In the demanding world of work vehicles, reliability isn’t just a convenience, it’s a business necessity. Whether you’re a contractor hauling materials across town, a delivery service keeping commerce flowing, or a tradesperson moving between job sites, your vehicle is as much a tool as anything in your toolbox.
The right work vehicle can become a trusted partner that contributes to your bottom line, while the wrong choice can drain resources through endless repairs and downtime.
Today’s market offers an array of options claiming to be work-ready, but experience in the field tells a different story for many models.
Some vehicles have established legendary reputations for durability and dependability under punishing conditions, while others consistently disappoint despite promising specifications.
This guide examines five work vehicles that have proven their worth through years of real-world use, maintaining their value and functionality despite demanding conditions.
We’ll also spotlight five vehicles that, despite their marketing as work-ready options, consistently fail to deliver the reliability and durability professional users require.
For each vehicle, we’ll explore key reliability factors, common failure points, maintenance considerations, and real-world performance to help you make informed decisions when selecting your next work vehicle.
5 Reliable Work Vehicles
Whether you’re managing a fleet or choosing a single vehicle for your business, understanding these distinctions can save thousands in operational costs and countless hours of frustration.
1. Toyota Tacoma
The Toyota Tacoma has earned its reputation as perhaps the most dependable midsize pickup truck on the market, with examples routinely exceeding 300,000 miles while maintaining their core functionality.
This long-standing reliability stems from Toyota’s conservative engineering approach rather than chasing cutting-edge technologies, the Tacoma employs proven mechanical systems refined over decades.
At the heart of Tacoma’s durability is its powertrain. The 3.5-liter V6 engine and accompanying transmission have demonstrated exceptional longevity, even when subjected to punishing conditions from construction sites to forestry services.
Owners report minimal issues with major components, and when problems do arise, they’re typically inexpensive sensors or peripheral systems rather than catastrophic failures.
The Tacoma’s frame construction deserves special mention. Unlike some competitors that have struggled with rust and structural integrity issues, Toyota’s frame treatment process has improved substantially after addressing earlier generation concerns, resulting in a platform that maintains its strength throughout harsh working environments.
The suspension system strikes an effective balance between load capacity and component durability, with leaf springs in the rear that handle repeated heavy loads without premature sagging.
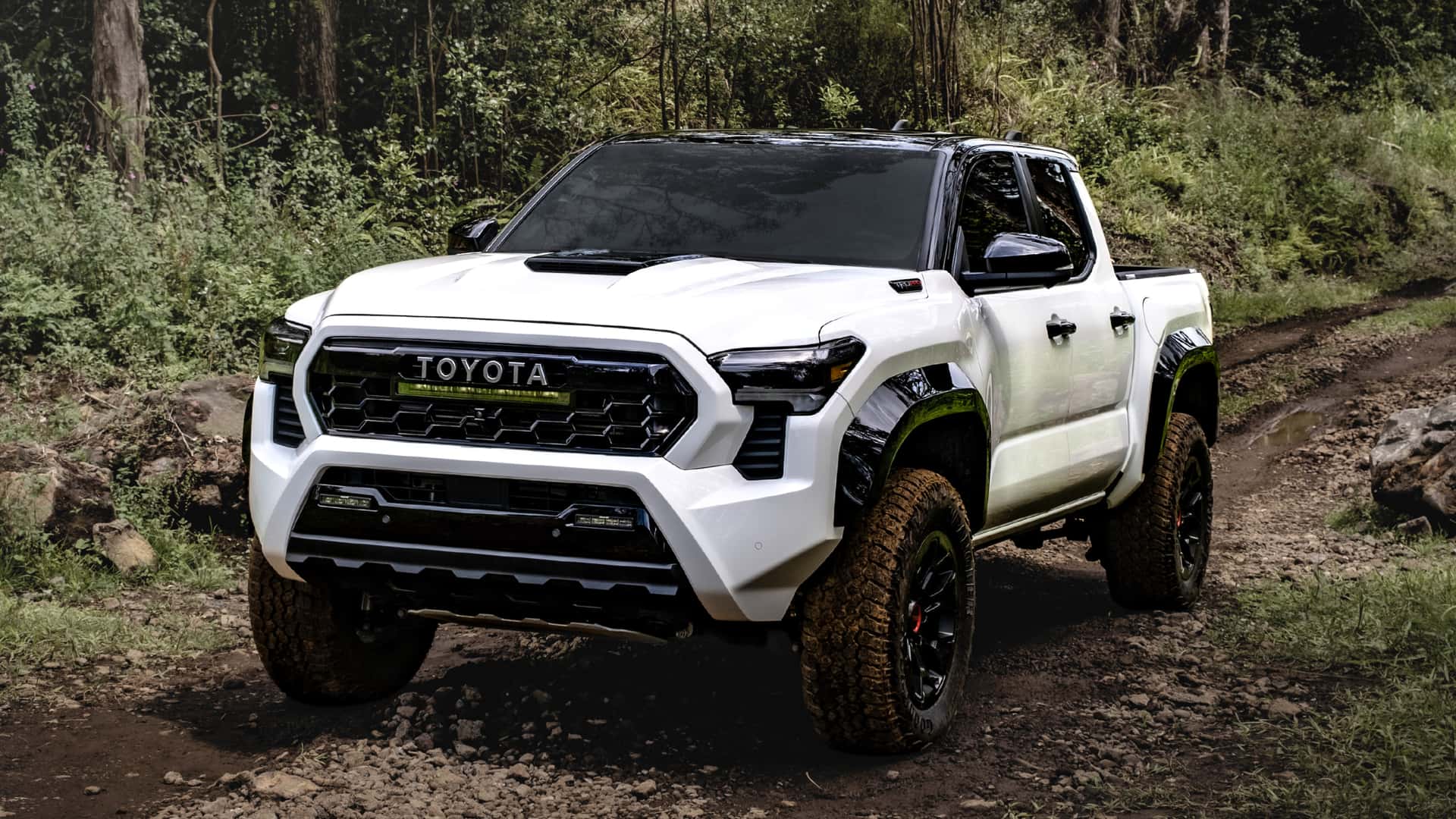
From a maintenance perspective, the Tacoma offers straightforward serviceability with accessible components and a design philosophy that prioritizes repair over replacement.
Fleet managers appreciate the predictable maintenance schedule and the availability of reasonably priced parts through both dealer networks and aftermarket suppliers. The modular design of many systems means repairs can often be performed without extensive disassembly.
Perhaps most telling is the Tacoma’s exceptional resale value historically among the highest in the automotive market. This value retention reflects both the truck’s longevity and the market’s confidence in its continued performance even at higher mileages.
For small businesses where vehicle costs significantly impact operating expenses, this residual value represents substantial savings over the total ownership period.
While the Tacoma doesn’t offer the highest towing capacity or the most spacious interior in its class, its reliability calculus makes it an ideal choice for businesses where dependability trumps maximum specifications.
The truck’s “right-sized” dimensions also provide maneuverability advantages on congested job sites where full-size pickups might struggle.
2. Ford F-250 Super Duty
The Ford F-250 Super Duty stands as a testament to purpose-built engineering for work applications, consistently proving itself as the backbone of countless commercial fleets and individual contractors’ operations across America.
What separates this heavy-duty pickup from less reliable alternatives is Ford’s dedicated chassis and powertrain development specifically for work applications, rather than modified passenger vehicle components.
The truck’s reliability centers around its Power Stroke diesel engine options, particularly the 6.7-liter variant introduced in 2011 and refined since.
Unlike previous generations that experienced well-documented issues, the current iteration delivers remarkable durability under load with proper maintenance.
These engines routinely exceed 500,000 miles in commercial service while maintaining their torque output and efficiency.
The TorqShift automatic transmission paired with these engines demonstrates similar longevity, with its robust cooling system preventing the overheating issues that plague lesser transmissions under heavy towing.
Structurally, the F-250’s fully boxed frame, constructed from high-strength steel, provides exceptional rigidity that prevents the flexing and eventual fatigue that leads to premature failure in work environments.
The suspension system, featuring twin-I-beam front suspension on two-wheel drive models and coil springs on four-wheel drive versions, delivers both the articulation needed for off-road situations and the stability required for heavy hauling.
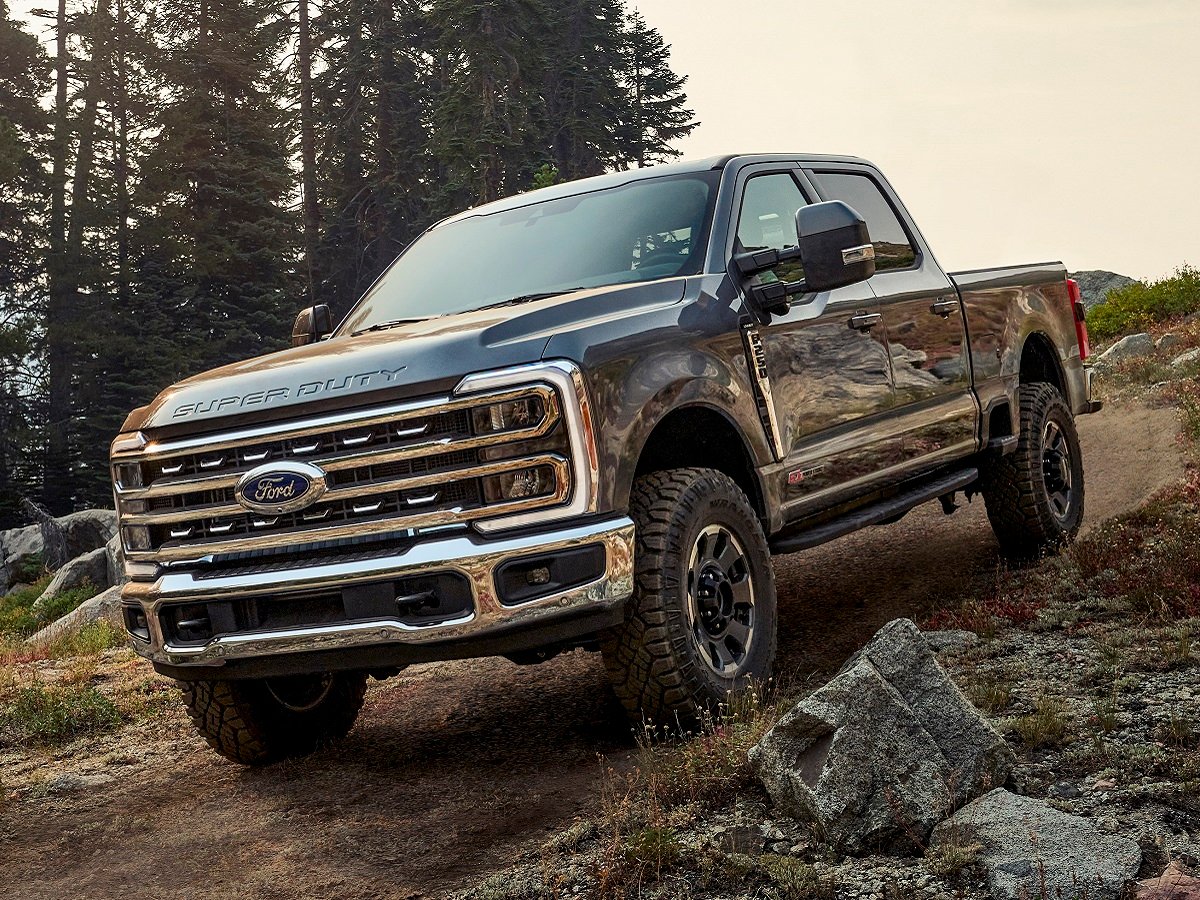
The electrical system represents another reliability highlight, with commercial-grade components that resist failure despite exposure to dust, moisture, and temperature extremes.
The truck’s modular wiring design means that when electrical problems do occur, they can typically be isolated and repaired without extensive dashboard disassembly or complete harness replacement.
Beyond core mechanical reliability, the F-250 excels in practical work functionality. The steel cargo bed resists the denting and punctures that aluminum alternatives may suffer, while the integrated tie-down system maintains its integrity through years of securing heavy loads.
Interior surfaces use durable materials that withstand the abuse of work gloves, tools, and daily grime without deteriorating.
Fleet managers particularly value the Super Duty’s comprehensive diagnostic systems and extensive dealer network, ensuring that when maintenance is required, downtime is minimized.
The truck’s commonality in commercial fleets means independent repair shops are also well-versed in servicing these vehicles, providing additional maintenance options beyond dealerships.
While the initial purchase price exceeds lighter-duty alternatives, the F-250’s lower lifetime operating cost and exceptional residual value make it a financially sound choice for businesses that depend on their vehicles daily.
3. Mercedes-Benz Sprinter
Despite perceptions of Mercedes-Benz as primarily a luxury brand, its Sprinter van has established an impressive reputation for longevity and reliability in commercial service worldwide.
Originally developed with a commercial-first mindset, the Sprinter’s design prioritizes function, durability, and total cost of ownership rather than the comfort-focused approach of passenger vehicles.
The Sprinter’s diesel powertrains represent the cornerstone of its reliability profile. The 3.0-liter V6 diesel and earlier 2.1-liter four-cylinder options were engineered for commercial duty cycles, with robust internal components and cooling systems designed for continuous operation.
These engines commonly exceed 400,000 miles in courier and delivery service with proper maintenance intervals. The transmission systems show similar durability, with examples in European taxi services routinely surpassing 300,000 miles without major rebuilds.
The Sprinter’s unibody construction provides an ideal balance between structural integrity and weight efficiency. Unlike truck-based vans with body-on-frame construction that can develop squeaks and alignment issues over time, the Sprinter’s integrated design maintains its integrity through years of service.
The suspension system, featuring independent front suspension and leaf springs in the rear, delivers both handling precision and load capacity without premature wear components.
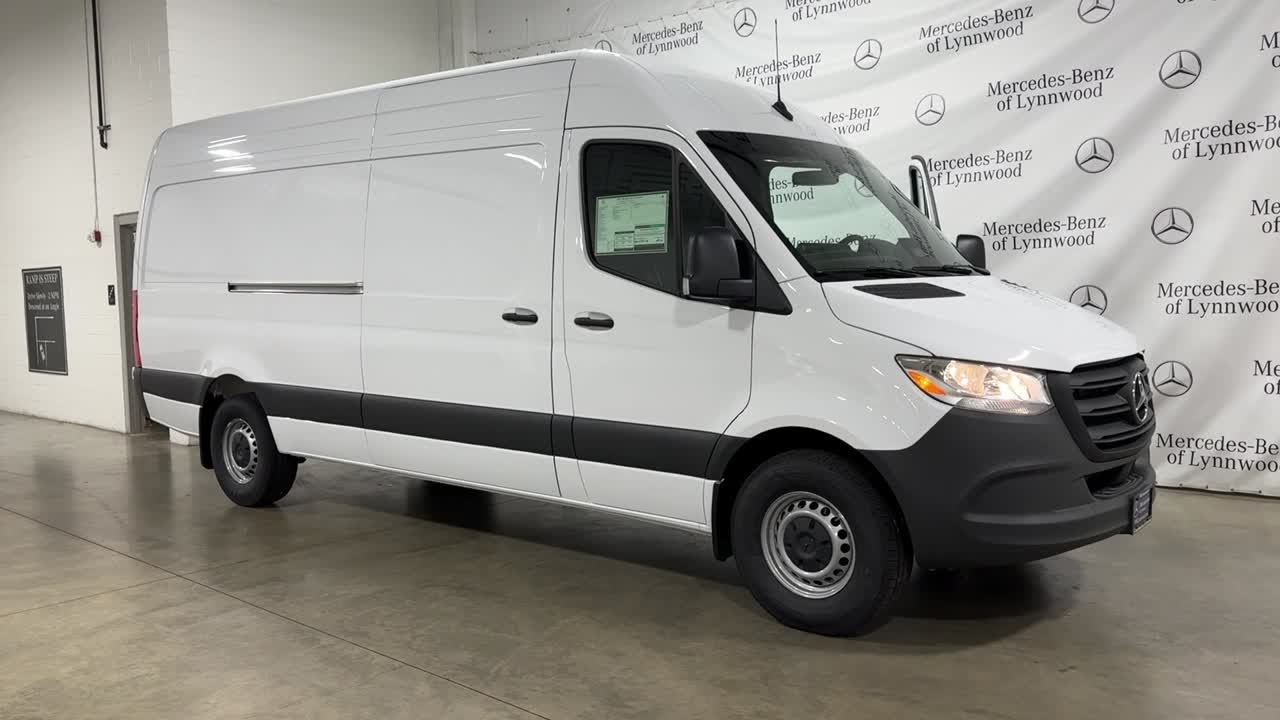
From a practical perspective, the Sprinter’s near-vertical walls and high roof design maximize usable cargo space while minimizing exterior dimensions.
This efficiency translates to lower fuel consumption compared to vans with similar cargo capacity. The interior cargo area features numerous attachment points engineered to maintain their strength through thousands of loading cycles, unlike competitors, where mounting points often fail after repeated use.
The electrical system employs commercial-grade components with enhanced protection against moisture and vibration, critical factors in long-term reliability.
The CAN bus network facilitates efficient troubleshooting when issues arise, reducing diagnostic time and associated labor costs. Fleet managers appreciate the detailed maintenance tracking capabilities through the vehicle’s onboard systems.
While parts and service costs exceed some competitors, the extended service intervals (with oil changes stretching to 20,000 miles under ideal conditions) and reduced frequency of component failure offset these expenses over the vehicle’s lifetime.
The extensive Mercedes-Benz commercial vehicle dealer network provides specialized service capabilities designed around minimizing business disruption.
Perhaps most telling is the Sprinter’s adoption as the platform of choice for demanding applications like ambulance services, where reliability directly impacts life-safety functions.
This confidence extends to the robust used market for high-mileage examples, reflecting the vehicle’s reputation for continued serviceability well beyond mileages where competitors would typically be retired.
4. Honda Ridgeline
The Honda Ridgeline represents a departure from traditional truck design philosophy, yet its unibody construction and car-based platform have proven remarkably durable in work applications that don’t require maximum towing capacity.
For contractors and service technicians who prioritize reliability over extreme capability, the Ridgeline delivers exceptional dependability.
At the core of the Ridgeline’s reliability is Honda’s 3.5-liter V6 engine and 9-speed automatic transmission (or earlier 6-speed), a powertrain combination shared with the highly-rated Pilot and Odyssey models.
This system routinely exceeds 250,000 miles without major issues when maintained properly. Unlike traditional truck engines designed primarily for low-end torque, the Ridgeline’s powertrain operates in its optimal efficiency range more frequently, reducing mechanical stress during daily operation.
The unibody construction, while limiting maximum payload compared to body-on-frame trucks, provides superior rigidity that prevents the development of squeaks, rattles, and alignment issues common in aging traditional pickups.
The independent suspension system, including a sophisticated rear multilink design rather than traditional leaf springs maintains ride quality and handling precision throughout the vehicle’s life without developing the saggy, worn-out character that plagues many work trucks after 100,000 miles.
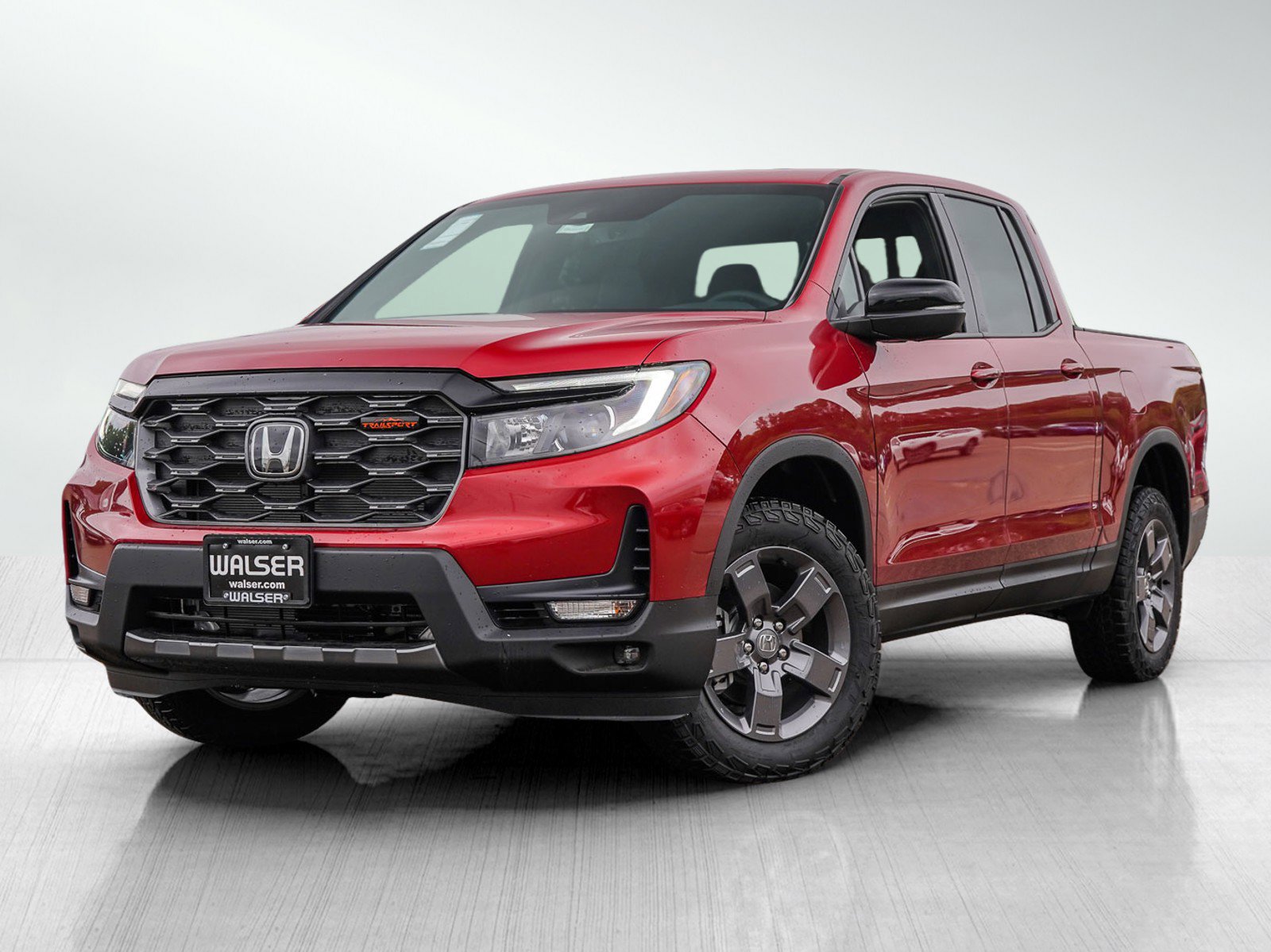
The Ridgeline’s composite bed represents another reliability advantage for work users. Unlike steel beds that rust or aluminum beds that can dent easily, the composite material resists corrosion, denting, and scratching.
The integrated trunk beneath the bed floor provides secure, weatherproof storage that remains functional throughout the vehicle’s life, while the dual-action tailgate maintains its alignment and operation where competing tailgate designs often sag or become misaligned over time.
From a maintenance perspective, Honda’s engineering philosophy emphasizes accessibility and straightforward service procedures.
Maintenance parts like filters, spark plugs, and fluids are generally easy to access, reducing labor time and associated costs during routine service.
The simplified drivetrain (compared to traditional 4WD trucks with transfer cases) means fewer components that could potentially fail. Electrical systems in the Ridgeline demonstrate exceptional reliability, with minimal issues reported related to sensors, switches, and electronic control modules.
This contrasts with many traditional work trucks, where electrical faults become increasingly common as mileage accumulates.
While the Ridgeline won’t satisfy users requiring maximum towing capacity or extreme off-road capability, its reliability makes it ideal for businesses where vehicle downtime directly impacts revenue.
The lower operating costs, including better fuel efficiency, reduced tire wear from the independent suspension, and fewer repairs contribute to a compelling total cost of ownership for appropriate work applications.
Also Read: 5 Vehicles That Make Great Workhorses and 5 That Fail At It
5. Isuzu NPR
In the commercial truck segment, few vehicles have established the reliability reputation of the Isuzu NPR series.
hese medium-duty cab-over trucks form the backbone of countless delivery fleets, service operations, and municipal agencies, regularly accumulating over 500,000 miles in commercial service while maintaining operational readiness.
The NPR’s dependability stems from its purpose-built commercial design rather than adapted passenger vehicle components.
The diesel powertrains available in NPR models represent commercial engineering at its finest, with robust internal components, oversized cooling systems, and simplified emission controls compared to passenger vehicles.
These engines operate well below their maximum stress levels during normal operation, contributing to their exceptional longevity.
The automatic transmissions paired with these engines employ larger cooling capacity and stronger internal components than light-duty alternatives, allowing them to handle the constant stop-and-go cycles of urban delivery without premature failure.
Structurally, the NPR’s ladder frame and commercial-grade suspension components maintain their integrity through years of maximum payload operation.
Unlike lighter-duty trucks that may develop sagging springs or frame fatigue when consistently operated at capacity, the NPR’s overbuilt chassis remains square and true despite punishing use.
The cab mounting system effectively isolates the driver compartment from chassis flex, preventing the development of squeaks, rattles, and misaligned doors that plague aging light-duty work vehicles.
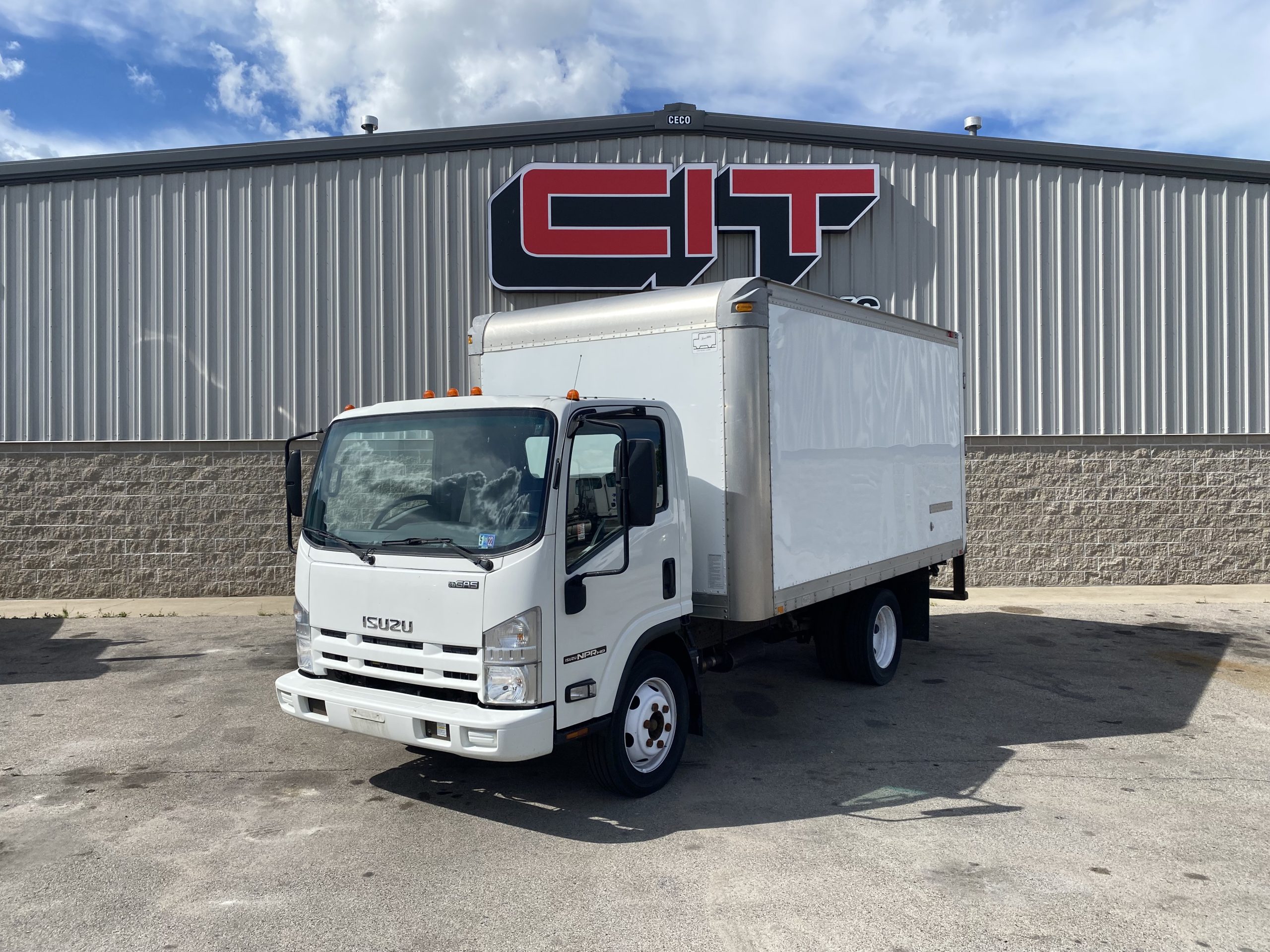
From a maintenance perspective, the NPR’s tilt-cab design provides unparalleled access to powertrain components, dramatically reducing service time and associated labor costs. Routine maintenance items like belts, hoses, and filters can be replaced in a fraction of the time required on conventional trucks.
This accessibility translates directly to reduced downtime and lower lifetime operating costs. The electrical system employs commercial-grade components with enhanced protection against environmental factors, with wiring harnesses and connectors designed specifically for extended service life.
Unlike consumer-grade vehicles, where electrical faults become increasingly common with age and mileage, the NPR’s electrical systems maintain their integrity through decades of service.
Fleet managers particularly appreciate the NPR’s consistent performance metrics over time, fuel economy, braking performance, and payload capacity show minimal degradation compared to newer examples.
This consistency allows for accurate operational cost forecasting, essential for businesses where vehicle expenses significantly impact profitability.
While the NPR’s initial acquisition cost exceeds comparable GVWR light-duty alternatives, its substantially longer service life and reduced maintenance requirements deliver superior lifetime value.
Many operators report NPR trucks remaining in primary service for 15+ years, compared to the 7-10 year replacement cycle typical with light-duty commercial vehicles.
5 Work Vehicles That Fail on the Job
When it comes to work vehicles, reliability isn’t optional — it’s mandatory. Whether you’re hauling heavy loads, navigating rough job sites, or making constant deliveries, your vehicle needs to perform without excuses.
Yet, not all trucks, vans, or utility vehicles live up to the promises stamped in their brochures. In this article, we’re breaking down five work vehicles that simply don’t cut it when the pressure’s on — vehicles that have earned a reputation for letting their owners down when they’re needed most.
1. Nissan Frontier (2005-2021 Generation)
The Nissan Frontier represents one of the most disappointing entries in the midsize truck market from a reliability perspective, particularly examples from the 2005-2021 generation that went unchanged for an extraordinary 16 years.
While this extended production run might suggest a refined, debugged platform, the reality proved quite different for many work users who experienced consistent failures across multiple vehicle systems.
The Frontier’s most catastrophic reliability issue centers around its transmission, specifically in models equipped with the 4.0L V6 engine and automatic transmission from 2005-2010.
These vehicles suffered from a fatal design flaw where coolant could mix with transmission fluid through a failed radiator transmission cooler, creating what mechanics dubbed “strawberry milkshake” fluid that would quickly destroy the transmission.
While Nissan eventually extended warranty coverage for this specific issue, many work users discovered the problem after warranty expiration, facing repairs exceeding $4,000.
Even after addressing this specific defect, the transmission remained a weak point, with many examples requiring rebuilds before reaching 150,000 miles.
The suspension system represents another failure point, with particularly premature wear in front end components including ball joints, control arm bushings, and tie rod ends.
Work users regularly report replacement intervals of 50,000-70,000 miles for these components half the lifespan expected in competing trucks subjected to similar conditions.
This accelerated suspension wear not only creates safety concerns but also results in abnormal tire wear patterns that increase operating costs through more frequent tire replacement.
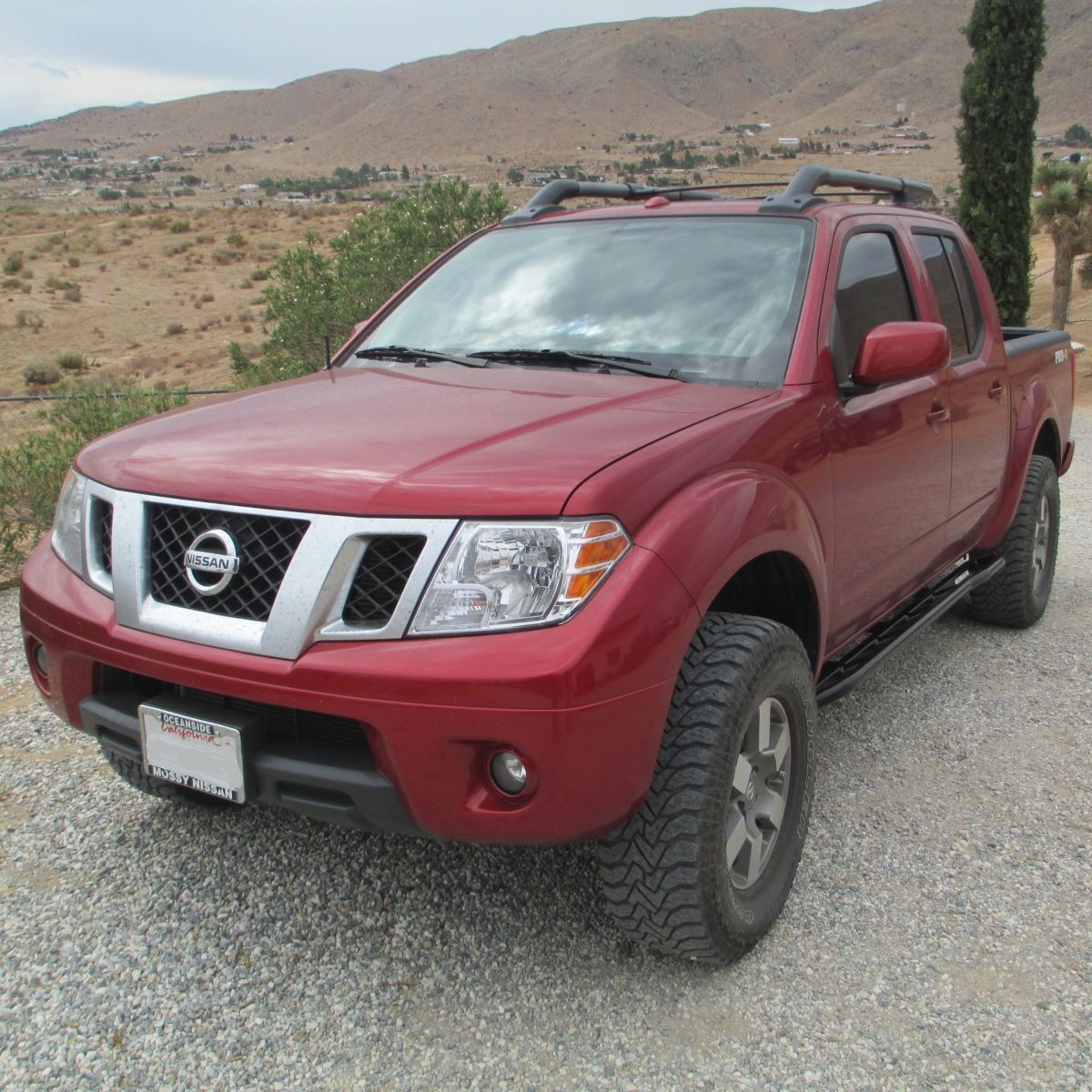
Electrically, the Frontier demonstrated numerous weaknesses inappropriate for work environments. The alternator proved particularly problematic, with replacement often necessary before 100,000 miles.
The vehicle’s body control modules and engine control units showed unusual susceptibility to moisture-related failures, creating intermittent electrical gremlins that proved difficult and expensive to diagnose.
Workers relying on accessory power for tools frequently encountered problems with the vehicle’s inadequate electrical system capacity.
Interior durability fell substantially short of work-ready standards, with seat fabrics showing accelerated wear, dashboard materials cracking from UV exposure, and door handles frequently breaking after several years of service.
While aesthetic concerns might be secondary for work vehicles, these failures often extended to functional components like HVAC controls and switchgear necessary for daily operation.
Perhaps most telling about the Frontier’s inadequacy as a work vehicle is its poor residual value compared to competitors like the Toyota Tacoma.
The market’s awareness of these reliability issues results in substantially lower resale values, increasing the total cost of ownership despite the Frontier’s lower initial purchase price. For businesses where vehicle costs directly impact profitability, this accelerated depreciation represents a significant hidden expense.
While Nissan completely redesigned the Frontier for 2022, addressing many of these concerns, the long legacy of the previous generation’s problems has made many work users understandably hesitant to trust the platform for critical business applications.
2. Ram ProMaster
The Ram ProMaster entered the North American commercial van market in 2014, promising European efficiency with American service support. Based on the Fiat Ducato platform with decades of European service, expectations were high for this front-wheel drive commercial van.
Unfortunately, the ProMaster has developed a concerning reputation for reliability issues that make it a problematic choice for businesses dependent on vehicle uptime.
Transmission failures represent the ProMaster’s most significant and expensive reliability concern. The six-speed automated manual transmission (marketed as an automatic) has demonstrated alarming failure rates, particularly in urban delivery applications involving frequent stops.
Many commercial users report complete transmission replacements necessary before 100,000 miles a critical failure point for vehicles expected to deliver 250,000+ miles of commercial service.
These replacements often cost between $4,000-7,000 depending on labor rates, creating substantial unexpected expenses for business owners. Electrical system issues plague the ProMaster throughout its service life, with problems ranging from minor annoyances to complete operational failures.
The body control module proves particularly problematic, with numerous reports of random electrical failures, including inoperative power door locks, erratic dashboard warnings, and unpredictable starting issues.
Many of these electrical gremlins prove frustratingly intermittent, creating diagnostic challenges that result in repeated dealer visits and extended downtime.
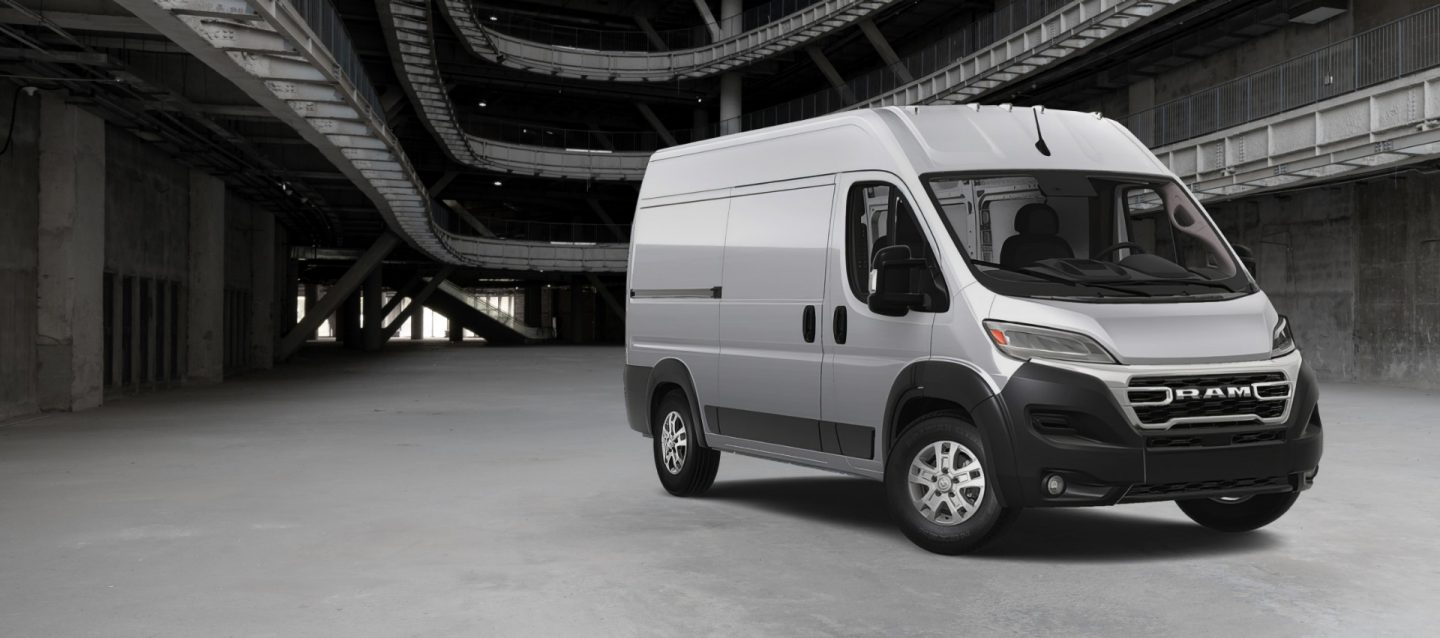
The cooling system represents another critical weakness inappropriate for work vehicles. Radiator failures occur with concerning frequency, often between 60,000-90,000 miles.
The thermostat housing, constructed from plastic components, shows a propensity for cracking and leaking, potentially leading to overheating events that can cause catastrophic engine damage if not addressed immediately.
For delivery operations where vehicles run continuously throughout the day, these cooling system vulnerabilities create significant business risk.
Suspension components demonstrate accelerated wear rates compared to competing commercial vans, particularly in the steering and front suspension systems.
The tie rod ends and control arm bushings frequently require replacement before 80,000 miles, creating both safety concerns and increased maintenance costs.
The brake system components, particularly calipers, show premature failure rates with many users reporting caliper replacements necessary at 40,000-60,000 miles, half the expected service interval.
For commercial users, perhaps the most telling reliability indicator comes from the used market, where ProMaster vans with over 150,000 miles sell for significantly less than comparable Mercedes Sprinter or Ford Transit models.
This market devaluation reflects the business community’s awareness of these vehicles’ problematic reliability history and the projected increased maintenance costs as mileage accumulates.
While FCA (now Stellantis) has implemented numerous technical service bulletins addressing specific issues, the ProMaster’s fundamental reliability concerns appear to be design-related rather than manufacturing defects that can be fully resolved through updates or recalls.
For businesses where vehicle dependability directly impacts revenue, the ProMaster represents a questionable investment despite its competitive purchase price and cargo capacity advantages.
3. Chevrolet Colorado/GMC Canyon (2015-2022 Generation)
The second-generation Chevrolet Colorado and its GMC Canyon twin entered the market in 2015 with substantial hype and promising specifications that suggested true work-truck capabilities in a midsize package.
Unfortunately, real-world experience has revealed numerous reliability concerns that make these trucks problematic choices for businesses dependent on vehicle uptime.
Transmission issues stand as perhaps the most significant reliability concern, particularly in models equipped with the 8-speed automatic transmission introduced for 2017.
These units have demonstrated alarming failure rates, with symptoms including harsh shifts, hesitation, shuddering (especially between 25-80 mph), and in some cases, complete transmission failure.
GM has issued multiple technical service bulletins and extended warranty coverage for certain aspects of the transmission, but many problems emerge after these coverage periods expire, leaving owners with repair bills exceeding $3,500.
For work users, these transmission problems create unpredictable downtime and substantial repair expenses. The 2.8L Duramax diesel engine option, while appealing for its torque specifications and theoretical fuel economy, has proven problematic in work applications.
Issues with the emissions control system particularly the exhaust gas recirculation (EGR) valve and diesel particulate filter (DPF), create recurring check engine lights and occasionally forced power reductions (“limp mode”) that render the vehicle temporarily unusable.
The high-pressure fuel pump has also demonstrated concerning failure rates, with replacement costs often exceeding $2,000, including labor.
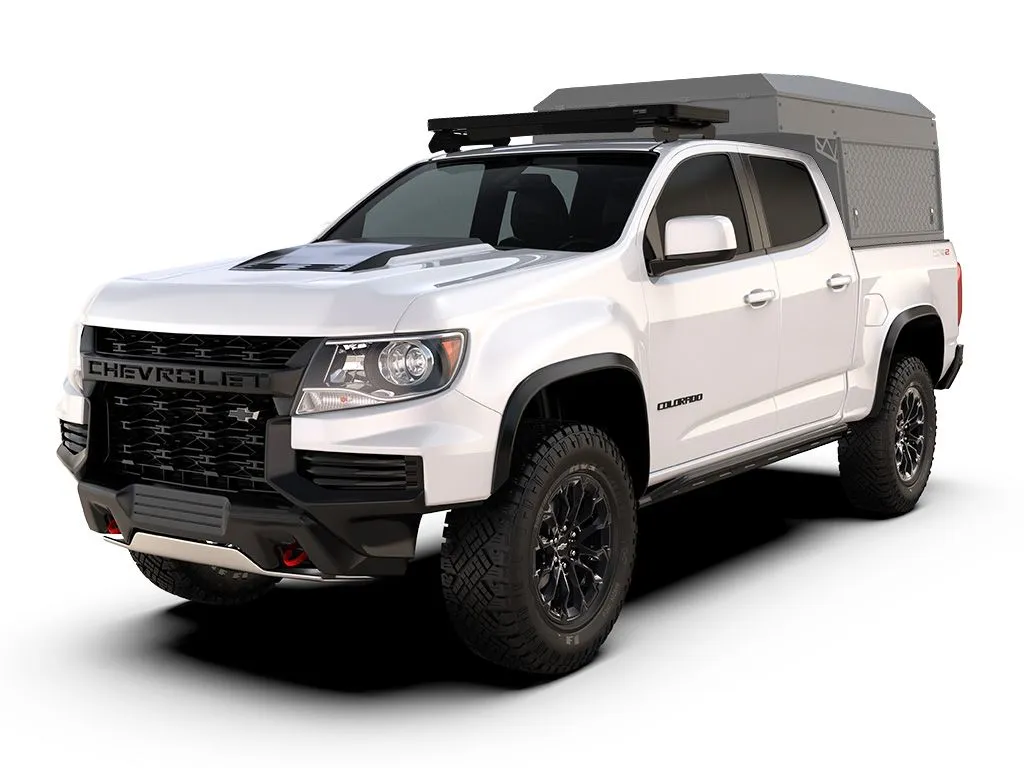
Electrical system reliability falls short of work-vehicle standards, with numerous reports of battery drain issues, faulty sensors triggering false warning lights, and problems with the infotainment system that can render critical functions like backup cameras inoperative.
The wiring harnesses show particular vulnerability to environmental exposure, with connections corroding prematurely in wet or salty conditions common to many work environments.
The cooling system represents another weakness, particularly in trucks equipped with the V6 engine option. Water pump failures occur with concerning frequency around 60,000-80,000 miles, often presenting with little warning before overheating.
The thermostat housing, constructed from plastic components, shows a propensity for developing leaks that can lead to coolant loss and potential engine damage if not detected promptly.
Interior durability proves inadequate for work applications, with seat bolsters wearing through before 100,000 miles, dashboard materials cracking from UV exposure, and door panels developing rattles after several years of service.
While aesthetic concerns might be secondary for work vehicles, the frequently failing power window switches, door lock actuators, and HVAC controls directly impact daily usability.
Perhaps most telling is the resale value trajectory of these trucks compared to competitors like the Toyota Tacoma. By the 100,000-mile mark, Colorado/Canyon models typically retain significantly less value, reflecting the market’s awareness of their problematic reliability history and projected increased maintenance costs as mileage accumulates.
4. Ford Transit Connect
The Ford Transit Connect arrived in North America promising European efficiency in a compact commercial package.
While its small footprint and initial fuel economy numbers attracted small businesses and service fleets, real-world experience has revealed numerous reliability concerns that make it problematic for work applications where vehicle dependability directly impacts revenue.
The powertrain represents the Transit Connect’s most significant reliability concern. Early models featured a 2.0L engine that developed timing chain issues with alarming frequency, often before reaching 100,000 miles.
Later models with the 1.6L and 2.5L engines improved somewhat but still suffer from premature failure of components like purge valves, throttle bodies, and EGR systems.
The six-speed automatic transmission demonstrates concerning durability limitations, with many examples requiring major service or complete replacement between 100,000-125,000 miles, woefully inadequate for commercial service where 200,000+ miles represents the minimum expected powertrain life.
Electrical system problems plague the Transit Connect throughout its service life. The battery wiring system proves particularly problematic, with numerous reports of unexplained battery drain that leaves vehicles unable to start after sitting overnight, a critical failure for service businesses that depend on morning dispatch reliability.
The body control module demonstrates vulnerability to moisture intrusion, creating intermittent electrical gremlins that prove frustratingly difficult to diagnose and repair.
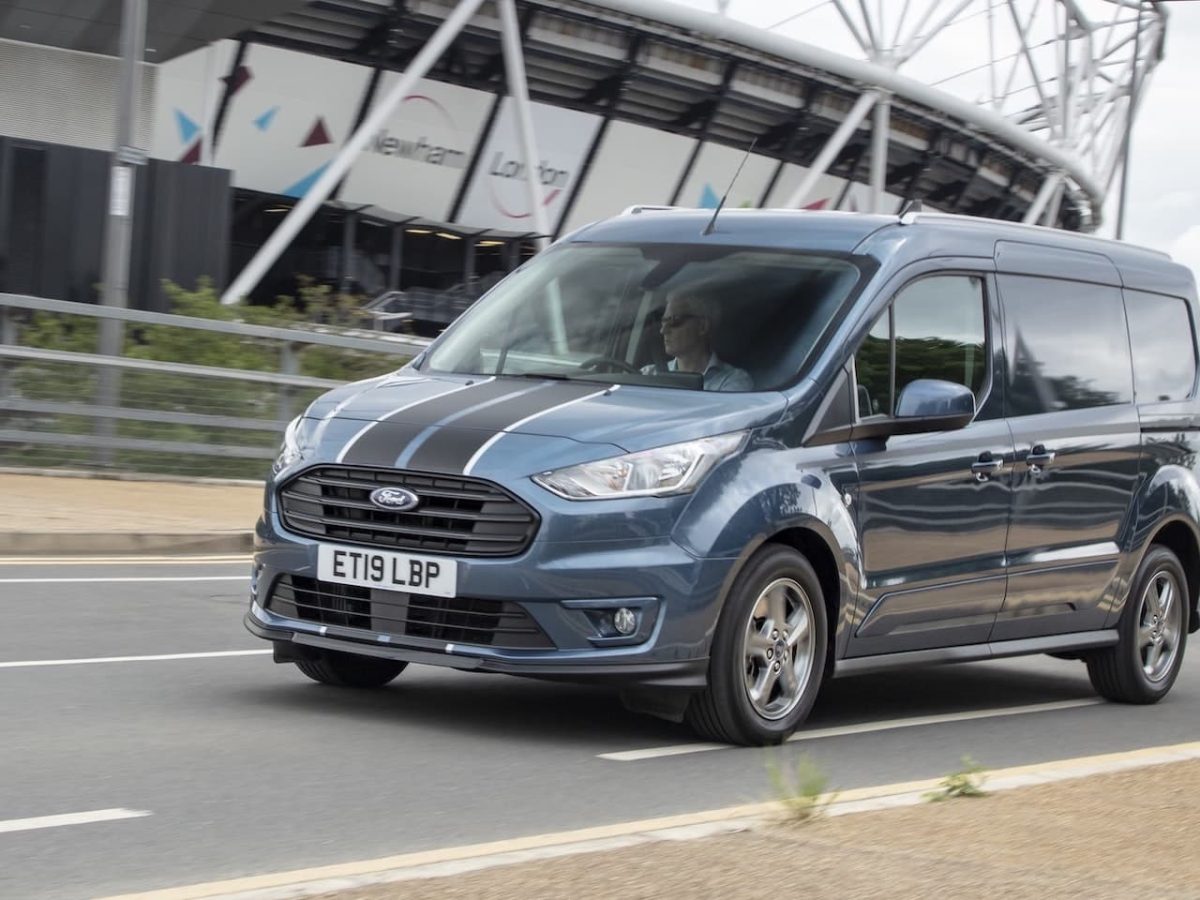
The cooling system represents another critical weakness inappropriate for work vehicles. Radiator failures occur with concerning frequency, often between 60,000-90,000 miles.
The water pump, driven by the timing belt in some engine configurations, shows premature failure rates that can lead to catastrophic engine damage if the timing belt fails consequently.
For mobile businesses where vehicles operate continuously throughout the day, these cooling system vulnerabilities create significant operational risk. Suspension durability falls substantially short of commercial standards, with control arm bushings, ball joints, and tie rod ends frequently requiring replacement before 80,000 miles.
The rear suspension demonstrates particular vulnerability to failure when consistently loaded to capacity, precisely the condition most commercial users employ regularly.
Workers report that loaded handling becomes increasingly unpredictable as these components wear, creating both safety concerns and accelerated tire wear that increases operating costs.
Interior durability proves inadequate for commercial application, with seat fabrics showing accelerated wear, dashboard materials cracking from UV exposure, and cargo area tie-downs often breaking under normal use.
While aesthetic concerns might be secondary for work vehicles, the frequently failing door latches and liftgate mechanisms directly impact functionality for delivery and service applications.
For businesses that selected the Transit Connect based on its promising fuel economy, real-world results often disappoint.
Under load and in actual delivery conditions, the small engines must work near maximum capacity, resulting in fuel consumption much closer to larger commercial vans without the corresponding capacity benefits.
This efficiency shortfall, combined with the reliability concerns, creates an unfavorable total cost of ownership despite the lower initial purchase price.
5. Jeep Gladiator
The Jeep Gladiator entered the market in 2020 with substantial fanfare as Jeep’s long-awaited return to the pickup truck segment.
While its distinctive styling and off-road capabilities attracted enthusiasts, its reliability record has proven problematic for those attempting to employ it as a serious work vehicle.
Despite sharing components with the Wrangler and Ram 1500, the Gladiator has developed specific reliability concerns that make it a questionable choice for businesses dependent on vehicle uptime.
Electronic systems represent the Gladiator’s most significant reliability vulnerability. The complex network of control modules managing everything from engine performance to four-wheel-drive systems has demonstrated concerning failure rates, with many owners reporting “limp mode” events that render the vehicle temporarily undrivable.
The instrument cluster frequently develops electronic glitches, sometimes displaying inaccurate information about critical systems, including fuel level and engine temperature, creating potential for unexpected operational failures. For work users, these unpredictable electronic issues create significant business disruption.
The cooling system has proven inadequate for sustained work applications, particularly when towing near the vehicle’s rated capacity. Despite Jeep’s advertised tow ratings, real-world experience shows the cooling system’s marginality when pulling trailers in hot conditions or on extended grades.
The electronic cooling fan control system frequently misinterprets sensor information, sometimes failing to engage cooling fans appropriately during high-load operations.
This cooling inadequacy forces operators to either reduce loads below rated capacity or risk potential engine and transmission damage.
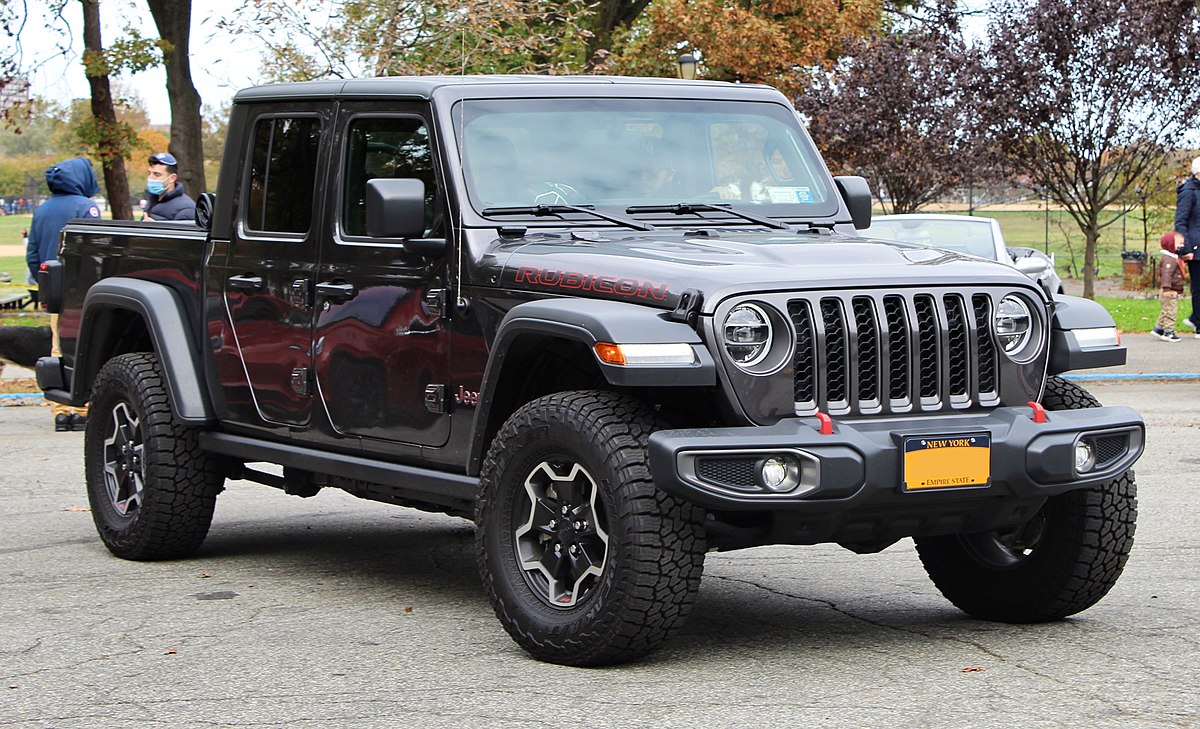
Suspension and steering components demonstrate accelerated wear compared to purpose-built work trucks, particularly the track bar and control arm bushings.
The sophisticated front suspension, while excellent for off-road articulation, shows vulnerability to alignment issues that create abnormal tire wear patterns, increasing operating costs through more frequent tire replacement.
The steering system demonstrates concerning “death wobble” oscillations in some examples, a severe vibration at highway speeds, requiring immediate reduction in speed for safety.
The bed design, while visually distinctive, creates functional limitations for work applications. The high load floor reduces effective cargo capacity, while the relatively thin sheet metal shows vulnerability to denting and deformation under heavy loads.
The tailgate hinges demonstrate concerning wear patterns after repeated use, developing slop and misalignment that worsens over time. Interior durability falls short of work-vehicle standards, particularly in high-touch areas like door handles, window switches, and HVAC controls.
The infotainment system demonstrates concerning failure rates, sometimes requiring complete module replacement at substantial cost.
While Jeep has implemented software updates addressing some electronic issues, many problems recur after updates or emerge in different systems following dealer intervention.
Perhaps most telling for work users is the Gladiator’s depreciation curve compared to established work trucks in the midsize segment.
Despite commanding premium prices when new, Gladiators typically experience steeper value depreciation after 50,000 miles, reflecting the market’s growing awareness of these reliability concerns.
For businesses where vehicle costs directly impact profitability, this accelerated depreciation represents a significant hidden expense beyond the higher initial purchase price.
Also Read: 5 Commuter Cars That Go the Distance and 5 That Stall in Traffic