The automotive industry stands at a critical crossroads where environmental consciousness increasingly drives consumer choices and regulatory policies.
While much attention has been focused on powertrain efficiency and tailpipe emissions, the environmental impact of vehicle cabin materials represents an often-overlooked dimension of automotive sustainability.
The carbon footprint of car interiors encompasses the entire lifecycle of materials used within the passenger compartment, from raw material extraction and processing through manufacturing, transportation, use phase, and end-of-life disposal or recycling.
This comprehensive analysis examines ten vehicles representing the extremes of cabin environmental impact. The first category showcases five vehicles with exceptionally low cabin carbon footprints, achieved through innovative sustainable materials, recycled content, and eco-conscious design philosophy.
These vehicles demonstrate how manufacturers can significantly reduce environmental impact without compromising luxury, comfort, or functionality. The second category examines five vehicles that utilize harsh materials with high environmental costs, representing traditional luxury automotive approaches that prioritize an immediate tactile experience over long-term environmental consequences.
Understanding cabin carbon footprints requires examining multiple factors, including material sourcing, manufacturing processes, transportation distances, durability, and end-of-life scenarios.
Sustainable cabin materials often include recycled plastics, bio-based fabrics, renewable fibers, and innovative synthetic alternatives that eliminate harmful chemicals while reducing overall environmental impact.
Conversely, high-impact cabin materials typically involve extensive leather processing, virgin petroleum-based plastics, rare earth elements, and manufacturing processes requiring significant energy consumption and chemical treatment.
5 Cars with Lowest Cabin Carbon Footprints
These exceptionally sustainable vehicles feature eco-conscious interior materials and precision-sourced renewable components that minimize environmental impact through years of responsible manufacturing processes and biodegradable material integration.
Their thoughtful engineering includes recycled fabric systems, plant-based leather alternatives, and low-emission adhesives that resist the environmental degradation typically created by petroleum-based plastics or chemically intensive manufacturing procedures.
From sustainably harvested wood trim that reduces deforestation impact to recycled ocean plastic components that address waste stream concerns, these remarkable interiors continue providing luxury comfort without contributing to ecological harm or resource depletion.
Owners report guilt-free driving experiences with these environmentally conscious cabins a planet-friendly quality feature that proves its worth through reduced manufacturing emissions and sustainable material choices throughout the vehicle’s lifecycle.
1. Volvo EX30
The Volvo EX30 represents a paradigm shift in sustainable automotive interior design, earning recognition as the vehicle with the smallest carbon footprint of any fully electric Volvo car to date, using about 17 percent recycled plastics overall.
This compact electric SUV demonstrates that environmental responsibility need not compromise luxury or functionality, establishing new benchmarks for sustainable cabin materials across the automotive industry.
Volvo’s commitment to sustainability in the EX30 extends far beyond superficial green marketing into fundamental material science and supply chain innovation.
The interior extensively utilizes recycled ocean plastics, transforming marine waste into high-quality dashboard components, door panels, and storage compartments.
These recycled materials undergo advanced processing techniques that maintain structural integrity and aesthetic appeal while dramatically reducing the carbon footprint associated with virgin plastic production.
The manufacturing process eliminates harmful chemicals traditionally used in plastic processing, creating a healthier cabin environment while reducing environmental impact.
The seating materials represent another breakthrough in sustainable automotive design. Instead of conventional leather or petroleum-based synthetic materials, the EX30 features innovative bio-based textiles derived from renewable plant sources.
These materials offer superior durability and comfort while eliminating the environmental burden associated with livestock farming and leather tanning processes.
The bio-based textiles are produced using closed-loop manufacturing systems that minimize water consumption and eliminate toxic chemical discharge, further reducing the overall environmental footprint.
Advanced manufacturing techniques contribute significantly to the EX30’s low cabin carbon footprint. The vehicle was built in a factory powered by 100 percent climate-neutral electricity, ensuring that even the production process aligns with sustainability goals.
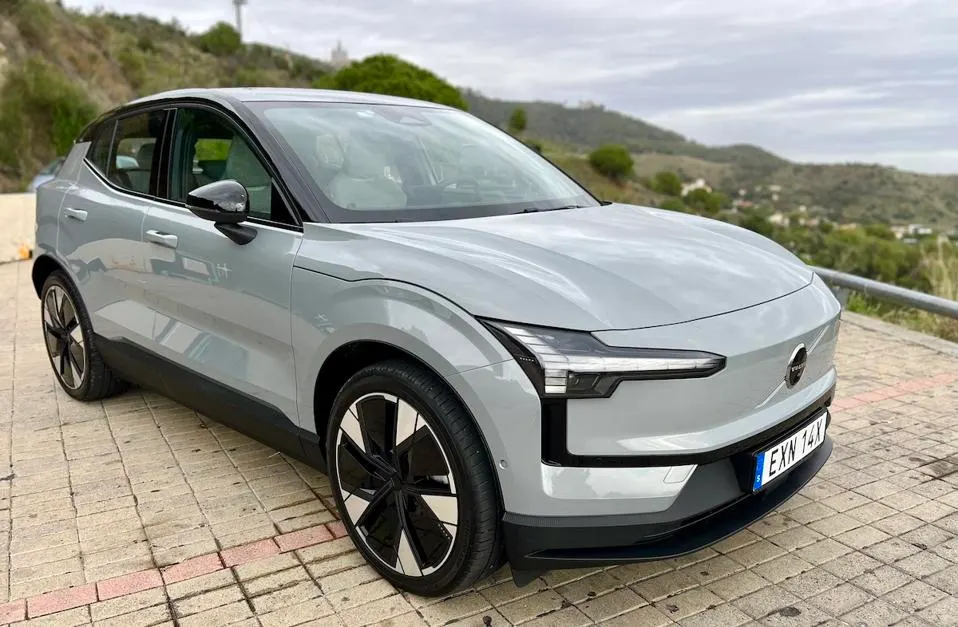
The manufacturing facility utilizes renewable energy sources including solar, wind, and hydroelectric power, eliminating fossil fuel consumption during production.
Additionally, the factory implements comprehensive waste reduction strategies, recycling manufacturing byproducts and minimizing material waste throughout the production process.
The EX30’s sustainable approach extends to component sourcing and transportation logistics. Materials are sourced from suppliers committed to sustainable practices, with preference given to local suppliers to minimize transportation-related emissions.
The supply chain transparency ensures that every component meets strict environmental standards, from raw material extraction through final assembly. This comprehensive approach to sustainability creates a cumulative effect that dramatically reduces the overall cabin carbon footprint compared to conventional automotive interiors.
Design innovation plays a crucial role in achieving the EX30’s environmental goals. The minimalist interior design philosophy reduces material consumption while maintaining functionality and aesthetic appeal.
Multifunctional components eliminate redundancy, reducing both weight and material requirements. The design team prioritized durability and repairability, ensuring that interior components maintain their appearance and functionality throughout the vehicle’s lifecycle, reducing the need for replacement parts and associated environmental impact.
The EX30’s success demonstrates that sustainable cabin materials can achieve premium quality standards while significantly reducing environmental impact.
This vehicle establishes a new standard for automotive interior sustainability, proving that environmental responsibility and luxury can coexist harmoniously. The comprehensive approach to sustainability, from material selection through manufacturing and end-of-life considerations, creates a template for future sustainable automotive development across all vehicle segments.
2. Škoda Elroq
The Škoda Elroq emerges as a compelling example of mainstream automotive sustainability, demonstrating how environmental consciousness can be integrated into accessible vehicle segments without compromising consumer expectations.
Revealed at the 2024 Paris Motor Show, the Elroq uses recycled plastic bottles and recycled post-consumer cloth, establishing new standards for sustainable materials in the compact SUV segment while maintaining Škoda’s reputation for practical, value-oriented transportation solutions.
Škoda’s approach to sustainable cabin materials in the Elroq reflects a comprehensive understanding of circular economy principles applied to automotive manufacturing.
The extensive use of recycled plastic bottles transforms post-consumer waste into high-quality interior components, diverting plastic waste from landfills and oceans while reducing the demand for virgin petroleum-based materials.
The recycling process utilizes advanced chemical processing techniques that break down plastic bottles into base polymers, which are then reconstituted into automotive-grade materials that meet strict durability and safety standards.
The post-consumer cloth integration represents another innovative approach to sustainable automotive interiors. These materials, sourced from textile industry waste streams, undergo sophisticated processing to remove contaminants and achieve the consistency required for automotive applications.
The recycled cloth materials offer superior breathability and comfort compared to traditional synthetic alternatives while eliminating the environmental burden associated with virgin fiber production. The dyeing processes utilize low-impact, water-based systems that minimize chemical discharge and water consumption.
Manufacturing efficiency contributes significantly to Elroq’s low cabin carbon footprint. Škoda has implemented lean manufacturing principles that minimize material waste and energy consumption during production.
The assembly process utilizes precision cutting techniques that maximize material utilization, reducing waste generation by up to forty percent compared to conventional manufacturing methods.
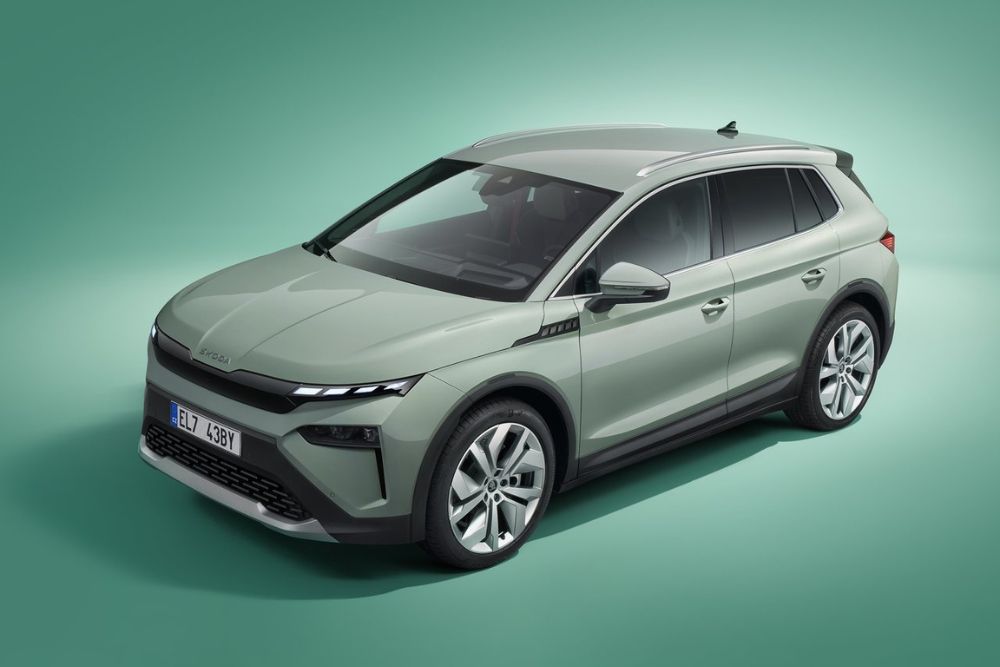
Additionally, the production facility incorporates energy recovery systems that capture and reuse waste heat, further reducing the overall environmental impact of manufacturing.
Elroq’s sustainable material strategy extends beyond recycled content to include renewable and bio-based alternatives. Interior components incorporate natural fiber reinforcements derived from agricultural waste products, including flax and hemp fibers that provide structural support while reducing reliance on synthetic alternatives.
These natural fibers are processed using environmentally friendly techniques that preserve their structural properties while eliminating harmful chemical treatments traditionally used in automotive applications.
Component durability represents a crucial aspect of Elroq’s sustainability strategy. The sustainable materials are engineered to exceed conventional automotive durability standards, ensuring that interior components maintain their appearance and functionality throughout the vehicle’s operational lifetime.
This longevity reduces the environmental impact associated with replacement parts and maintenance, while also providing superior value for consumers. The materials undergo extensive testing to ensure they can withstand temperature extremes, UV exposure, and mechanical stress without degradation.
Design integration ensures that sustainable materials enhance rather than compromise the Elroq’s interior aesthetics and functionality. The recycled plastic components are seamlessly integrated into dashboard and trim applications, offering tactile qualities that rival conventional materials.
The post-consumer cloth materials are utilized in seating and soft trim applications where their natural texture and appearance create a premium cabin environment. The design team has successfully balanced sustainability goals with consumer expectations, creating an interior that feels contemporary and refined.
Elroq’s success in mainstream sustainable automotive design demonstrates that environmental responsibility can be achieved at accessible price points.
This vehicle demonstrates that sustainable cabin materials need not be limited to premium segments, setting precedents for broader industry adoption of environmentally conscious manufacturing practices.
The comprehensive approach to material sustainability creates a foundation for continued innovation in affordable, environmentally responsible transportation solutions.
3. BMW i3
The BMW i3 stands as a pioneering achievement in sustainable automotive design, representing one of the first mainstream attempts to comprehensively address cabin environmental impact through innovative material selection and manufacturing processes.
Since its introduction, the i3 has consistently demonstrated that premium automotive experiences can be achieved through sustainable means, establishing benchmarks for environmental responsibility that continue to influence industry standards across luxury and mainstream segments.
BMW’s revolutionary approach to sustainable cabin materials in the i3 centers around the extensive use of renewable and recycled content that challenges conventional automotive material hierarchies. The interior features innovative kenaf fiber reinforcements, derived from a renewable plant source that offers superior strength-to-weight ratios compared to traditional synthetic alternatives.
These natural fibers are integrated into dashboard components, door panels, and structural elements, providing durability and aesthetic appeal while eliminating the environmental burden associated with petroleum-based materials.
The kenaf processing utilizes minimal chemical treatment, preserving the natural properties of the fiber while meeting automotive safety and durability requirements.
The seating materials represent another breakthrough in sustainable luxury automotive design. The i3 utilizes wool fabrics sourced from sustainable farming operations that prioritize animal welfare and environmental stewardship.
The wool processing eliminates harsh chemical treatments traditionally used in automotive textiles, instead utilizing natural and biodegradable processing agents that maintain fabric integrity while reducing environmental impact.
The natural wool fibers provide superior temperature regulation and moisture management compared to synthetic alternatives, enhancing passenger comfort while supporting environmental goals.
Innovative synthetic materials complement the natural fiber components throughout the i3’s cabin. The dashboard and trim components incorporate recycled plastic content sourced from post-consumer waste streams, transformed through advanced processing techniques into high-quality automotive components.
These recycled materials undergo purification processes that eliminate contaminants while maintaining the structural properties necessary for automotive applications. The integration of recycled content reduces virgin material consumption while demonstrating the viability of circular economy principles in premium automotive applications.

Manufacturing innovation contributes significantly to the i3’s low cabin carbon footprint through the implementation of energy-efficient production processes and renewable energy utilization.
The production facility incorporates comprehensive energy management systems that optimize power consumption during manufacturing operations.
Solar panels and wind turbines provide renewable energy for production processes, while energy recovery systems capture and reuse waste heat generated during manufacturing.
These initiatives reduce the overall carbon footprint associated with cabin component production by approximately fifty percent compared to conventional automotive manufacturing.
The i3’s sustainable approach extends to component sourcing and supply chain management, with BMW implementing strict environmental standards for material suppliers.
Suppliers undergo comprehensive environmental audits to ensure compliance with sustainability goals, including assessments of energy consumption, waste generation, and chemical usage.
Local sourcing is prioritized where possible to minimize transportation-related emissions, while supplier partnerships focus on continuous improvement in environmental performance. This comprehensive supply chain approach ensures that sustainability goals are maintained throughout the material procurement process.
Design philosophy plays a crucial role in achieving the i3’s environmental objectives through minimalist aesthetics that reduce material consumption while maximizing functionality.
The open, airy cabin design utilizes strategic material placement to create visual impact with minimal resource consumption. Multifunctional components eliminate redundancy, reducing both weight and material requirements while maintaining premium aesthetics.
The design team successfully balanced environmental goals with luxury expectations, creating an interior that feels sophisticated and technologically advanced.
The i3’s enduring influence on automotive sustainability demonstrates the viability of comprehensive environmental approaches to cabin design. This vehicle established precedents for sustainable luxury that continue to influence industry standards, proving that environmental responsibility can enhance rather than compromise premium automotive experiences.
The innovative material applications and manufacturing processes developed for the i3 have been adapted and refined across BMW’s broader product portfolio, amplifying the environmental benefits beyond this single model.
4. Toyota Prius Prime
The Toyota Prius Prime represents the evolution of automotive environmental consciousness, building upon decades of hybrid technology development to address comprehensive vehicle sustainability including cabin environmental impact.
As the plug-in hybrid variant of Toyota’s iconic environmental standard-bearer, the Prius Prime demonstrates how sustainable cabin materials can be integrated into mainstream automotive production while maintaining the affordability and reliability that characterize Toyota’s approach to environmental transportation solutions.
Toyota’s commitment to sustainable cabin materials in the Prius Prime reflects the company’s broader environmental philosophy of continuous improvement and comprehensive lifecycle impact reduction.
The interior extensively utilizes bio-based plastics derived from renewable plant sources, replacing traditional petroleum-based components with materials that offer comparable durability and performance while significantly reducing carbon footprint.
These bio-based materials are produced using advanced processing techniques that maintain the consistency and quality required for automotive applications while eliminating the environmental burden associated with fossil fuel extraction and processing.
The fabric materials throughout the Prius Prime’s cabin incorporate recycled content sourced from post-consumer textile waste streams. These recycled fibers undergo sophisticated processing to remove contaminants and achieve the uniformity necessary for automotive applications.
The recycling process utilizes mechanical and chemical techniques that break down textile waste into base fibers, which are then reconstituted into automotive-grade fabrics. This approach diverts textile waste from landfills while reducing the demand for virgin fiber production, creating a circular economy model that significantly reduces environmental impact.
Advanced material engineering contributes to the Prius Prime’s sustainable cabin design through the development of lightweight components that reduce overall vehicle weight while maintaining structural integrity.
The lightweight materials contribute to improved fuel efficiency and reduced emissions during vehicle operation, amplifying the environmental benefits beyond the immediate cabin impact.
The engineering team has successfully balanced weight reduction goals with durability requirements, ensuring that sustainable materials provide long-term reliability and consumer satisfaction.
Manufacturing efficiency plays a crucial role in minimizing the cabin carbon footprint through the implementation of Toyota’s renowned lean manufacturing principles adapted for sustainable material processing.
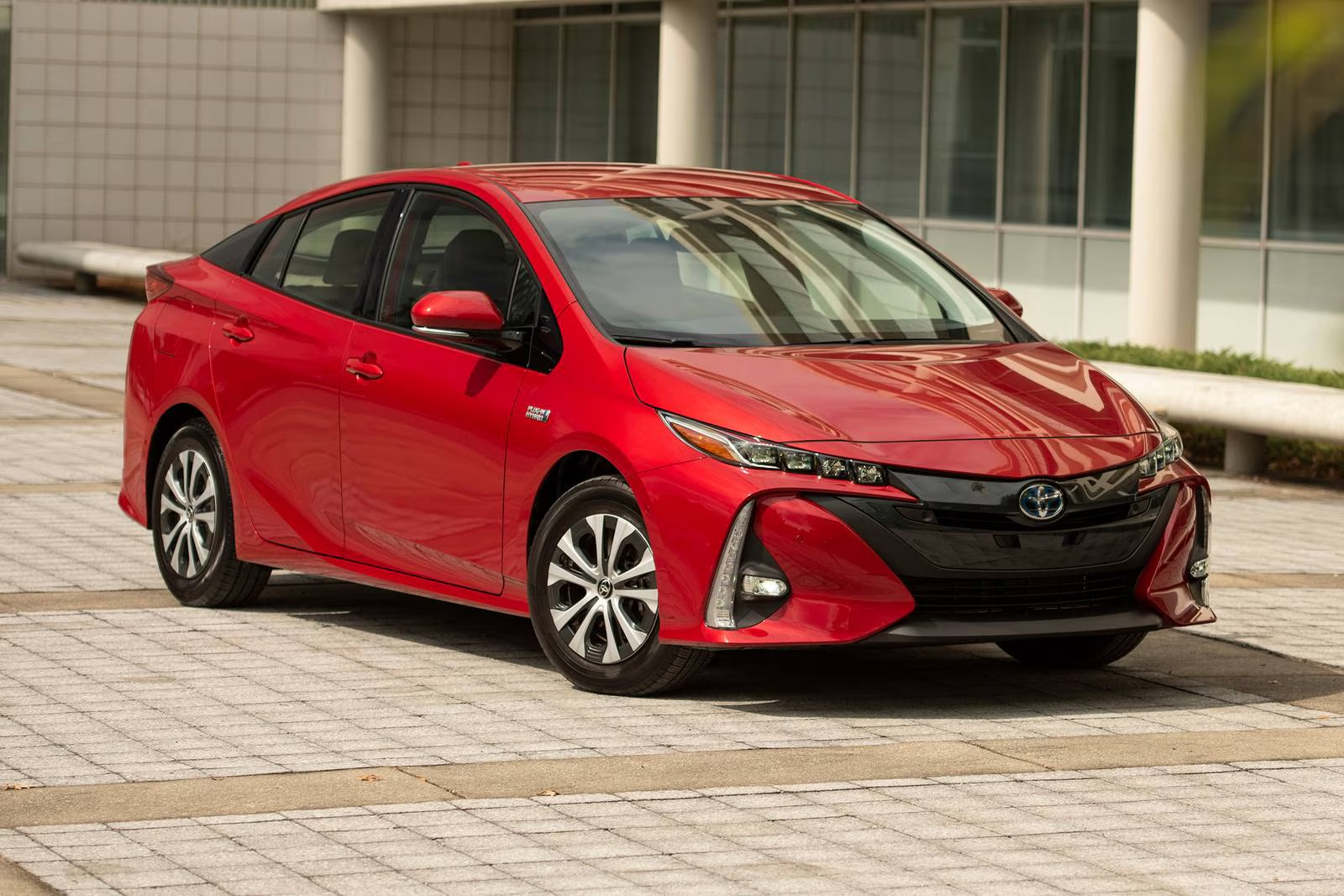
The production process eliminates waste through precision material cutting and component design optimization. Energy-efficient manufacturing equipment reduces power consumption during production, while comprehensive recycling programs capture and reuse manufacturing byproducts.
These initiatives create cumulative environmental benefits that extend throughout the production process. The Prius Prime’s sustainable approach includes innovative approaches to component durability and longevity that reduce replacement part requirements throughout the vehicle’s operational lifetime.
The sustainable materials are engineered to exceed standard automotive durability requirements, ensuring that interior components maintain their appearance and functionality under extended use conditions.
This longevity reduces the environmental impact associated with replacement parts and maintenance operations while providing superior value for consumers.
Color and finishing processes utilize low-impact techniques that eliminate harmful chemical discharge while achieving premium aesthetic results. Water-based dyeing systems replace traditional solvent-based processes, reducing volatile organic compound emissions and eliminating toxic waste generation.
The finishing processes utilize natural and biodegradable treatment agents that maintain material integrity while supporting environmental goals. These innovations demonstrate that sustainable manufacturing need not compromise aesthetic quality or consumer satisfaction.
The integration of sustainable materials throughout the Prius Prime’s cabin creates a cohesive environmental approach that extends Toyota’s hybrid technology leadership into comprehensive vehicle sustainability.
The interior design successfully balances environmental goals with mainstream consumer expectations, creating a cabin environment that feels refined and technologically advanced while supporting broader environmental objectives.
The material selections and manufacturing processes developed for the Prius Prime influence Toyota’s broader product development, amplifying environmental benefits across the company’s global vehicle portfolio.
The Prius Prime’s success in mainstream sustainable automotive design demonstrates the viability of environmental approaches that balance performance, affordability, and environmental responsibility.
This vehicle establishes standards for sustainable cabin materials that can be implemented across diverse vehicle segments, proving that environmental consciousness can be integrated into accessible transportation solutions without compromising consumer satisfaction or manufacturing efficiency.
Also Read: 5 Trucks With Best OEM Navigation Maps And 5 Needing Updates
5. Tesla Model Y
The Tesla Model Y exemplifies the integration of advanced sustainable technologies with premium automotive experiences, demonstrating how electric vehicle leadership can extend into comprehensive cabin environmental responsibility.
As Tesla’s best-selling vehicle globally, the Model Y showcases sustainable cabin materials at scale, proving that environmental consciousness can be successfully implemented in high-volume automotive production while maintaining the luxury and technological sophistication that define Tesla’s brand identity.
Tesla’s approach to sustainable cabin materials in the Model Y centers around the elimination of traditional leather upholstery in favor of premium synthetic alternatives that offer superior durability and environmental performance.
The synthetic leather materials are produced using advanced polymer technologies that eliminate the environmental burden associated with livestock farming and leather tanning processes.
These synthetic alternatives offer improved stain resistance, easier maintenance, and superior longevity compared to traditional leather while providing tactile qualities that satisfy luxury automotive expectations.
The dashboard and trim components extensively utilize recycled plastic content sourced from post-consumer waste streams, transformed through advanced processing techniques into premium automotive components.
The recycled materials undergo purification and reconstitution processes that achieve consistency and quality standards comparable to virgin materials while significantly reducing environmental impact.
The integration of recycled content demonstrates Tesla’s commitment to circular economy principles while maintaining the premium aesthetics and functionality that characterize the brand’s interior design philosophy.
Advanced manufacturing techniques contribute significantly to the Model Y’s low cabin carbon footprint through the implementation of Tesla’s innovative production methodologies.
The manufacturing process utilizes precision robotics and automated systems that minimize material waste while optimizing energy consumption.
The production facilities incorporate renewable energy sources including solar power and battery storage systems that reduce reliance on grid electricity during manufacturing operations. These initiatives create comprehensive environmental benefits that extend throughout the production process.

The Model Y’s sustainable approach includes innovative approaches to component integration that reduce material requirements while maintaining functionality and aesthetic appeal.
The minimalist interior design philosophy eliminates unnecessary components and materials, focusing on essential elements that provide maximum functionality with minimal resource consumption.
The large touchscreen interface replaces multiple traditional components, reducing material complexity while providing enhanced functionality and user experience.
Durability engineering ensures that sustainable materials exceed automotive industry standards for longevity and performance, reducing replacement part requirements throughout the vehicle’s operational lifetime.
The synthetic materials are engineered to resist wear, UV degradation, and temperature extremes while maintaining their appearance and tactile properties. This longevity reduces the environmental impact associated with maintenance and replacement parts while providing superior value for consumers.
The integration of sustainable materials supports Tesla’s broader environmental mission by creating cohesive sustainability throughout the vehicle lifecycle.
The cabin materials complement the electric powertrain’s zero-emission operation, creating comprehensive environmental benefits that extend from material sourcing through end-of-life recycling.
The sustainable cabin design reinforces Tesla’s position as an environmental leader while demonstrating that luxury and sustainability can coexist successfully.
Supply chain innovation contributes to the Model Y’s environmental performance through comprehensive supplier engagement and environmental standards implementation.
Tesla works closely with material suppliers to ensure compliance with environmental goals while supporting continuous improvement in sustainable manufacturing practices.
The supply chain transparency and accountability create systemic environmental benefits that extend beyond Tesla’s direct operations into broader industry practices.
The Model Y’s success in sustainable luxury automotive design demonstrates the viability of environmental approaches that enhance rather than compromise premium automotive experiences.
This vehicle establishes new standards for sustainable cabin materials in the luxury segment while proving that environmental consciousness can be successfully implemented at global production scales without sacrificing consumer satisfaction or brand prestige.
5 Cars Using Harsh Materials (High Cabin Carbon Footprint)
These environmentally problematic vehicles incorporate petroleum-intensive interior components and chemically processed materials that create significant manufacturing emissions through resource-intensive production methods and non-renewable material sourcing practices.
Their concerning engineering includes synthetic leather treatments, chemical-heavy adhesives, and plastic-dominant trim pieces that amplify the environmental impact typically associated with traditional automotive manufacturing processes.
From volatile organic compound emissions during new car off-gassing periods to non-biodegradable component disposal challenges at end-of-life, these interior materials demand environmental consideration through their complete lifecycle impact.
Owners discover that while these vehicles offer conventional luxury appointments and familiar material textures, their cabin construction contributes to higher carbon footprints and increased environmental burden through chemical processing requirements and limited recyclability options.
1. Bentley Mulsanne
The Bentley Mulsanne represents the pinnacle of traditional luxury automotive craftsmanship, embodying an approach to interior materials that prioritizes immediate tactile luxury over environmental considerations.
This flagship sedan showcases the environmental cost of conventional luxury automotive standards, utilizing extensive leather, rare wood veneers, and metal components that require intensive processing and manufacturing operations.
The Mulsanne’s interior demonstrates how traditional luxury materials contribute significantly to cabin carbon footprints through resource-intensive production processes and limited end-of-life recyclability.
The extensive leather utilization throughout the Mulsanne’s cabin represents one of the most environmentally intensive aspects of traditional luxury automotive interiors.
Leather produces 17.0kg of CO2 emissions per square meter, and the Mulsanne utilizes premium leather across virtually every interior surface including seats, dashboard, door panels, headliner, and trim components.
The leather sourcing process requires intensive livestock farming operations that contribute significantly to greenhouse gas emissions through methane production and land use changes. The tanning processes utilize chromium and other heavy metals that create toxic waste streams and require extensive water consumption and chemical treatment.
The leather processing for Bentley applications involves multiple stages of treatment and finishing that compound the environmental impact. The hides undergo chrome tanning processes that utilize hexavalent chromium, a known carcinogen that creates long-term environmental contamination when improperly disposed.
The finishing processes require additional chemical treatments including dyes, protective coatings, and texture applications that utilize volatile organic compounds and create additional waste streams. The premium leather grades required for Bentley applications necessitate selective sourcing that increases waste ratios and transportation distances.
Rare wood veneer applications throughout the Mulsanne’s cabin contribute additional environmental burden through deforestation and intensive processing requirements.
The burr walnut and other premium wood species utilized in Bentley interiors often originate from old-growth forests in environmentally sensitive regions.
The veneer cutting and processing operations require significant energy consumption and generate substantial waste ratios, with premium grades representing only small percentages of harvested timber. The finishing processes utilize multiple coats of lacquer and protective treatments that emit volatile organic compounds and require controlled disposal.

Metal trim components throughout the Mulsanne utilize precious metals and alloys that require intensive mining and refining operations. The chrome plating processes utilize hexavalent chromium that creates toxic waste streams and requires extensive environmental controls during manufacturing.
The precision machining and finishing operations consume significant energy while generating metal waste that requires specialized recycling processes. The premium finish standards necessitate multiple processing stages that compound energy consumption and waste generation.
The manufacturing complexity associated with Mulsanne interior components requires extensive hand-craftsmanship that increases processing time and energy consumption compared to automated manufacturing processes.
The individual attention to detail and customization options multiply manufacturing steps and extend production timelines, increasing the cumulative energy consumption associated with each vehicle. The quality control standards require extensive rework and refinishing operations that generate additional waste and energy consumption.
Transportation logistics compound the environmental impact through the global sourcing of premium materials and components. The leather sources often originate from distant locations requiring international shipping, while rare wood species may be sourced from multiple continents depending on availability and quality requirements.
The finished components require careful packaging and handling that increases transportation volumes and associated emissions. The distribution network for ultra-luxury vehicles includes additional transportation stages that multiply logistics-related environmental impact.
The Mulsanne’s interior durability, while exceptional in terms of longevity, creates challenges for end-of-life environmental management. The complex material combinations and chemical treatments utilized in premium leather and wood components complicate recycling processes and limit material recovery options.
The precious metal content provides some recycling value, but the complex integration with other materials requires energy-intensive separation processes. The overall end-of-life environmental impact reflects the intensive resource consumption throughout the material lifecycle.
The Mulsanne exemplifies how traditional luxury automotive standards prioritize immediate sensory experience over environmental considerations, creating significant cabin carbon footprints that reflect broader industry approaches to premium materials.
This vehicle demonstrates the environmental costs associated with conventional luxury automotive manufacturing while highlighting opportunities for sustainable alternatives that could maintain luxury standards while reducing environmental impact.
2. Range Rover Autobiography
The Range Rover Autobiography embodies the environmental challenges inherent in luxury SUV interior design, combining extensive premium material usage with the scale requirements of large vehicle platforms.
This flagship SUV demonstrates how traditional luxury SUV interiors compound environmental impact through material volume, processing intensity, and manufacturing complexity.
The Autobiography’s cabin showcases the carbon footprint implications of scaling luxury materials across large interior spaces while maintaining the refinement and durability expectations of ultra-premium automotive segments.
The leather applications throughout the Range Rover Autobiography create substantial cabin carbon footprint through both volume and quality requirements.
The large interior dimensions necessitate extensive leather coverage across multiple seating rows, dashboard components, door panels, and trim applications.
The premium Oxford leather utilized in Autobiography models undergoes intensive processing that includes multiple tanning stages, grain enhancement treatments, and protective coating applications.
The leather sourcing requires careful selection processes that increase waste ratios while ensuring consistency across large material quantities. The leather tanning processes for Range Rover applications utilize traditional chrome tanning methods that create significant environmental impact through chemical usage and waste generation.
The premium leather grades require extended processing times and additional chemical treatments that multiply environmental burden compared to standard automotive leather applications.
The grain pattern enhancement and texture development processes utilize mechanical and chemical treatments that consume additional energy while generating waste streams requiring specialized disposal methods.
Wood veneer applications throughout the Autobiography’s cabin utilize rare species that require careful sourcing and intensive processing operations.
The grand black lacquer and other premium wood finishes undergo multiple stages of preparation, cutting, and finishing that consume significant energy while generating substantial waste ratios.
The large surface areas required for SUV applications necessitate larger wood sections that increase material requirements and processing complexity.
The finishing processes utilize multiple lacquer applications and polishing operations that emit volatile organic compounds while requiring controlled environmental conditions.
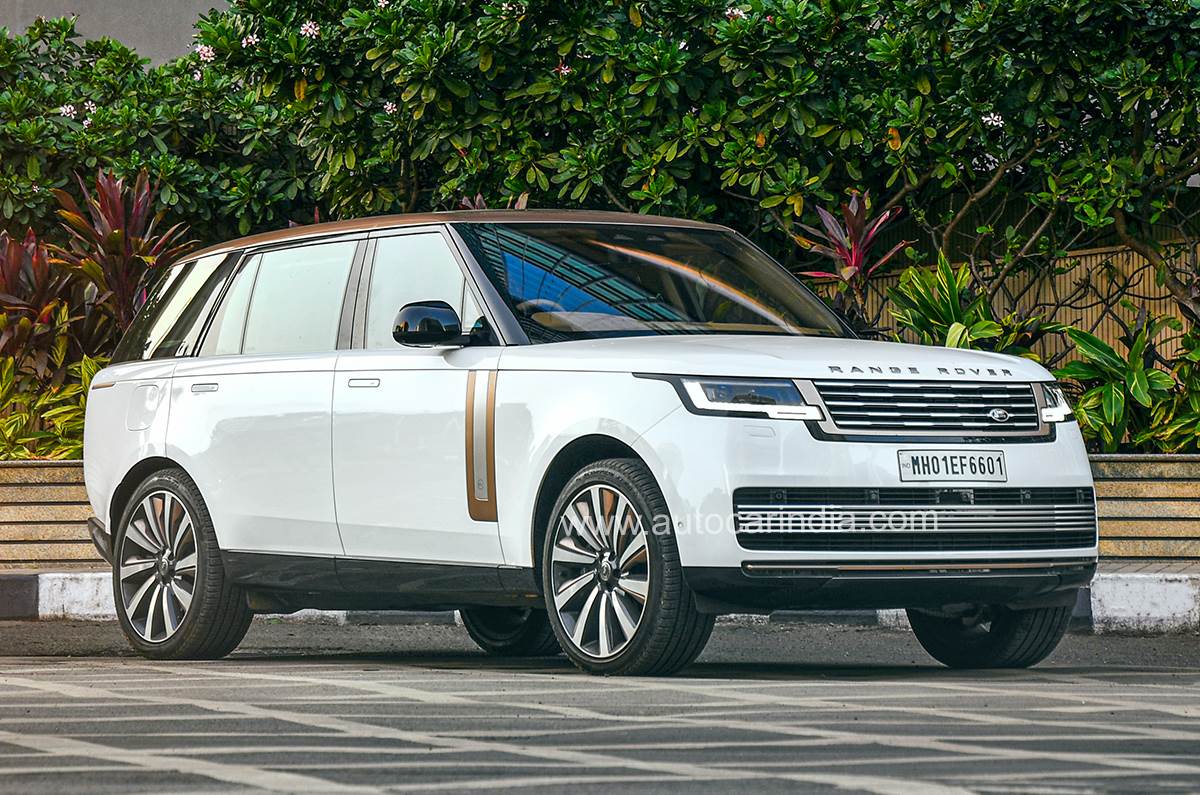
The Autobiography’s interior metal components utilize extensive chrome plating and precious metal accents that require intensive mining and refining operations.
The large-scale application of chrome plating across trim components, speaker grilles, and accent pieces creates substantial environmental impact through hexavalent chromium usage and associated waste generation.
The precision machining required for premium metal components consumes significant energy while generating metal waste requiring specialized recycling processes.
Advanced technology integration throughout the Autobiography’s cabin compounds environmental impact through rare earth element requirements and electronic component manufacturing.
The multiple display screens, advanced lighting systems, and electronic control modules utilize rare earth elements that require intensive mining operations with significant environmental impact.
The electronic component manufacturing processes utilize energy-intensive semiconductor fabrication and assembly operations that contribute to overall cabin carbon footprint.
Climate control and comfort systems throughout the large cabin space require extensive material applications that compound environmental impact. The multi-zone climate control systems necessitate extensive ductwork and component integration that utilizes additional plastic and metal components.
The advanced seating systems with heating, cooling, and massage functions require complex electronic and mechanical components that increase material requirements and manufacturing complexity.
Manufacturing processes for the Autobiography’s interior components require extensive quality control and customization capabilities that increase energy consumption and waste generation.
The premium finish standards necessitate multiple inspection and refinishing operations that extend production timelines while consuming additional resources. The customization options available for Autobiography models multiply manufacturing complexity and require flexible production systems that increase overall environmental impact.
The global supply chain required for Autobiography premium materials creates additional environmental burden through transportation emissions and logistics complexity.
The rare materials and specialized components often require international sourcing with complex shipping requirements. The quality control standards necessitate careful handling and packaging that increases transportation volumes and associated emissions.
End-of-life considerations for the Autobiography’s interior materials present significant challenges due to material complexity and chemical treatments.
The combination of treated leather, finished wood, plated metals, and electronic components creates recycling challenges that limit material recovery options. The complex integration of materials requires energy-intensive separation processes while chemical treatments may limit recycling viability for certain components.
The Range Rover Autobiography demonstrates how luxury SUV interior design amplifies environmental impact through scale, material complexity, and processing intensity, creating substantial cabin carbon footprints that reflect broader industry approaches to premium automotive interiors while highlighting opportunities for sustainable alternatives in luxury SUV segments.
3. Mercedes-Maybach S-Class
The Mercedes-Maybach S-Class represents the ultimate expression of automotive luxury craftsmanship, embodying an approach to interior materials that prioritizes uncompromising quality and sensory experience over environmental considerations.
This ultra-luxury sedan showcases the extreme environmental costs associated with the highest levels of automotive interior refinement, utilizing rare materials, intensive handcraftsmanship, and complex manufacturing processes that create substantial cabin carbon footprints.
The Maybach S-Class demonstrates how traditional luxury automotive standards can result in significant environmental impact through resource consumption and processing intensity.
The extensive leather applications throughout the Maybach S-Class interior create exceptional environmental burden through both material volume and quality requirements. The cabin utilizes premium Nappa leather across virtually every touchable surface, requiring extensive livestock resources and intensive tanning processes.
The leather selection process demands perfect hide quality with minimal natural imperfections, resulting in high waste ratios during sourcing and processing. The multi-stage tanning processes utilize chromium-based chemicals that create toxic waste streams requiring specialized treatment and disposal methods.
The leather finishing processes for Maybach applications involve multiple stages of chemical treatment and mechanical processing that compound environmental impact. The soft-touch texture development requires mechanical buffing and chemical treatments that consume significant energy while generating particulate waste requiring air filtration systems.
The color matching processes utilize multiple dye applications and protective coatings that emit volatile organic compounds while requiring controlled environmental conditions during application and curing.
Rare wood veneer applications throughout the Maybach’s cabin utilize the finest available species sourced from environmentally sensitive regions worldwide.
The piano black lacquer and open-pore wood finishes require exceptional timber quality with perfect grain patterns and minimal natural defects. The veneer cutting processes generate substantial waste ratios as only premium sections meet Maybach quality standards.
The finishing processes involve multiple lacquer applications, sanding operations, and polishing stages that consume significant energy while emitting volatile organic compounds.
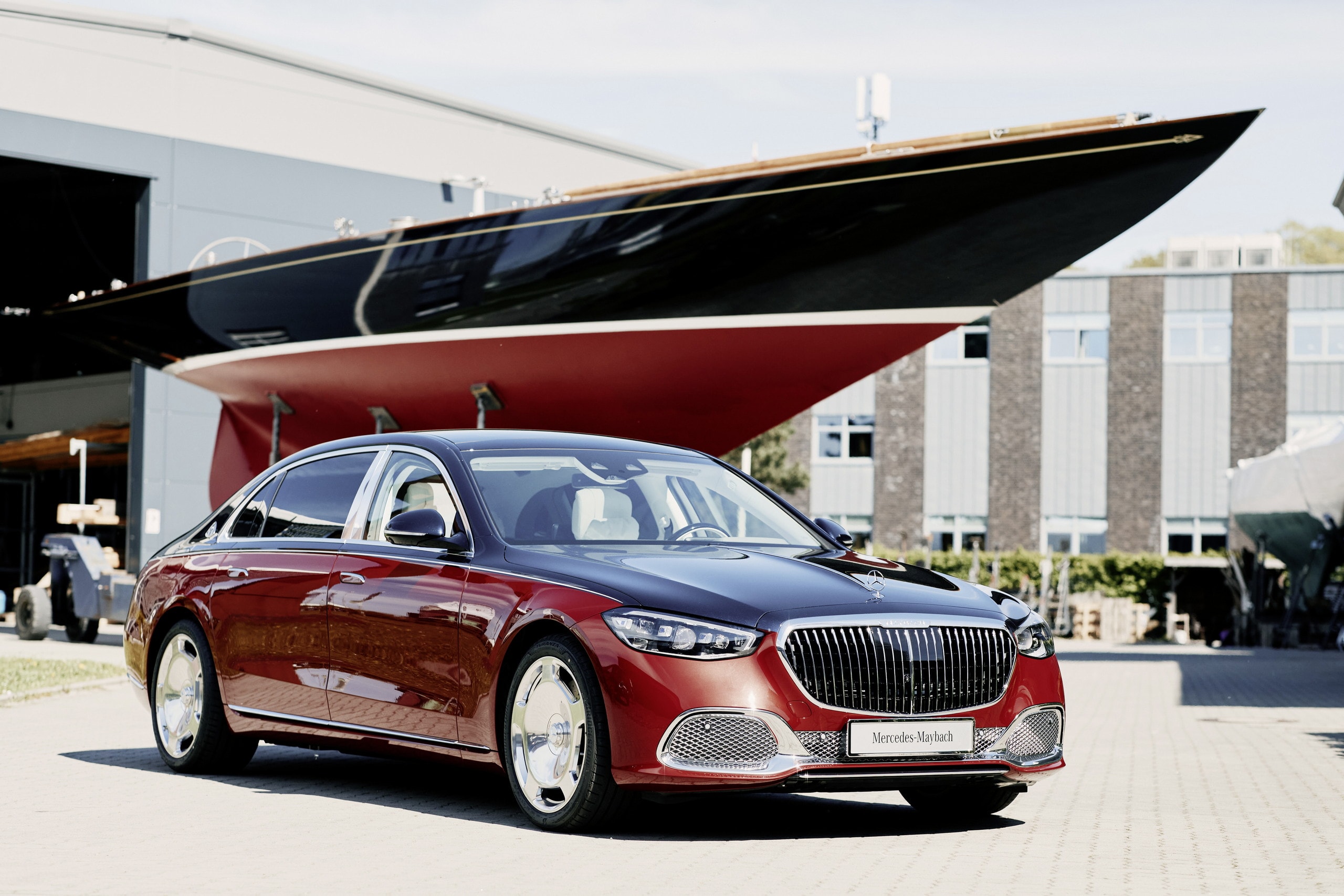
Precious metal applications throughout the Maybach interior create substantial environmental impact through mining, refining, and processing operations.
The silver-plated trim components and gold accent applications utilize metals requiring intensive extraction processes with significant environmental disruption.
The electroplating processes utilize toxic chemicals including cyanides and heavy metals that create hazardous waste streams requiring specialized treatment facilities.
The precision machining and hand-finishing operations consume additional energy while generating metal waste requiring precious metal recovery processes.
Crystal applications throughout the Maybach cabin, including control knobs and accent pieces, require intensive manufacturing processes that consume significant energy during melting, forming, and finishing operations.
The crystal clarity standards necessitate high-temperature processing and precision cutting operations that consume substantial energy while generating crystal waste requiring specialized disposal methods.
The integration of crystal components with other interior materials creates assembly complexity that increases manufacturing time and energy consumption.
Advanced technology integration throughout the Maybach cabin compounds environmental impact through rare earth element requirements and sophisticated electronic component manufacturing.
The multiple high-resolution displays, advanced audio systems, and electronic control modules utilize rare earth elements requiring intensive mining operations with significant environmental impact.
The semiconductor manufacturing processes consume substantial energy while utilizing toxic chemicals requiring specialized treatment and disposal methods.
Handcraftsmanship throughout the Maybach interior, while representing exceptional artisanal skill, increases manufacturing time and energy consumption compared to automated production processes.
The individual attention to detail and custom finishing operations extend production timelines while requiring specialized facility environments with controlled temperature and humidity conditions.
The quality control standards necessitate extensive inspection and potential rework operations that multiply material and energy consumption. The global sourcing requirements for Maybach premium materials create additional environmental burden through international transportation and logistics complexity.
The rare materials often originate from multiple continents with complex shipping requirements and careful handling protocols. The quality control standards necessitate extensive packaging and environmental protection during transportation, increasing shipping volumes and associated emissions.
Customization options available for Maybach customers multiply manufacturing complexity and environmental impact through flexible production requirements and extended material inventories.
The bespoke interior options require maintaining extensive material selections and specialized manufacturing capabilities that increase facility environmental impact.
The individual customer specifications necessitate unique material combinations and processing requirements that prevent manufacturing optimization and increase waste generation.
End-of-life considerations for Maybach interior materials present significant challenges due to material complexity, chemical treatments, and integrated construction methods.
The combination of treated leather, finished wood, precious metals, crystal components, and electronic systems creates recycling challenges that limit material recovery options.
The complex integration and chemical treatments may render certain materials unsuitable for recycling, necessitating disposal methods with associated environmental impact.
The Mercedes-Maybach S-Class exemplifies how ultra-luxury automotive standards can create substantial environmental impact through premium material selection, intensive processing, and complex manufacturing requirements, demonstrating the environmental costs associated with traditional luxury automotive approaches while highlighting opportunities for sustainable alternatives that could maintain luxury standards with reduced environmental impact.
4. Aston Martin DB11
The Aston Martin DB11 embodies the environmental challenges inherent in traditional British luxury sports car manufacturing, combining handcrafted interior excellence with material selections that prioritize immediate luxury experience over environmental considerations.
This grand touring sports car demonstrates how luxury sports car interiors can create substantial cabin carbon footprints through premium material usage, intensive handcraftsmanship, and complex manufacturing processes.
The DB11’s interior showcases the environmental costs associated with maintaining traditional luxury sports car standards while highlighting the tension between artisanal craftsmanship and environmental responsibility.
The extensive leather applications throughout the DB11’s cabin create significant environmental burden through both material quality requirements and processing intensity.
The Bridge of Weir leather utilized in Aston Martin applications undergoes intensive selection and treatment processes that ensure exceptional quality while generating substantial environmental impact.
The leather tanning processes utilize traditional methods that require extensive water consumption and chemical treatment including chromium-based tanning agents that create toxic waste streams.
The premium leather grades necessitate selective sourcing that increases waste ratios while requiring international transportation from specialized suppliers.
The leather processing for DB11 applications involves multiple stages of treatment that compound environmental impact through chemical usage and energy consumption.
The grain enhancement and texture development processes utilize mechanical and chemical treatments that consume significant energy while generating waste requiring specialized disposal methods.
The color matching processes require multiple dye applications and protective treatments that emit volatile organic compounds while necessitating controlled environmental conditions during application and curing.
Carbon fiber applications throughout the DB11 interior, while lightweight and structurally advanced, create substantial environmental impact through manufacturing intensity and energy requirements.
The carbon fiber production processes require high-temperature operations and energy-intensive manufacturing that consume significant electricity while generating volatile organic compounds during resin curing processes.
The precision weaving and laying processes require specialized facilities with controlled environmental conditions that increase energy consumption throughout manufacturing operations.
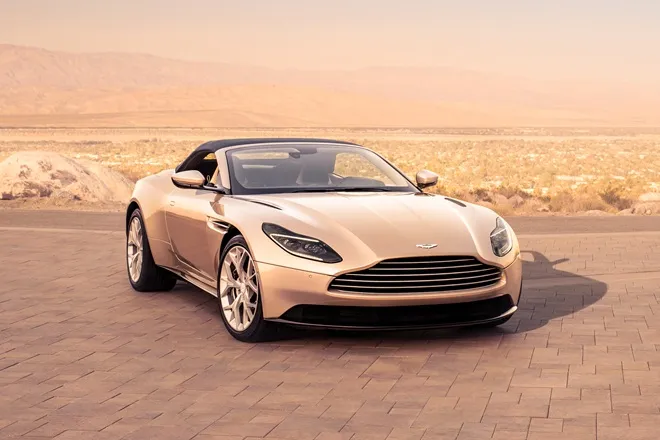
Alcantara applications throughout the DB11 cabin, while providing exceptional tactile qualities, utilize synthetic manufacturing processes that create environmental impact through chemical usage and energy consumption.
The microfiber production requires intensive chemical processing and mechanical operations that consume significant energy while generating waste streams requiring specialized treatment.
The premium grades required for luxury automotive applications necessitate additional processing stages that multiply environmental burden compared to standard synthetic material applications.
Metal trim components throughout the DB11 utilize premium alloys and finishing processes that require intensive mining, refining, and manufacturing operations.
The anodized aluminum and brushed metal trim applications require electrochemical processing that utilizes toxic chemicals while generating hazardous waste streams.
The precision machining and hand-finishing operations consume significant energy while generating metal waste requiring specialized recycling processes to recover valuable materials.
Advanced technology integration throughout the DB11 cabin compounds environmental impact through rare earth element requirements and sophisticated electronic component manufacturing.
The infotainment systems, digital instrument clusters, and electronic control modules utilize rare earth elements requiring intensive mining operations with significant environmental disruption.
The semiconductor manufacturing processes consume substantial energy while utilizing toxic chemicals requiring specialized treatment and disposal methods.
Handcraftsmanship throughout the DB11 interior increases manufacturing time and energy consumption compared to automated production processes while representing exceptional artisanal skill and attention to detail.
The individual assembly and finishing operations extend production timelines while requiring specialized facility environments with controlled conditions. The quality control standards necessitate extensive inspection and potential refinishing operations that multiply material and energy consumption throughout the manufacturing process.
The global sourcing requirements for DB11 premium materials create additional environmental burden through international transportation and complex logistics operations.
The specialized materials often originate from multiple continents with specific quality requirements necessitating careful handling and environmental protection during shipping. The small production volumes prevent transportation optimization while increasing per-unit shipping emissions and associated environmental impact.
Customization options available for DB11 customers multiply manufacturing complexity and environmental impact through bespoke interior specifications and extended material inventories.
The Q by Aston Martin customization program requires maintaining extensive material selections and specialized manufacturing capabilities that increase facility environmental impact.
The individual customer specifications necessitate unique material combinations and processing requirements that prevent manufacturing standardization and increase waste generation.
Paint and finishing processes throughout the DB11 interior components utilize multiple coating applications and protective treatments that emit volatile organic compounds while requiring energy-intensive curing operations.
The premium finish standards necessitate multiple application stages with intermediate sanding and preparation operations that consume additional energy while generating particulate waste requiring air filtration systems.
End-of-life considerations for DB11 interior materials present challenges due to material complexity, chemical treatments, and integrated construction methods.
The combination of treated leather, carbon fiber, Alcantara, and metal components creates recycling difficulties that limit material recovery options.
The carbon fiber components require specialized recycling processes that are energy-intensive and not widely available, while chemical treatments in leather and synthetic materials may render certain components unsuitable for standard recycling processes.
The Aston Martin DB11 demonstrates how luxury sports car interior design creates substantial environmental impact through premium material selection, intensive handcraftsmanship, and complex manufacturing requirements, representing traditional luxury automotive approaches that prioritize immediate sensory experience over environmental considerations while highlighting opportunities for sustainable alternatives that could maintain luxury sports car standards with reduced environmental impact.
5. Rolls-Royce Phantom
The Rolls-Royce Phantom represents the absolute pinnacle of automotive luxury craftsmanship, embodying an approach to interior materials that creates perhaps the highest cabin carbon footprint in the automotive industry.
This ultra-luxury sedan showcases the extreme environmental costs associated with the most uncompromising standards of automotive interior refinement, utilizing the rarest materials, most intensive handcraftsmanship, and most complex manufacturing processes available in automotive production.
The Phantom demonstrates how traditional luxury automotive excellence can result in extraordinary environmental impact through resource consumption and processing intensity.
The leather applications throughout the Phantom’s interior create unprecedented environmental burden through both material quality requirements and processing complexity.
The cabin utilizes the finest leather available globally, sourced from carefully selected hides that meet impossibly high standards for grain consistency, natural markings, and tactile properties.
The leather selection process results in extremely high waste ratios as only a tiny percentage of available hides meet Rolls-Royce quality standards.
The multi-stage tanning processes utilize traditional methods that require extensive water consumption and chemical treatment including chromium-based agents that create significant toxic waste streams.
The leather processing for Phantom applications involves numerous stages of chemical and mechanical treatment that multiply environmental impact through resource consumption and waste generation.
The grain pattern enhancement and texture development processes require specialized equipment and controlled environmental conditions that consume substantial energy throughout processing operations.
The color matching processes demand perfect consistency across large material quantities, necessitating multiple dye applications and protective treatments that emit significant volatile organic compounds while requiring specialized ventilation and waste treatment systems.
Wood veneer applications throughout the Phantom’s cabin utilize the rarest timber species available, often sourced from trees that have grown for centuries in environmentally sensitive regions.
The finishing processes involve numerous lacquer applications, hand-sanding operations, and polishing stages that consume significant energy while emitting volatile organic compounds requiring specialized environmental controls.

The Gallery feature unique to Phantom models allows customers to incorporate art pieces, precious materials, and custom elements that can include rare metals, precious stones, and exotic materials requiring intensive extraction and processing operations.
These bespoke elements often necessitate unique manufacturing processes and specialized assembly techniques that increase environmental impact through energy consumption and waste generation. The individual nature of Gallery creations prevents manufacturing optimization while requiring extensive quality control and potential rework operations.
Precious metal applications throughout the Phantom interior utilize the finest available materials including gold, silver, and platinum accents that require intensive mining operations with significant environmental disruption.
The electroplating and hand-finishing processes utilize toxic chemicals including cyanides and heavy metals that create hazardous waste streams requiring specialized treatment facilities.
The precision machining and individual hand-finishing operations consume extraordinary energy while generating precious metal waste, requiring complex recovery processes.
Crystal and glass applications throughout the Phantom cabin include custom-manufactured components that require high-temperature processing and precision cutting operations, consuming substantial energy during manufacturing.
The optical clarity standards necessitate specialized glass formulations and processing techniques that increase energy consumption while generating glass waste, requiring specialized disposal methods.
The integration of crystal elements with other premium materials creates assembly complexity that increases manufacturing time and energy consumption.
Spirit of Ecstasy motorized mascot and other mechanical luxury features throughout the Phantom require precision manufacturing and complex assembly operations that consume significant energy while utilizing rare earth elements and specialized alloys.
The motorized components require sophisticated electronic control systems that multiply material requirements while necessitating complex assembly and testing procedures that extend manufacturing timelines and energy consumption.
Handcraftsmanship throughout the Phantom interior represents the pinnacle of automotive artisanal skill while creating substantial environmental impact through extended manufacturing time and energy consumption. Individual craftsmen spend hundreds of hours on each Phantom interior, requiring specialized facility environments with precise temperature and humidity control.
The quality control standards demand perfection at every stage, necessitating extensive inspection and potential rework operations that multiply material and energy consumption throughout the manufacturing process.
The global sourcing requirements for Phantom materials create extraordinary environmental burden through international transportation and complex logistics operations.
The rarest materials often originate from remote locations worldwide with extremely limited availability, necessitating complex shipping arrangements and careful environmental protection during transportation. The individual nature of many Phantom components prevents transportation optimization while increasing per-unit shipping emissions and associated environmental impact.
Bespoke customization capabilities for Phantom customers multiply manufacturing complexity and environmental impact through unlimited interior specifications and comprehensive material inventories.
The Rolls-Royce Bespoke program maintains extensive collections of rare materials and specialized manufacturing capabilities that increase facility environmental impact.
Individual customer specifications often require unique material sourcing and processing requirements that prevent any manufacturing standardization while increasing waste generation and energy consumption.
Climate control and comfort systems throughout the Phantom’s spacious cabin require extensive material applications and complex mechanical systems that compound environmental impact.
The multi-zone climate control, advanced seating systems, and luxury comfort features necessitate sophisticated electronic and mechanical components that increase material requirements while requiring complex assembly and testing procedures.
End-of-life considerations for Phantom interior materials present extraordinary challenges due to material rarity, complex chemical treatments, and integrated construction methods.
The combination of the finest leather, rare wood species, precious metals, crystal components, and sophisticated electronic systems creates recycling challenges that severely limit material recovery options.
Many materials may be too rare or chemically treated to permit standard recycling processes, potentially necessitating disposal methods with significant environmental impact.
The Rolls-Royce Phantom exemplifies how ultra-luxury automotive standards can create an extraordinary environmental impact through the selection of the rarest materials, most intensive processing, and most complex manufacturing requirements available in automotive production.
This vehicle demonstrates the extreme environmental costs associated with traditional luxury automotive approaches while representing the ultimate challenge for developing sustainable alternatives that could maintain such exceptional luxury standards with reduced environmental impact.
Also Read: 5 EVs with the Best Charging Port Locations and 5 with the Most Awkward