The fuel cap may seem like an insignificant component of a vehicle, but when its hinge mechanism fails, it can lead to a cascade of problems, including check engine lights, failed emissions tests, and decreased fuel efficiency.
While modern vehicles have evolved to include sophisticated tethering systems for fuel caps, certain makes and models are notorious for premature hinge failures.
These failures typically occur due to poor design choices, substandard materials, or the fuel cap’s exposure to environmental elements. For car owners, a broken fuel cap hinge often leads to inconvenience at the pump, potential safety hazards from improper fuel cap sealing, and unexpected repair costs.
This article examines eight vehicles across different manufacturers that have demonstrated recurring issues with fuel cap hinges. By understanding these common problem areas, prospective buyers can make more informed decisions, while current owners can anticipate potential issues before they escalate into more serious problems.
From economy sedans to luxury SUVs, fuel cap hinge failures transcend price points and vehicle classifications, highlighting that even the smallest components can significantly impact vehicle reliability.
1. Honda Civic (2006-2011)
The Honda Civic, particularly models manufactured between 2006 and 2011, has gained notoriety among owners for its problematic fuel cap hinge design.
This generation of Civic represented Honda’s attempt to modernize its compact car offering, but the redesigned fuel system unfortunately included a fuel cap assembly that proved susceptible to premature failure.
The primary issue stems from the plastic hinge that connects the fuel cap to the vehicle, which tends to become brittle over time due to constant exposure to temperature fluctuations, fuel vapors, and environmental factors like UV radiation and road debris.
Honda’s design utilized a relatively thin plastic material for the hinge that lacked sufficient reinforcement. The engineering team seemingly prioritized weight reduction and cost-effectiveness over durability for this component.
Owners typically report issues emerging after approximately 4-5 years of regular use, with the problem becoming more prevalent in vehicles operated in regions with extreme temperature variations or high humidity.
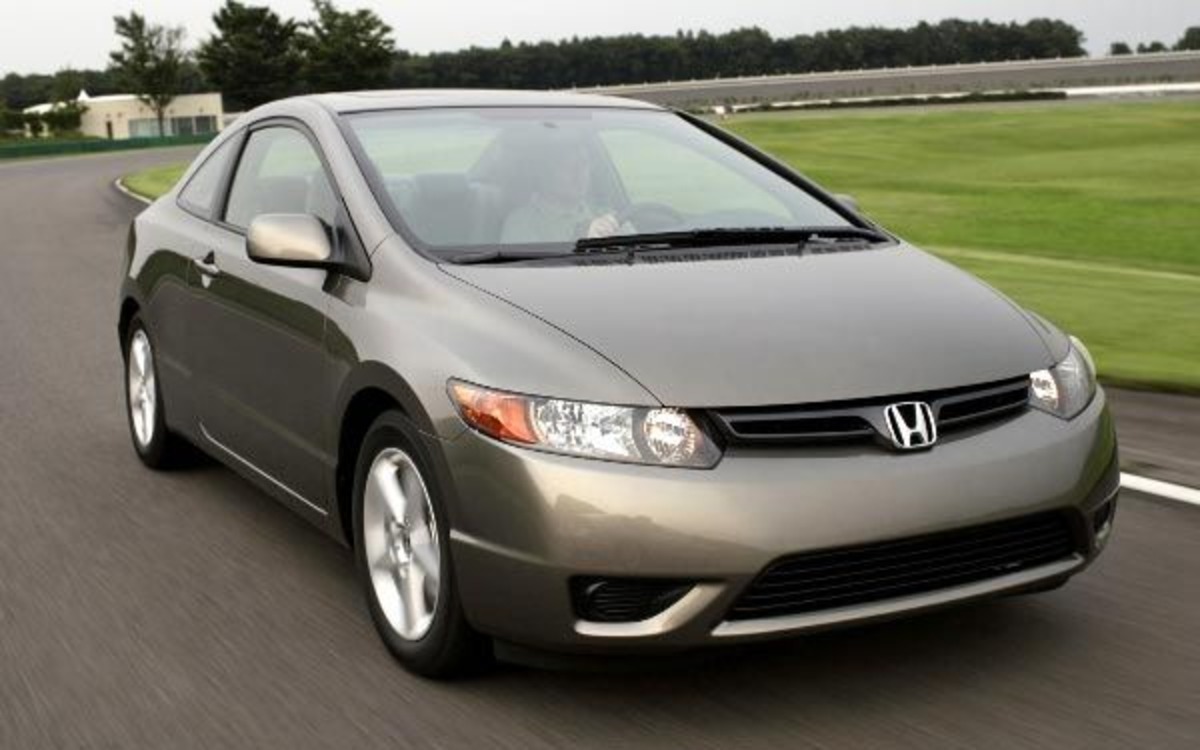
When the hinge begins to fail, owners often notice excessive play in the cap’s movement. This progresses to partial cracks before complete separation occurs. Once broken, the cap either dangles awkwardly from its tether or, in some cases, becomes completely detached.
The most concerning aspect is that a loose or improperly sealed fuel cap triggers the vehicle’s Evaporative Emission Control System (EVAP) warning, illuminating the check engine light.
This not only creates unnecessary concern for owners but also masks potentially more serious engine problems that might go unnoticed. Honda acknowledged these issues in their later designs, implementing a more robust hinge mechanism in subsequent Civic generations.
For owners of affected models, aftermarket solutions have emerged, including reinforced OEM-style replacements and universal caps designed with more durable materials. The repair is relatively straightforward, with replacement caps costing between $15 and-35, though dealer-supplied OEM parts can run significantly higher.
Forum discussions and technical service bulletins reveal that the hinge problem extends beyond mere inconvenience; improper fuel cap sealing has been linked to reduced fuel economy and even fuel vapor leakage in severe cases.
For a vehicle line known for reliability, this recurring issue represents an unusual weak point in Honda’s otherwise stellar engineering reputation. Savvy owners have learned to inspect the cap hinge regularly and replace it preventatively at the first signs of wear, avoiding the cascade of diagnostic issues that can follow a complete failure.
2. Toyota Corolla (2009-2013)
The Toyota Corolla, one of the world’s best-selling automotive nameplates, has maintained a reputation for outstanding reliability throughout its long production history.
However, the tenth-generation Corolla models manufactured between 2009 and 2013 have exhibited a surprising vulnerability in their fuel cap hinge design.
This flaw stands out particularly because it contradicts Toyota’s typically robust engineering principles that have defined the brand for decades. The issue with the Corolla’s fuel cap hinge arises from an apparent cost-cutting measure that utilized a thinner grade of plastic for the hinge mechanism compared to previous generations.
This design compromise manifests after approximately 60,000-80,000 miles of typical usage when the small pivot points within the hinge assembly begin to wear excessively.
The problem is particularly prevalent in regions experiencing significant temperature variations, as the continuous expansion and contraction of the plastic material accelerates fatigue failure in the component.
Toyota’s engineering team designed the fuel filler system with an integrated tether to prevent complete loss of the cap if the hinge fails. However, this precautionary measure ultimately highlighted the frequency of the problem, as numerous owners reported their caps dangling by the tether after hinge failure.
The issue creates multiple inconveniences, from difficulty in properly torquing the cap to maintain a proper seal to the aesthetic unpleasantness of a dangling cap during refueling.
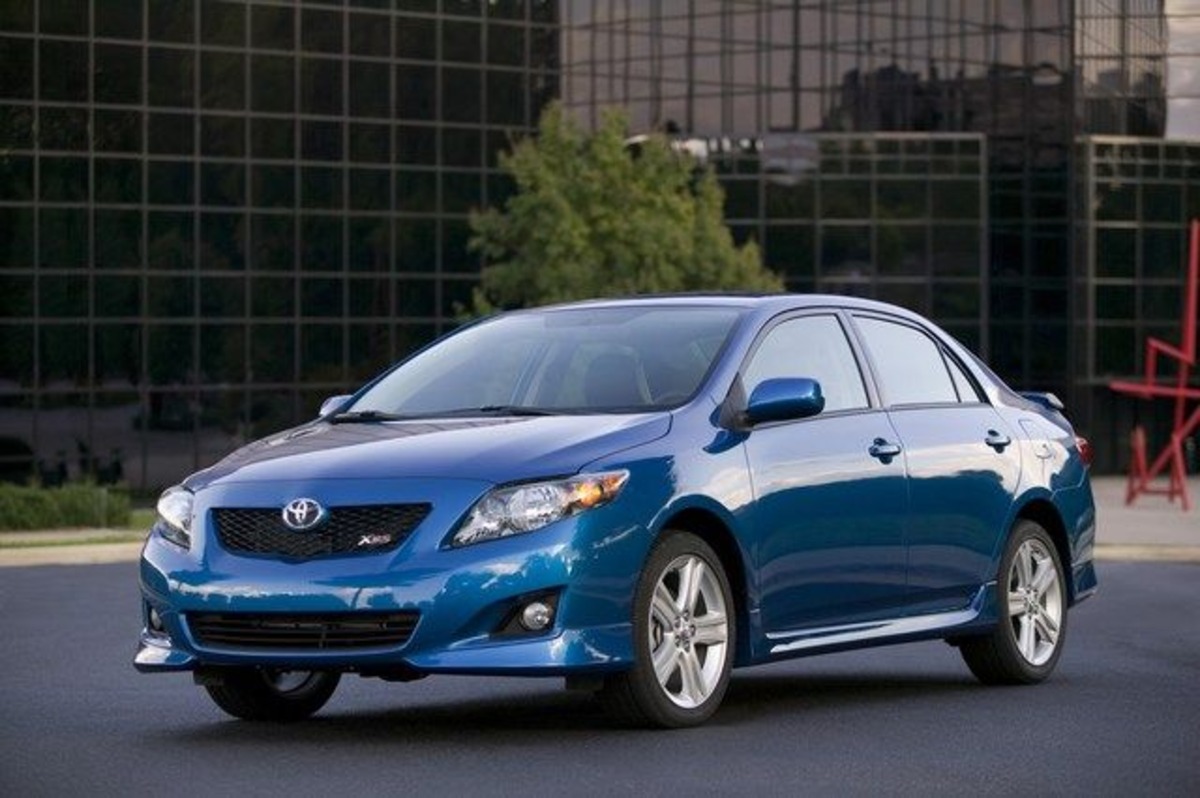
Service records and customer complaints indicate that the problem typically begins with an audible clicking or cracking sound when operating the fuel cap.
This warning sign precedes complete failure, which often occurs suddenly during routine refueling. Owners have reported instances where the check engine light activates following hinge failure due to the cap’s inability to maintain proper pressure within the fuel system, triggering the vehicle’s onboard diagnostic system to flag an EVAP system leak.
Toyota’s response to the issue has been mixed. While never issuing an official recall for the fuel cap hinge specifically, the company introduced a redesigned cap with reinforced hinge points for later production runs of the same generation.
Dealership service departments frequently encounter this problem, with technicians often recommending complete replacement rather than attempting repairs on the fragile original design.
Aftermarket solutions have flourished in response to the widespread nature of this problem, with third-party manufacturers producing strengthened replacement caps featuring metal-reinforced hinge components.
These aftermarket options often cost between $20-40, compared to the $50-75 typically charged for OEM replacements. DIY-inclined owners have also developed temporary fixes involving reinforcement with epoxy or small metal braces, though these solutions generally only delay inevitable replacement.
The Toyota Corolla’s fuel cap hinge problem serves as a reminder that even the most reliable vehicle platforms can harbor specific component vulnerabilities.
For prospective buyers of used Corollas from this generation, inspecting the fuel cap hinge integrity should be part of any pre-purchase evaluation, as replacement, while not excessively expensive, represents an unexpected maintenance item for a vehicle renowned for its low ownership costs.
3. Ford Focus (2012-2018)
The third-generation Ford Focus, produced between 2012 and 2018, represents one of Ford’s most ambitious attempts to create a truly global compact car platform.
While the vehicle received accolades for its engaging driving dynamics and fuel efficiency, it developed a troublesome reputation regarding its fuel cap hinge durability.
This particular issue affects a significant percentage of vehicles in this production run, with problems typically emerging after three to four years of ownership, regardless of mileage accumulation.
The engineering deficiency centers on Ford’s decision to implement a complex multi-part hinge mechanism that prioritized a sleek appearance and operational smoothness over long-term durability.
The hinge assembly consists of small interconnected plastic components that operate around a central pivot point. This intricate design proved vulnerable to the constant stress cycles of opening and closing, particularly in extreme temperature conditions.
The problem becomes exponentially worse in regions with cold winters, as the plastic becomes increasingly brittle when exposed to freezing temperatures, leading to accelerated failure rates.
Customer complaints typically follow a predictable progression: initially, owners notice increased resistance when operating the fuel cap, followed by unusual squeaking or grinding noises from the hinge mechanism.
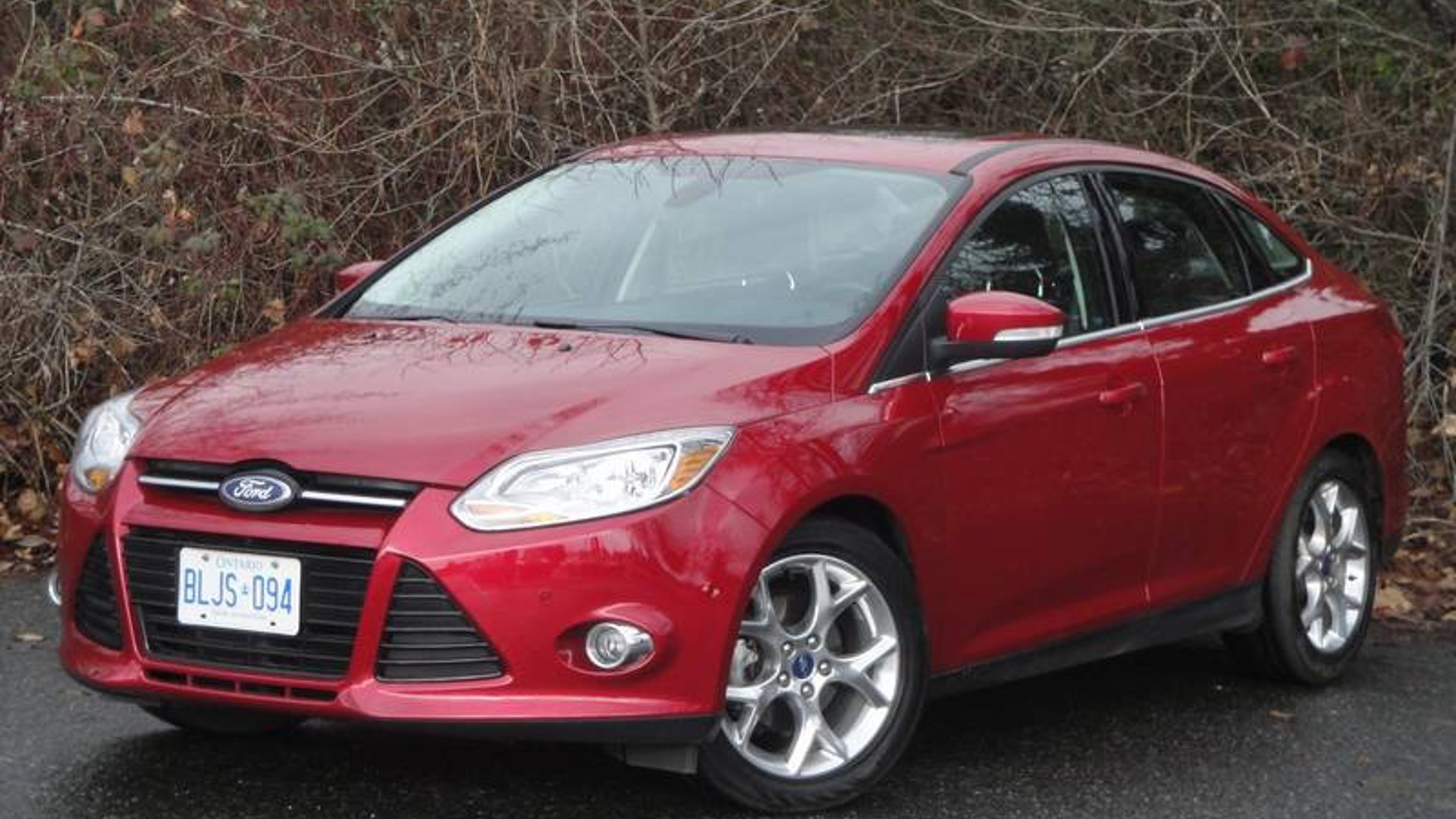
As degradation continues, the hinge develops visible stress fractures before catastrophic failure occurs, typically during a routine refueling stop. The most commonly reported point of failure is the primary pivot pin that serves as the main articulation point for the entire assembly.
Ford’s technical service bulletins acknowledge the issue indirectly, with revised part numbers appearing for replacement fuel caps midway through the production cycle.
Dealership service departments frequently encounter this complaint, with experienced technicians often preemptively recommending replacement of fuel caps showing early signs of hinge deterioration during routine maintenance visits.
The replacement procedure itself is straightforward but requires a precise OEM part to ensure proper function with the Focus’s capless fueling system.
The financial impact on owners varies considerably. While the replacement part itself is relatively inexpensive (approximately $25-45 for OEM quality), the diagnostic process can become costly if the issue progresses to the point where it triggers check engine lights or affects the vehicle’s emissions control systems.
In such cases, owners report spending $100-200 for diagnostic fees before the true cause is identified. This scenario becomes particularly frustrating when dealerships pursue complex EVAP system testing before identifying the simple mechanical failure at the root of the problem.
Online owner communities have extensively documented this issue, with numerous DIY guides emerging to address fuel cap hinge repair. Some resourceful owners have developed reinforcement techniques using small metal brackets or specialized adhesives to strengthen the hinge assembly.
However, most technical experts advise complete replacement as the only reliable long-term solution, as repair attempts typically provide only temporary relief before complete failure occurs.
Ford addressed this design flaw in subsequent model years and during the 2016 mid-cycle refresh of the third-generation Focus, implementing a more robust single-piece hinge design with thicker material at crucial stress points.
This engineering correction substantially reduced failure rates in later production vehicles. For owners of affected models, aftermarket alternatives offering improved durability have emerged, though compatibility issues with the Focus’s fuel door and sealing systems sometimes complicate the selection of non-OEM replacements.
Also Read: You Can Still Buy This 1980s Engine Brand New From the Factory
4. Chevrolet Cruze (2011-2015)
The Chevrolet Cruze, representing General Motors’ critical entry in the competitive compact sedan segment, was marketed as a durable, fuel-efficient alternative to established Japanese competitors when introduced for the 2011 model year.
Despite numerous engineering advances over previous Chevrolet compact offerings, the first-generation Cruze (2011-2015) developed a persistent reputation for fuel cap hinge failures that frustrated owners and dealership service departments alike.
The issue stems from Chevrolet’s implementation of a complex dual-material hinge design that incorporated both rigid and flexible plastic components intended to provide smooth operation while maintaining a secure seal.
This seemingly innovative approach proved problematic in real-world applications as the dissimilar materials expanded and contracted at different rates during temperature cycles.
The constant differential movement between components accelerated wear at contact points, creating play in the hinge mechanism that progressively worsened until failure occurred.
Engineering analysis of failed components reveals a critical design oversight: the metal reinforcement within the hinge assembly was inadequately protected from moisture intrusion.
Over time, exposure to rain, snow, and even normal atmospheric humidity caused oxidation of the metal elements, leading to expansion and eventual cracking of the surrounding plastic components.
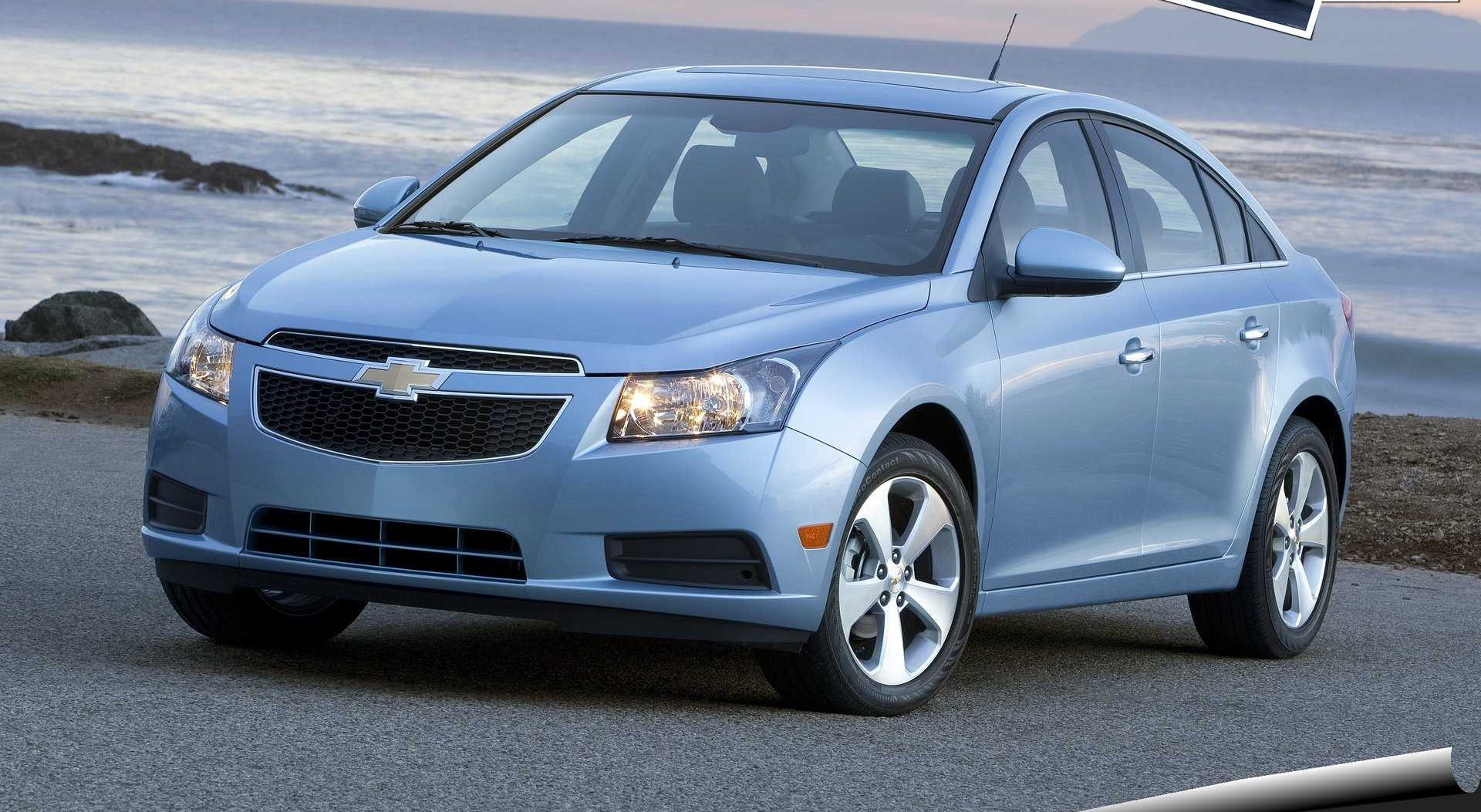
This design vulnerability was particularly pronounced in coastal regions and areas using road salt during winter months, where corrosive elements accelerated the deterioration process.
Customer complaints typically emerge around the 40,000-mile mark, though premature failures have been documented with much lower mileage in vehicles operated in harsh environments.
The progression begins subtly with increased resistance when operating the fuel cap, followed by visible deformation of the hinge components. As deterioration advances, the cap begins to seat improperly, creating an inadequate seal that triggers the vehicle’s onboard diagnostic system.
This often results in a check engine light with corresponding EVAP system fault codes, creating confusion for owners who may not connect these electronic warnings to a simple mechanical failure.
General Motors’ approach to addressing the issue evolved over the production run. Early service bulletins instructed technicians to replace the entire fuel filler assembly, a labor-intensive procedure costing owners $150-200 even under warranty coverage (due to diagnostic fees and related expenses).
By 2013, GM had introduced a redesigned cap with improved hinge materials, available as a standalone replacement part at significantly lower cost.
However, intercompatibility issues between different production runs complicated the replacement process, requiring careful part selection based on vehicle production date.
The financial implications for owners extend beyond the immediate repair costs. The compromised seal resulting from hinge deterioration allows fuel vapor leakage, reducing fuel efficiency by approximately 2-3% according to technical studies.
More concerning, the improper sealing can prevent the vehicle’s evaporative emissions system from performing its self-diagnostic routines properly, potentially masking other system issues and complicating emissions testing procedures required in many states.
Online forums devoted to Cruze ownership contain numerous threads documenting this issue, with ingenious DIY solutions ranging from reinforcement with specialized adhesives to complete adaptation of universal fuel caps.
These community-developed fixes typically provide temporary relief but often compromise the vehicle’s emissions compliance, creating potential regulatory issues during inspections.
The consensus among professional mechanics recommends OEM replacement using the latest revised parts to ensure proper system function and regulatory compliance.
GM addressed this design deficiency comprehensively in the second-generation Cruze introduced for 2016, implementing a simplified single-material hinge with improved environmental protection. This engineering correction eliminated a persistent source of customer dissatisfaction with an otherwise competent compact sedan offering.
5. Volkswagen Jetta (2005-2010)
The fifth-generation Volkswagen Jetta, produced between 2005 and 2010, represented VW’s ambitious attempt to capture greater market share in the competitive North American compact sedan segment.
While the vehicle gained praise for its European driving dynamics and solid construction, it developed a surprisingly consistent problem with fuel cap hinge durability that contradicted the German automaker’s reputation for precision engineering.
This issue affected a substantial percentage of vehicles across all trim levels and engine options within this production run. Volkswagen’s design approach for the fuel cap utilized a sophisticated dual-axis hinge mechanism intended to provide smooth operation and precise alignment with the fuel filler neck.
This complex assembly incorporated multiple small plastic components operating in conjunction with metal spring elements to maintain proper tension throughout the cap’s range of motion.
The engineering concept appeared sound on paper, but real-world implementation revealed significant flaws in material selection and environmental protection.
The primary failure point typically occurs at the junction where the plastic hinge components meet the metal spring assembly. In this area, the continuous mechanical stress of normal operation combines with environmental exposure to accelerate material fatigue.
The problem becomes particularly acute in vehicles operated in regions with significant temperature variations or high humidity levels, as these conditions exacerbate the differential expansion rates between the dissimilar materials used in the assembly.

A distinguishing characteristic of the Jetta’s fuel cap hinge failure is the abruptness with which complete breakdown occurs. Unlike some vehicles where gradual deterioration provides warning signs, Jetta owners frequently report normal operation followed by sudden, complete hinge separation during routine refueling.
This catastrophic failure mode creates particular frustration as it often leaves owners stranded at fuel stations attempting to jury-rig temporary solutions to secure their fuel caps.
Volkswagen’s response to the issue evolved throughout the production cycle. Early dealership service guidance suggested complete replacement of the fuel filler door assembly, a labor-intensive procedure requiring partial disassembly of the rear quarter panel.
This approach proved unnecessarily complex and expensive, with costs ranging from $250-400 depending on labor rates. By 2008, VW had introduced a standalone replacement cap with a revised hinge design available at significantly lower cost, though compatibility issues with earlier production vehicles sometimes complicated the replacement process.
Technical service bulletins issued to dealerships acknowledged the problem indirectly, referencing “improved durability” in replacement components without explicitly identifying the failure mode.
This somewhat guarded approach left many owners frustrated when seeking warranty coverage for what was a design deficiency rather than normal wear and tear.
The issue became particularly contentious when hinge failures triggered check engine lights relating to the EVAP system, as some dealerships initially pursued complex emissions diagnostics before identifying the simple mechanical failure at the root of the problem.
Online Volkswagen owner communities have extensively documented this issue, with numerous DIY guides emerging to address fuel cap hinge repair. Resourceful owners developed reinforcement techniques using epoxy compounds or small metal brackets to strengthen vulnerable areas of the assembly.
However, engineering analysis suggests these solutions typically provide only temporary relief due to the fundamental material incompatibilities in the original design. Most technical experts recommend complete replacement with revised OEM components as the only reliable long-term solution.
Volkswagen addressed this design flaw comprehensively in the sixth-generation Jetta introduced for the 2011 model year, implementing a simplified hinge design with improved material selection and environmental protection.
This engineering correction eliminated what had become a persistent source of customer dissatisfaction with an otherwise well-regarded vehicle platform.
6. Nissan Altima (2007-2012)
The fourth-generation Nissan Altima, produced between 2007 and 2012, established itself as a formidable competitor in the mid-size sedan market, earning praise for its distinctive styling, powerful engine options, and value proposition.
However, amid its commercial success, a persistent issue with the fuel cap hinge mechanism emerged as a commonly reported reliability concern among owners.
This problem affects a significant percentage of vehicles across all trim levels, typically manifesting after three to five years of ownership, regardless of mileage accumulation.
Nissan’s approach to the fuel cap design prioritized a sleek, integrated appearance that aligned with the vehicle’s aesthetic direction. The engineering team implemented a sophisticated multi-component hinge system utilizing a combination of rigid and flexible plastic materials intended to provide smooth operation while maintaining proper alignment with the fuel filler neck.
The assembly incorporated small metal pins at critical pivot points, surrounded by plastic bushings designed to reduce friction and ensure consistent operation throughout the vehicle’s lifecycle.
The fundamental flaw in this design emerged from an apparent miscalculation regarding the environmental stresses the assembly would encounter during normal use.
The junction points between the metal pins and surrounding plastic components prove particularly vulnerable to deterioration when exposed to the temperature extremes experienced in the fuel filler area.
The problem is exacerbated by the location of the Altima’s fuel door on the driver’s side of the vehicle, where in many regions it receives maximum sun exposure while parked, accelerating the material degradation through UV exposure and heat cycling.
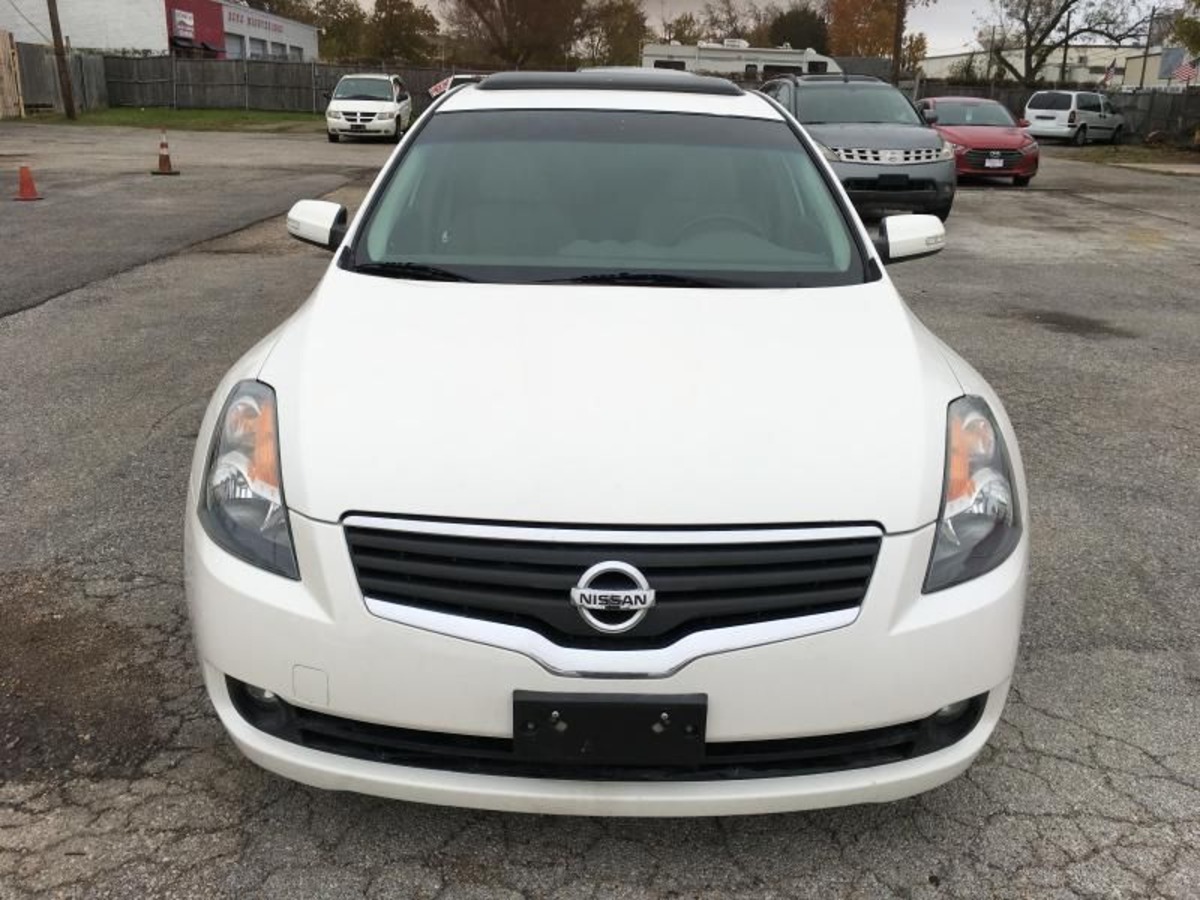
Customer complaints typically follow a predictable pattern: initial symptoms include increased resistance when operating the cap, followed by audible creaking or cracking noises emanating from the hinge assembly.
As deterioration progresses, visible stress fractures appear in the plastic components before catastrophic failure occurs, usually during a routine refueling stop.
The most common failure mode involves the separation of the primary pivot point, rendering the cap incapable of maintaining proper alignment with the filler neck.
Nissan’s technical response to the issue evolved throughout the production cycle. Early service recommendations involved replacement of the entire fuel filler assembly, a labor-intensive procedure costing $175-250, depending on regional labor rates.
By mid-production, Nissan had introduced a revised standalone cap with reinforced hinge components, available at substantially lower cost but requiring careful part selection to ensure compatibility with specific vehicle production dates.
The problem extends beyond mere inconvenience, as improper fuel cap sealing can trigger the vehicle’s onboard diagnostic system to flag potential evaporative emissions system leaks.
This commonly results in illumination of the check engine light with corresponding EVAP system fault codes. Technical studies indicate that even minor misalignment of the cap due to partial hinge deterioration can allow sufficient vapor leakage to trigger these warnings, creating confusion for owners who may not associate electronic diagnostic codes with a simple mechanical failure.
Online owner communities have extensively documented this issue, with numerous DIY repair approaches emerging to address the problem. These range from reinforcement of weakened components with specialized adhesives to complete adaptation of universal fuel caps.
While these community-developed solutions often provide temporary relief, they frequently compromise the precise sealing characteristics required by the vehicle’s evaporative emissions control system, potentially creating compliance issues during emissions testing.
Nissan addressed this design deficiency comprehensively in the fifth-generation Altima introduced for the 2013 model year, implementing a significantly simplified hinge design with improved material selection and additional UV protection additives in the plastic components.
This engineering correction eliminated what had become a persistent source of customer dissatisfaction with an otherwise competitive mid-size sedan offering.
7. Hyundai Sonata (2010-2014)
The sixth-generation Hyundai Sonata, manufactured between 2010 and 2014, represented Hyundai’s ambitious leap into premium territory within the mid-size sedan segment.
With its “Fluidic Sculpture” design language and impressive feature set, the Sonata gained significant market traction and critical acclaim. However, amid its many engineering achievements, a persistent vulnerability in the fuel cap hinge design emerged as a common point of failure, affecting a substantial number of vehicles across the production run.
Hyundai’s approach to the fuel cap assembly emphasized aesthetic integration with the vehicle’s flowing design language. The engineering team implemented a sophisticated hinge mechanism featuring multiple articulation points to ensure smooth operation and proper alignment with the fuel filler neck.
This complex assembly utilized a combination of injection-molded plastic components with small metal reinforcements at critical stress points. While visually impressive and initially smooth in operation, this design choice prioritized form over long-term function.
The primary vulnerability in the system stems from the junction between the plastic body of the cap and the hinge assembly. At this critical interface, material thickness was reduced to maintain the cap’s sleek profile, creating a stress concentration point particularly susceptible to fatigue failure.
Engineering analysis of failed components reveals microscopic stress fractures developing along this junction after approximately 40,000-60,000 miles of normal use, progressively weakening the structure until catastrophic failure occurs.
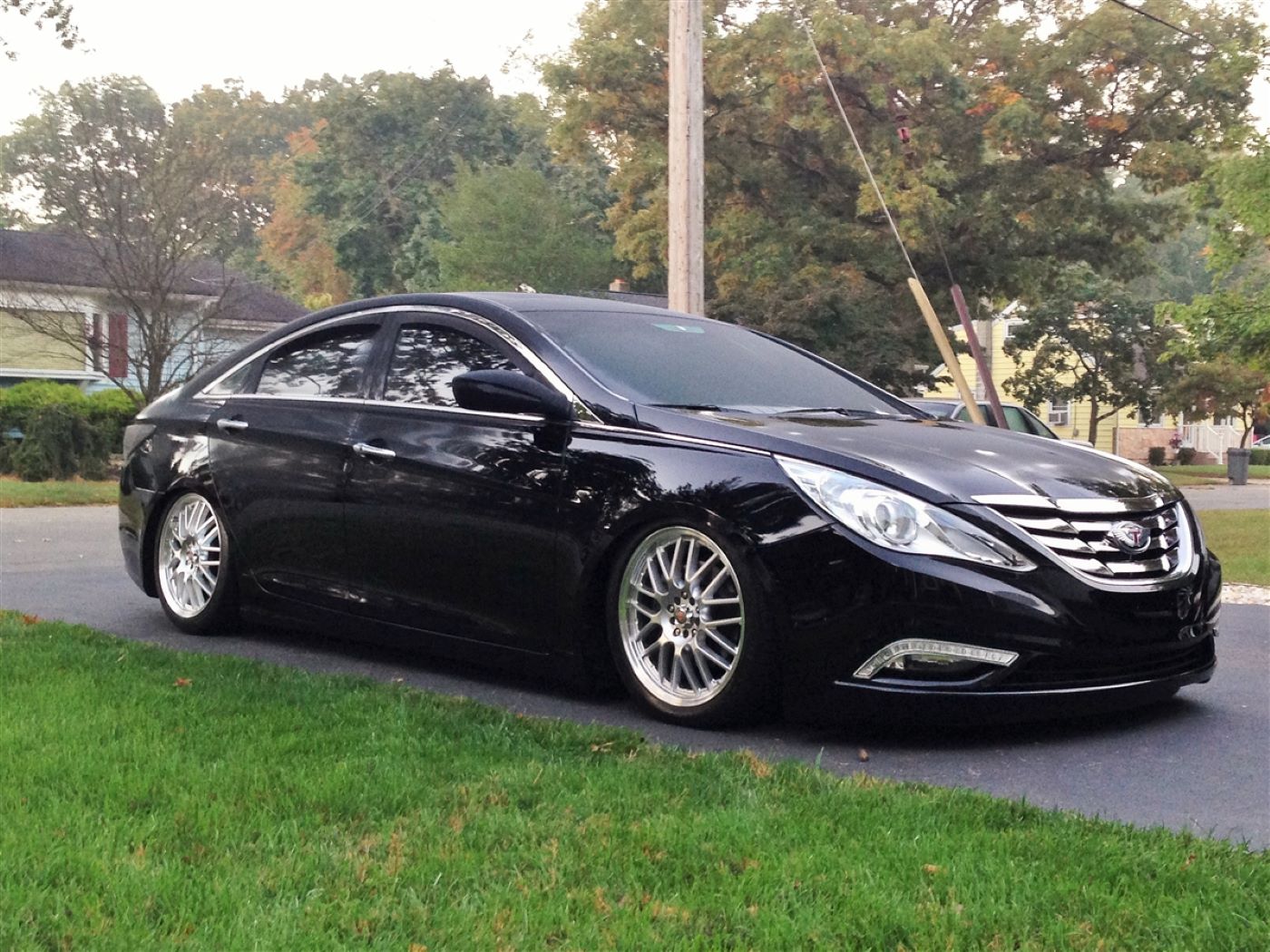
The problem manifests most severely in regions experiencing significant temperature variations or high UV exposure. The constant expansion and contraction of the plastic material during temperature cycles accelerates the formation of micro-fractures, while prolonged UV exposure contributes to material embrittlement that reduces impact resistance.
This environmental vulnerability explains the higher failure rates reported in southern and southwestern states compared to more temperate regions. Customer complaints typically begin with subtle symptoms increased resistance when operating the cap, followed by unusual sounds from the hinge mechanism during operation.
As deterioration advances, visible deformation becomes apparent at the connection points before complete separation occurs. The most problematic aspect of this failure is its tendency to happen suddenly during refueling, leaving owners without an effective means to secure the fuel system until replacement parts can be obtained.
Hyundai’s response to the issue evolved throughout the production cycle. Initial service recommendations involved the replacement of the entire fuel filler assembly, an unnecessarily complex and expensive procedure.
By 2012, Hyundai had introduced a revised standalone cap with reinforced connection points, available at substantially lower cost. Technical service bulletins issued to dealerships acknowledged the issue indirectly, referencing “improved durability” in replacement components without explicitly identifying the design deficiency.
The financial implications for owners extend beyond the immediate repair costs. The compromised seal resulting from hinge deterioration often triggers check engine lights related to the evaporative emissions control system, leading to failed emissions tests in states with inspection requirements.
This secondary effect creates additional expenses as some owners unnecessarily pursue complex diagnostic procedures before identifying the simple mechanical failure causing their emissions compliance issues.
Online owner communities have documented this issue extensively, with numerous DIY reinforcement techniques emerging to address early-stage deterioration before complete failure occurs.
These approaches typically involve applying specialized adhesives to strengthen vulnerable areas or installing small metal braces across known stress points. While sometimes effective as preventative measures, these community-developed solutions rarely restore full functionality once significant deterioration has occurred.
Hyundai addressed this design flaw comprehensively in the seventh-generation Sonata introduced for the 2015 model year, implementing a significantly simplified hinge design with improved material selection and more generous dimensioning at critical stress points.
This engineering correction eliminated what had become a persistent source of customer dissatisfaction with an otherwise impressive vehicle platform.
8. BMW 3 Series (2006-2011)
The fifth-generation BMW 3 Series (E90/E91/E92/E93), produced between 2006 and 2011, upheld the model’s legendary status as the benchmark sports sedan while introducing innovative technologies and refined luxury features.
Despite its engineering excellence across most systems, this generation developed a surprisingly consistent issue with fuel cap hinge durability that contradicted BMW’s reputation for meticulous design and premium materials.
This problem affected vehicles across the model range, though it appeared with higher frequency in convertible and coupe variants. BMW’s approach to the fuel cap design reflected the company’s philosophy of sophisticated engineering and premium presentation.
The cap assembly featured a complex multi-component hinge system manufactured primarily from high-grade thermoplastics with selective metal reinforcement at presumed stress points.
The design incorporated a dual-pivot mechanism intended to provide precise movement and proper alignment throughout the cap’s operational range. This sophisticated approach initially delivered the smooth, substantial feel expected from a premium vehicle, but longevity issues emerged as vehicles accumulated age and mileage.
The fundamental engineering oversight appears to center on insufficient accommodation for the thermal expansion differential between the metal and plastic components within the hinge assembly.
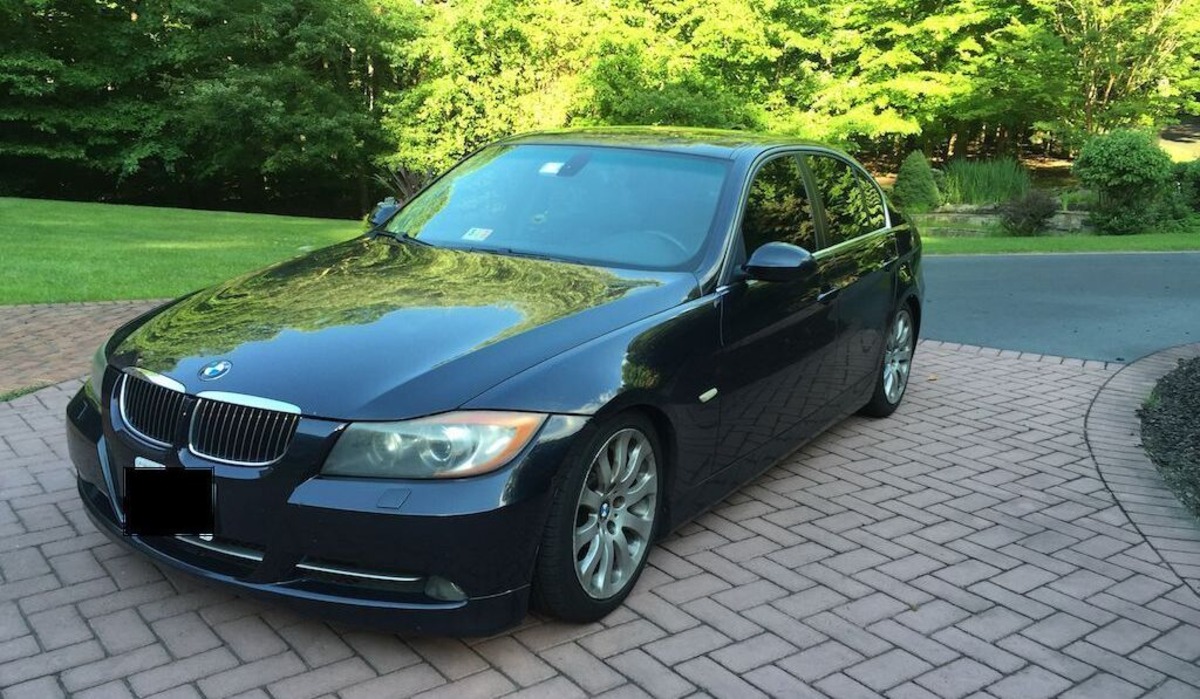
Under the extreme temperature variations experienced in the fuel filler area, these materials expand and contract at substantially different rates, creating internal stresses that progressively weaken the structure.
Technical analysis reveals material fatigue initiating at the interface between metal reinforcement elements and surrounding plastic components, typically becoming critical after approximately 6-7 years, regardless of mileage accumulation.
A distinguishing characteristic of the 3 Series fuel cap hinge failure is its accelerated progression in vehicles operated in regions with significant seasonal temperature variations.
Customer data indicates substantially higher failure rates in the northern United States and Canada compared to more temperate regions, suggesting that repeated freeze-thaw cycles play a significant role in accelerating material degradation.
The problem also demonstrates a correlation with usage patterns, with vehicles driven primarily for short trips showing higher failure rates due to the increased frequency of fuel cap operation relative to mileage accumulation.
The failure typically progresses through identifiable stages: initial symptoms include subtle resistance when operating the cap, followed by visible deformation of the plastic components around metal insertion points.
As deterioration advances, the cap begins to misalign with the filler neck when closed, creating potential for improper sealing. The final stage involves complete separation of the hinge components, rendering the cap unusable or dependent on its tethering system to prevent loss.
BMW’s response to the issue evolved from initial denial to eventual acknowledgment through revised parts. Early dealer service guidance suggested complete replacement of the fuel filler assembly, a labor-intensive procedure with costs ranging from $300-450, depending on model variant and regional labor rates.
By late 2009, BMW had introduced a redesigned cap with improved material formulation and modified reinforcement structure, available as a standalone replacement at substantially lower cost, though still premium-priced at $85-120 compared to mass-market equivalents.
The financial implications for owners extend beyond the immediate repair expenses. The precise engineering of BMW’s fuel and evaporative emissions systems means that even slight misalignment of the cap due to partial hinge deterioration can trigger diagnostic trouble codes related to system integrity.
This often leads to illumination of warning lights and potential complications during emissions testing, creating additional service visits and expenses before the root cause is correctly identified.
Online BMW enthusiast communities have extensively documented this issue, with numerous DIY approaches emerging to address early-stage deterioration.
These range from reinforcement with specialized aerospace-grade adhesives to fabrication of custom metal bracing for vulnerable areas. While sometimes effective as preventative measures, these community-developed solutions rarely restore the premium feel and precise function expected from an undamaged original component.
BMW addressed this design deficiency comprehensively in the sixth-generation 3 Series introduced for the 2012 model year, implementing a significantly redesigned fuel cap with simplified mechanics and improved material selection.
This engineering correction eliminated what had become an unexpected quality concern in an otherwise exceptional vehicle platform.
8. Mazda CX-7 (2007-2012)
The Mazda CX-7, produced between 2007 and 2012, represented Mazda’s distinctive entry into the increasingly popular crossover SUV segment.
Embodying the brand’s “Zoom-Zoom” philosophy with sporty handling and turbocharged performance options, the CX-7 carved out a niche among driving enthusiasts seeking utility without sacrificing driving dynamics.
However, amid its many engaging qualities, a persistent issue with fuel cap hinge durability emerged as a common point of failure across the model’s production run, affecting a significant percentage of vehicles regardless of trim level or drivetrain configuration.
Mazda’s engineering approach for the fuel cap reflected the vehicle’s sporting pretensions, with a design that prioritized tight integration with the vehicle’s flowing bodywork and precise operational feel.
The hinge mechanism featured a sophisticated three-point articulation system using injection-molded composite materials with selective reinforcement at presumed stress points.
This complex design delivered impressive initial quality impressions but harbored fundamental vulnerabilities that emerged as vehicles accumulated age and environmental exposure.
The primary engineering deficiency centers on the junction between the main cap body and the articulating hinge components. At this critical interface, material thickness was compromised to maintain the cap’s streamlined appearance, creating a stress concentration point particularly susceptible to fatigue failure.
Technical analysis of failed components reveals characteristic stress patterns indicating that normal operational forces gradually exceed the material’s endurance limit after multiple years of service, leading to progressive weakening and eventual failure.
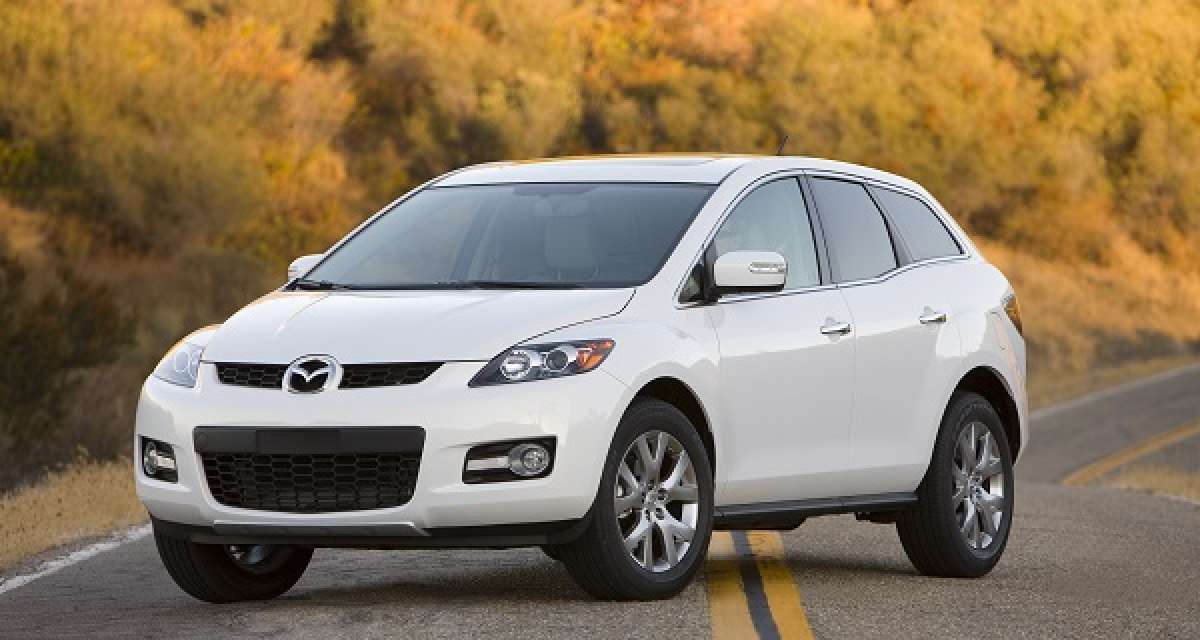
A distinguishing characteristic of the CX-7’s fuel cap failure mode is its correlation with climate conditions. Owner-reported data shows substantially higher failure rates in regions experiencing extreme temperature variations or raised UV exposure levels.
This environmental vulnerability suggests that material choices optimized for manufacturing efficiency and initial appearance may have inadequately accounted for long-term environmental degradation factors.
The problem appears particularly acute in the southwestern United States, where intense solar radiation accelerates the plastic degradation process.
Customer complaints typically follow a predictable progression: initial symptoms include increased resistance when operating the cap, often accompanied by audible creaking or clicking sounds from the hinge area.
As deterioration advances, visible deformation becomes apparent at stress concentration points before complete separation occurs, typically during a routine refueling stop.
This sudden failure mode creates particular frustration as it leaves owners without an effective means to secure their fuel system until replacement parts can be obtained.
Mazda’s official response to the issue evolved throughout the production cycle. Early service recommendations directed technicians toward the replacement of the entire fuel filler assembly, an unnecessarily complex and expensive procedure costing $200-350, depending on regional labor rates.
By mid-production, Mazda had introduced a revised standalone cap with reinforced connection points, available at substantially lower cost but requiring careful part selection to ensure compatibility with specific vehicle variants.
The problem extends beyond mere inconvenience, as compromised cap integrity often triggers the vehicle’s onboard diagnostic system to detect potential evaporative emissions system leaks.
This commonly results in illumination of the check engine light with corresponding EVAP system fault codes. Technical studies indicate that even minor misalignment of the cap due to partial hinge deterioration can create sufficient vapor leakage to trigger these warnings, creating confusion for owners who may not associate electronic fault codes with a simple mechanical failure.
Online owner communities have documented this issue extensively, with numerous DIY reinforcement techniques emerging to address early-stage deterioration.
These approaches typically involve applying specialized structural adhesives to strengthen vulnerable areas or installing small reinforcement brackets across known stress points.
While sometimes effective as preventative measures, these community-developed solutions rarely restore full functionality once significant deterioration has occurred.
When Mazda discontinued the CX-7 after the 2012 model year, replacing it with the more mainstream CX-5, the company implemented significant design improvements to the fuel system components.
The redesigned fuel cap featured in subsequent Mazda crossover models incorporated simplified mechanics, more generous material thickness at critical stress points, and improved environmental protection additives in the plastic formulation.
These engineering corrections eliminated what had become a persistent quality concern on an otherwise engaging vehicle platform that prioritized driving enjoyment in the crossover segment.
Also Read: Why Mechanics in Remote Villages Prefer These Specific Engines