilution issues that can accelerate wear in direct injection engines.
Oil circulation received particular attention during design. The engine features a variable displacement oil pump that delivers appropriate oil pressure based on engine needs, reducing parasitic losses while ensuring adequate lubrication.
The oil cooler effectively manages oil temperatures during extended high-load operation, preventing oil degradation that can accelerate engine wear.
Mercedes specifies a 229.5 or higher oil standard, which ensures adequate protection for turbocharged operation.
Perhaps most important to the M278’s durability is its advanced electronic control system. The powertrain control module continuously monitors dozens of parameters, adjusting operation to protect engine components when necessary.
This includes sophisticated knock control, variable valve timing adjustment, and turbocharger wastegate operation that prevents damaging operating conditions.
Owners who achieve maximum longevity typically follow Mercedes’ recommended 10,000-mile oil change intervals (though many choose to reduce this to 7,500 miles for added protection), use only Mercedes-approved synthetic oils, follow the recommended coolant replacement schedule, and address minor issues promptly before they cascade into major problems.
With this maintenance approach, these engines routinely exceed 200,000 miles without major repair, with numerous examples approaching 300,000 miles on original internals remarkable for a luxury performance engine producing between 402-449 horsepower.
10. BMW N55 3.0L Turbo Inline-Six
The BMW N55 3.0L turbocharged inline-six, produced from 2009 to 2019 and featured across numerous BMW models from the 1-Series through the 7-Series, represents a significant achievement in balancing performance with longevity.
Following the more problematic N54 twin-turbo engine, the N55 addressed many of its predecessor’s reliability concerns while maintaining impressive performance capabilities.
The foundation of the N55’s durability is its closed-deck aluminum block with cast-iron cylinder liners.
The block features substantial reinforcement around high-stress areas, creating a rigid structure that maintains precise bearing alignment throughout the engine’s lifespan.
The crankshaft is forged steel, precisely balanced, and supported by seven main bearings that distribute the load evenly across the engine’s length.
This traditional inline-six layout naturally balances primary and secondary forces, reducing vibration that can accelerate wear on bearings and other components.
BMW’s approach to turbocharging represents a thoughtful balance between performance and reliability.

Unlike the N54’s twin-turbo setup, the N55 employs a single twin-scroll turbocharger that combines the response benefits of smaller turbos with the simplicity and reliability advantages of a single-turbo design.
Operating at moderate boost levels (around 11-13 psi), the turbocharger stays well within its design parameters, preventing excessive heat generation and bearing loads that often compromise turbocharger longevity.
The direct injection system operates at over 2,000 psi, delivering precisely controlled fuel directly into the combustion chamber.
This approach allows for excellent atomization and combustion efficiency while reducing carbon buildup through precise spray patterns.
The injectors are positioned to minimize cylinder wall wetting, reducing oil dilution issues that can accelerate wear in direct injection engines.
Valvetrain design contributes significantly to longevity. The N55 features BMW’s Valvetronic system, which provides infinitely variable valve lift without using a traditional throttle plate.
This reduces pumping losses and improves efficiency while creating less stress on valve components.
The Double-VANOS variable valve timing system is hydraulically actuated with improved seals compared to earlier designs, addressing a common failure point in previous BMW engines.
Oil circulation received particular attention during design. The engine features a volume-controlled oil pump that delivers appropriate pressure based on engine needs, reducing parasitic losses while ensuring adequate lubrication.
The oil cooler effectively manages oil temperatures during extended high-load operation, preventing oil degradation that can accelerate engine wear.
BMW specifies LL-01 rated synthetic oils, which ensure adequate protection for turbocharged operation.
Owners who achieve maximum longevity typically follow a more conservative maintenance schedule than BMW’s recommended 10,000-mile oil change intervals, often changing oil every 5,000-7,500 miles for added protection.
Other best practices include allowing proper warm-up before applying heavy loads, permitting adequate cool-down after spirited driving, and addressing minor issues promptly before they cascade into major problems.
With documented examples exceeding 200,000 miles on original internals when maintained according to these principles, the N55 engine demonstrates that modern turbocharged performance and exceptional longevity can coexist when engineering priorities and maintenance practices align properly.
Also Read: 10 SUVs With the Most Durable Engines That Can Last a Lifetime