In the automotive industry, warranty claims serve as a crucial indicator of vehicle quality and reliability. When customers experience fewer issues requiring warranty service, it not only speaks to the durability of the vehicles but also indicates superior manufacturing processes and quality control measures.
Today’s car buyers increasingly prioritize long-term dependability alongside traditional factors like performance, design, and fuel efficiency. Manufacturers with minimal warranty claims typically enjoy stronger customer loyalty, enhanced brand reputation, and lower operational costs associated with honoring warranty services.
These brands have demonstrated consistent excellence in engineering and production standards, often investing heavily in rigorous testing protocols and quality assurance systems. Their commitment to reliability manifests in vehicles that maintain functionality with minimal intervention over extended periods.
This analysis examines the ten automotive brands with the fewest warranty claims, highlighting their achievements in delivering dependable vehicles to consumers.
By exploring each manufacturer’s approach to quality control, engineering philosophy, and technological implementation, we gain valuable insights into what constitutes truly reliable automotive manufacturing in today’s competitive market.
1. Lexus
Lexus has consistently maintained its position as an industry leader with the fewest warranty claims, setting a gold standard for automotive reliability. As Toyota’s luxury division, Lexus benefits from its parent company’s renowned manufacturing principles while raising quality control to even more exacting standards.
The brand’s remarkable reliability stems from a multi-faceted approach to vehicle development and production that prioritizes durability at every stage. Central to Lexus’s success is its adherence to the “Takumi” philosophy, where master craftsmen with decades of experience oversee production.
These highly skilled artisans inspect components with extraordinary precision, often detecting flaws invisible to the untrained eye or automated systems. This human element of quality control complements advanced manufacturing technology, creating a harmonious balance that consistently delivers exceptional results.
Lexus implements a conservative engineering approach that favors proven technology over cutting-edge but untested innovations. New features and systems undergo exhaustive testing, often for years longer than industry averages, before incorporation into production models.
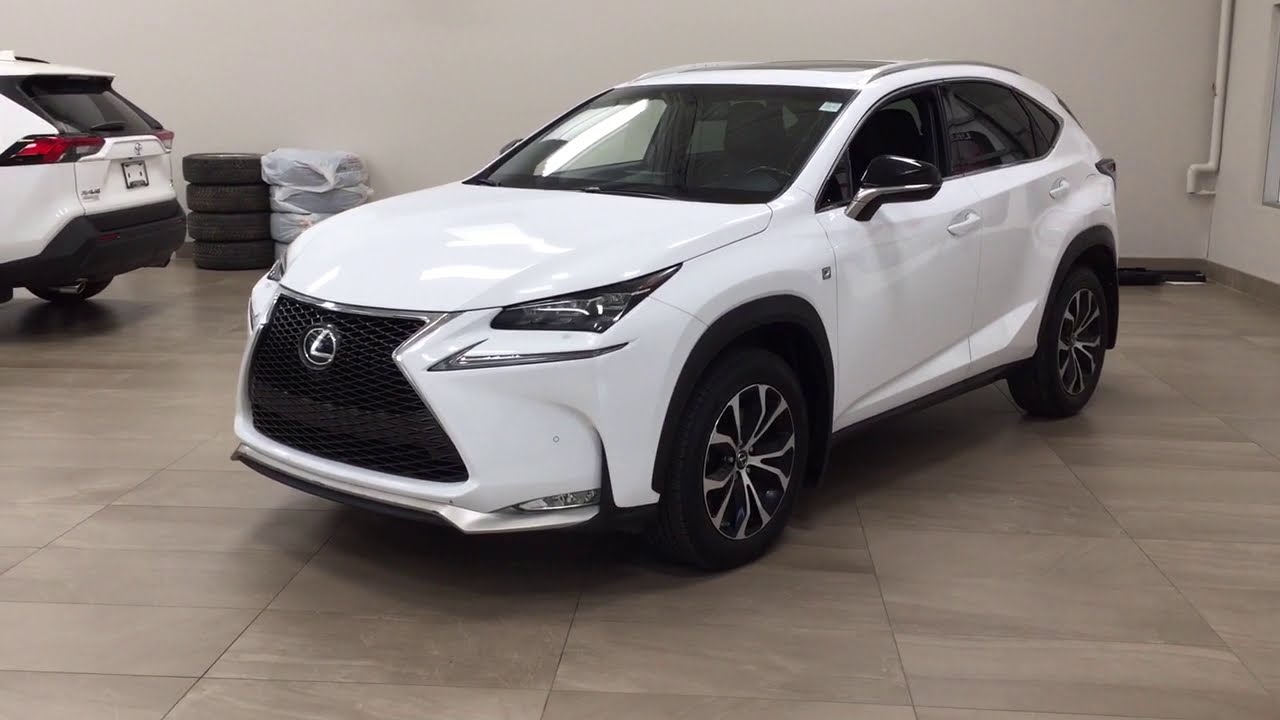
This methodical process ensures that when innovations reach consumers, they’ve been thoroughly vetted for long-term reliability. The brand’s manufacturing facilities maintain extraordinarily strict tolerance standards, with components often required to meet specifications tighter than industry norms.
Assembly line processes incorporate multiple inspection points, with vehicles subjected to comprehensive testing before leaving the factory. This includes water testing for leaks, road simulations for suspension and noise issues, and detailed electronic diagnostics.
Lexus also implements a proactive approach to potential problems through its field monitoring system, which collects real-world performance data. This allows engineers to identify and address emerging issues before they become widespread concerns.
When combined with meticulous maintenance schedules designed to prevent problems rather than address them reactively, the result is vehicles that simply require fewer warranty claims throughout their operational lifespans.
2. Toyota
Toyota’s remarkably low warranty claim rate stands as testament to the manufacturer’s unwavering commitment to its legendary production system and quality-first philosophy.
The Toyota Production System (TPS), often studied and emulated by manufacturers across industries, emphasizes continuous improvement (kaizen) and respect for people, creating a foundation for building exceptionally reliable vehicles with minimal defects requiring warranty service.
At the heart of Toyota’s approach is its jidoka principle, intelligent automation with human oversight, which empowers workers to stop production immediately when defects are detected.
This prevents flawed components from progressing through assembly, drastically reducing the likelihood of warranty-eligible issues reaching customers. Every Toyota employee is trained to function as a quality inspector, with the authority and responsibility to identify and address problems proactively.
Toyota’s engineering philosophy emphasizes evolutionary rather than revolutionary development. New technologies are typically tested extensively in controlled environments and then gradually implemented across the model lineup only after proving their reliability.
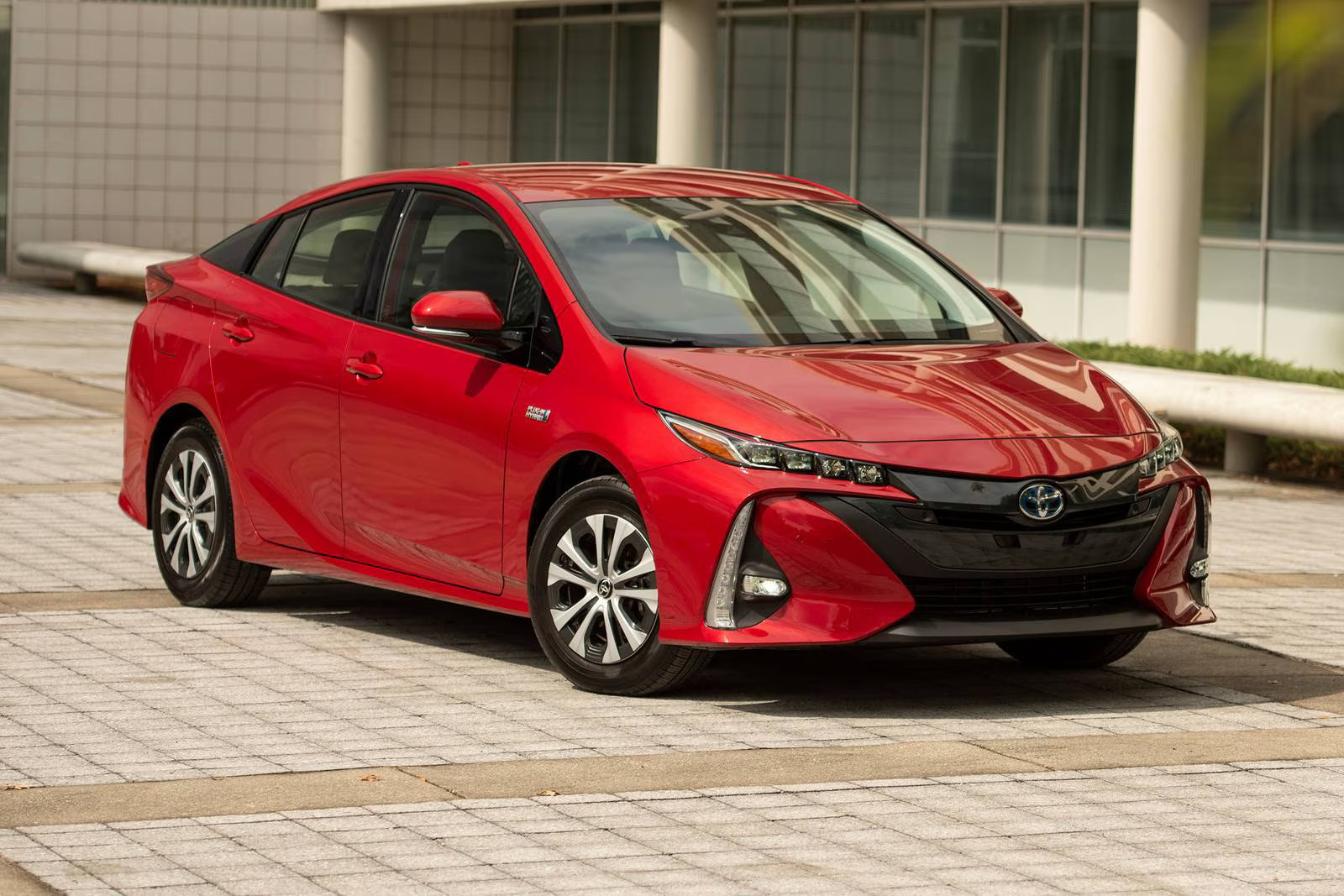
This measured approach contrasts with competitors who may rush innovations to market before their long-term dependability has been established. Each component undergoes rigorous validation testing, often exceeding industry standards by significant margins to ensure durability under extreme conditions.
The manufacturer’s global quality control standards ensure consistent production excellence across all facilities worldwide. Whether assembled in Japan, the United States, or elsewhere, Toyota vehicles adhere to identical quality benchmarks and manufacturing processes.
Advanced statistical quality control methods identify even minor deviations from specifications, allowing adjustments before issues manifest in completed vehicles. Toyota’s supplier relationships further bolster its reliability record.
The company works closely with parts manufacturers, providing training in TPS methods and maintaining strict quality requirements. Many suppliers have decades-long relationships with Toyota, creating an ecosystem of partners equally committed to minimizing defects.
This collaborative approach extends to comprehensive warranty data analysis, where patterns in the limited warranty claims that do occur inform continuous refinement of components and systems.
3. Porsche
Porsche has established an impressive record of minimal warranty claims through its meticulous approach to engineering and manufacturing excellence.
Despite producing high-performance vehicles that operate under demanding conditions, the German manufacturer maintains exceptional reliability standards that translate directly into fewer warranty-related issues for owners.
This remarkable achievement stems from Porsche’s unique combination of traditional craftsmanship and cutting-edge technological implementation.
The company’s Stuttgart and Leipzig production facilities operate on a principle of deliberate, measured assembly rather than volume-focused manufacturing.
Each Porsche vehicle undergoes significantly longer assembly times compared to mass-market brands, allowing for comprehensive inspection and testing at every production stage.
This methodical approach enables technicians to identify and address potential issues before vehicles leave the factory floor, substantially reducing the likelihood of warranty claims later in the ownership experience.
Porsche’s engineering philosophy emphasizes overengineered components designed to withstand stresses far exceeding typical operating conditions.
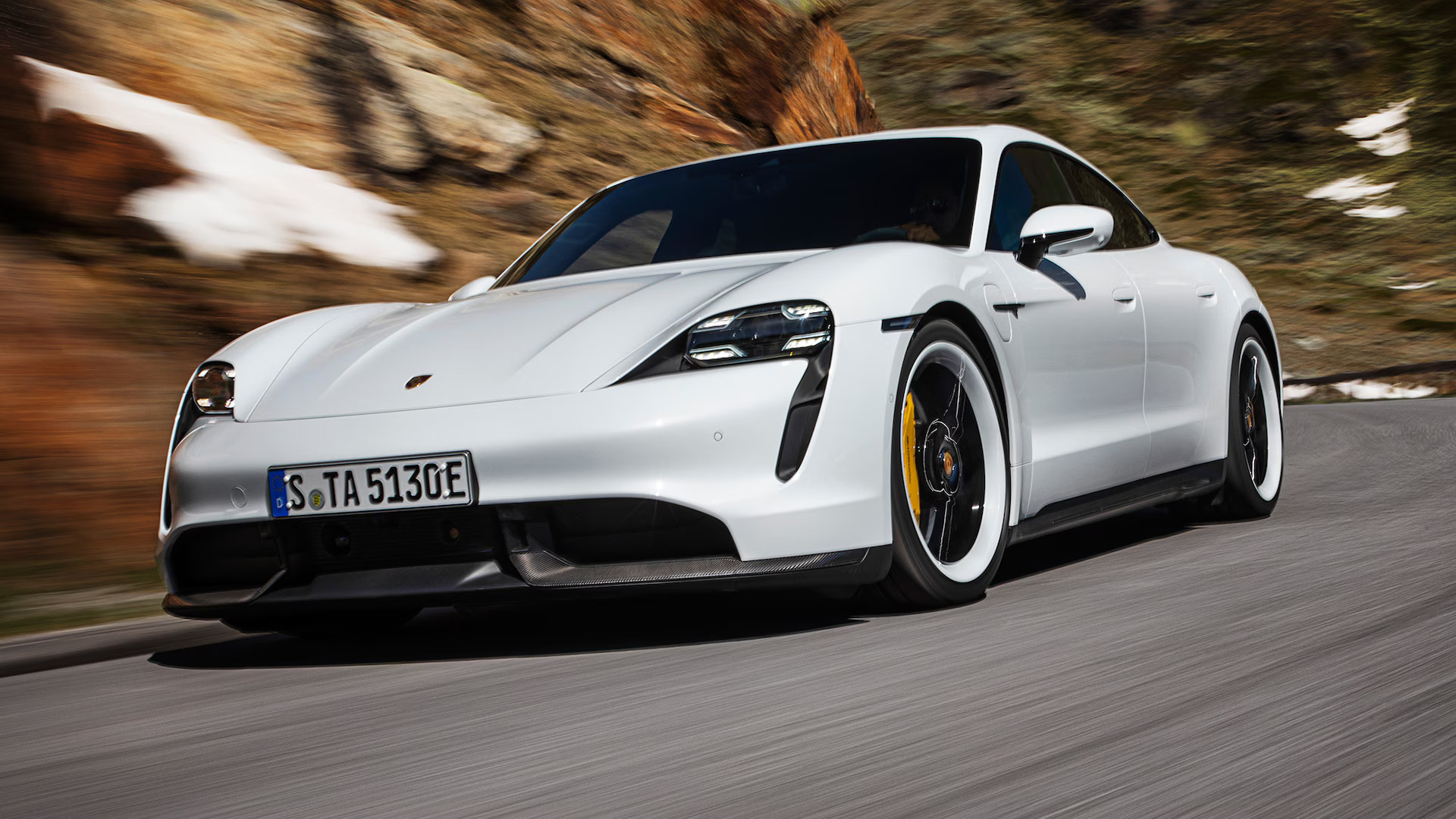
Engine and transmission assemblies, often the most warranty-prone vehicle systems, receive particular attention with enhanced cooling, strengthened internal components, and conservative tuning that prioritizes longevity alongside performance.
This approach creates substantial mechanical headroom that contributes significantly to long-term reliability even under enthusiastic driving conditions.
Material selection plays a crucial role in Porsche’s reliability equation. The company utilizes premium-grade alloys, composites, and electronics components, often sourced from specialized suppliers with extensive automotive experience.
These higher-specification materials command premium prices but yield dividends through extended durability and resistance to wear, corrosion, and thermal stress, all factors that typically drive warranty claims in performance vehicles.
Porsche’s comprehensive pre-delivery inspection process exceeds industry standards, with each vehicle undergoing extensive testing before reaching customers. This includes dynamic performance assessment on dedicated test tracks, simulated climate condition exposure, and exhaustive electronic systems verification.
The company also maintains a sophisticated data tracking system that monitors warranty trends across its global service network, allowing engineers to quickly identify and address emerging concerns before they affect significant numbers of vehicles.
This proactive approach to quality management helps Porsche maintain its position among manufacturers with the fewest warranty claims despite producing some of the market’s most technically complex vehicles.
4. Honda
Honda’s exceptionally low warranty claim rate stems from its deeply embedded philosophy of engineering excellence and systematic approach to quality control that permeates every aspect of vehicle development and production.
From initial concept to final assembly, Honda implements multiple layers of validation and verification that consistently deliver products requiring minimal warranty service over their lifespans. This achievement is particularly notable given the brand’s diverse product lineup spanning economy models to premium offerings.
At the foundation of Honda’s reliability is its rigorous design process that emphasizes simplicity and functional efficiency. Engineers prioritize straightforward, proven mechanical solutions over unnecessarily complex systems whenever possible, reducing potential failure points while maintaining performance standards.
When new technologies are introduced, they undergo exhaustive validation testing at Honda’s dedicated R&D facilities in Japan and North America, often accumulating millions of test miles before approval for production implementation.
Honda’s manufacturing protocol incorporates numerous quality checkpoints throughout the assembly process, with specialized teams dedicated to specific vehicle systems like powertrains, electronics, and chassis components.
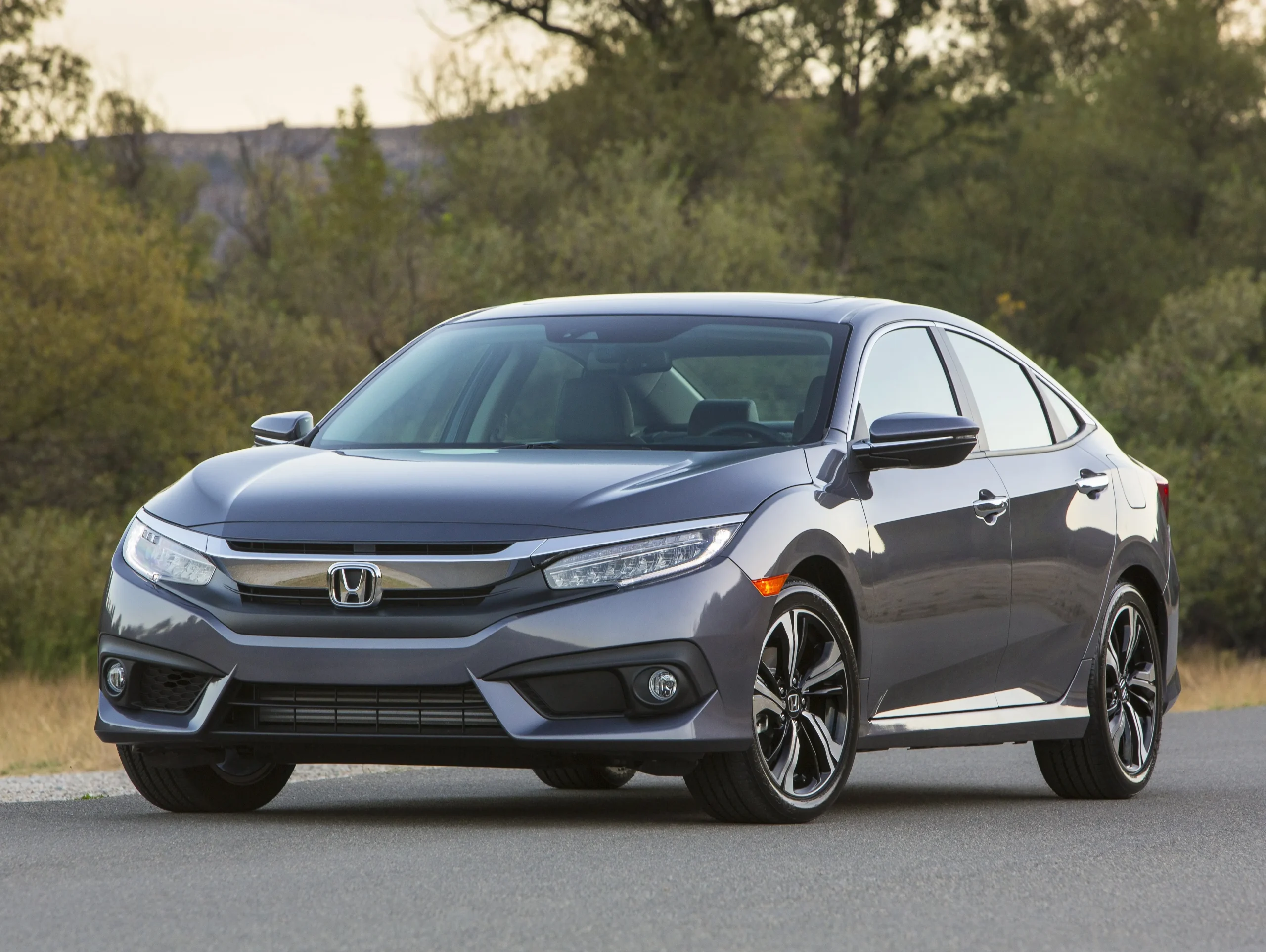
This specialized oversight enables early detection of potential issues that might otherwise manifest as warranty claims. The company maintains remarkable consistency across its global manufacturing network through standardized training and quality control methodologies, ensuring that a Honda assembled in Ohio meets identical quality benchmarks to one built in Japan.
Parts sourcing represents another critical element in Honda’s warranty performance. The company maintains exceptionally strict supplier certification requirements and typically develops long-term partnerships with component manufacturers.
Many key components, particularly those related to powertrains and critical vehicle systems, are produced in-house rather than outsourced, giving Honda complete control over quality standards for these crucial elements. This integrated approach to manufacturing helps eliminate the supplier inconsistency issues that often plague other manufacturers.
Honda further distinguishes itself through its comprehensive data collection and analysis system that monitors vehicle performance across global markets.
This feedback loop provides engineers with real-world information about how vehicles perform under diverse operating conditions, enabling continuous refinement of components and systems. When rare issues do arise, Honda has demonstrated a willingness to implement solutions promptly, often extending warranty coverage proactively rather than waiting for widespread claims.
This consumer-focused approach not only minimizes warranty claims but has helped establish Honda’s reputation as a brand committed to standing behind its products with integrity.
Also Read: 10 Japanese Cars That Outlive American and German Rivals
5. Mazda
Mazda has secured its position among manufacturers with the fewest warranty claims through a distinctive approach that balances innovative engineering with meticulous attention to long-term reliability.
Despite being a smaller automaker compared to many industry giants, Mazda has leveraged this relative agility into a significant advantage in quality control and consistency across its vehicle lineup.
The company’s focused model range allows for intensified quality oversight that directly translates into exceptional reliability metrics and minimal warranty service requirements.
Central to Mazda’s success is its holistic vehicle development philosophy that considers the entire ownership experience rather than just initial quality impressions.
The company implements what it calls “Monotsukuri Innovation,” an integrated approach where design, engineering, and manufacturing teams collaborate from the earliest development stages to identify and eliminate potential reliability concerns.
This process includes extensive computer modeling of component stress and wear patterns, followed by accelerated real-world durability testing that simulates years of usage in compressed timeframes.
Mazda maintains particularly strict production tolerances, especially for engine components, transmissions, and electronic systems areas traditionally prone to warranty claims across the industry.
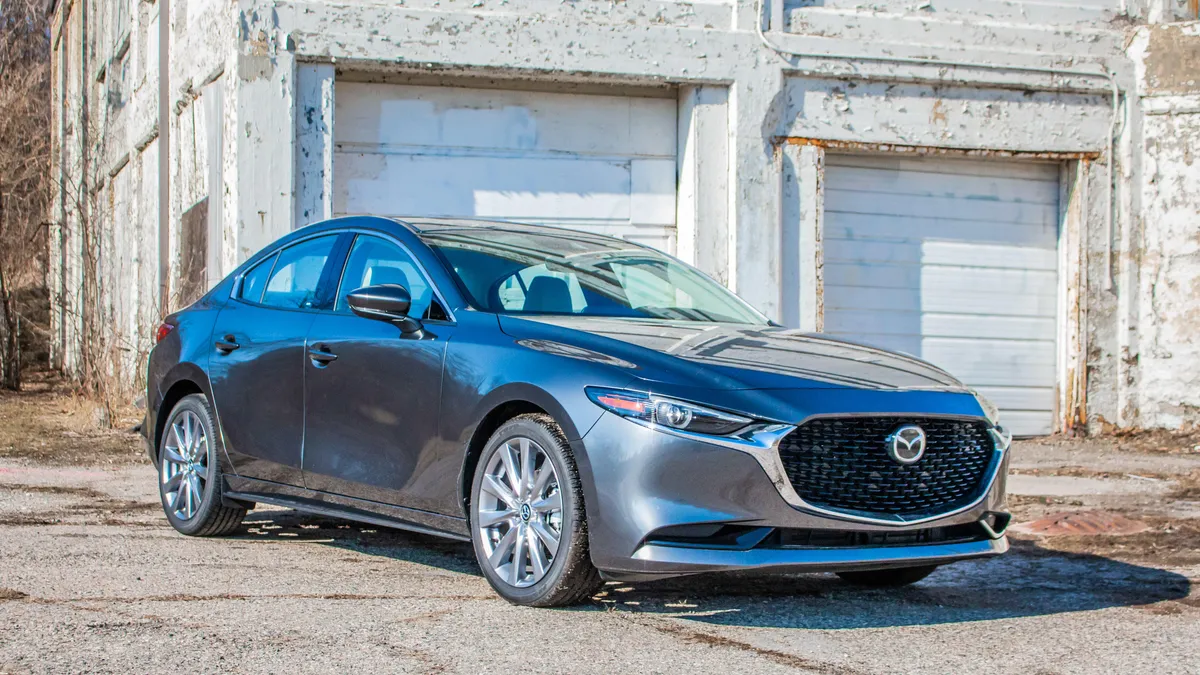
The manufacturer’s SkyActiv technology suite exemplifies this approach, with engines featuring precisely engineered components that operate with remarkably tight specifications while maintaining exceptional durability.
By focusing on fundamental engineering excellence rather than adding complex systems to compensate for underlying deficiencies, Mazda creates vehicles with inherent reliability advantages.
The company’s production facilities, particularly its flagship plants in Japan, implement a quality verification system that includes multiple inspection stages throughout assembly.
Vehicles undergo a comprehensive evaluation, including road simulation testing, water intrusion verification, and detailed electronic systems diagnostics, before receiving approval for shipment.
Mazda also implements a unique “craftsman approach” where specific assembly teams maintain responsibility for designated vehicle sections, fostering accountability and pride in workmanship that directly impacts quality outcomes.
Mazda further enhances its warranty performance through sophisticated data collection from its dealer service network. This information flows directly to engineering teams, creating a continuous improvement feedback loop that quickly identifies emerging patterns.
When potential concerns are detected, Mazda has demonstrated a willingness to implement preemptive solutions through service campaigns, often addressing issues before they generate significant warranty claims.
This proactive stance, combined with its fundamental engineering integrity and production discipline, enables Mazda to maintain its impressive position among manufacturers with minimal warranty service requirements despite lacking the enormous resources of larger automotive conglomerates.
6. Subaru
Subaru has earned its place among manufacturers with the fewest warranty claims through a distinctive combination of engineering conservatism, specialized production expertise, and a focused product development strategy.
Unlike brands that spread resources across diverse vehicle architectures, Subaru concentrates on refining a core set of technologies, particularly its signature boxer engines and symmetrical all-wheel-drive systems.
This specialized approach has allowed the company to develop extraordinary expertise in these areas, resulting in robust systems that demonstrate exceptional reliability despite operating in demanding conditions.
The company’s Gunma, Japan manufacturing complex serves as the centerpiece of its quality control program, maintaining production standards that significantly exceed industry averages.
Assembly line employees undergo extensive training in Subaru’s specialized manufacturing techniques, with many workers developing career-long expertise in specific vehicle systems.
This institutional knowledge creates an environment where subtle quality deviations are quickly identified and addressed before they can affect production vehicles. Subaru’s relatively modest production volume compared to industry giants allows for additional inspection time per vehicle, further enhancing quality outcomes.
Subaru implements an unusually rigorous component testing regime that subjects systems to extreme conditions far beyond typical customer usage.
Powertrains endure extended high-RPM operations, suspension components face accelerated impact testing, and electronic systems undergo thermal cycling that exceeds environmental extremes found in operational markets.
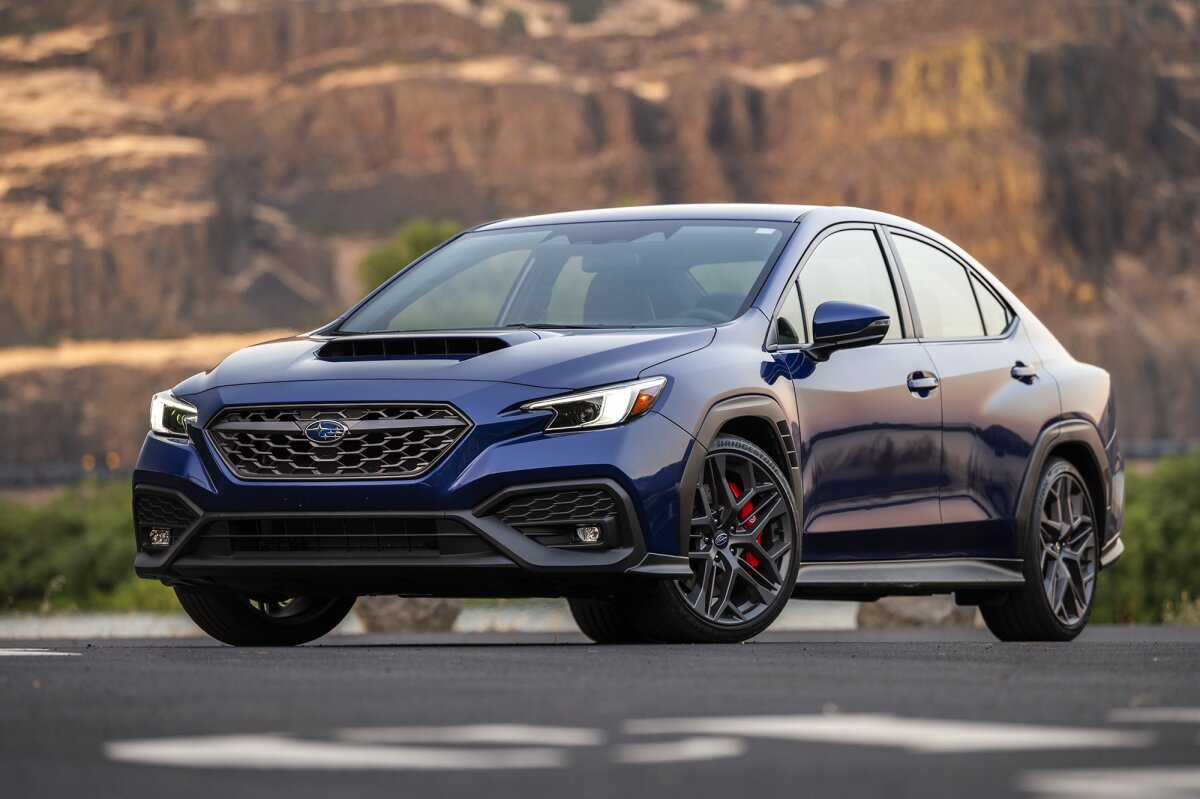
This “overbuilt” engineering philosophy creates substantial durability margins that translate directly to fewer warranty claims throughout vehicle lifespans.
Even components not directly related to performance receive similar attention, with interior materials, body seals, and ancillary systems designed to maintain functionality through extended service periods.
The company’s approach to technology implementation further strengthens its warranty performance. Subaru typically allows new technologies to mature in the marketplace before adoption, studying competitor implementations and identifying potential weaknesses before developing its solutions.
When innovations are introduced, they undergo extensive validation in controlled environments and limited production models before wider implementation across the vehicle lineup. This measured approach sometimes positions Subaru behind competitors in introducing cutting-edge features, but it consistently delivers superior long-term reliability as a result.
Subaru enhances its warranty performance through comprehensive dealer technician training programs that ensure proper diagnosis and repair procedures. This reduces repeat repair incidents that often inflate warranty claim statistics for other manufacturers.
The company also maintains detailed warranty tracking systems that analyze repair patterns across global markets, allowing engineering teams to quickly identify and address emerging concerns.
This combination of specialized expertise, concentrated product development, rigorous testing, and responsive service infrastructure enables Subaru to maintain its impressive position among manufacturers with minimal warranty service requirements despite producing vehicles designed for challenging operational environments.
7. Buick
Buick has transformed its reputation over the past decade, emerging as a standout performer with remarkably few warranty claims despite its historical struggles with reliability perception.
This dramatic improvement stems from a comprehensive overhaul of development processes, manufacturing standards, and quality control protocols implemented across General Motors’ global operations.
Buick’s success represents a case study in how focused quality initiatives can substantially raise reliability performance when consistently applied throughout an organization.
Central to Buick’s warranty claim reduction has been its implementation of the Global Vehicle Development Process (GVDP), a rigorous engineering methodology that emphasizes early problem detection and resolution.
This system incorporates multiple validation gates before designs progress to production, with each phase requiring specific reliability benchmarks to be met.
Particularly notable is Buick’s enhanced durability testing regimen that subjects pre-production vehicles to accelerated wear protocols simulating years of customer usage. These tests create detailed stress mappings that engineers use to reinforce components prone to fatigue or premature failure.
Manufacturing excellence forms another cornerstone of Buick’s reliability improvements. The brand’s production facilities have adopted sophisticated statistical process control methods that continuously monitor assembly variables, identifying subtle deviations that might impact long-term durability.
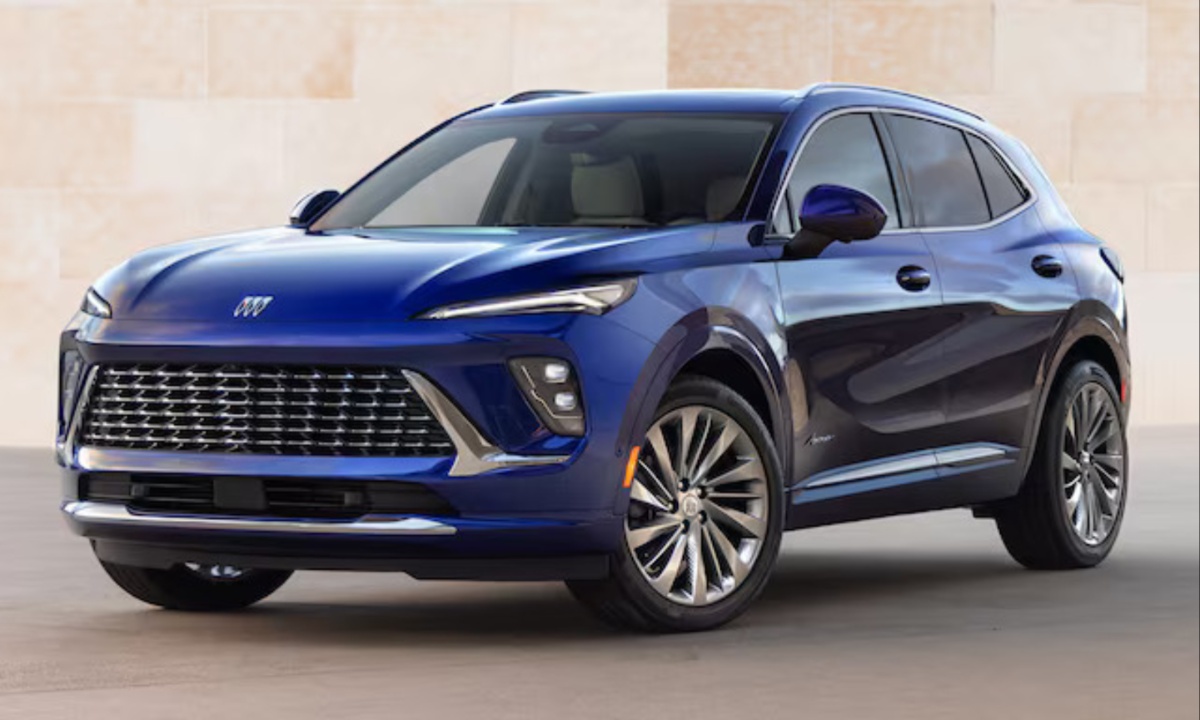
Buick has invested significantly in manufacturing precision, implementing enhanced tooling and assembly verification systems across production lines.
Assembly workers undergo specialized training programs focused on critical systems, creating workforce expertise in areas traditionally associated with warranty claims, such as electrical connections, fluid systems, and drivetrain integration.
Buick has also revolutionized its supplier quality management approach, implementing more stringent component validation requirements before parts receive approval for vehicle integration.
The company now maintains comprehensive component life-cycle testing facilities that subject individual parts to extreme operating conditions, identifying potential failure modes before they reach production vehicles. This enhanced supplier oversight has dramatically reduced component-related warranty claims that previously plagued the brand.
Perhaps most influential in Buick’s warranty performance transformation has been its implementation of sophisticated data analytics systems that monitor vehicle performance across dealer networks in real-time.
This early warning infrastructure allows engineering teams to identify emerging patterns and implement corrective actions before issues generate substantial warranty claims. When concerns are detected, Buick has demonstrated a willingness to implement preemptive service actions and extend coverage for potentially affected systems, addressing issues proactively rather than reactively.
This comprehensive approach spanning development, manufacturing, supplier management, and service operations has raised Buick from an average performer to one of the industry’s reliability leaders as measured by warranty claim frequency.
8. Acura
Acura has established itself among manufacturers with the fewest warranty claims through a sophisticated approach to engineering and quality assurance that leverages parent company Honda’s renowned reliability while adding additional premium-specific protocols.
As Honda’s luxury division, Acura benefits from foundational manufacturing excellence but implements enhanced quality control measures reflecting the raised expectations and complexity of luxury vehicles. This dual advantage creates a distinctive reliability profile that consistently delivers exceptional warranty performance across its product lineup.
The brand implements what it terms “Precision Crafted Performance” as more than a marketing slogan; it serves as a comprehensive development philosophy emphasizing meticulous attention to component durability alongside performance metrics.
Acura’s engineering teams operate with stricter reliability targets than those applied to mainstream Honda products, with particular focus on systems unique to luxury vehicles such as adaptive suspensions, advanced driver assistance technologies, and complex infotainment interfaces.
These systems undergo specialized validation processes designed to identify potential failure points under diverse operating conditions before receiving production approval.
Acura’s manufacturing protocol incorporates additional inspection stations beyond standard Honda processes, with specialized teams focused exclusively on premium-specific components and finish quality.
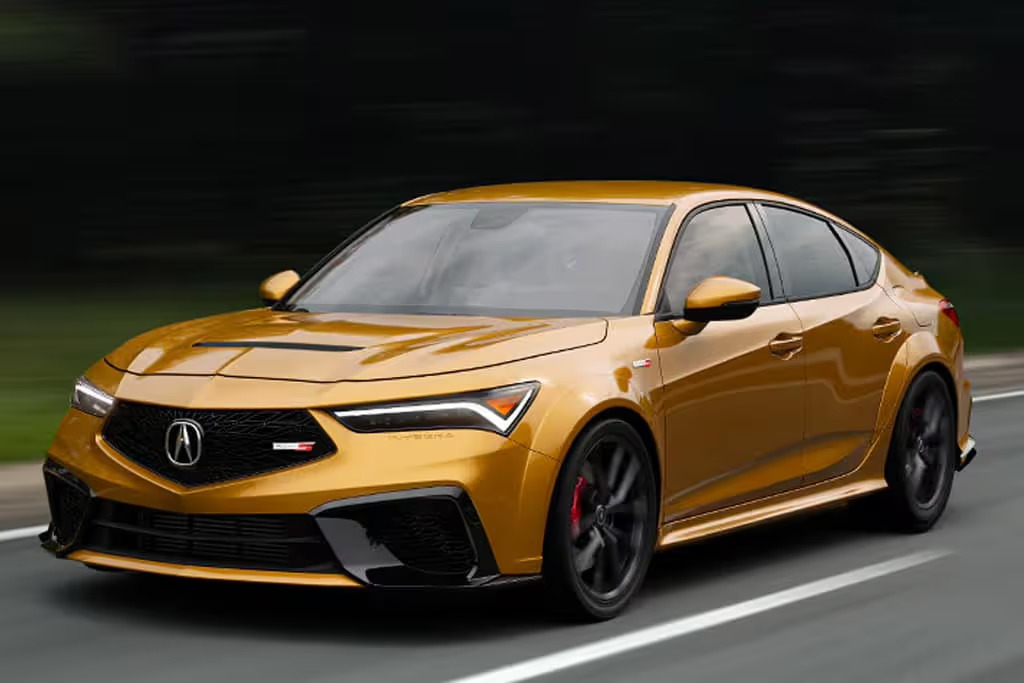
Vehicles undergo extended dynamic testing, including evaluation on specialized road surfaces designed to reveal potential noise, vibration, and harshness concerns that might otherwise manifest as comfort-related warranty claims.
Interior materials and electronic components receive particular scrutiny, with enhanced durability testing for touchpoints and interface elements that experience frequent customer interaction.
The brand’s approach to technology implementation further strengthens its warranty performance. While incorporating advanced features expected in luxury segments, Acura typically validates new technologies thoroughly before implementation, often allowing competitors to serve as early adopters before introducing refined versions with enhanced reliability characteristics.
This measured approach sometimes positions Acura behind luxury market trends, but consistently delivers superior long-term dependability as customer-facing technologies mature under its rigorous development process.
Acura further distinguishes its warranty performance through a sophisticated dealer service infrastructure. Technicians receive specialized certification requiring advanced diagnostic capabilities and system-specific expertise.
This ensures accurate first-time repair completion, reducing the repeat service visits that often inflate warranty claim statistics for other luxury brands. The company maintains comprehensive technical support systems that connect dealership personnel directly with engineering specialists for complex diagnoses, further enhancing repair efficiency.
This holistic approach spanning development, manufacturing, technology implementation, and service operations enables Acura to maintain its position among manufacturers with minimal warranty service requirements despite competing in segments where technological complexity typically challenges reliability metrics.
9. Mitsubishi
Mitsubishi has quietly established itself among manufacturers with the fewest warranty claims through a distinctive combination of engineering conservatism, focused product development, and industry-leading warranty coverage that reflects profound confidence in vehicle reliability.
Despite maintaining a lower profile than many competitors, Mitsubishi has leveraged its specialized expertise and disciplined approach to deliver vehicles that consistently demonstrate exceptional durability with minimal service requirements throughout their operational lifespans.
The company’s reliability foundation rests significantly on its conservative engineering philosophy that prioritizes proven technologies refined through iterative development rather than frequent radical redesigns.
Mitsubishi typically maintains core vehicle architectures longer than industry averages, allowing for continuous refinement that addresses potential reliability concerns through multiple product cycles.
This approach creates exceptionally mature platforms where failure points have been systematically identified and eliminated through real-world operational data rather than theoretical projections.
Mitsubishi implements particularly rigorous validation testing protocols that subject vehicles to extreme environmental conditions at dedicated facilities worldwide.
Its Okazaki proving grounds in Japan and weather testing centers across multiple continents expose vehicles to temperature extremes, humidity variations, and road conditions that exceed typical customer usage scenarios.
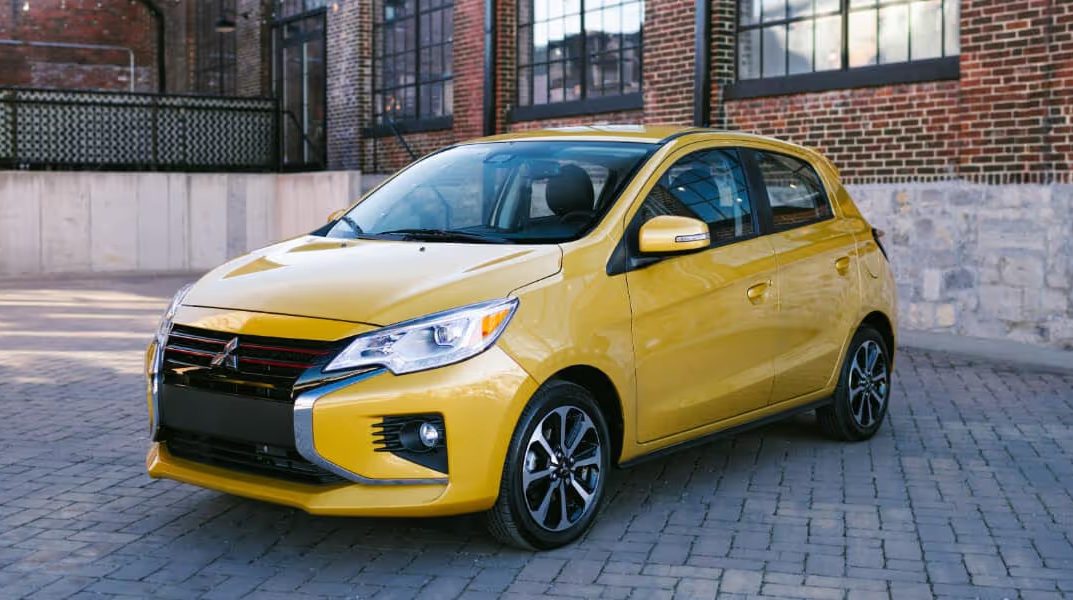
Components undergo accelerated aging processes that simulate extended service periods, identifying potential degradation patterns before production implementation. This exhaustive testing regimen creates substantial durability margins that translate directly to fewer warranty claims throughout vehicle lifespans.
Quality control within Mitsubishi’s manufacturing operations incorporates multiple inspection layers with enhanced focus on systems historically prone to warranty claims across the industry.
The company maintains particularly strict tolerance requirements for electronic components, sealing systems, and powertrain integration areas that typically generate significant warranty expenses for many manufacturers.
Vehicles undergo a comprehensive evaluation, including extensive road testing, water intrusion verification, and detailed electronic systems diagnostics, before receiving approval for shipment from production facilities.
Perhaps most telling about Mitsubishi’s confidence in its reliability engineering is the company’s industry-leading warranty coverage, particularly its powertrain protection that extends significantly beyond competitor offerings.
This extraordinary warranty commitment represents more than a marketing strategy; it reflects internal reliability data demonstrating exceptional durability expectations. The company’s ability to offer such coverage while maintaining profitability provides compelling evidence of its vehicles’ fundamental reliability characteristics.
Mitsubishi further enhances its warranty performance through sophisticated tracking systems that identify emerging concerns quickly, allowing engineering teams to implement countermeasures before issues generate substantial claims.
This combination of engineering conservatism, rigorous testing, manufacturing discipline, and proactive service management enables Mitsubishi to maintain its impressive position among manufacturers with minimal warranty service requirements.
10. Kia
Kia’s remarkable transformation from budget alternative to reliability leader represents one of the automotive industry’s most compelling quality improvement narratives. Now consistently ranking among manufacturers with the fewest warranty claims, Kia has implemented comprehensive reforms across its development, manufacturing, and quality assurance operations that have fundamentally altered its reliability profile.
This extraordinary evolution demonstrates how focused organizational commitment to quality improvement can dramatically enhance warranty performance even against established industry benchmarks.
At the foundation of Kia’s reliability renaissance has been its complete overhaul of vehicle development processes, implementing what the company terms its “Quality Gate” system.
This rigorous methodology establishes multiple checkpoints throughout development where specific quality and durability metrics must be achieved before projects advance.
Particularly notable has been Kia’s enhanced durability testing regimen, which now includes extended validation protocols that exceed industry standards for component lifecycle assessment.
Test vehicles accumulate substantially more evaluation miles before production approval, with a specialized focus on systems historically prone to generating warranty claims.
Manufacturing excellence forms another cornerstone of Kia’s warranty performance transformation. The company has invested billions in state-of-the-art production facilities incorporating advanced quality control technologies that monitor assembly precision in real-time.
These systems maintain extraordinary tolerances, particularly for critical components like powertrain assemblies, electronic systems, and body structures.
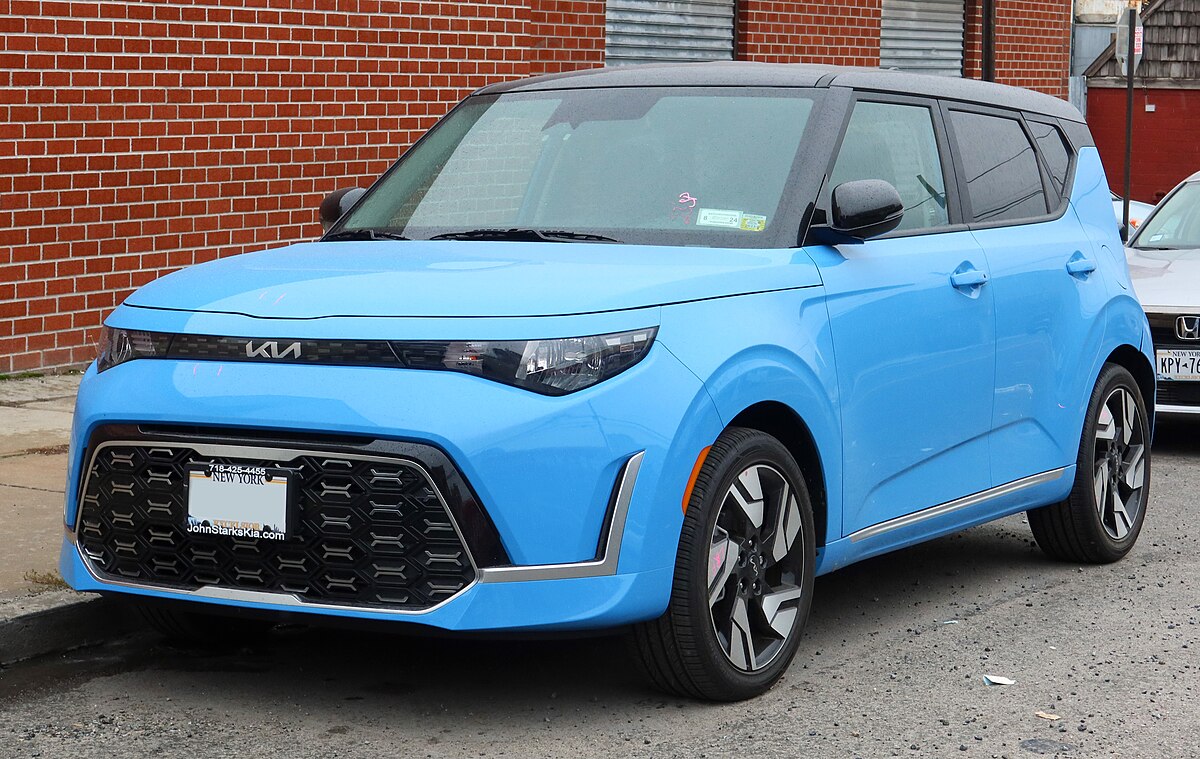
Assembly line workers undergo comprehensive training focused on quality-critical operations, creating specialized expertise that directly impacts reliability outcomes. Kia’s manufacturing facilities now regularly receive industry recognition for production quality, reflecting fundamentally transformed operational standards.
Supplier management represents a third critical element in Kia’s reliability improvement strategy. The company has implemented substantially more rigorous component qualification requirements, subjecting supplier-provided parts to extensive validation testing before production approval.
Many key components previously sourced externally have been brought under direct Kia manufacturing control, ensuring consistent quality standards across critical vehicle systems. This enhanced supplier oversight has dramatically reduced component-related warranty claims that previously affected the brand’s reliability perception.
Perhaps most visibly reflective of Kia’s confidence in its transformed reliability is the company’s industry-leading warranty coverage, particularly its comprehensive powertrain protection that extends significantly beyond competitor offerings.
Unlike some manufacturers who restrict warranty terms to minimize exposure to potential claims, Kia’s extensive coverage demonstrates fundamental confidence in vehicle durability.
The company supports this warranty commitment through sophisticated data collection systems that monitor vehicle performance across global markets, enabling engineering teams to identify emerging patterns and implement solutions promptly.
This comprehensive approach spanning development methodology, manufacturing precision, supplier management, and proactive service operations has raised Kia from an industry laggard to a legitimate reliability leader as measured by warranty claim frequency.
Also Read: 10 Vehicles Still Driven After 30 Years on the Road