The modern crossover has become the vehicle of choice for millions of drivers seeking the perfect balance between SUV versatility and sedan-like handling. However, not all crossovers are created equal when it comes to suspension system reliability.
While some models sail past 100,000 miles with minimal suspension issues, others seem to require constant attention from as early as 30,000 miles. This difference in reliability often stems from engineering choices, build quality, and the intended purpose of each vehicle.
Suspension systems bear the brunt of everyday driving challenges from pothole-riddled city streets to rough country roads. They’re responsible for maintaining ride comfort, handling, and stability under various conditions.
A reliable suspension isn’t just about avoiding repair costs; it directly impacts safety, performance, and resale value. For the average crossover owner, unexpected suspension repairs can range from several hundred to thousands of dollars, making suspension reliability a crucial but often overlooked factor when choosing a vehicle.
In this comprehensive guide, we’ll examine five crossover models known for exceptional suspension durability and five notorious for frequent suspension problems.
We’ll explore the engineering factors behind their performance, common failure points, ownership costs, and what prospective buyers should watch for.
Whether you’re in the market for a new crossover or maintaining your current vehicle, understanding these suspension tendencies could save you significant time, money, and frustration.
5 Crossovers That Rarely Need Suspension Work
These exceptionally durable crossovers feature overbuilt suspension components and intelligent designs that withstand years of punishment from potholed urban streets and rough country roads.
Advanced materials and precise manufacturing tolerances create suspension systems that maintain ride quality and handling characteristics well beyond 150,000 miles with minimal intervention.
Owners report crossing the 100,000-mile threshold without replacing a single control arm, strut, or bushing, a testament to the engineering priority placed on long-term durability. The initial investment in these reliable platforms pays dividends through dramatically reduced maintenance costs and fewer unexpected repair bills throughout the ownership experience.
1. Toyota RAV4 (2013-Present)
The Toyota RAV4 stands as a testament to Toyota’s legendary reputation for building vehicles that simply refuse to quit. Since its redesign in 2013 and continuing through subsequent generations, the RAV4 has consistently demonstrated exceptional suspension durability even under challenging conditions.
The secret lies in Toyota’s conservative engineering approach that prioritizes reliability over cutting-edge technology, using time-tested suspension components that sacrifice some handling sharpness for long-term dependability.
The RAV4 employs a straightforward MacPherson strut front suspension and double wishbone rear configuration, built with high-quality bushings and components that resist deterioration.
Toyota’s superior rust protection also plays a significant role in suspension longevity, particularly in regions where road salt and moisture accelerate corrosion.
This attention to weatherproofing means RAV4 owners in harsh climates don’t face the premature control arm and subframe issues common in competing models.
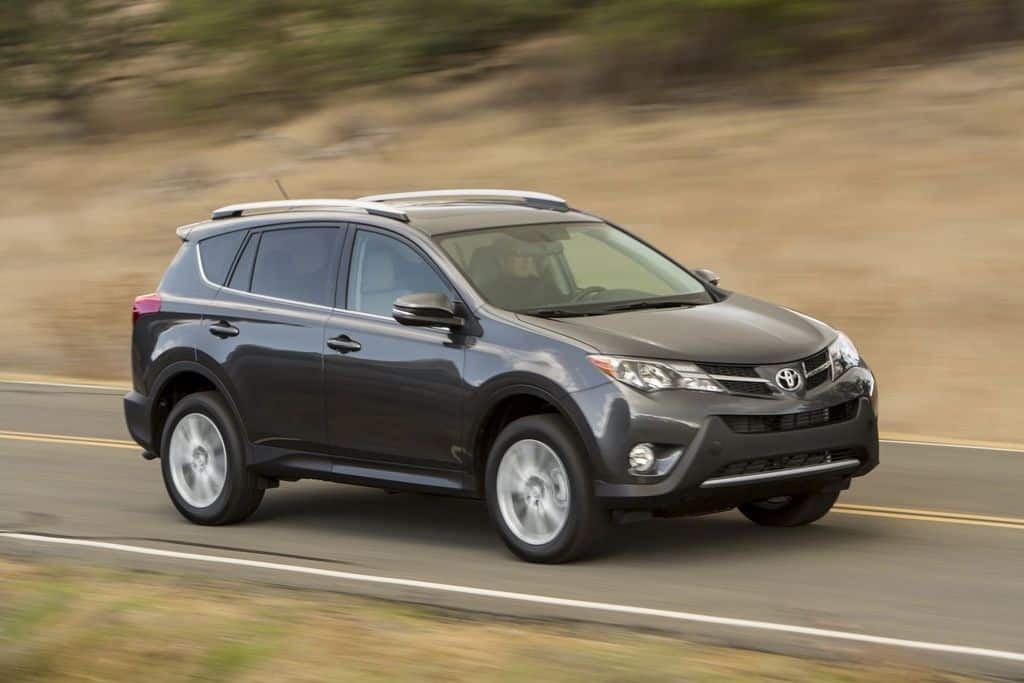
Owner data across multiple reliability surveys consistently shows RAV4s regularly exceeding 150,000 miles before requiring significant suspension work beyond routine maintenance.
When issues do eventually arise, they typically manifest as gradual bushing wear rather than catastrophic failures, giving owners ample warning before repairs become necessary.
The simplicity of the system also translates to lower repair costs when components finally do need replacement. Perhaps most telling is how the RAV4 performs in fleets and rental services, where vehicles endure punishing conditions and minimal maintenance.
Even in these demanding scenarios, the RAV4’s suspension maintains its integrity remarkably well. Toyota’s 10-year suspension warranty in some markets further demonstrates their confidence in the system’s durability.
For prospective buyers, this translates to predictable ownership costs and exceptional resale value. The most common owner-reported suspension maintenance typically involves nothing more than occasional strut replacements around 120,000-150,000 miles far beyond the point where many competitors require complete suspension overhauls.
2. Subaru Forester (2014-Present)
The Subaru Forester has cultivated a dedicated following among outdoor enthusiasts and all-weather drivers, largely due to its exceptionally durable suspension system that handles everything from urban commuting to off-road adventures.
What makes the Forester’s suspension particularly noteworthy is its ability to withstand abuse while maintaining consistent ride quality throughout its lifespan, even when regularly subjected to rough terrain.
At the heart of this durability is Subaru’s unique approach to chassis design. Unlike many crossovers built on modified car platforms, the Forester features a purpose-built chassis with substantial ground clearance and long-travel suspension components designed from the outset for mixed-terrain capability.
The fully independent suspension system utilizes larger-than-average bushings and ball joints that absorb punishment without rapid deterioration, while Subaru’s excellent weight distribution minimizes uneven wear patterns.
Particularly impressive is the Forester’s resistance to strut and shock absorber failure. While many crossovers require replacement of these components by 60,000 miles, Forester owners routinely report original equipment lasting beyond 100,000 miles with minimal performance degradation.
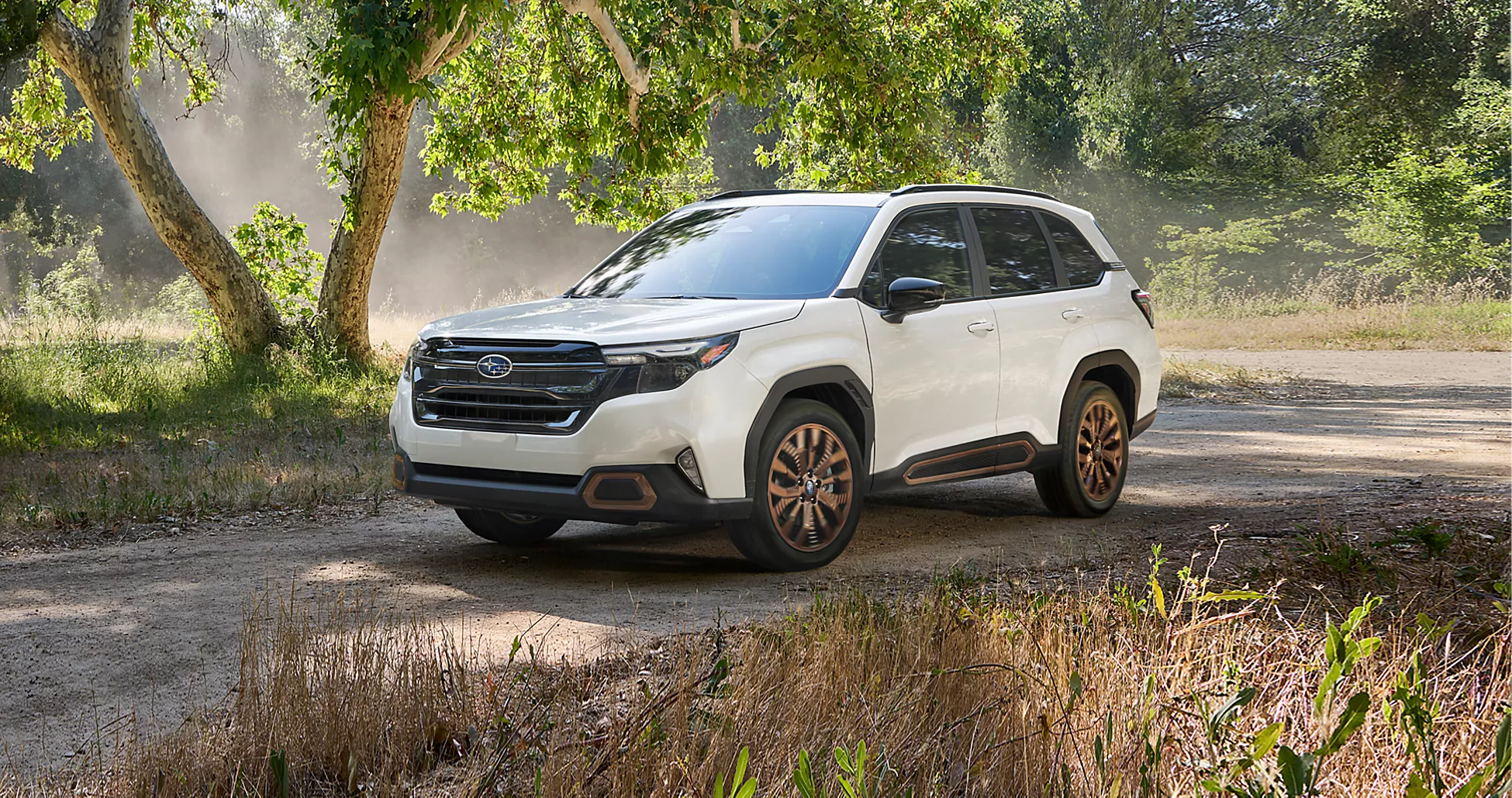
The vehicle’s symmetrical all-wheel-drive system contributes to this longevity by distributing forces more evenly across all suspension components, preventing the accelerated wear common in front-wheel-drive crossovers.
Forester owners in online forums and reliability surveys consistently highlight the vehicle’s ability to maintain alignment specifications even after years of use on rough roads.
This resistance to suspension geometry changes not only preserves handling characteristics but also prevents the cascading wear issues that plague less robust systems.
When minor issues do develop, they typically manifest as control arm bushing wear around 120,000 miles, considerably later than competitors. The most telling evidence of the Forester’s suspension quality comes from owners in extreme environments.
From the pothole-riddled streets of northeastern cities to the rugged mountain roads of Colorado, Foresters maintain their ride height and handling characteristics with minimal intervention.
Subaru’s continuous refinement of the system across generational changes has only improved this already impressive reliability record, making the post-2014 models particularly noteworthy for suspension durability.
3. Honda CR-V (2012-Present)
The Honda CR-V has established itself as a benchmark for suspension reliability in the compact crossover segment, consistently outperforming competitors in long-term durability tests and owner satisfaction surveys.
Honda’s meticulous engineering approach is evident in every aspect of the CR-V’s suspension design, which prioritizes long-term reliability without compromising the vehicle’s car-like handling characteristics that owners prize.
Honda’s success with the CR-V’s suspension stems from its sophisticated yet conservative approach to component design. The vehicle utilizes a MacPherson strut front suspension with a multi-link rear configuration, built with precision-manufactured components that maintain tight tolerances even after years of service.
Particularly notable is Honda’s use of high-quality, properly-engineered rubber compounds in bushings and isolators, which resist the hardening and cracking that often necessitates premature repairs in lesser systems.
CR-V owners consistently report reaching the 100,000-mile mark with virtually no suspension-related issues beyond routine maintenance. When components do eventually require attention, the progression is typically gradual and predictable.
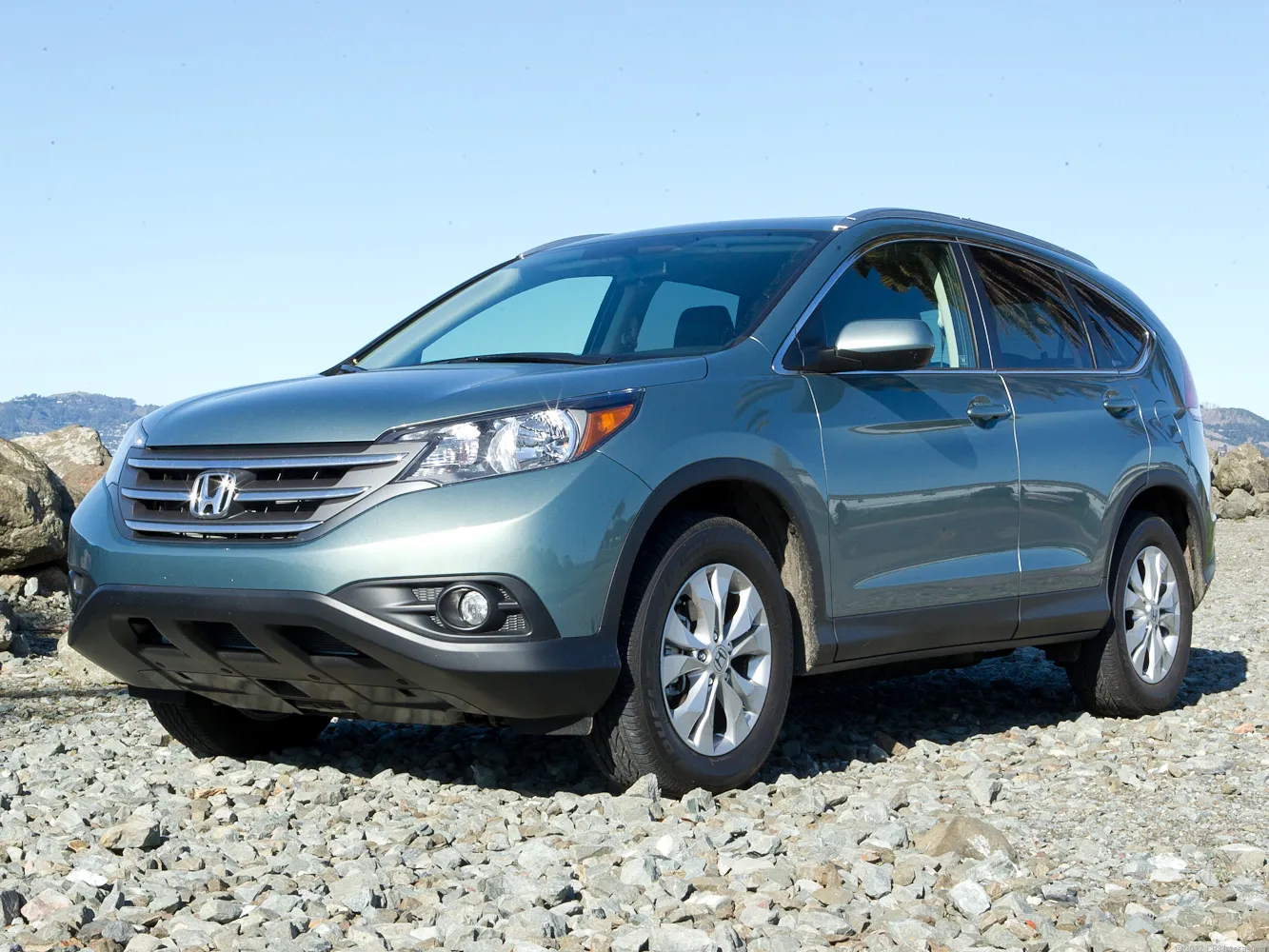
The most common first repair involves rear compliance bushings around 120,000 miles, providing ample warning before replacement becomes necessary. This predictable wear pattern allows owners to plan maintenance rather than respond to sudden failures.
Honda’s commitment to proper suspension geometry also contributes significantly to component longevity. The CR-V maintains excellent weight distribution and appropriate suspension travel, preventing the overloading of any single component that accelerates wear in many competitive systems.
This balanced approach means that when repairs eventually become necessary, they typically involve individual components rather than complete suspension rebuilds.
The CR-V’s suspension durability is particularly impressive considering its widespread use in varied environments. From urban delivery fleets to family vehicles in rural areas, the CR-V maintains consistent performance characteristics regardless of operating conditions.
Honda’s continuous refinement of the platform across generational changes has only enhanced this reliability, with incremental improvements addressing the few weak points identified in earlier iterations.
For buyers seeking a crossover that delivers both engaging driving dynamics and exceptional suspension longevity, the CR-V stands as one of the segment’s most compelling options.
4. Mazda CX-5 (2017-Present)
The Mazda CX-5 represents a remarkable engineering achievement in the crossover segment, delivering both exceptional handling precision and outstanding suspension durability.
Unlike many competitors that sacrifice long-term reliability for initial ride comfort, Mazda has developed a suspension system that maintains its performance characteristics well beyond 100,000 miles with minimal intervention.
This accomplishment becomes even more impressive considering the CX-5’s sporty driving dynamics, which typically place greater demands on suspension components.
Mazda’s success with the CX-5 suspension stems from its “Skyactiv” engineering philosophy, which focuses on optimizing every component for maximum efficiency and durability.
The front MacPherson strut and rear multi-link suspension utilize higher-quality materials than typically found in this price segment, with particular attention paid to bushing compounds that resist deterioration from heat cycling and environmental exposure.
Mazda engineers have also precisely calibrated the suspension geometry to minimize uneven tire wear and component stress during everyday driving conditions.
The 2017 redesign marked a significant advancement in suspension durability, with Mazda addressing the few weakness points identified in earlier generations.
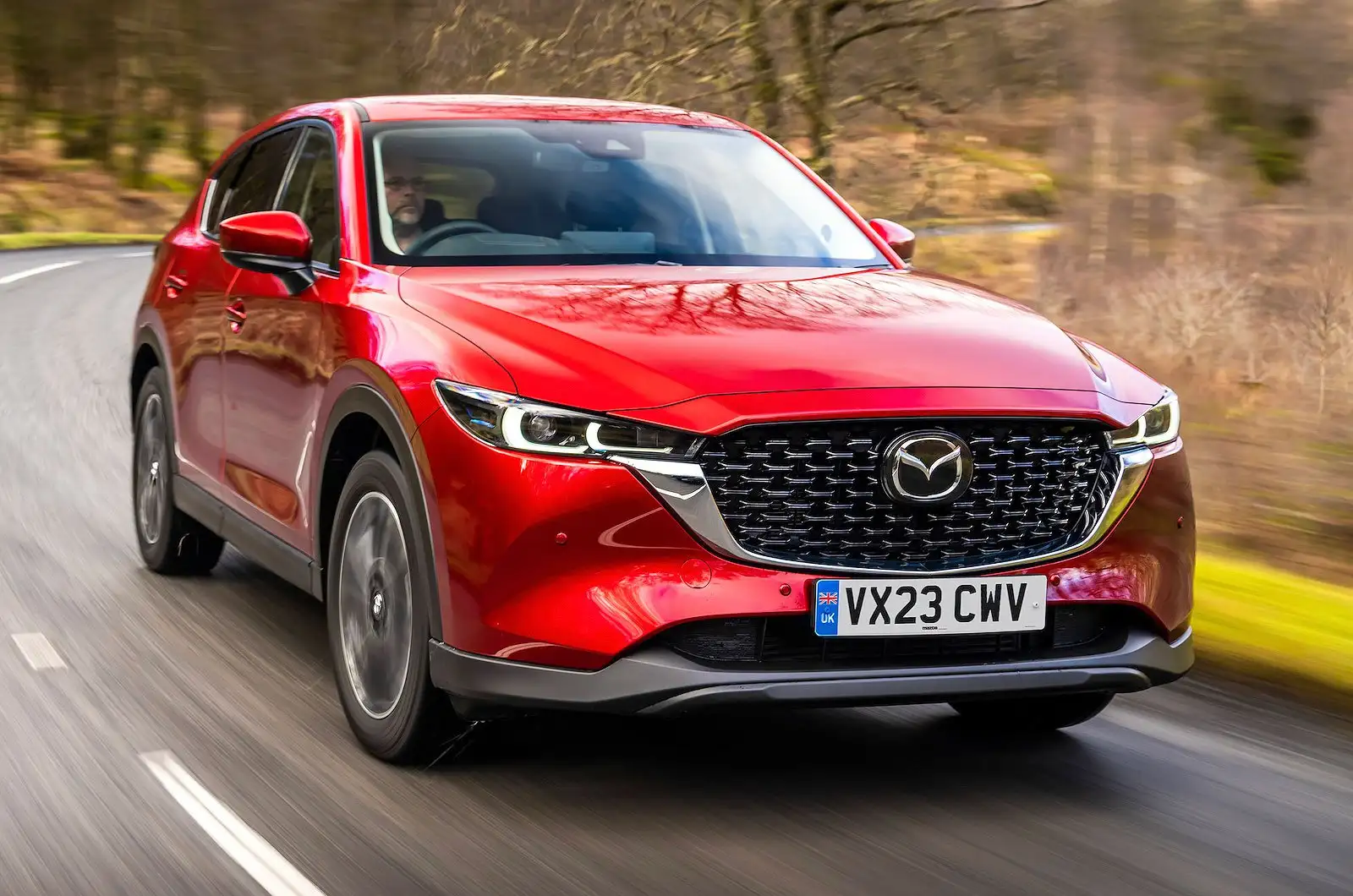
Owner reports and service records from this generation consistently show remarkably low rates of suspension-related warranty claims compared to segment averages.
Even components normally considered wear items, such as stabilizer bar links and control arm bushings, routinely exceed 120,000 miles before requiring replacement in the CX-5.
Perhaps most impressive is how the CX-5’s suspension maintains its precise handling characteristics over time. While many crossovers develop increasing body roll and diminished responsiveness as suspension components wear, the CX-5 preserves its engaging driving dynamics with minimal degradation.
This resistance to performance deterioration stems from Mazda’s use of more robust mounting points and better isolation techniques that prevent chassis flex from compromising suspension alignment.
The CX-5’s suspension reliability extends across diverse driving conditions, from smooth highways to rough urban environments. Owner forums consistently report original equipment struts and shocks maintaining effectiveness beyond 100,000 miles, with many reaching 130,000 miles before replacement becomes necessary.
When maintenance is eventually required, the modular design of the system makes repairs straightforward and typically less expensive than competitors with more complex arrangements.
For drivers seeking both driving enjoyment and long-term durability, the CX-5’s suspension system represents one of the strongest offerings in the crossover market.
Also Read: 5 Cars With Longest Brake Pad Lifespans and 5 That Chew Through Pads
5. Lexus NX (2015-Present)
The Lexus NX exemplifies how proper engineering and superior component quality can create a crossover suspension system that performs exceptionally well throughout the vehicle’s lifespan.
As Toyota’s luxury division, Lexus approaches suspension design with an uncompromising commitment to durability while still delivering the refined ride quality luxury buyers expect.
This balanced approach has resulted in the NX becoming one of the most dependable luxury crossovers from a suspension perspective. What sets the Lexus NX apart from competitors is its overbuilt nature.
While many luxury crossovers prioritize initial ride softness over long-term durability, Lexus engineers the NX suspension with significantly more structural margin than necessary for typical driving conditions.
The front independent MacPherson strut and rear double-wishbone system utilize higher-grade aluminum components and more substantial mounting points than similar-sized vehicles, preventing the gradual loosening and geometry changes that plague many luxury competitors over time.
Particularly noteworthy is Lexus’s superior approach to electronic suspension components. While many European luxury crossovers suffer from frequent failures of electronic dampers and height sensors, the NX utilizes more conservatively designed systems with better environmental protection.
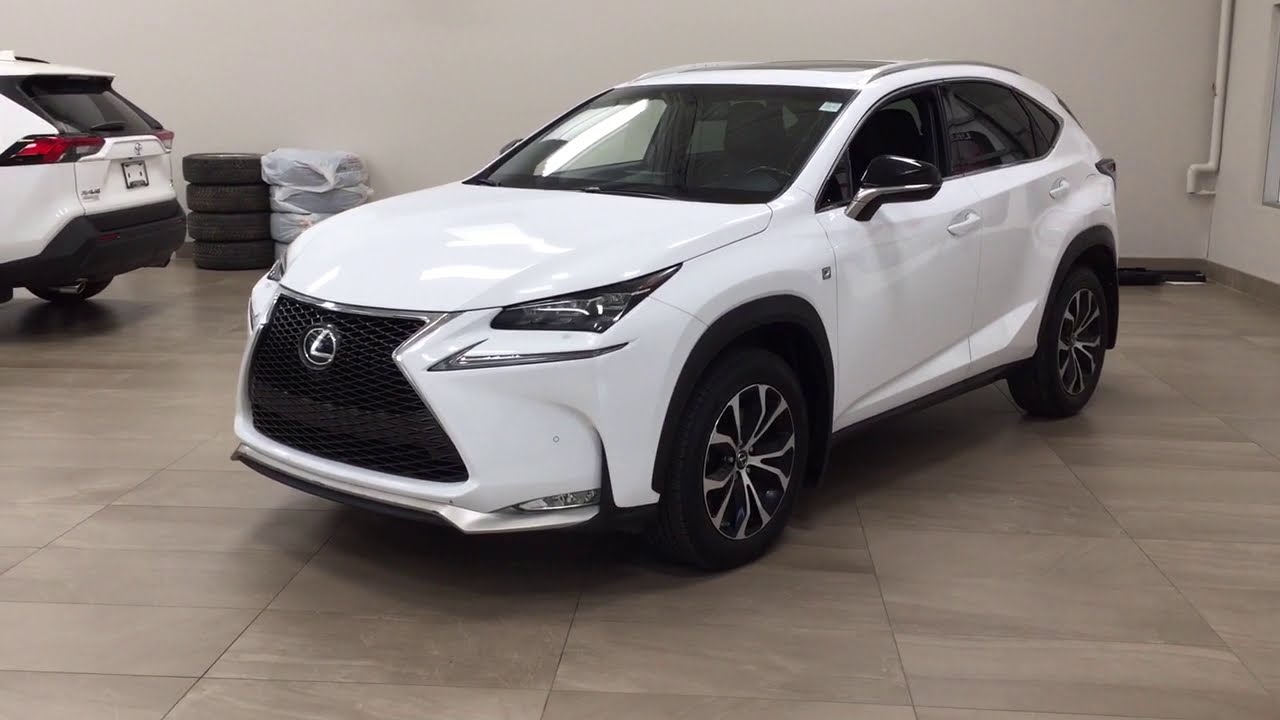
This results in significantly fewer electronic suspension failures even as vehicles age, sparing owners the expensive diagnostic and replacement procedures common with competitors.
The NX’s suspension reliability is further enhanced by Toyota/Lexus’s extensive real-world testing regimen, which subjects components to more severe conditions than typically encountered in customer use.
This testing identifies and eliminates potential failure points before production begins. Owner reports consistently highlight how the NX maintains its composed ride quality and handling precision well beyond 100,000 miles with minimal intervention, often requiring nothing more than standard strut replacements around 120,000-150,000 miles.
For luxury crossover buyers, this durability translates to both lower ownership costs and a more consistent driving experience throughout the vehicle’s life.
While competitors often develop increasing rattles, clunks, and handling degradation as they age, the NX maintains its refined character with minimal maintenance.
This consistency, combined with excellent parts availability and reasonable repair costs when service is eventually needed, makes the NX one of the smartest long-term investments in the luxury crossover segment from a suspension perspective.
5 Crossovers That Constantly Need Suspension Work
Despite their supposedly rugged nature, these problematic crossovers develop alarming suspension noises and handling issues after encountering even modest road imperfections.
Their underbuilt components and cost-cutting engineering decisions result in premature wear of control arms, end links, and strut mounts, often beginning before 50,000 miles.
Owners report budgeting thousands for regular suspension overhauls, with repair forums filled with discussions about which aftermarket parts might finally outlast the originals.
The constant clunks, rattles, and vibrations not only compromise ride comfort but also represent a significant unexpected cost that quickly erodes any initial purchase savings.
1. Range Rover Evoque (2012-2019)
The Range Rover Evoque fascinated buyers with its striking design and prestigious badge, but beneath its fashionable exterior lies a suspension system plagued with chronic reliability issues that have frustrated owners and technicians alike.
The first-generation Evoque’s suspension problems stem from a perfect storm of complex engineering, questionable material choices, and design compromises made to accommodate its distinctive styling.
At the heart of the Evoque’s suspension woes is its adaptive damping system, which utilizes electronically controlled shock absorbers to adjust damping rates based on driving conditions.
While impressive in theory, these units have demonstrated alarming failure rates, often beginning around 40,000 miles. The electronic actuators and sensors within these dampers frequently malfunction, resulting in error messages, unpredictable ride quality, and eventual complete failure.
Replacement costs are exacerbated by the integrated design that prevents individual component repair, forcing complete assembly replacement at considerable expense.
Equally problematic are the Evoque’s control arms and bushings, which deteriorate at an accelerated rate compared to competitors. The vehicle’s substantial weight, combined with relatively compact suspension components, creates excessive stress on these parts, particularly in the front suspension.
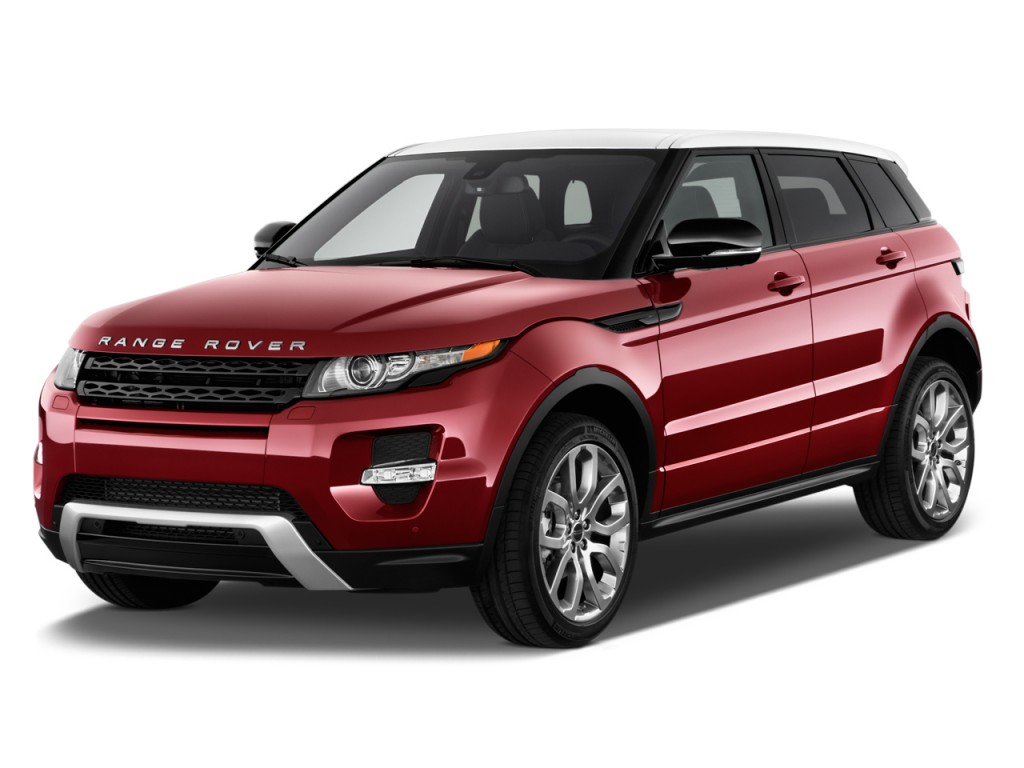
Owners routinely report needing complete control arm replacements by 60,000 miles, with premature bushing deterioration evident much earlier through increasing road noise and diminishing handling precision.
The Evoque’s air suspension system (when equipped) represents another significant failure point, with compressors and air springs demonstrating poor longevity compared to other luxury crossovers.
The system’s complexity means that failures often cascade, with initial leaks leading to compressor overwork and eventual failure. Many owners report complete air suspension system replacements costing thousands of dollars before vehicles reach 75,000 miles.
Perhaps most frustrating for Evoque owners is how these suspension issues manifest in both reliability surveys and resale value. The model consistently ranks below average in suspension reliability metrics, with suspension repairs representing one of the most common dealer service visits.
This reputation has significantly impacted depreciation rates, with suspension concerns frequently cited by appraisers when valuing used examples.
For prospective buyers tempted by depreciated used Evoques, thorough inspection of the entire suspension system is essential, as repair costs can quickly exceed the initial savings compared to more reliable alternatives.
2. Cadillac XT5 (2017-2021)
The Cadillac XT5 represents a cautionary tale of how sophisticated suspension technology, when improperly executed, can lead to chronic reliability issues and frustrated owners.
Despite Cadillac’s premium positioning and promises of American luxury, the XT5’s suspension system has become notorious among owners and service departments for its frequent failures and costly repair requirements, often beginning well before 50,000 miles.
Central to the XT5’s suspension problems is its advanced but problematic Continuous Damping Control (CDC) system. This electronically adjustable suspension utilizes complex sensors and actuators to modify damping characteristics based on driving conditions.
However, the system has proven remarkably failure-prone, with sensors frequently providing inaccurate readings that trigger warning lights and place the system in limp mode.
The electronic dampers themselves often develop internal leaks or electrical failures, requiring complete replacement at costs exceeding $1,000 per corner, a repair commonly needed by 60,000 miles.
Equally concerning are the XT5’s structural suspension mounting points, which have demonstrated a propensity for premature wear. The subframe bushings, which isolate the suspension from the chassis, frequently deteriorate much earlier than expected, leading to alignment issues, uneven tire wear, and characteristic clunking noises over bumps.
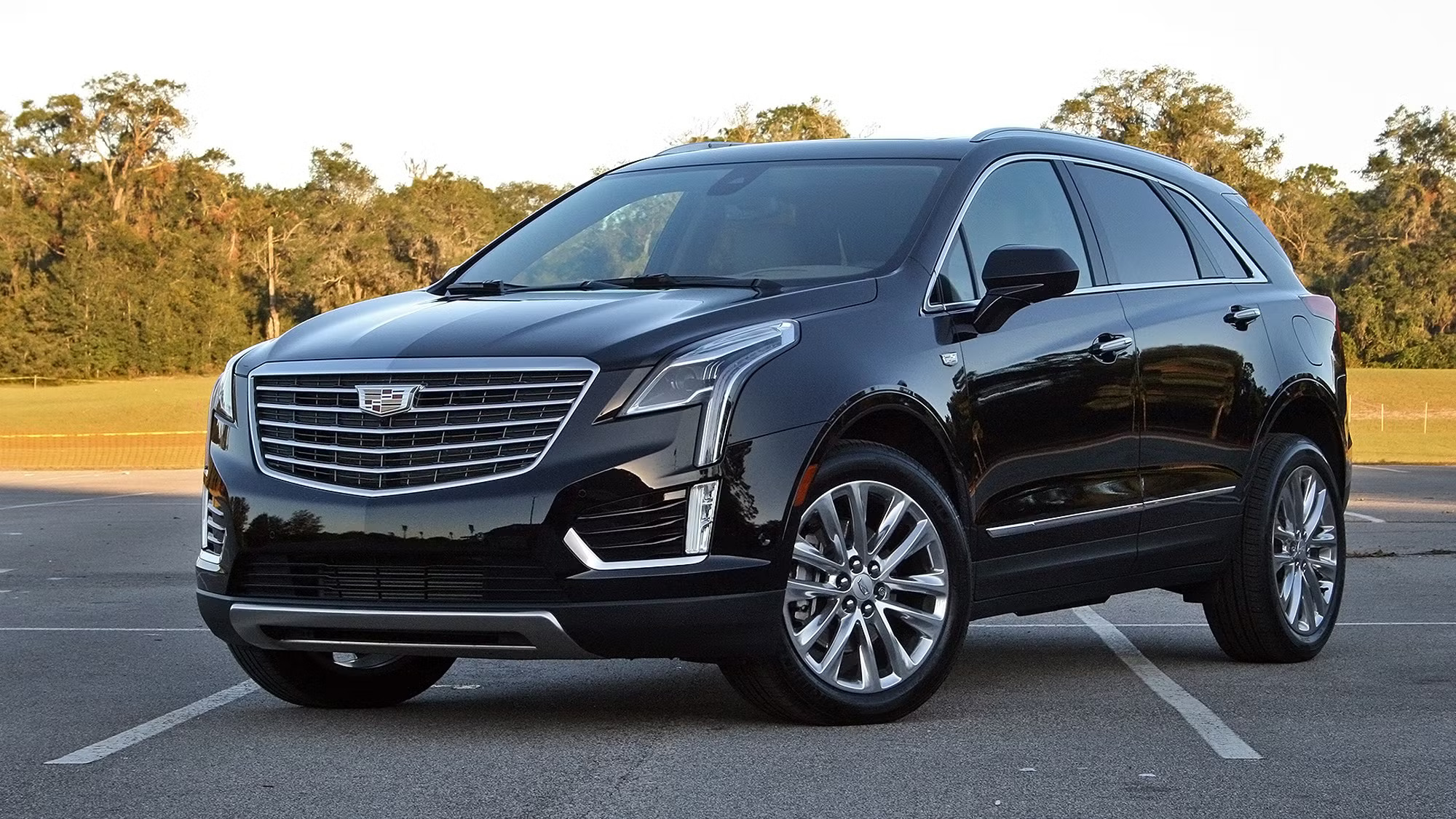
This deterioration accelerates wear on other components, creating a cascade of failures that compound repair costs. The XT5’s rear suspension has proven particularly problematic, with toe links and control arms exhibiting poor durability compared to competitors.
Owners in regions with challenging road conditions frequently report requiring complete rear suspension rebuilds by 70,000 miles, with repair costs often approaching $3,000 when performed at dealerships.
These issues are exacerbated by Cadillac’s design choices that make component replacement labor-intensive, further increasing maintenance costs. Perhaps most telling is how XT5 suspension issues have impacted the vehicle’s standing in reliability surveys and owner satisfaction metrics.
The model consistently ranks below segment averages, specifically for suspension durability, with many owners reporting multiple suspension-related dealer visits within their first three years of ownership.
For prospective buyers, these chronic issues should prompt careful consideration, particularly for used examples approaching the 40,000-60,000 mile range when these problems typically manifest.
The combination of premium purchase price and above-average maintenance costs makes the XT5 one of the more financially challenging crossovers to maintain long-term from a suspension perspective.
3. Jeep Compass (2017-2021)
The Jeep Compass occupies an unfortunate position in the crossover market, promising rugged Jeep capability while delivering some of the segment’s most problematic suspension reliability.
Despite a complete redesign for 2017 that was intended to address previous generation issues, the Compass continues to frustrate owners with premature suspension failures, inconsistent quality control, and repair costs disproportionate to its modest price point.
The Compass’s front suspension has proven particularly troublesome, with strut assemblies frequently failing much earlier than class averages. Owners commonly report developing characteristic clunking and knocking noises as early as 30,000 miles, with strut bearing plate failures being especially prevalent.
The problem is compounded by deteriorating strut mounts that allow excessive movement, accelerating wear on related components. Complete front strut replacement is commonly required before 60,000 miles, significantly earlier than competitors in the same price range.
Control arm bushings represent another chronic failure point in the Compass suspension system. The rubber compounds used appear particularly susceptible to heat cycling and environmental deterioration, leading to premature hardening and cracking.
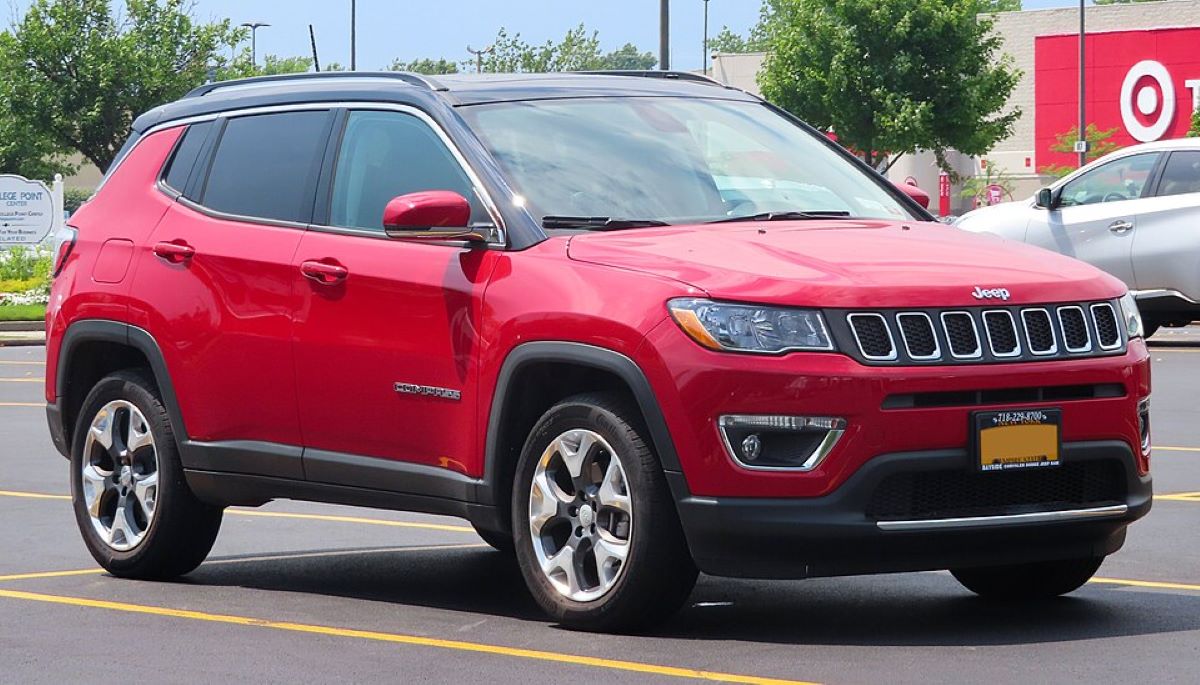
This bushing failure manifests as increasingly vague steering response, wandering at highway speeds, and characteristic popping noises during low-speed maneuvering.
Many owners report requiring complete control arm replacements by 50,000 miles, with repair costs often exceeding $800 for both sides. The Compass’s rear suspension geometry also demonstrates concerning longevity issues, particularly in its stabilizer links and bushings.
These components frequently develop and play much earlier than expected, creating noticeable rattling over uneven surfaces. The problem is exacerbated by questionable material choices in the rear trailing arms, which show poor corrosion resistance in regions where road salt is used, sometimes requiring replacement after just a few winter seasons.
Perhaps most troubling for Compass owners is how these suspension issues impact the vehicle’s overall driving dynamics and safety as they progress. The gradual deterioration of multiple components creates increasingly unpredictable handling characteristics and extended stopping distances, problems often dismissed during routine service until they become severe.
Technical service bulletins addressing suspension issues have been released throughout the generation, indicating manufacturer awareness of these shortcomings, yet comprehensive solutions have remained elusive.
For budget-conscious shoppers attracted to the Compass’s styling and features, these suspension reliability concerns should prompt serious consideration of more durable alternatives or extended warranty coverage to mitigate the substantial repair costs that frequently arise by mid-lifecycle.
4. Nissan Rogue (2014-2019)
The Nissan Rogue represents one of the most popular yet suspension-troubled entries in the compact crossover segment. While attractive pricing and generous feature content have made it a sales success, owners frequently discover that these initial savings are often offset by persistent suspension issues that begin manifesting much earlier than competitors, sometimes before vehicles reach 40,000 miles.
The most notorious suspension problem affecting this generation of Rogue involves its strut assemblies, which demonstrate alarmingly high failure rates compared to segment averages.
Owners consistently report developing characteristic knocking noises over even minor road imperfections, with strut mount bearings being particularly prone to premature failure.
This issue is so common that numerous technical service bulletins have been issued, yet permanent solutions remain elusive, with many owners reporting repeated failures even after dealer repairs.
Equally problematic is the Rogue’s rear suspension design, which employs a semi-independent setup with a torsion beam rather than the fully independent arrangements found in many competitors.
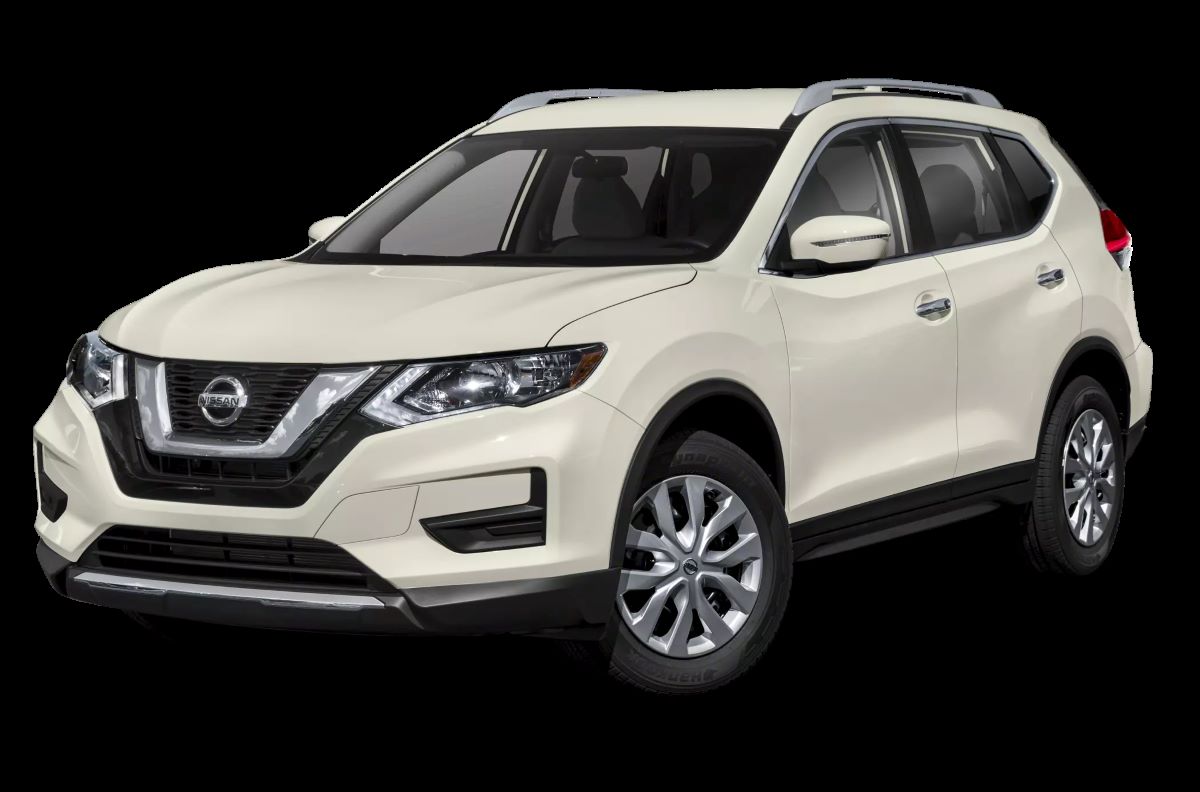
This cost-saving measure contributes to accelerated wear of rear suspension bushings and mounting points, creating increasing alignment issues as vehicles age.
Owners frequently report developing characteristic clunking noises from the rear suspension by 50,000 miles, with complete bushing replacement often necessary by 70,000 miles.
The Rogue’s control arm assemblies have demonstrated poor durability as well, with ball joints frequently developing excessive play long before expected replacement intervals.
This deterioration creates inconsistent handling characteristics, accelerated tire wear, and safety concerns as the condition worsens. The integrated design of many control arm components means that relatively minor failures often necessitate complete assembly replacement rather than more economical component repair.
What makes these issues particularly frustrating for Rogue owners is the inconsistent quality control evident across production runs. While some vehicles operate without significant problems, others experience multiple suspension failures within their first few years of operation.
This inconsistency has contributed to the model’s below-average performance in reliability surveys, specifically regarding suspension durability. For used vehicle shoppers, these concerns make a thorough pre-purchase inspection essential, as repair costs can quickly accumulate when multiple suspension components require attention simultaneously, a common scenario with higher-mileage examples.
The prevalence of these issues across multiple model years suggests structural design flaws rather than isolated manufacturing defects, making the 2014-2019 Rogue one of the more suspension-problematic mainstream crossovers of its era.
5. Ford Escape (2013-2019)
The Ford Escape’s third generation arrived with ambitious styling and modern features, but quickly developed a reputation for suspension fragility that has frustrated owners and dealership service departments alike.
What makes the Escape particularly noteworthy in this discussion is not just the frequency of suspension problems, but how early in the vehicle’s lifecycle these issues typically emerge, often beginning before 40,000 miles.
The Escape’s front suspension demonstrates several chronic failure points, with control arm bushings being particularly problematic. The rubber compounds used deteriorate prematurely, creating increasing play in the suspension geometry that manifests as wandering steering, uneven tire wear, and characteristic clunking noises over bumps.
Many owners report requiring complete control arm replacement by 50,000 miles significantly earlier than segment averages. The problem is exacerbated by Ford’s design choice to integrate multiple components into single assemblies, forcing complete replacement rather than more economical individual bushing renewal.
Equally concerning are the Escape’s rear suspension issues, particularly in its multi-link arrangement. The trailing arm bushings frequently develop excessive compliance, creating alignment issues that accelerate tire wear and compromise handling.
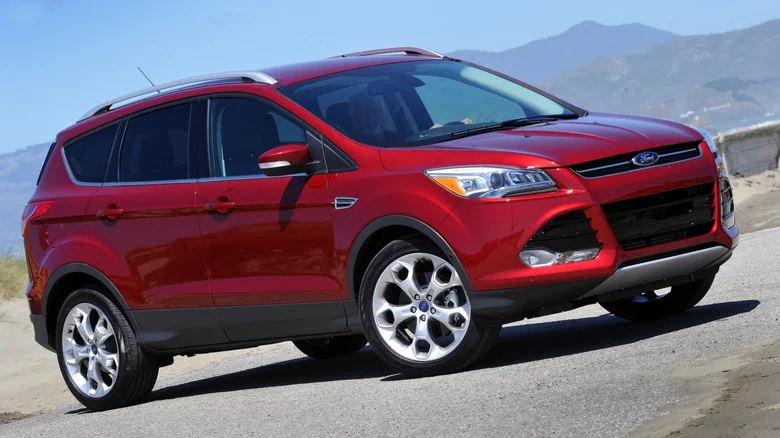
More seriously, the rear subframe mounting points have demonstrated alarming rates of premature corrosion in regions where road salt is used, sometimes requiring complete subframe replacement, a repair costing thousands of dollars that owners report needing as early as 70,000 miles in severe cases.
The Escape’s strut assemblies represent another significant failure point, with many owners experiencing internal leaking or impact damage far earlier than expected.
The front strut bearing plates are particularly notorious, often developing characteristic grinding noises during steering that indicate imminent failure. These issues have been common enough to prompt multiple technical service bulletins, yet comprehensive solutions have remained elusive across production years.
Perhaps most telling about the Escape’s suspension woes is their impact on owner satisfaction scores and trade-in behavior. Data from multiple sources shows Escape owners trading vehicles earlier than segment averages, with suspension concerns frequently cited as motivating factors.
Service records indicate suspension repairs represent one of the most common non-maintenance dealer visits for this generation. For used vehicle shoppers, these patterns should prompt careful pre-purchase inspection focusing specifically on suspension components, as repair costs can quickly accumulate when addressing the multiple issues commonly found in higher-mileage examples.
The persistence of these problems across multiple model years and production facilities suggests fundamental design or material choices rather than isolated manufacturing defects, making suspension reliability a significant consideration for anyone considering this generation of Escape.
Also Read: 5 SUVs That Maintain Power After 100K Miles and 5 That Feel Gutless