In the automotive world, raw horsepower numbers often steal the spotlight, but torque-to-weight ratio remains one of the most telling metrics of a car’s real-world performance character.
While horsepower determines top speed potential, torque-to-weight ratio dictates how explosively a vehicle accelerates from rest, how effortlessly it climbs hills, and how responsive it feels during everyday driving scenarios.
This fundamental relationship between rotational force and mass separation defines the difference between cars that feel genuinely quick and those that merely look fast on paper.
Torque, measured in pound-feet or Newton-meters, represents the twisting force an engine generates, while the torque-to-weight ratio divides this figure by the vehicle’s mass.
A higher ratio typically translates to better acceleration, more responsive throttle behavior, and an overall more engaging driving experience. Modern automotive engineering has produced some remarkable extremes in this metric, from hyperelectric vehicles delivering instantaneous torque through multiple motors to traditional supercars achieving incredible ratios through lightweight construction and high-output engines.
Conversely, some vehicles struggle with underwhelming torque-to-weight ratios, often resulting from conservative engine tuning, heavy construction, or prioritizing other attributes like fuel economy over performance.
These underpowered vehicles, while serving their intended purposes, demonstrate how challenging it can be to achieve satisfying performance across all automotive segments. Understanding these extremes helps illustrate the critical role torque to weight ratio plays in defining a vehicle’s character and capabilities.
5 Cars with Exceptional Torque-to-Weight Ratios
These performance-focused vehicles deliver outstanding torque-to-weight ratios that translate into explosive acceleration and impressive pulling power across the entire rev range.
While the standard Tesla Model S had more than enough torque, the Plaid gets no less than 1,050 lb-ft (1,420 Nm), which made it the quickest accelerating production car in history when it went on sale three years ago.
High-performance sports cars and supercars achieve their exceptional ratios through lightweight construction materials like carbon fiber and aluminum, combined with powerful turbocharged or supercharged engines that produce massive torque figures.
Electric vehicles particularly excel in this category due to their instant torque delivery characteristics, with some models producing over 1,000 lb-ft of torque while maintaining relatively modest curb weights.
These vehicles demonstrate their superior torque-to-weight ratios through sub-4-second 0-60 mph times and quarter-mile performances that leave conventional vehicles far behind.
The combination of advanced materials engineering and sophisticated powertrains creates driving experiences where acceleration feels effortless and immediate across all speed ranges.
1. Rimac Nevera – The Electric Torque Monster
The Rimac Nevera represents the absolute pinnacle of torque-to-weight engineering, delivering an astronomical 1,741 pound-feet of torque while weighing approximately 5,070 pounds.
This yields an extraordinary torque-to-weight ratio of 343 lb-ft per ton, making it one of the most torque-dense production vehicles ever created.
The Croatian hypercar achieves this through four independent electric motors, each precisely controlling one wheel with instantaneous torque delivery that internal combustion engines simply cannot match.
What makes the Nevera’s torque delivery truly remarkable is its consistency across the entire rev range. Unlike traditional engines that produce peak torque within specific RPM bands, electric motors generate maximum torque from zero RPM, providing relentless acceleration that feels almost supernatural.
The car’s 120kWh battery pack, while contributing significantly to its weight, enables this torque monster to accelerate from 0-60 mph in just 1.85 seconds, demonstrating how effectively the Nevera translates its torque advantage into real-world performance.
The engineering complexity behind this achievement involves sophisticated torque vectoring systems that can independently modulate power to each wheel thousands of times per second.
This capability allows the Nevera to maintain traction and stability despite its enormous torque output, something that would be impossible with a conventional drivetrain.
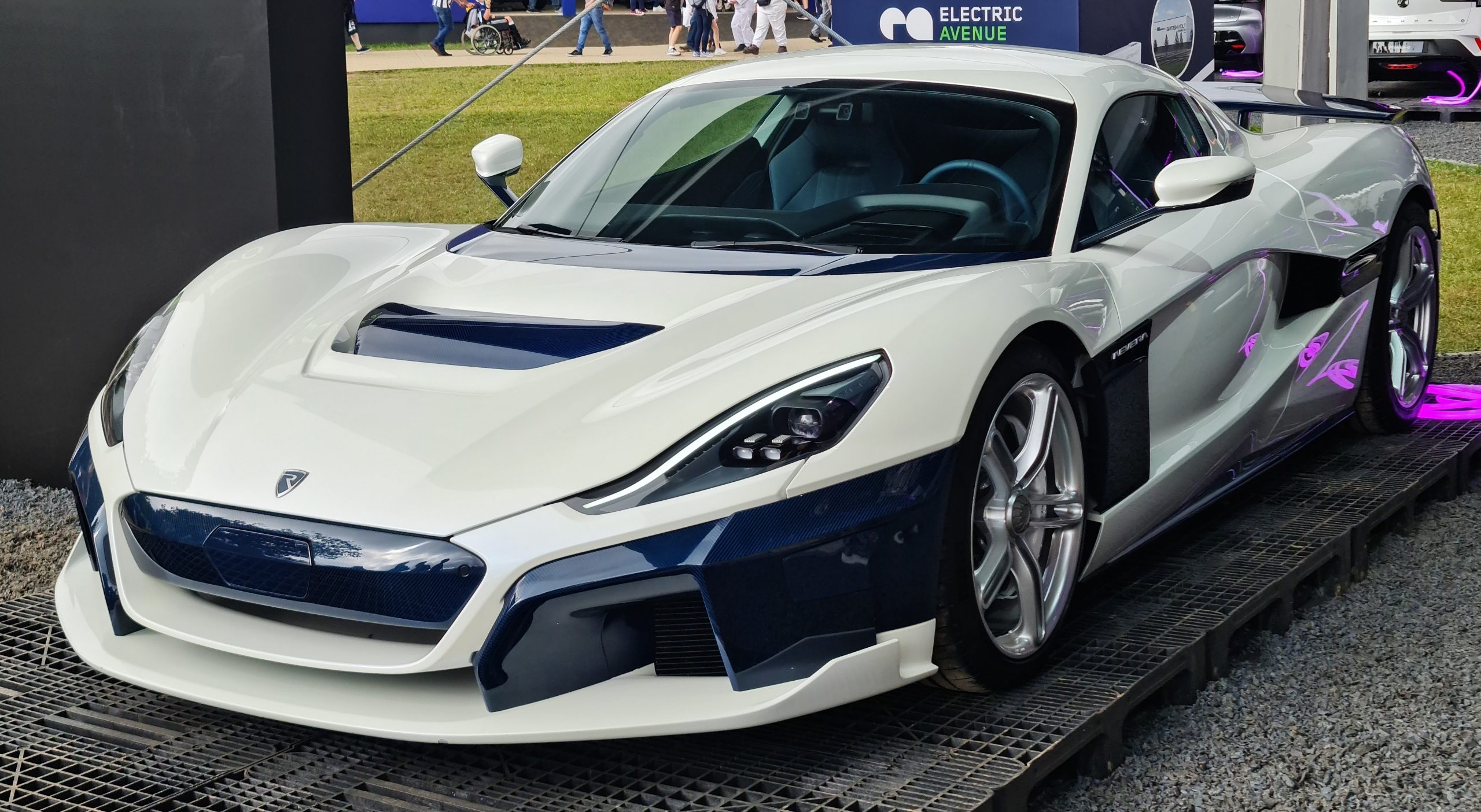
The carbon fiber monocoque construction helps offset some of the battery weight, though the Nevera still weighs considerably more than most supercars. Beyond straight-line acceleration, the Nevera’s torque-to-weight advantage manifests in incredible mid-range responsiveness.
Whether exiting corners on a racetrack or overtaking on public roads, the instantaneous torque delivery provides a level of performance that redefines expectations.
The car’s four-motor setup also enables innovative features like “drift mode,” where torque distribution can be precisely controlled to initiate and maintain controlled slides.
The thermal management required to sustain this torque output represents another engineering marvel. Each motor requires sophisticated cooling systems to prevent overheating during extended high-performance driving, while the battery pack features its advanced thermal management to maintain optimal operating temperatures.
This complexity adds weight but ensures the Nevera can deliver its full torque potential consistently, unlike some high-performance vehicles that suffer from heat-related power reduction.
Despite its extraordinary capabilities, the Nevera’s torque-to-weight ratio comes with challenges. The instantaneous torque delivery requires extremely sophisticated traction control systems and places enormous stress on tires, brakes, and suspension components.
The car’s weight distribution, influenced by the large battery pack, also affects handling characteristics compared to lighter, more traditionally proportioned supercars. Nevertheless, the Nevera demonstrates how electric powertrains can achieve torque-to-weight ratios that seemed impossible just a decade ago.
2. McLaren 765LT – Lightweight Engineering Excellence
The McLaren 765LT exemplifies how traditional automotive engineering can achieve exceptional torque-to-weight ratios through meticulous weight reduction and engine optimization.
Producing 590 pound-feet of torque while weighing just 3,060 pounds, the 765LT delivers an impressive torque-to-weight ratio of 386 lb-ft per ton.
This achievement represents the culmination of McLaren’s “Longtail” philosophy, which prioritizes performance through weight reduction and aerodynamic efficiency rather than simply adding more power.
At the heart of the 765LT lies McLaren’s twin-turbocharged 4.0-liter V8 engine, extensively modified from the already potent 720S powerplant. The engine produces its peak torque of 590 lb-ft from 5,500-6,500 RPM, but the real magic happens in how McLaren has optimized the entire powerplant for responsiveness.
Shorter gear ratios, revised turbocharger mapping, and enhanced cooling systems ensure that torque delivery feels immediate and linear throughout the rev range. Weight reduction efforts throughout the 765LT contribute significantly to its exceptional ratio.
Carbon fiber construction extends beyond the obvious body panels to include components like the front and rear anti-roll bars, saving precious pounds while maintaining structural integrity.
The titanium roll cage, carbon fiber seats, and deletion of various comfort features result in a weight saving of approximately 176 pounds compared to the standard 720S, directly improving the torque-to-weight equation.
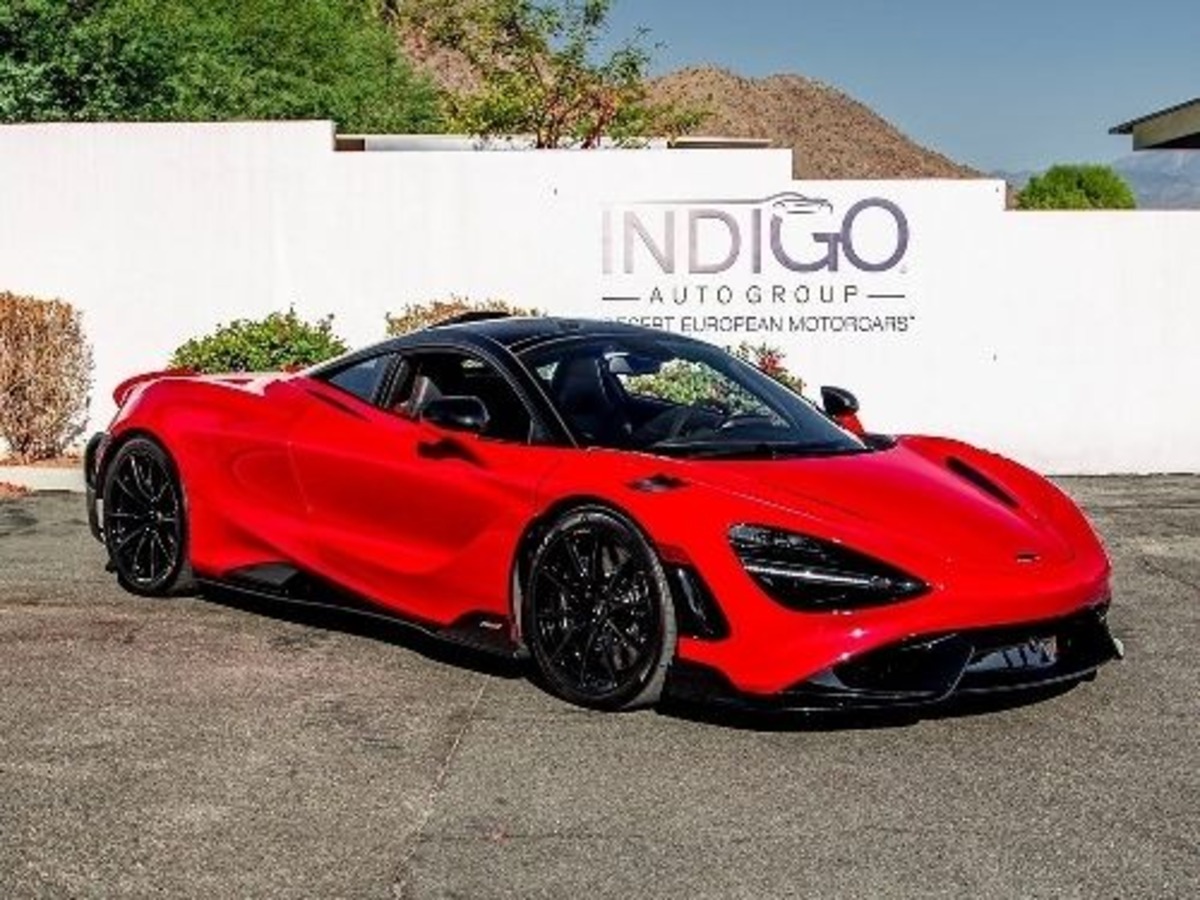
The 765LT’s suspension system showcases how proper engineering can maximize torque deployment. The adaptive dampers and anti-roll bars work in conjunction with McLaren’s Proactive Chassis Control system to ensure optimal tire contact patches under acceleration.
This sophisticated system prevents wheelspin and maintains traction even when the full 590 lb-ft is deployed, allowing the car to achieve its claimed 0-60 mph time of 2.7 seconds consistently.
Aerodynamic enhancements play a crucial role in the 765LT’s ability to utilize its torque effectively. The extended rear wing, revised front splitter, and side-mounted air intakes don’t just provide downforce; they also improve cooling efficiency, allowing the engine to maintain peak torque output during extended high-performance driving.
The active aerodynamics adjust automatically based on driving conditions, optimizing either drag reduction for straight-line acceleration or downforce for cornering stability.
The 765LT’s torque-to-weight advantage becomes particularly apparent during track driving, where the combination of high torque output and low mass creates extraordinary acceleration out of corners.
The car’s ability to put down power efficiently while maintaining balance demonstrates how traditional engineering approaches can still compete with more exotic solutions.
The mechanical limited-slip differential and precise torque delivery characteristics make the 765LT’s power accessible to a broader range of drivers compared to some more powerful but heavier alternatives.
3. Porsche Taycan Turbo GT – Electric Precision Engineering
The Porsche Taycan Turbo GT represents the German manufacturer’s most focused approach to electric performance, achieving an impressive torque-to-weight ratio through careful engineering optimization.
With 774 pound-feet of torque and a curb weight of approximately 5,060 pounds, the Turbo GT delivers a ratio of 306 lb-ft per ton. While not the highest on paper, the Taycan’s sophisticated torque management and delivery systems make it one of the most effective high-torque vehicles ever produced.
Porsche’s two-speed transmission on the rear axle sets the Taycan apart from most electric vehicles, which typically use single-speed reduction gears.
This innovation allows the Turbo GT to optimize torque delivery across different speed ranges, providing explosive acceleration from rest while maintaining efficiency at higher speeds.
The first gear maximizes torque multiplication for launch acceleration, while the second gear enables sustained high-speed performance that many electric vehicles struggle to achieve.
The Taycan’s 800-volt electrical architecture represents another significant advancement in torque delivery efficiency. This high-voltage system reduces electrical losses and enables more precise control of the dual electric motors, allowing for incredibly accurate torque vectoring between the front and rear axles.
The result is traction management that can adapt to changing conditions thousands of times per second, ensuring optimal power deployment regardless of surface conditions or driving demands.
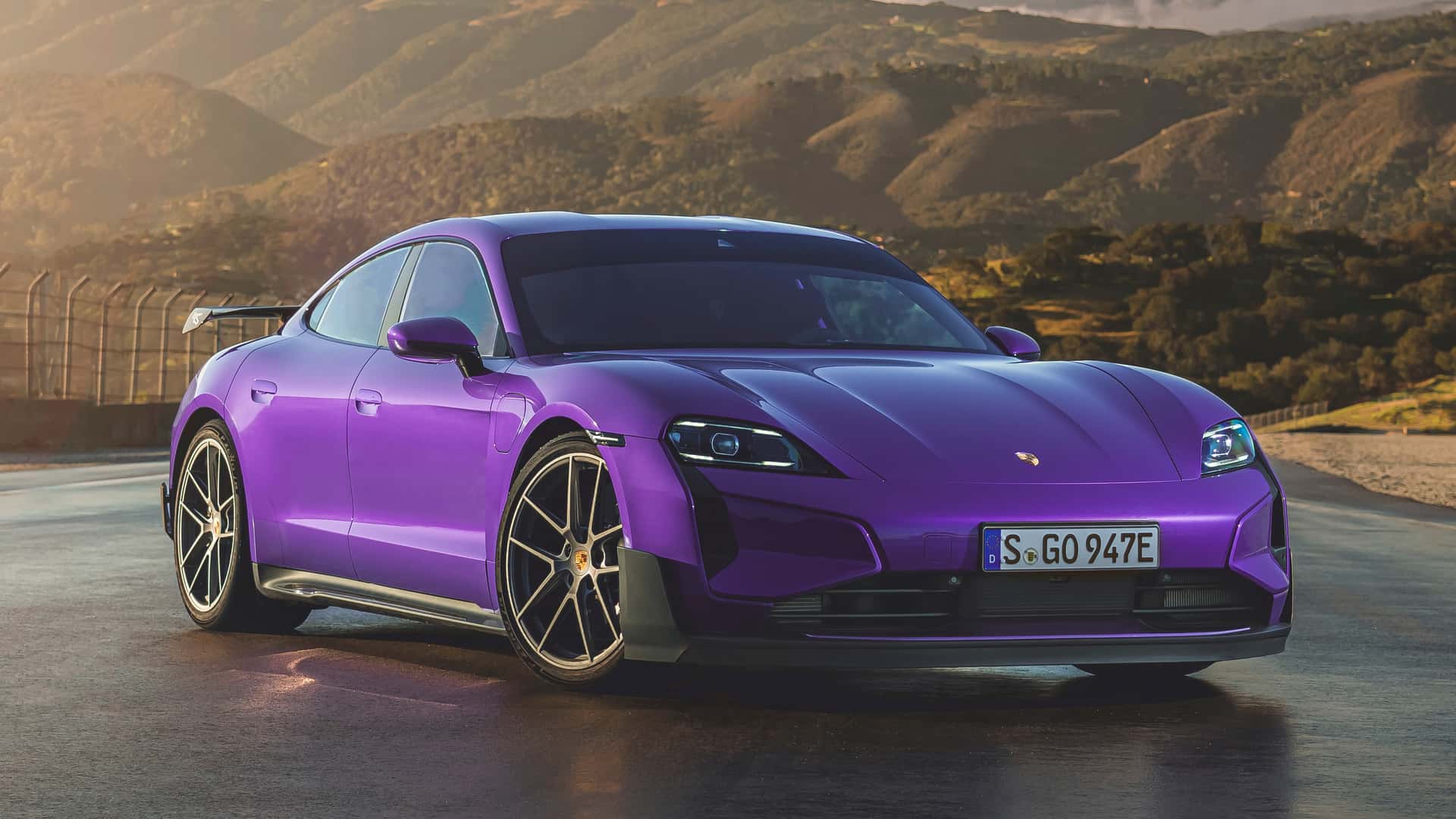
Weight distribution plays a crucial role in the Taycan’s torque utilization effectiveness. The battery pack’s low mounting position creates a center of gravity approximately four inches lower than comparable internal combustion sports sedans, improving stability under acceleration and cornering.
This low center of gravity allows the Taycan to put down its substantial torque more effectively while maintaining predictable handling characteristics that inspire confidence at the limit.
The Taycan Turbo GT’s launch control system demonstrates sophisticated torque management technology. When activated, the system preheats the battery and motors to optimal operating temperatures while adjusting suspension settings and stability systems for maximum acceleration potential.
The result is repeatable 0-60 mph times of just 2.1 seconds, showcasing how properly managed electric torque can deliver consistent performance that rivals or exceeds traditional supercars.
Thermal management systems in the Taycan ensure sustained torque delivery during extended high-performance driving. Multiple cooling circuits serve the battery pack, drive motors, and power electronics, preventing the thermal limiting that affects many high-performance electric vehicles.
This sophisticated cooling allows the Taycan to maintain near-peak torque output during track sessions or spirited driving, something that sets it apart from many electric competitors that suffer from reduced performance as temperatures rise.
The Taycan’s torque-to-weight advantage extends beyond straight-line performance to include remarkable efficiency in energy consumption. The precise torque control systems can modulate power delivery to optimize range while still providing impressive performance when demanded.
This balance between efficiency and performance demonstrates how advanced torque management can serve multiple objectives simultaneously, making high-performance electric vehicles more practical for everyday use.
4. Ferrari SF90 Stradale – Hybrid Power Integration
The Ferrari SF90 Stradale represents the pinnacle of hybrid performance engineering, combining a twin-turbocharged V8 engine with three electric motors to produce a combined torque output of 590 pound-feet while weighing 3,461 pounds.
This configuration yields a torque-to-weight ratio of 341 lb-ft per ton, achieved through one of the most sophisticated powertrains ever installed in a road car.
The SF90’s approach to torque delivery demonstrates how traditional and electric powertrains can be integrated to create performance that exceeds what either technology could achieve independently.
The heart of the SF90’s torque production lies in its 4.0-liter twin-turbocharged V8 engine, which produces 568 pound-feet of torque on its own. However, the real innovation comes from the integration of three electric motors: two mounted on the front axle and one positioned between the engine and eight-speed dual-clutch transmission.
This configuration enables not only all-wheel drive capability but also sophisticated torque vectoring that can independently control power delivery to each wheel.
Electric motor placement in the SF90 creates unique torque delivery characteristics that traditional powertrains cannot match. The rear-mounted electric motor provides instant torque fill during turbo lag, creating seamless power delivery that feels naturally aspirated despite the twin-turbo configuration.
Meanwhile, the front-mounted motors enable precise torque vectoring during cornering, allowing the SF90 to rotate or stabilize as needed through differential torque application between the front wheels.
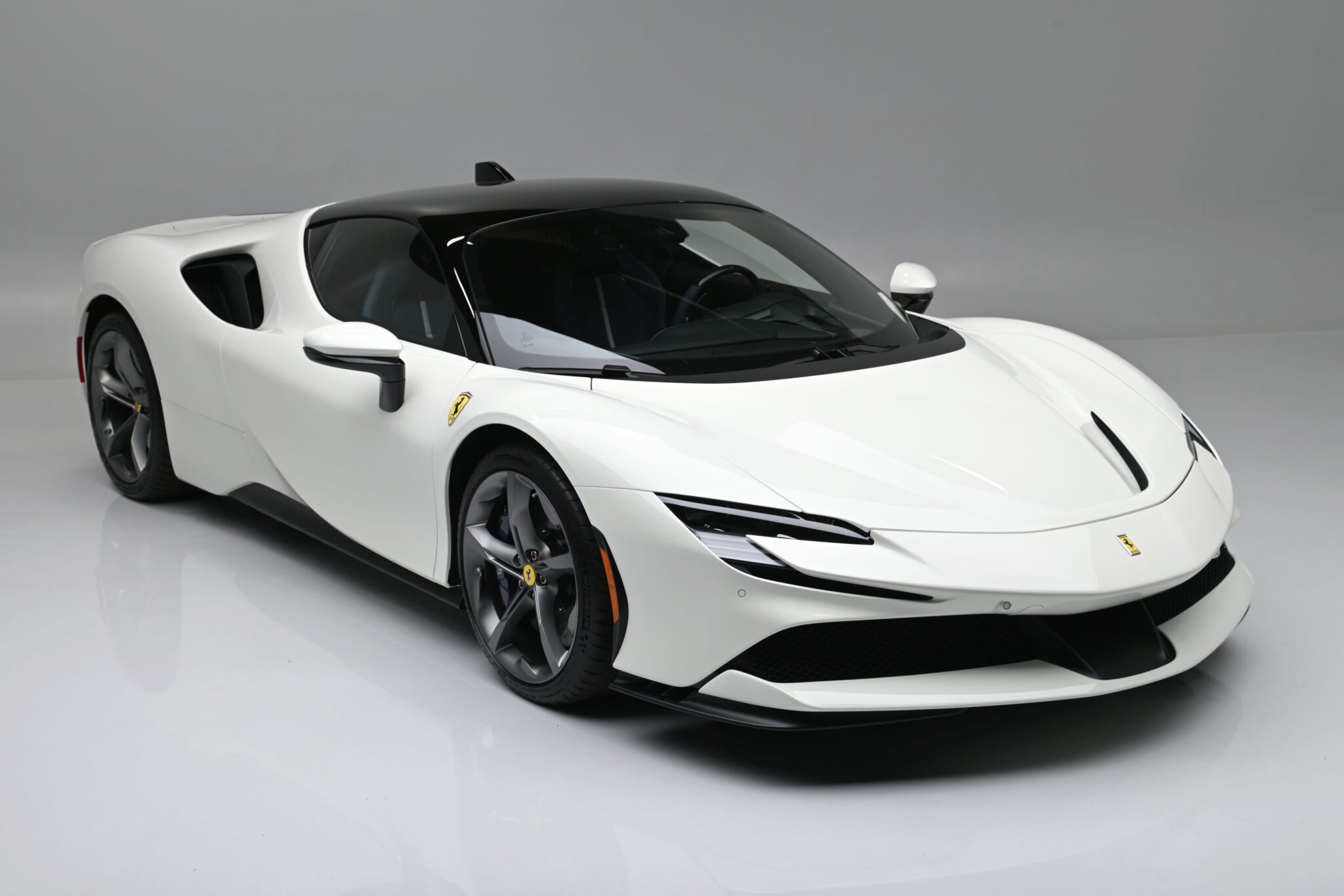
The SF90’s torque management system represents one of the most sophisticated implementations of hybrid technology in a performance vehicle.
The Manettino dial and various driving modes alter not just engine parameters but also electric motor deployment strategies, changing the character of torque delivery from efficient and smooth to aggressive and track-focused.
This versatility allows a single vehicle to exhibit multiple personalities while maintaining exceptional torque-to-weight performance across all configurations.
Battery integration in the SF90 demonstrates how hybrid systems can achieve high torque-to-weight ratios without the extreme weight penalties associated with large battery packs.
The relatively small 7.9kWh battery provides sufficient energy for the electric motors while keeping weight to a minimum. The battery’s strategic placement helps optimize weight distribution while ensuring adequate cooling for sustained high-performance operation.
The SF90’s advanced traction control systems are essential for managing its substantial torque output effectively. The Ferrari Dynamic Enhancer system works in conjunction with electronic stability programs to ensure optimal traction across all four wheels, even when the combined powertrains are producing maximum torque.
This sophisticated management allows drivers to access the full performance potential safely, regardless of driving conditions or skill level. Carbon fiber construction throughout the SF90 contributes significantly to its impressive torque-to-weight ratio.
The chassis, body panels, and numerous interior components utilize advanced carbon fiber composites to minimize weight while maintaining structural integrity.
This lightweight construction amplifies the effectiveness of the hybrid powertrain’s torque output, creating acceleration and responsiveness that feels almost supernatural compared to heavier alternatives.
Also Read: 5 Brands With Top Security Ratings and 5 With Zero Theft Prevention Focus
5. Koenigsegg Jesko – Engineering Extremes
The Koenigsegg Jesko represents Swedish engineering’s approach to achieving extraordinary torque-to-weight ratios through innovative engine design and extreme weight reduction.
Producing up to 1,106 pound-feet of torque on E85 fuel while weighing approximately 3,131 pounds, the Jesko achieves an astronomical torque-to-weight ratio of 707 lb-ft per ton.
This achievement requires revolutionary approaches to both engine design and vehicle construction that push the boundaries of what’s possible in automotive engineering.
The Jesko’s twin-turbocharged 5.0-liter V8 engine incorporates numerous innovations that enable its extreme torque output. The flat-plane crankshaft reduces rotational mass while enabling higher rev limits, while the advanced turbocharging system features tumble valve-equipped intake ports that improve mixture preparation and combustion efficiency.
The result is an engine that produces massive torque while maintaining the high-rev characteristics typically associated with naturally aspirated designs.
Revolutionary transmission technology in the Jesko contributes significantly to its torque delivery effectiveness. The Light Speed Transmission (LST) features nine forward gears with the ability to shift directly between any gear ratio without sequential progression.
This capability allows the Jesko to maintain optimal engine speed for maximum torque production across a wide range of vehicle speeds, something impossible with conventional transmission designs.
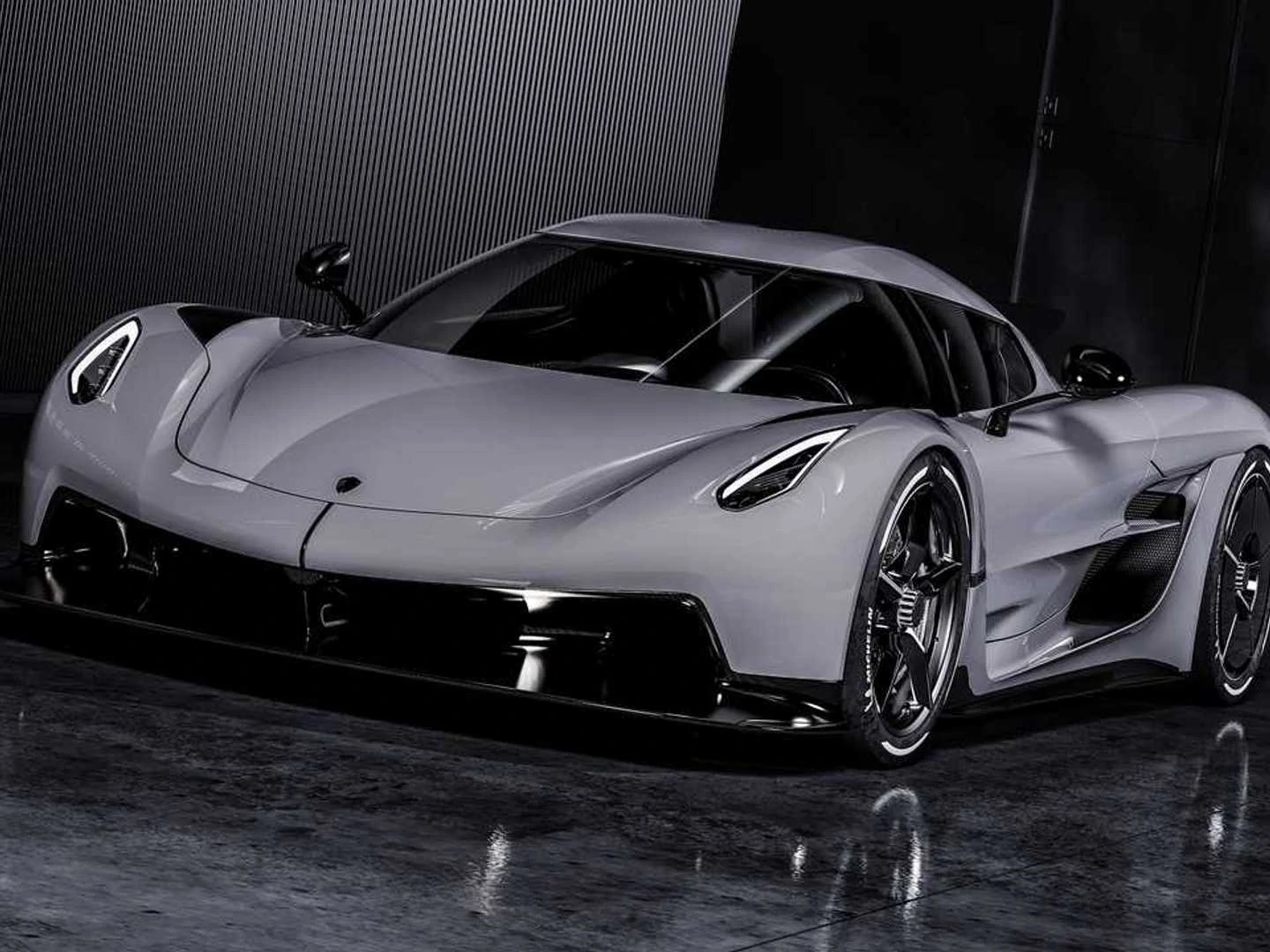
Weight reduction efforts in the Jesko extend to every component, from the carbon fiber monocoque chassis to the titanium exhaust system. The extensive use of advanced materials and manufacturing techniques results in a power-to-weight ratio that approaches single-seater race cars while maintaining road car refinement and reliability.
This extreme approach to weight reduction directly amplifies the effectiveness of the engine’s enormous torque output. Active aerodynamics in the Jesko play a crucial role in managing the vehicle’s extreme torque-to-weight capabilities.
The active rear wing and front splitter work together to provide appropriate downforce levels for different driving conditions, ensuring that the massive torque can be effectively transmitted to the road surface.
The aerodynamic systems also contribute to cooling efficiency, allowing the engine to maintain peak torque output during extended high-performance driving.
The Jesko’s sophisticated traction management systems are essential for safely deploying its extreme torque output. Advanced stability control systems work in conjunction with the limited-slip differential to prevent wheelspin while allowing experienced drivers to explore the vehicle’s limits safely.
The electronic systems can modulate torque delivery thousands of times per second, ensuring optimal traction regardless of road conditions or driver inputs.
Cooling system design in the Jesko represents another area where extreme engineering enables exceptional torque-to-weight performance. Multiple heat exchangers and advanced ducting ensure optimal operating temperatures for the engine, transmission, and differential during sustained high-performance operation.
This thermal management capability allows the Jesko to maintain its peak torque output consistently, unlike some high-performance vehicles that suffer from heat-related power reduction during track use.
5 Cars Struggling with Low Torque-to-Weight Ratios
These disappointing vehicles suffer from poor torque-to-weight ratios that make them feel sluggish and unresponsive despite having seemingly adequate engine sizes and displacement figures.
V8 models under the wide-ranging Stellantis umbrella fare far better than the 2024 Chevrolet Silverado, as well. Heavy curb weights combined with engines tuned for fuel economy rather than performance create vehicles that struggle to deliver satisfying acceleration or responsive power delivery.
Many of these cars feature large, naturally aspirated engines that produce modest torque figures, or they carry excessive weight from luxury features and safety equipment that overwhelms their powertrains.
The mismatch between engine output and vehicle mass results in disappointing acceleration times and a general sense of lethargy that makes highway merging and hill climbing feel labored.
These vehicles often require significant throttle input to achieve even moderate acceleration, creating driving experiences that feel disconnected and unresponsive compared to their more efficiently engineered competitors.
1. Mitsubishi Mirage – Economy Over Enthusiasm
The Mitsubishi Mirage represents the end of automotive efficiency prioritization, achieving remarkable fuel economy at the expense of performance.
With just 74 pound-feet of torque and a curb weight of approximately 2,051 pounds, the Mirage delivers a torque-to-weight ratio of only 72 lb-ft per ton.
This figure, while serving the vehicle’s intended purpose as an ultra-efficient urban runabout, creates driving characteristics that many enthusiasts find deeply unsatisfying and occasionally problematic in real-world scenarios.
The Mirage’s 1.2-liter three-cylinder engine embodies a minimum viable powertrain philosophy, designed primarily to meet emissions and fuel economy targets rather than provide engaging driving experiences.
The tiny displacement and cylinder count result in inherently low torque production, while the engine’s optimization for efficiency rather than performance further constrains torque output. Peak torque arrives at 4,000 RPM, requiring significant engine speed to access the limited pulling power available.
Real-world driving implications of the Mirage’s poor torque-to-weight ratio become apparent in numerous scenarios. Highway merging requires extensive planning and often full-throttle acceleration for uncomfortably long periods.
Hill climbing becomes an exercise in momentum preservation, as the engine lacks sufficient torque to maintain speed on moderate inclines without downshifting and high RPM operation. Even city driving can feel labored when carrying passengers or cargo.
The continuously variable transmission (CVT) in the Mirage attempts to optimize the limited torque available, but the system’s programming prioritizes fuel economy over responsiveness.

The CVT holds engine speed at efficient levels rather than allowing quick access to peak torque, creating a disconnect between throttle input and vehicle response that many drivers find frustrating. This transmission behavior exacerbates the already poor torque-to-weight situation.
Weight reduction efforts in the Mirage help partially offset the engine’s torque deficit, but the savings come primarily from reduced equipment levels and cheaper materials rather than advanced lightweight construction.
The relatively low curb weight of just over 2,000 pounds helps the anemic engine move the vehicle, but the savings aren’t sufficient to create satisfying performance. The weight reduction also comes at the cost of refinement and structural rigidity.
Despite its performance limitations, the Mirage’s torque-to-weight characteristics serve specific market needs effectively. Urban commuting, where sustained high-speed acceleration isn’t required, allows the Mirage to function adequately while delivering exceptional fuel economy.
The vehicle’s low purchase price and minimal operating costs make it attractive to budget-conscious buyers who prioritize efficiency over driving enjoyment.
The Mirage’s situation illustrates the challenges facing manufacturers attempting to create ultra-efficient vehicles. Achieving extreme fuel economy often requires engine designs and calibrations that severely constrain torque production, creating vehicles that struggle with basic performance tasks.
While the Mirage serves its intended purpose, it demonstrates how extreme efficiency priorities can result in torque-to-weight ratios that compromise fundamental drivability.
2. Chevrolet Trax – Compact SUV Compromises
The Chevrolet Trax exemplifies the challenges inherent in creating affordable compact SUVs, delivering 162 pound-feet of torque while weighing approximately 3,300 pounds for a torque-to-weight ratio of just 98 lb-ft per ton.
This underwhelming figure results from the fundamental compromise between SUV functionality, fuel economy requirements, and cost constraints that define the entry-level crossover segment.
The Trax’s torque deficit becomes particularly apparent when the vehicle is loaded with passengers and cargo or when operating in challenging driving conditions.
The Trax’s turbocharged 1.4-liter four-cylinder engine represents GM’s attempt to balance efficiency with acceptable performance, but the small displacement and conservative tuning limit torque production.
While turbocharging typically enhances torque output, the Trax’s engine prioritizes fuel economy and emissions compliance over peak torque figures.
The turbocharger spools relatively slowly, creating a noticeable lag between throttle application and torque delivery that makes the already modest output feel even more inadequate.
Weight considerations in the Trax demonstrate the inherent challenges of the compact SUV formula. The higher seating position, increased ground clearance, and SUV body structure add significant mass compared to equivalent sedans or hatchbacks, while the entry-level positioning prevents the use of expensive lightweight materials.
This weight penalty directly impacts the torque-to-weight ratio and creates a vehicle that feels sluggish despite reasonable power figures on paper.
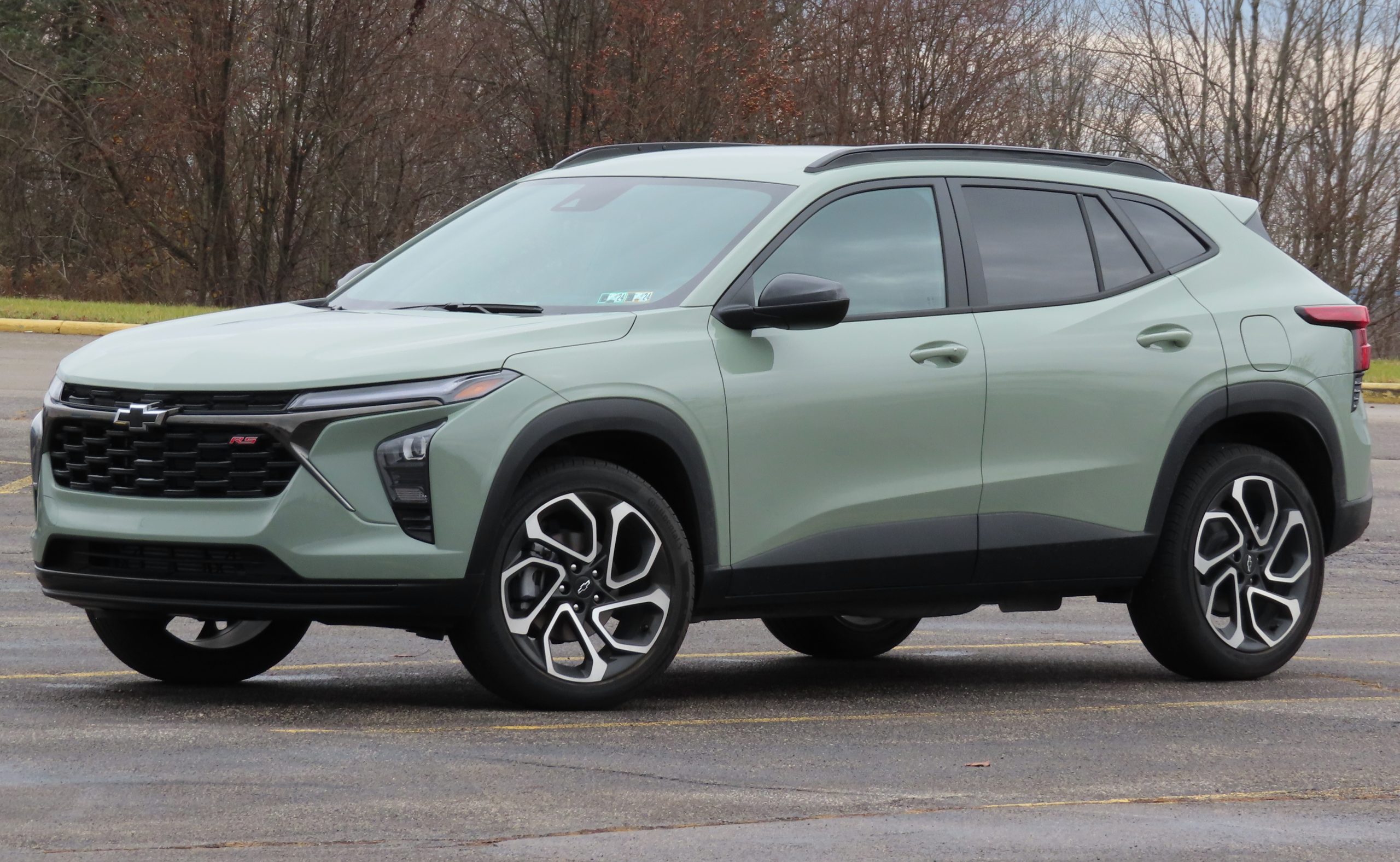
The continuously variable transmission in the Trax attempts to optimize the limited torque available, but like many CVT applications, it prioritizes efficiency over performance.
The transmission’s programming keeps engine speeds low for fuel economy, often placing the engine outside its peak torque band during normal driving.
When acceleration is demanded, the CVT’s rubber-band effect creates engine speed increases without proportional vehicle acceleration, highlighting the torque deficit.
Real-world performance implications of the Trax’s poor torque-to-weight ratio manifest in various driving scenarios. Highway merging becomes challenging, particularly when the vehicle is loaded or when operating at altitude.
Mountain driving reveals the engine’s inability to maintain speed on grades without significant downshifting and high RPM operation. Even city driving can feel labored when air conditioning is operating or when carrying additional passengers.
The Trax’s torque deficit becomes more pronounced when compared to competitors or previous-generation vehicles. Many rival compact SUVs offer similar or better torque-to-weight ratios despite comparable pricing and efficiency targets.
Earlier SUVs, while less efficient, often provided better low-end torque that made them feel more responsive despite lower peak power figures. This comparison highlights how modern efficiency requirements can sometimes compromise fundamental drivability.
Despite its performance limitations, the Trax serves specific market segments effectively. Urban drivers who prioritize fuel economy, cargo space, and elevated seating position over acceleration may find the vehicle adequate for their needs.
The Trax’s low purchase price and reasonable operating costs make it attractive to budget-conscious buyers, though the torque deficit ensures that driving enjoyment remains minimal.
3. Nissan Versa – Sedan Struggles
The Nissan Versa represents the challenges facing modern economy sedans, producing just 122 pound-feet of torque while weighing approximately 2,599 pounds, resulting in a torque-to-weight ratio of 94 lb-ft per ton.
This modest figure reflects the sedan’s focus on affordability and fuel efficiency rather than driving engagement, creating a vehicle that struggles with basic performance tasks while serving its primary mission of economical transportation.
The Versa’s torque characteristics demonstrate how extreme cost and efficiency pressures can compromise fundamental drivability. The Versa’s naturally aspirated 1.6-liter four-cylinder engine embodies a conservative design philosophy, prioritizing reliability and fuel economy over torque production.
The engine’s relatively small displacement and efficiency-focused tuning result in peak torque delivery at higher RPM ranges, requiring significant engine speed to access the limited pulling power available.
This characteristic creates a disconnect between driver expectations and actual performance, particularly during low-speed driving scenarios. Transmission choices in the Versa further compromise its already modest torque-to-weight ratio.
The continuously variable transmission, while optimizing fuel efficiency, keeps engine speeds in economical ranges rather than torque-producing RPM bands.
The CVT’s programming prioritizes efficiency over responsiveness, creating sluggish acceleration that makes the torque deficit feel even more pronounced. Manual transmission options, where available, require frequent shifting to maintain the engine in its narrow torque band.

Weight considerations in the Versa demonstrate how cost-cutting measures can inadvertently impact performance. While the sedan architecture should theoretically provide weight advantages over SUVs, the Versa’s focus on interior space and cost-effective construction prevents the extreme weight reduction that might offset the engine’s torque limitations.
The resulting curb weight, while reasonable for the class, still exceeds what the modest engine can move with authority. Real-world driving implications of the Versa’s poor torque-to-weight ratio become apparent in numerous scenarios.
Highway merging requires careful planning and often full-throttle acceleration for extended periods. Air conditioning operation noticeably impacts acceleration, as the engine lacks sufficient torque reserves to overcome the additional load.
Hill climbing becomes challenging, particularly with passengers or cargo, requiring downshifting and high RPM operation to maintain speed. The Versa’s torque deficit becomes more apparent when comparing it to previous-generation vehicles or international market alternatives.
Earlier Versas often featured larger engines with better low-end torque characteristics, while global market versions sometimes offer more powerful engine options.
These comparisons highlight how North American market efficiency requirements and cost pressures can result in powertrains that compromise basic drivability.
Interior space priorities in the Versa may justify some performance compromises, as the vehicle offers impressive passenger and cargo accommodations relative to its footprint and price point.
However, the torque-to-weight deficit ensures that accessing this space requires patience and planning, particularly when merging onto highways or climbing hills with a full load of passengers and luggage.
Despite its performance limitations, the Versa serves specific transportation needs effectively. Urban commuters who prioritize fuel economy, reliability, and low purchase prices may find the vehicle adequate for daily transportation.
The sedan’s low operating costs and reasonable interior space make it attractive to budget-conscious buyers, though the torque deficit ensures that driving satisfaction remains minimal.
4. Jeep Compass – Off-Road Pretensions, On-Road Limitations
The Jeep Compass attempts to combine off-road capability with on-road efficiency, resulting in a compromise that satisfies neither objective completely.
With 175 pound-feet of torque and a curb weight of approximately 3,487 pounds, the Compass achieves a torque-to-weight ratio of just 100 lb-ft per ton.
This modest figure reflects the inherent challenges of creating affordable SUVs that attempt to serve multiple purposes while meeting stringent efficiency requirements, resulting in a vehicle that feels underpowered in most driving scenarios.
The Compass’s naturally aspirated 2.4-liter four-cylinder engine represents Chrysler’s attempt to balance efficiency with acceptable performance, but the conservative tuning and emissions equipment severely constrain torque production.
The engine produces its peak torque at 3,900 RPM, requiring significant engine speed to access maximum pulling power. This characteristic creates sluggish, low-speed response that makes the vehicle feel particularly underpowered during city driving and parking maneuvers.
All-wheel drive capability in the Compass adds functional versatility but exacerbates the torque-to-weight deficit through additional mechanical complexity and weight.
The all-wheel drive system’s components, including transfer case, rear differential, and driveshafts, add approximately 200 pounds to the vehicle’s curb weight while consuming additional power through drivetrain losses. This weight penalty directly impacts the already modest torque-to-weight ratio.
The continuously variable transmission in the Compass attempts to optimize the limited torque available, but the system’s efficiency-focused programming often keeps the engine operating outside its peak torque band.
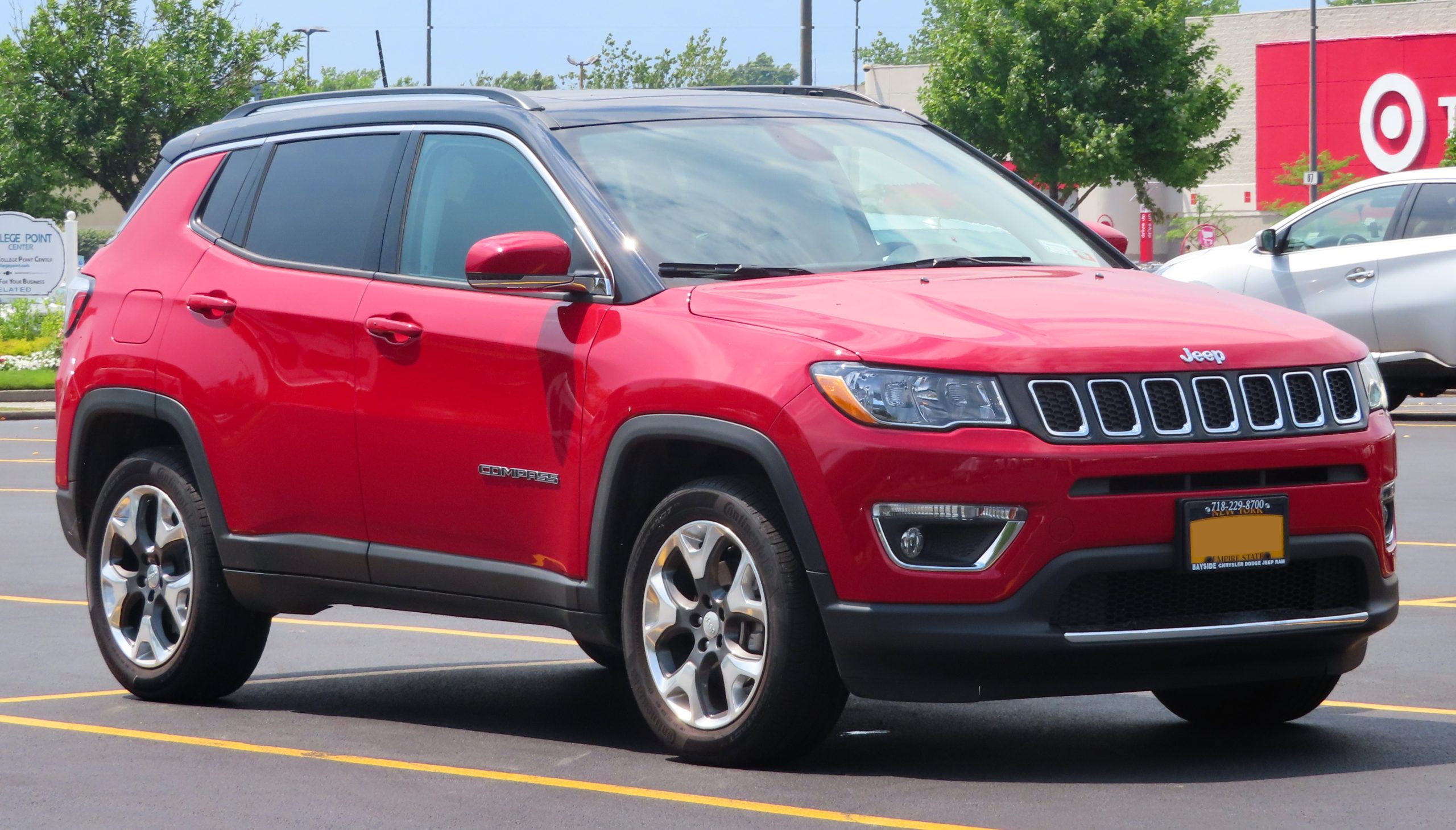
During acceleration, the CVT creates the characteristic rubber-band effect where engine RPM increases without proportional vehicle acceleration, highlighting the torque deficit and creating an unsatisfying driving experience that many buyers find frustrating.
Ground clearance and SUV proportions in the Compass contribute to its weight penalty while also impacting aerodynamic efficiency. The higher stance and upright seating position require additional structural reinforcement and result in increased frontal area, both of which work against acceleration performance.
These SUV characteristics, while providing utility advantages, directly compromise the vehicle’s ability to utilize its modest torque output effectively.
Real-world performance implications of the Compass’s poor torque-to-weight ratio become particularly apparent during loaded operation. Adding passengers and cargo to the vehicle’s generous interior space pushes the torque deficit to problematic levels, where highway merging becomes genuinely challenging and mountain driving requires extensive use of lower gears.
The vehicle’s off-road pretensions become academic when it struggles with basic on-road performance tasks. Competitive comparisons reveal how the Compass’s torque-to-weight ratio falls short of segment expectations.
Many rival compact SUVs offer turbocharged engines or more powerful naturally aspirated units that provide better torque characteristics. Some competitors achieve similar efficiency figures while delivering noticeably better acceleration and drivability, highlighting the Compass’s compromised powertrain calibration.
Despite its performance limitations, the Compass offers certain advantages that may justify its torque deficit for specific buyers. The vehicle’s Jeep heritage provides perceived off-road capability, while the spacious interior and reasonable fuel economy serve family transportation needs.
However, the poor torque-to-weight ratio ensures that the Compass feels underpowered in most driving scenarios, compromising the overall ownership experience.
5. Subaru Ascent – Three-Row Weight Reality
The Subaru Ascent represents the challenges inherent in creating three-row SUVs with efficient powertrains, delivering 277 pound-feet of torque while weighing approximately 4,467 pounds for a torque-to-weight ratio of 124 lb-ft per ton.
While not the worst figure among underpowered vehicles, the Ascent’s ratio becomes problematic when considering the vehicle’s intended mission of carrying up to eight passengers and their cargo.
The SUV’s weight reality overwhelms its turbocharged engine’s torque output, creating driving characteristics that feel inadequate for the vehicle’s size and purpose.
The Ascent’s turbocharged 2.4-liter four-cylinder engine represents Subaru’s attempt to balance efficiency with three-row SUV capability, but the conservative turbocharger tuning and CVT transmission compromise torque delivery.
While the engine produces reasonable peak torque figures, the turbocharger exhibits significant lag at low RPM, exactly where three-row SUVs need pulling power most.
This lag creates sluggish response during city driving and makes the vehicle feel underpowered when starting from rest with a full passenger load.
Weight considerations in the Ascent demonstrate the fundamental challenges of three-row SUV design. The extended wheelbase, additional row of seating, and structural reinforcements required for the larger body create substantial mass that overwhelms the four-cylinder engine’s torque output.
When loaded with passengers and cargo, the Ascent’s weight can approach or exceed 5,500 pounds, pushing the effective torque-to-weight ratio below 100 lb-ft per ton.
The continuously variable transmission in the Ascent attempts to optimize the turbocharged engine’s characteristics, but the system’s programming often conflicts with the driver’s torque demands.
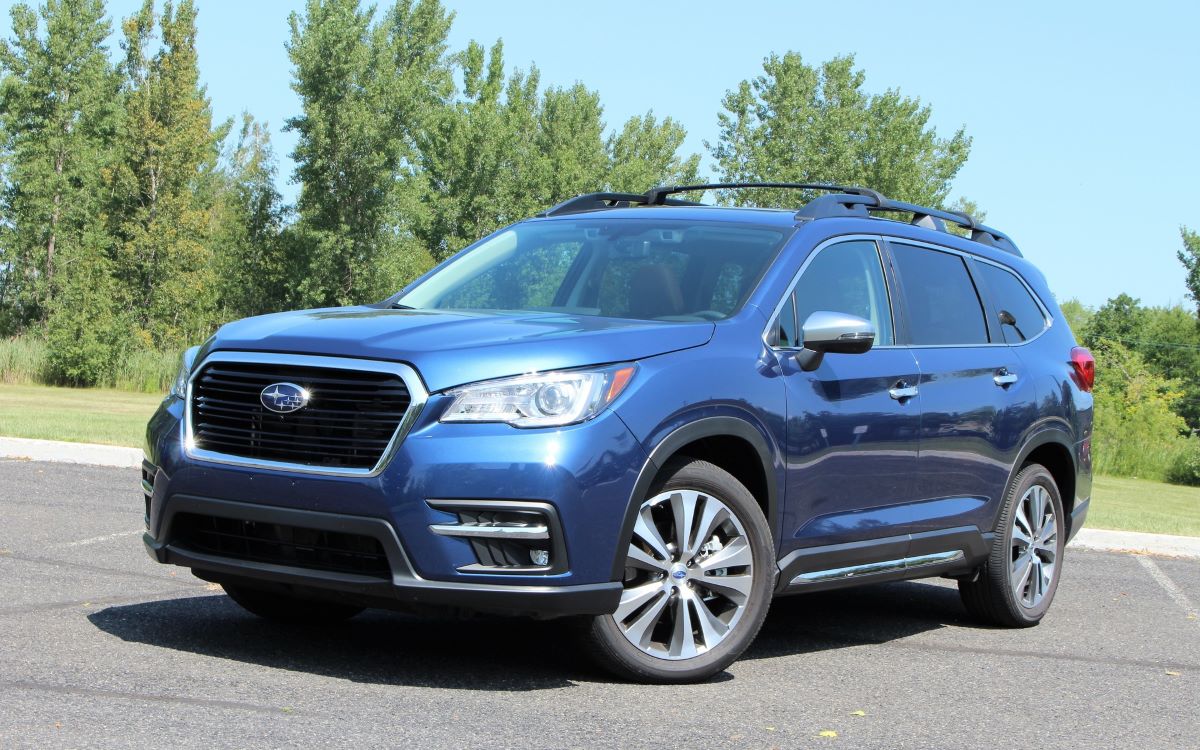
The CVT’s efficiency focus keeps the engine operating at low RPM during steady-state driving, placing it outside the turbocharger’s effective range.
When acceleration is demanded, the transmission’s response creates high engine speeds without immediate torque delivery, highlighting the powertrain’s inadequacy.
All-wheel drive standard equipment in the Ascent provides capability advantages, but further compromises the torque-to-weight equation through additional drivetrain losses and weight.
The full-time all-wheel drive system consumes power continuously, reducing the effective torque available at the wheels. While this system provides excellent traction and stability, it exacerbates the fundamental torque deficit that characterizes the Ascent’s performance.
Real-world performance implications of the Ascent’s modest torque-to-weight ratio become apparent in family-oriented driving scenarios. Loading the vehicle with passengers and vacation cargo creates acceleration that feels genuinely inadequate for highway merging and mountain driving.
The turbo lag becomes more pronounced under load, creating dangerous situations where immediate acceleration is needed but not available. Competitive analysis reveals how the Ascent’s torque-to-weight ratio compares unfavorably to alternatives.
Many three-row SUVs offer V6 engines with better torque characteristics or more powerful turbocharged units that provide superior pulling power.
Some competitors achieve similar fuel economy figures while delivering noticeably better acceleration and towing capability, highlighting the Ascent’s powertrain limitations.
Despite its performance deficits, the Ascent offers certain advantages that may appeal to specific buyers. The vehicle’s standard all-wheel drive, generous interior space, and strong safety ratings serve family needs effectively.
However, the poor torque-to-weight ratio when loaded ensures that the Ascent struggles with its primary mission of moving large families and their belongings efficiently, compromising the fundamental utility that three-row SUV buyers expect.
Also Read: 5 Hybrids With Lowest Cold-start Fuel Use And 5 Guzzlers To Avoid