Engine cooling systems represent a critical lifeline for modern power plants, preventing catastrophic thermal failure during operation. While most contemporary engines rely heavily on cooling fans to maintain optimal operating temperatures, some remarkable engine designs demonstrate exceptional resilience when faced with cooling system failures.
This unique capability stems from various engineering approaches: some engines feature overbuilt components with extraordinary thermal tolerances, others employ air-cooled designs that bypass conventional water-cooling dependencies, and some leverage innovative thermal management solutions that distribute heat through alternative pathways.
When a cooling fan fails, these engines can continue functioning at least temporarily without immediate breakdown. Understanding which engines possess this remarkable survivability provides valuable knowledge for mechanics, automotive enthusiasts, and everyday drivers who might encounter emergencies.
This analysis explores the top ten engines renowned for their ability to withstand cooling fan failures, examining their design characteristics, historical performance records, and the engineering principles that contribute to their exceptional thermal endurance.
While no engine can operate indefinitely without proper cooling, these exceptional power plants demonstrate impressive resilience that distinguishes them in the automotive landscape.
1. Air-Cooled Volkswagen Flat-Four Engine
The air-cooled Volkswagen flat-four engine, most famously powering the iconic Beetle and Type 2 Bus, stands as perhaps the quintessential example of an engine designed to operate without conventional water cooling or electric fans.
First conceived in the 1930s by Ferdinand Porsche, this remarkable power plant relies entirely on ambient airflow directed across the cylinder fins by a fan connected directly to the crankshaft. This elegant simplicity eliminates numerous potential failure points found in water-cooled systems.
The fundamental genius of the VW air-cooled design lies in its thermal efficiency principles. The horizontally-opposed cylinder layout exposes maximum surface area to cooling air, while individual cylinder cooling fins significantly increase the heat dissipation capacity.
Each cylinder and cylinder head is surrounded by specially designed aluminum fins that conduct heat away from combustion chambers rapidly. The engine’s magnesium-alloy crankcase further enhances heat dissipation properties, helping maintain tolerable operating temperatures even under stress.
What truly distinguishes this engine is its ability to maintain operational integrity even when subjected to extreme conditions. Multiple documented cases exist of Beetles traversing scorching deserts with compromised cooling systems.
The engine’s inherent thermal resilience stems from its conservative engineering approach relatively low compression ratios (typically 6.6:1 to 8.0:1) coupled with modest power outputs reduce internal heat generation, while generous clearances between moving parts accommodate thermal expansion without seizing.
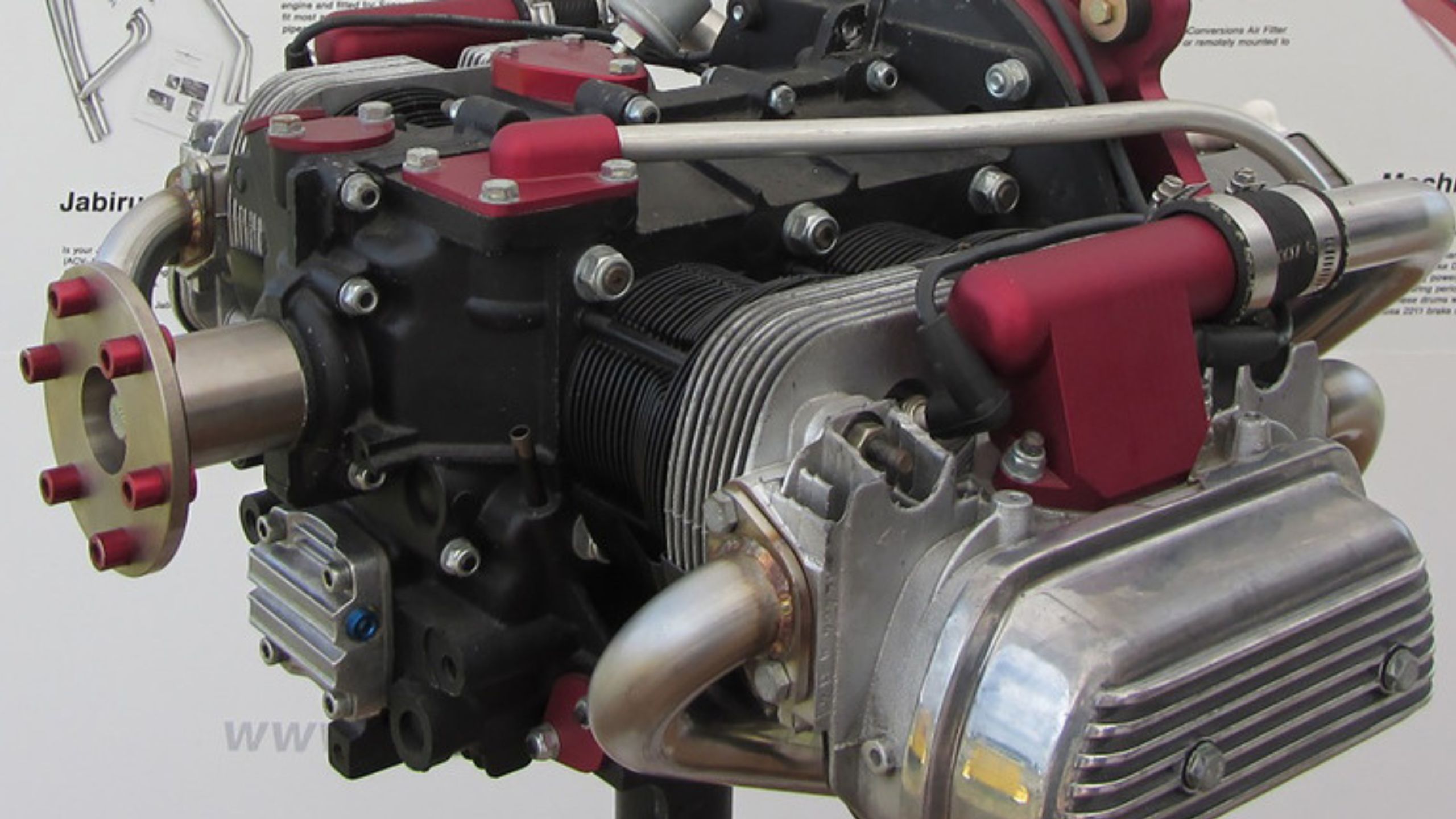
Another critical factor contributing to the flat-four’s survivability is its oil system design. The engine employs a substantial oil capacity (typically 2.5-3 liters) that serves dual purposes: lubrication and auxiliary cooling.
As oil circulates through the engine, it absorbs considerable heat, effectively becoming a secondary cooling medium. This large oil volume provides significant thermal inertia, resisting rapid temperature increases during temporary cooling system compromises.
Historical evidence confirms the engine’s remarkable durability. During the 1960s and 1970s, Volkswagen Beetles completed numerous desert rallies, including the punishing Baja 1000, often with modified but still fundamentally air-cooled engines.
Military variants deployed in North Africa during World War II demonstrated similar resilience in extreme heat. The engine’s proven ability to withstand inadequate cooling made it a preferred choice for remote regions with limited mechanical support facilities throughout its production run spanning nearly seven decades.
While modern emissions and performance requirements eventually rendered the air-cooled design obsolete for mainstream automotive applications, its fundamental engineering principles continue influencing applications where cooling system simplicity and reliability are paramount.
The legacy of this remarkable engine lives on in ultralight aircraft engines, certain motorcycle designs, and specialized off-road applications where mechanical simplicity translates directly to survival in challenging environments.
2. Porsche Air-Cooled Flat-Six Engine
The Porsche air-cooled flat-six engine represents perhaps the most sophisticated evolution of air-cooling principles in automotive history. Developed as a more powerful evolution of the Volkswagen flat-four design, Porsche engineers refined and expanded these principles to create a high-performance engine capable of both exceptional power output and remarkable thermal stability.
From its introduction in the original 911 in 1964 until the final air-cooled models in 1998, this engine defined the Porsche brand and established new benchmarks for air-cooled performance.
What makes the Porsche flat-six particularly resilient against cooling fan failures is its comprehensive thermal management strategy. Unlike simpler air-cooled designs, Porsche employed a complex system of targeted air delivery.
The engine features carefully engineered ducting that directs air precisely where needed most primarily to the cylinder heads, where combustion temperatures are highest.
The cooling fan, driven directly by the engine through a belt system, pushes air through these passages in a carefully calculated flow pattern that ensures even cooling across all cylinders.
This systematic approach means that even with reduced airflow from a partially functioning fan, critical components receive preferential cooling. The engine’s materials selection further enhances its thermal resilience.
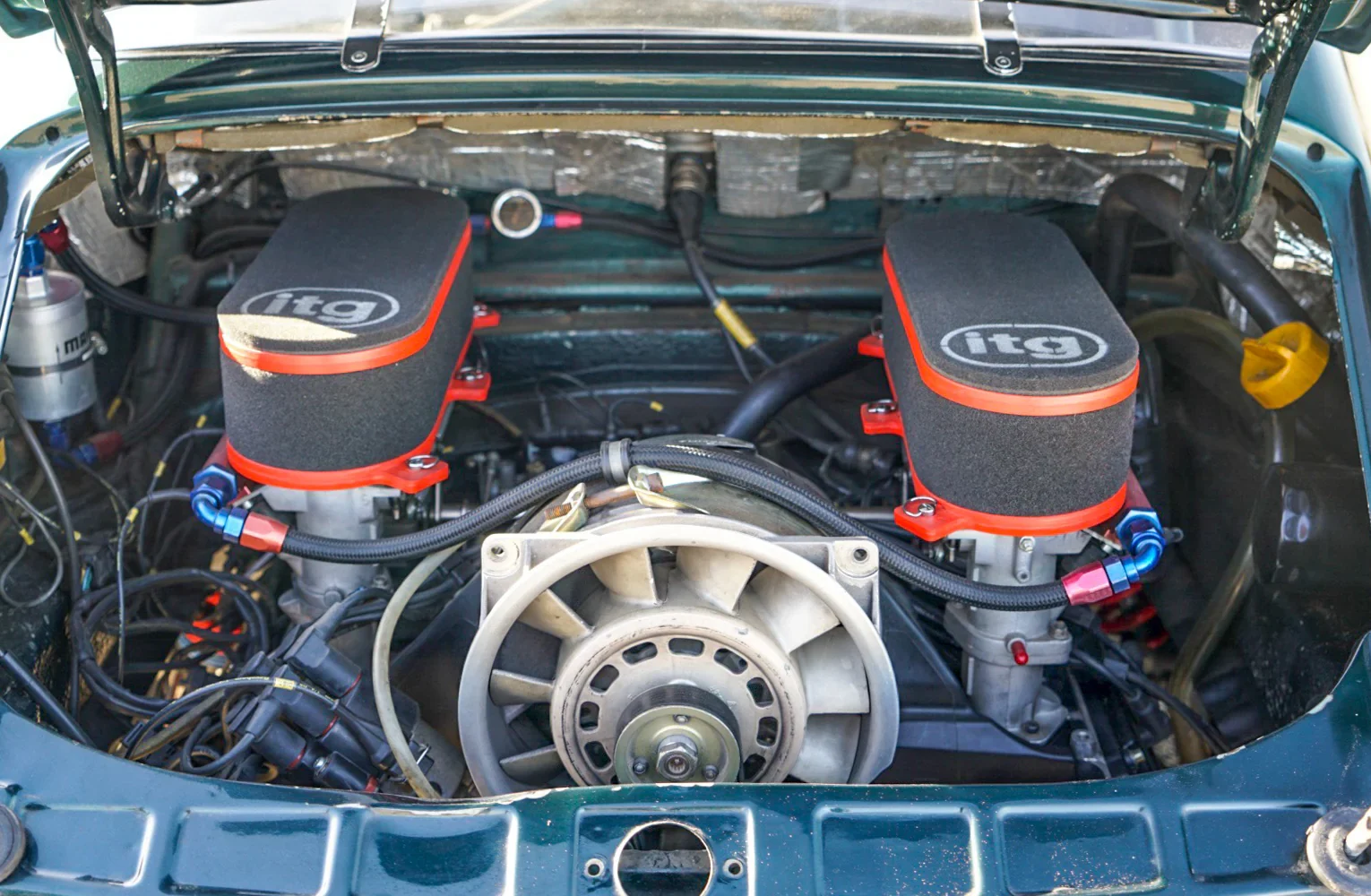
Porsche engineers employed aluminum alloys with specific heat transfer properties for cylinder heads and barrels. These components feature precisely engineered cooling fins whose size, spacing, and orientation were developed through extensive testing to maximize heat dissipation efficiency.
Later iterations of the design incorporated additional oil cooling circuits and, in turbocharged variants, specialized oil jets that sprayed lubricant directly onto critical areas such as piston undersides to manage localized heating.
Another key factor in the engine’s ability to survive cooling compromise is its fundamental architecture. The horizontally opposed cylinder layout inherently improves cooling by exposing maximum surface area to airflow while eliminating hot spots that occur in more compact engine designs.
The generous spacing between cylinders promotes effective air circulation, while the relatively long strokes used in many variants reduce piston speeds and associated friction heating.
Historical evidence of the engine’s durability abounds in motorsport applications. Air-cooled Porsche engines dominated endurance racing for decades, including multiple victories at the 24 Hours of Le Mans and the punishing Dakar Rally.
These successes came despite the brutal demands of sustained high-power operation in variable conditions, precisely the scenario that would reveal cooling system inadequacies. The engine’s proven ability to maintain thermal stability even when pushed to extremes demonstrates its inherent resilience.
Particularly impressive is the engine’s capacity for thermal self-regulation. As operating temperatures rise, the aluminum components expand at different rates from the steel crankcase, slightly altering the engine’s internal geometry in ways that can improve efficiency and reduce heat generation under certain conditions.
This passive adaptation mechanism contributes to the engine’s remarkable ability to survive temporary cooling system impairments. While modern emissions regulations and performance requirements eventually forced Porsche to abandon air cooling in favor of water-cooled designs, the engineering principles developed during the air-cooled era continue influencing performance engine design.
The air-cooled flat-six remains among the most coveted and collectible engines ever produced, celebrated not just for its distinctive sound and character but for its legendary reliability and ability to perform consistently even when cooling systems are compromised.
3. Deutz Air-Cooled Diesel Engines
The Deutz air-cooled diesel engine series represents perhaps the most extreme application of air-cooling technology in high-stress industrial applications.
Originally developed in Germany following World War II, these engines were designed specifically to operate reliably in environments where water cooling systems would be impractical or vulnerable to failure.
The resulting design philosophy has created what many consider the ultimate expression of cooling system independence. What distinguishes Deutz air-cooled diesels from other air-cooled designs is their engineering focus on absolute reliability under adverse conditions.
Unlike automotive applications, where intermittent operation and variable loads are normal, industrial diesel engines frequently operate continuously at high loads for extended periods, conditions that would quickly reveal any cooling system inadequacies. Deutz addressed this challenge through several innovative approaches to thermal management.
The fundamental architecture employs individual cylinders with extensive cooling fins cast directly into the iron cylinder material. This modular design allows for optimal cooling fin arrangement around each combustion chamber while eliminating potential failure points such as head gaskets and water jackets.
The direct integration of cooling surfaces with combustion chambers minimizes thermal resistance, allowing heat to transfer efficiently from the combustion process to the cooling surfaces.
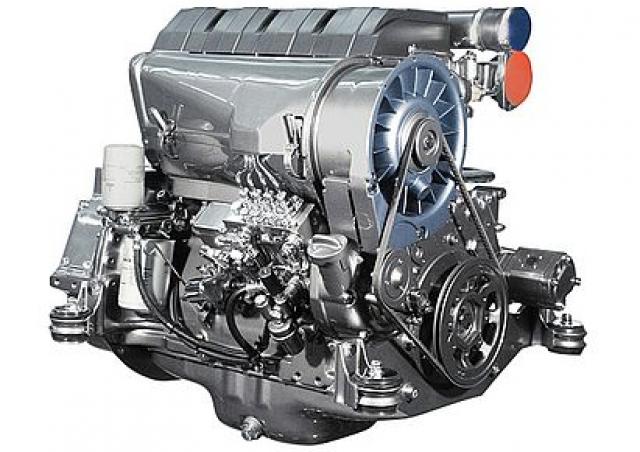
Most distinctive in the Deutz approach is the cooling fan system design. Rather than employing a single large fan, Deutz engines typically use an axial fan of substantial diameter mounted directly to the crankshaft.
This arrangement eliminates intermediary drive mechanisms that could fail while ensuring that airflow scales proportionally with engine speed. The fan’s design priority is redundancy and robustness rather than noise optimization, with multiple large blades capable of moving substantial air volume even with partial damage.
The engines also incorporate sophisticated baffling systems that direct cooling air precisely where needed most. Internal ducting ensures that hotter components, particularly exhaust valve areas and injector tips, receive prioritized airflow.
This targeted cooling approach means that even with compromised airflow, critical components remain within operational temperature ranges longer than would otherwise be possible.
Oil cooling plays a crucial role in the thermal management strategy. Deutz engines typically employ substantial oil capacities and dedicated oil coolers that serve as auxiliary heat exchangers.
The lubricating oil effectively becomes a heat transfer medium, absorbing thermal energy from internal components and releasing it through dedicated cooling surfaces. This oil-based heat transfer system provides significant thermal inertia, slowing temperature increases during cooling system impairment.
Historical evidence of these engines’ remarkable durability comes from their widespread deployment in challenging environments worldwide. Deutz air-cooled diesels have powered everything from agricultural equipment in remote regions to military generators in desert conditions.
Particularly notable is their adoption for emergency power generation applications where reliability during crises is paramount. Mining operations in remote locations similarly favor these engines for their ability to continue functioning when cooling systems are compromised.
Modern Deutz air-cooled designs continue incorporating these fundamental principles while improving efficiency and emissions compliance. The company’s F1L410 and F2L511 series engines remain in production for applications requiring exceptional reliability.
While water-cooled designs have generally supplanted air-cooled engines in many applications due to noise and emissions regulations, Deutz air-cooled diesels continue setting the standard for operational survival when cooling systems face compromise.
4. Radial Aircraft Engines
Radial aircraft engines, particularly those developed during aviation’s Golden Age from the 1920s through the 1950s, represent perhaps the most sophisticated air-cooling engineering achievement in internal combustion engine history.
These engines were designed explicitly to operate reliably in the most cooling-critical application possible, aircraft propulsion, where cooling system failure could be catastrophic and where weight and reliability were paramount concerns.
The fundamental architecture of radial engines provides inherent advantages for cooling system resilience. The cylinders are arranged radially around a central crankcase, resembling spokes on a wheel, with each cylinder directly exposed to the airstream.
This arrangement maximizes cooling surface area while ensuring that each cylinder receives fresh air rather than pre-heated air from another cylinder. The design eliminates the cooling imbalances common in inline or V-configuration engines, where rear cylinders often operate hotter than front cylinders.
Materials selection played a crucial role in radial engine thermal management. Most successful designs employed aluminum cylinder heads with steel cylinder barrels, often with fins machined directly into the material rather than cast.
This approach optimized both heat transfer properties and structural integrity. The fins themselves were precisely engineered in terms of spacing, depth, and profile to maximize air contact while minimizing airflow resistance.
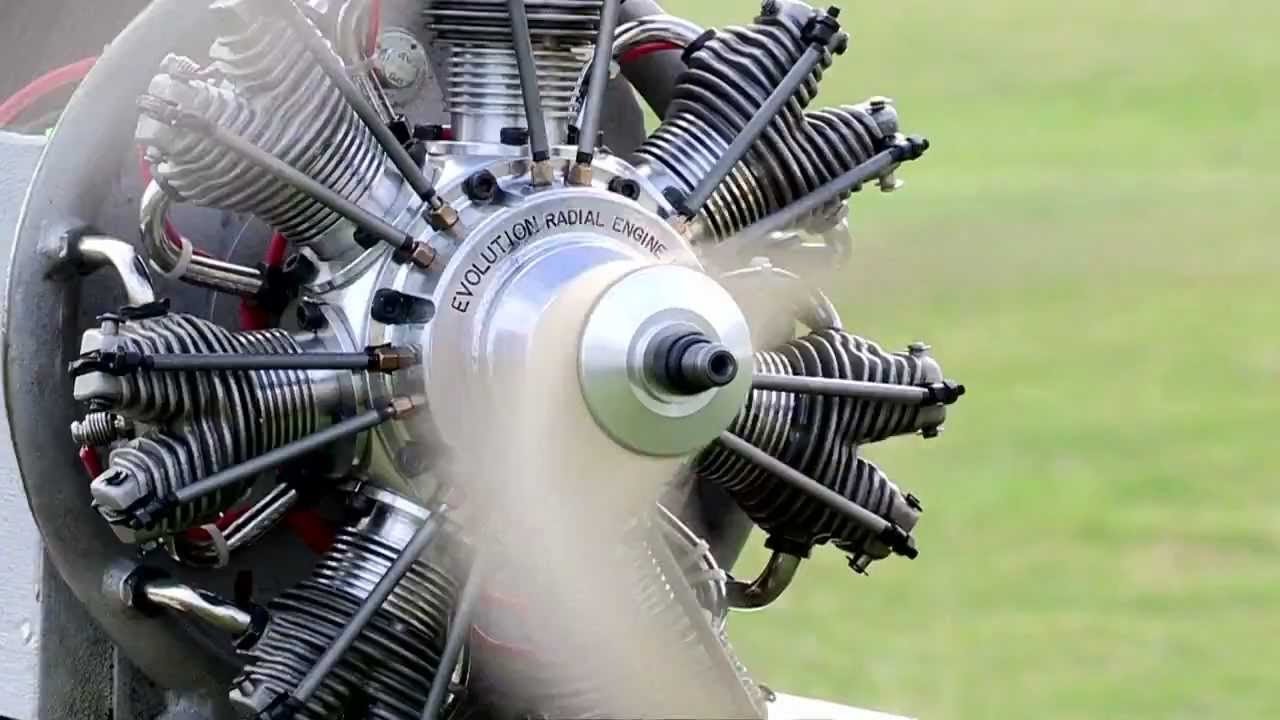
More sophisticated designs incorporated copper inserts in critical areas to enhance heat transfer from combustion chambers. What particularly distinguishes radial engines in terms of cooling resilience is their operational design envelope.
Aircraft engines are typically sized significantly larger than minimum requirements, allowing them to operate at a fraction of maximum output during cruise conditions.
This conservative operating strategy dramatically reduces thermal stress during normal operation, creating substantial thermal headroom when cooling is compromised. Additionally, pilots could manipulate mixture settings and power outputs to manage engine temperatures actively when necessary.
Historical evidence of radial engine cooling resilience comes from numerous documented cases of aircraft completing long flights with damaged cooling systems. During World War II, many aircraft returned safely despite suffering battle damage that affected cooling airflow.
The Pratt & Whitney R-2800 “Double Wasp” engine, for example, gained a reputation for extraordinary ruggedness, with documented cases of continued operation despite significant cooling fin damage from combat.
The oil system design further enhanced thermal resilience. Radial engines typically employed dry-sump lubrication systems with large external oil tanks.
This arrangement allowed for substantial oil volumes that provided significant thermal inertia while also serving as auxiliary cooling media. Oil jets directed at critical components such as valve guides and piston undersides managed localized hot spots effectively, even when cooling was compromised.
Another key factor contributing to radial engine survivability was their inherent mechanical simplicity compared to liquid-cooled alternatives. The elimination of coolant pumps, radiators, hoses, and associated components removed numerous potential failure points.
This simplicity translated directly to reliability, particularly in combat or harsh environment operations where damage was likely. While modern aviation has largely transitioned to turbine engines, the engineering principles developed for radial engines continue influencing contemporary air-cooled designs.
The calculated balance between power output, thermal management, and mechanical simplicity established by radial engines represents a high watermark in internal combustion engine design that continues to instruct engineers about survivability under adverse conditions.
Also Read: 5 Cars With Engines That Never Overheat and 5 That Are Cooling System Nightmares
5. BMW Boxer Motorcycle Engines
The BMW boxer motorcycle engine represents one of the most enduring and successful air-cooled designs in transportation history.
First introduced in 1923 with the R32 model and continuing in production in evolved forms until the late 2000s (with some variants still produced today), this horizontally-opposed twin-cylinder configuration has demonstrated extraordinary resilience against cooling system compromises across nearly a century of service.
What distinguishes the BMW boxer design is its fundamentally balanced approach to thermal management. The horizontally opposed cylinder arrangement places both cylinders directly in the airstream, ensuring neither operates at a cooling disadvantage.
This symmetric cooling dynamic eliminates the thermal imbalances common in V-twin or inline configurations, where rear cylinders typically run hotter than front cylinders.
The cylinders’ prominent projection into the airflow creates a self-cooling effect that increases with vehicle speed precisely when engine loads and heat generation typically rise.
Material selection plays a crucial role in the boxer engine’s thermal resilience. BMW engineers employed aluminum alloys with high thermal conductivity for cylinder heads while using cast iron or aluminum cylinders with steel liners for the barrels.
This combination optimizes heat transfer from combustion chambers while maintaining dimensional stability under thermal stress. The cooling fins themselves evolved significantly over decades of development, with later models featuring precisely engineered fin designs that maximize surface area while directing airflow to critical areas.
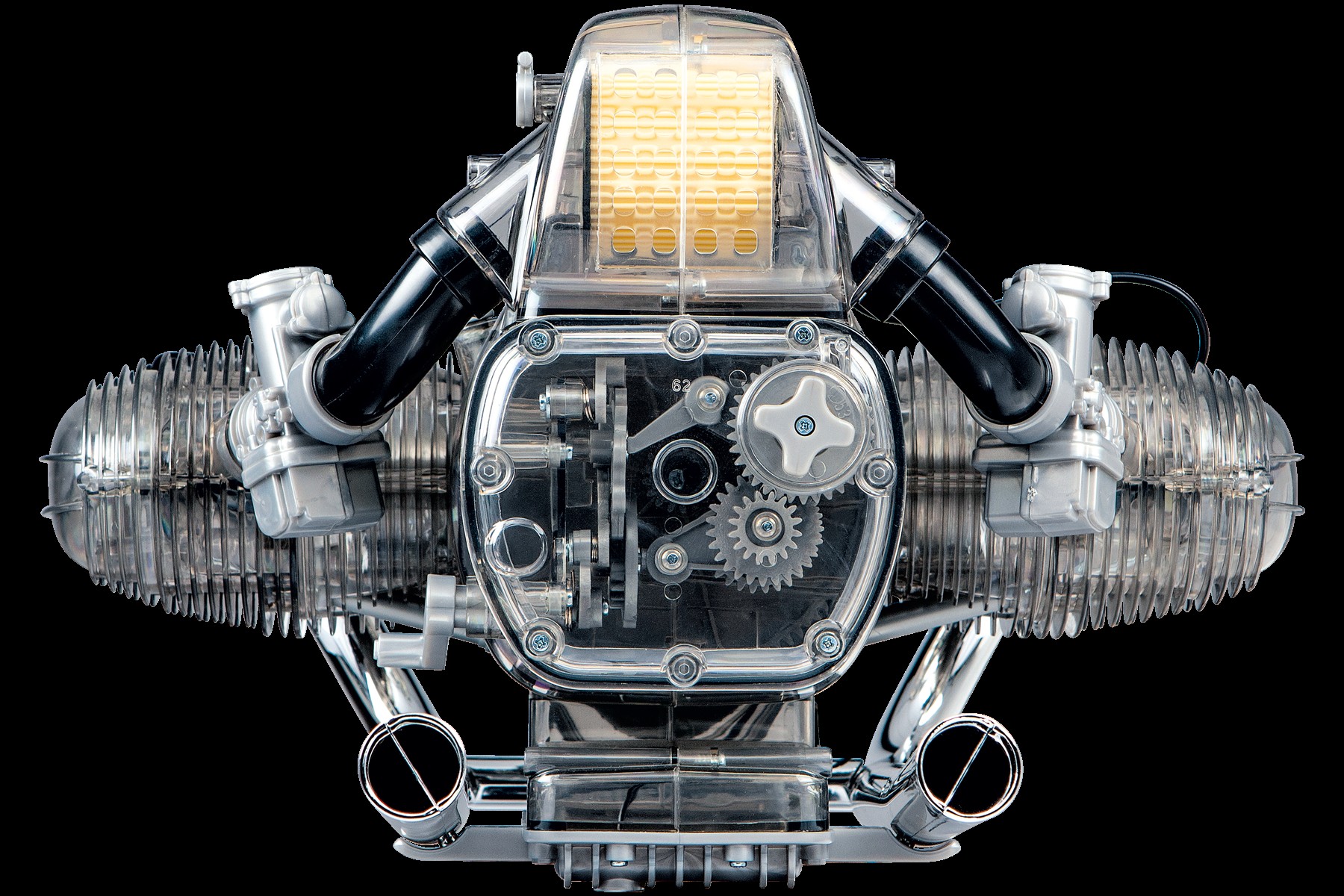
The boxer’s inherent mechanical characteristics further enhance its ability to survive cooling system impairments. The engine employs relatively conservative internal geometries, moderate compression ratios, generous bearing surfaces, and substantial oil clearances that accommodate thermal expansion without catastrophic consequences.
This mechanical forgiveness creates a wider thermal operating envelope than more highly stressed designs. Additionally, the layout distributes heat generation across a broad physical area rather than concentrating it in a compact space, reducing localized hot spots.
Oil system design represents another significant contributor to the boxer’s cooling resilience. BMW employed wet-sump lubrication with substantial oil capacities (typically 3-4 liters) that provide significant thermal inertia.
The lubrication system often incorporates an oil cooler mounted prominently in the airflow, creating a supplementary cooling circuit that remains effective even when other cooling is compromised. On later models, thermostatic oil control valves prioritize oil cooling based on operating conditions.
Historical evidence of the boxer engine’s remarkable durability comes from its extensive use in extreme environments. BMW motorcycles have completed countless desert rallies, including the punishing Paris-Dakar event, often with minimal modifications to their cooling systems.
Perhaps most telling is the boxer engine’s adoption by police forces and military units worldwide, including desert deployments where cooling system reliability is critical. The Australian outback and African safari touring applications further demonstrate the design’s capacity to withstand extreme heat with compromised cooling.
The evolution of the boxer design into the 1970s-2000s introduced additional features enhancing cooling resilience. The R100 series incorporated oil jets directed at piston undersides for localized cooling of these critical components.
Later oilhead models added oil-cooling circuits to complement traditional air cooling, creating a hybrid approach that maintained the fundamental simplicity of air cooling while adding thermal capacity.
Even the transition to partial liquid cooling in the 2000s with the “hexhead” engines maintained the fundamental boxer architecture while addressing modern emissions requirements.
What’s particularly impressive about the BMW boxer design is its proven longevity under adverse conditions. Documented cases exist of these engines exceeding 300,000 miles with minimal rebuilding, often in challenging environments where cooling systems face regular stress.
This extraordinary durability testifies to the fundamental soundness of the thermal management approach and the conservative engineering margins incorporated into the design.
6. Lycoming and Continental Aircraft Engines
The horizontally-opposed aircraft engines manufactured by Lycoming and Continental represent perhaps the most successful and widely deployed air-cooled designs in history.
These engines have powered the majority of general aviation aircraft produced since the 1950s, accumulating billions of flight hours across varied and often challenging operating conditions.
Their remarkable thermal resilience stems from sophisticated engineering approaches developed specifically for aviation applications, where cooling system reliability directly impacts safety.
What distinguishes these engines from other air-cooled designs is their comprehensive thermal management strategy. Unlike automotive applications, where variable loads and speeds are normal, aircraft engines must maintain consistent temperatures across widely varying conditions from ground operations with minimal airflow to high-power climbs to extended cruise operations.
This challenging requirement led to several innovative approaches to cooling system design. The fundamental architecture employs horizontally opposed cylinders (typically four, six, or eight) arranged to ensure each cylinder receives equivalent cooling airflow.
This balanced layout eliminates the cooling imbalances common in other configurations. Each cylinder features extensive cooling fins precisely engineered in terms of size, spacing, and orientation to maximize heat dissipation while minimizing aerodynamic drag.
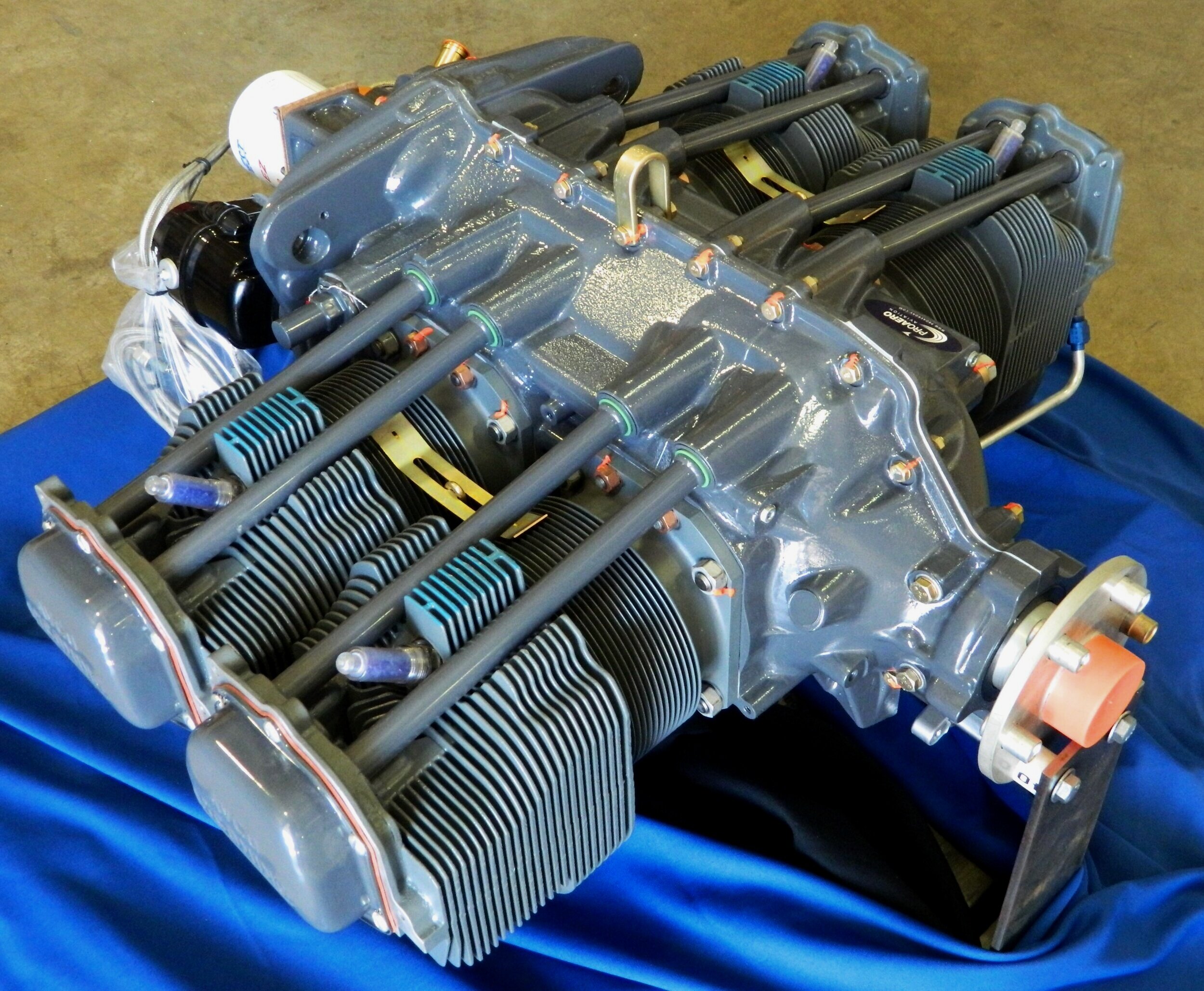
The cylinder heads incorporate additional fins around valve areas where combustion temperatures are highest. Materials selection significantly enhances thermal resilience.
Most designs employ aluminum cylinder heads for optimal heat conductivity, coupled with steel cylinder barrels or nitrided steel liners that maintain dimensional stability under thermal stress.
In more advanced designs, critical areas such as valve guides and seats incorporate additional materials like bronze or beryllium copper selected specifically for their thermal properties, creating local heat-transfer enhancements in the most thermally stressed regions.
The baffling system represents a crucial innovation in these engines’ cooling approach. Carefully engineered sheet metal baffles direct cooling air precisely where needed, creating pressure differentials that force air through cylinder fin passages rather than flowing around them.
This systematic approach means that even with compromised airflow, the remaining air is utilized with maximum efficiency. The baffling design has been continuously refined based on thermal imaging and operational data to eliminate hot spots and optimize cooling effectiveness.
Oil system design provides substantial auxiliary cooling capacity. These engines typically employ dry-sump lubrication systems with remote oil tanks holding significant oil volumes (8-12 quarts)
This arrangement creates thermal inertia while allowing oil to cool between circulation cycles. The oil circulates through dedicated passages in critical areas, effectively becoming a secondary cooling medium.
Many installations include oil coolers that function as additional heat exchangers, creating redundancy in the thermal management system. Operating characteristics further enhance cooling resilience.
These engines are typically operated at 65-75% of maximum rated power during cruise conditions, creating substantial thermal headroom. Lean-of-peak operation techniques, where the engine runs with excess air, can reduce internal temperatures significantly.
Pilots can actively manage engine temperatures through power settings, mixture controls, and cooling airflow, creating operational flexibility when cooling is compromised.
Historical evidence of these engines’ extraordinary durability comes from their extensive service record. Lycoming and Continental engines routinely achieve 2,000+ hours between overhauls, often in challenging environments ranging from desert training facilities to Arctic bush operations.
Their proven reliability has made them the predominant choice for applications where engine failure would be catastrophic, including single-engine aircraft operations over inhospitable terrain.
Modern variants continue incorporating these fundamental thermal management principles while improving efficiency and reliability. The basic engineering approach remains unchanged after decades of refinement, testifying to the soundness of the original design philosophy.
This remarkable continuity demonstrates how effectively these engines have solved the challenge of reliable air cooling under variable conditions.
7. Harley-Davidson Evolution V-Twin Engine
The Harley-Davidson Evolution V-twin engine, produced from 1984 to 1999, represents a significant achievement in air-cooled engine thermal management for high-performance motorcycle applications.
Developed during a critical period when Harley-Davidson was fighting for survival against Japanese competition, the “Evo” engine needed to deliver both improved reliability and enhanced performance while maintaining the traditional air-cooled V-twin architecture that defined the brand’s identity.
The resulting design created an engine with remarkable resilience against cooling system compromises. What distinguishes the Evolution engine from its predecessors and many competitors is its comprehensive approach to thermal management within air-cooling constraints.
The 45-degree V-twin layout inherently creates cooling challenges, with the rear cylinder typically running hotter than the front due to its position in the airflow path.
Harley engineers addressed this fundamental issue through several innovative approaches that dramatically improved thermal balance between cylinders.
Material selection played a crucial role in the Evolution’s thermal resilience. The engine employed aluminum cylinder heads with significantly improved thermal conductivity compared to the iron heads used on previous generations.
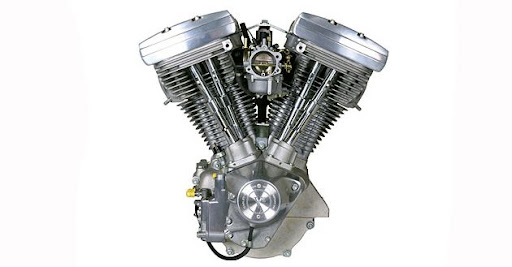
These heads featured redesigned cooling fins with optimized spacing and greater surface area, particularly around valve areas where temperatures are highest. The cylinders themselves used aluminum with cast-iron liners, creating an effective heat transfer pathway from combustion chambers to cooling fins.
The Evolution’s internal geometry further enhanced its ability to withstand cooling system compromises. The engine employed relatively conservative specifications, moderate compression ratios, substantial bearing surfaces, and generous clearances between moving parts that allowed for thermal expansion without catastrophic consequences.
This mechanical forgiveness created a wider thermal operating envelope than more highly stressed designs. The combustion chamber design improved flame propagation, reducing the likelihood of detonation under high-temperature conditions.
Oil system design represented another significant advance in the Evolution’s cooling approach. The engine employed a high-capacity oil pump and substantial oil volume that served dual purposes: lubrication and auxiliary cooling.
Oil passages directed lubricant to critical areas such as valve guides and rocker arm assemblies, effectively creating an additional cooling circuit for these thermally stressed components. Later models incorporated an oil cooler mounted prominently in the airflow, further enhancing the engine’s thermal management capabilities.
Production techniques also contributed to the Evolution’s cooling resilience. Improved casting methods allowed for more precise control of metal thickness in critical areas, eliminating the hot spots that plagued earlier designs.
More consistent fin formation improved cooling effectiveness, while tighter quality control ensured more uniform heat dissipation across production engines. These manufacturing improvements translated directly to better thermal stability under adverse conditions.
Historical evidence of the Evolution engine’s durability comes from its extensive real-world service record. The engine powered Harley-Davidson motorcycles through the brand’s renaissance, proving itself capable of extended high-speed operation in conditions ranging from Death Valley summer rides to cross-country touring.
Documented cases exist of Evolution engines exceeding 100,000 miles without major rebuilding, often in challenging environments where cooling systems face regular stress.
Particularly notable is the Evolution engine’s performance in modified form. Despite being designed for relatively modest outputs of 50-70 horsepower in stock form, the basic architecture proved capable of supporting significantly higher power levels with appropriate modifications.
This thermal headroom demonstrated the fundamental soundness of the cooling system design and the conservative engineering margins incorporated into the platform.
While Harley-Davidson eventually transitioned to partially liquid-cooled designs for their high-performance models, the Evolution engine’s success in managing heat through purely air-cooled means set a benchmark for V-twin motorcycle engines.
Its ability to maintain reliable operation despite the inherent cooling challenges of its configuration testifies to the sophisticated thermal management approach incorporated into what appears superficially to be a simple, traditional design.
8. Honda GX Series Industrial Engines
The Honda GX series of single-cylinder industrial engines represents perhaps the most widely deployed small air-cooled engine platform globally, with applications ranging from generators and water pumps to construction equipment and agricultural implements.
First introduced in the 1980s and continuously refined since, these engines have established an unparalleled reputation for reliability under adverse conditions, including situations where cooling systems face compromise.
What distinguishes the GX series from competitor designs is Honda’s systematic approach to thermal management within strict cost and weight constraints.
Unlike automotive or aircraft engines, where cost is a secondary consideration to performance, industrial engines must balance reliability with economic viability. Honda achieved this balance through several innovative design approaches that maximize cooling efficiency while minimizing complexity.
The fundamental architecture employs an overhead valve (OHV) design with the valvetrain contained within the cylinder head. This arrangement concentrates the most thermally stressed components, valves, valve seats, and combustion chamber in a single area where cooling can be prioritized.
The cylinder head features extensive cooling fins strategically placed to maximize heat dissipation from these critical areas. The fins themselves are precisely engineered in terms of size, spacing, and orientation to optimize airflow while maintaining structural integrity.
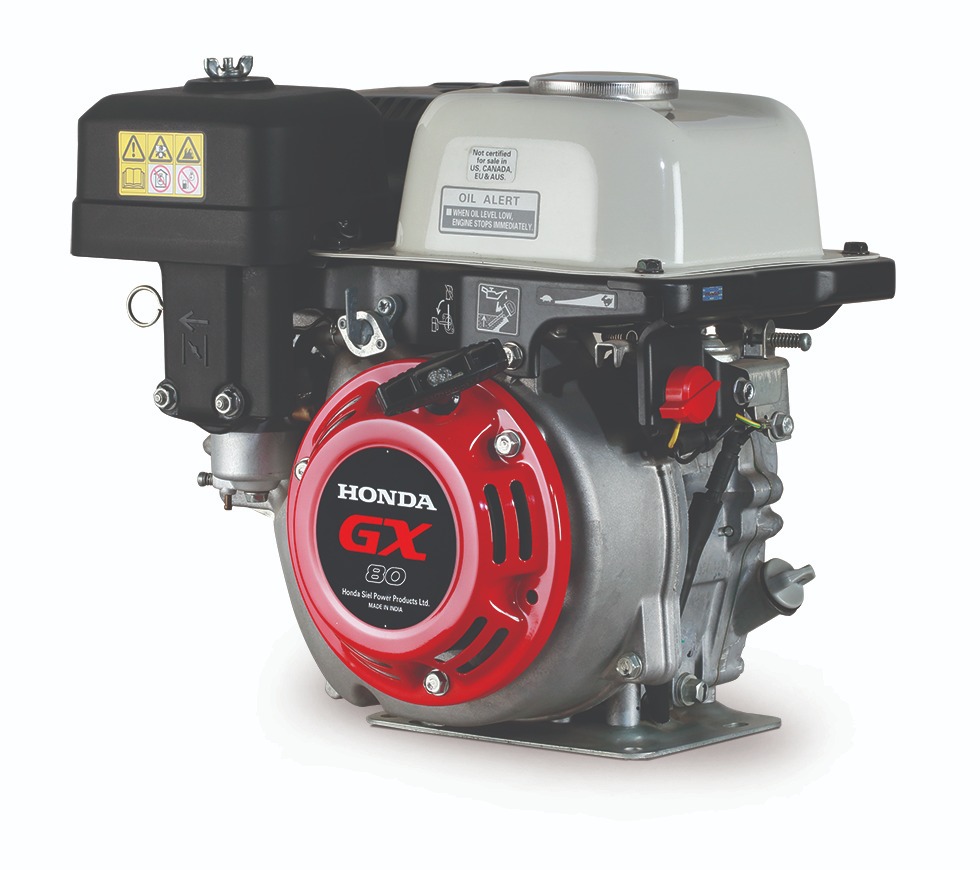
Materials selection significantly enhances thermal resilience. The GX series employs an aluminum cylinder head with excellent thermal conductivity paired with a cast iron cylinder sleeve that maintains dimensional stability under temperature fluctuations.
This combination optimizes heat transfer while preserving critical tolerances between piston and cylinder. The piston itself typically incorporates a steel insert at the top ring land, preventing deformation in this critical area during high-temperature operation.
The cooling fan system represents a crucial innovation in the GX approach to thermal management. Unlike many industrial engines that employ simple flat fan blades, Honda developed a sophisticated flywheel-integrated fan with precisely engineered blade profiles that maximize airflow while minimizing noise and power consumption.
The fan housing incorporates carefully designed ducting that directs cooling air specifically to the cylinder head and barrel rather than allowing it to dissipate ineffectively. This targeted cooling approach means that even with partially compromised airflow, critical components receive preferential cooling.
Oil system design further enhances thermal resilience. The GX engines employ a splash lubrication system with precisely positioned oil dippers and strategic internal oil passages.
This arrangement ensures that oil reaches critical components such as valve guides and rocker arms, creating an auxiliary cooling effect beyond pure lubrication.
The engines also incorporate an effective oil scraper system that prevents excessive oil accumulation in the combustion chamber, which could lead to carbon buildup and associated hot spots.
The GX series’ operating characteristics further contribute to its cooling resilience. These engines typically operate at relatively low engine speeds (3,000-3,600 RPM) compared to automotive applications, reducing friction-generated heat.
The governor system prevents sustained operation at excessive loads, creating an inherent protection mechanism against overheating. Additionally, most applications incorporate automatic decompression systems that reduce starting loads, preventing heat buildup during difficult starting conditions.
Historical evidence of the GX series’ extraordinary durability comes from its extensive deployment in challenging environments worldwide. These engines power equipment in environments ranging from equatorial construction sites to remote mining operations, often with minimal maintenance.
Their adoption by rental equipment companies, who prioritize reliability above all other factors, testifies to their proven ability to withstand adverse operating conditions, including compromised cooling.
What’s particularly impressive about the GX series is its progressive refinement over decades of production. Honda has continuously incorporated improvements based on field data, gradually enhancing thermal management while maintaining backward compatibility with existing applications.
This evolutionary approach has created an engine platform that combines sophisticated thermal engineering with exceptional reliability, establishing a benchmark for small industrial engines worldwide.
9. Briggs & Stratton Vanguard V-Twin Engines
The Briggs & Stratton Vanguard V-twin engine series represents one of the most successful commercial air-cooled designs in the small engine market, widely deployed in applications ranging from zero-turn mowers and generators to pressure washers and industrial equipment.
Developed to compete in the premium segment against Honda and Kawasaki offerings, the Vanguard engines incorporate sophisticated thermal management strategies that enable them to continue functioning even when cooling systems are compromised.
What distinguishes the Vanguard V-twin design from many competitors is its comprehensive approach to thermal balance a significant challenge in V-twin configurations where the rear cylinder typically runs hotter than the front.
Briggs & Stratton engineers addressed this fundamental issue through several innovative design elements that dramatically improve heat distribution and dissipation across the engine.
The basic architecture employs a 90-degree V-angle rather than the narrower angles used in many compact V-twins. This wider separation between cylinders significantly improves cooling airflow to the rear cylinder, reducing the thermal imbalance common in other V-configurations.
Each cylinder features individual cooling fins precisely engineered in size, spacing, and orientation to maximize heat dissipation while maintaining structural integrity. The cylinder heads incorporate additional fins around valve areas where combustion temperatures are highest.
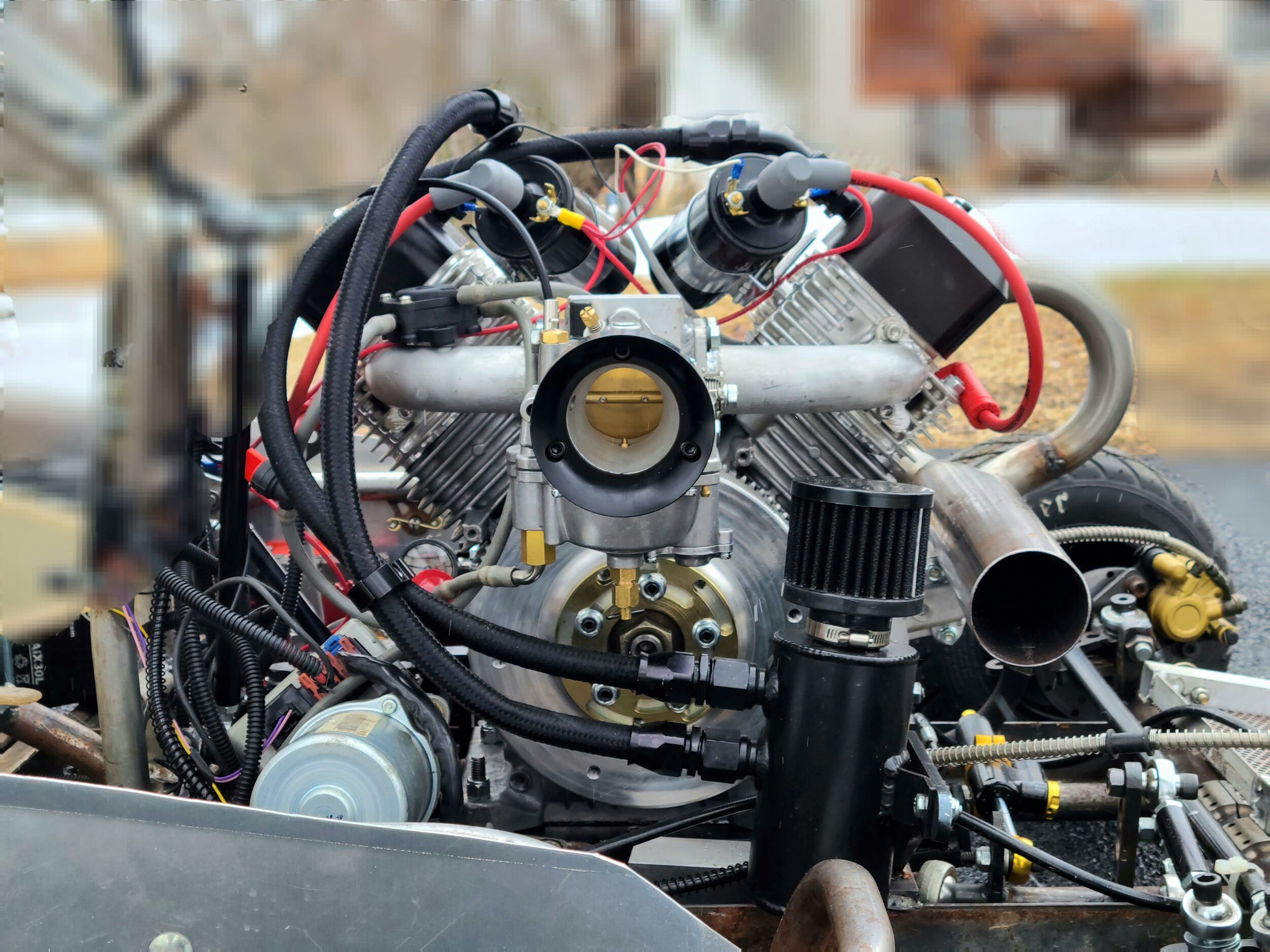
Materials selection plays a crucial role in the Vanguard’s thermal resilience. The engine employs aluminum cylinder heads with superior thermal conductivity paired with cast iron cylinder sleeves that maintain dimensional stability under thermal stress.
This combination optimizes heat transfer while preserving critical tolerances between pistons and cylinders. The pistons themselves incorporate features specifically designed to manage heat, including strut-supported designs that reduce deformation under thermal load.
The cooling fan system represents a significant innovation in the Vanguard approach. Unlike many small engines that employ simple paddle-type fans, the Vanguard uses a sophisticated flywheel-integrated fan with precisely engineered blade profiles that maximize airflow while minimizing noise and power consumption.
The fan housing incorporates carefully designed baffling that directs cooling air specifically toward the hottest regions of each cylinder rather than allowing it to dissipate ineffectively. This targeted cooling approach means that even with reduced airflow, critical components receive preferential cooling.
Oil system design further enhances thermal resilience. The Vanguard employs a pressure lubrication system with a gear-driven oil pump rather than the simpler splash systems common in lower-cost engines.
This arrangement ensures consistent oil delivery to critical components regardless of engine orientation or operating conditions. Oil passages direct lubricant specifically to valve guides and rocker arm assemblies, effectively creating an auxiliary cooling circuit for these thermally stressed components.
Many applications incorporate an oil filter, maintaining lubricant cleanliness that directly impacts cooling effectiveness. Electronic engine management systems in modern Vanguard engines provide additional thermal protection.
Electronic ignition systems can automatically adjust timing based on operating conditions, reducing heat generation under stress. Some models incorporate electronic fuel management that optimizes air-fuel ratios based on engine temperature, creating an adaptive response to cooling system limitations.
These sophisticated controls allow the engine to modify its operation when facing cooling challenges, extending the period before thermal damage occurs.
Historical evidence of the Vanguard’s durability comes from its extensive adoption in commercial applications where reliability directly impacts profitability.
Commercial landscaping operations, rental equipment fleets, and industrial applications choose these engines specifically for their ability to maintain operation under adverse conditions.
Documented cases exist of Vanguard engines exceeding 2,000 hours of service in high-demand applications, often in challenging environments where cooling systems face regular stress.
What’s particularly impressive about the Vanguard series is how it achieves sophisticated thermal management within the constraints of a relatively simple, affordable design.
By focusing engineering resources specifically on cooling system effectiveness rather than adding complex systems, Briggs & Stratton created an engine platform that combines excellent thermal resilience with mechanical simplicity a combination that translates directly to reliability in real-world applications.
10. Toyota 22R Inline-Four Engine
The Toyota 22R inline-four engine, produced from 1981 to 1997, represents one of the most durably engineered water-cooled engines ever developed for mass production vehicles.
While fundamentally a water-cooled design, this remarkable powerplant deserves inclusion in this analysis for its extraordinary ability to survive cooling system failures that would render most water-cooled engines inoperable within minutes.
The 22R’s exceptional thermal resilience stems from Toyota’s engineering philosophy that prioritized reliability above all other considerations. What distinguishes the 22R from other water-cooled designs is its conservative approach to thermal stress.
Unlike many engines designed with minimal cooling system margins to maximize efficiency, the 22R incorporated substantial thermal headroom throughout its design. The engine block features unusually thick casting walls that absorb and distribute heat effectively, while the cylinder head gasket employs robust materials that maintain sealing integrity even under extreme temperature fluctuations.
These fundamental design choices create an engine unusually resistant to warping and head gasket failure, common failure modes during cooling system compromise. Materials selection significantly enhances thermal resilience.
The 22R employs a cast iron engine block with excellent thermal stability paired with an aluminum cylinder head that promotes rapid heat dissipation.
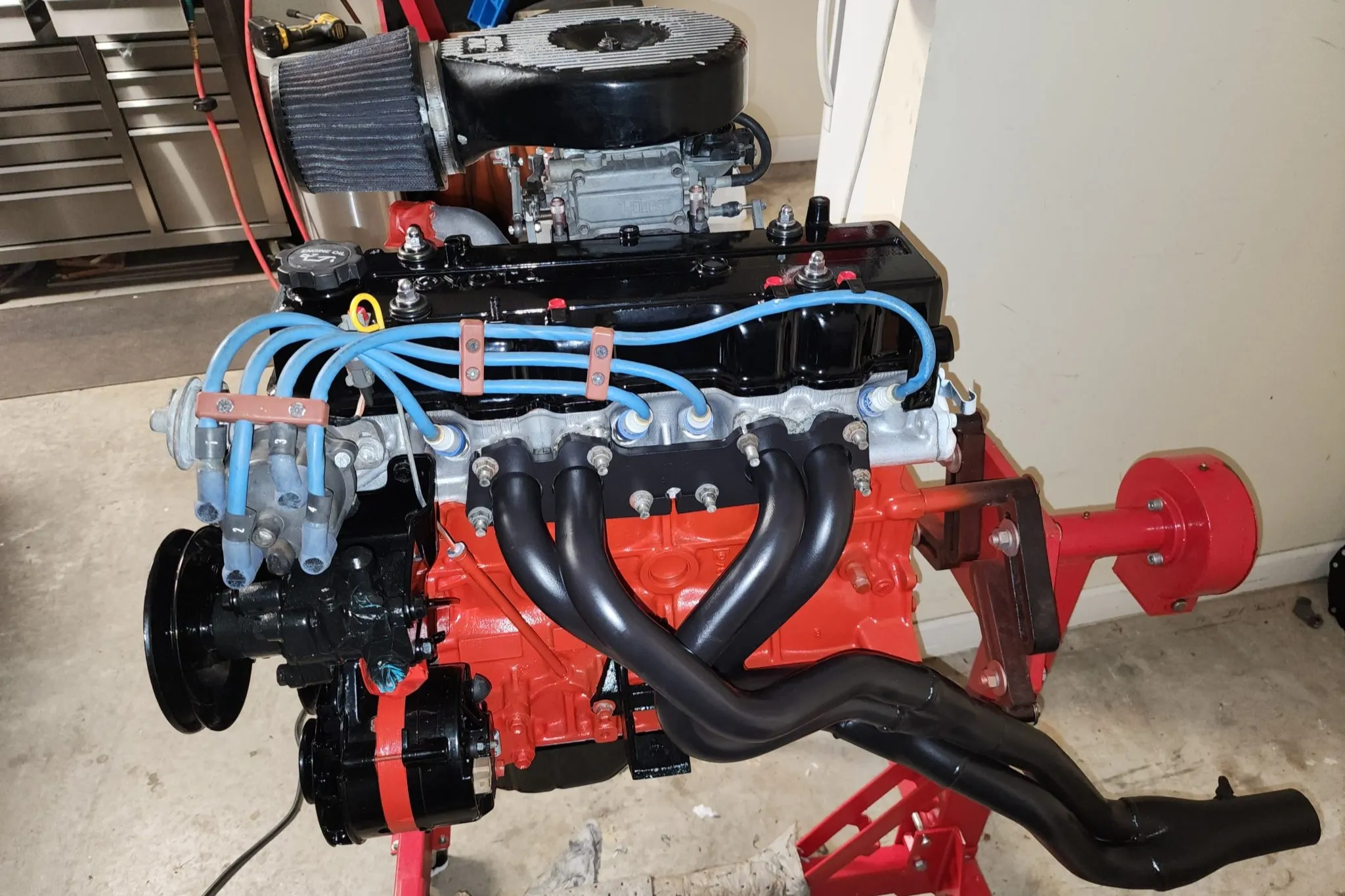
This combination optimizes structural integrity under thermal stress and cooling effectiveness during normal operation. Critical components such as valve seats and guides use materials specifically selected for thermal stability, preventing the dimensional changes that lead to accelerated wear during temperature excursions.
Internal geometry further contributes to the 22R’s survival capabilities. The engine employs relatively conservative specifications, moderate compression ratios, substantial bearing surfaces, and generous clearances between moving parts that accommodate thermal expansion without catastrophic consequences.
The combustion chamber design promotes even flame propagation, reducing hot spots that could lead to detonation under high-temperature conditions. The water jacket design features unusually large passages that continue providing some cooling effect even whenthe coolant flow is significantly reduced.
The cooling system itself incorporates several features that enhance survival during partial failures. The water pump is robustly constructed with a precision-balanced impeller and substantial shaft bearings, providing some circulation even when compromised.
The thermostat housing design minimizes stress on this critical component, reducing failure likelihood. Many 22R installations incorporate an auxiliary transmission oil cooler as a secondary heat exchanger, providing additional thermal capacity during cooling system stress.
Oil system design represents another significant contributor to the 22R’s cooling resilience. The engine employs a high-capacity oil pump and substantial oil volume that serves dual purposes: lubrication and auxiliary cooling.
Oil passages direct lubricant to critical areas such as valve guides and camshaft bearings, effectively creating an additional cooling circuit for these thermally stressed components. The oil pan features cooling fins in many applications, providing additional heat dissipation surface area.
Historical evidence of the 22R’s remarkable durability under cooling system compromise comes from countless documented cases of these engines surviving catastrophic cooling failures.
Toyota pickup trucks and 4Runners powered by 22R engines have completed desert crossings with damaged radiators, completed off-road expeditions with compromised water pumps, and continued operating despite coolant losses that would render most engines inoperable.
This extraordinary record establishes the 22R as perhaps the most thermally resilient water-cooled production engine ever mass-produced. What’s particularly impressive about the 22R is how it achieves this exceptional thermal resilience without sacrificing practicality.
Unlike some over-engineered designs that achieve durability at the expense of efficiency or performance, the 22R delivered reasonable power output, acceptable fuel economy, and excellent emissions compliance while maintaining its legendary durability.
This balanced approach explains why the engine remained in production for nearly two decades and why vehicles equipped with it continue operating reliably decades after manufacture.
The 22R’s legacy continues to influence modern engine design, particularly for applications where reliability under adverse conditions is paramount. Its fundamental engineering principles, conservative thermal loading, robust materials selection, and substantial safety margins represent timeless approaches to creating engines capable of surviving cooling system compromise.
While modern emissions and efficiency requirements have driven manufacturers toward more highly stressed designs, the 22R stands as a benchmark for what can be achieved when durability is the primary design objective.
Also Read: 5 Trucks With the Best Cold Weather Reliability and 5 That Freeze Up Fast