In an era of increasingly complex automotive technology, the ability to maintain and repair your vehicle has become a cherished skill for many enthusiasts and practical-minded owners alike.
While modern cars continue to integrate sophisticated electronics and sealed components, certain vehicles stand out for their DIY-friendly design. These models feature accessible engine bays, widely available parts, straightforward mechanical systems, and robust support communities that make home repairs feasible and even enjoyable.
Whether you’re a seasoned mechanic or a novice with basic tools, the following twelve vehicles represent some of the best options for those who prefer to handle maintenance and repairs personally.
Each offers a unique combination of simplicity, accessibility, durability, and community support that empowers owners to save money and develop valuable skills.
From dependable sedans to rugged off-roaders and classic trucks, these vehicles continue to earn praise for their repairability in an age when many manufacturers prioritize dealer service over DIY accessibility.
1. Toyota Corolla (1990s-2000s Models)
The Toyota Corolla, particularly models from the 1990s through early 2000s, stands as a paragon of DIY-friendly design. These vehicles earned their reputation through an elegant simplicity that modern cars often lack.
Under the hood, you’ll find a spacious engine bay with clearly arranged components and plenty of room to maneuver tools – a stark contrast to today’s tightly packed engine compartments.
What truly distinguishes the Corolla is its legendary 1ZZ-FE engine, which combines remarkable reliability with straightforward engineering. Common maintenance tasks like oil changes, spark plug replacements, and filter swaps require minimal specialized tools and can be completed by novices following basic online tutorials.
Even more complex procedures like timing belt replacements or brake overhauls remain within reach of moderately experienced home mechanics.
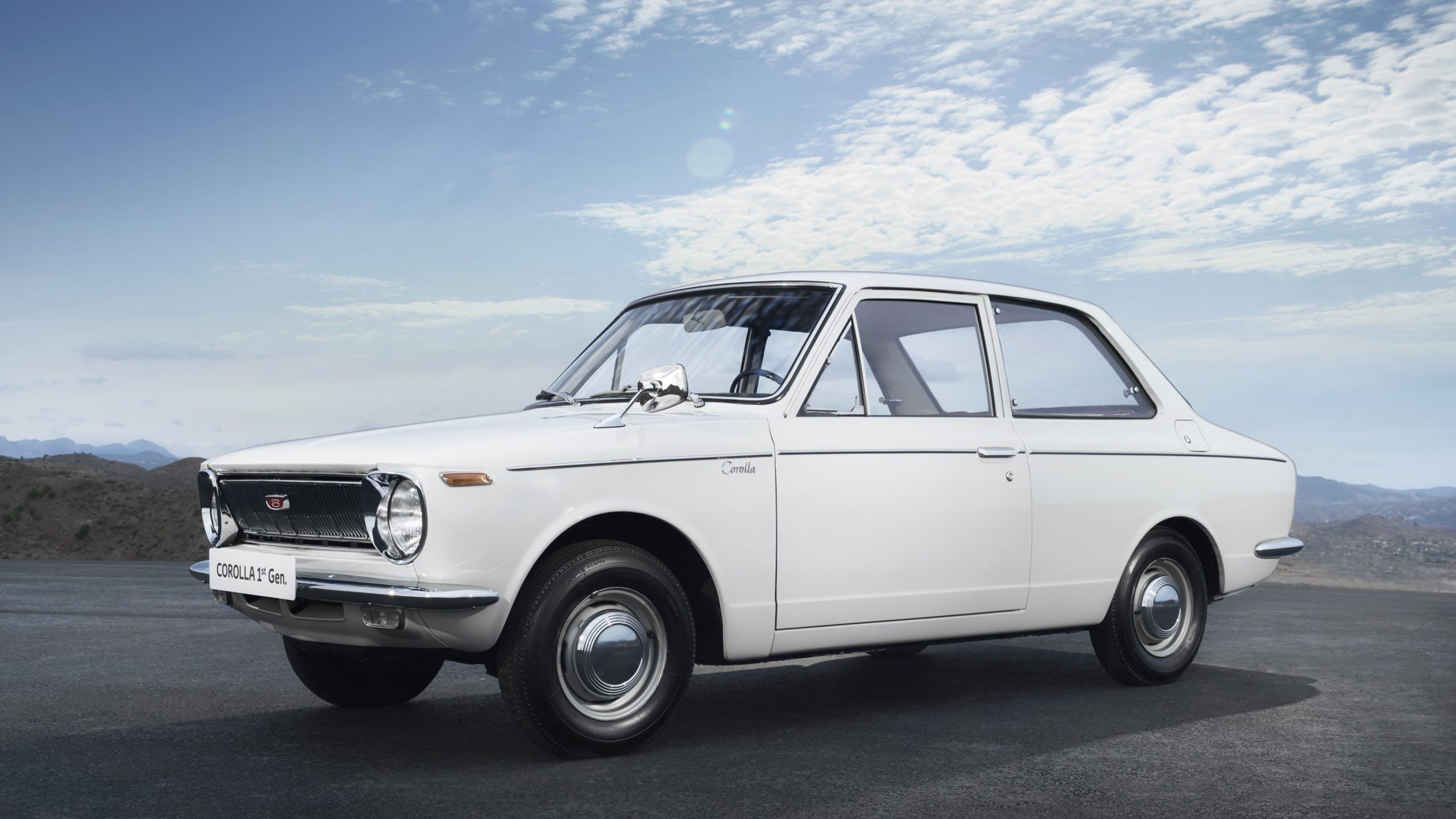
Parts availability further enhances the Corolla’s DIY appeal. Given Toyota’s global market penetration and the Corolla’s immense production numbers, compatible components remain widely available at reasonable prices through both traditional auto parts stores and online retailers.
The aftermarket ecosystem supports virtually every repair scenario, from routine maintenance to major system overhauls. The extensive ownership community represents perhaps the Corolla’s greatest advantage for DIY repairers.
The vehicle’s electrical systems also reflect an era before the complex computerization that complicates modern repairs. With relatively simple wiring harnesses and fewer electronic control modules, electrical troubleshooting remains accessible even without specialized diagnostic equipment.
The OBD-II system in later models strikes an ideal balance – providing useful diagnostic information without the proprietary complexity of newer vehicles.
2. Jeep Wrangler TJ (1997-2006)
The Jeep Wrangler TJ generation represents the golden era of DIY-friendly 4×4 vehicles, combining rugged simplicity with unprecedented accessibility. This model strikes the perfect balance between modern reliability and old-school repairability, making it an ideal platform for home mechanics and off-road enthusiasts alike.
What immediately distinguishes the TJ is its straightforward body-on-frame construction and exposed components. Unlike unibody vehicles with integrated structures, the TJ’s separate frame allows for easier access to suspension, drivetrain, and steering components.
The removable body panels further enhance accessibility – simply removing the hood provides unrestricted access to the entire engine bay, while detachable fenders facilitate wheel and brake work without contortion.
The 4.0L inline-six engine powering many TJ models ranks among the most reliable and repair-friendly powerplants ever produced. Its linear design features accessible spark plugs, straightforward belt routing, and adequate workspace around critical components.
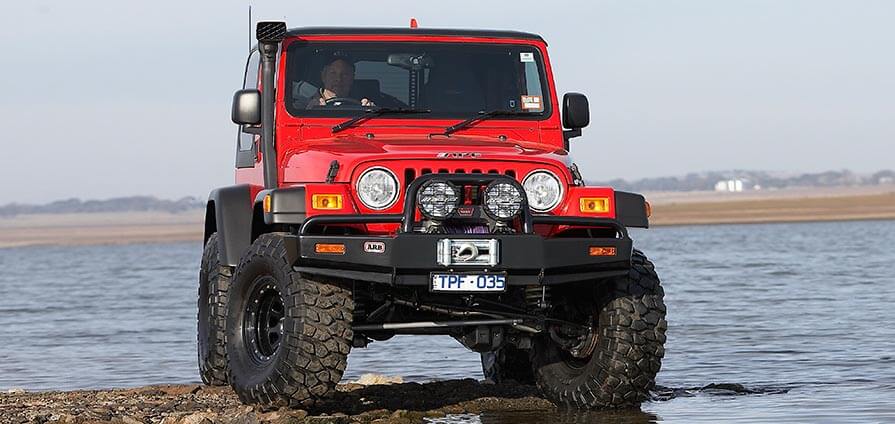
The engine’s low-pressure fuel injection system and relatively simple electronics make diagnosis and repair manageable without specialized equipment. Even major procedures like head gasket replacements are straightforward compared to modern V-configuration engines.
The TJ’s mechanical systems extend this DIY-friendly approach throughout the vehicle. The manual transmission and transfer case features conventional designs with serviceable components, while the solid front and rear axles eliminate the complexity of independent suspension.
Basic hand tools are sufficient for most repairs, and the vehicle’s robust construction forgives occasional amateur mistakes that might damage more delicate modern designs.
Perhaps most valuable to DIY mechanics is the unparalleled Jeep community support. Countless forums, YouTube channels, and specialized websites offer step-by-step guidance for virtually every repair scenario.
Detailed upgrade paths, common problem fixes, and troubleshooting guides have been refined through decades of collective experience. The standardized nature of many TJ components means that aftermarket support remains robust, with affordable replacement parts readily available through multiple channels.
3. Honda Civic (1990s-Early 2000s)
The Honda Civic from the 1990s through the early 2000s particularly the fifth, sixth, and seventh generations established itself as one of the most DIY-friendly vehicles ever produced.
These models combined Honda’s engineering excellence with exceptional accessibility, creating a platform that continues to serve as an ideal entry point for aspiring home mechanics.
The Civic’s engine bay exemplifies intelligent design with remarkable accessibility. Critical maintenance components like the oil filter, spark plugs, and air filter are positioned with clear access paths, while the compact four-cylinder engine leaves ample working space around its perimeter.
The D-series and B-series engines found in these models feature non-interference designs in many cases, reducing catastrophic damage risk during timing belt failures a forgiving characteristic for DIY mechanics learning belt replacement procedures.
Honda’s approach to fasteners and assembly further enhances the DIY experience. Components typically connect with standard metric bolts in logical patterns, while color-coded electrical connectors simplify reassembly.
The Civic’s wiring harnesses follow intuitive routing with accessible connection points, making electrical troubleshooting significantly more approachable than in many contemporary vehicles.

Parts interchangeability represents another significant advantage. The extensive production numbers and Honda’s component standardization across multiple models mean that salvage yard parts often fit without modification.
The massive aftermarket support ecosystem ensures that replacement components remain affordable and widely available, whether seeking OEM-equivalent parts or performance upgrades.
This collective knowledge allows owners to approach even complex repairs with confidence, following proven methods refined by countless owners.
The vehicle’s fundamental reliability paradoxically enhances its DIY appeal while major failures are uncommon, the predictable wear patterns and well-documented maintenance requirements create perfect learning opportunities without constant emergency repairs.
Even the dashboard warning systems strike a user-friendly balance, providing meaningful diagnostic information without requiring proprietary scan tools for basic troubleshooting.
4. Ford F-150 (1980s-2000s)
The Ford F-150 trucks from the 1980s through the early 2000s established themselves as DIY repair champions through a combination of straightforward design, massive production numbers, and unparalleled parts availability.
These workhorses particularly the ninth (1992-1996) and tenth (1997-2003) generations offer home mechanics an ideal balance of modern features and accessibility.
At the heart of the F-150’s DIY appeal lies its traditional body-on-frame construction with a spacious engine bay. Whether housing the bulletproof 4.9L straight-six, the ubiquitous 5.0L V8, or the later modular V8 engines, these trucks provide generous working room around critical components.
Basic maintenance procedures require minimal specialized tools oil changes, spark plug replacements, and filter services can be completed with standard hand tools in comfortable working positions.
The truck’s raised stance creates another significant DIY advantage: substantial undercarriage accessibility without requiring a lift. Basic jack stands provide sufficient clearance for exhaust work, differential service, and driveshaft maintenance.
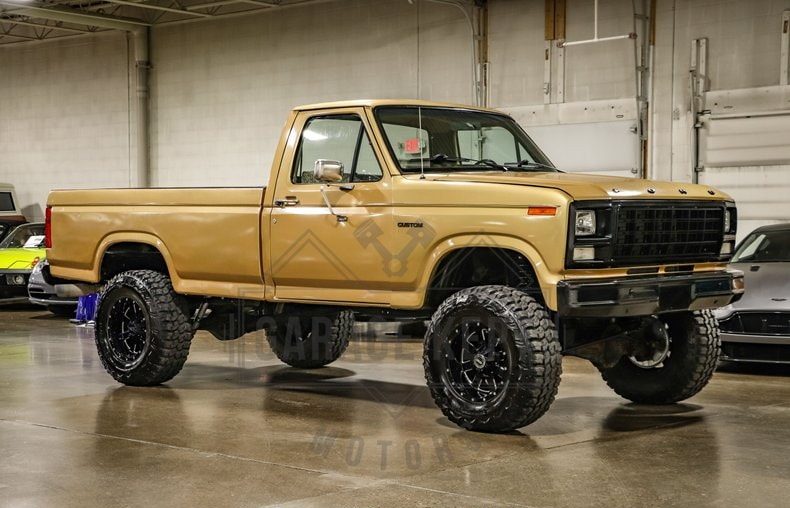
The separate frame construction allows for straightforward suspension component replacement, while the solid rear axle eliminates the complexity found in independent rear suspension systems.
The F-150’s electrical systems reflect an era before over-computerization. While offering useful features like OBD-II diagnostics in later models, these trucks maintain relatively simple electrical architectures that home mechanics can troubleshoot using basic multimeters.
Wiring harnesses follow logical routing with accessible connection points, and critical components like alternators, starters, and ignition modules can be replaced with minimal specialized knowledge.
Perhaps the F-150’s greatest advantage lies in its unmatched parts ecosystem. As America’s best-selling vehicle for decades, compatible components remain available through multiple channels from dealerships and auto parts chains to salvage yards and specialized online retailers.
The aftermarket support is exceptional, with repair parts ranging from budget-friendly options to premium replacements for virtually every component. The knowledge base surrounding these trucks is equally impressive.
Dedicated forums like Ford-Trucks.com host thousands of detailed repair guides, while printed manuals like the Haynes and Chilton series provide comprehensive coverage. The standardized nature of many repairs across multiple model years means that instructions often apply to entire generations with minimal adaptation required.
Also Read: 12 Trucks Compared for Best Fuel Economy Under Heavy Loads
5. Volkswagen Beetle (Air-cooled Models)
The classic air-cooled Volkswagen Beetle stands as perhaps the definitive DIY-friendly vehicle, earning its reputation through an ingenious simplicity that modern automotive engineers have largely abandoned.
Produced from 1938 through 2003 (in Mexico), these iconic vehicles were explicitly designed with home maintenance in mind during an era when professional service wasn’t always available.
The Beetle’s rear-mounted, air-cooled engine represents a masterpiece of accessible engineering. With just four cylinders, no water pump, no radiator, and remarkably few moving parts, the powerplant can be maintained with basic hand tools and fundamental mechanical knowledge.
The entire engine can be removed by disconnecting just four bolts and a few cables a procedure many owners perform in their driveways without specialized equipment. This modularity extends to major components like the transmission, which can be separated from the engine in under an hour with basic tools.
Parts standardization across decades of production creates another significant advantage. A carburetor from a 1960s model often fits directly onto a 1970s engine, while many body panels remain interchangeable across multiple years.
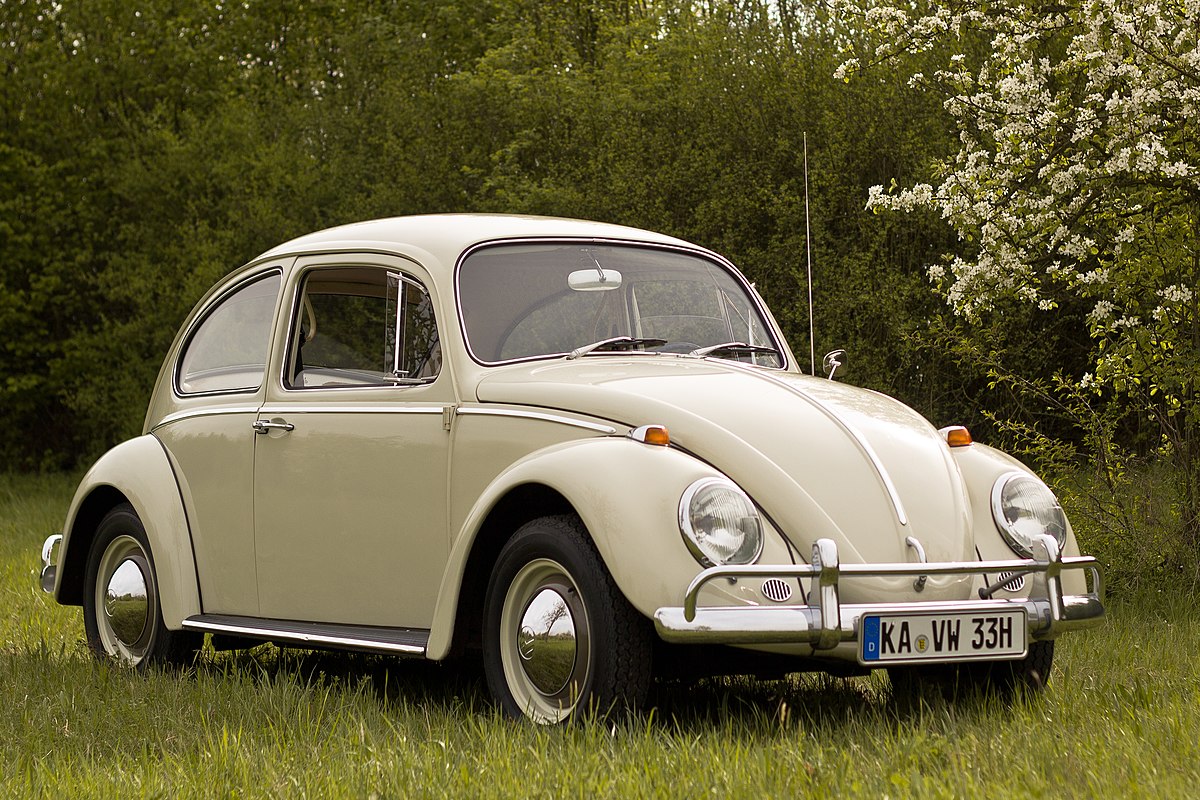
This standardization fostered the development of one of the most robust aftermarket parts networks in automotive history. From complete reproduction body panels to performance upgrades, virtually every component remains readily available at reasonable prices.
The Beetle’s electrical system exemplifies elegant simplicity with its 6-volt (early models) or 12-volt architecture using straightforward wiring routes that can be traced by hand.
A basic understanding of automotive electricity allows owners to diagnose and repair most issues without specialized equipment. The absence of computers, complex sensors, or multiplexed systems means that electrical problems remain fundamentally mechanical in nature loose connections, worn components, or basic circuit issues rather than software glitches.
6. Toyota Tacoma (First Generation, 1995-2004)
The first-generation Toyota Tacoma earned its reputation as a DIY-friendly vehicle through Toyota’s legendary reliability combined with thoughtful design choices that prioritize serviceability.
This mid-sized pickup offers an ideal platform for home mechanics seeking a balance between modern features and straightforward repairability. The Tacoma’s engine bay exemplifies intelligent engineering with generous access to critical components.
Whether equipped with the efficient 2.4L four-cylinder or the more powerful 3.4L V6, these engines feature logically arranged service points with clear approaches.
Regular maintenance items like oil filters, spark plugs, and belts can be accessed without elaborate disassembly procedures. The V6 engine, while more complex than the four-cylinder, still maintains reasonable accessibility for common repairs like valve cover gasket replacements or starter motor swaps.
The truck’s traditional body-on-frame construction creates substantial advantages for DIY maintenance. Its raised stance provides natural undercarriage access without specialized lifting equipment, while the separate frame allows straightforward replacement of suspension and steering components.
The solid rear axle design eliminates the complexity of independent rear suspension systems, making differential service and axle repairs approachable for home mechanics with basic tools.
Toyota’s commitment to component longevity means that many Tacomas require fewer repairs than comparable trucks of the era, but when service is necessary, parts availability remains exceptional.
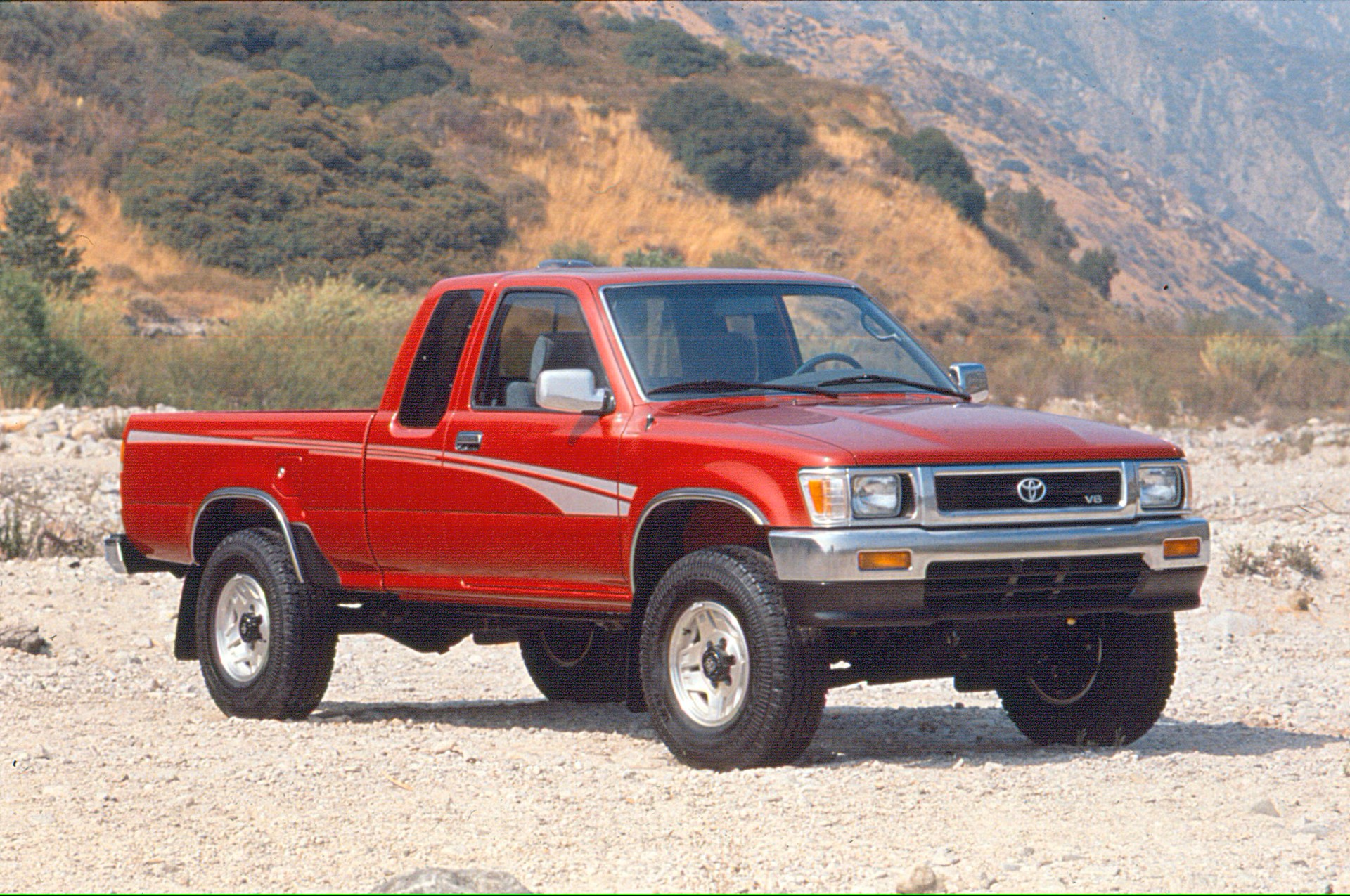
The global production numbers and Toyota’s practice of sharing components across multiple models ensure that replacement parts remain widely available through both OEM and aftermarket channels.
This generation shares many components with 4Runners and other Toyota trucks, further expanding the compatible parts ecosystem. The Tacoma community has developed comprehensive resources for DIY maintenance over decades of ownership.
This collective knowledge allows owners to approach even intimidating repairs with confidence, following tested methods refined by the community.
The truck’s electrical and fuel systems strike an ideal balance between functionality and simplicity. While offering modern features like fuel injection and engine management computers, these systems remain straightforward enough for home diagnosis and repair.
The OBD-II port in 1996 and later models provide useful diagnostic information without requiring expensive proprietary tools for basic troubleshooting.
7. Mazda Miata/MX-5 (NA/NB Generations, 1989-2005)
The first two generations of the Mazda Miata (known as the NA from 1989-1997 and NB from 1999-2005) represent nearly perfect platforms for DIY automotive maintenance.
These lightweight roadsters combine accessible engineering with remarkable component durability, creating an ideal learning environment for home mechanics of all experience levels.
The Miata’s engine bay design exemplifies thoughtful engineering with the 1.6L and 1.8L four-cylinder engines positioned longitudinally with generous surrounding space.
Critical maintenance points like oil filters, spark plugs, and belts remain clearly accessible without requiring contortion or special tools. The timing belt service often intimidating on other vehicles becomes straightforward with clear access to all components.
Even more complex procedures like cylinder head removal benefit from the engine’s compact design and logical component layout. The car’s fundamental simplicity extends throughout its systems.
The manual transmission offers textbook accessibility for clutch replacements, while the differential can be serviced without elaborate procedures.
The double-wishbone suspension design, while sophisticated in performance, uses conventional components that can be replaced individually without specialized alignment tools (though professional alignment remains recommended afterward).
Even the pop-up headlights on NA models, often complicated on other vehicles, use straightforward mechanical linkages that remain serviceable decades later.
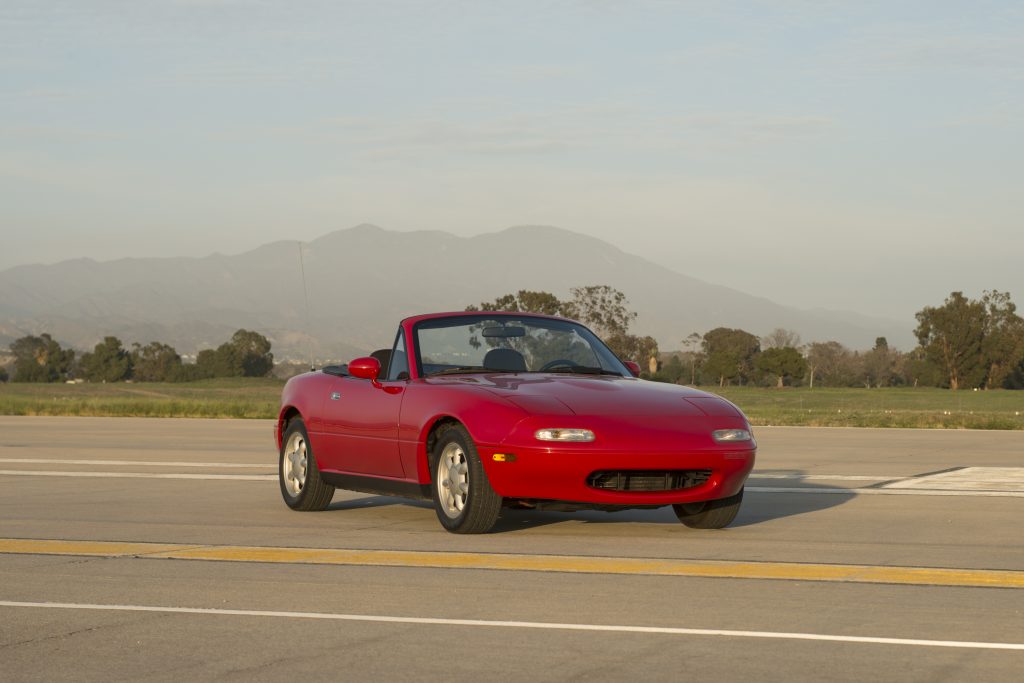
Parts availability represents another significant advantage for Miata owners. With over a million units produced across these generations and a dedicated enthusiast community, replacement components remain readily available through multiple channels.
The robust aftermarket support ranges from OEM-equivalent maintenance parts to performance upgrades for virtually every system. Salvage components often interchange directly between model years, creating additional sourcing options.
The standardized nature of many repairs across model years means that instructions often apply to both generations with minimal adaptation required.
The car’s electrical system strikes an ideal balance between functionality and simplicity. While offering modern features like fuel injection and engine management, these systems remain straightforward enough for home diagnosis and repair.
The absence of unnecessary complexity means that most electrical issues can be diagnosed using basic tools and logical troubleshooting rather than requiring specialized diagnostic equipment.
8. Chevrolet/GMC Trucks (1988-1998 GMT400 Platform)
The GMT400 platform trucks comprising the Chevrolet C/K series and GMC Sierra models from 1988 through 1998 represent perhaps the pinnacle of DIY-friendly design from General Motors.
These vehicles combine modern reliability with traditional accessibility, creating an ideal platform for home mechanics to handle everything from routine maintenance to major repairs.
The spacious engine bay design stands as one of the GMT400’s greatest advantages. Whether housing the bulletproof 5.7L V8, the efficient 4.3L V6, or other available powerplants, these trucks provide exceptional access to all engine components.
Spark plugs, valve covers, intake manifolds, and even cylinder heads can be serviced without the contortionist maneuvers required on many modern vehicles.
The thoughtful component placement extends to accessories like alternators, power steering pumps, and A/C compressors, which can typically be replaced with basic hand tools and without extensive disassembly.
The truck’s conventional body-on-frame construction creates substantial advantages for undercarriage maintenance. The raised stance provides natural access to the exhaust, drivetrain, and suspension components without requiring specialized lifts.
The solid front axle on 4×4 models and the straightforward independent front suspension on 2WD variants both use serviceable components with logical assembly sequences.
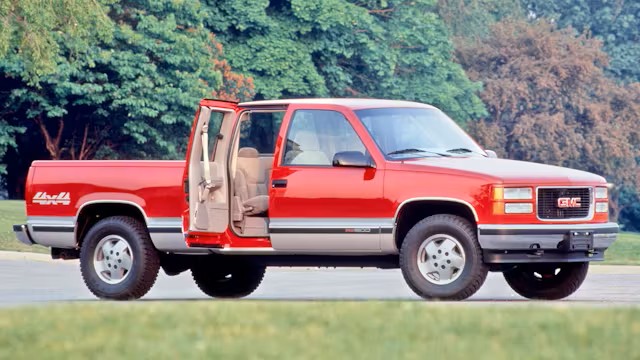
The rear leaf spring suspension eliminates the complexity found in coil-spring designs, making spring and shock replacement particularly straightforward.
Parts availability represents another significant advantage. As some of America’s best-selling vehicles during their production run, these trucks benefit from extensive aftermarket support.
Replacement components remain widely available through multiple channels from local auto parts stores to specialized online retailers and salvage yards.
The standardized nature of many components across multiple model years means that parts often interchange directly, expanding sourcing options significantly.
The electrical systems on these trucks reflect an era before excessive computerization. While offering modern features like fuel injection and basic engine management, they maintain accessible architectures that home mechanics can diagnose with fundamental knowledge and simple tools.
The introduction of OBD-II diagnostics in later models (1996+) provides useful information without requiring expensive proprietary equipment for basic troubleshooting.
The standardized nature of many repairs across multiple model years means that instructions often apply across the entire production run with minimal adaptation required.
9. Subaru Impreza/Legacy (1990s-Early 2000s)
The Subaru Impreza and Legacy models from the 1990s through the early 2000s offer a unique combination of modern all-wheel-drive technology and surprising DIY accessibility.
These vehicles particularly those equipped with the naturally-aspirated EJ series engines present home mechanics with logically designed systems that can be maintained without specialized equipment or dealer-only tools.
The horizontally opposed “boxer” engine layout, while distinctive, creates several DIY advantages once understood. The symmetrical design means that procedures learned on one side of the engine often apply identically to the opposite side, effectively halving the learning curve for many repairs.
While the low, wide configuration does present challenges for certain procedures, particularly spark plug replacement, the engine bay generally provides adequate access to critical maintenance points.
Oil changes, filter replacements, and belt services can be performed with standard tools in reasonable working positions. Subaru’s approach to component standardization creates another significant advantage.
Many parts from sensors and electrical connectors to suspension components remain consistent across multiple models and years, allowing repair knowledge to transfer between vehicles.
The all-wheel-drive system, while sophisticated in performance, uses relatively straightforward mechanical principles with serviceable components. Even the manual transmissions and transfer systems can be maintained without specialized equipment beyond basic hand tools.
Parts availability remains excellent due to Subaru’s practice of evolutionary rather than revolutionary design changes. Many components interchange between multiple model years, creating a vast compatible parts ecosystem that spans nearly a decade of production.
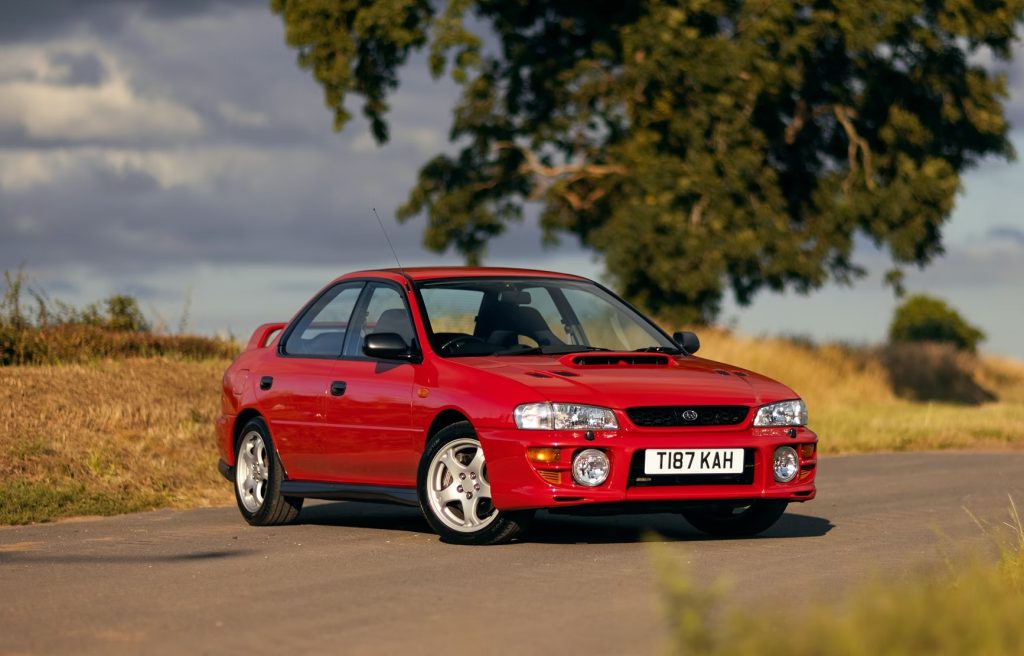
The aftermarket support ranges from OEM-equivalent maintenance parts to performance upgrades for virtually every system, while salvage components often transfer directly between compatible models.
The electrical systems in these vehicles strike an ideal balance between functionality and accessibility. While offering modern features like multiport fuel injection and engine management computers, these systems maintain logical architectures that can be diagnosed using basic tools and methodical approaches.
The OBD-II diagnostic capabilities in 1996 and later models provide useful information without requiring expensive proprietary scanners for most basic troubleshooting.
10. Mercedes-Benz W123 Series (1976-1985)
The Mercedes-Benz W123 series comprising sedan (240D, 300D, etc.), coupe, and wagon variants represents perhaps the pinnacle of German engineered serviceability.
These vehicles were designed during an era when Mercedes prioritized longevity and repairability above all else, creating what many consider the most durable passenger cars ever produced.
What immediately distinguishes the W123 from modern vehicles is its fundamentally mechanical nature. The diesel variants in particular especially the legendary OM617 five-cylinder turbodiesel operate with minimal electronics and remarkable accessibility.
These engines were explicitly designed for service intervals measured in hundreds of thousands of miles, with features like adjustable valves, serviceable injection pumps, and accessible glow plug systems.
The simplified fuel delivery systems eliminate the complexity of electronic fuel injection, allowing home mechanics to perform most maintenance with basic tools and fundamental understanding.
The vehicle’s construction follows a philosophy of deliberate accessibility. Components are generally fastened with standard metric bolts in logical patterns, while service points are positioned with clear access paths.
The engine bay provides adequate working space around the inline engines, whether diesel or gasoline powered. Even seemingly complex procedures like valve adjustments become straightforward exercises in precision rather than challenges of accessibility.
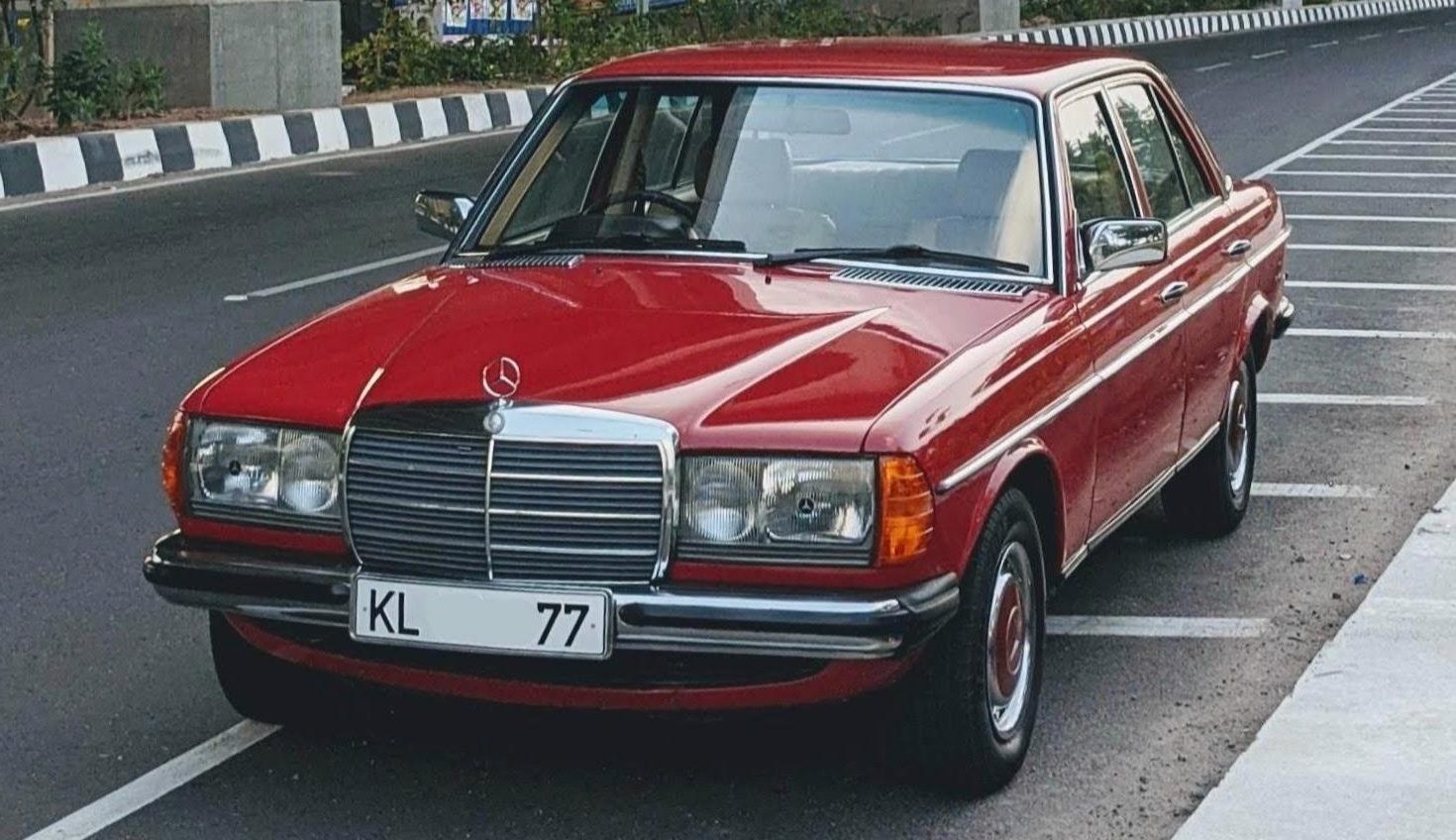
Mercedes’ approach to documentation further enhances the DIY experience. The factory service manuals for these vehicles set new standards for clarity and detail, with exceptional illustrations and precise procedures for virtually every repair scenario.
These resources have been supplemented by decades of enthusiast-generated content, creating comprehensive guidance for everything from routine maintenance to complete restorations.
Parts availability remains remarkable for vehicles of this age. Mercedes-Benz continues to manufacture many original components through its Classic Center, while a robust network of independent specialists provides both new and refurbished parts.
The vehicle’s global popularity ensures that salvage components remain available through specialized dismantlers, while pattern parts manufacturers offer cost-effective alternatives for many worn items.
The W123’s electrical system exemplifies intelligent simplicity. While offering comfort features like power windows and central locking, these systems use straightforward relay-based architectures that can be diagnosed with basic tools and logical troubleshooting.
Wiring diagrams remain clear and consistent, with color-coded harnesses that follow intuitive routing throughout the vehicle. What truly distinguishes the W123 series is its fundamental durability.
Components were typically engineered to substantial safety margins, allowing them to withstand occasional maintenance lapses or amateur repair attempts without catastrophic failure. This forgiving nature creates an ideal learning platform for developing mechanics, as minor mistakes rarely result in major damage.
11. Volvo 240 Series (1975-1993)
The Volvo 240 series has earned legendary status among DIY mechanics for combining Swedish engineering excellence with remarkable accessibility during its nearly two-decade production run.
These vehicles available in sedan, wagon, and even coupe variants were designed during an era when Volvo prioritized straightforward serviceability alongside their trademark safety features.
The spacious engine bay design provides exceptional access to all powertrain components, whether housing the durable B21/B23 four-cylinder engines or the later B230 variants.
Critical maintenance points like oil filters, spark plugs, and ignition components can be accessed without elaborate disassembly procedures. Even major repairs like timing belt replacements or head gasket services benefit from logical component layouts and clear access paths.
The longitudinal engine mounting creates natural working channels on either side of the engine, while the relatively high hood line provides excellent vertical clearance.
Volvo’s approach to fasteners and assembly further enhances the DIY experience. Components typically connect with standard metric bolts in logical patterns, while color-coded electrical connectors simplify reassembly.
The wiring harnesses follow intuitive routing with accessible junction points, making electrical troubleshooting significantly more approachable than in many contemporary vehicles.
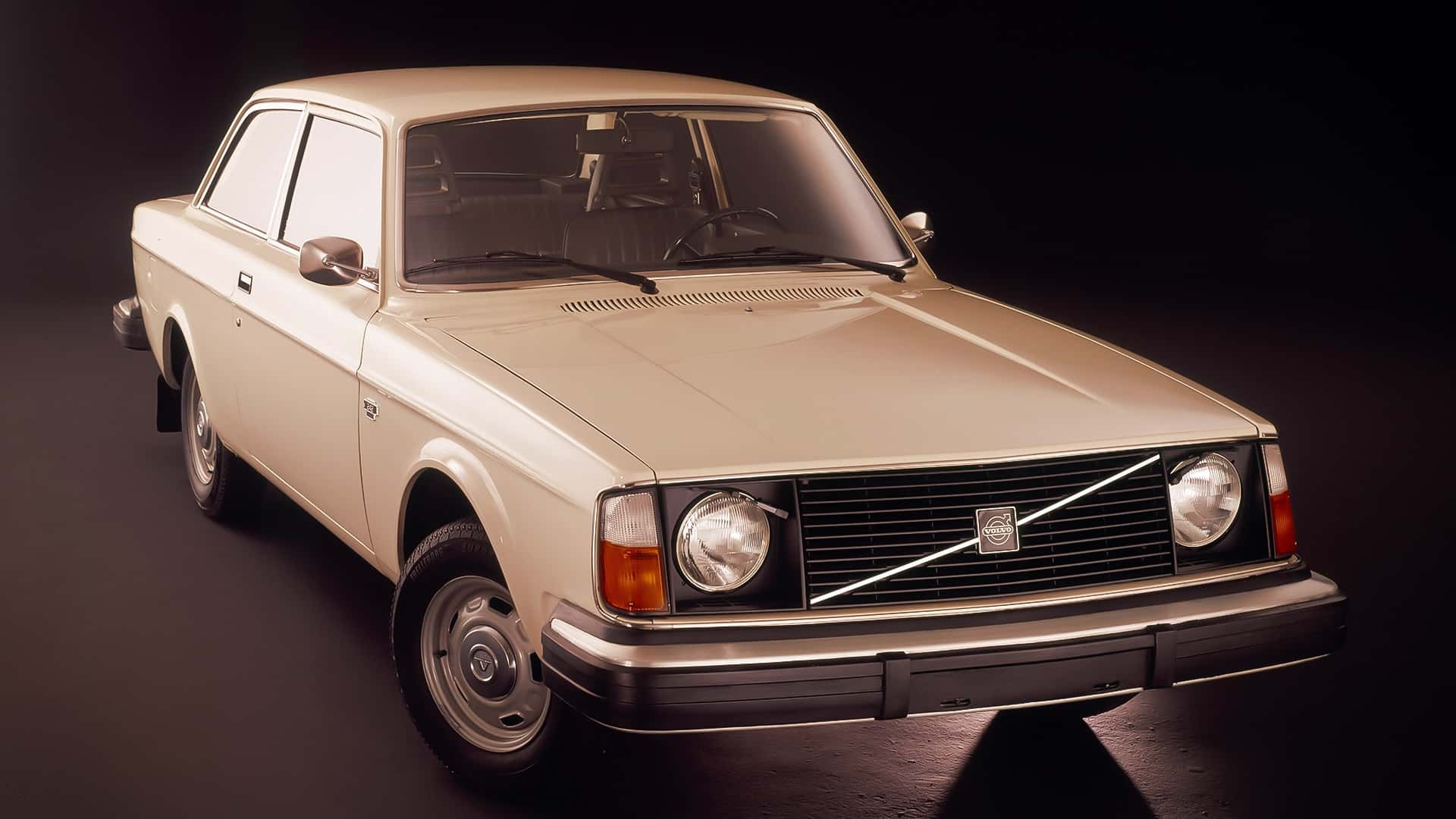
The 240’s fundamental mechanical nature represents perhaps its greatest advantage for home mechanics. The K-Jetronic fuel injection system on many models uses mechanical rather than electronic principles, allowing diagnosis through pressure testing rather than requiring electronic interfaces.
The ignition systems remain similarly accessible, with external coils and straightforward distributor assemblies that can be serviced with basic tools and fundamental understanding.
Parts availability remains exceptional for vehicles of this age. Volvo maintained remarkable parts standardization across the production run, with many components interchanging directly between model years spanning more than a decade.
The global popularity of the 240 series ensures that both OEM and aftermarket components remain widely available through multiple channels, from specialized Volvo parts suppliers to general European auto parts retailers and even salvage sources.
Perhaps most importantly, the 240 series embodies a philosophy of design transparency. Systems follow logical principles with clear cause-and-effect relationships, allowing owners to develop genuine understanding rather than simply following prescribed procedures. This characteristic creates an ideal educational platform for developing mechanical skills that transfer to other vehicles.
12. Honda CRX/Civic Hatchback (1988-1991)
The Honda CRX and related Civic hatchbacks from the fourth generation (1988-1991) represent perhaps the ideal entry point into automotive DIY maintenance. These lightweight, efficient vehicles combine exceptional reliability with unparalleled accessibility, creating perfect platforms for building mechanical confidence and practical skills.
The engine bay design exemplifies Honda’s engineering brilliance from this era. Whether equipped with fuel-efficient D-series engines or more performance-oriented B-series powerplants, these vehicles feature logically arranged components with generous access space.
Critical maintenance points like oil filters, spark plugs, and ignition components can be reached without contortion or special tools. Even more involved procedures like timing belt replacements benefit from clear visual and physical access to all relevant components.
The vehicle’s fundamental simplicity extends throughout its systems. The manual transmission offers textbook accessibility for clutch replacements, while the suspension components use conventional designs that can be serviced with basic hand tools.
The front-wheel-drive layout eliminates the complexity of driveshafts, transfer cases, and differential systems found in many larger vehicles. Even the brake system follows straightforward principles with accessible components that make pad replacements and fluid changes ideal learning experiences for novice mechanics.
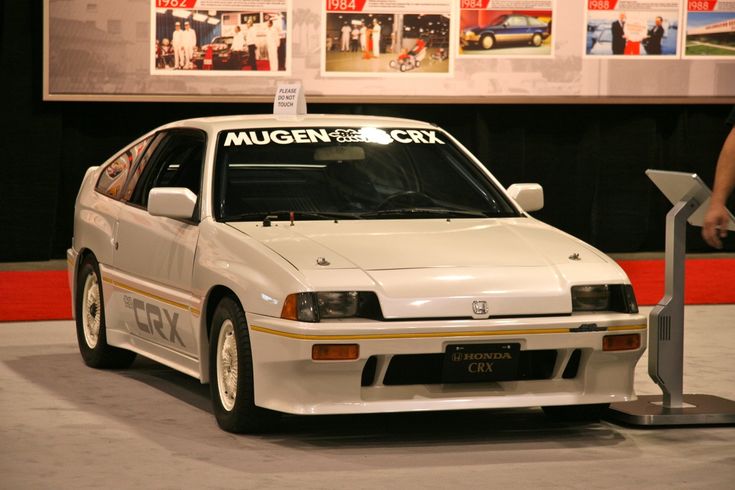
The electrical systems in these Honda models represent a perfect middle ground between functionality and simplicity.
While offering modern features like fuel injection and engine management, these systems maintain logical architectures that can be diagnosed using basic tools and methodical approaches.
The wiring harnesses follow intuitive routing with color-coded connectors that simplify troubleshooting and repair. Many models predate the OBD-II standard, using simpler diagnostic systems that communicate through blink codes rather than requiring specialized scanners.
Parts availability remains exceptional despite the vehicle’s age. Honda’s practice of component sharing across multiple models ensures that compatible parts remain widely available through both OEM and aftermarket channels.
The massive enthusiast community has driven the development of an extensive aftermarket ecosystem, offering everything from maintenance components to performance upgrades for virtually every system.
Perhaps most importantly, these Honda models embody a philosophy of design transparency. Systems follow logical principles with clear cause-and-effect relationships, allowing owners to develop genuine understanding rather than simply following prescribed procedures.
This characteristic creates an ideal educational platform for developing mechanical skills that transfer to other vehicles and practical applications.
Also Read: 12 Cars That Real Estate Agents Depend On For Travel