The automotive world is filled with engineering marvels and spectacular failures, nowhere more evident than in the realm of high-performance engines.
Some powerplants become legends, running hundreds of thousands of miles while delivering exhilarating performance year after year. Others, despite impressive specifications and marketing hype, become cautionary tales of mechanical fragility and premature failure.
The difference between a performance engine that lasts and one that burns out fast often comes down to fundamental engineering philosophy. Engines built to last typically feature conservative design margins, proven metallurgy, robust cooling systems, and meticulous attention to lubrication and thermal management.
They prioritize durability over absolute peak power, understanding that sustained performance over decades matters more than dyno-sheet bragging rights.
Conversely, engines that burn out fast often push boundaries too aggressively, sacrificing long-term reliability for impressive performance figures.
They may feature exotic materials that sound impressive but haven’t been thoroughly tested, cooling systems inadequate for real-world conditions, or internal components stressed beyond their sustainable limits. This analysis examines ten notable performance engines, five celebrated for their longevity and five infamous for their fragility.
Understanding what separates the legends from the lemons provides valuable insight into automotive engineering principles and helps enthusiasts make informed decisions about which performance machines will reward long-term ownership versus those that promise excitement but deliver heartbreak.
5 Engines Built to Last
These exceptionally robust powerplants feature conservative tuning parameters and precision-engineered internals that deliver sustained high performance through years of demanding track use and spirited driving across diverse operating conditions and maintenance schedules.
Their thoughtful engineering includes forged pistons, reinforced crankshafts, and effective cooling systems that resist the thermal stress typically created by repeated redline operation or sustained high-load driving during racing applications and performance driving events.
From track day sessions that demand consistent power delivery to canyon carving scenarios where reliability matters for safety, these remarkable engines continue providing full performance without developing internal component failures or power degradation issues.
Owners report decades of enthusiastic driving with these bulletproof performance solutions a durability-enhancing quality feature that proves its worth through maintained power output and extended component life throughout aggressive driving applications and regular high-performance usage scenarios.
1. Toyota 2JZ-GTE – The Bulletproof Turbo Icon
The Toyota 2JZ-GTE stands as perhaps the most legendary performance engine of the 1990s, earning mythical status among tuners and enthusiasts worldwide.
First introduced in 1991 in the Toyota Aristo and later powering the iconic Supra Turbo, this 3.0-liter twin-turbocharged inline-six has achieved something few engines manage: it’s simultaneously capable of massive power increases while maintaining exceptional reliability in stock form.
The foundation of the 2JZ-GTE’s legendary durability lies in its massively overbuilt construction. Toyota’s engineers designed this engine with cast-iron block construction featuring a closed-deck design that provides exceptional rigidity.
The cylinder walls are thick enough to handle significant bore increases, while the forged steel crankshaft and connecting rods were engineered with safety margins that far exceeded the engine’s stock power output. This conservative approach to internal component strength meant the engine could handle substantially more power than Toyota initially extracted from it.
The head design showcases Toyota’s commitment to longevity. The aluminum cylinder head features four valves per cylinder actuated by dual overhead camshafts, with Toyota’s variable valve timing system ensuring optimal performance across the rev range.
The head gasket, often a weak point in turbocharged engines, was engineered with multiple layers of steel and advanced sealing technology that rarely fails when properly maintained. The combustion chamber design promotes efficient burning while managing heat effectively, contributing to the engine’s ability to run reliably even under boost.
Turbocharging implementation on the 2JZ-GTE demonstrates masterful engineering restraint. The sequential twin-turbo system uses relatively small turbos that spool quickly while avoiding the extreme heat and pressure that can destroy engine internals.

The primary turbo operates alone at lower RPMs, providing excellent throttle response, while the secondary turbo joins in at higher RPMs for maximum power. This staged approach reduces thermal stress compared to single large turbo setups, contributing significantly to the engine’s longevity.
The lubrication system deserves special recognition for its role in the engine’s durability. The oil pump provides generous flow rates, while the oil passages are sized to ensure adequate lubrication even under extreme conditions.
The oil cooling system, including an oil cooler on many applications, helps maintain optimal oil temperatures during spirited driving. Toyota’s specification for oil change intervals and recommended oil viscosities reflects their understanding of what this high-performance engine needs to survive long-term.
Cooling system design further demonstrates Toyota’s commitment to durability. The radiator capacity, water pump flow rates, and coolant passage sizing all exceed what would be minimally adequate, providing thermal management margins that prevent overheating even during track use.
The intercooler system effectively manages intake air temperatures, keeping combustion temperatures within safe limits and preventing detonation that could destroy pistons and valves.
What truly sets the 2JZ-GTE apart is its remarkable ability to handle power modifications. Stock engines routinely handle 500-600 horsepower with basic bolt-on modifications, while built examples have exceeded 1,000 horsepower while maintaining street reliability.
This capability stems from the engine’s fundamental overengineering. Toyota built in safety margins that tuners have exploited for decades. Maintenance requirements for the 2JZ-GTE remain reasonable despite its performance capabilities.
Regular oil changes with quality synthetic oil, attention to the cooling system, and periodic replacement of wear items like the timing belt and water pump will keep these engines running for hundreds of thousands of miles.
Many examples have exceeded 200,000 miles while maintaining their original performance capabilities, a testament to Toyota’s engineering excellence.
The 2JZ-GTE’s legacy extends far beyond its original applications. It has become the engine of choice for numerous swaps, powering everything from drift cars to drag racers to road racing machines.
This widespread adoption speaks to both its reliability and its tuning potential, qualities that have made it one of the most respected performance engines ever produced.
2. Chevrolet LS Series – Small Block Perfection Evolved
The Chevrolet LS series represents the culmination of decades of small-block V8 evolution, combining modern materials and manufacturing techniques with proven architectural concepts.
Introduced in 1997 with the LS1, this engine family has become the gold standard for V8 performance, offering exceptional power, reliability, and modification potential across numerous applications from Corvettes to pickup trucks.
The LS architecture builds upon the successful small-block Chevrolet foundation while incorporating significant improvements in every major system.
The aluminum block construction on most variants reduces weight while providing excellent thermal conductivity for improved heat dissipation. The deep-skirt design with six-bolt main bearing caps creates exceptional bottom-end strength, allowing the engine to handle significant power increases without internal modifications.
The cylinder bore spacing and deck height provide room for displacement increases, making the LS platform incredibly versatile for different applications.
Internal component quality sets the LS apart from many competitors. The forged steel crankshafts feature generous journal sizes and fillet radii that resist fatigue failure.
Connecting rods, while powder-metal in most applications, are surprisingly strong and rarely fail even in modified applications. The pistons feature modern alloys and coatings that resist heat and wear, while the piston rings use advanced materials and face coatings for improved sealing and longevity.
The cylinder head design showcases modern combustion science applied to pushrod architecture. The cathedral port design on early LS heads and later rectangular port configurations provide excellent airflow while maintaining good low-RPM torque characteristics.
The combustion chamber shape promotes efficient burning and knock resistance, allowing the use of higher compression ratios on pump gasoline. The valvetrain, featuring roller lifters and rocker arms, reduces friction while providing precise valve control across the entire RPM range.
Fuel injection and engine management systems on LS engines represent significant advances over earlier designs. The electronic throttle body provides precise airflow control, while the sophisticated engine management system optimizes fuel delivery, ignition timing, and other parameters for maximum efficiency and power.
The coil-on-plug ignition system eliminates distributors and spark plug wires, reducing maintenance while improving combustion consistency. These systems contribute significantly to the engine’s reliability and performance across all operating conditions.
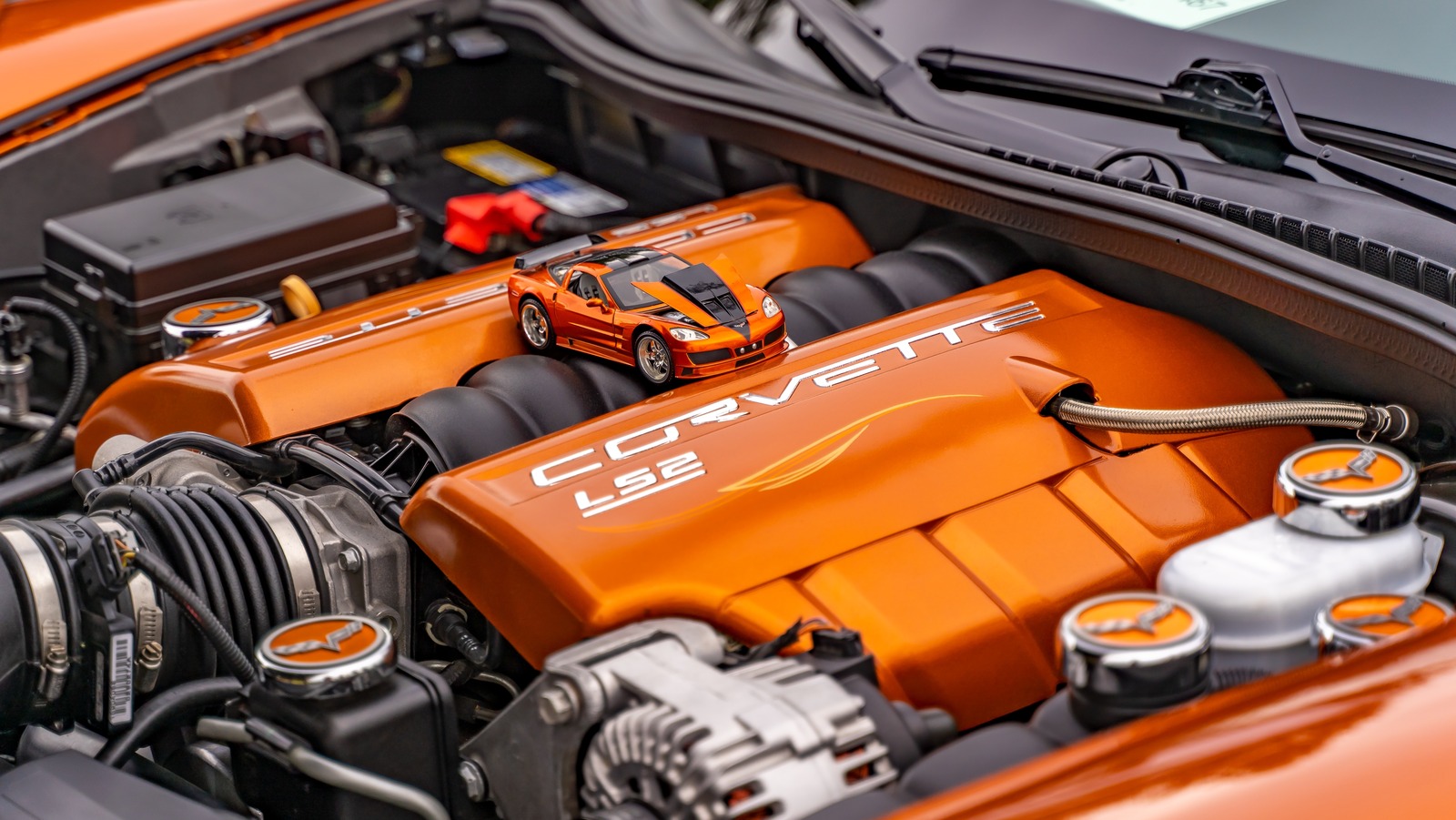
The oiling system demonstrates Chevrolet’s attention to lubrication engineering. The oil pump provides adequate flow for high-RPM operation, while the oil passages are sized and positioned to ensure all critical components receive proper lubrication.
The oil pan design in most applications provides adequate capacity for extended high-performance driving. The recommended oil change intervals, while longer than older engines, reflect the improved materials and tighter manufacturing tolerances that reduce wear rates.
Cooling system capability matches the engine’s performance potential. The water pump flow rates, combined with properly sized radiators and cooling passages, maintain optimal operating temperatures even during demanding use.
The aluminum construction aids heat dissipation, while the combustion chamber design helps manage peak temperatures during high-performance operation. The cooling system’s ability to maintain consistent temperatures contributes significantly to the engine’s longevity.
Manufacturing quality represents a significant advance over earlier American V8s. Computer-controlled machining ensures consistent tolerances, while improved metallurgy and quality control reduce the likelihood of manufacturing defects.
The assembly process incorporates lessons learned from decades of engine production, resulting in remarkably consistent performance and reliability across the entire production run.
Modification potential is where the LS truly shines. Stock engines routinely handle 500+ horsepower with basic modifications like camshafts, headers, and tuning.
The strong bottom end allows significant displacement increases through stroker kits, while the head design responds well to porting and larger valves. Forced induction applications regularly exceed 700 horsepower while maintaining street reliability, demonstrating the fundamental strength of the architecture.
Maintenance requirements remain reasonable despite the engine’s performance capabilities. Regular oil changes with quality oil, attention to the cooling system, and periodic replacement of wear items will keep LS engines running reliably for hundreds of thousands of miles.
Many high-mileage examples continue performing at original specifications, a testament to the engine’s fundamental durability. The LS series’ widespread adoption across GM’s lineup, from economy cars to supercars, demonstrates its versatility and reliability.
This broad application base has created an enormous aftermarket support network, making parts readily available and affordable. The engine’s popularity in swap applications further validates its reputation for reliability and performance, as enthusiasts consistently choose LS power for projects where failure is not an option.
3. BMW S54 – High-Revving Naturally Aspirated Masterpiece
The BMW S54 represents the pinnacle of naturally aspirated inline-six development, combining traditional BMW engineering excellence with modern materials and manufacturing techniques.
Introduced in 2000 and powering the E46 M3, Z3 M Coupe/Roadster, and Z4 M models, this 3.2-liter engine delivers exhilarating performance while maintaining the reliability that discerning BMW enthusiasts demand from their ultimate driving machines.
The foundation of the S54’s exceptional character lies in its sophisticated bottom-end construction. The aluminum block features a bedplate design that bolts to the main bearing caps, creating exceptional rigidity that allows the engine to rev freely to its 8,000 RPM redline without harmful vibrations.
The forged steel crankshaft is fully counterweighted and balanced to aircraft standards, ensuring smooth operation throughout the rev range. The connecting rods, also forged steel, feature aggressive weight reduction while maintaining the strength necessary for high-RPM operation.
This attention to internal balance and strength allows the S54 to deliver its power smoothly and reliably across its entire operating range. The cylinder head design showcases BMW’s mastery of airflow engineering.
The individual throttle bodies for each cylinder eliminate intake manifold compromises, providing immediate throttle response and optimal airflow distribution. The dual VANOS variable valve timing system optimizes valve events for both low-end torque and high-RPM power, while the aggressive cam profiles enable the engine to breathe efficiently at its lofty redline.
The combustion chamber design promotes efficient burning while resisting knock, allowing the use of high compression ratios that enhance both power and efficiency.
Lubrication system design reflects BMW’s understanding of high-performance engine requirements. The dry-sump oil system eliminates oil starvation concerns during high-G cornering and provides consistent lubrication regardless of vehicle attitude. The oil pump provides generous flow rates, while the oil cooler maintains optimal temperatures during track use.
The oil passages are sized to ensure adequate lubrication even at maximum RPM, while the recommended oil specifications and change intervals reflect the demands of high-performance operation.
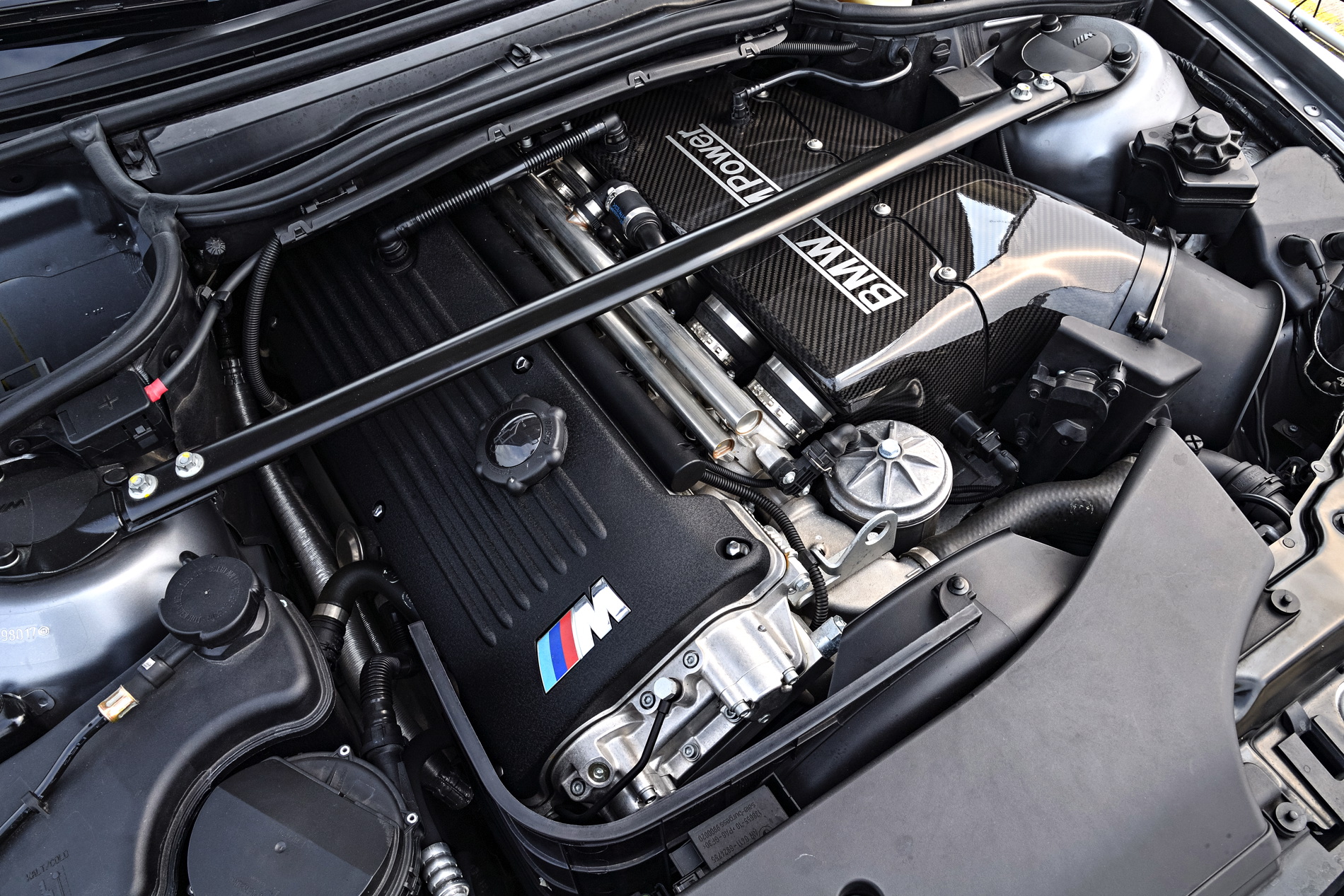
The cooling system demonstrates BMW’s commitment to thermal management in high-performance applications. The radiator capacity and cooling fan capabilities exceed what would be minimally adequate, providing thermal margins for track use and spirited driving.
The water pump flow rates ensure consistent coolant circulation, while the thermostat and temperature sensors maintain optimal operating temperatures across all conditions. The cooling system’s ability to maintain stable temperatures contributes significantly to the engine’s reliability and performance consistency.
Electronic engine management on the S54 represents sophisticated integration of multiple systems. The engine control unit optimizes fuel delivery, ignition timing, and valve timing for maximum performance while protecting the engine from potentially damaging conditions.
The knock sensors detect early signs of detonation and adjust timing accordingly, while the various temperature and pressure sensors provide comprehensive monitoring of engine health. This electronic sophistication allows the S54 to extract maximum performance while maintaining long-term reliability.
Manufacturing quality reflects BMW’s premium positioning and engineering standards. Precision machining ensures consistent tolerances, while quality control procedures minimize manufacturing variations.
The assembly process incorporates extensive testing to ensure each engine meets BMW’s exacting standards. This attention to manufacturing quality results in engines that perform consistently and reliably throughout their service life.
The S54’s naturally aspirated configuration eliminates many of the reliability concerns associated with forced induction. Without turbochargers or superchargers to complicate the system, maintenance requirements remain relatively straightforward.
The absence of boost-related components reduces the number of potential failure points while simplifying diagnostic procedures. This natural aspiration also contributes to the engine’s linear power delivery and immediate throttle response that enthusiasts prize.
Modification potential, while more limited than turbocharged engines, still offers significant performance improvements. Headers, intake systems, and engine management modifications can increase power substantially while maintaining reliability.
The strong internal components handle increased power well, while the sophisticated electronics can be recalibrated to optimize performance with modifications. More extensive modifications, including displacement increases and forced induction, are possible but require careful attention to maintain the engine’s legendary reliability.
Maintenance requirements reflect the S54’s high-performance nature but remain reasonable for owners who understand the engine’s needs. Regular oil changes with high-quality synthetic oil are essential, as is attention to the cooling system and periodic replacement of wear items.
The dual VANOS system requires occasional service, while the individual throttle bodies need periodic cleaning and synchronization. Owners who maintain these engines properly report reliable service well beyond 200,000 miles while retaining original performance characteristics.
The S54’s reputation among enthusiasts continues to grow as examples age gracefully. Unlike many high-performance engines that develop reliability issues as they accumulate miles, well-maintained S54s continue delivering their original performance while requiring only routine maintenance.
This long-term reliability, combined with the engine’s exceptional character, has established the S54 as one of the finest naturally aspirated engines ever produced.
4. Honda K20A – VTEC Engineering at Its Peak
The Honda K20A represents the culmination of Honda’s decades-long development of high-revving, naturally aspirated four-cylinder engines. Introduced in 2001 and powering various Honda and Acura models including the Civic Type R, RSX Type S, and TSX, this 2.0-liter engine combines Honda’s legendary reliability with performance capabilities that shame much larger engines.
The K20A demonstrates that displacement is no substitute for engineering excellence. The foundation of the K20A’s exceptional performance lies in its sophisticated bottom-end construction.
The aluminum block features a closed-deck design that provides exceptional rigidity despite the engine’s compact dimensions. The forged steel crankshaft is fully counterweighted and balanced to exacting standards, enabling smooth operation to the engine’s 8,000+ RPM redline.
The connecting rods, also forged steel, are lightweight yet incredibly strong, reflecting Honda’s understanding of the stresses involved in high-RPM operation. The pistons feature advanced alloys and coatings that resist heat and wear while maintaining precise tolerances throughout their service life.
The cylinder head design showcases Honda’s mastery of airflow engineering and variable valve timing technology. The K20A’s i-VTEC system represents an evolution of Honda’s famous VTEC technology, combining variable valve timing with variable lift and duration.
At low RPMs, the engine operates on conservative cam profiles that provide good drivability and fuel economy. Above the VTEC engagement point, typically around 6,000 RPM, the system switches to aggressive profiles that enable the engine to breathe efficiently at high RPM while producing substantial power.
This dual-personality approach allows the K20A to be both docile in daily driving and explosive when performance is demanded. The intake and exhaust systems demonstrate Honda’s attention to breathing efficiency. The intake manifold design optimizes airflow velocity and distribution, while the throttle body sizing provides adequate airflow without sacrificing throttle response.
The exhaust ports are shaped to promote efficient scavenging, while the exhaust manifold design maintains appropriate back-pressure for optimal power production. These systems work together to enable the K20A to produce impressive specific output figures while maintaining emissions compliance and fuel efficiency.
Fuel injection and engine management systems on the K20A reflect Honda’s integration expertise. The engine control unit coordinates fuel delivery, ignition timing, and VTEC operation to optimize performance across the entire RPM range.
The fuel injectors are sized to provide adequate flow for maximum power while maintaining precise control for idle stability and emissions compliance. The ignition system features individual coils for each cylinder, eliminating distributors while providing consistent spark energy across all operating conditions.

The lubrication system design demonstrates Honda’s understanding of high-RPM engine requirements. The oil pump provides generous flow rates, while the oil passages are sized and positioned to ensure all critical components receive adequate lubrication even at maximum RPM.
The oil capacity, while modest due to the engine’s compact size, is adequate for the application when combined with appropriate oil change intervals. The recommended oil specifications reflect the demands of high-performance operation while maintaining compatibility with Honda’s extended service intervals.
Manufacturing quality represents Honda’s commitment to precision and consistency. Computer-controlled machining ensures tight tolerances, while quality control procedures minimize manufacturing variations.
The assembly process incorporates extensive testing to verify that each engine meets Honda’s exacting standards. This attention to manufacturing quality results in engines that perform consistently throughout their service life while requiring minimal maintenance beyond routine service items.
The K20A’s naturally aspirated configuration contributes significantly to its reliability and character. Without forced induction complications, the engine delivers linear power with immediate throttle response that enthusiasts prize.
The absence of turbochargers or superchargers eliminates many potential failure points while simplifying maintenance requirements. This natural aspiration also contributes to the engine’s distinctive high-RPM character that has made it legendary among sport compact enthusiasts.
Modification potential for the K20A is substantial despite its naturally aspirated configuration. Headers, intake systems, and engine management modifications can increase power significantly while maintaining reliability.
The strong internal components handle increased compression ratios and more aggressive camshafts well, while the sophisticated VTEC system can be modified for enhanced performance. More extensive modifications, including displacement increases and forced induction, are possible but require careful attention to maintain the engine’s fundamental reliability.
The K20A’s reputation in motorsports validates its performance and reliability credentials. The engine has been successful in various racing applications, from autocrossing to road racing to time attack events.
This motorsports success demonstrates the engine’s ability to perform reliably under the most demanding conditions while providing the power and responsiveness that competitive driving requires.
Maintenance requirements for the K20A remain reasonable despite its high-performance capabilities. Regular oil changes with high-quality oil are essential, as is attention to the cooling system and periodic replacement of wear items like spark plugs and filters.
The VTEC system requires occasional valve adjustments to maintain optimal performance, while the timing chain should be inspected periodically. Owners who maintain these engines properly report reliable service well beyond 200,000 miles while retaining their original performance characteristics and distinctive high-RPM personality.
Also Read: 5 Engines That Get Better With Age and 5 That Get Worse
5. Porsche M96/M97 – Boxer Excellence Despite Early Issues
The Porsche M96 and M97 flat-six engines represent Porsche’s evolution from air-cooled to water-cooled technology while maintaining the distinctive character that defines the 911 experience.
Introduced in 1997 with the 996-generation 911, these engines initially faced criticism from purists but have proven their worth through decades of service. Despite some well-publicized early issues, properly maintained examples demonstrate remarkable longevity and performance capabilities that justify Porsche’s engineering reputation.
The foundation of the M96/M97’s design lies in its horizontally opposed configuration, which provides a low center of gravity and excellent balance.
The aluminum construction reduces weight while providing good thermal conductivity for heat dissipation. The Nikasil cylinder linings, initially controversial due to fuel quality issues in some markets, provide excellent wear resistance and thermal properties when used with appropriate fuel.
The crankcase design features substantial reinforcement to handle the stresses of high-performance operation while maintaining the structural rigidity necessary for precise engine control.
The flat-six configuration creates unique engineering challenges that Porsche has addressed through sophisticated solutions. The horizontal orientation requires careful attention to lubrication system design to ensure all components receive adequate oil regardless of vehicle attitude.
The dry-sump oiling system eliminates these concerns while providing other benefits, including reduced oil temperatures and consistent pressure under all conditions. The oil pump provides generous flow rates, while the external oil tank allows for greater oil capacity and improved cooling.
Cylinder head design showcases Porsche’s commitment to breathing efficiency and power production. The four-valve-per-cylinder layout with dual overhead camshafts provides excellent airflow potential, while the combustion chamber design promotes efficient burning and knock resistance.
The VarioCam variable valve timing system optimizes valve events across the RPM range, providing good low-end torque while enabling high-RPM power production. The intake manifold design incorporates variable-length runners that optimize airflow velocity for different operating conditions.
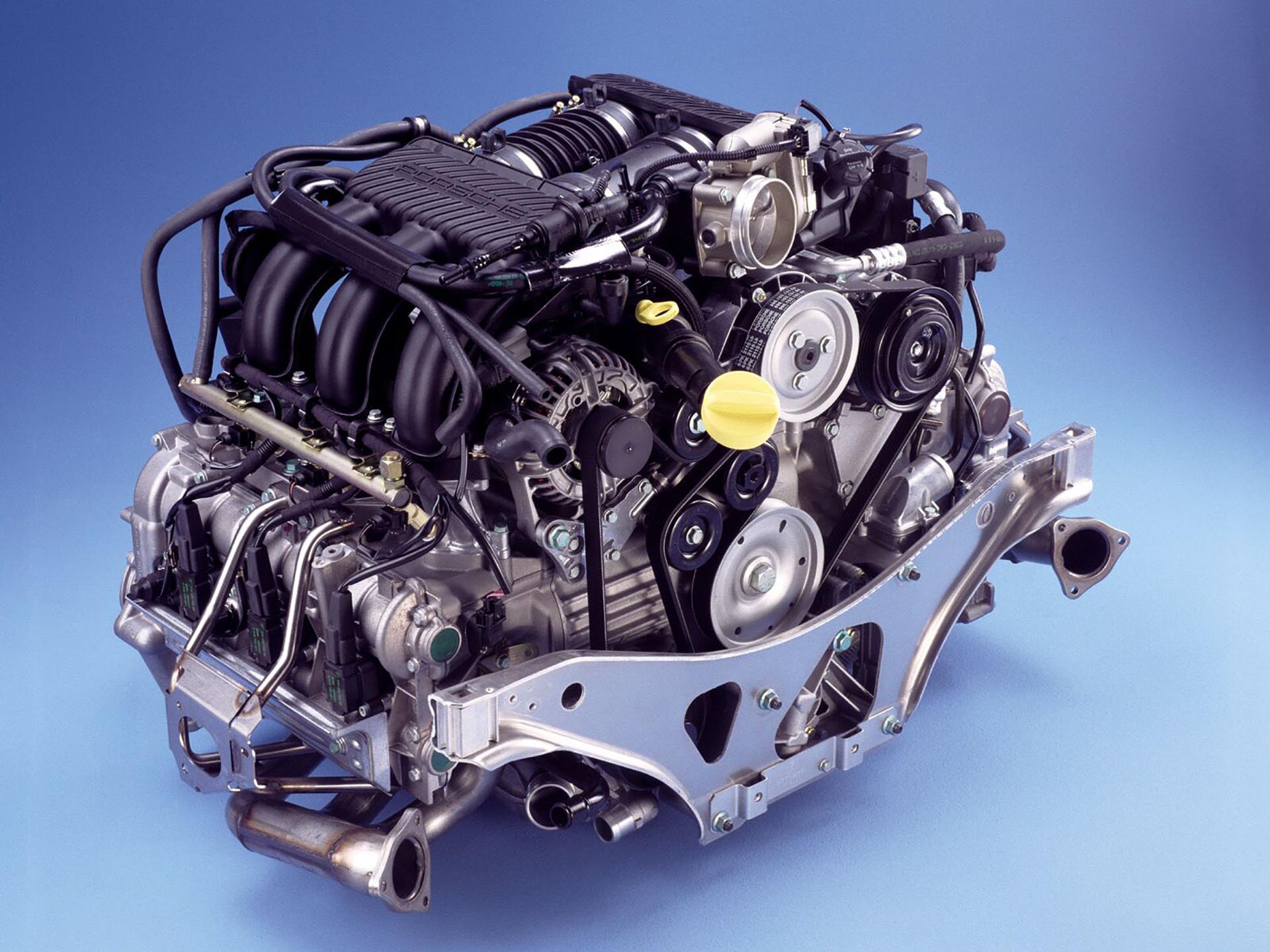
The cooling system represents a significant departure from Porsche’s air-cooled heritage while maintaining the thermal management necessary for sustained high-performance operation.
The radiator capacity and cooling fan systems provide adequate heat rejection even during track use, while the water pump flow rates ensure consistent coolant circulation.
The thermostat and temperature control systems maintain optimal operating temperatures across all conditions, contributing significantly to engine longevity and performance consistency.
Early M96 engines experienced some well-documented issues, particularly with intermediate shaft bearings and rear main seal leakage. However, Porsche addressed these concerns through design improvements and updated service procedures.
The M97 evolution incorporated numerous refinements that improved reliability while increasing power output. Understanding these early issues and ensuring proper maintenance addresses most concerns, allowing these engines to provide reliable service for hundreds of thousands of miles.
The electronic engine management system integrates multiple functions to optimize performance while protecting the engine from potentially damaging conditions. The Motronic system controls fuel delivery, ignition timing, and variable valve timing while monitoring numerous sensors for signs of problems.
The knock sensors detect early detonation and adjust timing accordingly, while temperature and pressure sensors provide comprehensive engine monitoring. This sophisticated electronic control enables the engine to extract maximum performance while maintaining long-term reliability.
Manufacturing quality reflects Porsche’s premium positioning and motorsports heritage. Precision machining ensures consistent tolerances, while quality control procedures minimize manufacturing variations.
The assembly process incorporates extensive testing to verify that each engine meets Porsche’s exacting standards. This attention to manufacturing quality, combined with continuous improvement programs, has resulted in engines that become more reliable as production issues are identified and resolved.
Modification potential for the M96/M97 is substantial, particularly for naturally aspirated applications. Headers, intake systems, and engine management modifications can increase power significantly while maintaining reliability.
The strong internal components handle increased compression ratios and more aggressive camshafts well, while the sophisticated electronics can be recalibrated for enhanced performance. Forced induction applications are possible but require careful attention to maintain the engine’s fundamental reliability characteristics.
The M96/M97’s reputation in motorsports validates its performance capabilities and fundamental strength. These engines have been successful in various racing applications, from club racing to professional motorsports. The racing experience has informed ongoing development and improvement programs, ensuring that street engines benefit from competition-proven technologies and solutions.
Maintenance requirements for the M96/M97 reflect their high-performance nature but remain reasonable for owners who understand their needs. Regular oil changes with high-quality synthetic oil are essential, as is attention to the cooling system and periodic replacement of wear items.
The IMS bearing issue on early engines requires attention, but preventive measures are available and effective. The rear main seal should be monitored and replaced if leakage develops. Owners who address these known issues and maintain their engines properly report reliable service and exceptional performance that justifies Porsche’s engineering reputation.
5 Engines That Burn Out Fast
These fragile powerplants suffer from premature failure due to aggressive tuning strategies, inadequate cooling capacity, and lightweight component designs that prioritize peak power over longevity during high-stress operating conditions and performance driving scenarios.
Their problematic engineering includes thin cylinder walls, minimal safety margins, and inadequate lubrication systems that amplify the failure risks typically associated with sustained high-RPM operation or track use without proper preparation.
From catastrophic bearing failures that destroy entire engines to overheating issues that warp cylinder heads during spirited driving sessions, these powerplants demand careful operation and frequent rebuilding.
Owners discover that while these engines offer impressive peak performance numbers and racing pedigree, their reliability limitations create expensive maintenance requirements and require conservative driving approaches to avoid costly engine rebuilds or complete replacement procedures.
1. Subaru EJ25 – Head Gasket Nightmares and Ringland Failures
The Subaru EJ25 boxer engine, despite its rally-bred heritage and enthusiastic following, has earned an unfortunate reputation for catastrophic failures that can destroy the engine without warning.
Used in various Subaru models including the WRX, STI, Forester, and Legacy, this 2.5-liter turbocharged flat-four promises exciting performance but delivers heartbreak with alarming frequency. The EJ25’s problems stem from fundamental design compromises that prioritize packaging and cost over long-term reliability.
The most notorious issue plaguing the EJ25 is its propensity for head gasket failure, a problem that has affected multiple generations of the engine. The horizontal boxer configuration creates unique challenges for head gasket sealing, as the gaskets must seal against both vertical and horizontal forces while managing significant thermal expansion differences between the aluminum heads and the iron block.
Subaru’s original head gasket design proved inadequate for these stresses, leading to failures that can occur as early as 60,000 miles in some cases. When the head gaskets fail, coolant can enter the combustion chambers or mix with the engine oil, leading to catastrophic damage if not immediately addressed.
The closed-deck block design, while providing good rigidity, creates problematic cooling around the cylinder bores. The lack of adequate coolant flow in these critical areas leads to hot spots that contribute to detonation and thermal stress.
This cooling inadequacy becomes particularly problematic under boost, where combustion temperatures soar and the engine’s thermal management capabilities are overwhelmed. The result is often piston damage, ring land failures, and complete engine destruction during what should be normal operation.
Ringland failure represents another devastating weakness of the EJ25 design. The thin ring lands on the pistons, combined with the engine’s tendency toward detonation, creates a perfect storm for catastrophic piston failure.
When a ring land breaks, typically the top ring land between the first and second compression rings, the piston loses compression and oil control almost immediately.
The broken pieces can cause additional damage as they circulate through the engine, often requiring complete engine replacement rather than simple repair. This failure mode can occur suddenly during normal driving, leaving owners stranded with destroyed engines.
The turbocharging system compounds the EJ25’s inherent weaknesses. The factory turbocharger sizing often creates a compromise between spool-up time and thermal efficiency, resulting in high exhaust gas temperatures that stress the entire system.
The intercooler sizing and positioning often prove inadequate for sustained high-performance driving, leading to heat soak that reduces performance and increases the likelihood of detonation. The boost control systems, particularly on earlier models, can be erratic and contribute to overboosting conditions that exceed the engine’s durability limits.

Oiling system inadequacies contribute to premature bearing wear and failure. The oil pickup design can cause starvation during high-G cornering or acceleration, leading to bearing damage and eventual engine failure.
The oil capacity, while adequate for normal driving, proves insufficient for sustained high-performance use without frequent changes and careful monitoring.
The oil passage sizing to critical components like turbocharger bearings often proves marginal, leading to premature turbo failure that can damage the engine when metal particles circulate through the oiling system.
The engine management system, particularly on earlier models, lacks the sophistication necessary to protect the engine from its design limitations.
The knock detection systems often prove inadequate or poorly calibrated, failing to detect and prevent the detonation that destroys pistons and ring lands.
The fuel mapping in stock form frequently runs dangerously lean under certain conditions, contributing to the thermal stress that leads to catastrophic failures. Even professional tuning cannot completely overcome the fundamental design limitations that make the EJ25 inherently fragile.
Despite its problems, the EJ25 continues to attract enthusiasts drawn to its distinctive sound and rally heritage. However, potential owners must understand that reliable operation requires extensive modifications, frequent maintenance, and the acceptance that catastrophic failure remains possible regardless of precautions taken.
The engine’s fundamental design limitations cannot be completely overcome, making it a poor choice for anyone prioritizing long-term reliability over short-term excitement.
2. BMW N54 – Twin-Turbo Complexity and Carbon Buildup
The BMW N54 twin-turbocharged inline-six, introduced in 2006, represents BMW’s ambitious attempt to combine high performance with improved fuel efficiency through downsizing and forced induction.
While the engine delivers impressive performance and has gained a devoted following among tuning enthusiasts, its complex design and numerous reliability issues have made it one of BMW’s most problematic powerplants.
The N54’s failures stem from over-engineering combined with inadequate validation testing, resulting in an engine that requires constant attention and expensive repairs to maintain operation.
The most pervasive problem plaguing the N54 is carbon buildup on the intake valves, a consequence of the direct injection system that has no port injection to wash deposits away.
Unlike traditional port-injected engines, where fuel flowing over the intake valves helps keep them clean, direct injection engines inject fuel directly into the combustion chamber, allowing carbon deposits to accumulate on the valve faces and seats.
Over time, these deposits reduce airflow, cause rough idling, and decrease performance. The cleaning process requires removing the intake manifold and manually cleaning each valve, a labor-intensive procedure that can cost thousands of dollars and needs to be repeated every 60,000-80,000 miles.

The twin-turbocharger system, while innovative, introduces multiple failure points that plague owners throughout the engine’s life. The turbos themselves frequently fail due to wastegate rattle, a condition where the wastegate actuator arm breaks or becomes disconnected, causing the wastegate flap to rattle against its seat.
This failure requires turbocharger replacement and often occurs multiple times during the engine’s life. The turbo oil feed lines, made of plastic, often crack and leak, causing oil starvation that destroys the turbocharger bearings. Even when replaced with updated parts, these components continue to fail with frustrating regularity.
Despite its numerous problems, the N54 continues to attract enthusiasts due to its impressive tuning potential and performance capabilities. However, potential owners must understand that reliable operation requires extensive preventive maintenance, immediate attention to any symptoms, and budgeting for frequent, expensive repairs.
The engine’s complexity and inherent design flaws make it unsuitable for anyone prioritizing reliability over performance, and even dedicated enthusiasts often abandon these engines due to their relentless reliability issues and crushing maintenance costs.
3. Audi/Volkswagen 2.7T – Turbo Failures and Sludge Problems
The Audi/Volkswagen 2.7-liter twin-turbocharged V6, known internally as the AAN and APB engines, represents one of the most ambitious yet problematic performance engines of the late 1990s and early 2000s.
Featured in high-performance models like the Audi S4, S6, A6, and Allroad, this engine promised BMW-rivaling performance with Audi’s trademark refinement. Instead, it delivered a maintenance nightmare that has destroyed countless engines and left owners facing repair bills that often exceed the vehicles’ values.
The 2.7T’s most devastating weakness lies in its catastrophic tendency toward oil sludge formation, a problem that can destroy the engine within 60,000-80,000 miles.
The combination of small oil passages, inadequate oil capacity, extended service intervals, and heat-sensitive oil seals creates perfect conditions for oil breakdown and sludge formation.
Once sludge begins forming, it blocks critical oil passages, leading to bearing failure, turbocharger destruction, and complete engine seizure. The problem is insidious because it often develops without obvious symptoms until catastrophic failure occurs.
The twin-turbocharger system, while providing impressive performance, introduces multiple failure points that plague owners throughout the engine’s abbreviated lifespan. The K03 turbochargers are undersized for the engine’s displacement and power output, causing them to operate at the limits of their design parameters.
This constant stress leads to premature bearing failure, compounded by the oiling system’s inability to provide adequate lubrication to the turbos. When one turbo fails, metal particles circulate through the engine, often destroying the second turbo and causing extensive internal damage.
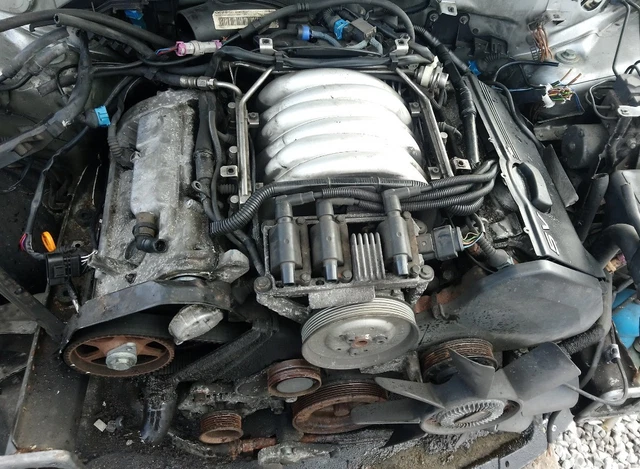
Turbocharger oil supply problems represent a fundamental design flaw that contributes to the engine’s poor reliability. The oil feed lines to the turbos are inadequately sized and prone to restriction, while the oil drain lines can become blocked with sludge or debris.
When oil flow to the turbos is restricted, bearing temperatures soar and failure occurs rapidly. The symptoms are often subtle until catastrophic failure occurs, leaving owners with repair bills exceeding $8,000 for turbocharger replacement and associated damage.
The engine’s cooling system proves inadequate for the thermal loads generated by twin-turbo operation. The radiator capacity, while adequate for naturally aspirated applications, cannot handle the sustained heat generation of turbocharged operation.
The intercooler design and placement often result in heat soak during stop-and-go driving, reducing performance and increasing the likelihood of detonation. The cooling system’s inability to maintain optimal temperatures contributes to oil breakdown and accelerated component wear.
Oil capacity represents another critical design flaw that contributes to the 2.7T’s reliability problems. The approximately 6-quart oil capacity is inadequate for a twin-turbocharged V6, particularly given the engine’s tendency toward oil consumption and the demands of turbocharger lubrication.
Combined with Audi’s recommendation for extended oil change intervals, this inadequate capacity virtually guarantees oil degradation and sludge formation. Even owners who perform frequent oil changes often experience problems due to the fundamental inadequacy of the system’s design.
Audi’s initial response to the 2.7T’s problems was inadequate, with the company denying that design defects were responsible for the widespread failures.
Warranty extensions and goodwill repairs came only after significant owner pressure and negative publicity. Many owners found themselves facing complete engine replacement costs shortly after their warranty periods expired, leading to class-action lawsuits and damaged brand reputation.
4. Mitsubishi 4G63T – Crankwalk and Oiling Issues
The Mitsubishi 4G63T turbocharged four-cylinder engine, despite its legendary status in rally racing and tuning circles, suffers from several critical design flaws that can lead to catastrophic failure without warning.
Most famously used in the Eclipse GSX, Talon TSi, and Evolution models, this 2.0-liter turbocharged engine has earned both admiration for its tuning potential and infamy for its reliability problems. The engine’s issues stem from cost-cutting measures and design compromises that prioritize performance over longevity.
The most notorious problem affecting the 4G63T is “crankwalk,” a condition where the crankshaft gradually moves forward in the block, eventually causing catastrophic engine failure.
This problem primarily affects the 1995-1999 model years and stems from the thrust bearing design and oiling system inadequacies. The thrust bearing, responsible for controlling fore-and-aft crankshaft movement, receives inadequate lubrication and operates under higher loads than it can sustain.
As the bearing wears, the crankshaft moves forward, eventually causing the timing belt to contact the block and potentially causing valve-to-piston contact that destroys the engine.
The root cause of crankwalk lies in the oiling system’s inability to provide adequate lubrication to the thrust bearing. The oil passage feeding the thrust bearing is small and easily restricted, while the bearing design itself proves inadequate for the stresses involved.
The problem is exacerbated by the engine’s tendency toward oil starvation during high-G maneuvering, which is common in the performance driving these engines were designed for. Once crankwalk begins, it progresses rapidly and cannot be stopped without complete engine disassembly and rebuild.
Oil starvation represents another critical weakness of the 4G63T design. The oil pickup location and oil pan design prove inadequate for sustained high-performance driving, particularly during cornering or acceleration when oil moves away from the pickup.
This starvation can occur even with adequate oil levels, leading to bearing damage and turbocharger failure. The problem is compounded by the engine’s relatively small oil capacity, which provides little safety margin for oil loss or degradation.

The turbocharger oiling system compounds the lubrication problems. The oil feed to the turbo is often undersized, while the oil return line can become restricted with carbon deposits or debris.
When the turbo doesn’t receive adequate oil flow, bearing temperatures soar and failure occurs rapidly. The symptoms are often subtle until catastrophic failure destroys the turbo and sends metal particles throughout the engine. Turbo replacement requires careful attention to the oiling system to prevent immediate failure of the replacement unit.
Cooling system inadequacies contribute to the 4G63T’s reliability problems. The radiator capacity and cooling system design often prove marginal for sustained high-performance use, leading to overheating that can cause head gasket failure or engine damage.
The intercooler design and placement result in heat soak during traffic or track use, reducing performance and increasing the likelihood of detonation. The cooling system’s inability to maintain consistent temperatures contributes to thermal stress that accelerates component wear.
Knock sensor failures can leave the engine vulnerable to detonation damage. The knock sensor system, designed to detect and prevent harmful detonation, frequently malfunctions or becomes insensitive over time.
When the system fails to detect knock, the engine operates without protection from the timing retard that prevents piston and valve damage. This vulnerability is particularly dangerous in modified applications where increased boost pressure makes detonation more likely.
The 4G63T’s aftermarket support, while extensive, often focuses on increasing performance rather than addressing fundamental reliability issues. Many modifications exacerbate the engine’s inherent problems while providing impressive power gains.
Turbo upgrades often exceed the oiling system’s capabilities, while increased boost pressure accelerates the crankwalk problem and other failure modes.
Maintenance requirements for the 4G63T are extensive and cannot guarantee reliability. Frequent oil changes with high-quality synthetic oil are essential, as is constant monitoring of oil levels and temperatures.
The timing belt must be replaced at precise intervals, while the cooling system requires frequent attention. Even with meticulous maintenance, the fundamental design flaws cannot be completely overcome, making catastrophic failure always possible.
5. Nissan VQ35HR – Oil Consumption and Gallery Gasket Failures
The Nissan VQ35HR, a 3.5-liter naturally aspirated V6 introduced in 2007, represents Nissan’s attempt to refine its successful VQ platform while increasing performance and reducing emissions.
Featured in vehicles like the 350Z, G35, and various Infiniti models, this engine promised improved power and efficiency over its predecessors. However, the VQ35HR suffers from several critical design flaws that lead to catastrophic failures, most notably excessive oil consumption and oil gallery gasket failures that can destroy the engine without warning.
The most devastating problem affecting the VQ35HR is the failure of the oil gallery gaskets, small seals that prevent oil from leaking between internal passages within the engine block. When these gaskets fail, oil pressure drops dramatically as oil bypasses its intended path through the lubrication system.
The failure typically occurs without warning, and the resulting oil starvation can destroy bearings, pistons, and other internal components within minutes. The gasket failure is often misdiagnosed initially, as the symptoms can mimic other problems, leading to continued operation that causes complete engine destruction.
The oil gallery gasket problem stems from the use of inadequate sealing materials that cannot withstand the thermal cycling and chemical exposure present in modern engines.
The gaskets, made of paper or composite materials, deteriorate over time and eventually fail to maintain proper sealing. The problem is exacerbated by extended oil change intervals and the use of lower-quality oils that accelerate gasket degradation. Once the gaskets begin failing, the problem progresses rapidly and cannot be repaired without complete engine disassembly.
The variable valve timing system adds complexity and potential failure points that contribute to the engine’s reliability problems. The VVT actuators, controlled by oil pressure, frequently malfunction due to oil sludge buildup or internal wear.

When the system fails, performance suffers and emissions increase, while diagnostic procedures become complex and expensive. The system’s dependence on clean oil and proper oil pressure makes it vulnerable to the oil-related problems that plague the engine.
Intake manifold problems compound the VQ35HR’s reliability issues. The plastic intake manifold components, while lightweight and cost-effective, prove less durable than traditional materials.
The manifold can develop cracks or warping that cause vacuum leaks, leading to rough idling and performance problems. The repair requires significant disassembly and expense, often approaching $2,000 for parts and labor. The problem typically occurs between 80,000-120,000 miles, often coinciding with other major failures.
Carbon buildup on intake valves affects performance and drivability over time. The combination of EGR operation and crankcase ventilation causes carbon deposits to accumulate on valve faces and intake ports, reducing airflow and causing rough idling.
The cleaning process requires significant labor and expense, while the problem typically returns within 50,000-60,000 miles. The carbon buildup contributes to performance degradation that makes the engine feel sluggish and unresponsive.
The VQ35HR’s reliability problems have significantly damaged Nissan’s reputation for dependability, particularly in the performance and luxury segments where these engines were prominently featured.
Many owners have abandoned the brand entirely after experiencing catastrophic failures, while resale values for affected vehicles remain depressed due to the engine’s poor reputation. The problems represent a significant failure in engineering and quality control that continues to affect Nissan’s market position years after production ended.
Also Read: 5 Manual Transmissions That Never Quit and 5 That Grind Constantly