The battle against automotive rust is as old as the automobile itself, representing one of the most persistent challenges facing vehicle owners worldwide.
Underbody protection and floor pan integrity serve as the primary defense mechanisms against the relentless assault of moisture, salt, chemicals, and road debris that threaten to compromise your vehicle’s structural integrity and long-term value.
Understanding which vehicles excel in underbody shielding versus those prone to premature rust formation has become increasingly critical for informed purchasing decisions.
Modern automotive engineering has evolved sophisticated approaches to combat corrosion, ranging from advanced galvanized steel construction and multi-layer protective coatings to innovative drainage systems and strategic material placement.
However, not all manufacturers have embraced these technologies equally, resulting in dramatic variations in rust resistance across different brands, models, and manufacturing periods.
The consequences of poor underbody protection extend far beyond aesthetic concerns, potentially compromising structural safety, reducing vehicle longevity, and devastating resale values.
This comprehensive analysis examines ten vehicles representing the extremes of underbody protection philosophy. The first five vehicles showcase exemplary engineering approaches to rust prevention, featuring robust protective systems that have proven their effectiveness through decades of real-world testing.
These vehicles demonstrate how proper material selection, advanced coating technologies, and thoughtful design integration can create remarkably durable underbody protection systems that maintain their integrity even in harsh environmental conditions.
Conversely, the five rust-prone vehicles highlighted represent cautionary tales of inadequate protection systems, design oversights, and material compromises that have resulted in premature corrosion problems.
These examples illustrate how cost-cutting measures, poor material choices, and insufficient protective treatments can lead to significant structural deterioration, expensive repairs, and reduced vehicle lifespan.
5 Cars With Exceptional Underbody SHIELDING
These exceptionally protected vehicles feature comprehensive corrosion-resistant coatings and precision-engineered underbody panels that provide superior protection against road salt, moisture infiltration, and debris damage through years of harsh weather exposure and challenging driving conditions.
Their thoughtful engineering includes galvanized steel construction, advanced polymer shields, and strategic drainage systems that resist the structural deterioration typically created by winter road treatments or aggressive off-road environments.
From salt-heavy coastal regions that accelerate corrosion processes to gravel roads that create constant stone bombardment, these remarkable protection systems continue preserving structural integrity without developing rust penetration or panel perforation throughout extended ownership periods.
Owners report decades of corrosion-free operation with these superior protection solutions a longevity-enhancing quality feature that proves its worth through maintained structural strength and preserved resale value throughout various climate exposures.
1. Audi A4 Allroad Quattro (2017-2025)
The Audi A4 Allroad Quattro represents the pinnacle of German engineering excellence in underbody protection, incorporating multiple layers of sophisticated corrosion prevention technologies that have established it as one of the most rust-resistant vehicles in its class.
Audi’s commitment to long-term durability becomes immediately apparent when examining the comprehensive protection systems integrated throughout the vehicle’s underbody architecture.
The foundation of the Allroad’s exceptional rust resistance begins with its advanced multi-metal construction approach. The vehicle utilizes a combination of high-strength galvanized steel, aluminum components, and strategic composite materials that work together to create an inherently corrosion-resistant structure.
The galvanization process involves coating steel components with multiple layers of zinc, creating a sacrificial barrier that prevents moisture and oxygen from reaching the underlying metal.
This galvanization extends beyond basic coverage to include full-body immersion treatments that ensure even the most complex geometric areas receive adequate protection. Audi’s proprietary underbody coating system represents another crucial element in the Allroad’s protection strategy.
The vehicle features a comprehensive multi-layer coating application that begins during the manufacturing process with electro-coating treatments applied in controlled environments. This initial coating provides baseline protection while ensuring optimal adhesion for subsequent layers.

The primary underbody coating consists of a specialized polymer-based compound that maintains flexibility across temperature variations while providing excellent resistance to impact damage, chemical exposure, and abrasion from road debris.
The drainage system integration within the Allroad’s underbody design demonstrates Audi’s attention to moisture management principles. Strategic drain holes, carefully positioned throughout the floor pan assembly, prevent water accumulation in critical areas where standing moisture could initiate corrosion processes.
These drainage points incorporate debris shields that prevent clogging while maintaining effective water evacuation capabilities. The door frame construction includes advanced water management channels that direct moisture away from structural components, reducing the likelihood of trapped water causing localized corrosion.
Advanced material selection extends throughout the Allroad’s underbody construction, with particular attention paid to dissimilar metal junction points where galvanic corrosion typically initiates.
Audi engineers have implemented specialized barrier coatings and isolation techniques at these critical interfaces, preventing the electrochemical reactions that often lead to accelerated corrosion in other vehicles.
The exhaust system mounting points feature corrosion-resistant hardware and isolation materials that prevent rust transfer between different metal components.
Maintenance accessibility represents another significant advantage of the Allroad’s protection system design. The underbody layout facilitates regular inspection and cleaning procedures that help maintain the protection system’s effectiveness over time.
Access panels and inspection points allow owners to monitor critical areas without requiring extensive disassembly procedures. The coating system’s self-healing properties help maintain protection effectiveness even when minor damage occurs during normal operation.
2. Lexus GX 460 (2010-2025)
The Lexus GX 460 exemplifies Toyota’s legendary reputation for building vehicles that withstand decades of harsh environmental exposure while maintaining structural integrity.
This body-on-frame SUV incorporates time-tested protection methodologies combined with modern corrosion prevention technologies to create one of the most durable underbody protection systems available in the luxury SUV segment.
Toyota’s approach to underbody protection in the GX 460 begins with fundamental design philosophy emphasizing simplicity, redundancy, and proven materials.
The vehicle’s frame construction utilizes high-strength steel components that undergo comprehensive galvanization treatments during manufacturing.
This galvanization process involves multiple immersion stages that ensure complete coverage of all frame surfaces, including internal cavities and complex geometric areas that are difficult to protect through conventional coating methods.
The frame design itself incorporates drainage considerations that prevent water accumulation in critical structural areas. Strategic drain holes, positioned throughout the frame rails, allow trapped moisture to escape while preventing debris accumulation that could compromise drainage effectiveness.
The frame rail construction includes internal baffles that direct water flow toward drainage points while maintaining structural integrity requirements for off-road capability and towing capacity.
Body mounting systems between the frame and body panels incorporate advanced isolation materials that prevent galvanic corrosion at dissimilar metal interfaces.
These mounting points utilize stainless steel hardware combined with specialized barrier coatings that maintain their protective properties across temperature variations and chemical exposure conditions. The isolation materials resist compression set and chemical degradation, ensuring long-term effectiveness of the corrosion prevention system.
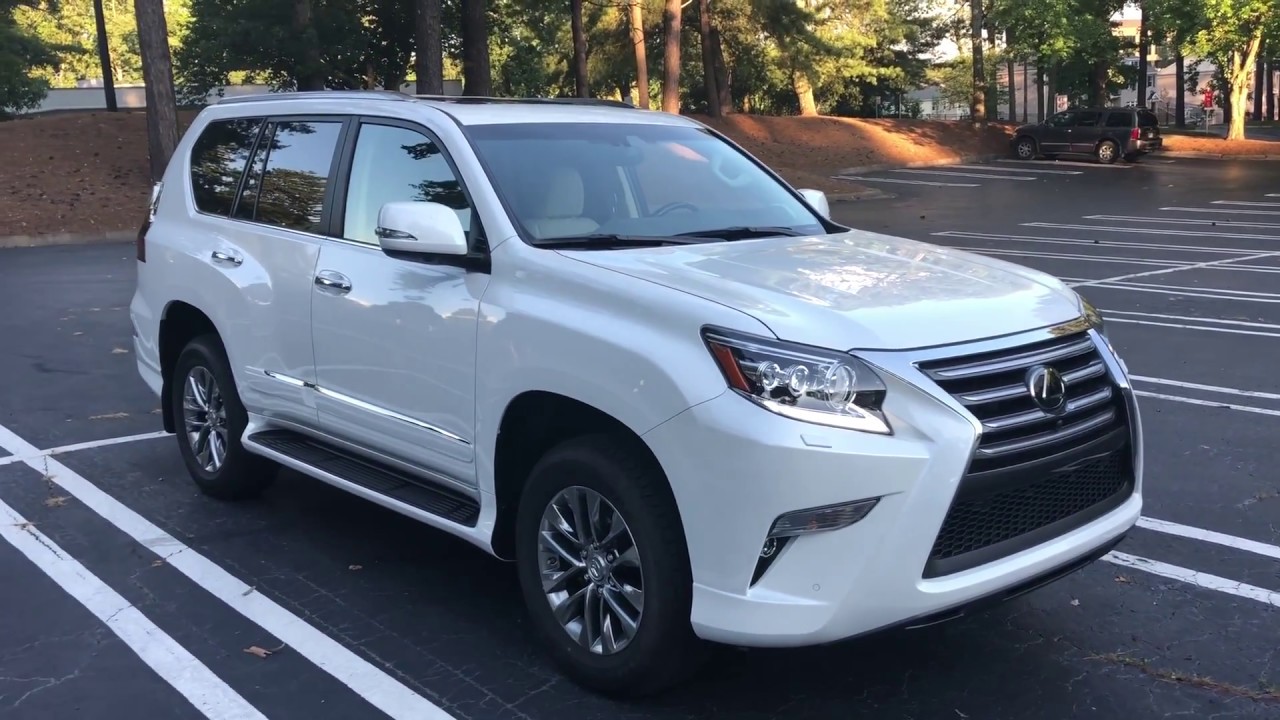
The GX 460’s underbody coating system features a multi-layer approach that provides both impact protection and corrosion resistance. The primary coating consists of a flexible polymer compound that maintains adhesion across the full range of operating temperatures while providing excellent resistance to stone chip damage and abrasion from off-road debris.
This coating system includes self-leveling properties that help fill minor surface irregularities while maintaining uniform thickness across complex surface geometries.
Exhaust system protection receives particular attention in the GX 460’s design, recognizing the high-temperature corrosion challenges associated with exhaust component operation.
Heat shields incorporate corrosion-resistant materials and mounting systems that prevent rust initiation at attachment points. The exhaust pipe routing avoids critical structural areas while maintaining ground clearance requirements for off-road capability.
Catalytic converter shields provide impact protection while preventing heat-related damage to surrounding components. Fuel system protection includes comprehensive shielding for fuel lines, tank mounting systems, and vapor recovery components.
The fuel tank construction utilizes corrosion-resistant materials with protective coatings that resist chemical degradation from fuel additives and environmental contaminants. Tank mounting straps feature galvanized construction with protective coatings that maintain their integrity across extended service intervals.
Long-term durability validation of the GX 460’s protection systems comes from extensive real-world experience across diverse operating environments.
Vehicles operating in coastal areas, northern climates with heavy road salt usage, and desert environments with extreme temperature variations have demonstrated exceptional underbody integrity retention across high-mileage service intervals. Independent reliability studies consistently rate the GX 460 among the most durable vehicles in its class for underbody corrosion resistance.
3. Porsche Macan (2014-2025)
The Porsche Macan represents a masterclass in European automotive engineering, combining high-performance capabilities with exceptional underbody protection systems that maintain their effectiveness across diverse operating conditions.
Porsche’s approach to corrosion prevention reflects decades of experience building vehicles that must perform reliably in demanding environments while maintaining their structural integrity over extended service intervals.
The Macan’s underbody protection begins with advanced material selection and construction techniques that create an inherently corrosion-resistant foundation.
The vehicle utilizes a mixed-material construction approach that strategically places aluminum, high-strength steel, and advanced composites in locations that optimize both performance and corrosion resistance characteristics.
The aluminum components undergo specialized surface treatments that enhance their natural corrosion resistance while providing excellent adhesion for subsequent protective coatings.
Porsche’s proprietary coating system represents one of the most sophisticated approaches to underbody protection available in the luxury compact SUV segment.
The multi-stage coating process begins with comprehensive surface preparation that ensures optimal adhesion and coverage uniformity. The primary coating application utilizes advanced electrostatic deposition techniques that provide superior coverage of complex geometric areas and internal cavities that are difficult to protect through conventional spray application methods.
The coating formulation itself incorporates advanced polymer chemistry that provides exceptional resistance to impact damage, chemical exposure, and thermal cycling effects.
The coating maintains its protective properties across temperature ranges from extreme cold to high-heat conditions associated with performance driving applications.
Self-healing properties help maintain protection effectiveness when minor damage occurs during normal operation, while the coating’s flexibility prevents cracking and delamination that could compromise long-term effectiveness.
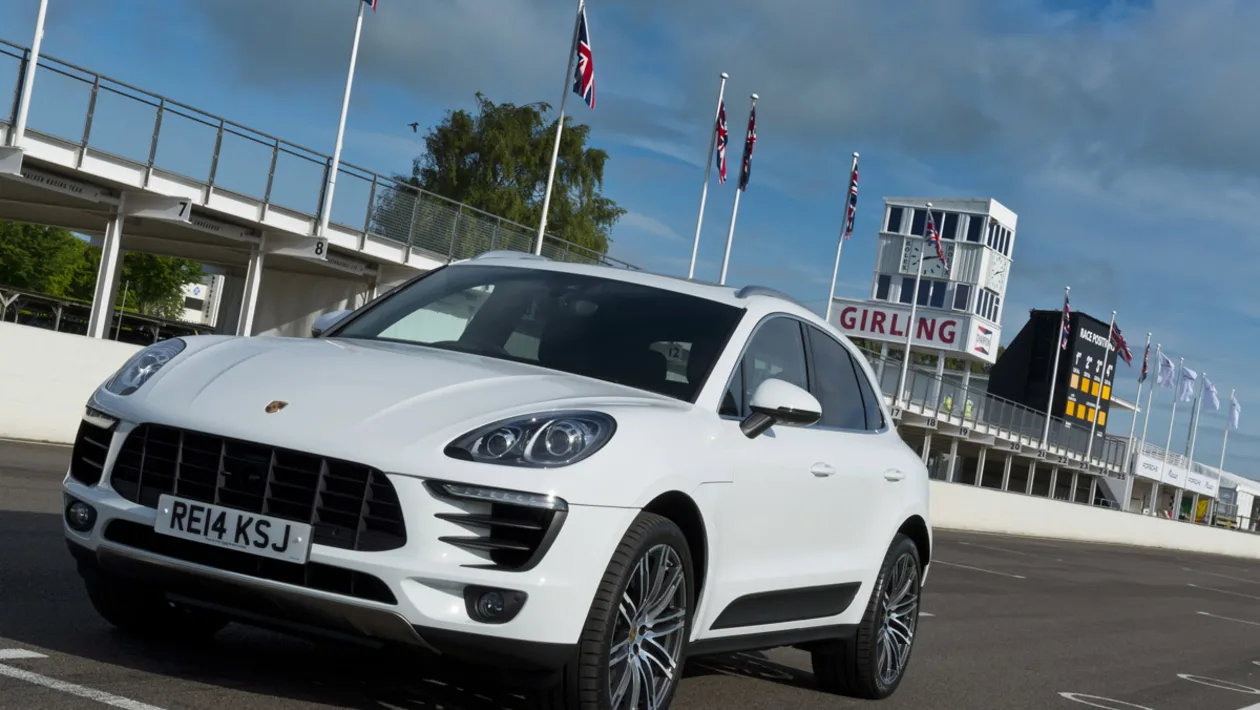
Drainage system integration throughout the Macan’s underbody design demonstrates Porsche’s comprehensive approach to moisture management.
Strategic drainage points prevent water accumulation in critical areas while incorporating debris shields that maintain drainage effectiveness across extended service intervals.
The door frame construction includes advanced water management systems that direct moisture away from structural components while maintaining the vehicle’s refined aesthetic appearance.
The exhaust system protection reflects Porsche’s performance-oriented design philosophy while maintaining exceptional corrosion resistance. High-temperature resistant coatings and heat shields protect surrounding components from heat-related degradation while maintaining the system’s performance characteristics.
Exhaust component mounting systems utilize corrosion-resistant hardware and isolation materials that prevent rust transfer between different metal components.
Suspension system protection extends throughout the Macan’s underbody architecture, with particular attention paid to components subject to road salt exposure and impact damage.
Control arm and subframe mounting points feature advanced protective coatings and corrosion-resistant hardware that maintain their effectiveness across extended service intervals.
The air suspension system components, when equipped, incorporate comprehensive sealing and protection measures that prevent corrosion-related failures.
The vehicle’s comprehensive electrical system protection includes advanced routing techniques and protective coverings that shield wiring harnesses from moisture intrusion and chemical exposure.
Connector systems utilize sealed designs with gold-plated contacts that resist corrosion in harsh environmental conditions. The electrical system routing avoids areas prone to water accumulation while incorporating strain relief systems that prevent damage from vehicle movement and vibration.
Long-term effectiveness validation comes from extensive testing in extreme environmental conditions, including salt spray chambers, thermal cycling facilities, and real-world exposure in harsh climates.
Independent corrosion resistance studies consistently rate the Macan among the top performers in its class for underbody protection effectiveness and long-term durability characteristics.
4. Toyota Land Cruiser 200 Series (2008-2021)
The Toyota Land Cruiser 200 Series stands as a monument to automotive durability engineering, incorporating underbody protection systems that have been refined through decades of real-world testing in some of the world’s most challenging environments.
Toyota’s approach to corrosion prevention in the Land Cruiser reflects a fundamental philosophy of over-engineering protection systems to ensure reliable operation across extended service intervals in harsh conditions.
The Land Cruiser’s frame construction utilizes Toyota’s most advanced galvanization processes, with comprehensive zinc coating coverage that extends to internal frame cavities and complex geometric areas.
The galvanization process involves multiple immersion stages that ensure complete coverage of all steel surfaces, creating a sacrificial barrier that prevents moisture and oxygen from reaching the underlying metal. This treatment extends beyond standard automotive applications to include marine-grade corrosion resistance capabilities.
Frame design incorporates extensive drainage considerations that prevent water accumulation in critical structural areas. The frame rail construction includes multiple drain holes positioned to evacuate trapped moisture while preventing debris accumulation that could compromise drainage effectiveness.
Internal baffles direct water flow toward drainage points while maintaining the structural integrity required for extreme off-road use and heavy-duty towing applications.
The underbody coating system features a multi-layer approach designed for extreme durability in harsh environmental conditions. The primary coating consists of a thick-film polymer compound that provides exceptional resistance to impact damage from rocks, debris, and off-road obstacles.
This coating system maintains its protective properties across extreme temperature variations while resisting chemical degradation from road salt, automotive fluids, and industrial contaminants.
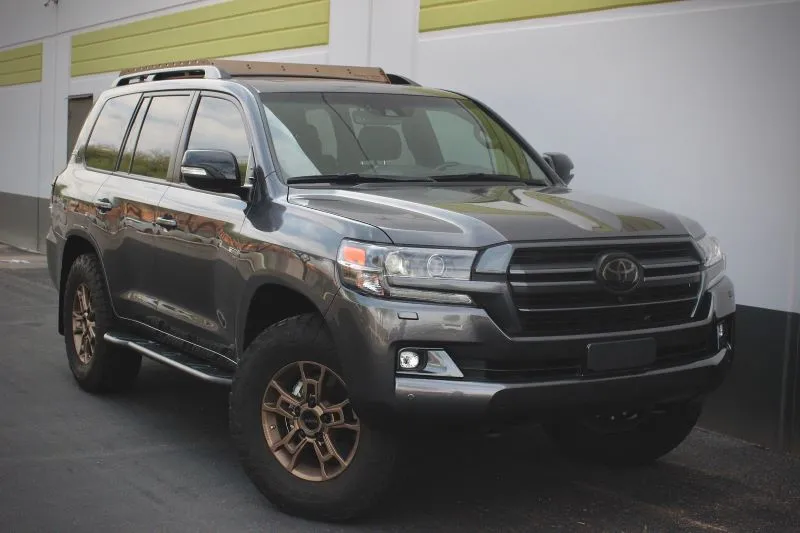
Skid plate integration throughout the Land Cruiser’s underbody provides both impact protection and additional corrosion barriers. These plates utilize high-strength steel construction with comprehensive protective coatings that resist corrosion while providing mechanical protection for critical components.
The skid plate mounting systems incorporate corrosion-resistant hardware and isolation materials that prevent rust initiation at attachment points. Fuel system protection includes comprehensive shielding and corrosion-resistant construction throughout the fuel delivery system.
The fuel tank construction utilizes advanced materials and protective coatings that resist chemical degradation while maintaining structural integrity across extended service intervals. Fuel line routing incorporates protective coverings and mounting systems that resist corrosion and impact damage in off-road conditions.
The exhaust system design reflects Toyota’s commitment to long-term durability in harsh operating conditions. Exhaust component construction utilizes corrosion-resistant materials and protective coatings that maintain their effectiveness across extended high-temperature operation cycles.
Heat shield systems protect surrounding components while incorporating drainage features that prevent moisture accumulation around exhaust components.
Suspension system protection extends throughout the Land Cruiser’s robust underbody architecture. Control arm and differential mounting points feature heavy-duty protective coatings and corrosion-resistant hardware that maintain their effectiveness across extreme operating conditions.
The four-wheel-drive system components incorporate comprehensive sealing and protection measures that prevent corrosion-related failures in harsh environments.
Electrical system routing incorporates military-grade protection standards that shield wiring harnesses from moisture intrusion, chemical exposure, and mechanical damage.
Wire harness construction utilizes advanced insulation materials and protective coverings that resist degradation across extreme temperatures and environmental conditions.
Connector systems feature sealed designs with corrosion-resistant contact materials that maintain electrical integrity in harsh operating environments.
Real-world validation of the Land Cruiser’s protection systems comes from extensive service in extreme environments, including desert operations, coastal exposure, industrial applications, and northern climates with heavy road salt usage.
Vehicles with hundreds of thousands of miles in harsh conditions have demonstrated exceptional underbody integrity retention, validating the effectiveness of Toyota’s comprehensive protection approach.
Also Read: 5 Trucks With the Best LED Bed Lighting and 5 With Dim Lamps
5. BMW X5 (F15/G05 Generation 2014-2025)
The BMW X5 represents Bavarian engineering excellence in underbody protection, combining advanced materials science with sophisticated manufacturing processes to create one of the most corrosion-resistant luxury SUVs available.
BMW’s approach to underbody protection reflects decades of experience building vehicles that must maintain their performance and aesthetic qualities across extended service intervals in demanding environments.
The X5’s construction utilizes BMW’s advanced mixed-material architecture that strategically combines aluminum, high-strength steel, and carbon fiber reinforced plastic components to optimize both performance and corrosion resistance characteristics.
The aluminum components undergo specialized surface treatments that enhance their natural corrosion resistance while providing excellent adhesion for subsequent protective coatings. The steel components receive comprehensive galvanization treatments that create multiple barrier layers against corrosion initiation.
BMW’s proprietary coating system incorporates cutting-edge polymer chemistry that provides exceptional protection against environmental degradation.
The multi-stage coating process begins with comprehensive surface preparation using advanced cleaning and etching techniques that ensure optimal adhesion.
The primary coating application utilizes electrostatic deposition methods that provide superior coverage of complex geometric areas and internal cavities that are challenging to protect through conventional application techniques.
The coating formulation includes advanced additives that provide self-healing properties, allowing minor damage to seal automatically without compromising overall protection effectiveness.
The coating maintains its protective characteristics across extreme temperature ranges while resisting chemical degradation from road salt, automotive fluids, and environmental contaminants. UV stabilizers prevent coating degradation from solar exposure, ensuring long-term effectiveness in diverse climatic conditions.
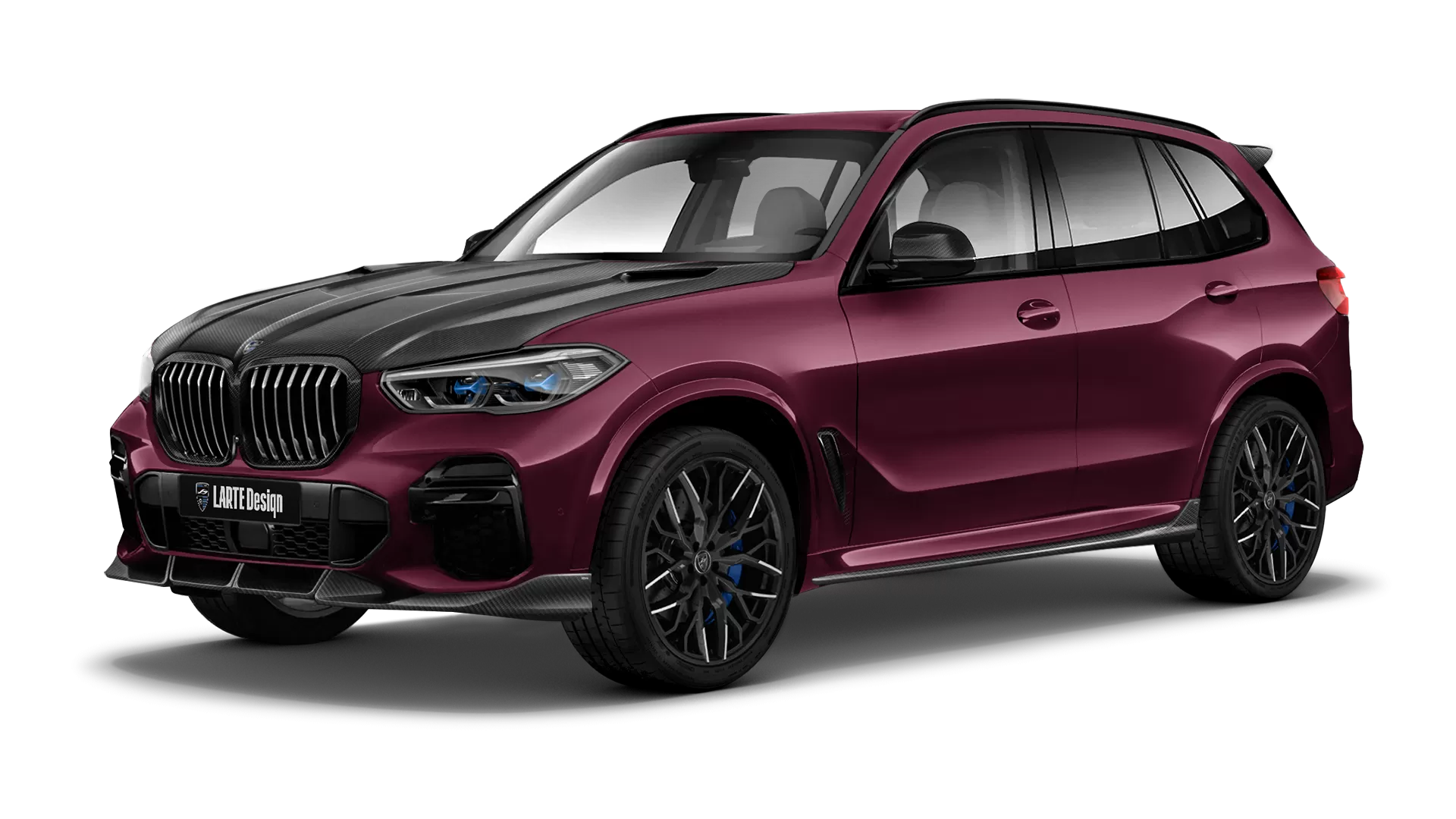
Underbody aerodynamic considerations in the X5’s design provide additional protection benefits while enhancing vehicle performance characteristics.
Strategic underbody paneling creates smooth airflow paths that reduce debris accumulation while providing additional corrosion barriers. These panels utilize advanced composite materials that resist impact damage and chemical degradation while maintaining their aerodynamic effectiveness across extended service intervals.
The exhaust system protection incorporates BMW’s performance-oriented design philosophy while maintaining exceptional corrosion resistance. High-temperature resistant coatings and advanced heat shield systems protect surrounding components from thermal degradation while maintaining the exhaust system’s performance characteristics.
Exhaust component mounting systems utilize corrosion-resistant hardware and thermal isolation materials that prevent heat-related damage to protection systems. Suspension system integration includes comprehensive protection for electronic damping systems and advanced suspension components.
The adaptive suspension components incorporate sealed construction and protective coatings that maintain their performance characteristics across extended exposure to harsh environmental conditions.
Control arm and subframe mounting points feature advanced protective treatments that resist corrosion while maintaining the precise handling characteristics BMW customers expect.
The vehicle’s advanced electrical system architecture includes comprehensive protection measures for the extensive electronic systems that control vehicle functions.
Wire harness routing utilizes protective channels and coverings that shield conductors from moisture intrusion and chemical exposure. Connector systems feature advanced sealing technologies and corrosion-resistant contact materials that maintain electrical integrity across extended service intervals.
Battery protection systems for conventional and hybrid powertrains incorporate advanced environmental sealing and thermal management features.
The battery housing construction utilizes corrosion-resistant materials and protective coatings that maintain structural integrity while protecting internal components from environmental contamination. Cooling system integration prevents thermal-related degradation while maintaining optimal battery performance characteristics.
Long-term durability validation includes extensive testing in controlled environmental chambers and real-world exposure programs across diverse climatic conditions.
Independent studies consistently rate the X5 among the top performers for underbody corrosion resistance and long-term structural integrity maintenance in the luxury SUV segment.
5 Cars with Rust-Prone Floor
These corrosion-vulnerable vehicles suffer from inadequate underbody protection due to minimal galvanization, poor drainage design, and insufficient sealing that allows moisture accumulation and accelerated rust formation in critical structural areas throughout normal driving exposure.
Their problematic engineering includes basic steel construction, limited protective coatings, and poor water management systems that amplify the corrosion damage typically associated with road salt exposure or high-humidity environments.
From floor pan perforation that compromises structural integrity to rocker panel deterioration that affects safety ratings, these vulnerable underbodies demand constant attention through preventive treatments and regular inspection schedules.
Owners discover that while these vehicles may offer attractive initial pricing, their corrosion susceptibility creates long-term maintenance expenses and structural concerns that significantly impact vehicle longevity and require expensive restoration work to maintain roadworthiness.
1. Nissan Altima (2002-2006)
The Nissan Altima from the early 2000s represents one of the most notorious examples of inadequate underbody protection in modern automotive history.
This generation of Altima has earned an unfortunate reputation for premature floor pan deterioration, subframe corrosion, and structural rust that often renders vehicles unsafe long before their mechanical components reach end-of-life conditions.
The fundamental issues with the 2002-2006 Altima’s underbody protection begin with material selection and treatment processes that proved inadequate for long-term corrosion resistance.
The floor pan construction utilized relatively thin-gauge steel with minimal galvanization treatment, creating a foundation that was inherently vulnerable to rust initiation.
The galvanization process, when applied, appeared to use older zinc coating techniques that provided limited coverage depth and poor adhesion characteristics compared to contemporary automotive standards.
The vehicle’s underbody coating system represented a significant compromise in protection effectiveness. The factory-applied coating appeared to be a thin-film treatment that provided minimal barrier protection against moisture intrusion and chemical exposure.
This coating system demonstrated poor adhesion characteristics, with widespread reports of coating delamination occurring within the first few years of service. Once the protective coating failed, the underlying steel became directly exposed to corrosive elements with predictable results.
Drainage system design flaws compounded the Altima’s corrosion susceptibility by creating multiple areas where water accumulation could occur.
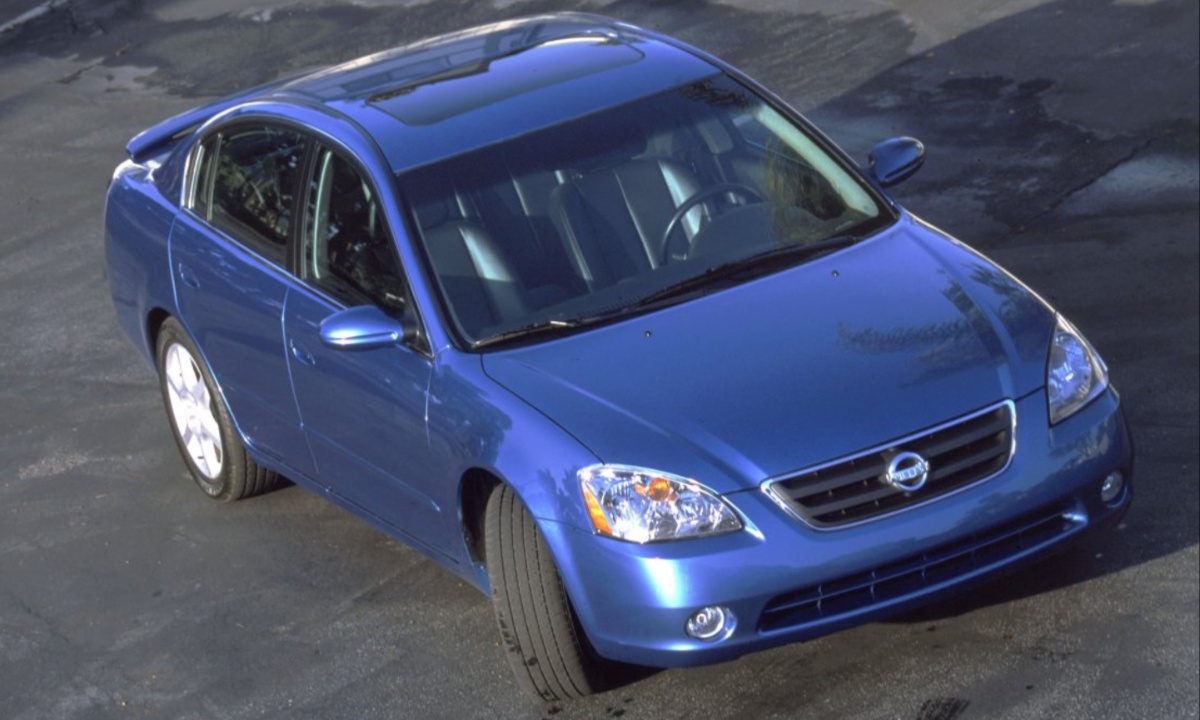
The floor pan construction included numerous low points and crevices where trapped moisture could initiate and sustain corrosion processes. Door frame construction incorporated water management systems that often became clogged with debris, causing water to accumulate in areas where it could contact unprotected steel surfaces.
The rear subframe mounting area represents perhaps the most critical failure point in the Altima’s underbody design. This structural component, which carries suspension loads and provides mounting points for safety-critical systems, demonstrated widespread corrosion problems that often progressed to complete structural failure.
The subframe mounting points utilized design configurations that trapped moisture while providing inadequate protective coatings, creating ideal conditions for accelerated corrosion.
Exhaust system routing and protection proved inadequate for preventing corrosion initiation in surrounding structural areas. Heat shield systems provided insufficient coverage while utilizing mounting methods that created additional penetration points through protective barriers.
Exhaust component replacement procedures often revealed extensive corrosion damage to surrounding floor pan areas that had been hidden during routine inspections.
Regional variations in corrosion severity have demonstrated the relationship between environmental conditions and protection system effectiveness.
Vehicles operated in northern climates with heavy road salt usage have experienced the most severe problems, while those in dry climates have shown better longevity.
However, even vehicles in relatively benign environments have demonstrated premature corrosion problems, indicating fundamental design and material inadequacies.
2. Ford Focus (2000-2007)
The first-generation Ford Focus represents a significant disappointment in underbody protection, particularly considering Ford’s established reputation and the vehicle’s otherwise competent engineering.
This generation of Focus has become synonymous with premature floor pan corrosion, sill deterioration, and structural rust problems that often appear within the first decade of service, creating safety concerns and devastating resale values.
The Focus’s underbody protection failures begin with fundamental material and design choices that prioritize cost reduction over long-term durability.
The floor pan construction utilized thin-gauge steel with inadequate galvanization treatment, creating a foundation that was inherently susceptible to corrosion initiation.
The steel thickness appeared insufficient to provide adequate reserve capacity once corrosion processes began, resulting in rapid progression from surface rust to structural perforations.
The factory coating system represented a minimal approach to corrosion protection that proved inadequate for real-world operating conditions. The applied coating appeared to be a thin-film treatment that provided limited barrier protection against moisture and chemical exposure.
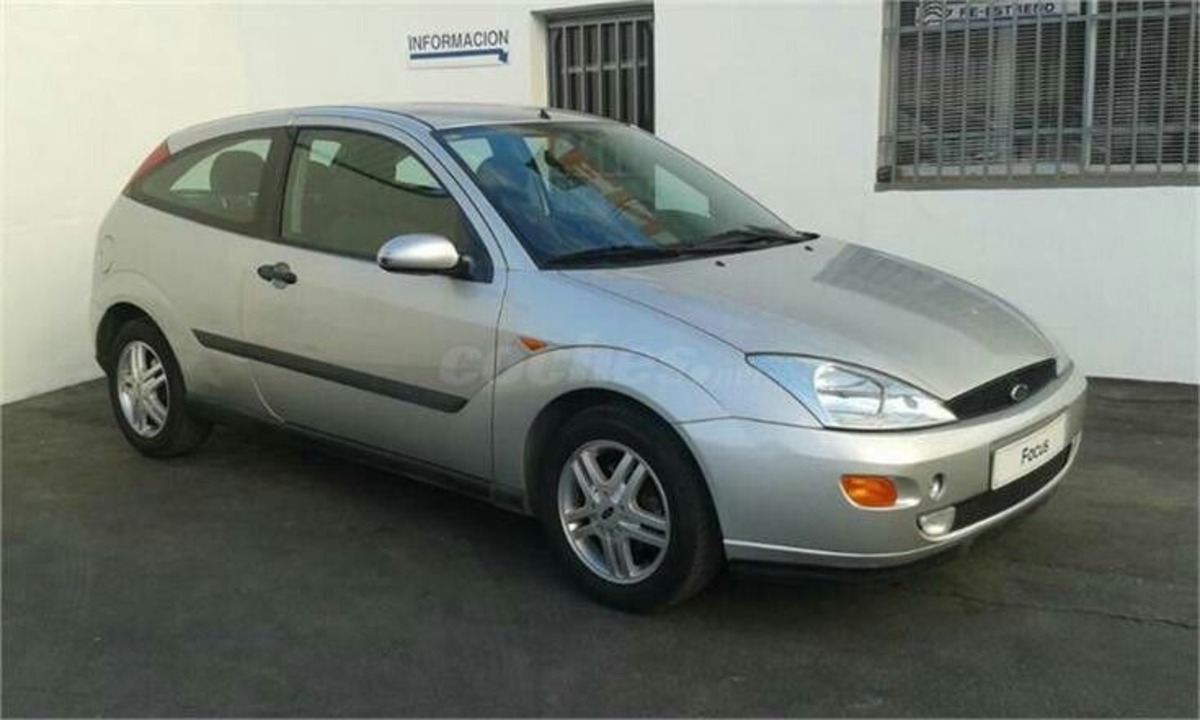
This coating system demonstrated poor adhesion characteristics, with widespread reports of coating failure occurring within the first few years of service, particularly in areas subject to stone chip damage and mechanical stress.
The Focus’s corrosion problems have had severe consequences for vehicle safety and owner satisfaction. Independent inspections have revealed widespread floor pan perforations, structural weakness, and safety system mounting point deterioration that often renders vehicles unsafe for continued operation.
The predictable nature of these problems has made this generation of Focus a poor choice for buyers seeking long-term reliability and value retention. Regional climate variations have demonstrated the relationship between environmental exposure and protection system adequacy.
Vehicles operated in coastal areas and northern climates with road salt exposure have experienced the most severe problems, while those in dry climates have shown somewhat better longevity. However, even vehicles in relatively benign environments have demonstrated premature corrosion problems, indicating fundamental inadequacies in protection system design and implementation.
3. Mazda RX-8 (2004-2012)
The Mazda RX-8 presents a unique case study in underbody corrosion problems, combining sports car performance aspirations with inadequate protection systems that have resulted in widespread structural deterioration problems.
While the vehicle’s rotary engine reliability issues receive significant attention, the RX-8’s underbody protection failures represent an equally serious concern that affects vehicle safety and long-term viability.
The RX-8’s underbody protection inadequacies stem from design priorities that emphasized performance and weight reduction over long-term corrosion resistance.
The floor pan construction utilized relatively thin steel sections with minimal protective treatments, creating a structure that was inherently vulnerable to corrosion initiation and progression.
The lightweight construction philosophy, while beneficial for performance characteristics, resulted in insufficient material thickness to provide adequate reserve capacity once corrosion processes began.
The factory coating system represented a compromise approach that proved inadequate for providing long-term protection in real-world operating conditions.
The applied coating appeared to be a thin-film treatment that provided minimal barrier protection against moisture intrusion and chemical exposure.
This coating system demonstrated poor durability characteristics, with reports of coating degradation and failure occurring within the first few years of service, particularly in areas subject to road debris impact and thermal cycling.
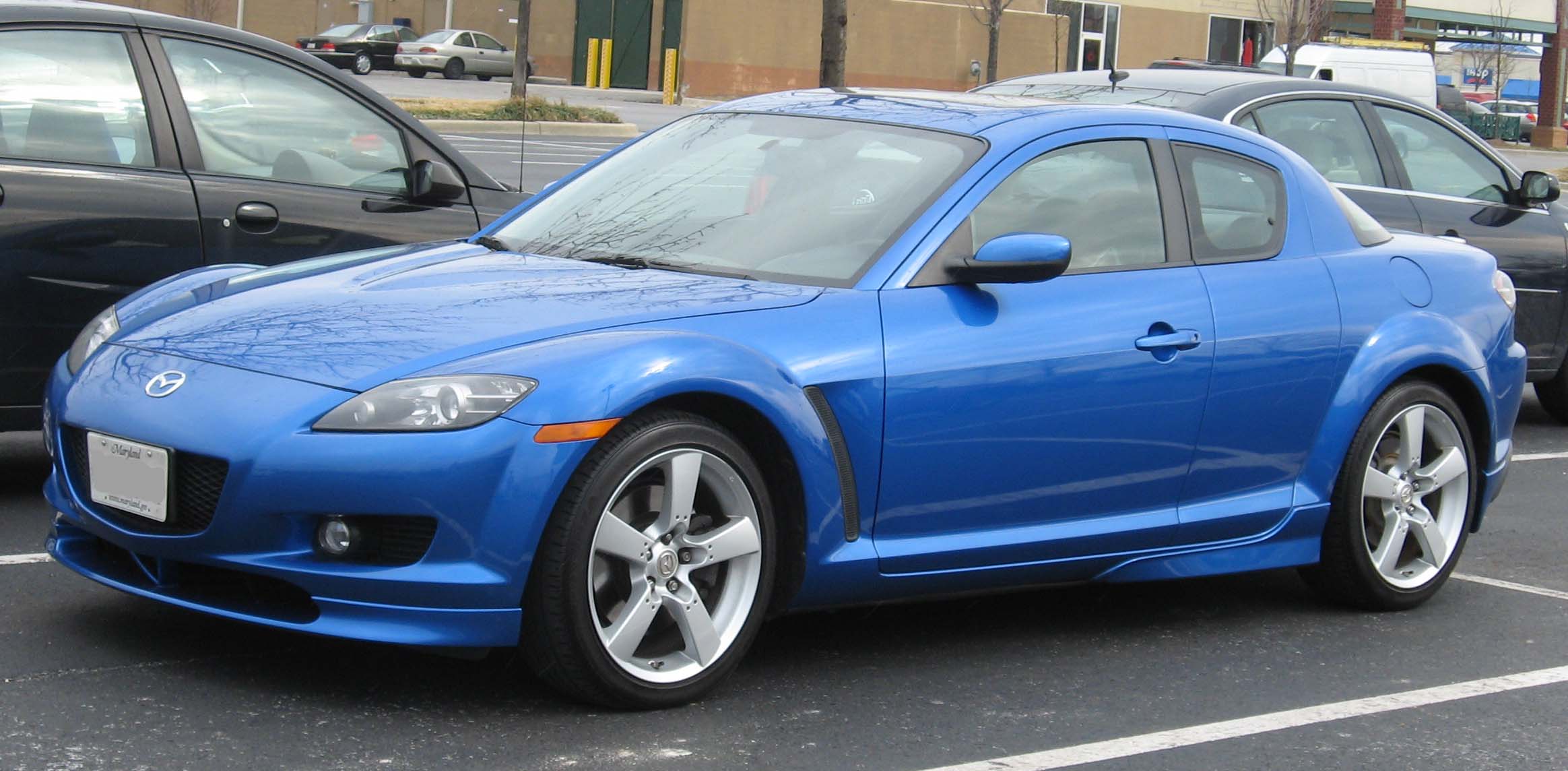
Structural design elements specific to the RX-8’s sports car architecture created multiple areas where corrosion problems could develop. The battery mounting location in the trunk area created a configuration where battery acid spillage and off-gassing could contact unprotected steel surfaces, initiating localized corrosion that often spread to surrounding structural areas.
The complex rear suspension geometry required multiple mounting points and brackets that created stress concentration areas where coating damage was likely to occur. The vehicle’s low ground clearance and aerodynamic underbody components created additional challenges for corrosion protection.
The proximity to road surfaces increased exposure to debris impact and chemical splash, while the aerodynamic panels often trapped moisture and debris against protective coatings. The panel mounting systems created multiple penetration points through protective barriers that often became corrosion initiation sites.
Cooling system requirements for the rotary engine created unique underbody routing challenges that compromised protection system integrity. Multiple radiators and cooling system components required complex plumbing arrangements that created numerous penetration points through protective barriers.
Oil cooler mounting and routing created additional areas where leakage could contact unprotected steel surfaces and initiate corrosion processes.
The exhaust system design, while optimized for rotary engine performance characteristics, created thermal management challenges that affected surrounding protection systems.
High-temperature operation and complex routing requirements resulted in heat shield configurations that provided insufficient coverage while creating mounting points that penetrated protective coatings. Thermal cycling effects often caused coating degradation in areas surrounding exhaust components.
Electrical system complexity in the RX-8 required extensive wiring harness routing through underbody areas that lacked adequate protection against moisture intrusion and corrosion damage.
The vehicle’s advanced electronic systems created requirements for numerous electrical connections and components located in vulnerable underbody areas. Many RX-8 vehicles have experienced electrical system problems as corrosion damage progressed through areas containing critical wiring harnesses.
The fuel system installation created multiple compromise points in the underbody protection system through inadequate sealing and protection of penetration points.
The fuel tank mounting configuration and filler tube routing created areas where protective barriers were compromised, while the fuel pump and associated components required electrical connections that often became vulnerable to moisture intrusion and corrosion damage.
Water management systems proved inadequate for preventing moisture accumulation in critical structural areas. The vehicle’s sports car proportions and door seal configurations created challenges for effective water drainage, while the complex underbody geometry included multiple areas where water could accumulate and initiate corrosion processes.
Sunroof drainage systems, when equipped, often became compromised by debris accumulation, causing water overflow into areas where it could contact unprotected steel surfaces.
Manufacturing quality control appears to have been inconsistent regarding protection system application and coverage. Reports from owners and service technicians indicate significant variations in coating quality and coverage between individual vehicles, suggesting inadequate process control during production.
Some vehicles demonstrated better corrosion resistance than others, indicating that proper application of protective treatments could have prevented many of the observed problems.
The RX-8’s corrosion problems have been compounded by the vehicle’s specialized nature and limited service network’s familiarity with proper repair procedures.
Many general repair facilities lack experience with rotary engine vehicles and associated underbody protection requirements, leading to inadequate repairs that fail to address underlying corrosion issues. The vehicle’s declining market value has also made extensive corrosion repairs economically unfeasible for many owners.
Long-term consequences of the RX-8’s underbody protection failures have been severe, with many vehicles experiencing structural deterioration that affects safety and roadworthiness.
Independent inspections have revealed floor pan perforations, battery tray deterioration, and suspension mounting point weakness that often render vehicles unsafe for continued operation. The specialized nature of the vehicle has made replacement parts increasingly difficult to obtain, further complicating repair efforts.
Regional variations in corrosion severity have demonstrated the critical importance of adequate environmental protection. Vehicles operated in coastal areas and northern climates with road salt exposure have experienced the most severe problems, while those in dry climates have shown better longevity.
However, the RX-8’s inherent protection system inadequacies have resulted in premature corrosion problems even in relatively benign environmental conditions.
4. Jeep Wrangler TJ (1997-2006)
The Jeep Wrangler TJ generation represents a significant disappointment in underbody protection, particularly given the vehicle’s intended use in challenging off-road environments where corrosion resistance should be a primary design consideration.
This generation of Wrangler has earned an unfortunate reputation for premature frame corrosion, floor pan deterioration, and structural rust problems that often compromise vehicle safety and off-road capability.
The TJ Wrangler’s underbody protection failures begin with a fundamental design philosophy that prioritized traditional construction methods over modern corrosion prevention technologies.
The frame construction utilized conventional steel fabrication with minimal galvanization treatment, creating a structure that was inherently vulnerable to corrosion initiation in challenging environmental conditions.
The frame design incorporated multiple areas where water and debris could accumulate, creating ideal conditions for sustained corrosion processes.
The factory coating system represented a minimal approach to corrosion protection that proved inadequate for the demanding conditions Wrangler owners typically encounter.
The applied coating appeared to be a basic treatment that provided limited barrier protection against moisture, mud, and chemical exposure associated with off-road use.
This coating system demonstrated poor durability characteristics when subjected to impact damage from rocks, debris, and mechanical stress associated with off-road driving.
Frame design elements specific to the TJ generation created multiple problematic areas where corrosion could initiate and progress rapidly. The frame rail construction included internal cavities that could trap water and debris while providing limited drainage capabilities.
These areas became primary sites for corrosion initiation that often progressed to complete structural failure of critical load-bearing components.
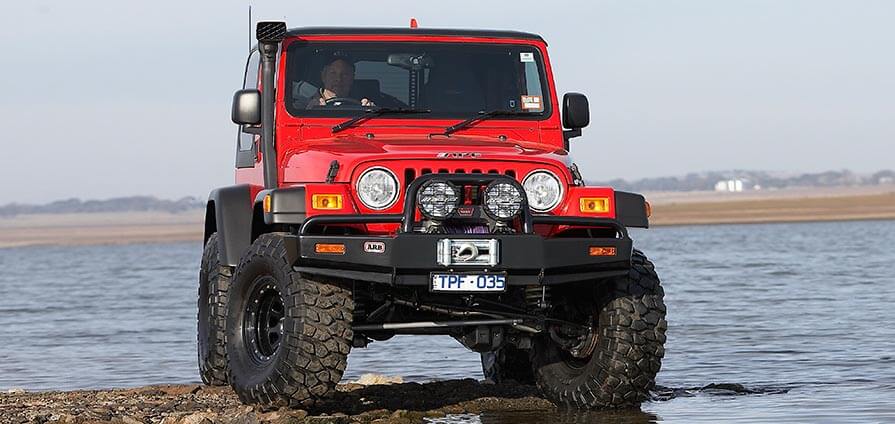
The body mounting system between the frame and tub created additional corrosion vulnerability points through inadequate protection of dissimilar metal interfaces.
The mounting hardware and isolation materials proved insufficient for preventing galvanic corrosion while providing inadequate sealing against moisture intrusion. Many TJ Wranglers have experienced body mounting failures due to corrosion damage that compromised structural integrity and safety.
Suspension mounting points represent particularly critical failure areas that combine structural loading with inadequate corrosion protection. The control arm mounting brackets and suspension component attachment points utilize configurations that create stress concentration areas where coating damage is likely to occur.
Once protective treatments fail in these areas, the combination of structural stress and environmental exposure creates conditions for accelerated corrosion progression.
The fuel system installation contributed to frame corrosion problems through inadequate protection of penetration points and mounting hardware.
The fuel tank mounting straps and associated components demonstrated poor corrosion resistance, with many vehicles requiring fuel system repairs due to mounting component failures. Fuel line routing created additional areas where protective barriers were compromised, often becoming corrosion initiation sites.
Exhaust system routing and mounting created thermal stress challenges that affected surrounding protection systems. The exhaust system’s proximity to frame components and the high-temperature operation associated with off-road driving created conditions where thermal cycling could cause coating degradation.
Heat shield systems provided insufficient coverage while utilizing mounting methods that created additional penetration points through protective coatings.
Regional variations in corrosion severity have demonstrated the critical relationship between environmental conditions and protection system adequacy.
Vehicles operated in northeastern states with heavy road salt usage have experienced the most severe problems, while those in southwestern desert environments have shown better longevity.
However, even vehicles in relatively benign climates have demonstrated premature corrosion problems when subjected to off-road use involving water crossings and muddy conditions.
5. Subaru Legacy/Outback (1995-2004)
The Subaru Legacy and Outback models from the late 1990s and early 2000s represent a significant disappointment in underbody protection, particularly given Subaru’s reputation for building durable all-wheel-drive vehicles capable of handling challenging weather conditions.
This generation of Legacy and Outback has become notorious for premature rear quarter panel corrosion, subframe deterioration, and structural rust problems that often appear within the first decade of service.
The Legacy/Outback’s underbody protection failures stem from design and manufacturing choices that prioritized cost control over long-term corrosion resistance.
The unibody construction utilized relatively thin steel sections with inadequate protective treatments, creating a structure that was inherently vulnerable to corrosion initiation in the challenging environmental conditions these vehicles were designed to handle.
The all-wheel-drive system’s complexity created additional penetration points and stress concentration areas that compromised the protection system’s integrity.
The factory coating system represented a minimal approach to corrosion protection that proved inadequate for the demanding conditions Legacy and Outback owners typically encounter.
The applied coating appeared to be a thin-film treatment that provided limited barrier protection against moisture, road salt, and chemical exposure associated with all-season driving.
This coating system demonstrated poor adhesion characteristics, with widespread reports of coating delamination occurring within the first few years of service.
The rear quarter panel area represents the most notorious failure point in the Legacy/Outback’s corrosion resistance. This area incorporates complex geometry with multiple panel joints, drainage channels, and structural reinforcements that create ideal conditions for water accumulation and debris retention.
The protective coatings in these areas proved inadequate for preventing corrosion initiation, while the panel design made early detection and repair extremely difficult.
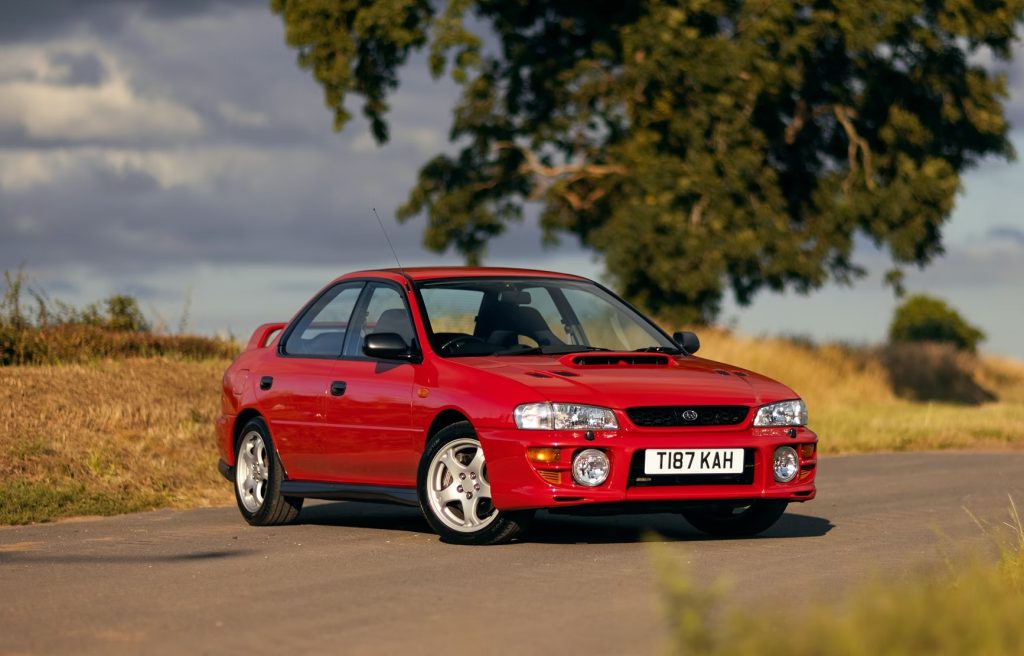
Structural design elements specific to the all-wheel-drive system created additional corrosion vulnerability points throughout the underbody. The rear differential mounting system and associated drivetrain components required complex brackets and mounting points that created stress concentration areas where coating damage was likely to occur.
The constant velocity joint boots and associated components often failed prematurely due to corrosion damage to the mounting and protection systems.
The fuel system installation contributed to structural corrosion problems through inadequate protection of the fuel tank mounting area and associated components.
The fuel tank mounting straps and brackets demonstrated poor corrosion resistance, while the fuel filler tube routing created additional penetration points through protective barriers.
Many Legacy and Outback vehicles have experienced fuel system mounting failures due to corrosion damage that compromised structural integrity. Exhaust system routing and mounting created thermal management challenges that affected surrounding protection systems.
The all-wheel-drive system’s complexity required routing exhaust components around drivetrain components, creating confined spaces where heat buildup could cause coating degradation. The exhaust system mounting points often became corrosion initiation sites that spread to surrounding structural areas.
The heating and air conditioning system installation created additional moisture management challenges that contributed to corrosion problems.
The evaporator housing and associated drainage systems often became compromised by debris accumulation, causing water to accumulate in areas where it could contact unprotected steel surfaces. The heater core installation required multiple penetrations through protective barriers that often became corrosion initiation sites.
The long-term consequences of these protection system failures have extended beyond individual vehicle problems to affect brand perception and resale values across the entire model line.
Prospective buyers of used Legacy and Outback vehicles from this era must budget for extensive corrosion repairs or risk purchasing vehicles with hidden structural damage that could compromise safety and roadworthiness.
Also Read: 5 EVs With the Best Torque Delivery and 5 With Lag