The relationship between time and engine performance is far more complex than most people realize. While conventional wisdom suggests that all mechanical components deteriorate with age, the reality is nuanced and fascinating.
Some engines actually improve their performance, efficiency, and reliability as they accumulate miles and years, while others begin their decline almost immediately after leaving the factory floor.
This phenomenon occurs due to various factors, including manufacturing tolerances, break-in procedures, metallurgy, and design philosophy.
Engines that get better with age typically benefit from the gradual wearing-in of components to optimal clearances, the seasoning of internal surfaces, and the settling of tolerances that may have been too tight from the factory.
These powerplants often feature robust construction, conservative tuning, and materials that improve with thermal cycling and mechanical stress.
Conversely, engines that deteriorate quickly usually suffer from aggressive tuning for maximum initial performance, complex systems that are prone to failure, or design compromises that prioritize short-term gains over long-term durability.
Understanding these characteristics can help enthusiasts make informed decisions about vehicle purchases and maintenance strategies. The following examination of ten notable engines reveals how engineering philosophy, manufacturing quality, and design intent ultimately determine whether an engine becomes a treasured classic or a maintenance nightmare as it ages.
5 Engines That Get Better With Age
These exceptionally engineered powerplants feature robust construction materials and precision-manufactured components that actually improve performance characteristics through years of proper break-in cycles and thermal conditioning across diverse operating conditions and maintenance schedules.
Their thoughtful engineering includes cast iron blocks, forged internal components, and conservative tuning parameters that resist the performance degradation typically created by thermal stress or mechanical wear during extended high-mileage operation.
From gradually loosening tolerances that reduce internal friction to improved oil circulation patterns that enhance lubrication efficiency, these remarkable engines continue developing smoother operation without experiencing power loss or reliability deterioration.
Owners report enhanced performance with these seasoned powerplants a longevity-enhancing quality feature that proves its worth through maintained power output and improved mechanical refinement throughout extended ownership periods spanning hundreds of thousands of miles.
1. Toyota 22R-E (1983-1995)
The Toyota 22R-E stands as perhaps the most compelling example of an engine that genuinely improves with age, earning legendary status among automotive enthusiasts and professionals alike.
This 2.4-liter four-cylinder engine, which powered everything from Toyota Pickups to 4Runners and Celicas, represents the pinnacle of conservative engineering philosophy combined with exceptional manufacturing quality.
The 22R-E’s improvement with age stems from its incredibly robust construction and conservative tuning. Toyota engineers designed this engine with generous bearing clearances, thick cylinder walls, and a cast-iron block that could withstand decades of abuse.
The initial break-in period for these engines often extended well beyond 50,000 miles, during which time the piston rings would properly seat, the cylinder walls would develop the ideal crosshatch pattern, and internal components would wear to optimal clearances.
What makes the 22R-E particularly remarkable is its tendency to actually gain power as it ages. Many owners report that their engines feel more responsive and produce better fuel economy after 100,000 miles than they did when new.
This phenomenon occurs because the factory tolerances were intentionally loose to ensure longevity, and the gradual wearing process creates tighter, more efficient sealing between components.
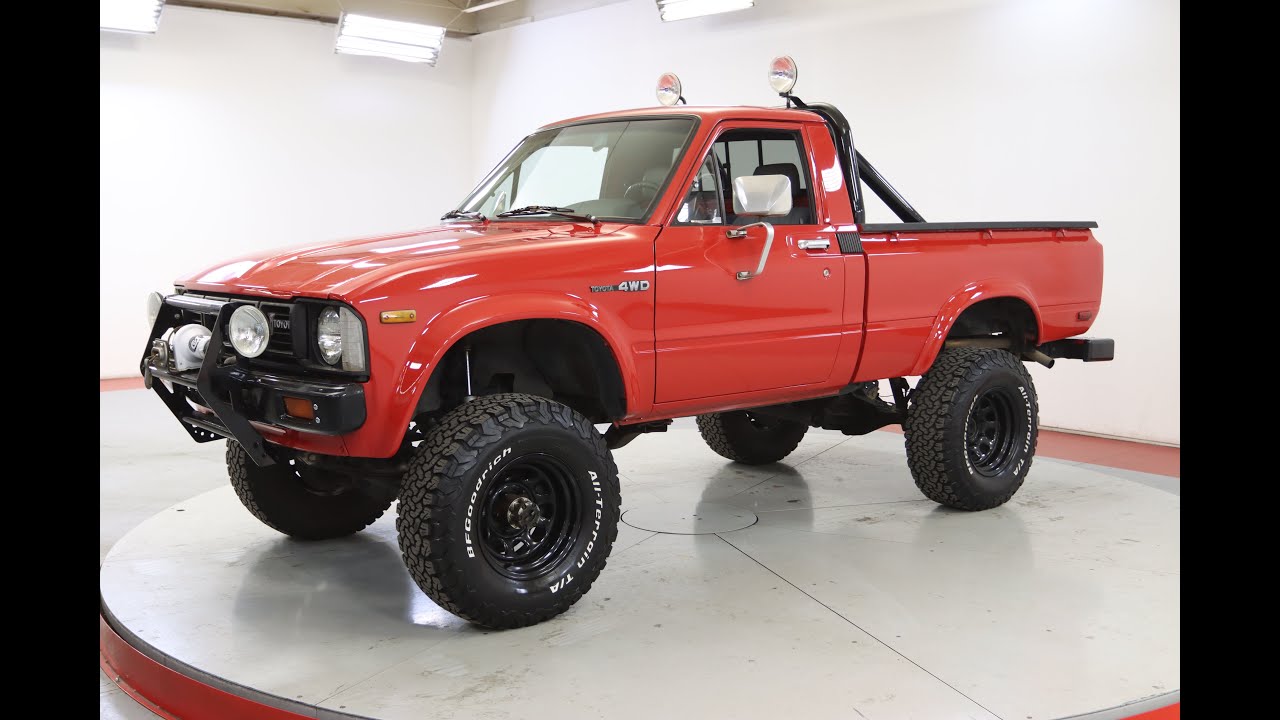
The engine’s fuel injection system, introduced in 1983, was similarly overbuilt and reliable. The electronic fuel injection components were designed with wide operating margins, meaning they continued to function accurately even as sensors and actuators aged.
The throttle body injection system was particularly robust, lacking the complexity of later multi-port systems while providing better fuel metering than carburetors.
Maintenance requirements for the 22R-E are minimal and straightforward. Regular oil changes, timing chain adjustments, and valve adjustments constitute the majority of required service.
The timing chain, rather than a belt, eliminates the risk of catastrophic interference engine damage, while the solid lifter valvetrain provides precise valve control that actually improves as components wear to optimal clearances.
The engine’s thermal management is exemplary, with a well-designed cooling system that prevents hot spots and maintains consistent operating temperatures.
The cylinder head design promotes even heat distribution, while the cast-iron construction provides excellent thermal mass for stable operating conditions. Perhaps most impressively, many 22R-E engines continue running strong well past 400,000 miles with nothing more than routine maintenance.
The combination of conservative engineering, excellent materials, and robust construction means these engines often outlast the vehicles they power, leading to a thriving market for 22R-E swaps into other chassis.
2. Mercedes-Benz OM617 Diesel (1974-1991)
The Mercedes-Benz OM617 diesel engine represents the golden age of passenger car diesel technology, demonstrating how proper engineering and conservative tuning can create an engine that becomes more refined and efficient as it accumulates miles.
This 3.0-liter inline-five naturally aspirated diesel powered various Mercedes-Benz models and established a reputation for longevity that remains unmatched in the automotive world.
The OM617’s improvement with age is rooted in its incredibly robust construction and the unique characteristics of diesel combustion. Mercedes engineers built this engine like a piece of industrial equipment, with forged steel crankshafts, massive bearing surfaces, and cylinder blocks that could withstand enormous pressures.
The initial break-in period for these engines often extended to 100,000 miles or more, during which time the engine would gradually reach peak efficiency.
One of the most remarkable aspects of the OM617 is how it becomes smoother and quieter with age. The initial diesel clatter that characterizes new engines gradually diminishes as components wear to optimal clearances.
The injection pump, manufactured by Bosch, is a mechanical masterpiece that improves its precision over time. The close-fitting tolerances in the injection pump benefit from the gradual wearing process, resulting in more accurate fuel delivery and better combustion characteristics.

The engine’s fuel efficiency often improves significantly after 150,000 miles, with many owners reporting economy figures that exceed the original specifications.
This improvement occurs because the piston rings seat properly over time, compression ratios stabilize at optimal levels, and the injection timing becomes more precise as components wear to their intended tolerances.
The OM617’s thermal management system is designed for the long haul, with oversized cooling passages and robust heat exchanger cores. The engine runs cooler as it ages, partly due to improved thermal conductivity between components and partly due to the optimization of clearances that occurs over time.
This thermal stability contributes to the engine’s longevity and continued improvement with age. Maintenance requirements are minimal and well-documented.
Regular oil changes with high-quality diesel oil, periodic valve adjustments, and occasional injection pump services constitute the majority of required maintenance. The engine’s design eliminates many common failure points found in gasoline engines, such as ignition systems and complex fuel delivery mechanisms.
The turbo variants of this engine family, while adding complexity, follow the same basic principles of improvement with age. The turbocharger systems were conservatively designed with wide operating margins, ensuring that boost pressures remain consistent even as components age.
Perhaps most remarkably, OM617 engines regularly accumulate over 500,000 miles with minimal major repairs. Many examples continue running strong well past 750,000 miles, with some documented cases exceeding one million miles.
This longevity, combined with the engine’s tendency to improve rather than deteriorate with age, has created a devoted following among diesel enthusiasts worldwide.
3. Honda B-Series VTEC (1989-2001)
The Honda B-Series VTEC engines, particularly the B16A and B18C variants, represent a fascinating case study in how high-performance engines can improve with proper break-in and aging.
These engines challenged conventional wisdom by demonstrating that high-revving, naturally aspirated powerplants could become more refined and efficient over time while maintaining their performance characteristics.
The B-Series VTEC improvement with age stems from Honda’s meticulous attention to manufacturing tolerances and material selection. These engines featured incredibly tight tolerances from the factory, which meant that the break-in period was crucial for optimal performance.
The initial 10,000 miles required careful operation, but subsequent performance often exceeded original specifications as components wore to ideal clearances.
The VTEC system itself benefits significantly from aging, as the variable valve timing mechanism becomes more precise over time. The hydraulic actuators that control cam lobe engagement wear to optimal clearances, resulting in smoother VTEC transitions and more consistent performance across the rev range.
Many owners report that their engines’ VTEC engagement becomes more seamless and powerful after 50,000 miles compared to when new. Honda’s choice of materials for the B-Series was exceptional, with aluminum blocks featuring iron cylinder liners and aluminum heads with excellent thermal conductivity.
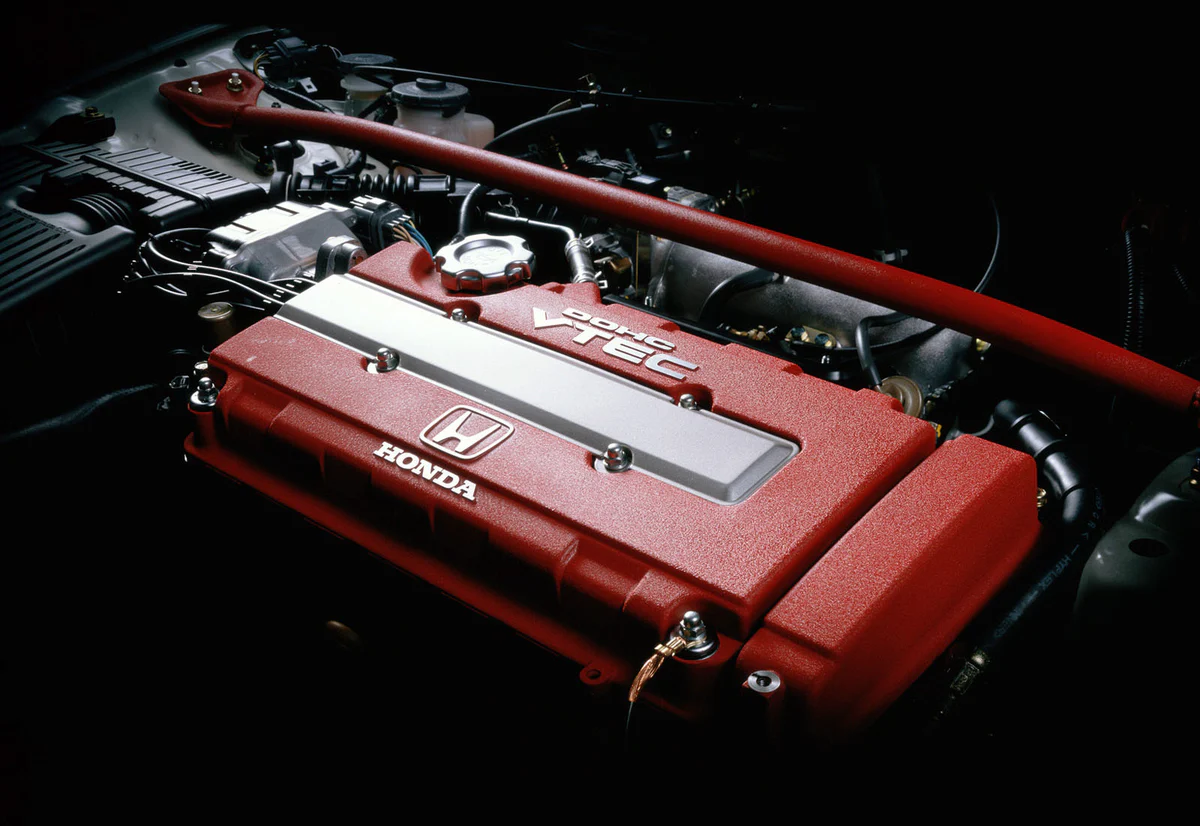
The thermal cycling that occurs during normal operation improves the metallurgical structure of these engines, creating stronger and more stable components over time. The cylinder bore finish becomes more optimal as the engine ages, contributing to better ring seal and improved compression.
The fuel injection system in B-Series engines was ahead of its time, featuring multi-point injection with precise control over fuel delivery. These systems become more accurate over time as fuel injectors break in and ECU adaptive learning optimizes fuel maps. The result is often improved fuel economy and more responsive throttle response after extended break-in periods.
One of the most remarkable aspects of B-Series VTEC engines is their ability to maintain compression ratios over time. While most engines experience gradual compression loss due to ring wear and valve seat recession, properly maintained B-Series engines often maintain or even slightly improve their compression ratios as components wear to optimal clearances.
The engine’s rev-happy nature contributes to its longevity and improvement with age. Regular high-RPM operation prevents carbon buildup, keeps ring tension optimal, and ensures that all engine components operate within their designed parameters.
This operational characteristic means that driven B-Series engines often perform better than garage queens. Maintenance requirements for B-Series VTEC engines are straightforward but critical.
Regular oil changes with high-quality oil, periodic valve adjustments, and attention to cooling system maintenance ensure continued improvement with age. The timing belt service intervals are non-negotiable, but the interference design means that proper maintenance prevents catastrophic failure.
The aftermarket support for B-Series engines is exceptional, with decades of development creating optimized parts and procedures. This support network ensures that these engines can continue improving and performing well beyond their original design life, with many examples running strong past 300,000 miles while maintaining their characteristic high-RPM performance.
4. Jeep 4.0L Inline-Six (1987-2006)
The Jeep 4.0L inline-six represents American automotive engineering at its finest, demonstrating how traditional design principles and robust construction can create an engine that genuinely improves with age and accumulated miles.
This engine powered various Jeep models for nearly two decades and earned a reputation for reliability and longevity that remains unmatched among American powerplants.
The 4.0L’s improvement with age is rooted in its incredibly robust construction and conservative engineering approach. Chrysler engineers designed this engine as an evolution of the earlier 258 cubic inch inline-six, incorporating modern fuel injection and electronic management while maintaining the proven architecture that had served the company well for decades.
The cast-iron block features thick cylinder walls, generous bearing surfaces, and cooling passages designed for extreme-duty operation. The initial break-in period for the 4.0L often extends well beyond conventional recommendations, with many owners reporting continued improvement in power delivery and fuel economy up to 100,000 miles.
This extended break-in occurs because of the engine’s conservative factory tolerances and the gradual seating of piston rings against the cylinder walls. The crosshatch pattern in the cylinders becomes optimal over time, creating a better ring seal and improved compression. One of the most remarkable characteristics of the 4.0L is its tendency to develop more torque as it ages.
The engine’s long-stroke design and relatively low compression ratio mean that it operates well within its stress limits, allowing components to wear to optimal clearances without compromising reliability. Many owners report that their engines feel stronger and more responsive after 150,000 miles than they did when new.
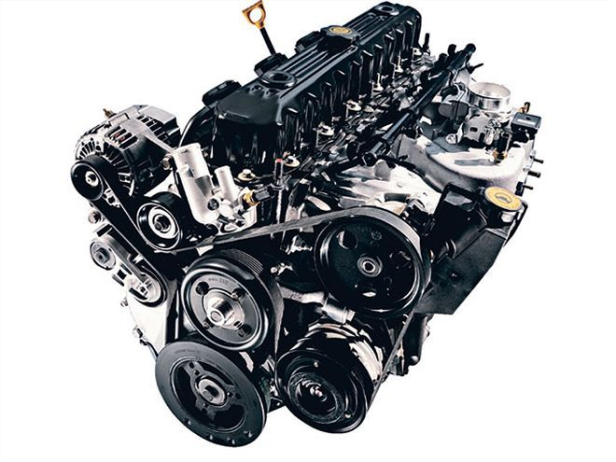
The fuel injection system used on the 4.0L was relatively simple but extremely reliable. The throttle body injection system provided better fuel metering than carburetors while avoiding the complexity of multi-port injection.
This system ages gracefully, with components that continue to function accurately even as they accumulate high mileage. The engine management system includes adaptive learning capabilities that optimize performance as the engine ages.
The 4.0L’s thermal management is exemplary, with a cooling system designed for extreme operating conditions. The engine runs cooler as it ages due to improved thermal conductivity between components and optimized clearances that develop over time. This thermal stability contributes to the engine’s longevity and continued improvement with age.
Maintenance requirements are minimal and straightforward, reflecting the engine’s truck-based design philosophy. Regular oil changes, periodic coolant system service, and occasional distributor maintenance constitute the majority of required service. The engine’s design eliminates many common failure points, such as timing belts and complex variable valve timing systems.
The 4.0L’s reputation for reliability extends to extreme-duty applications, where these engines regularly accumulate over 300,000 miles with minimal major repairs. Off-road enthusiasts particularly appreciate the engine’s ability to tolerate abuse while continuing to improve with age.
The combination of robust construction and conservative tuning means that even neglected examples often respond well to proper maintenance and continue running strong.
Perhaps most impressively, the 4.0L has become increasingly sought after as vehicle manufacturers have moved away from naturally aspirated inline-six engines.
The engine’s combination of reliability, performance, and improvement with age has created a devoted following among enthusiasts who recognize its exceptional qualities.
Also Read: 5 EVs With the Best Regenerative Paddles and 5 With Fixed Regeneration
5. Porsche 911 Air-Cooled Flat-Six (1963-1998)
The Porsche 911 air-cooled flat-six represents one of the most remarkable examples of an engine that not only improves with age but also becomes more characterful and engaging over time.
These engines, spanning over three decades of development, demonstrate how proper engineering and meticulous manufacturing can create power plants that become more desirable as they accumulate miles and years.
The improvement of air-cooled 911 engines with age stems from Porsche’s exceptional engineering standards and the unique characteristics of air-cooled operation.
These engines were built to incredibly tight tolerances using premium materials, with many components hand-fitted during assembly. The initial break-in period often extended to 10,000 miles or more, during which time the engine would gradually reach its peak performance potential.
The air-cooling system itself contributes significantly to the engine’s improvement with age. Unlike water-cooled engines that can suffer from cooling system failures and uneven thermal distribution, air-cooled engines maintain consistent operating temperatures that improve thermal efficiency over time.
The aluminum construction and magnesium crankcases benefit from thermal cycling, creating stronger and more stable components as the engine ages. One of the most remarkable aspects of air-cooled 911 engines is how they develop more character and personality with age.
The distinctive sound becomes more refined, the power delivery becomes more linear, and the overall driving experience improves as components wear to optimal clearances. Many enthusiasts prefer high-mileage examples over low-mileage garage queens because of these improved characteristics.

The mechanical fuel injection systems used on many air-cooled 911s improve their precision over time. The Bosch mechanical injection pumps and related components benefit from the gradual wearing process, resulting in more accurate fuel delivery and better throttle response. These systems, while complex, are remarkably durable and continue to function accurately even after decades of operation.
The engine’s lubrication system is designed for high-performance operation, with dry sump oiling that ensures consistent oil pressure under all operating conditions.
This system ages gracefully, with components that continue to function effectively even as they accumulate high mileage. The oil cooling system becomes more efficient over time as heat exchangers season and thermal management optimizes.
Maintenance requirements for air-cooled 911 engines are well-documented and straightforward, though they require attention to detail. Regular oil changes with high-quality oil, periodic valve adjustments, and attention to cooling system cleanliness ensure continued improvement with age.
The engines respond well to regular exercise, with driven examples typically showing better long-term reliability than stored vehicles. The aftermarket support for air-cooled 911 engines is exceptional, with specialists worldwide who understand these engines intimately.
This support network has created optimized maintenance procedures and upgraded components that enhance the engines’ natural tendency to improve with age. Many specialists report that properly maintained air-cooled 911 engines run better at 100,000 miles than they did when new.
Perhaps most remarkably, air-cooled 911 engines have become increasingly valuable as they age, with well-maintained examples commanding premium prices in the collector market. This appreciation reflects not only their rarity but their genuine improvement in character and performance over time, making them among the most desirable engines ever produced.
5 Engines That Get Worse With Age
These deteriorating power plants suffer from accelerated performance decline due to complex engineering designs, premium materials sensitivity, and tight manufacturing tolerances that create mounting reliability issues and reduced power output throughout normal aging processes and maintenance cycles.
Their problematic engineering includes aluminum construction, advanced direct injection systems, and aggressive tuning parameters that amplify the wear patterns typically associated with thermal cycling, carbon buildup, or component fatigue during high-mileage operation.
From gradually developing oil consumption issues to experiencing reduced power delivery that requires expensive rebuilding procedures, these engines demand increasing maintenance attention and costly repairs.
Owners discover that while these powerplants may offer impressive initial performance and fuel economy, their aging characteristics create escalating ownership costs and reliability concerns that significantly impact long-term vehicle value and require frequent diagnostic attention to maintain acceptable operation levels.
1. BMW N54 Twin-Turbo (2006-2016)
The BMW N54 twin-turbo inline-six represents a cautionary tale of how advanced technology and aggressive tuning can create an engine that deteriorates rapidly with age, despite impressive initial performance.
This 3.0-liter twin-turbocharged engine was BMW’s first production twin-turbo powerplant and showcased cutting-edge technology that ultimately proved problematic in long-term ownership.
The N54’s decline with age stems from its incredibly complex design and aggressive tuning from the factory. BMW engineers pushed this engine to its limits to achieve impressive power figures, resulting in components that operate near their stress limits from day one.
The twin-turbo configuration, while providing excellent performance, introduces multiple potential failure points that become increasingly problematic as the engine ages.
One of the most significant issues with the N54 is its high-pressure fuel pump system, which begins to deteriorate almost immediately after the warranty period expires.
The direct injection system requires extremely high fuel pressures, and the mechanical high-pressure pump struggles to maintain consistent pressure as it ages. This degradation results in poor drivability, reduced power output, and expensive repair bills that can exceed the vehicle’s value.
The turbocharger system presents another major concern, with the twin turbos experiencing wastegate failures, bearing deterioration, and boost control problems that become increasingly severe with age.
The complexity of the twin-turbo setup means that failures often cascade, with one turbo failure potentially damaging the other due to imbalanced airflow and backpressure conditions.

The engine’s carbon buildup issues are legendary among BMW owners, with direct injection causing severe carbon deposits on intake valves that progressively worsen performance.
Unlike port-injected engines, where fuel helps clean the valves, direct injection means that carbon accumulation is inevitable and requires expensive professional cleaning services to maintain engine performance.
The N54’s cooling system is another weak point that becomes increasingly problematic with age. The engine generates significant heat due to its aggressive tuning and twin-turbo configuration, and the cooling system components struggle to cope with these thermal loads over time.
Water pump failures, thermostat issues, and coolant leaks become increasingly common as the engine ages, often resulting in catastrophic overheating damage.
The engine management system, while sophisticated, becomes increasingly problematic as sensors and actuators age. The complex network of sensors required to manage the twin-turbo system, direct injection, and variable valve timing begins to fail unpredictably, resulting in poor drivability and expensive diagnostic procedures.
The adaptive learning capabilities that initially optimize performance become counterproductive as hardware deteriorates. Maintenance costs for the N54 escalate dramatically with age, often exceeding the vehicle’s depreciated value.
The engine requires premium synthetic oil, frequent carbon cleaning services, and regular replacement of expensive components like fuel pumps, turbochargers, and various sensors. Many owners discover that maintenance costs exceed their vehicle’s worth well before the engine reaches high mileage.
The N54’s reliability issues have become so well-documented that they significantly impact resale values and long-term ownership satisfaction. While the engine delivers impressive performance when new, its rapid deterioration with age makes it one of the least desirable BMW engines for long-term ownership. The combination of complex technology and aggressive tuning creates a perfect storm of reliability issues that worsen progressively with age.
2. Audi/Volkswagen 2.7T V6 (1997-2005)
The Audi/Volkswagen 2.7T biturbo V6 represents one of the most notorious examples of an engine that deteriorates rapidly with age, despite delivering impressive performance when new.
This 2.7-liter twin-turbocharged V6 powered various Audi models and gained a reputation for expensive failures that become increasingly severe as the engine accumulates miles.
The 2.7T’s decline with age is rooted in its aggressive tuning and inadequate supporting systems. Audi engineers designed this engine to deliver sports car performance in luxury sedans, pushing the twin-turbo configuration to its limits to achieve impressive power figures.
However, the supporting systems, particularly the cooling and lubrication systems, proved inadequate for long-term reliability under these stress levels.
The most infamous problem with the 2.7T is its tendency to develop severe sludge buildup that progressively worsens with age. The combination of high operating temperatures, extended oil change intervals, and marginal oil circulation creates conditions where conventional motor oil breaks down and forms sludge deposits throughout the engine.
This sludge accumulation restricts oil flow, leading to bearing damage, turbo failure, and eventually complete engine destruction. The turbocharger system presents another major reliability concern that becomes increasingly problematic with age.
The twin K03 turbos operate at extremely high temperatures and pressures, and their compact size allows them to spin at incredibly high RPMs. As the engine ages, oil contamination and heat cycling cause the turbo bearings to deteriorate, leading to catastrophic failures that often damage the engine internals due to metal contamination.
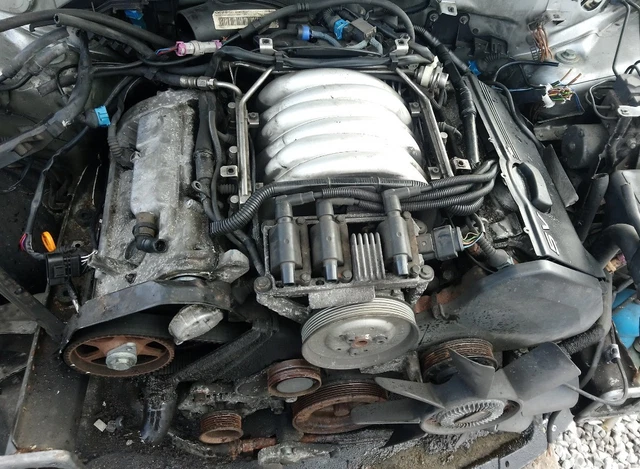
The engine’s cooling system is fundamentally inadequate for the heat loads generated by the twin-turbo configuration. As the engine ages, cooling system components fail with increasing frequency, and the marginal cooling capacity means that even minor failures can result in overheating and severe engine damage.
The complex cooling system layout makes maintenance expensive and failure diagnosis difficult. The 2.7T’s timing system presents another concern that worsens with age.
The timing belt system requires precise maintenance intervals, and interference engine design means that belt failure results in catastrophic valve damage. As the engine ages, belt tensioner and idler failures become more common, increasing the risk of timing belt failure and complete engine destruction.
The engine management system becomes increasingly unreliable as components age, with various sensors and actuators failing unpredictably. The complex boost control system, variable valve timing, and emissions controls create a web of interdependent systems that become less reliable over time. Diagnostic procedures become increasingly complex and expensive as the engine ages.
Maintenance costs for the 2.7T escalate dramatically with age, often exceeding the vehicle’s value well before high mileage is reached. The engine requires frequent oil changes with expensive synthetic oil, regular turbo system maintenance, and preemptive replacement of various components to prevent catastrophic failures.
Many owners discover that proper maintenance costs more than the depreciated vehicle’s worth. The 2.7T’s reputation for reliability issues has become so severe that it significantly impacts resale values and ownership satisfaction.
While the engine delivers impressive performance when properly maintained and relatively new, its rapid deterioration with age makes it one of the least desirable engines for long-term ownership. The combination of sludge issues, turbo failures, and cooling system inadequacies creates a perfect storm of reliability problems that worsen progressively with age.
3. Range Rover 4.6L V8 (1994-2002)
The Range Rover 4.6L V8, based on the Rover/Buick aluminum engine architecture, represents a prime example of how poor manufacturing quality and design compromises can create an engine that deteriorates rapidly with age.
This engine powered various Land Rover products during the 1990s and early 2000s, earning a reputation for catastrophic failures that became increasingly common as the engine accumulated miles.
The 4.6L V8’s decline with age stems from fundamental design flaws and manufacturing quality issues that were never adequately addressed during production.
The aluminum block construction, while lightweight, suffers from liner stability problems that worsen progressively with thermal cycling. The wet cylinder liners are prone to dropping or shifting, resulting in coolant contamination of the oil and eventual engine destruction.
One of the most notorious problems with the 4.6L V8 is its tendency to suffer liner drop failures that become increasingly common with age. The aluminum block expands and contracts with temperature changes, gradually loosening the press-fit cylinder liners.
This linear movement creates gaps that allow coolant to enter the combustion chambers and oil passages, resulting in hydro-lock, bearing damage, and complete engine failure.
The cooling system presents another major concern that becomes increasingly problematic as the engine ages. The aluminum construction generates significant thermal stresses, and the cooling system struggles to maintain consistent temperatures throughout the engine.
As components age, cooling system failures become more common, often resulting in overheating that accelerates liner drop and other thermal-related failures.
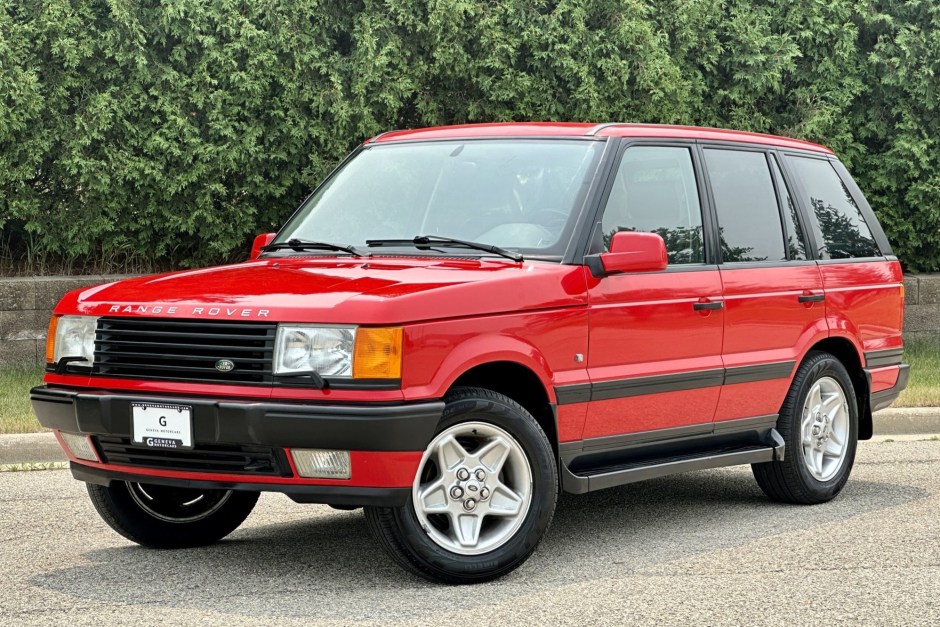
The engine’s head gasket design is fundamentally flawed, with the sealing system unable to cope with the thermal stresses generated by the aluminum construction. Head gasket failures become increasingly common with age, often recurring even after professional repairs.
The multi-layer steel gaskets used in later production runs provided some improvement, but never fully resolved the fundamental design issues. The 4.6L V8’s electrical system becomes increasingly unreliable as the engine ages, with various sensors and actuators failing unpredictably.
The engine management system requires precise inputs from multiple sensors, and failures often result in poor drivability and diagnostic challenges. The complexity of the system means that troubleshooting becomes increasingly expensive as the engine ages.
The lubrication system suffers from design compromises that become more problematic with age. The oil pump drive system is prone to failure, potentially resulting in complete loss of oil pressure and catastrophic engine damage.
The oil circulation patterns in the aluminum block create hot spots that contribute to oil breakdown and sludge formation over time. Maintenance costs for the 4.6L V8 escalate dramatically with age, often making the engine economically unviable for long-term ownership.
The specialized aluminum construction requires expensive coolants and specific maintenance procedures, while the potential for catastrophic failures means that even well-maintained examples face expensive repair bills. Many owners discover that engine replacement costs exceed the vehicle’s value.
The reputation of the 4.6L V8 has become so poor that it significantly impacts resale values and ownership satisfaction. While the engine provides adequate performance when new and properly maintained, its rapid deterioration with age and propensity for catastrophic failures make it one of the least desirable engines for long-term ownership.
The combination of liner drop issues, cooling system problems, and manufacturing quality concerns creates a perfect storm of reliability problems that worsen progressively with age.
4. Chrysler 2.7L V6 (1998-2010)
The Chrysler 2.7L V6 stands as one of the most problematic engines in modern automotive history, demonstrating how cost-cutting measures and design compromises can create a powerplant that deteriorates rapidly and catastrophically with age.
This engine powered various Chrysler, Dodge, and Plymouth models and quickly earned a reputation for expensive failures that often totaled the vehicles they powered.
The 2.7L V6’s rapid decline with age stems from fundamental design flaws and manufacturing shortcuts that prioritized initial cost savings over long-term reliability.
The engine features an aluminum block with iron sleeves, and the dissimilar metals create thermal expansion issues that worsen with age and thermal cycling. The cooling system design is inadequate for the engine’s heat generation, creating hot spots that contribute to accelerated wear and component failure.
The most notorious problem with the 2.7L V6 is its tendency to develop severe oil sludge that progressively worsens with age, eventually leading to complete engine destruction.
The combination of inadequate oil circulation, high operating temperatures, and poor crankcase ventilation creates conditions where even high-quality motor oil breaks down and forms thick sludge deposits. This sludge blocks oil passages, starves bearings of lubrication, and eventually causes catastrophic engine failure.
The timing chain system presents another major reliability concern that becomes increasingly problematic as the engine ages. The engine uses a complex timing chain setup with multiple chains, tensioners, and guides that are prone to premature wear and failure.
As the engine ages, chain stretch and tensioner failure become increasingly common, potentially resulting in valve-to-piston contact and complete engine destruction.

The cooling system is fundamentally inadequate for the engine’s thermal loads, and failures become increasingly common with age. The water pump, thermostat, and various cooling system components fail regularly, often without warning.
The marginal cooling capacity means that even minor cooling system failures can result in rapid overheating and severe engine damage, including warped heads and blown gaskets.
The 2.7L V6’s oil system design contributes significantly to its reliability problems. The oil pump drive system is prone to failure, and the oil passages in the aluminum block are inadequately sized for proper circulation.
As the engine ages, oil pressure drops and circulation becomes increasingly restricted, accelerating wear and increasing the likelihood of catastrophic failure.
The engine management system becomes increasingly unreliable as components age, with various sensors and actuators failing unpredictably. The complex emissions control systems create additional potential failure points, and diagnostic procedures become increasingly difficult as multiple systems interact unpredictably.
The cost of diagnosis and repair often exceeds the vehicle’s depreciated value. Maintenance requirements for the 2.7L V6 are extensive and expensive, often making long-term ownership economically unviable.
The engine requires frequent oil changes with expensive synthetic oil, regular cooling system maintenance, and preemptive replacement of various components to prevent catastrophic failures. Even with meticulous maintenance, many examples still suffer major failures well before reaching high mileage.
The reputation of the 2.7L V6 has become so notorious that it significantly impacts resale values and has resulted in numerous class-action lawsuits against Chrysler.
Many automotive professionals recommend immediate engine replacement when purchasing vehicles equipped with this engine, regardless of apparent condition.
The combination of sludge issues, timing chain problems, and cooling system inadequacies creates a perfect storm of reliability problems that make this engine one of the worst choices for long-term ownership.
5. Ford 6.0L Power Stroke Diesel (2003-2007)
The Ford 6.0L Power Stroke diesel represents one of the most problematic engines in modern diesel history, demonstrating how emissions compliance pressures and design compromises can create a powerplant that deteriorates rapidly and expensively with age.
This International-built engine powered Ford’s Super Duty trucks during the mid-2000s and quickly earned a reputation for catastrophic failures that often exceeded the vehicle’s value to repair.
The 6.0L Power Stroke’s decline with age stems from its incredibly complex emissions control systems and fundamental design flaws that were never adequately addressed during production.
The engine was designed to meet stringent emissions standards while maintaining the performance expectations of diesel truck buyers, resulting in compromises that prioritized short-term compliance over long-term reliability.
The most notorious problem with the 6.0L Power Stroke is its Exhaust Gas Recirculation (EGR) system, which becomes increasingly problematic with age and creates cascading failures throughout the engine.
The EGR cooler is prone to cracking and leaking, allowing coolant to enter the exhaust system and potentially causing hydro-lock and catastrophic engine damage. The EGR valve becomes clogged with soot over time, creating backpressure issues that affect turbocharger operation and overall engine performance.
The cooling system presents another major concern that becomes increasingly severe as the engine ages. The 6.0L generates enormous heat loads, and the cooling system struggles to cope with these thermal demands.
The oil cooler is prone to failure, often contaminating the cooling system with oil and requiring expensive repairs. Head gasket failures become increasingly common with age, often recurring even after professional repairs due to fundamental design inadequacies.

The turbocharger system deteriorates rapidly with age, with the variable geometry turbo suffering from carbon buildup and actuator failures that become increasingly severe over time.
The complex variable geometry system requires precise control, and as components age, the turbo often fails to respond properly to commands, resulting in poor performance and potential engine damage from over-boost or under-boost conditions.
The fuel injection system presents additional reliability concerns that worsen with age. The high-pressure oil activation system used to operate the fuel injectors is prone to leaks and pressure loss, resulting in poor performance and potential injector damage.
The fuel injectors themselves are expensive and prone to failure, often requiring replacement in sets to maintain proper engine operation. The 6.0L Power Stroke’s engine management system becomes increasingly unreliable as components age, with various sensors and actuators failing unpredictably.
The complex emissions control systems create a web of interdependent components that must function perfectly for proper engine operation. As these systems age, failures become more common, and diagnostic procedures become increasingly complex and expensive.
Maintenance costs for the 6.0L Power Stroke escalate dramatically with age, often making long-term ownership economically unviable. The engine requires expensive synthetic oil, frequent fuel filter changes, and regular maintenance of complex emissions systems.
The potential for catastrophic failures means that even well-maintained examples face expensive repair bills that can exceed the vehicle’s value. The reputation of the 6.0L Power Stroke has become so poor that it significantly impacts resale values and has spawned an entire industry of aftermarket solutions aimed at improving reliability.
Many owners choose to delete emissions systems entirely, though this approach creates legal and environmental concerns. The combination of EGR system failures, cooling system inadequacies, and turbocharger problems creates a perfect storm of reliability issues that make this engine one of the least desirable choices for long-term diesel truck ownership.
Also Read: 5 Hybrids With the Best Traction Off-Road and 5 Slipping Behind