The truck bed lighting landscape has undergone a revolutionary transformation in recent years, fundamentally changing how truck owners approach cargo visibility and safety.
Modern LED technology has evolved from basic aftermarket accessories to sophisticated lighting systems that rival factory installations in both performance and aesthetics.
Aim for white lights in the 5000-6000K range; it’s like having the sun on a dimmer switch, minus the sunburn. This temperature range provides optimal visibility without causing eye strain or creating harsh shadows that can obscure important details when loading or unloading cargo.
The importance of proper truck bed illumination extends far beyond mere convenience. Poor lighting in cargo areas contributes to workplace injuries, damaged equipment, and inefficient operations across industries.
Whether you’re a contractor loading tools at dawn, a weekend warrior packing camping gear after sunset, or a commercial fleet operator maximizing productivity during extended shifts, adequate lighting directly impacts safety and functionality.
Dim lighting Dirt and wear can reduce brightness. This highlights one of the critical issues facing truck owners who rely on inadequate or aging lighting systems.
Contemporary LED bed lighting systems offer unprecedented versatility, with options ranging from simple strip installations to comprehensive integrated systems featuring multiple brightness levels, color temperature adjustment, and smartphone connectivity.
The market now includes universal solutions that adapt to any truck make and model, as well as vehicle-specific kits designed to integrate seamlessly with factory wiring harnesses and control systems.
Advanced installations can include motion sensors, automatic dimming, and zone-specific controls that allow users to illuminate specific sections of the truck bed based on their immediate needs. The contrast between high-performance LED systems and inadequate lighting solutions has never been more pronounced.
While premium LED installations can transform a truck bed into a well-lit workspace rivaling professional garages, poor lighting systems leave users struggling with shadows, uneven illumination, and insufficient brightness for detailed work. Understanding these differences is crucial for making informed decisions about lighting upgrades that will serve users reliably for years to come.
5 Trucks with Outstanding LED Bed Lighting
These exceptionally illuminated vehicles feature comprehensive LED lighting arrays and precision-positioned light clusters that deliver brilliant cargo area visibility through years of reliable operation across demanding work environments and challenging weather conditions.
Their thoughtful engineering includes multiple light zones, weather-sealed housings, and intelligent switching systems that resist the performance degradation typically created by vibration stress or moisture infiltration during heavy-duty usage cycles.
From detailed equipment loading that requires precise visibility to late-night cargo organization where accurate illumination matters, these remarkable lighting systems continue providing daylight-quality brightness without developing LED failure or dimming issues over extended service life.
Owners report enhanced productivity with these superior illumination solutions a work-enhancing quality feature that proves its worth through improved safety and operational efficiency throughout commercial and recreational hauling applications.
1. Ford F-150 with Premium LED Integration Systems
The Ford F-150 has established itself as the undisputed leader in factory and aftermarket LED bed lighting solutions, setting industry standards that competitors struggle to match.
Our Premium F-150 LED bed light kits are custom designed for your 2024+ F-150. With over 100 LEDs packed into each kit, you’ll never have another unsure step or trouble loading/unloading your cargo.
This extensive LED count represents a quantum leap over traditional incandescent systems, providing uniform illumination that eliminates the shadows and dark spots that plague inferior lighting setups.
The F-150’s lighting ecosystem encompasses multiple tiers of sophistication, from basic factory installations to premium aftermarket systems that transform the truck bed into a professional workspace.
The Starkey Bed Lighting Kit adds a premium OEM-Style cargo box lighting system to your F-150 in minutes! This system gives you the quality that is normally only found from the factory, while providing an easy to install system.
These OEM-style installations maintain the truck’s warranty coverage while delivering performance that exceeds factory specifications. What sets the F-150 apart is its comprehensive approach to bed lighting integration.
The truck’s electrical architecture is designed to accommodate advanced lighting systems without requiring extensive modifications to the vehicle’s wiring harness.

This thoughtful engineering allows for seamless integration of aftermarket systems that can be controlled through the truck’s infotainment system, smartphone apps, or traditional manual switches.
The result is a lighting system that feels like a natural extension of the truck’s capabilities rather than an obvious aftermarket addition. The Ford F-150’s LED bed lighting systems also excel in durability and weather resistance.
These installations are designed to withstand the harsh conditions that define truck ownership, from construction sites covered in dust and debris to outdoor adventures involving water, mud, and extreme temperatures.
The LED technology used in premium F-150 installations maintains consistent performance across temperature ranges that would cause traditional lighting systems to fail or provide inadequate illumination.
Advanced F-150 LED systems often include multiple brightness levels and color temperature options, allowing users to adjust the lighting to match specific tasks and environmental conditions.
Whether loading delicate equipment that requires soft, even lighting or unloading heavy machinery that demands maximum visibility, these systems provide the flexibility needed for diverse applications.
The integration with the truck’s existing controls means users can adjust lighting settings without taking their hands off their work or struggling with separate control devices.
2. Chevrolet Silverado with Advanced Strip Lighting Technology
The Chevrolet Silverado has carved out a distinctive niche in the LED bed lighting market through its emphasis on strip lighting technology that provides comprehensive coverage across the entire cargo area.
Unlike point-source lighting systems that create hotspots and shadows, the Silverado’s approach to LED integration focuses on continuous illumination that adapts to different cargo configurations and loading scenarios.
This philosophy has resulted in lighting systems that perform exceptionally well in real-world applications where uniform visibility is paramount. Silverado LED installations typically feature high-density strip lighting that runs along the bed rails, tailgate, and strategic interior positions to create overlapping coverage zones.
This design eliminates the common problem of shadows cast by tall cargo items, ensuring that users can see into corners and recesses that remain dark with traditional lighting approaches.
The strips themselves utilize cutting-edge LED technology that provides exceptional color rendering, making it easier to distinguish between similar-looking items and identify potential hazards or damage during loading and unloading operations.
The Silverado’s electrical system is engineered to support sophisticated lighting installations without compromising the truck’s other electrical systems.

This robust foundation allows for the integration of smart lighting controls that can automatically adjust brightness based on ambient light conditions, time of day, or user preferences.
Some installations include proximity sensors that activate the lighting system when movement is detected near the tailgate, providing hands-free operation that’s particularly valuable when carrying heavy or awkward cargo.
Durability represents another key strength of Silverado LED bed lighting systems. The truck’s design philosophy emphasizes rugged reliability, and this extends to the lighting installations that are built to withstand years of heavy use in demanding environments.
The LED strips are typically housed in protective channels that shield them from impact damage while allowing for easy cleaning and maintenance.
This protection is crucial for maintaining optimal light output over the system’s operational life, as dust, dirt, and debris can significantly reduce illumination effectiveness.
The Silverado’s approach to LED bed lighting also emphasizes energy efficiency, with systems designed to provide maximum illumination while minimizing draw on the truck’s electrical system.
This efficiency is particularly important for users who need to operate the lighting system for extended periods or in situations where the engine isn’t running.
Advanced installations often include intelligent power management that automatically dims or shuts off the lighting system to preserve battery power while still providing adequate illumination for safety and visibility.
3. Ram 1500 with Multi-Zone LED Configuration
The Ram 1500 has distinguished itself in the competitive truck bed lighting market through its innovative multi-zone LED configuration that treats the cargo area as a series of distinct lighting zones rather than a single space requiring uniform illumination.
This approach recognizes that different areas of the truck bed serve different purposes and may require different types of lighting depending on the specific task being performed. The result is a highly flexible system that can be customized to match individual user preferences and work requirements.
Ram’s multi-zone approach typically divides the truck bed into several distinct areas: the front bulkhead zone, left and right side zones, tailgate area, and corners that traditionally remain poorly lit with conventional systems.
Each zone can be controlled independently, allowing users to illuminate only the areas they’re actively using while conserving power and reducing unnecessary glare.
This selective illumination is particularly valuable for users who frequently work with mixed cargo loads or need to access specific items without disturbing the entire truck bed contents.
The LED technology used in Ram 1500 installations emphasizes high color rendering index (CRI) values that make it easier to distinguish between similar colors and identify details that might be obscured by poor-quality lighting.

This attention to color accuracy is particularly important for professionals who need to quickly identify specific tools, parts, or materials in low-light conditions.
The high CRI also reduces eye strain during extended work sessions, making the lighting system more comfortable for prolonged use. Ram’s electrical integration for LED bed lighting systems is designed with future expansion in mind.
The wiring harnesses and control modules can accommodate additional lighting zones or upgraded components without requiring complete system replacement.
This modular approach allows users to start with a basic installation and add features over time as their needs evolve or as new technology becomes available.
The system’s architecture also supports integration with aftermarket accessories like bed covers, toolboxes, and cargo management systems. The Ram 1500’s LED bed lighting systems excel in harsh weather conditions, with weatherproofing that goes beyond basic water resistance to include protection against dust, debris, and temperature extremes.
The lighting components are designed to maintain consistent performance whether the truck is being used in desert conditions with extreme heat and dust or in winter environments with freezing temperatures and road salt.
This reliability is crucial for users who depend on their trucks for professional applications where lighting failure could compromise safety or productivity.
4. GMC Sierra with Intelligent Lighting Control
The GMC Sierra has established a reputation for sophisticated, intelligent lighting control systems that go beyond simple on/off functionality to provide adaptive illumination that responds to changing conditions and user requirements.
A malfunctioning control unit can cause this issue. Try resetting the system or checking for software updates. This advanced approach to lighting control reflects GMC’s commitment to integrating smart technology throughout their vehicle lineup, creating systems that learn from user behavior and optimize performance accordingly.
The Sierra’s intelligent lighting control typically includes automatic brightness adjustment based on ambient light conditions, ensuring optimal visibility without creating excessive glare or battery drain.
The system uses sensors to monitor external lighting conditions and adjusts the LED output to provide consistent visibility regardless of whether the truck is being used in broad daylight, at dusk, or in complete darkness.
This automatic adjustment eliminates the need for manual brightness control while ensuring that the lighting system always provides appropriate illumination for current conditions. Advanced Sierra installations often include programmable lighting scenes that can be customized for specific tasks or user preferences.

For example, users might program a “loading” scene that provides maximum illumination across all zones, a “maintenance” scene that focuses light on specific areas while dimming others, or an “evening” scene that provides gentle illumination for casual use without disturbing nearby activities.
These programmable scenes can be activated through the truck’s infotainment system, dedicated control panels, or smartphone applications. The Sierra’s LED bed lighting systems also feature advanced diagnostic capabilities that monitor system performance and alert users to potential issues before they result in lighting failure.
This predictive maintenance approach can identify problems like failing LED modules, loose connections, or deteriorating wiring before they compromise system performance.
The diagnostic system can also track usage patterns and suggest maintenance schedules based on actual operating conditions rather than arbitrary time intervals.
Energy management represents another key strength of the Sierra’s intelligent lighting control system. The truck can monitor battery voltage and automatically adjust lighting output or shut down non-essential lighting zones to preserve starting power.
This intelligent power management is particularly valuable for users who frequently operate the lighting system with the engine off or who use their trucks in remote locations where battery failure could create serious problems. The system can also integrate with the truck’s charging system to optimize LED performance when the alternator is providing power.
Also Read: 5 Hybrids With Most Engine-Off Coasting and 5 With Engine Noise
5. Toyota Tundra with High-Efficiency LED Arrays
The Toyota Tundra has earned recognition for its high-efficiency LED arrays that maximize illumination while minimizing power consumption, reflecting Toyota’s broader commitment to efficiency and reliability across its vehicle lineup.
The Tundra’s approach to LED bed lighting emphasizes long-term durability and consistent performance, with systems designed to maintain optimal light output over extended operational periods without requiring frequent maintenance or component replacement.
Tundra LED installations typically feature high-density arrays that pack maximum LED count into compact housings, providing exceptional light output from relatively small fixtures.
This efficient use of space is particularly important for truck bed applications where mounting space may be limited by cargo requirements, bed covers, or other accessories.
The compact nature of these LED arrays also reduces their visual impact, maintaining the truck’s clean appearance while providing professional-grade illumination.
The efficiency of Tundra LED systems extends beyond simple power consumption to include thermal management that ensures consistent performance even during extended operation periods.

The LED arrays incorporate advanced heat dissipation technology that prevents thermal buildup that could reduce light output or shorten component life.
This thermal management is particularly important for users who operate their lighting systems for hours at a time or in high-temperature environments where heat buildup could compromise performance.
Toyota’s approach to LED bed lighting integration emphasizes reliability and simplicity, with control systems that provide advanced functionality without unnecessary complexity.
The lighting controls are designed to be intuitive and reliable, with failsafe mechanisms that ensure basic lighting functionality even if advanced features experience problems.
This philosophy reflects Toyota’s understanding that truck owners need lighting systems they can depend on in critical situations, regardless of environmental conditions or operating circumstances.
The Tundra’s LED bed lighting systems also excel in compatibility with aftermarket accessories and modifications. The electrical system is designed to accommodate additional lighting zones, upgraded components, or integration with other electrical accessories without compromising system reliability.
This flexibility is particularly valuable for users who customize their trucks for specific applications or who need to integrate lighting systems with specialized equipment or cargo management systems.
5 Trucks with Problematic Dim Bed Lighting
These poorly illuminated vehicles struggle with inadequate cargo area lighting due to insufficient LED output and poorly designed light placement that fails to provide adequate visibility for safe loading, unloading, and cargo organization during low-light working conditions.
Their problematic engineering includes limited light distribution, basic housing designs, and minimal LED clusters that amplify the visibility challenges typically associated with large truck bed dimensions and equipment shadows.
From struggling to locate tools during evening work sessions to safety concerns while handling cargo in darkness, these lighting systems demand supplemental illumination sources and careful positioning strategies.
Owners discover that while these trucks offer solid hauling capabilities, their bed lighting requires aftermarket upgrades and additional portable lighting solutions to achieve acceptable visibility levels for safe and efficient cargo handling operations.
1. Older Ford F-150 Models with Incandescent Systems
Older Ford F-150 models equipped with factory incandescent bed lighting represent one of the most common examples of inadequate cargo illumination in the truck market.
These systems, typically found in trucks manufactured before the widespread adoption of LED technology, suffer from multiple fundamental limitations that compromise their effectiveness in real-world applications.
The incandescent bulbs used in these installations produce significantly less light output per watt consumed compared to modern LED alternatives, resulting in dim, yellowish illumination that fails to provide adequate visibility for detailed work or safe cargo handling.
The primary issue with older F-150 incandescent bed lighting stems from the inherent inefficiency of incandescent technology itself. These bulbs convert most of their electrical energy into heat rather than light, resulting in poor illumination that becomes even worse as the bulbs age and their filaments deteriorate.
The warm color temperature of incandescent bulbs, typically around 2700K, creates a yellowish cast that makes it difficult to distinguish colors accurately and can cause eye strain during extended use. This poor color rendering is particularly problematic for professionals who need to identify specific tools, parts, or materials quickly and accurately.
Heat generation represents another significant problem with older F-150 incandescent bed lighting systems. The excessive heat produced by these bulbs can create safety hazards when working with flammable materials or in confined spaces.

The heat also accelerates the deterioration of nearby plastic components, including light housings, wiring insulation, and bed liner materials. This thermal stress contributes to premature system failure and increases maintenance requirements, as bulbs burn out more frequently and components degrade faster than they would with cooler-operating LED alternatives.
The electrical load imposed by incandescent bed lighting systems also creates practical problems for older F-150 owners. These systems draw significantly more current than LED alternatives, which can strain the truck’s electrical system and drain the battery more quickly when operated with the engine off.
This increased electrical demand is particularly problematic for users who need to operate the lighting system for extended periods or who have added other electrical accessories that compete for available power.
The higher current draw also increases the risk of voltage drops that can further reduce light output and compromise system reliability. Durability issues plague older F-150 incandescent bed lighting systems, with bulbs that are vulnerable to shock and vibration damage from normal truck operation.
The filaments in incandescent bulbs are particularly susceptible to failure when subjected to the constant jarring and bouncing that characterizes truck use, especially in off-road or construction environments.
This vulnerability to mechanical stress means that bulbs may fail unexpectedly, leaving users without adequate lighting when they need it most. The frequent bulb replacement requirements also increase the total cost of ownership and create inconvenience for users who depend on reliable cargo lighting.
2. Early Chevrolet Silverado Single-Point Lighting
Early Chevrolet Silverado models equipped with single-point lighting systems exemplify the limitations of centralized illumination approaches that fail to provide adequate coverage across the entire truck bed area.
These systems typically rely on one or two centrally-mounted fixtures that create significant shadows and uneven lighting distribution, making it difficult to see into corners, behind tall cargo items, or near the tailgate where much loading and unloading activity occurs.
The single-point approach represents a fundamental design flaw that cannot be adequately addressed through simple bulb upgrades or minor modifications.
The shadow problems created by Silverado single-point lighting systems are particularly pronounced when working with tall or bulky cargo items that block light from reaching other areas of the truck bed.
Tools, equipment boxes, lumber, and other common cargo items create large shadow zones that remain virtually invisible even when the lighting system is operating at full output.
These shadows create safety hazards as users may trip over unseen objects, mishandle cargo due to poor visibility, or fail to notice damage or hazards that could affect loading decisions.
Uneven light distribution represents another critical limitation of early Silverado single-point systems. The areas directly beneath the light fixtures may be adequately illuminated, but light intensity drops off rapidly with distance, creating rings of progressively dimmer illumination that make it difficult to maintain consistent visibility across the work area.
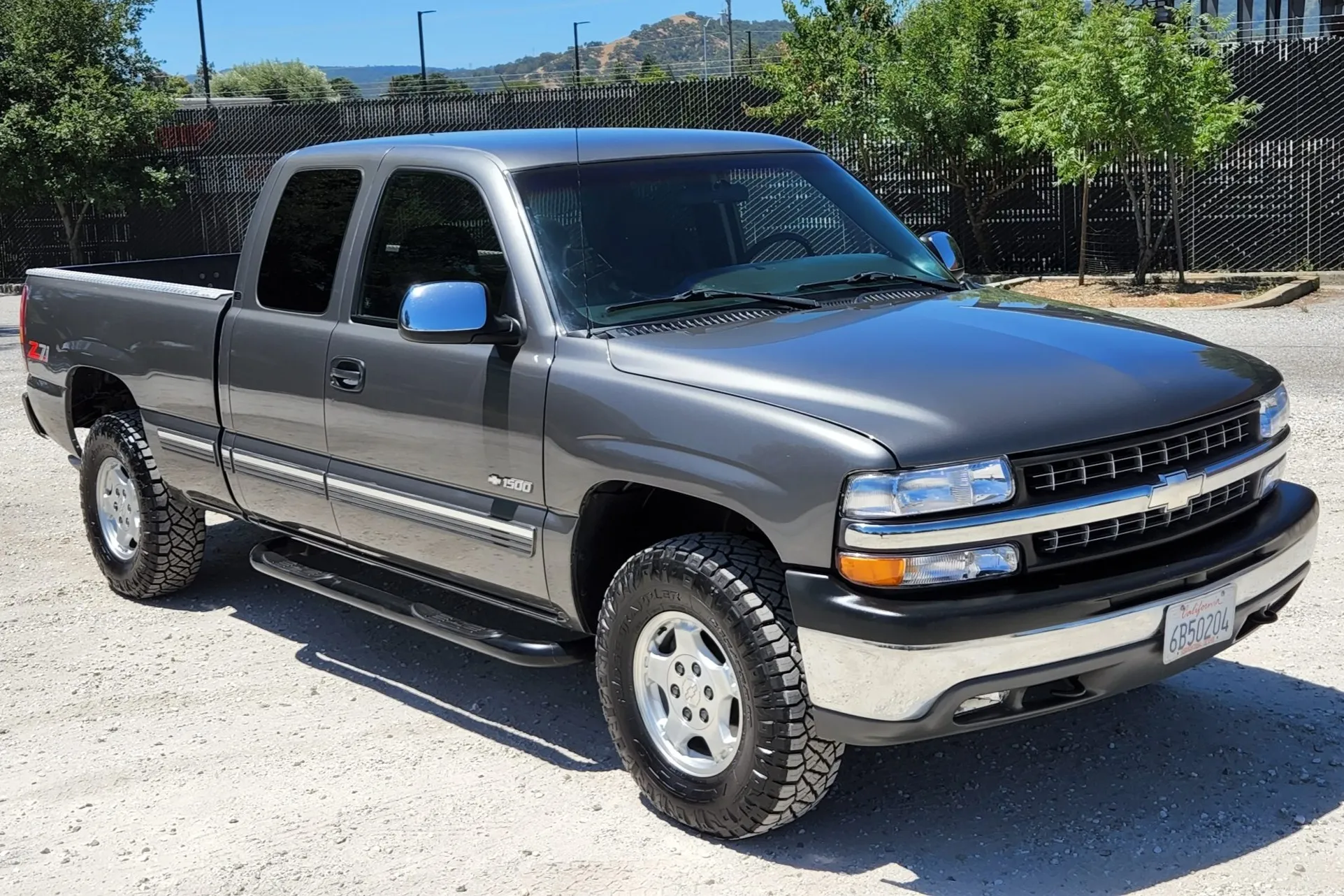
This uneven distribution forces users to constantly reposition themselves or their cargo to maintain adequate visibility, reducing efficiency and increasing the risk of accidents or mistakes.
The mounting position of single-point lighting systems in early Silverado models often compounds these distribution problems by placing the light source in locations that are easily blocked by users’ bodies or by cargo handling equipment.
When users position themselves between the light source and their work area, they create shadows that eliminate illumination precisely where it’s needed most. This self-shadowing effect is particularly problematic when loading or unloading heavy items that require careful positioning and handling.
Maintenance access represents an additional challenge with early Silverado single-point lighting systems. The centralized mounting positions often place light fixtures in locations that are difficult to reach for bulb replacement or cleaning, requiring users to climb into the truck bed or use ladders to access the lighting components.
This difficulty in maintenance access often results in deferred maintenance that allows performance to degrade gradually as bulbs dim with age or fixtures accumulate dirt and debris that reduce light output.
The resulting poor illumination may develop so gradually that users don’t realize how compromised their lighting has become until they experience a complete failure or compare their system to a properly functioning installation.
3. Dodge Ram with Inadequate Electrical Supply
Dodge Ram trucks from certain model years suffer from electrical supply limitations that prevent bed lighting systems from operating at their full potential, creating dim and unreliable illumination that fails to meet user needs.
These electrical supply problems typically manifest as voltage drops under load, insufficient current capacity for proper LED operation, or poor electrical connections that introduce resistance and reduce system performance.
The result is lighting that may appear to function normally but provides inadequate illumination for safe and efficient cargo handling. Voltage drop issues in Dodge Ram electrical systems can cause LED bed lighting to operate at reduced brightness even when the control systems indicate normal operation.
Faulty wiring or a malfunctioning alternator may cause your vehicle’s headlights to appear dim. This principle applies equally to bed lighting systems, where electrical problems can cause significant performance degradation.
When voltage drops below the optimal operating range for LED systems, the lights may still illuminate but will produce significantly less light output, creating the appearance of dim or failing bulbs when the actual problem lies in the electrical supply system.
Insufficient current capacity represents another common problem with Dodge Ram bed lighting installations. Some truck configurations may have electrical systems that are marginal for supporting high-performance LED installations, particularly when other electrical accessories are operating simultaneously.
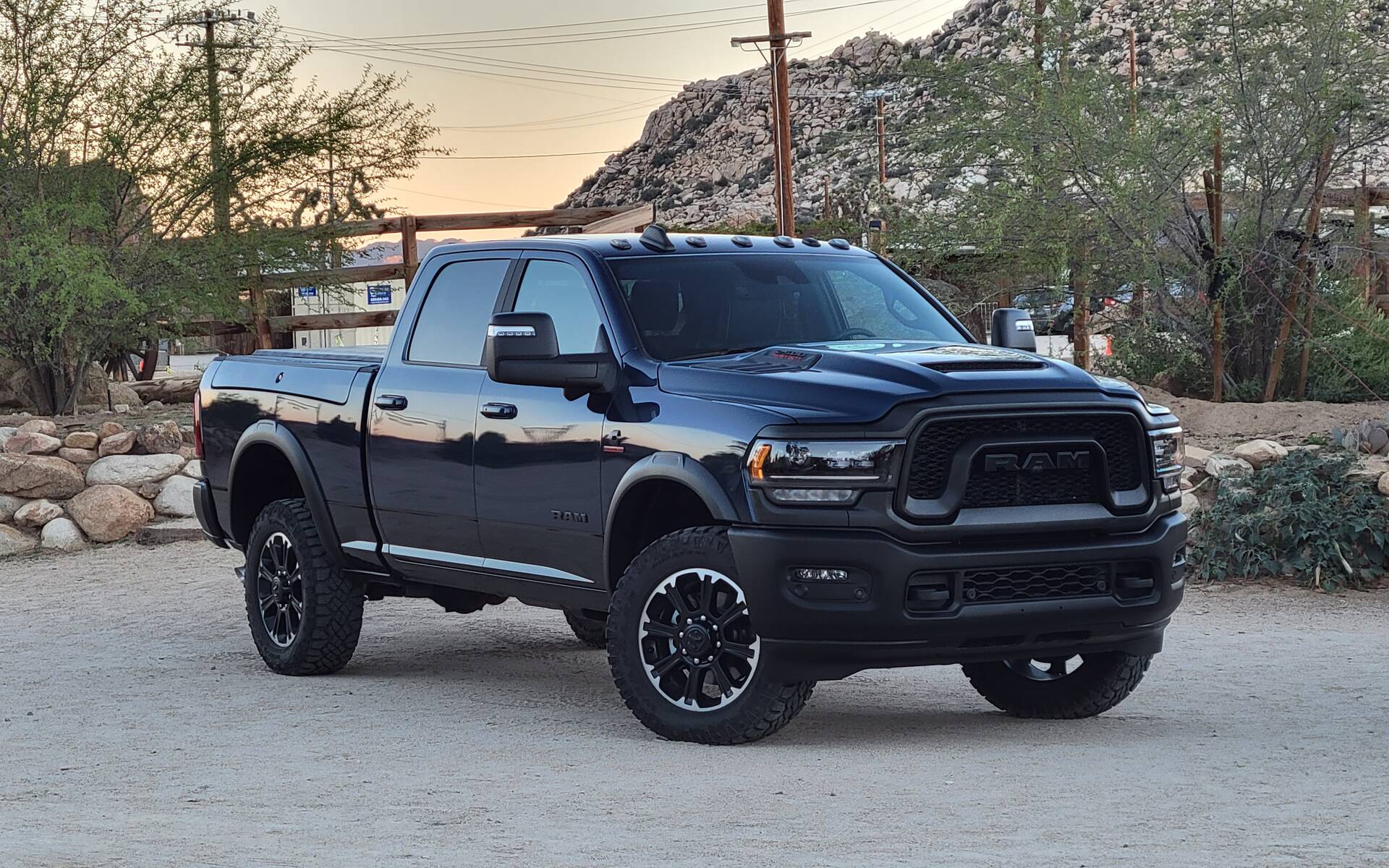
This current limitation can cause LED systems to operate in reduced-power modes or to cycle on and off unpredictably, creating inconsistent illumination that makes it difficult to complete tasks safely and efficiently.
Poor electrical connections plague many Dodge Ram bed lighting installations, particularly in trucks that have been exposed to harsh environmental conditions or that have been modified with aftermarket accessories.
Corrosion, loose connections, and damaged wiring can introduce electrical resistance that reduces voltage and current delivery to the lighting system.
These connection problems often develop gradually, causing a slow degradation in lighting performance that may not be immediately obvious but significantly compromises system effectiveness over time.
The complexity of modern Dodge Ram electrical systems can also create integration challenges for aftermarket bed lighting installations. The truck’s computer-controlled electrical systems may not properly recognize or support aftermarket lighting components, leading to compatibility issues that prevent optimal system operation.
These integration problems can cause LED systems to operate in failsafe modes that provide reduced light output, or they may prevent certain features like automatic dimming or remote control from functioning properly.
Ground loop problems represent another electrical issue that can affect Dodge Ram bed lighting performance. Poor grounding connections can cause voltage instabilities that affect LED operation, creating flickering, dimming, or inconsistent light output.
These grounding issues are often difficult to diagnose and may require extensive electrical troubleshooting to identify and resolve, making them particularly frustrating for users who expect reliable lighting performance from their truck’s electrical system.
4. Nissan Titan with Poor Light Distribution
The Nissan Titan’s factory bed lighting system suffers from fundamental design flaws in light distribution that create uneven illumination patterns and leave significant portions of the cargo area poorly lit.
These distribution problems stem from fixture placement decisions that prioritize ease of installation over optimal lighting performance, resulting in systems that provide adequate illumination in some areas while leaving others in relative darkness.
The poor distribution characteristics make it difficult to achieve consistent visibility across the truck bed, forcing users to work around the lighting system’s limitations rather than benefiting from truly effective illumination.
Hot spots and dark zones characterize the Nissan Titan’s problematic light distribution, with areas of excessive brightness directly beneath light fixtures contrasted by dimly lit zones that receive little or no direct illumination.
This uneven distribution creates visual adaptation problems for users, as their eyes struggle to adjust between bright and dark areas, potentially causing temporary vision problems that increase the risk of accidents or mistakes.
The contrast between illuminated and shadowed areas can also make it difficult to judge distances accurately or identify potential hazards that may be partially obscured by shadows.
The fixture mounting positions in Nissan Titan bed lighting systems often create interference problems with common cargo items and accessories.
Light fixtures mounted in positions that seemed logical during the design phase may be easily blocked by toolboxes, bed extenders, cargo nets, or other accessories that Titan owners commonly install.

This interference problem is compounded by the limited number of fixtures in the factory system, which means that blocking even one light source can significantly compromise illumination in large areas of the truck bed.
Reflector design problems contribute to the Nissan Titan’s poor light distribution characteristics. The reflectors and lens systems used in factory installations may not be optimized for truck bed applications, failing to spread light evenly across the work area or directing too much light upward where it serves no useful purpose.
Poor reflector design can also create glare problems that make it difficult for users to see clearly when positioning themselves at certain angles relative to the light fixtures.
The color temperature and quality of light produced by Nissan Titan bed lighting systems may also contribute to distribution problems by providing illumination that makes it difficult to distinguish details or identify colors accurately.
Poor color rendering can make evenly distributed light appear dim or inadequate because users cannot easily distinguish between similar-looking objects or identify important visual cues that would be apparent under higher-quality illumination.
This problem is particularly pronounced when working with materials or equipment that rely on color coding for identification or safety purposes.
Maintenance issues compound the Nissan Titan’s light distribution problems by making it difficult to keep the system operating at peak performance.
Fixtures that are difficult to access for cleaning may accumulate dirt, dust, or debris that further reduces light output and worsens distribution characteristics.
Poor maintenance access can also delay bulb replacement, allowing failing bulbs to operate at reduced output for extended periods and creating additional distribution problems as different fixtures operate at different brightness levels.
5. GMC Sierra with Failing Control Systems
GMC Sierra trucks equipped with electronic lighting control systems face unique challenges when these control systems begin to malfunction, creating unpredictable and inadequate bed lighting performance that can leave users without reliable illumination when they need it most.
A malfunctioning control unit can cause this issue. Try resetting the system or checking for software updates. These control system failures can manifest in various ways, from complete system shutdown to erratic operation that makes it impossible to depend on the lighting system for critical tasks.
Electronic control module failures represent one of the most serious problems affecting GMC Sierra bed lighting systems. When the control module malfunctions, it may fail to properly regulate power delivery to the LED fixtures, causing them to operate at reduced brightness or to cycle on and off unpredictably.
These module failures can be difficult to diagnose because they may occur intermittently, creating problems that appear and disappear without an obvious cause.
The electronic nature of these failures often requires specialized diagnostic equipment and expertise to identify and resolve, making repairs more complex and expensive than simple bulb replacements.
Sensor malfunctions can cause GMC Sierra automatic lighting systems to behave erratically, failing to activate when needed or remaining on when they should shut off.
Motion sensors, ambient light sensors, and door position sensors that are designed to provide convenient automatic operation may malfunction due to environmental contamination, electrical problems, or component aging.
When these sensors fail, users may find themselves without lighting when they expect it to activate automatically, or they may discover that the system has been operating unnecessarily and draining the battery.

Software conflicts and corruption can affect GMC Sierra lighting control systems, particularly in trucks equipped with integrated infotainment and vehicle management systems.
Software problems may prevent users from accessing lighting controls through the dashboard interface, cause lighting scenes to malfunction, or create conflicts between different electrical systems that prevent proper lighting operation.
These software issues may require dealer service or specialized programming equipment to resolve, making them particularly inconvenient for users who need immediate lighting system reliability.
Wiring harness problems specific to the control system can create intermittent faults that are difficult to reproduce and diagnose. The complex wiring required for electronic lighting control systems includes multiple data communication lines, power feeds, and sensor connections that can develop problems due to vibration, environmental exposure, or installation errors.
These wiring problems may cause the control system to operate unpredictably or to lose communication with individual lighting zones, resulting in partial system failures that leave portions of the truck bed inadequately illuminated.
Temperature sensitivity affects some GMC Sierra electronic lighting control systems, causing them to malfunction in extreme hot or cold conditions when reliable lighting is often most critically needed.
Electronic components may shut down or operate erratically when temperatures exceed their operating specifications, leaving users without lighting in the environmental conditions where visibility is most challenging.
This temperature sensitivity can be particularly problematic for users who operate their trucks in extreme climates or who need lighting reliability during seasonal temperature extremes.
Also Read: 5 Cars With the Lowest Cabin Carbon Footprints and 5 Using Harsh Materials