The cooling system is the unsung hero of any vehicle, quietly maintaining optimal engine temperatures through scorching summer traffic jams and frigid winter mornings.
When functioning properly, most drivers never give it a second thought. However, when cooling systems fail, the consequences can be catastrophic from being stranded roadside to facing catastrophic engine damage and repair bills in the thousands.
Some manufacturers have engineered remarkably resilient cooling systems that seem impervious to time and harsh conditions, while others have produced notorious designs plagued by chronic overheating issues, head gasket failures, and coolant leaks.
This stark contrast in reliability comes from differences in engineering philosophy, material quality, component layout, and sometimes simply poor design choices that weren’t adequately tested under real-world conditions.
Whether you’re shopping for a used vehicle or want to understand what makes your current ride reliable (or problematic), this guide examines five vehicles renowned for their bulletproof cooling systems and five infamous for their cooling system nightmares, providing valuable insights into what separates the dependable from the disastrous under the hood.
5 Cars With Engines That Never Overheat
These engineering marvels feature meticulously designed cooling systems with generous capacity margins that maintain optimal operating temperatures in even the most extreme conditions.
Their intelligent thermostat programming, precision-manufactured water pumps, and optimized coolant flow paths create thermal stability that owners can depend on year after year without worry.
From Death Valley summers to bumper-to-bumper traffic with the AC blasting, these exceptional engines maintain rock-solid temperature readings without the fluctuations that plague lesser designs.
Owners report routinely reaching six-figure mileages without a single cooling-related repair, evidence that thoughtful engineering pays dividends through reduced maintenance costs and enhanced reliability.
1. Toyota Land Cruiser
The Toyota Land Cruiser has built its legendary reputation on reliability across all systems, but its cooling system deserves special recognition.
Engineered to withstand the harshest environments on Earth, from the scorching Australian Outback to the frigid Arctic Circle, the Land Cruiser’s cooling system exemplifies Toyota’s overbuilt philosophy.
At the heart of this durability is a large-capacity radiator with an optimized fin design that maximizes heat dissipation. Unlike many modern vehicles that use plastic tank radiators prone to cracking, Land Cruisers typically feature all-aluminum radiator constructions with superior thermal conductivity and structural integrity.
Toyota’s meticulous engineering extends to the water pump, which uses high-grade bearings and seals designed for extended service life, often lasting well beyond 150,000 miles without replacement.
The Land Cruiser’s cooling system layout also contributes to its reliability. The engine bay provides excellent airflow, with minimal obstruction to the radiator.
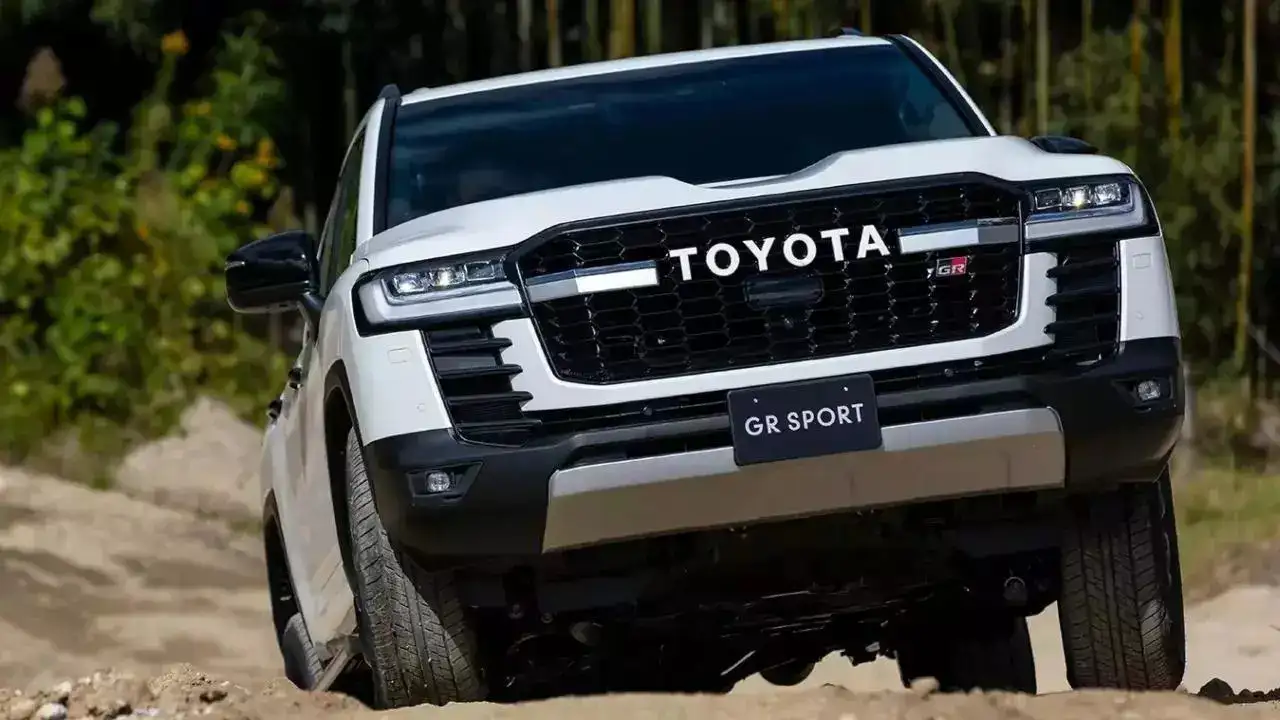
Additional oil coolers for the transmission and power steering system prevent heat transfer into the main cooling circuit, keeping engine temperatures stable even under heavy loads like towing or rock crawling.
Perhaps most impressive are the Land Cruiser’s auxiliary cooling system features. Models destined for extreme environments often include secondary fans, oversized reservoirs, and additional coolant capacity that provide substantial thermal margin.
The thermostat housing and water outlet fittings are typically made from cast aluminum rather than plastic, eliminating common failure points found in lesser vehicles.
Long-term Land Cruiser owners consistently report reaching 300,000+ miles with minimal cooling system intervention beyond routine maintenance. For expeditions in remote areas where reliability isn’t just about convenience but survival, the Land Cruiser’s cooling system has earned its reputation as virtually bulletproof.
When properly maintained with scheduled coolant changes using Toyota’s recommended formulations, these systems often outlast many other vehicle components.
2. Honda Accord (4-cylinder models)
Honda’s engineering prowess shines brightly in the Accord’s cooling system, particularly in its 4-cylinder variants. Since the early 1990s, these models have established themselves as paragons of thermal management reliability, with countless examples running well beyond 250,000 miles without significant cooling system failures.
The Accord’s cooling system success begins with Honda’s fundamental engine design philosophy: precision manufacturing with tight tolerances and meticulous attention to flow dynamics.
The water jackets within the engine block feature optimized pathways that ensure even cooling across all cylinders, eliminating hot spots that can lead to premature failure. Honda’s integration of coolant passages directly into the cylinder head gasket design provides excellent sealing and proper coolant distribution.
A standout feature is Honda’s remarkably durable water pump design. Unlike many competitors who utilize pressed-fit impellers prone to failing, Honda typically employs cast impellers with superior structural integrity.
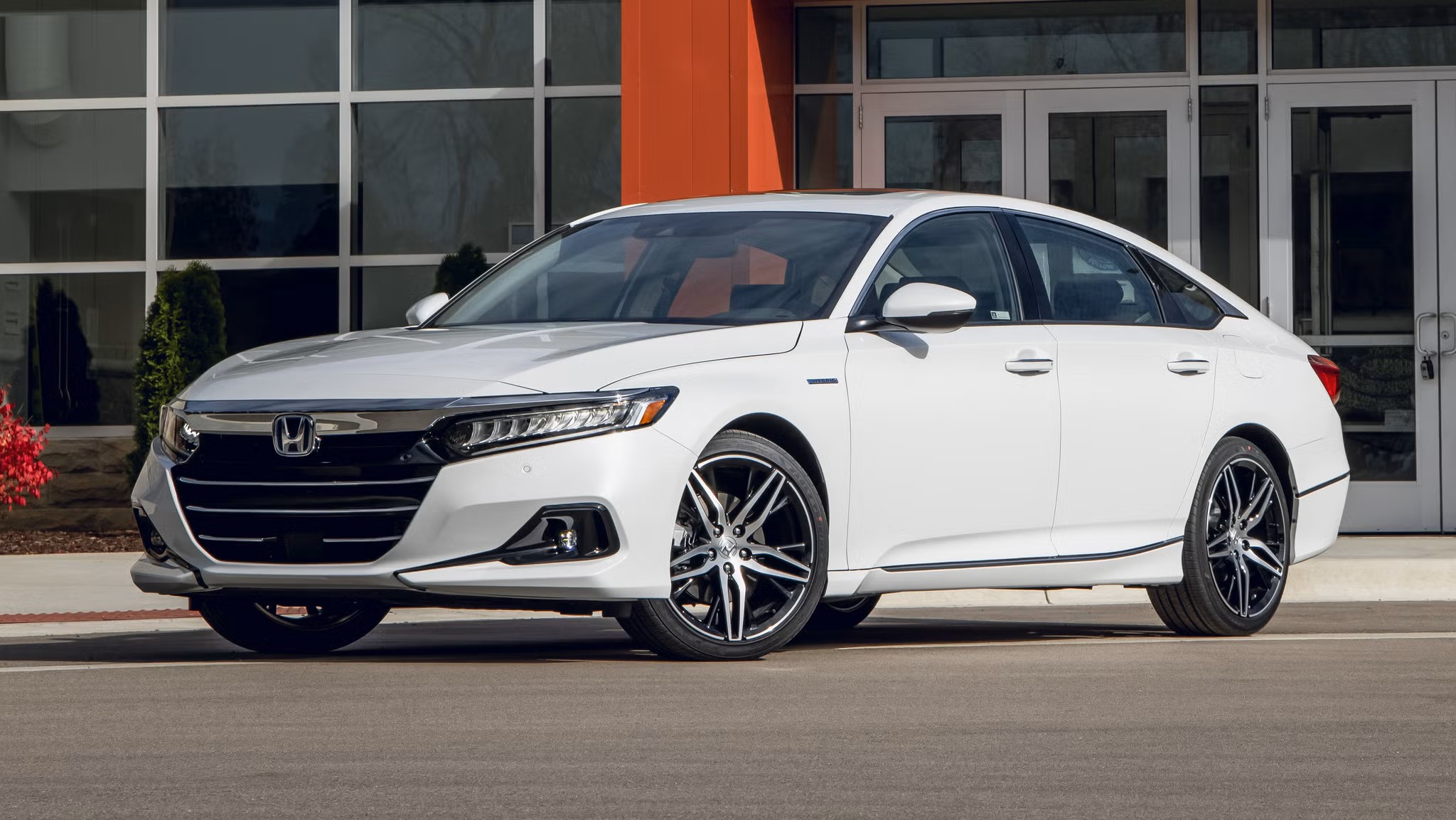
The pump’s bearing assembly is engineered for longevity, with many original water pumps in Accords easily reaching 150,000 miles before replacement becomes necessary.
The radiator design further enhances system reliability through proper sizing and strategic placement. Honda engineers provide adequate cooling capacity with optimized airflow patterns across the radiator surface.
The company’s early adoption of aluminum radiator technology with plastic end tanks featured improved sealing methods that resisted the typical leakage issues found in competitors’ designs.
Honda’s cooling system implementation also benefits from intelligent electronic control. The Accord’s electric cooling fans are regulated by a sophisticated temperature management system that balances cooling needs with fuel efficiency.
This prevents unnecessary fan operation while ensuring prompt activation when temperatures rise. Additionally, the system incorporates a slow-cooling feature after engine shutdown that helps prevent heat soak and component stress.
Perhaps most impressive is Honda’s remarkably stable coolant chemistry. Their proprietary blue coolant formulation resists breakdown and maintains protective properties longer than many alternatives.
When maintained according to Honda’s conservative service intervals, the cooling system in 4-cylinder Accords often remains trouble-free for the vehicle’s entire operational life.
3. Lexus LS Series
The Lexus LS series represents Toyota’s uncompromising approach to luxury engineering, and nowhere is this more evident than in its cooling system design.
Since the original LS 400 debuted in 1989, the flagship sedan has consistently featured some of the most overengineered cooling systems in the automotive industry, designed not just for adequacy but for absolute reliability under all conditions.
Central to the LS cooling system’s resilience is its substantial overcapacity. Lexus engineers didn’t merely calculate the minimum cooling requirements for their powerplants; they designed systems with significant thermal margins.
The radiators in LS models feature larger-than-necessary core dimensions with optimized fin density and tube construction that provide exceptional heat rejection capacity. This overcapacity means the system rarely operates near its limits, reducing thermal stress and extending component life.
The water pump designs in LS models showcase Toyota’s commitment to durability. Unlike mass-market vehicles, Lexus employs water pumps with precision-balanced impellers, higher-grade seals, and superior bearing assemblies that routinely outlast 150,000 miles of service.
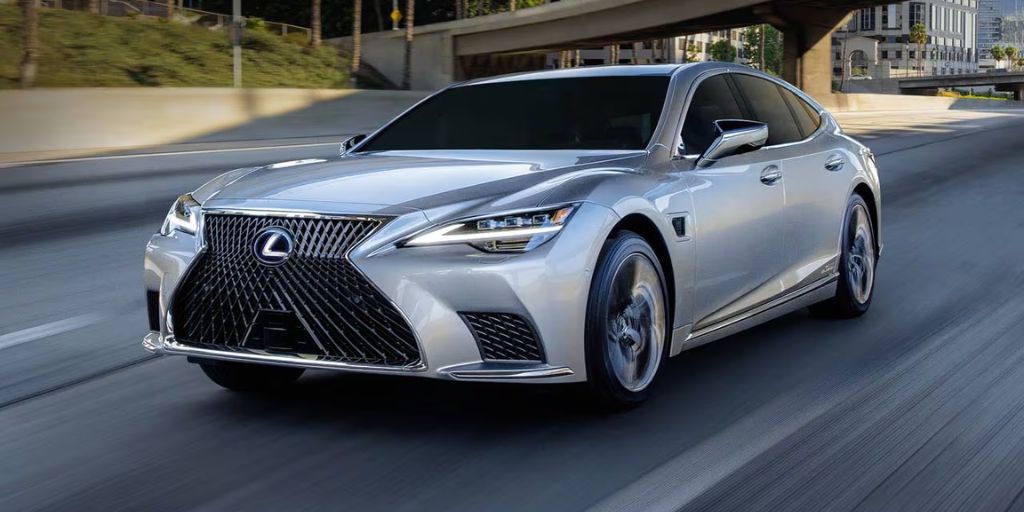
The belt-driven pumps operate at carefully calculated speeds to provide consistent flow without cavitation issues that plague lesser designs. Lexus further enhances cooling system reliability through intelligent thermal management.
The LS series pioneered sophisticated electronic cooling fan control that anticipates heating conditions rather than merely reacting to them. This predictive approach, combined with variable speed fan operation, maintains more consistent temperatures while reducing wear on electrical components.
Material selection distinguishes the LS cooling system from competitors. Lexus uses high-grade aluminum alloys for crucial components like thermostat housings and water outlets locations where many manufacturers cut costs with plastic parts prone to degradation and failure.
All hoses feature reinforced construction with multiple layers and high-temperature rubber compounds that resist hardening and cracking. Perhaps most impressive is Lexus’s approach to coolant pathways.
The engine block and cylinder head designs incorporate precision-cast coolant passages that ensure even temperature distribution across all cylinders. This eliminates hot spots that can lead to warping, head gasket failures, or local boiling points that cause air pockets within the system.
LS owners routinely report trouble-free cooling system operation well beyond 200,000 miles with only routine maintenance. In the rare cases where issues do arise, they typically result from neglected maintenance rather than inherent design flaws.
The Lexus LS cooling system exemplifies how proper engineering, quality materials, and conservative operational parameters create exceptional reliability.
4. Volvo 240 Series
While production of the venerable Volvo 240 series ended in 1993, these Swedish workhorses continue to demonstrate remarkable cooling system longevity that modern vehicles struggle to match.
The 240’s cooling system epitomizes Volvo’s no-nonsense, function-over-form engineering philosophy that prioritized reliability above all else. The foundation of the 240’s cooling prowess begins with its straightforward layout.
Unlike modern engines with complex, space-constrained designs, the 240’s engine bay provides generous space for a large-capacity copper-brass radiator.
This traditional radiator construction, while heavier than aluminum alternatives, offers superior durability and easier repair when damaged. The generous sizing provides significant thermal headroom, allowing the system to handle extreme conditions without strain.
Volvo’s approach to water pump design in the 240 series focused on simplicity and overbuilt construction. The cast iron pump housing resists corrosion and warping, while the impeller design prioritizes flow volume over efficiency.

This seemingly outdated approach resulted in pumps that commonly reached 200,000+ miles before requiring replacement, far exceeding the service life of modern lightweight alternatives.
Perhaps most notable is the 240’s thermostat housing arrangement. Unlike many vehicles with plastic housings prone to cracking or difficult-to-access locations, Volvo positioned the thermostat in a simple, accessible cast housing at the front of the engine.
This design not only improved reliability but also simplified maintenance, encouraging regular service that further extended system life. The cooling system’s plumbing in 240 models reflects Volvo’s overengineered approach.
Large-diameter hoses with gradual bends minimize flow restrictions, while robust clamps and connection points resist leakage. The expansion tank is positioned to effectively purge air from the system, preventing circulation issues that plague many modern designs.
Volvo’s coolant formulation recommendations for the 240 series were similarly conservative. The manufacturer specified a simple ethylene glycol mixture without the complex additive packages required by many contemporary vehicles.
This straightforward approach prevented chemical incompatibilities that often cause corrosion and component failure in sophisticated modern cooling systems. Even decades after production ended, 240 series Volvos continue to demonstrate remarkable cooling system reliability in daily use.
While lacking the thermal efficiency of modern designs, their overbuilt construction and serviceability have created a legacy of durability that many contemporary vehicles fail to achieve despite advanced technology.
For enthusiasts seeking a vehicle that will maintain stable temperatures through decades of service, the Volvo 240’s cooling system remains a benchmark of functional engineering.
Also Read: 5 Crossovers That Rarely Need Suspension Work and 5 That Constantly Do
5. Mazda Miata (MX-5)
The Mazda Miata has cemented its reputation as one of the most reliable sports cars ever produced, and its cooling system plays a significant role in this distinction.
Despite its compact dimensions and sporting pretensions, the Miata’s thermal management system demonstrates how thoughtful engineering can create exceptional reliability without excessive complexity or cost.
Mazda’s approach to the Miata’s cooling system begins with proper sizing and integration. Unlike some sports cars that sacrifice cooling capacity for styling or packaging constraints, Mazda engineers ensured the radiator was adequately sized for the engine’s heat rejection needs.
The front-mounted radiator receives unobstructed airflow, with carefully designed ducting that directs air efficiently across the entire core surface a simple but effective approach that many performance vehicles overlook in favor of more aggressive styling.
The water pump design in the Miata exemplifies Mazda’s commitment to reliability through simplicity. Rather than employing cutting-edge materials or complex impeller designs, Mazda opted for a conventional but extremely durable cast impeller pump.
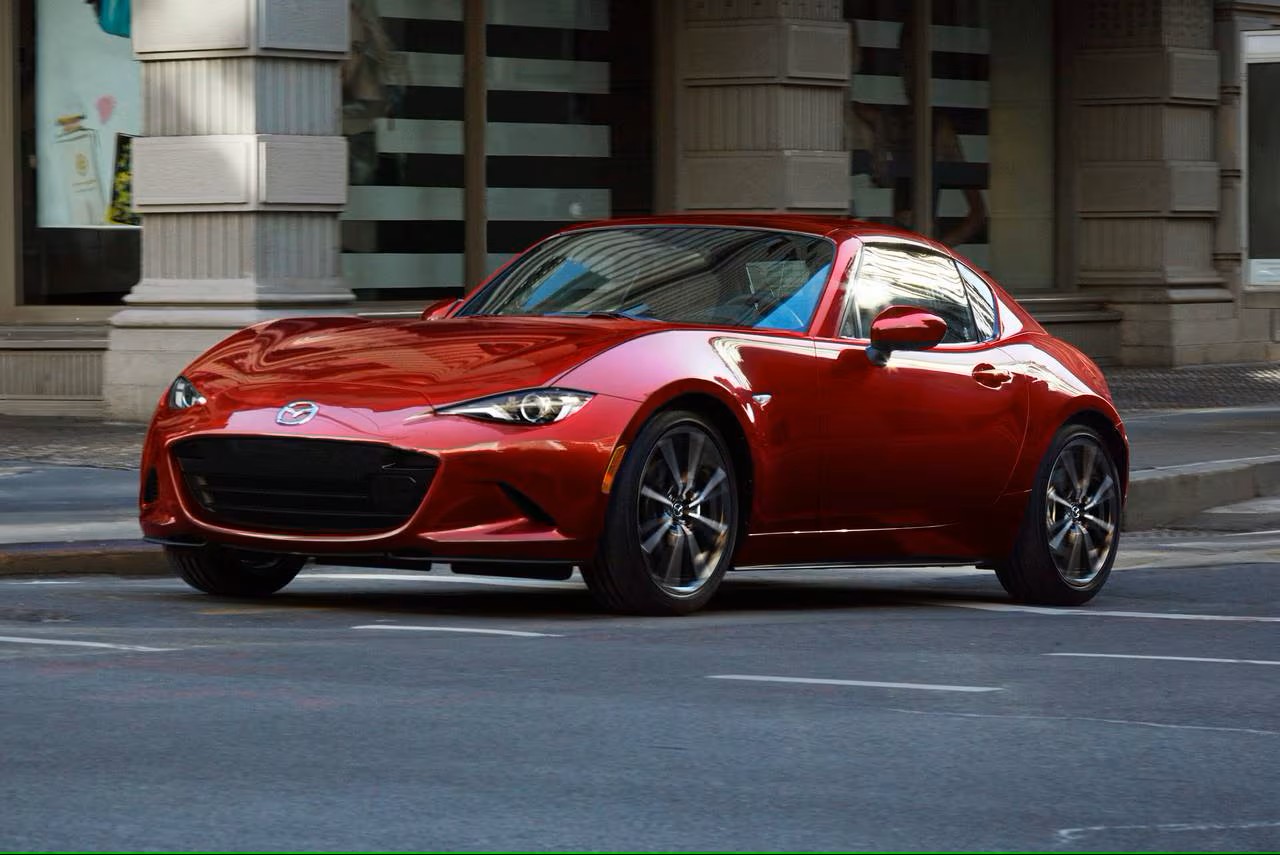
The pump’s location is optimized for consistent coolant flow throughout the engine, with short, direct pathways that minimize restriction. This no-frills approach has resulted in water pumps that routinely exceed 150,000 miles of service without failure.
Perhaps most impressive is the Miata’s cooling system layout, which incorporates natural advantages of physics. The engine’s orientation allows for a thermosiphon effect that promotes natural coolant circulation even when the water pump isn’t operating.
This passive cooling capability prevents heat soak after shutdown, a common issue in performance vehicles that can lead to component degradation over time.
Mazda’s attention to detail extends to the Miata’s expansion tank and bleed system design. The carefully positioned tank ensures complete air purging during filling, preventing air pockets that can lead to localized overheating.
The bleed points are easily accessible, encouraging proper maintenance and complete system purging during coolant changes. The cooling fan system in the Miata strikes an ideal balance between simplicity and effectiveness.
Early models utilized a mechanical fan that provided cooling proportional to engine speed, while later versions transitioned to electric fans with straightforward control logic. This avoids the complex variable-speed systems that often become problematic in other vehicles as they age.
Miata owners consistently report exceptional cooling system reliability even in demanding conditions like track days and autocross events where thermal management is critical.
The system maintains stable temperatures without the need for aftermarket upgrades that many sports cars require for serious performance driving.
This reliability stems not from revolutionary technology but from Mazda’s fundamentally sound approach to engineering, proper sizing, quality components, and straightforward design that prioritizes function over marketing appeal.
5 Cars That Are Cooling System Nightmares
These problematic vehicles feature notoriously fragile cooling systems plagued by design flaws that transform minor components into catastrophic failure points requiring expensive repairs.
Their undersized radiators, fragile plastic parts in high-heat locations, and poor airflow management create a perfect storm of thermal vulnerability that begins manifesting well before 60,000 miles.
Owners quickly become familiar with the coolant smell, temperature warning lights, and the sinking feeling of steam rising from under the hood during what should be routine driving conditions.
What starts as occasional overheating often progresses to blown head gaskets, warped cylinder heads, and even complete engine failure, turning modest repair costs into budget-crushing expenses.
1. BMW N54-Powered 3-Series (2006-2010)
The BMW N54 engine found in 2006-2010 3-Series models represented BMW’s ambitious foray into twin-turbo technology for mainstream vehicles.
While celebrated for its performance potential, this powerplant has become notorious for cooling system failures that can leave owners facing repair bills running into thousands of dollars.
The N54’s cooling system woes begin with its fundamentally flawed water pump design. Unlike conventional mechanical water pumps, BMW employed an electronically controlled variable-speed pump that, while theoretically more efficient, proved catastrophically unreliable in practice.
These pumps typically fail without warning between 60,000-80,000 miles, well short of reasonable service expectations.
The failure mode is particularly problematic: the plastic impeller deteriorates gradually, providing no symptoms until complete failure occurs, often leaving drivers stranded with rapidly overheating engines.
Compounding this primary weakness is the N54’s complex thermostat assembly. BMW integrated the thermostat into a plastic housing that commonly develops stress cracks around mounting points and sealing surfaces.
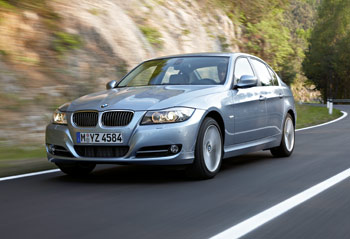
These cracks allow coolant leakage that can rapidly deplete the system, again with minimal warning until temperatures spike dangerously. The thermostat’s electrical components also frequently fail, causing the unit to remain closed and preventing proper coolant circulation.
The radiator design in N54-powered models further exacerbates cooling issues. BMW’s decision to use lightweight plastic end tanks bonded to aluminum cores created a fundamental weakness at the seam locations.
These joints deteriorate over time, typically developing minor leaks that progressively worsen. Additionally, the radiator’s relatively compact dimensions provide inadequate thermal capacity for the heat output of the twin-turbocharged engine, particularly when driven enthusiastically.
The expansion tank represents another critical failure point in this cooling system. Constructed from brittle plastic that degrades with heat cycling and exposure to engine bay temperatures, these tanks commonly develop cracks near the cap sealing surface or at the level sensor mount.
These failures often occur without warning, causing rapid coolant loss and potential engine damage if not caught quickly. Perhaps most concerning is the cascade effect these cooling system failures create.
When one component fails, the resulting overheating event stresses the remaining components, accelerating their deterioration. This leads many owners into a cycle of repeated repairs as different parts of the system fail sequentially.
BMW’s integration of the cooling system with other engine subsystems means these failures often affect turbocharger operation, oil cooling, and HVAC function as well.
The BMW community has reluctantly accepted that a comprehensive cooling system replacement every 60,000 miles is essentially mandatory preventative maintenance for N54-powered vehicles.
This represents an extraordinary maintenance burden far exceeding industry norms and contradicting BMW’s premium positioning. While the N54 engine delivered impressive performance, its cooling system reliability issues remain a cautionary tale of prioritizing innovation over durability.
2. Subaru Impreza/WRX with EJ Series Engines (2000-2014)
The Subaru EJ series engines, particularly those powering Impreza and WRX models from 2000-2014, have developed a notorious reputation for cooling system-related issues that frequently culminate in the dreaded head gasket failure.
Despite their popularity among enthusiasts for their unique boxer configuration and performance potential, these engines have left many owners facing expensive repairs that often exceed the vehicle’s value.
The fundamental problem stems from Subaru’s head gasket design and material choice. Unlike most manufacturers who transitioned to multi-layer steel (MLS) head gaskets in the 1990s, Subaru continued using composite gaskets with a graphite or non-metallic coating.
These gaskets proved particularly susceptible to degradation from electrolysis, an electrochemical reaction that occurs within the cooling system due to the interaction between different metals, coolant chemistry, and electrical currents.
As these gaskets deteriorate, they typically develop external leaks that seep coolant down the engine block’s sides, often so gradually that owners don’t notice the declining coolant level.
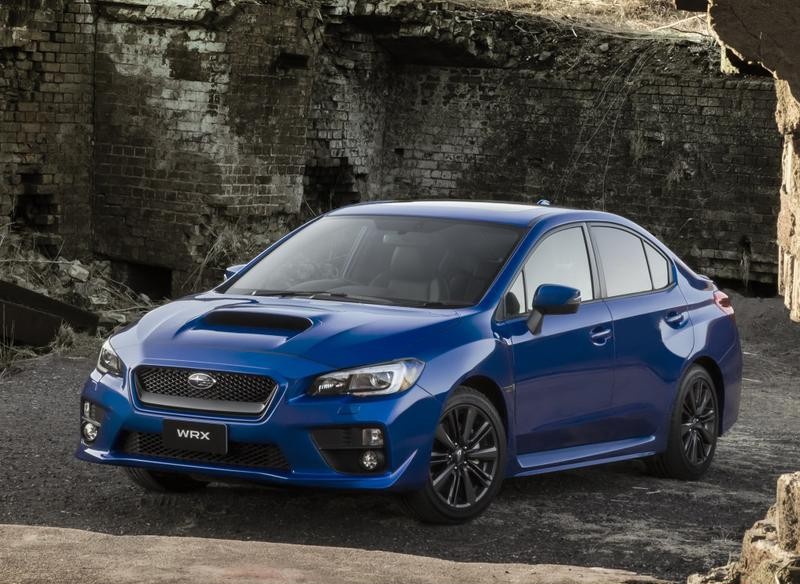
Exacerbating this core issue is the EJ’s cooling system layout. The boxer engine configuration positions the cylinder heads at the sides of the engine rather than the top, creating challenging coolant flow paths.
This layout makes complete air bleeding difficult, allowing air pockets to form that create localized hot spots, further stressing the already vulnerable head gaskets.
The horizontally opposed design also means that half the engine operates at a different temperature than the other half, creating uneven thermal expansion that places additional stress on gasket seals.
Subaru’s thermostat housing design compounds these problems. Constructed of plastic that degrades over time, these housings frequently develop cracks that cause coolant leaks.
Their location makes detection difficult until significant leakage occurs, allowing engines to run with compromised cooling performance for extended periods, further accelerating head gasket deterioration.
The radiator in these models presents another weakness. Subaru typically used aluminum radiators with plastic end tanks that develop stress cracks around mounting points and connection fittings.
These failures often coincide with head gasket issues, creating a perfect storm of cooling system breakdown that can lead to catastrophic overheating events.
Perhaps most frustrating for owners is that these cooling system issues tend to manifest between 80,000-120,000 miles, just as many other vehicle systems remain in excellent condition.
The repair process requires extensive disassembly, as the engine must be removed from the vehicle to replace the head gaskets properly. Labor costs alone typically exceed $1,500, with parts adding hundreds more.
Worse still, unless upgrade components are used during repair, the problem often recurs within another 100,000 miles. While Subaru enthusiasts have developed extensive workarounds, including preventative head gasket replacement, upgraded thermostats, and specialized coolant additives, these measures represent extraordinary maintenance requirements that far exceed industry norms.
The enduring popularity of these vehicles despite these well-documented issues speaks to their other compelling qualities, but their cooling system weaknesses remain a significant liability for owners.
3. Chrysler 2.7L V6 (2001-2010)
The Chrysler 2.7L V6 engine, widely deployed across the manufacturer’s lineup from 2001-2010 in vehicles like the Sebring, Intrepid, and 300, represents perhaps one of the most catastrophically flawed cooling systems ever mass-produced by a major manufacturer.
Unlike systems that merely develop leaks or gradual failures, the 2.7L’s cooling issues frequently result in complete engine destruction, often with minimal warning.
At the heart of this engine’s cooling nightmare is its oil sludge problem, which directly impacts the cooling system. The engine’s design places the water pump at the rear of the engine, driven by the timing chain.
This location makes inspection nearly impossible without major disassembly, while also positioning the pump in an area prone to oil contamination from a poorly designed PCV system.
As oil sludge builds up, it often enters the water pump seal, causing it to fail and allowing coolant to mix with engine oil, creating a deadly emulsion that destroys bearing surfaces and leads to catastrophic engine failure.
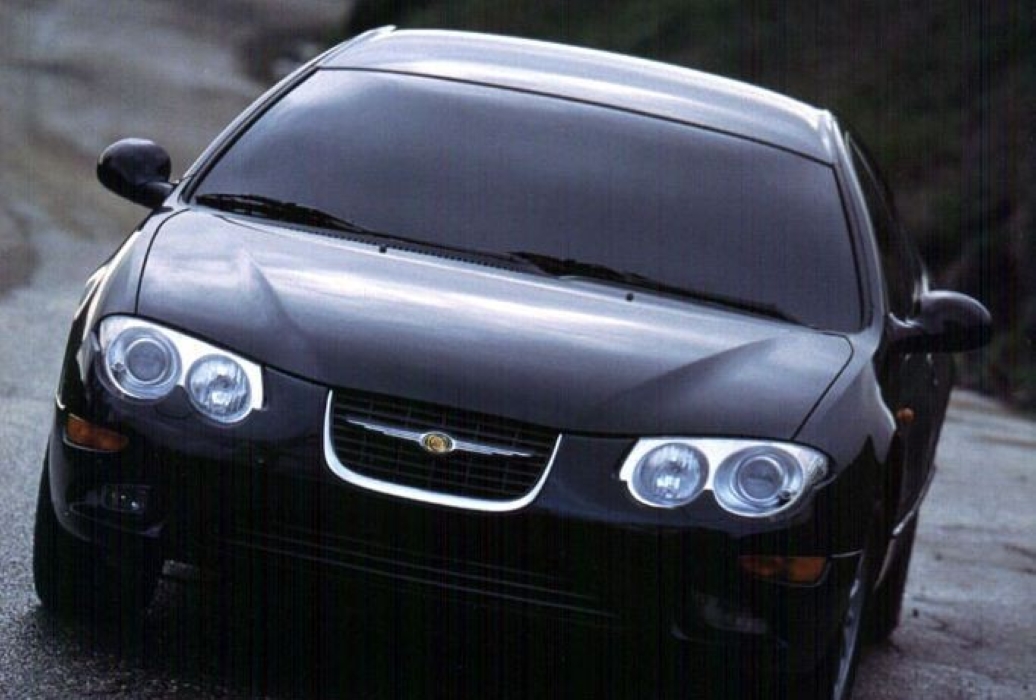
Compounding this fundamental flaw is the engine’s internal coolant passage design. The 2.7L features narrow coolant jackets that are exceptionally prone to clogging from the slightest coolant contamination or additive precipitation.
The restrictive passages create hot spots within the cylinder heads, leading to warping and gasket failures. These narrow passages also make the system particularly vulnerable to damage from stop-leak products that many owners use when first noticing minor leaks, inadvertently accelerating the engine’s demise.
The radiator design further exacerbates these issues. Chrysler outfitted these vehicles with undersized radiators that provide inadequate cooling capacity for the engine’s heat output, particularly in hot climates or under load conditions.
The radiator’s plastic end tanks frequently crack around connection points, introducing air into the system that creates air pockets and localized overheating, further stressing the already compromised engine.
Perhaps most problematic is the 2.7L’s timing chain tensioner system, which is hydraulically operated by engine oil pressure.
When coolant mixes with oil due to a water pump failure, the contaminated oil fails to properly maintain tension, allowing the timing chain to jump and causing catastrophic valve-to-piston contact.
This failure cascade typically occurs with little warning, sometimes only days after the first symptoms appear. The thermostat housing, constructed of brittle plastic, represents another critical failure point.
Its location and design make it prone to cracking after several years of heat cycling, creating cooling system leaks that often go unnoticed until significant coolant loss occurs.
When these leaks develop, they typically allow coolant to seep onto electrical components, creating starting and performance issues that divert diagnostic attention away from the underlying cooling system failure.
The 2.7L’s cooling system issues have become so notorious that many mechanics refuse to perform anything but a complete engine replacement when these vehicles develop cooling problems.
The pattern of catastrophic failure has severely impacted resale values, with many otherwise sound vehicles being scrapped when their engines fail.
Despite facing multiple class-action lawsuits over the design, Chrysler never issued a comprehensive recall, leaving owners to bear the financial burden of these inherent design flaws.
4. Range Rover Sport (2005-2013)
The Range Rover Sport produced between 2005 and 2013 exhibits a cooling system that perfectly embodies the stereotype of British luxury vehicles: beautiful, complex, and fundamentally flawed.
Despite commanding premium prices and projecting an image of rugged capability, these vehicles harbor cooling system deficiencies that regularly strand owners and generate repair bills that can exceed $5,000 when multiple components fail simultaneously.
The cooling system’s problems begin with its extraordinarily complex layout. Land Rover engineers created an intricate network of hoses, pumps, and control valves designed to precisely manage temperatures across two separate cooling circuits.
While impressive in theory, this complexity introduces dozens of potential failure points, many of which are inaccessible without significant disassembly. The system features over 15 different hose connections, each secured with proprietary clips that deteriorate over time and create leak points throughout the engine bay.
The water pump design exemplifies the Range Rover Sport’s cooling system weaknesses. Unlike conventional units with simple mechanical operation, Land Rover employed an electronically controlled pump with variable flow rates.
The pump’s plastic impeller frequently cracks or separates from its shaft between 60,000-90,000 miles, causing catastrophic cooling loss. Worse still, its location behind multiple components makes replacement a labor-intensive procedure requiring specialized tools and expertise.
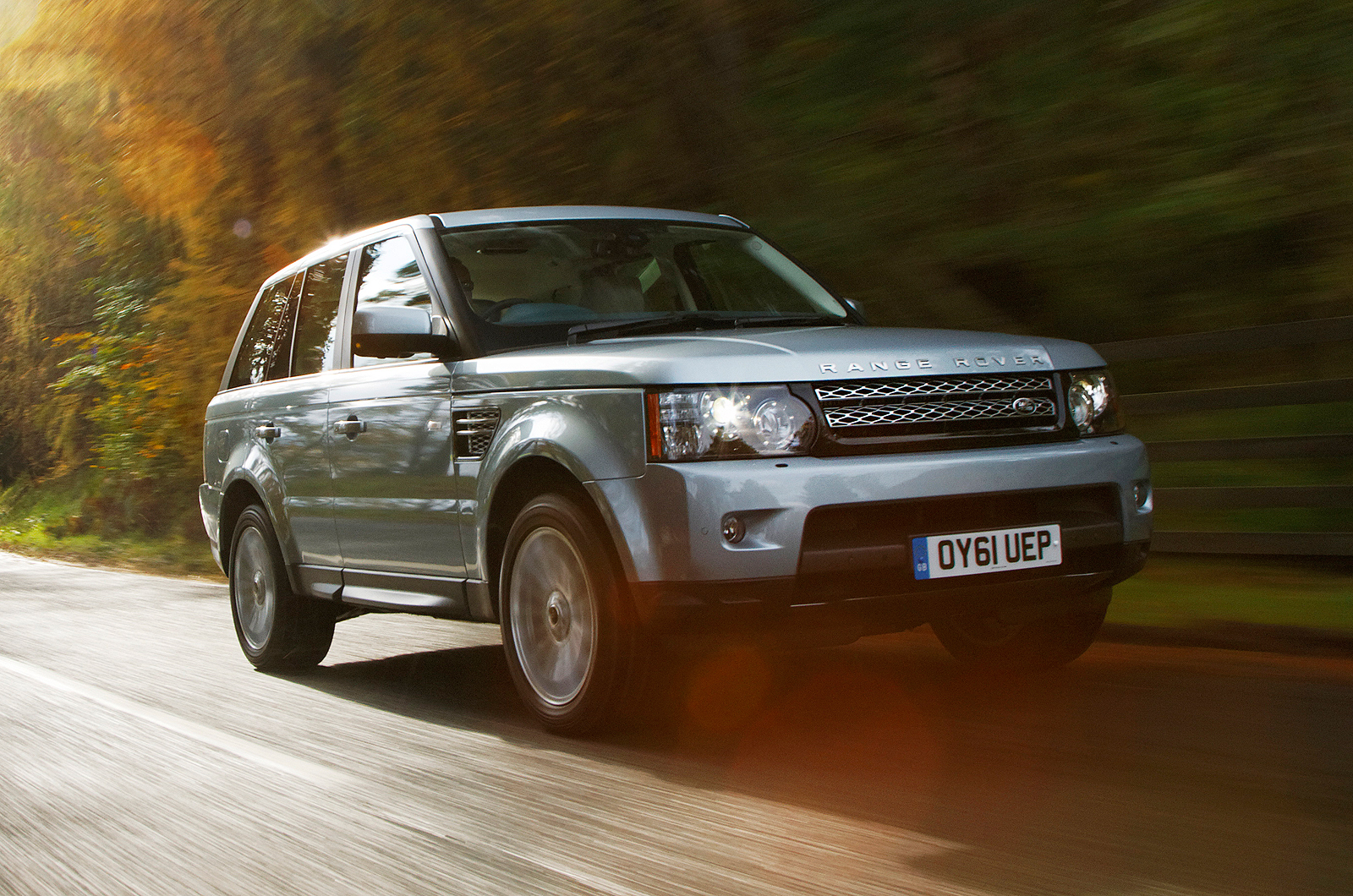
Perhaps most problematic is the vehicle’s thermostat housing assembly. Constructed primarily from plastic components bonded together, these housings invariably crack and leak after repeated heat cycling.
The housing integrates multiple sensors and control valves, meaning that replacement requires not just the housing itself but often several electronic components. The failure typically occurs where plastic components meet metal fittings, a fundamental materials engineering oversight that no amount of maintenance can prevent.
The radiator in Range Rover Sport models presents another critical weakness. While adequately sized for cooling capacity, its mounting design subjects it to excessive vibration and stress from off-road use, precisely the condition these vehicles are marketed to handle.
This vibration causes the plastic end tanks to develop cracks at mounting points, creating slow leaks that often go undetected until significant coolant loss occurs. The radiator’s location makes visual inspection challenging, further delaying detection of developing problems.
Compounding these issues is the expansion tank design. Located in a heat-soaked area of the engine bay and constructed from brittle plastic, these tanks develop stress cracks around the cap sealing surface and level sensor mount.
When they fail, they often do so catastrophically, spraying pressurized coolant throughout the engine bay and creating a sudden loss of cooling capacity.
Perhaps most frustrating for owners is that Land Rover’s official repair procedures often require specialized diagnostic equipment and dealer-only parts, making independent repairs challenging and expensive.
The cooling system’s integration with the vehicle’s complex electronic architecture means that improper repairs often trigger multiple error codes and drivability issues, forcing owners back to dealers despite the premium repair costs.
The Range Rover Sport’s cooling system failures exemplify how engineering complexity without corresponding durability creates a perfect storm of reliability issues.
Despite the vehicle’s premium positioning and price point, its cooling system demonstrates fragility that would be unacceptable in vehicles costing a fraction of its price.
5. Chevrolet Cruze 1.4T (2011-2016)
The Chevrolet Cruze, equipped with the 1.4-liter turbocharged engine, represents General Motors’ attempt to create a competitive compact car with European-inspired driving dynamics.
Unfortunately, the cooling system design has proven to be its Achilles’ heel, earning the vehicle a reputation for reliability issues that contradict Chevrolet’s marketing promises of dependability and value.
The water outlet housing stands as the Cruze’s most notorious cooling system failure point. In an apparent cost-cutting measure, GM constructed this critical component from brittle thermoplastic instead of the traditional metal.
This housing, which directs coolant flow from the engine to the radiator, consistently develops cracks along stress points after approximately 60,000 miles of regular heat cycling.
The failure typically occurs without warning, causing rapid coolant loss and potential overheating. Compounding this design flaw, the housing’s location requires extensive disassembly to access, transforming what should be a simple repair into a labor-intensive procedure costing several hundred dollars.
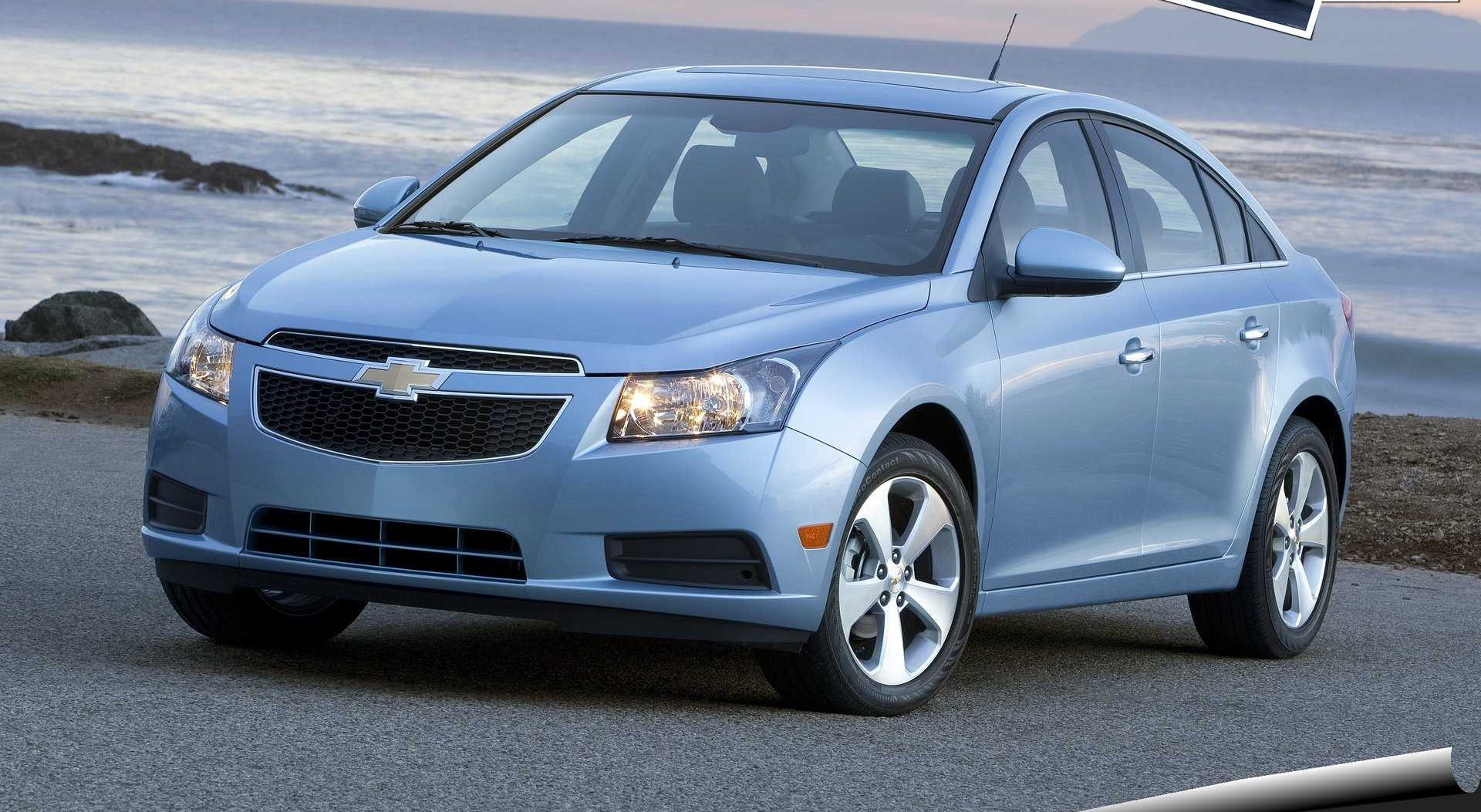
The Cruze’s water pump design compounds these cooling system woes. Unlike conventional designs with simple mechanical operation, GM utilized a complex variable-flow pump with plastic internal components.
These pumps commonly fail between 70,000-100,000 miles, often leaking coolant directly onto the timing belt, creating a risk of catastrophic engine failure if the belt deteriorates and breaks.
The pump’s location makes early detection of these leaks nearly impossible without specialized inspection procedures rarely performed during routine maintenance.
Perhaps most problematic is the Cruze’s coolant surge tank design. Constructed from thin-walled plastic and subjected to constant pressurization cycles, these tanks develop stress cracks around the cap sealing surface and pressure sensor mounting points.
When they fail, the pressurized system typically sprays coolant across the engine bay, creating a safety hazard from hot coolant and potentially damaging electrical components. The failure often occurs suddenly, leaving drivers stranded without warning.
The radiator in 1.4T Cruze models presents another weakness. To reduce weight and cost, GM employed aluminum cores with plastic end tanks connected by crimped joints. These joints deteriorate over time, developing leaks at the seam between the plastic and metal components.
The radiator’s positioning behind multiple front-end components makes visual inspection difficult, allowing minor leaks to go undetected until significant coolant loss occurs.
Exacerbating these hardware issues is the Cruze’s problematic coolant level monitoring system. The electronic sensor frequently provides false readings or fails, removing an important early warning mechanism for developing cooling system problems.
Many owners report that their coolant warning light never illuminated despite significant coolant loss, allowing engines to run dangerously low on coolant and risking serious damage.
General Motors has issued multiple technical service bulletins addressing these cooling system failures, but has avoided comprehensive recalls despite the pattern of consistent failures across the model range.
The recommended repair procedures typically involve replacing components with identical parts sharing the same design flaws, virtually guaranteeing that owners will face the same issues again as their vehicles age.
The Cruze’s cooling system problems have significantly impacted resale values and owner satisfaction, with many vehicles being traded in or sold at substantial losses when owners tire of repeated repairs.
What makes these failures particularly frustrating is that they occur in a vehicle marketed specifically for its reliability and low cost of ownership, promises that its cooling system design fundamentally undermines.
Also Read: 5 Cars That Hold Alignment Perfectly and 5 That Constantly Drift