Brake pads are a critical but often overlooked component of your vehicle’s safety system. As the friction material that clamps against your brake rotors, they convert kinetic energy into heat, bringing your vehicle to a stop.
However, not all brake pads are created equal, and more importantly, not all vehicles treat their brake pads with the same level of mercy. Several factors influence brake pad longevity, including vehicle weight, typical driving conditions, braking system design, and driving habits.
Heavier vehicles naturally place more strain on brake pads, while vehicles designed for performance often sacrifice pad longevity for enhanced stopping power.
Understanding which vehicles are gentle on their brake pads and which ones are notorious for rapid wear can help consumers make informed decisions when purchasing a vehicle and budget appropriately for maintenance costs.
This article explores five vehicles known for extraordinary brake pad longevity, sometimes exceeding 70,000 miles, and five that might send you to the service center for replacements far more frequently than you’d like, potentially as soon as 20,000 miles under certain driving conditions.
5 Cars With the Longest Brake Pad Lifespans
These exceptional vehicles feature innovative brake designs and intelligent systems that significantly extend pad life while maintaining superior stopping performance in all conditions.
Advanced regenerative braking technology and high-quality materials combine to reduce wear, allowing these models to achieve impressive mileage between brake services.
Smart weight distribution and optimized braking algorithms ensure even pad wear across all four corners, eliminating the premature replacement often required on front pads alone
Owners report routinely exceeding 70,000 miles on original equipment pads, dramatically reducing maintenance costs and service visits throughout the vehicle’s lifetime.
1. Toyota Prius
The Toyota Prius stands as a testament to efficient engineering, not just in fuel economy but also in brake pad longevity. The regenerative braking system that defines hybrid vehicles fundamentally changes how frequently the conventional friction brakes engage.
When a Prius driver applies the brakes, the electric motor operates in reverse, acting as a generator that both slows the vehicle and recharges the battery pack. This ingenious system means that the traditional brake pads only engage at lower speeds or during more aggressive stopping scenarios.
Prius owners routinely report brake pad lifespans exceeding 75,000 miles, with some stretching beyond 100,000 miles in predominantly highway or gentle urban driving conditions.
This extraordinary longevity stems from the vehicle’s lightweight design (approximately 3,000 pounds), aerodynamic profile that reduces the need for sudden braking, and the aforementioned regenerative braking technology that handles approximately 60-80% of routine deceleration duties.
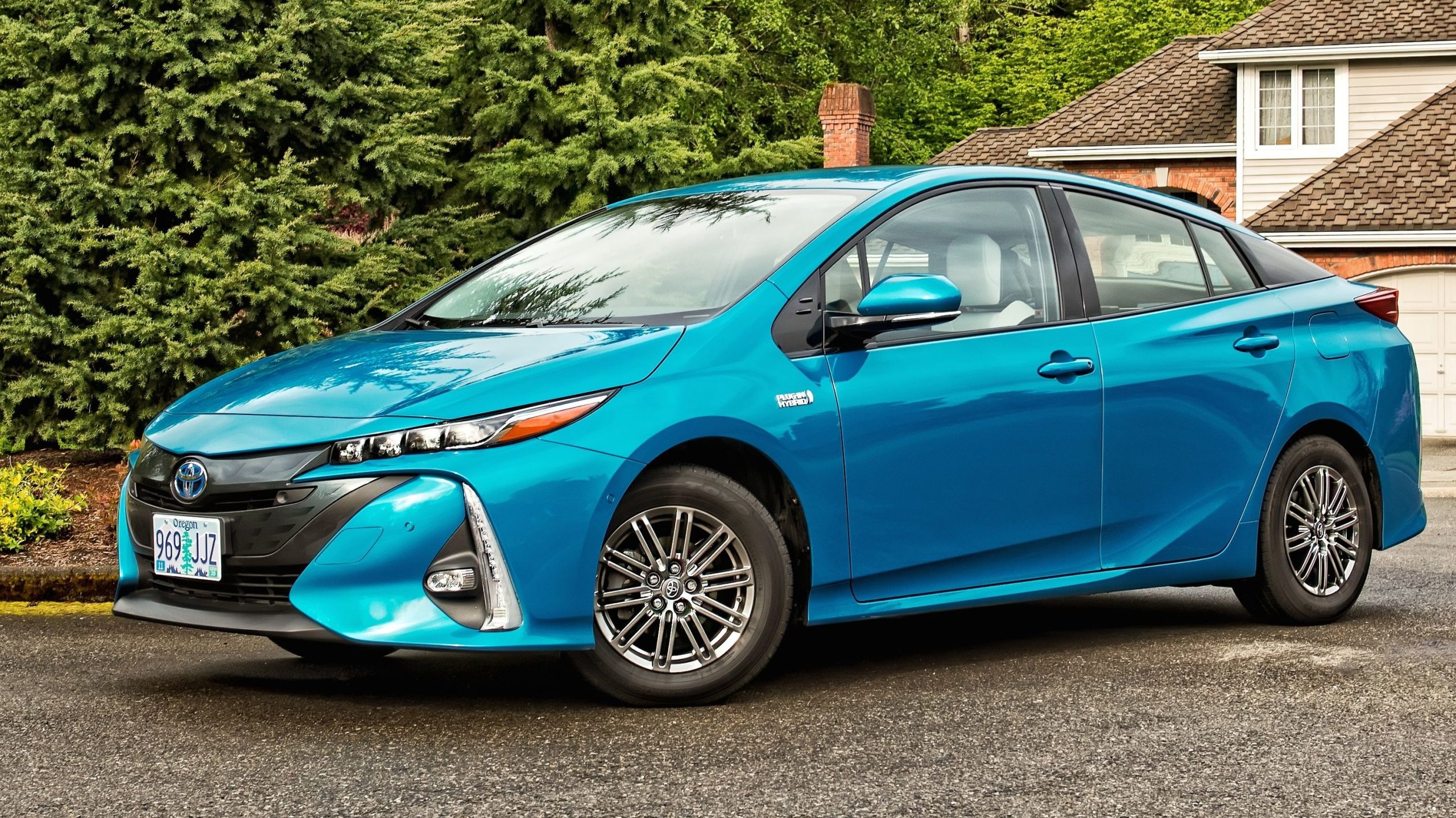
Toyota’s commitment to quality components also plays a role. The factory-installed brake pads feature ceramic compounds that resist heat fade and wear more evenly than traditional metallic or semi-metallic alternatives.
These high-quality materials, combined with the reduced workload, create a perfect storm of brake pad preservation. The vehicle’s onboard computer system further optimizes brake pad life by calculating precisely how much regenerative braking to apply before engaging the friction brakes.
This intelligent brake force distribution ensures that the pads only work when necessary, dramatically reducing wear patterns that plague conventional vehicles. For cost-conscious consumers, this extended brake component lifespan translates to significant maintenance savings over the vehicle’s lifetime.
While the average driver might replace brake pads every 30,000-50,000 miles on a conventional vehicle, many Prius owners report completing only one brake service through 120,000 miles of ownership, a compelling economic argument that extends beyond the obvious fuel savings.
2. Lexus ES 300h
As Lexus’s luxury hybrid sedan, the ES 300h exemplifies how upscale engineering can deliver both comfort and remarkable brake pad durability. Like its Toyota cousin, the ES 300h employs a sophisticated regenerative braking system that dramatically reduces wear on conventional brake pads.
However, Lexus takes this engineering a step further with an adaptive variable suspension system that optimizes weight transfer during braking events, ensuring more even distribution of braking forces.
The ES 300h typically achieves between 70,000 and 90,000 miles on a single set of brake pads under normal driving conditions. This exceptional performance stems from several factors beyond just the regenerative braking system.
Lexus engineers have developed a particularly refined brake pedal feel that encourages smoother, more gradual deceleration, naturally reducing pad wear.
The electronic brake force distribution system dynamically adjusts braking pressure between front and rear wheels, preventing the front-heavy wear pattern common in many vehicles.
Material quality plays a crucial role in the ES 300h’s brake longevity story. Lexus equips these vehicles with premium ceramic-composite brake pads that offer superior heat dissipation properties.
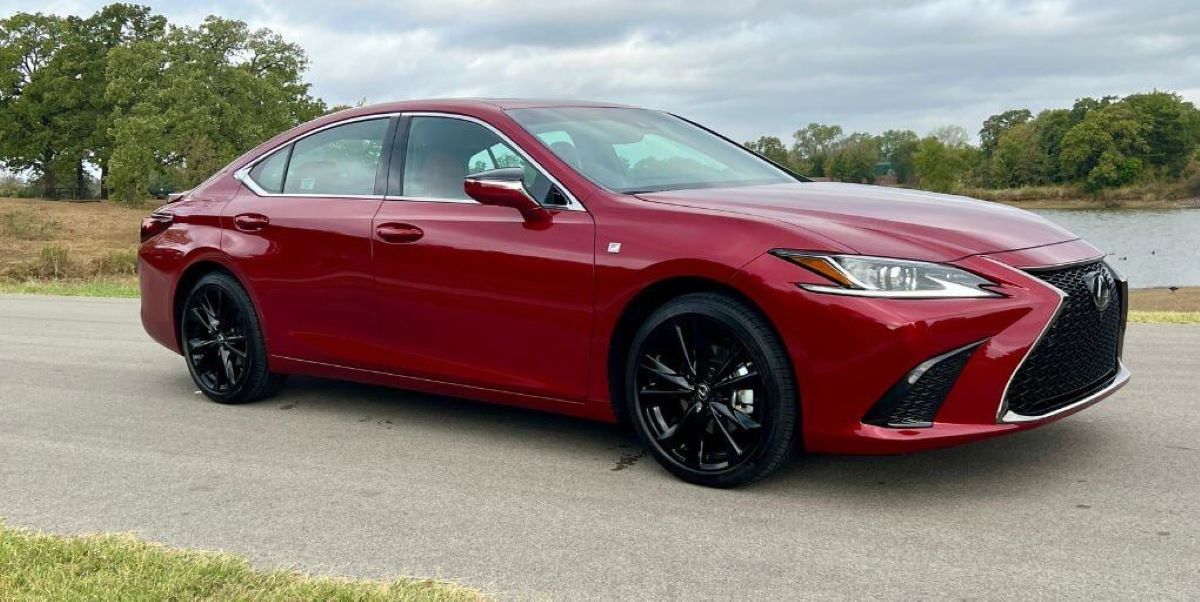
These high-grade components resist the thermal degradation that accelerates wear in lesser materials, particularly important given the vehicle’s substantial 3,700-pound curb weight.
The vehicle’s drive mode selector further contributes to brake preservation. When operated in ECO mode, the system increases regenerative braking aggressiveness while softening throttle response, encouraging a driving style that naturally reduces conventional brake usage.
Meanwhile, the Brake Hold feature, which automatically maintains brake pressure when stopped at traffic lights or in congestion, eliminates the subtle but cumulative wear that occurs when drivers continually apply and release brakes in stop-and-go traffic.
Lexus service records indicate that many ES 300h owners complete their entire lease terms without requiring brake service, a significant advantage for both personal owners and the certified pre-owned market.
This exceptional component’s longevity contributes to the model’s strong residual values and reputation for low total cost of ownership despite its luxury positioning.
3. Honda Civic
The Honda Civic has earned its reputation for reliability across all components, but its brake pad longevity in non-performance trim levels deserves special recognition.
Standard Civic models typically achieve between 60,000 and 80,000 miles on original brake pads, significantly outperforming many competitors in the compact segment.
This impressive durability stems from a carefully optimized combination of vehicle weight, braking system design, and quality components. Base and mid-level Civic models tip the scales at approximately 2,800 pounds, making them substantially lighter than many compact competitors.
This reduced mass translates directly to less kinetic energy that needs to be dissipated during braking events. Honda’s engineers have capitalized on this advantage by designing a braking system that provides confident stopping power without over-engineering the components to the point where premature wear becomes inevitable.
The Civic’s brake system incorporates several subtle but effective features that extend pad life. The electronic brake distribution system continuously adjusts hydraulic pressure to maintain ideal brake balance between front and rear wheels across various driving conditions.
This prevents the front brakes from handling an excessive proportion of stopping duties, reducing the accelerated wear commonly seen in front brake pads on many vehicles.
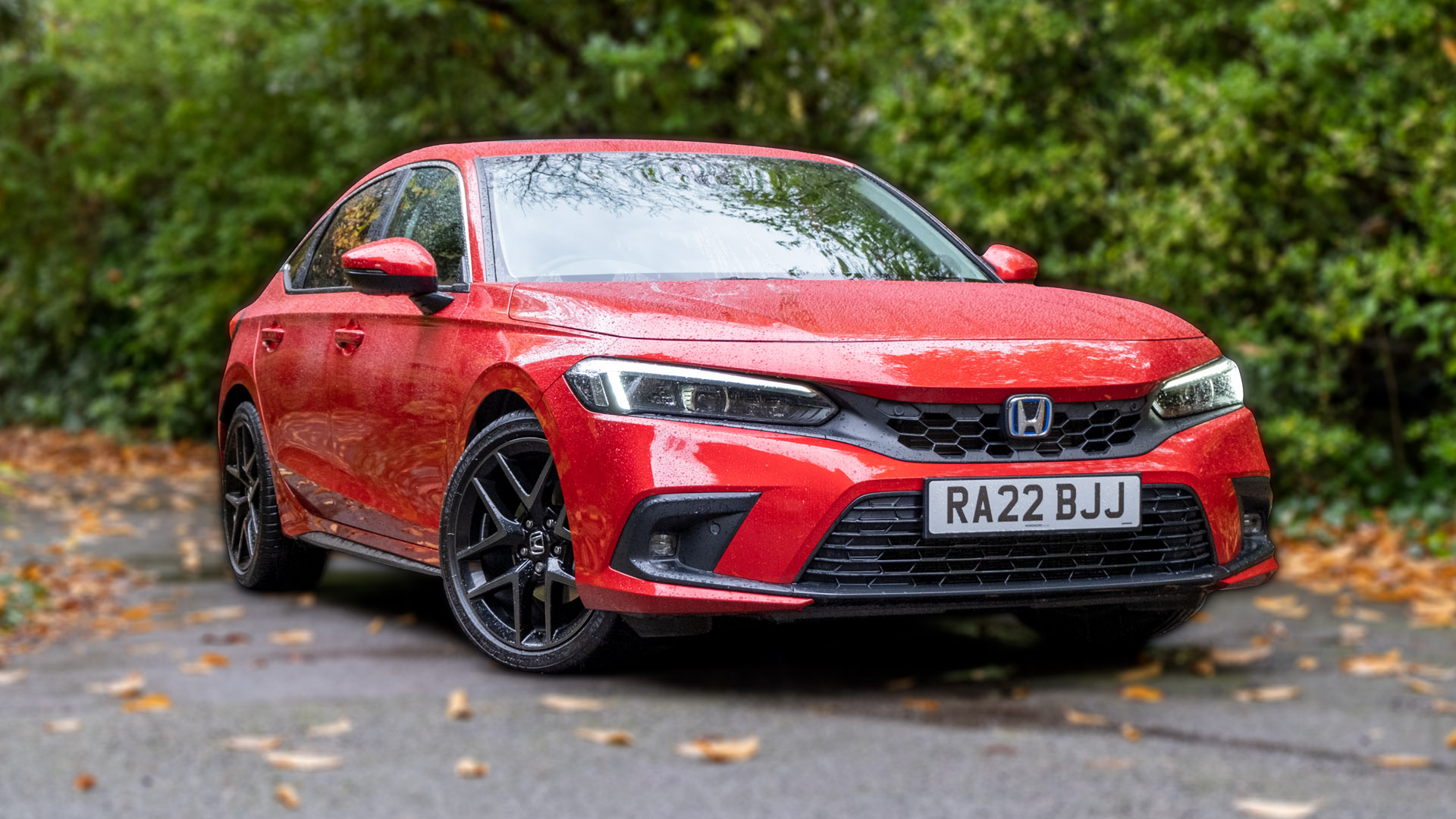
Material science plays a crucial role in the Civic’s brake longevity equation. Honda equips most non-performance Civics with semi-metallic brake pads that strike an optimal balance between initial bite, noise characteristics, and wear resistance.
These pads feature a progressive friction coefficient that increases with temperature, providing responsive performance during typical driving while avoiding the extremely high-temperature friction that can accelerate wear during more spirited driving sessions.
The vehicle’s suspension geometry further contributes to brake preservation by maintaining consistent tire contact patches throughout the suspension’s travel range.
This ensures that braking forces transmit efficiently to the road surface rather than creating excessive heat in the brake components themselves. Additionally, the Civic’s inherent handling balance reduces the tendency for drivers to “ride the brakes” through corners, a common habit that significantly accelerates pad wear.
Honda’s service data indicates that Civic owners who follow recommended maintenance schedules, including regular brake fluid exchanges every 30,000 miles, experience even longer brake pad lifespans due to the maintained hydraulic efficiency and reduced system contamination.
This comprehensive approach to braking system design and maintenance recommendations helps explain why Civic brake pads routinely outlast those in similarly sized competitors by 15,000 to 20,000 miles.
4. Subaru Outback
The Subaru Outback defies conventional expectations about brake pad longevity in all-wheel-drive vehicles. Typically, AWD systems add weight and complexity that accelerate brake wear, but the Outback achieves impressive brake pad lifespans of 65,000 to 85,000 miles under normal driving conditions.
This exceptional performance stems from Subaru’s holistic approach to the vehicle’s drivetrain and braking systems. At the heart of the Outback’s brake preservation capabilities lies Subaru’s symmetrical all-wheel-drive system.
Unlike reactive AWD systems that primarily operate in front-wheel drive until slippage occurs, Subaru’s system continuously distributes power to all four wheels.
This constant power distribution means that engine braking affects all four wheels equally, reducing the workload on the friction brakes during deceleration.
The vehicle’s boxer engine design further contributes by lowering the center of gravity, which promotes more stable braking characteristics and reduces the forward weight transfer that typically overworks front brake pads.
Subaru equips the Outback with oversized brake rotors relative to the vehicle’s weight class. These larger rotors provide enhanced thermal capacity, allowing heat to dissipate more effectively during braking events.
Lower operating temperatures directly correlate with reduced brake pad wear rates, particularly during challenging driving scenarios like mountain descents or towing situations where heat buildup can otherwise accelerate pad degradation.
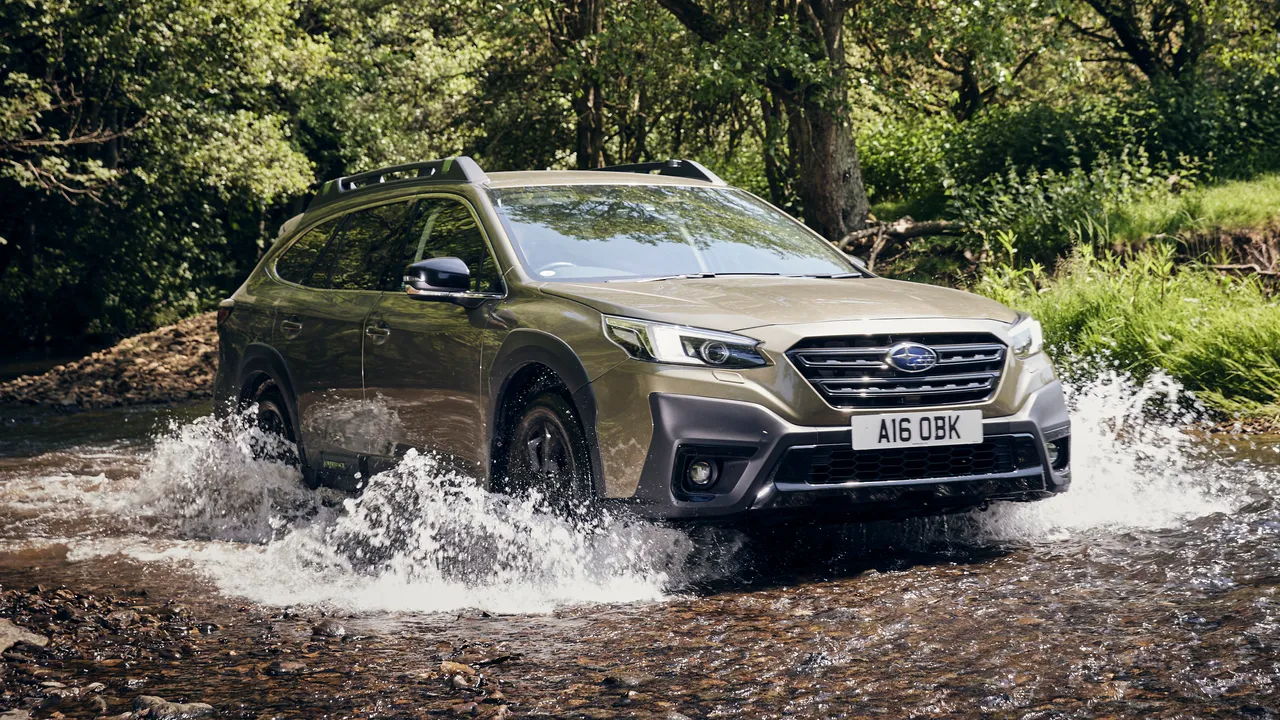
The Outback’s brake pad compounds themselves reflect careful engineering choices. Subaru utilizes ceramic-composite materials with higher-than-average silicon content, improving heat resistance while maintaining effective friction characteristics across a wide temperature range.
These pads feature progressive wear indicators that allow owners to monitor remaining pad life without removal, encouraging timely but not premature replacement.
Vehicle dynamics also play a crucial role in the Outback’s brake longevity story. The suspension system provides exceptional wheel articulation, ensuring consistent tire contact with the road surface even on uneven terrain.
This consistent contact means that braking forces transfer efficiently to the ground rather than creating excessive heat in the brake components. Additionally, the Outback’s X-Mode system, when engaged for off-road or slippery conditions, incorporates hill descent control that manages downhill speeds without heavy brake application.
Perhaps most impressively, the Outback achieves this brake longevity despite being frequently used in challenging conditions. Many Outback owners regularly venture off-pavement or into mountainous terrain environments that typically accelerate brake wear.
The vehicle’s ability to maintain long brake pad life even under these demanding scenarios speaks to the fundamental robustness of its braking system design and component quality.
Also Read: 5 Cars With Digital Dashboards That Age Well and 5 That Glitch Out
5. Mazda MX-5 Miata
The Mazda MX-5 Miata proves that sports cars needn’t be brake pad destroyers. While many performance-oriented vehicles sacrifice component longevity for stopping power, the Miata achieves the remarkable feat of delivering both engaging braking performance and exceptional pad life, with owners routinely reporting 60,000 to 75,000 miles before replacement becomes necessary.
This impressive durability stems from a perfect storm of weight management, engineering precision, and driving dynamics. At approximately 2,400 pounds, the Miata stands as one of the lightest production cars available in today’s market.
This featherweight design fundamentally changes the physics of deceleration, requiring significantly less braking force and generating proportionally less brake pad wear to achieve the same stopping performance as heavier vehicles.
Mazda’s “gram strategy” philosophy, which scrutinizes every component for weight-saving opportunities, creates a virtuous cycle where lighter weight allows for appropriately sized rather than oversized braking components.
The Miata’s brake system features perfectly matched components for its weight and performance envelope. Unlike many sports cars that utilize oversized brakes designed to withstand track abuse (at the cost of rapid street wear), the Miata’s braking system prioritizes balance and efficiency.
The single-piston front calipers and relatively modest rotor dimensions might seem underwhelming compared to multi-piston setups in other sports cars, but they provide ideal thermal characteristics for the vehicle’s weight and typical use cases.
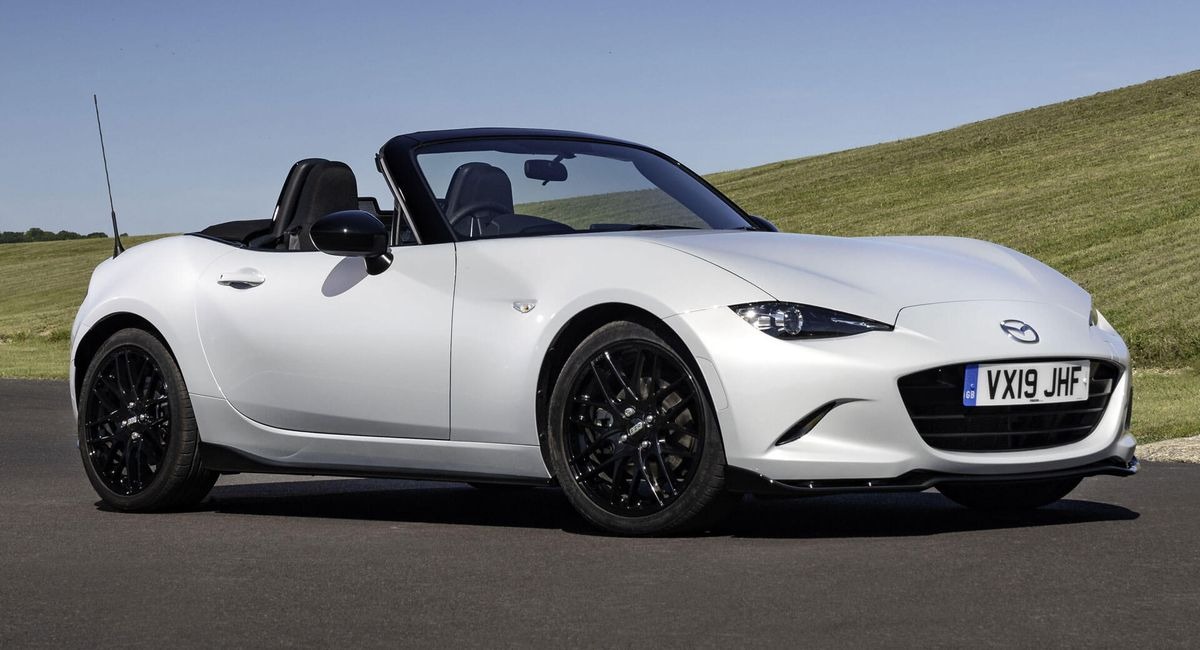
Mazda engineers have optimized the Miata’s brake pad compounds specifically for its unique requirements. The standard pads utilize a semi-metallic composition with higher-than-average organic content, providing excellent initial bite and modulation while resisting the extreme heat cycling that accelerates pad wear.
These compounds are engineered to operate most efficiently within the temperature range typically encountered during spirited street driving rather than the extreme temperatures seen on racetracks.
The vehicle’s 50:50 weight distribution and low center of gravity further contribute to brake preservation by ensuring balanced weight transfer during deceleration.
This even distribution prevents the front-heavy braking dynamics common in many vehicles, where the front pads handle disproportionate workloads and wear prematurely as a result.
Additionally, the Miata’s direct steering feel and responsive handling characteristics allow drivers to slow the car partially through cornering forces rather than relying solely on brakes when approaching turns.
Perhaps counterintuitively, the Miata’s manual transmission (selected by a high percentage of buyers) significantly extends brake pad life through engine braking.
Downshifting naturally slows the vehicle without brake application, particularly noticeable on the flowing back roads that Miata owners tend to favor.
This driving style, encouraged by the car’s engaging transmission, naturally preserves brake components while enhancing the connected driving experience that defines the Miata ownership experience.
5 Cars That Chew Through Brake Pads
Despite manufacturer claims of durability, these notorious models consume brake pads at alarming rates, often requiring replacement after just 15,000 miles of normal driving.
Their aggressive brake bias and poor heat management cause accelerated pad wear, creating a recurring maintenance expense that quickly erodes any initial purchase savings.
Owners report constant brake dust accumulation on wheels and frequent squealing sounds as early warning signs of the premature deterioration plaguing these problematic systems.
What should be routine maintenance becomes a significant ownership cost, with some drivers reporting spending thousands on brake service during normal lease periods.
1. BMW M3/M4
The BMW M3 and its two-door M4 sibling represent the pinnacle of Bavarian performance engineering, delivering exhilarating driving experiences at the expense of brake pad longevity.
These high-performance machines typically require brake pad replacement every 20,000 to 30,000 miles under normal driving conditions and potentially much sooner under spirited use. This accelerated wear rate stems from multiple engineering and usage factors inherent to these performance-focused vehicles.
At approximately 3,800 pounds, modern M3/M4 models carry substantially more mass than their predecessors, requiring significantly more braking force to decelerate effectively.
This weight, combined with the vehicles’ capability to reach high speeds rapidly, thanks to turbocharged six-cylinder engines producing over 500 horsepower in Competition models, creates a demanding scenario for brake components.
The kinetic energy that must be dissipated during braking increases exponentially with speed, placing enormous thermal loads on the brake pads during aggressive driving.
BMW equips these vehicles with compound brake pads designed primarily for performance rather than longevity. These pads feature high-friction compounds that deliver exceptional initial bite and fade resistance under extreme conditions but wear significantly faster than comfort-oriented compositions.
The M-specific brake calibration favors aggressive initial pad engagement to provide the direct pedal feel that performance drivers expect, but this characteristic accelerates wear during routine driving scenarios.
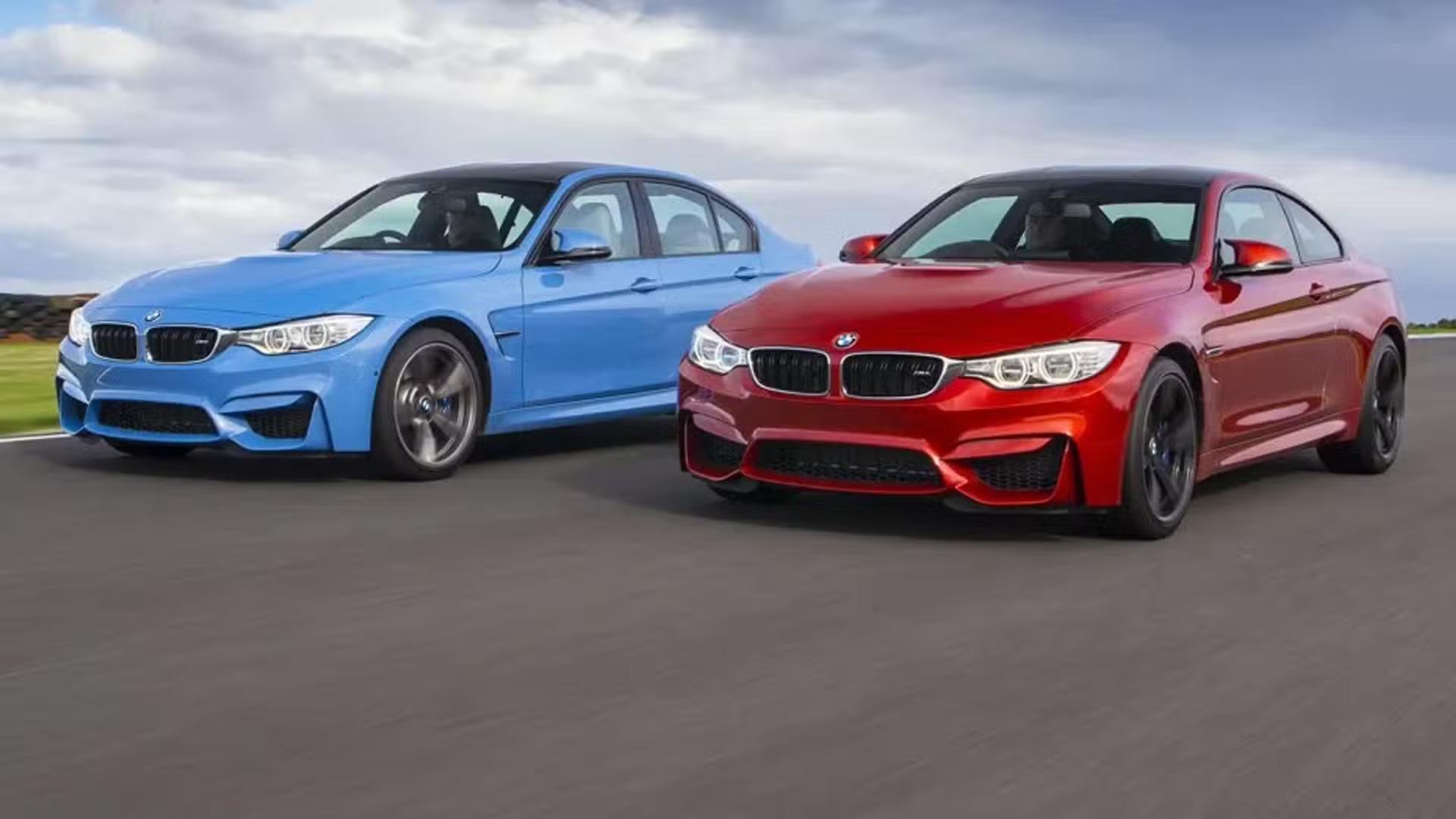
The vehicles’ driving modes further influence brake pad consumption. When operated in Sport or Sport Plus settings, the throttle mapping becomes more aggressive, encouraging rapid acceleration followed by harder braking events.
Additionally, the M3/M4’s limited-slip differential and performance-oriented stability control settings allow drivers to explore the vehicles’ handling limits more frequently, scenarios that invariably involve heavy braking into corners.
The typical M3/M4 owner’s driving profile substantially differs from mainstream vehicle operators. These enthusiast-focused models attract drivers who regularly exploit their performance capabilities, whether on winding back roads, authorized track days, or even during spirited highway on-ramp acceleration and deceleration cycles.
This usage pattern dramatically accelerates brake wear compared to more conservative driving styles. Interestingly, BMW acknowledges this consumption rate in its maintenance recommendations, categorizing brake pads as “wear items” similar to tires rather than long-life components.
The vehicles’ instrument cluster features sophisticated pad wear sensors that provide early warning when replacement becomes necessary, typically illuminating when approximately 20% pad material remains, a feature necessitated by the predictably short service intervals.
This transparent approach reflects BMW’s understanding that exceptional performance inevitably comes with maintenance implications that enthusiast owners generally accept as part of the ownership experience.
2. Porsche Cayenne
The Porsche Cayenne exemplifies the challenging physics problem of creating a performance SUV. Combining substantial mass with sports car aspirations, this luxury performance vehicle typically requires brake pad replacement every 25,000 to 35,000 miles and potentially much sooner when driven enthusiastically.
This accelerated wear pattern stems from the fundamental contradiction inherent in the vehicle’s design brief: delivering Porsche-worthy driving dynamics in a package weighing over 4,500 pounds.
The Cayenne’s substantial weight creates enormous kinetic energy during movement, requiring exceptional braking force to arrest. Particularly in Turbo and GTS variants with outputs exceeding 500 horsepower, the vehicle can accelerate to highway speeds with astonishing rapidity, creating scenarios where equally rapid deceleration becomes necessary.
The energy dissipation requirements in these braking events generate extreme heat in the brake system, often exceeding 900°F during aggressive driving dramatically accelerating pad wear.
Porsche engineers have attempted to mitigate these challenges through oversized braking components, with front rotors measuring up to 415mm (16.3 inches) on higher-performance variants.
These massive rotors provide improved thermal capacity but require correspondingly aggressive pad compounds to generate appropriate friction levels.
These high-performance compounds prioritize fade resistance and initial bite over longevity, accepting accelerated wear as a necessary compromise for consistent performance.
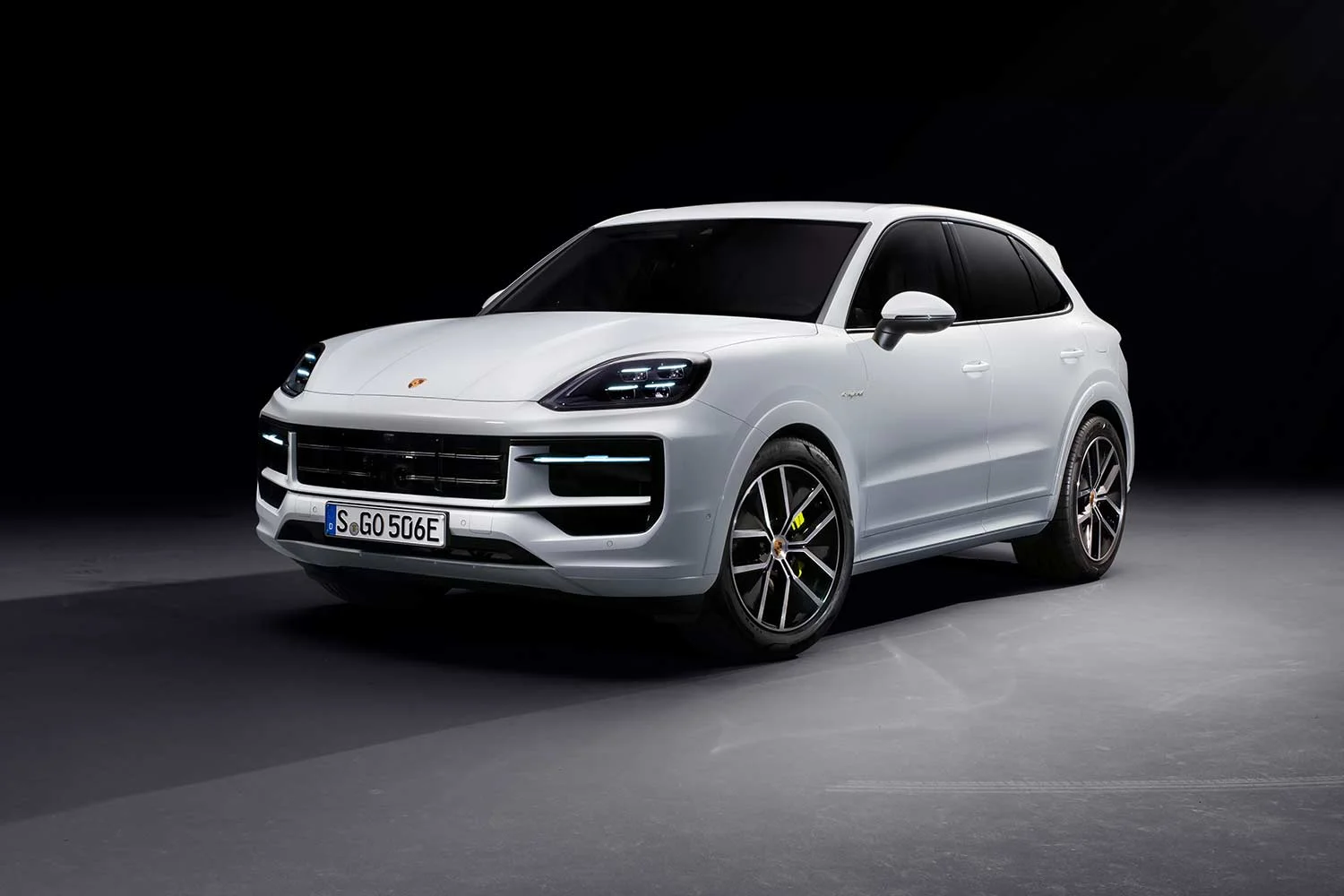
The Cayenne’s brake system employs multi-piston fixed calipers (up to 10 pistons on Turbo models) that distribute clamping force more evenly across the pad surface.
While this design improves braking performance and pedal feel, it also ensures that the entire pad surface experiences maximum pressure during every braking event, eliminating the partial-pad engagement that sometimes extends pad life in sliding-caliper designs found on more mainstream vehicles.
Vehicle usage patterns further compound wear issues. Cayenne owners typically expect and utilize the vehicle’s capability to accelerate rapidly from stoplights, navigate winding roads at speeds that defy its SUV categorization, and handle occasional towing duties.
This diverse usage profile creates varied thermal cycling in the brake components, heating during aggressive driving, then cooling during highway cruising a pattern particularly detrimental to pad longevity.
Porsche’s optional Ceramic Composite Brake (PCCB) system improves heat resistance but doesn’t substantially extend pad life, as the ceramic rotors require specific pad compounds that still experience similar wear rates.
The primary advantage comes from the rotors themselves, which can last through multiple pad replacement cycles, unlike the standard iron rotors that typically require replacement with every second or third pad change due to surface degradation and minimum thickness limitations.
3. Jeep Grand Cherokee SRT/Trackhawk
The Jeep Grand Cherokee SRT and its even more powerful Trackhawk variant represent the extreme edge of the performance SUV spectrum, delivering muscle car acceleration in a high-riding package, a combination that wreaks havoc on brake components.
These high-performance Jeeps typically require brake pad replacement every 20,000 to 30,000 miles under mixed driving conditions, with some owners reporting even shorter intervals under aggressive use.
This accelerated wear stems from the fundamental physics challenge of repeatedly stopping a 5,000+ pound vehicle designed for speeds that would impress dedicated sports cars.
The Trackhawk, with its supercharged 6.2-liter Hellcat V8 producing 707 horsepower, can accelerate to 60 mph in just 3.5 seconds. This blistering acceleration capability creates scenarios where equally dramatic deceleration becomes necessary, placing enormous thermal loads on the braking system.
A single aggressive stop from highway speeds can generate brake temperatures exceeding 1,000°F well into the range where pad material experiences accelerated degradation with each application.
To combat these extreme conditions, Jeep equips these models with massive Brembo braking systems featuring 15.75-inch front rotors clamped by six-piston calipers.
While impressive on paper, even these substantial components struggle with the vehicle’s mass during repeated high-performance driving scenarios.
The pads use high-temperature compounds designed to resist fade under extreme conditions, but these compounds typically sacrifice longevity for performance a necessary trade-off to ensure safety under the most demanding circumstances.
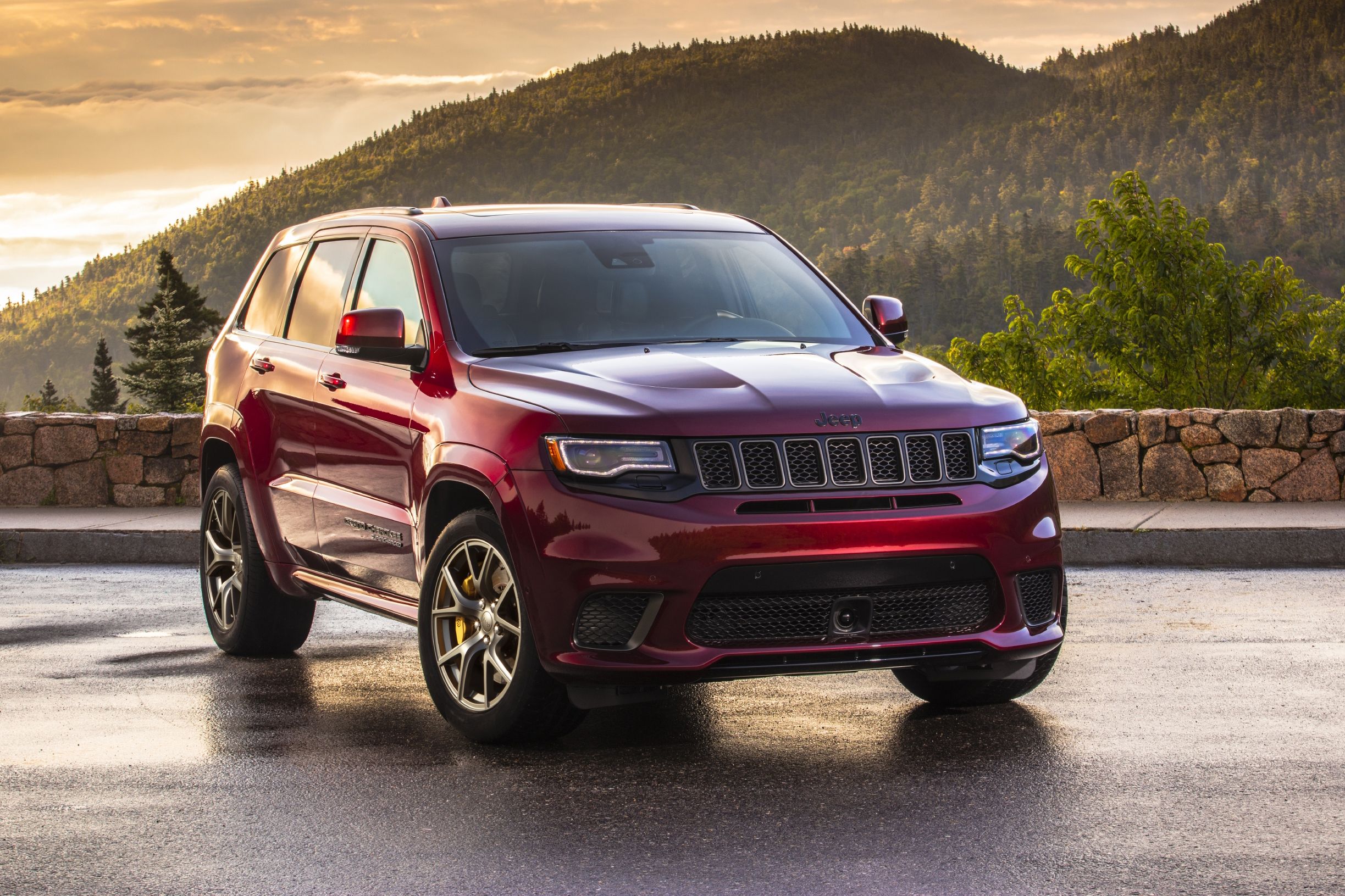
The SRT and Trackhawk’s performance-oriented suspension geometry, featuring reduced body roll and improved front-end stability, inadvertently contributes to accelerated brake wear.
The more direct weight transfer during braking events places even greater demands on the front brake components, which handle approximately 70% of stopping duties.
This front-biased braking distribution accelerates pad wear on the front axle, often requiring front pad replacement while rear pads retain significant material.
The typical driving profile of SRT and Trackhawk owners further compounds wear issues. These vehicles attract enthusiasts who appreciate their unique combination of straight-line acceleration, imposing presence, and all-weather capability.
This ownership demographic tends to exploit the vehicles’ performance potential more frequently than typical SUV owners, whether at sanctioned drag strip events, during spirited back-road driving, or simply through aggressive urban traffic navigation.
Interestingly, Jeep acknowledges these challenges in their official maintenance schedules, which recommend brake inspections at shorter intervals for SRT and Trackhawk models compared to standard Grand Cherokee variants.
The vehicles’ onboard diagnostics include sophisticated pad wear sensors and brake temperature monitoring, providing early warnings when components approach their service limits, features necessitated by the predictable wear patterns these high-performance SUVs exhibit throughout their operational lives.
4. Mercedes-AMG GT
The Mercedes-AMG GT represents the pinnacle of German grand touring performance, delivering supercar acceleration and handling in a relatively practical package, albeit one that consumes brake pads at an alarming rate.
These hand-built performance machines typically require brake pad replacement every 15,000 to 25,000 miles under mixed driving conditions, with even shorter intervals when driven as their engineers intended.
This accelerated wear pattern stems from several factors inherent to the vehicle’s design philosophy and typical usage profile. At the heart of the AMG GT’s brake consumption issue lies its formidable powertrain, a hand-assembled 4.0-liter biturbo V8 producing between 469 and 720 horsepower depending on the specific variant.
This prodigious power enables the vehicle to achieve 0-60 mph times as low as 3.1 seconds and top speeds approaching 200 mph. The capacity to reach extraordinary velocities necessitates equally extraordinary stopping power, placing enormous thermal demands on the braking system during deceleration events.
Mercedes equips the AMG GT with an advanced composite braking system featuring multi-piston fixed calipers (up to 6 pistons front, 4 rear) clamping massive ventilated and perforated rotors.
While visually impressive and capable of generating tremendous stopping force, this system prioritizes fade resistance and pedal feel over component longevity.
The high-friction pad compounds necessary to complement these oversized components generate optimal performance when operating at raised temperatures a characteristic that accelerates material wear during routine driving when optimal operating temperatures aren’t consistently maintained.
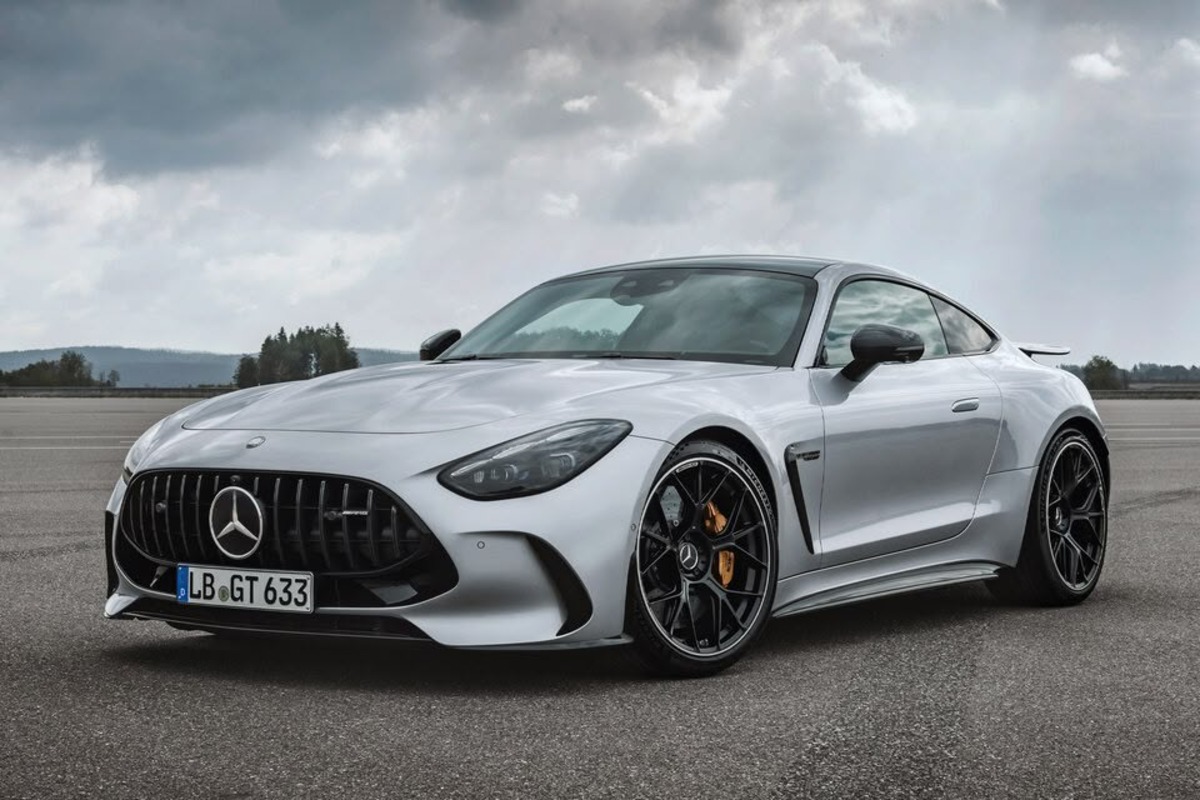
The vehicle’s transmission calibration further influences brake wear patterns. The AMG Speedshift dual-clutch transmission, particularly when operated in Sport+ or Race modes, delivers aggressive downshifts accompanied by throttle blips that encourage performance-oriented driving styles.
This calibration naturally leads drivers to approach corners at higher speeds, requiring harder braking inputs and generating higher brake temperatures than would occur with more conservative driving patterns.
The AMG GT’s typical ownership demographic significantly impacts brake component longevity. These vehicles attract driving enthusiasts and performance-oriented owners who regularly explore the car’s considerable capabilities.
Many AMG GT owners participate in track days, high-performance driving events, or simply enjoy spirited drives on challenging roads, all scenarios that dramatically accelerate brake wear compared to typical commuting or touring use.
Mercedes acknowledges these wear characteristics by incorporating sophisticated brake monitoring systems that analyze remaining pad thickness and provide early replacement warnings.
Additionally, the manufacturer offers optional ceramic composite brakes (AMG Carbon Ceramic Braking System) that provide improved fade resistance during track use but don’t significantly extend pad life.
They primarily benefit rotor longevity, allowing the ceramic rotors to survive multiple pad replacement cycles, unlike their conventional counterparts.
5. Tesla Model S Plaid
The Tesla Model S Plaid represents the cutting edge of electric performance, delivering hypercar acceleration figures in a practical sedan package.
However, this remarkable performance envelope comes with significant consequences for brake component longevity, with owners typically reporting brake pad replacement intervals of 25,000 to 35,000 miles, substantially shorter than many conventional vehicles despite the benefits of regenerative braking.
This seemingly contradictory situation stems from several factors unique to high-performance electric vehicles. At approximately 4,800 pounds, the Model S Plaid carries substantial mass due to its large battery pack and electric drivetrain components.
This weight, combined with the vehicle’s astonishing acceleration capability (0-60 mph in less than 2 seconds under ideal conditions), creates enormous kinetic energy that must be dissipated during deceleration events.
While regenerative braking handles a significant portion of routine slowing, the system’s maximum regenerative capacity (limited by battery charging constraints) proves insufficient during aggressive driving or emergency stopping scenarios.
The friction braking system consequently experiences dramatic thermal loading when called upon, particularly during repeated high-performance driving.
Tesla equips the Plaid with substantial braking hardware, including 390mm front rotors with 6-piston Brembo calipers, but even these robust components face challenges when repeatedly arresting the vehicle’s substantial mass from high speeds.
The pad compounds, selected for high-temperature stability and initial bite, necessarily sacrifice longevity to maintain performance consistency under these demanding conditions.
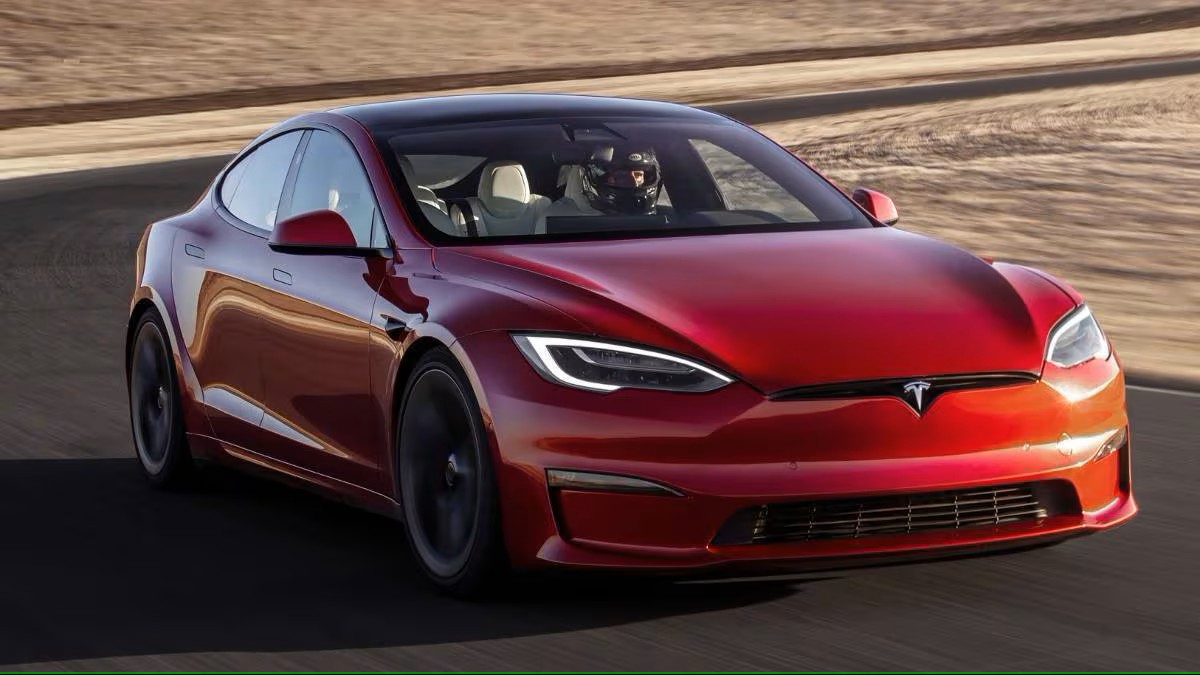
The Plaid’s regenerative braking system presents a unique wear pattern challenge. During routine driving, the friction brakes remain largely disengaged as the electric motors handle deceleration.
However, this means the pads frequently cool completely between applications, creating a thermal cycling scenario where pads repeatedly heat rapidly from ambient temperature to several hundred degrees during aggressive stops.
This thermal shock pattern accelerates material degradation compared to systems that maintain more consistent operating temperatures. Driver behavior significantly influences brake wear in the Plaid.
The vehicle’s breathtaking acceleration capability naturally encourages spirited driving, with owners frequently demonstrating the “Plaid Mode” launch control feature that enables the headline-grabbing acceleration figures.
These rapid acceleration events often conclude with equally aggressive deceleration, creating significant brake heat and corresponding pad wear despite the limited frequency of friction brake usage.
Tesla has acknowledged these challenges through ongoing brake system development. The manufacturer offers an optional “Carbon Ceramic Brake Kit” specifically engineered for track use and high-performance driving scenarios, featuring more temperature-stable components.
However, even with these upgraded components, pad wear remains a consideration for owners who regularly exploit the vehicle’s performance capabilities.
This reality reflects the fundamental physics challenge of managing extreme performance in a production vehicle regardless of powertrain type. Ultimately, the energy of motion must be dissipated, and brake pads bear the consequences of this immutable fact.
Also Read: 5 Cars With Fast Touchscreens and 5 That Lag Like Old Phones