In the automotive world, the term “million-mile engine” has become the holy grail for budget-conscious car buyers who prioritize longevity over luxury.
While most drivers will never actually reach that mythical seven-figure odometer reading, the engines that earn this reputation represent the pinnacle of engineering reliability, build quality, and design excellence.
These powerplants don’t just survive hundreds of thousands of miles, they thrive, often outlasting multiple transmissions, suspension components, and even the bodies of the vehicles they power.
The difference between a truly reliable engine and one that barely makes it past the warranty period often comes down to fundamental design philosophy, manufacturing quality, and materials selection.
The best budget engines share common characteristics: robust bottom-end construction, conservative tuning that prioritizes longevity over peak performance, proven technology rather than cutting-edge innovation, and extensive real-world testing before market introduction.
These engines typically feature cast-iron blocks or high-quality aluminum construction, well-designed oiling systems, adequate cooling capacity, and timing chains rather than belts where critical.
Conversely, engines that struggle with reliability often suffer from cost-cutting measures in critical areas, overly complex designs that introduce multiple failure points, inadequate testing, or aggressive tuning that pushes components beyond their long-term durability limits.
Some manufacturers prioritize short-term performance metrics or fuel economy numbers over proven reliability, resulting in engines that may impress in initial reviews but disappoint owners after 100,000 miles.
Understanding these differences can save budget-conscious buyers thousands in repair costs and countless hours of frustration, making the distinction between truly reliable powerplants and those that merely look good on paper crucial for smart car shopping.
5 Budget Engines With Million-Mile Potential
These exceptionally durable powerplants feature simple engineering designs and precision-manufactured components that deliver extraordinary longevity through years of reliable operation across demanding commercial applications and high-mileage driving scenarios without expensive maintenance requirements.
Their thoughtful engineering includes cast iron construction, naturally aspirated configurations, and conservative tuning parameters that resist the wear patterns typically created by complex systems or aggressive performance demands during extended service intervals and heavy-duty usage cycles.
From taxi fleet operations that accumulate massive mileage to delivery vehicles requiring constant reliability without costly repairs, these remarkable engines continue providing dependable service without developing major component failures or requiring complete rebuilds.
Owners report exceptional value with these endurance-focused powerplants a cost-effectiveness quality feature that proves its worth through minimal repair expenses and extended operational life throughout commercial transportation duties and personal high-mileage applications spanning decades of continuous service.
1. Toyota 2ZR-FE 1.8L Four-Cylinder
The Toyota 2ZR-FE represents everything that makes Toyota engines legendary for their durability and longevity. This naturally aspirated 1.8-liter four-cylinder engine has powered millions of Corollas, Camrys, and various other Toyota models since 2007, establishing itself as one of the most reliable powerplants ever created for the budget car segment.
The engine’s design philosophy centers around proven, conservative engineering principles rather than chasing headline-grabbing performance figures or cutting-edge technology that could introduce reliability concerns.
At the heart of the 2ZR-FE’s durability lies its robust aluminum block construction with cast-iron cylinder liners, providing the perfect balance of weight savings and long-term durability.
The cylinder head features dual overhead camshafts with Toyota’s proven Variable Valve Timing with intelligence (VVT-i) system, which has been refined over decades to provide optimal performance across the rev range while maintaining exceptional reliability.
The engine’s compression ratio of 10.0:1 strikes an ideal balance between efficiency and stress on internal components, ensuring that the engine can operate reliably on regular gasoline while still delivering respectable fuel economy.
The oiling system deserves particular praise for its simplicity and effectiveness. Toyota engineers designed the 2ZR-FE with generous oil passages and a robust oil pump that ensures consistent lubrication even under extreme conditions.
The engine’s oil capacity of 4.4 quarts with filter provides adequate thermal mass for oil cooling, while the straightforward oil change procedure encourages regular maintenance.
Many owners report oil change intervals extending beyond Toyota’s recommended 10,000 miles without adverse effects, though most reliability experts recommend more frequent changes for maximum longevity.

One of the most impressive aspects of the 2ZR-FE is its tolerance for neglect and abuse. Numerous documented cases exist of these engines surviving severe overheating incidents, extended oil change intervals exceeding 20,000 miles, and even complete loss of coolant without catastrophic failure.
This resilience stems from conservative engineering margins throughout the design, including generous bearing clearances, robust piston ring packages, and cylinder head designs that resist warping under thermal stress.
The timing chain system represents another major reliability advantage over timing belt designs found in many competing engines. The 2ZR-FE’s timing chain typically lasts the life of the engine with minimal maintenance, eliminating the expensive and complex timing belt replacement services required every 60,000 to 100,000 miles in many other budget engines.
When timing chain issues do occasionally arise, they typically manifest as gradual noise increase rather than catastrophic failure, providing owners with warning.
Common maintenance items for the 2ZR-FE remain refreshingly simple and inexpensive. Regular oil changes, air filter replacements, and spark plug changes every 100,000 miles represent the primary maintenance requirements.
The engine’s simple port fuel injection system avoids the carbon buildup issues that plague many direct injection engines, while the straightforward ignition system rarely requires attention beyond routine spark plug replacement.
Performance characteristics of the 2ZR-FE prioritize smoothness and efficiency over raw power output. The engine produces approximately 132 horsepower and 128 lb-ft of torque, figures that may seem modest by modern standards but prove perfectly adequate for daily driving when paired with Toyota’s well-calibrated transmissions.
The engine’s power delivery remains linear and predictable throughout its rev range, with a willingness to rev cleanly to its 6,200 rpm redline even after hundreds of thousands of miles.
Real-world longevity reports for the 2ZR-FE consistently exceed expectations, with numerous examples documented above 300,000 miles without major internal work.
Taxi fleets, delivery services, and rideshare drivers have proven the engine’s commercial-grade durability in the most demanding applications. Many owners report original engines approaching 400,000 miles while still passing emissions tests and consuming minimal oil between changes, a testament to the exceptional ring seal and cylinder wall finish quality.
2. Honda K24A 2.4L Four-Cylinder
Honda’s K24A engine represents the pinnacle of the company’s K-series engine family, combining proven reliability with robust performance capabilities that make it equally suitable for daily driving and enthusiast applications.
Introduced in 2001, this 2.4-liter naturally aspirated four-cylinder has powered everything from Accords and CR-Vs to Element crossovers, establishing an enviable reputation for durability that extends well beyond typical Honda reliability standards.
The K24A’s architecture centers around Honda’s time-tested aluminum block and head construction, featuring the company’s signature i-VTEC variable valve timing system that provides excellent performance across the rev range while maintaining exceptional fuel efficiency.
The engine’s bore and stroke dimensions of 87mm x 99mm create an oversquare design that promotes high-rpm breathing while maintaining adequate low-end torque for everyday drivability. This design philosophy ensures that the engine feels responsive and willing throughout its operating range, unlike many budget engines that struggle at either end of the performance spectrum.
Internal construction quality sets the K24A apart from many competing engines in its price range. The aluminum block features robust main bearing supports with four-bolt main caps for the center three bearings, providing exceptional bottom-end strength that rivals much more expensive engines.
The crankshaft is fully counterweighted and constructed from high-quality forged steel, while the connecting rods feature premium construction that easily handles the engine’s 7,000 rpm redline even after hundreds of thousands of miles of use.
The cylinder head design showcases Honda’s extensive experience with high-performance four-cylinder engines. The dual overhead camshaft layout features Honda’s signature VTEC system, which switches between two different cam profiles to optimize performance at different engine speeds. Unlike some variable valve timing systems that introduce complexity and potential failure points, Honda’s VTEC system has proven remarkably reliable over decades of use, with most failures traced to inadequate oil changes rather than inherent design flaws.

Honda’s attention to oiling system design becomes apparent in the K24A’s impressive longevity under diverse operating conditions. The engine features a robust oil pump driven directly from the crankshaft, ensuring consistent oil pressure even at idle speeds.
Oil passages throughout the engine are generously sized, while the oil pan design incorporates baffling to prevent oil starvation during aggressive driving or extreme angles. The 4.5-quart oil capacity provides adequate thermal mass for cooling, while the easily accessible oil filter location encourages regular maintenance.
One of the most impressive aspects of K24A durability involves its tolerance for high-mileage operation without major internal work. Many examples exist of these engines exceeding 300,000 miles while maintaining original compression specifications and minimal oil consumption.
The engine’s robust ring package and precision cylinder wall finish contribute to exceptional long-term seal retention, while conservative piston design ensures minimal thermal expansion issues even under sustained high-load operation.
The timing chain system represents a significant reliability advantage over timing belt designs found in previous Honda engines and many current competitors.
The K24A’s timing chain typically operates trouble-free for the engine’s entire service life, eliminating expensive maintenance intervals and potential catastrophic failure modes associated with timing belts.
When timing chain stretch does eventually occur after extreme mileage, the symptoms develop gradually and provide adequate warning before causing engine damage.
Fuel injection system design prioritizes reliability and serviceability over cutting-edge technology. The K24A employs traditional port fuel injection rather than direct injection, avoiding carbon buildup issues that plague many modern engines while maintaining excellent fuel atomization and distribution.
The fuel rail and injector design prove exceptionally durable, with most fuel system issues traceable to contaminated fuel or inadequate filter maintenance rather than component failure.
Performance characteristics of the K24A strike an excellent balance between power output and longevity. Depending on specific application and tuning, the engine produces between 160 and 190 horsepower with torque figures ranging from 162 to 172 lb-ft.
The engine’s power delivery remains smooth and linear throughout its rev range, with a particular willingness to rev that makes it feel more powerful than its displacement might suggest. The 7,000 rpm redline reflects Honda’s confidence in the engine’s internal durability, while the broad torque curve ensures excellent drivability in real-world conditions.
3. General Motors Ecotec 2.4L Four-Cylinder (LE5)
General Motors’ Ecotec 2.4-liter four-cylinder engine, specifically the LE5 variant, represents a significant departure from GM’s historically problematic small engines, establishing itself as one of the most reliable powerplants the company has ever produced for budget-oriented vehicles.
Introduced in 2006, this naturally aspirated engine has powered numerous Chevrolet, Pontiac, Saturn, and Buick models, earning a reputation for exceptional durability that rivals the best offerings from Honda and Toyota.
The LE5’s fundamental architecture showcases GM’s commitment to proven engineering principles rather than experimental technology. The aluminum block construction features cast-iron cylinder liners that provide exceptional wear resistance and heat dissipation characteristics.
The cylinder bore spacing of 103mm provides generous water jacket capacity around each cylinder, ensuring consistent cooling even under sustained high-load operation. The deck height and overall block design create a rigid foundation that minimizes distortion under thermal and mechanical stress.
Internal component quality reflects GM’s recognition that budget engines must prioritize longevity over maximum performance output. The crankshaft features full counterweighting and robust main journal dimensions, while the connecting rods employ high-quality steel construction with precision machining tolerances.
The pistons feature conservative design with adequate ring land thickness and thermal expansion characteristics that prevent scuffing even under severe operating conditions. The piston rings themselves employ premium materials and coatings that ensure excellent long-term sealing characteristics.
The cylinder head design incorporates dual overhead camshafts with GM’s Variable Valve Timing (VVT) system, providing excellent performance optimization across the engine’s operating range while maintaining reliability standards.
The combustion chamber design promotes excellent fuel mixing and flame propagation, contributing to clean emissions and consistent combustion characteristics that reduce stress on internal components.
The valve train employs hydraulic lash adjusters that automatically maintain proper valve clearances throughout the engine’s service life, eliminating complex adjustment procedures.

Oiling system design receives particular attention in the LE5, reflecting GM’s understanding that oil circulation represents the most critical factor in engine longevity.
The oil pump features robust construction with direct crankshaft drive, ensuring consistent pressure delivery even at idle speeds. Oil passages throughout the engine are generously dimensioned, while the oil pan incorporates baffling to prevent oil starvation during aggressive driving maneuvers.
The 5.0-quart oil capacity provides excellent thermal mass for oil cooling while ensuring adequate reserve capacity. One of the most impressive aspects of LE5 reliability involves its exceptional tolerance for extended maintenance intervals and adverse operating conditions.
Numerous documented cases exist of these engines surviving oil change intervals exceeding 15,000 miles without internal damage, though such practices are not recommended for optimal longevity. The engine’s robust bearing design and generous clearances contribute to this tolerance, while the effective oiling system ensures adequate lubrication even with degraded oil.
The timing chain system eliminates the maintenance requirements and potential failure modes associated with timing belt designs found in many competing engines.
The LE5’s timing chain typically operates trouble-free for the engine’s entire service life, with tensioner and guide systems designed for extended durability.
When timing chain issues do occasionally develop after extreme mileage, they typically manifest as gradual noise increase rather than catastrophic failure, providing owners with adequate warning.
Fuel system design emphasizes simplicity and reliability over cutting-edge technology. The LE5 employs traditional port fuel injection with a robust fuel rail design and high-quality injectors that resist contamination and wear.
The intake manifold design promotes excellent fuel distribution to all cylinders, while the straightforward throttle body design eliminates complex electronic throttle control systems that can introduce reliability concerns.
Performance characteristics of the LE5 provide an excellent balance between power output and fuel efficiency. The engine produces approximately 169 horsepower and 160 lb-ft of torque, figures that provide adequate performance for most applications while ensuring conservative stress levels on internal components.
The engine’s power delivery remains smooth and linear throughout its rev range, with excellent throttle response that makes the car feel more powerful than displacement alone might suggest.
Real-world durability reports consistently demonstrate the LE5’s exceptional longevity potential. Many examples exist of these engines exceeding 250,000 miles without major internal work, while maintaining original compression specifications and minimal oil consumption.
Fleet applications, including taxi service and delivery vehicles, have proven the engine’s commercial-grade durability under the most demanding operating conditions.
4. Mazda Skyactiv-G 2.0L Four-Cylinder
Mazda’s Skyactiv-G 2.0-liter four-cylinder engine represents the culmination of decades of rotary and piston engine development, combining innovative engineering approaches with proven reliability principles to create one of the most durable budget engines available today.
Introduced in 2011, this naturally aspirated powerplant has established an exceptional reputation for longevity while delivering impressive fuel efficiency and performance characteristics that make it equally suitable for economy-focused and enthusiast applications.
The Skyactiv-G’s fundamental design philosophy centers around achieving maximum thermal efficiency through innovative combustion chamber design, compression ratio optimization, and advanced engine management strategies.
The 13.0:1 compression ratio represents one of the highest ratios used in a production gasoline engine designed for regular fuel, achieved through careful combustion chamber shaping, piston crown design, and precisely controlled fuel injection timing. This high compression ratio contributes to exceptional fuel efficiency while ensuring complete combustion that reduces carbon deposits and internal contamination.
Block construction employs lightweight aluminum with cast-iron cylinder liners, providing optimal balance between weight reduction and long-term durability.
The cylinder bore spacing and deck height create generous water jacket capacity around each cylinder, ensuring consistent cooling even under sustained high-load operation.
The block features robust main bearing supports with cross-bolted main caps that provide exceptional bottom-end strength, while the deep-skirt design minimizes noise and vibration while maximizing structural rigidity.
Internal component quality reflects Mazda’s commitment to long-term durability despite the engine’s high compression ratio and performance orientation.
The forged steel crankshaft features full counterweighting and generous journal dimensions, while the connecting rods employ premium steel construction with precision weight matching.
The pistons feature lightweight aluminum construction with reinforced ring lands and thermal barrier coatings that prevent heat-related damage. The piston rings utilize advanced materials and coatings that ensure excellent sealing characteristics throughout the engine’s service life.

The cylinder head design showcases Mazda’s extensive experience with high-performance engine development. The dual overhead camshaft layout incorporates Mazda’s Variable Valve Timing system, which optimizes valve timing across the engine’s operating range for maximum efficiency and performance.
The combustion chamber shape promotes excellent fuel mixing and flame propagation, contributing to clean combustion that reduces deposits and internal stress. The valve train employs hydraulic lash adjusters that maintain proper valve clearances automatically, eliminating maintenance requirements while ensuring optimal performance.
Oiling system design receives extensive attention in the Skyactiv-G, reflecting the critical importance of lubrication in high-compression engines. The oil pump features robust construction with precise internal clearances, ensuring consistent pressure delivery across all operating conditions.
Oil passages throughout the engine are carefully sized to provide adequate flow without excessive pressure drop, while the oil pan design incorporates sophisticated baffling to prevent oil starvation during aggressive driving maneuvers. The 4.3-quart oil capacity provides adequate thermal mass for cooling while maintaining compact packaging.
One of the most remarkable aspects of Skyactiv-G durability involves its ability to maintain performance and efficiency characteristics even after extended high-mileage operation.
The engine’s high compression ratio and advanced combustion management contribute to exceptionally clean internal operation, with minimal deposit formation and excellent ring seal retention. Many owners report engines exceeding 200,000 miles while maintaining original compression specifications and fuel efficiency ratings, a testament to the engine’s exceptional build quality.
The timing chain system eliminates maintenance requirements associated with timing belt designs while providing exceptional durability. The Skyactiv-G’s timing chain typically operates trouble-free throughout the engine’s service life, with tensioner and guide systems designed for extended operation.
The chain drive system’s design minimizes stretch and wear, ensuring consistent valve timing throughout the engine’s operational life. Fuel injection system design emphasizes precision and reliability through sophisticated direct injection technology.
Unlike many direct injection systems that suffer from carbon buildup issues, the Skyactiv-G incorporates design features that minimize deposit formation while maintaining excellent fuel atomization characteristics.
The high-pressure fuel system components prove exceptionally durable, with most fuel system issues traceable to contaminated fuel rather than component failure. Performance characteristics of the Skyactiv-G provide an excellent balance between power output, fuel efficiency, and long-term durability.
The engine produces approximately 155 horsepower and 150 lb-ft of torque, figures that provide spirited performance while ensuring conservative stress levels on internal components.
The engine’s power delivery remains smooth and linear throughout its rev range, with exceptional throttle response that makes the vehicle feel more powerful than displacement alone might suggest.
Also Read: 5 Hybrids With the Best Traction Off-Road and 5 Slipping Behind
5. Subaru EJ25 2.5L Boxer Four-Cylinder (Non-Turbo)
Subaru’s naturally aspirated EJ25 2.5-liter boxer four-cylinder engine represents one of the most unique and durable powerplants available in the budget car segment, combining the inherent balance advantages of horizontally opposed cylinder configuration with proven reliability that has made it a favorite among enthusiasts and practical car buyers alike.
While turbocharged variants of the EJ25 have experienced various reliability issues, the naturally aspirated version has established an exceptional reputation for longevity and consistent performance across diverse operating conditions.
The EJ25’s horizontally opposed cylinder configuration provides fundamental advantages in engine balance, vibration control, and center of gravity optimization that contribute directly to long-term durability.
The opposing pistons naturally cancel each other’s reciprocating forces, eliminating the need for balance shafts while reducing stress on engine mounts and supporting structures. This inherent balance allows the engine to operate smoothly at higher rpm levels while minimizing vibration-induced wear on internal components and external accessories.
Block construction employs aluminum with cast-iron cylinder liners, providing optimal thermal characteristics and wear resistance. The split-case design divides the block horizontally, allowing access to internal components without complete engine removal for major service operations.
The cylinder bore spacing and water jacket design ensure consistent cooling across all cylinders, while the low deck height contributes to compact packaging and reduced center of gravity. The main bearing supports feature robust construction with adequate material thickness to handle the unique stress patterns created by the boxer configuration.
Internal component quality reflects Subaru’s extensive experience with boxer engine development spanning several decades. The forged steel crankshaft features 180-degree crank pin spacing that creates the characteristic boxer engine firing order, while robust main journal dimensions ensure adequate bearing area for long-term durability.
The connecting rods employ high-quality steel construction with precision machining tolerances, while the pistons feature lightweight aluminum construction optimized for the unique combustion chamber geometry created by the horizontally opposed layout.

The cylinder head design incorporates dual overhead camshafts per bank, creating a total of four camshafts that provide exceptional valve train control and breathing capability. Each cylinder head features independent cooling circuits and oil supply systems, ensuring consistent operating conditions across all cylinders regardless of vehicle attitude or operating conditions.
The valve train employs hydraulic lash adjusters that automatically maintain proper valve clearances, eliminating maintenance requirements while ensuring optimal performance throughout the engine’s service life.
Oiling system design addresses the unique challenges presented by the horizontally opposed cylinder configuration, where conventional oil pan designs cannot rely on gravity alone for oil return.
The EJ25 employs a sophisticated dry sump-like oiling system with multiple oil return paths and a robust oil pump that ensures consistent lubrication regardless of vehicle attitude. Oil passages throughout the engine are generously dimensioned, while the oil pan design incorporates baffling and multiple pickup points to prevent oil starvation during aggressive driving maneuvers.
One of the most impressive aspects of naturally aspirated EJ25 reliability involves its exceptional tolerance for diverse operating conditions and maintenance practices.
The engine’s robust construction and generous engineering margins allow it to survive conditions that would destroy many conventional engines, including severe overheating incidents, extended oil change intervals, and operation at extreme angles during off-road use. This tolerance stems from conservative design parameters throughout the engine, including generous bearing clearances and robust cooling system design.
The timing belt system represents the primary maintenance consideration for EJ25 engines, requiring replacement every 105,000 miles along with associated water pump and tensioner components.
While this represents a significant maintenance expense, the timing belt design provides several reliability advantages over timing chain systems, including precise timing control, reduced noise, and the ability to absorb torsional vibrations that might otherwise stress internal components. When properly maintained, the timing belt system proves exceptionally reliable throughout multiple replacement cycles.
Fuel injection system design emphasizes simplicity and reliability through traditional port fuel injection technology. The EJ25 avoids the complexity and potential carbon buildup issues associated with direct injection systems, while providing excellent fuel distribution and atomization characteristics.
The intake manifold design takes advantage of the boxer configuration to provide equal-length runners to all cylinders, ensuring consistent fuel delivery and optimal performance balance. Performance characteristics of the naturally aspirated EJ25 provide an excellent balance between power output and long-term durability.
The engine produces approximately 165 horsepower and 166 lb-ft of torque, figures that provide adequate performance for most applications while ensuring conservative stress levels on internal components. The engine’s power delivery remains smooth and linear throughout its rev range, with the characteristic boxer engine sound that many enthusiasts find appealing.
Real-world durability reports consistently demonstrate the EJ25’s exceptional longevity potential when properly maintained. Many examples exist of these engines exceeding 300,000 miles without major internal work, while maintaining original compression specifications and minimal oil consumption. The engine’s reputation among Subaru enthusiasts and fleet operators reflects its proven ability to provide reliable service under diverse and demanding operating conditions.
5 Budget Engines That Don’t Even Try
These disposable powerplants suffer from planned obsolescence due to cost-cutting manufacturing decisions, inadequate materials selection, and minimal engineering investment that creates predictable failure patterns well before reaching reasonable mileage expectations for budget-conscious consumers.
Their problematic engineering includes plastic components in critical areas, basic metallurgy choices, and insufficient quality control measures that amplify the reliability issues typically associated with extremely low-cost production methods during normal operating conditions.
From timing chain failures that destroy entire engines to oil consumption problems that require constant monitoring and expensive repairs, these powerplants demand replacement rather than repair strategies.
Owners discover that while these engines offer attractive initial purchase prices and basic transportation capability, their reliability limitations create false economy through frequent breakdowns and premature replacement requirements that ultimately cost more than investing in proven, durable alternatives.
1. Nissan CVT-Equipped QR25DE 2.5L Four-Cylinder
Nissan’s QR25DE 2.5-liter four-cylinder engine, particularly when paired with the company’s continuously variable transmission (CVT), represents one of the most problematic powerplant combinations in modern budget car segments.
While the engine itself shows reasonable design principles, its integration with Nissan’s notoriously unreliable CVT systems and various cost-cutting measures implemented throughout its production run have created a reliability nightmare that has cost Nissan considerable market share and customer loyalty.
The QR25DE’s basic architecture appears sound on paper, featuring aluminum block construction with cast-iron cylinder liners and dual overhead camshaft cylinder head design. However, closer examination reveals numerous cost-cutting measures that compromise long-term durability in favor of initial manufacturing cost reduction.
The block casting quality varies significantly between production runs, with some examples suffering from porosity issues that lead to internal coolant leaks and head gasket failures. The cylinder head design, while functional, lacks the robust construction found in competing engines from Honda and Toyota.
Internal component quality represents the most significant weakness in the QR25DE’s design. The crankshaft employs cast construction rather than forged steel, creating potential failure points under sustained high-load operation.

The connecting rods feature lightweight construction that prioritizes fuel economy over durability, while the pistons employ cost-optimized designs that prove susceptible to ring land damage and excessive oil consumption after moderate mileage accumulation. The piston rings themselves utilize budget-oriented materials that lose sealing effectiveness much earlier than competing engines.
The oiling system design reveals numerous compromises that affect long-term reliability. The oil pump features plastic components that prove susceptible to wear and failure, particularly in high-mileage applications where oil contamination and viscosity breakdown occur.
Oil passages throughout the engine are sized for adequate flow under ideal conditions but lack the generous margins found in truly reliable engines. The oil pan design provides minimal baffling, making the engine susceptible to oil starvation during aggressive driving or steep grade operation.
One of the most problematic aspects of QR25DE operation involves its integration with Nissan’s CVT systems. The CVT’s operating characteristics create unique stress patterns on the engine that traditional automatic transmissions do not impose.
The constant load variation and lack of distinct shift points place unusual demands on the engine’s power delivery characteristics, contributing to accelerated wear on internal components. Additionally, CVT failure modes often result in metal contamination that can damage the engine’s oiling system and internal components.
Real-world reliability reports consistently demonstrate the QR25DE’s problematic nature, particularly when combined with CVT transmissions. Engine failures commonly occur between 80,000 and 120,000 miles, often involving catastrophic internal damage that requires complete engine replacement.
Oil consumption problems develop early in the engine’s life, with many examples consuming more than one quart per 1,000 miles by 60,000 miles of operation. The combination of engine and transmission problems often results in total vehicle loss, making these powertrains among the least cost-effective options in the budget car segment.
2. Ford 1.6L EcoBoost Four-Cylinder (Sigma)
Ford’s 1.6-liter EcoBoost four-cylinder engine represents an ambitious attempt to combine small displacement with turbocharged performance, but the execution reveals numerous fundamental flaws that make it one of the least reliable budget engines ever produced by a major manufacturer.
The engine’s problems stem from aggressive downsizing combined with inadequate testing and cost-cutting measures that prioritize short-term performance metrics over long-term durability, resulting in a powerplant that often fails catastrophically well before reaching 100,000 miles.
The fundamental design philosophy behind the 1.6 EcoBoost prioritizes maximum power output from minimal displacement, creating stress levels on internal components that far exceed those found in naturally aspirated engines of similar output.
The turbocharger system operates at extremely high boost pressures to compensate for the small displacement, creating thermal and mechanical stresses that the engine’s budget-oriented construction cannot adequately handle.

The combination of high boost pressure, direct injection, and aggressive timing maps creates operating conditions that push every component beyond its optimal operating range.
Block construction employs lightweight aluminum with thin-wall casting techniques that reduce material costs but compromise structural integrity.
The cylinder bore spacing is minimized to reduce overall engine size, creating inadequate water jacket capacity around each cylinder. This design leads to uneven cooling, hot spots, and eventual head gasket failure in many applications.
The deck surface proves susceptible to warping under thermal stress, making head gasket sealing problematic even after professional repair attempts.
Real-world reliability statistics for the 1.6 EcoBoost are among the worst in the modern automotive industry, with widespread reports of complete engine failure before 80,000 miles.
Common failure modes include head gasket failure, turbocharger destruction, timing belt failure, and catastrophic internal damage due to oil system problems.
Repair costs often exceed the vehicle’s value, making these engines particularly problematic for budget-conscious buyers who cannot afford unexpected major repairs.
3. Chrysler 2.4L World Engine (Tigershark)
Chrysler’s 2.4-liter World Engine, marketed under the Tigershark designation in its final iterations, represents one of the most problematic budget engines ever produced by an American manufacturer.
Despite multiple revisions and updates throughout its production run, the fundamental design flaws and cost-cutting measures have never been adequately addressed, resulting in an engine that consistently fails to meet even basic reliability expectations while generating enormous warranty costs and customer dissatisfaction for Chrysler and its dealers.
The World Engine project originated as a joint venture between Chrysler, Mitsubishi, and Hyundai, intended to create a cost-effective powerplant that could be manufactured globally with minimal local adaptation. However, this collaborative approach resulted in numerous compromises and design decisions that prioritized manufacturing cost reduction over long-term durability.
The engine’s fundamental architecture shows promise, but execution reveals shortcuts and material choices that ensure premature failure under normal operating conditions.
Block construction employs aluminum casting with thin-wall techniques that reduce material costs but compromise structural integrity and heat dissipation capabilities. The cylinder bore spacing is minimized to reduce overall engine dimensions, creating inadequate water jacket capacity around each cylinder.
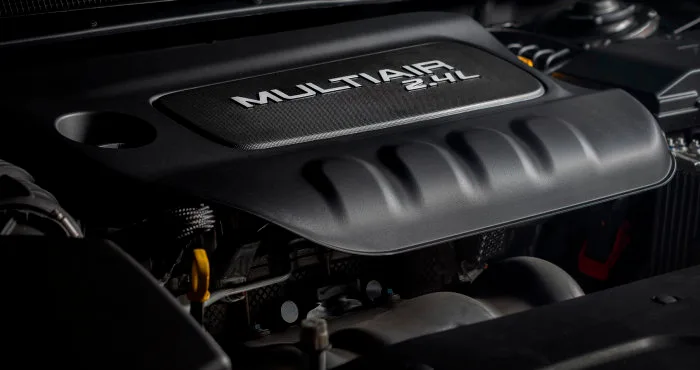
This design leads to uneven cooling, hot spot development, and eventual head gasket failure in the majority of applications. The deck surface proves particularly susceptible to warping under thermal stress, making head gasket replacement a temporary fix rather than a permanent solution.
Internal component quality reflects the cost-optimization priorities that plague every aspect of the World Engine’s design. The crankshaft employs cast iron construction with minimal counterweighting, creating excessive vibration levels that stress engine mounts and accessories while contributing to premature bearing wear.
The connecting rods feature lightweight construction with inadequate big-end bearing area, resulting in bearing failures that often occur without warning and cause catastrophic internal damage. The pistons employ cost-optimized aluminum alloys with thin ring lands that prove susceptible to cracking under thermal stress.
The oiling system represents perhaps the most problematic aspect of the World Engine’s design, with inadequate oil pump capacity and poorly designed oil passages that create lubrication problems throughout the engine.
The oil pump drive system proves particularly troublesome, with frequent failures that result in complete loss of oil pressure and catastrophic engine damage.
Oil consumption problems develop early in the engine’s life, with many examples consuming more than one quart per 1,000 miles by 50,000 miles of operation. The positive crankcase ventilation system becomes contaminated rapidly, contributing to sludge formation and accelerated component wear.
Real-world reliability statistics for the World Engine are among the worst in the automotive industry, with frequent complete engine failures occurring before 80,000 miles.
Common failure modes include oil pump failure, timing chain system destruction, head gasket failure, and catastrophic bearing damage. The engine’s reputation has become so problematic that it significantly affects the resale values of vehicles equipped with this powerplant, making it particularly costly for budget-conscious buyers.
4. Volkswagen 1.4L TSI Four-Cylinder (EA211)
Volkswagen’s 1.4-liter TSI engine from the EA211 family represents the German automaker’s attempt to combine small displacement with turbocharged performance while maintaining the premium feel expected from European vehicles.
However, the execution reveals numerous fundamental flaws that make it one of the least reliable engines in the budget car segment, with problems stemming from over-engineering, inadequate testing, and the use of experimental technologies that prove problematic in real-world applications.
The EA211’s basic architecture appears sophisticated on paper, featuring aluminum construction with integrated exhaust manifold design and advanced turbocharging technology.
However, this complexity introduces numerous potential failure points, while the cost-cutting measures required to make the engine affordable for budget applications compromise the very engineering excellence that Volkswagen traditionally represents.
The result is an engine that combines German complexity with budget-car reliability, creating the worst possible combination for long-term ownership costs.
The cylinder head design incorporates an integrated exhaust manifold that reduces external plumbing complexity but creates severe thermal management challenges.
The exhaust ports are cast directly into the cylinder head, creating hot spots that lead to head warping, valve seat recession, and eventual head gasket failure.
The cooling system design proves inadequate for the thermal loads created by this integrated design, with frequent overheating issues that accelerate component failure throughout the engine.
Turbocharger system design prioritizes compact packaging over durability, with the turbocharger mounted directly to the integrated exhaust manifold in the cylinder head.
This arrangement subjects the turbocharger to extreme thermal cycling that leads to premature bearing failure, oil coking, and eventual turbocharger destruction.
The oil feed system to the turbocharger lacks adequate capacity for high-temperature operation, while the oil drain system often becomes restricted due to coking, creating pressure buildup that damages turbocharger seals.

The timing chain system represents a major reliability concern, with premature chain stretch occurring due to inadequate tensioner design and poor chain quality.
The timing chain tensioner employs a complex hydraulic design that proves susceptible to sludge-related failures, while the chain guides utilize plastic construction that becomes brittle under the elevated temperatures created by the integrated exhaust manifold design. When timing chain problems develop, they often result in valve-to-piston contact and catastrophic internal engine damage.
Direct injection fuel system implementation introduces complexity and maintenance requirements that make the engine unsuitable for budget applications.
Carbon buildup on intake valves occurs rapidly due to the lack of fuel washing action, requiring expensive cleaning procedures every 40,000 to 50,000 miles.
The high-pressure fuel pump proves particularly problematic, with frequent failures that can contaminate the fuel system with metal particles. Fuel injector problems occur regularly, often requiring a complete fuel system overhaul at costs that exceed the vehicle’s value.
Real-world reliability reports consistently demonstrate the EA211’s problematic nature, with frequent major failures occurring before 80,000 miles.
Common problems include turbocharger failure, timing chain system destruction, carbon buildup requiring expensive cleaning, and various electronic system failures that result in poor drivability and expensive diagnostic procedures.
The complexity of the engine makes independent repair difficult and expensive, while dealer service costs often exceed what budget car owners can afford.
5. Mitsubishi 4B12 2.4L Four-Cylinder (MIVEC)
Mitsubishi’s 4B12 2.4-liter four-cylinder engine with MIVEC variable valve timing represents the culmination of the company’s declining engineering standards and cost-cutting measures that have characterized Mitsubishi’s automotive division in recent decades.
While the engine’s basic architecture shows some promise, the execution reveals numerous fundamental flaws and quality control issues that make it one of the least reliable powerplants available in the budget car segment, with problems affecting virtually every major system and component.
The 4B12’s development occurred during Mitsubishi’s financial difficulties, resulting in severe cost constraints that compromised every aspect of the engine’s design and manufacturing.
The basic architecture employs aluminum block construction with cast-iron cylinder liners, a proven combination that should provide adequate durability. However, the casting quality varies significantly between production batches, with numerous examples suffering from porosity issues that lead to internal coolant leaks, oil contamination, and eventual catastrophic failure.
Block construction reveals numerous cost-cutting measures that affect long-term reliability. The cylinder bore spacing is minimized to reduce material costs, creating inadequate water jacket capacity around each cylinder.
The main bearing supports lack adequate material thickness, leading to distortion under load and premature bearing wear. The deck surface machining quality proves inconsistent, making head gasket sealing problematic even with new components. The block casting frequently contains inclusions and porosity that create potential failure points throughout the engine’s structure.
Internal component quality reflects Mitsubishi’s budget constraints and declining manufacturing standards. The crankshaft employs cast iron construction with minimal counterweighting, creating excessive vibration levels that stress supporting components and contribute to premature bearing failure.
The connecting rods feature lightweight construction with inadequate big-end bearing area, resulting in bearing failures that often occur without warning.

The pistons employ cost-optimized aluminum alloys with thin ring lands that prove susceptible to cracking and ring sealing problems. The MIVEC variable valve timing system represents one of the most problematic aspects of the 4B12’s design, combining complexity with poor execution and inadequate quality control.
The MIVEC actuators prove exceptionally susceptible to sludge-related failures, with contamination causing the system to stick in various positions and create rough idle conditions, poor performance, and potential internal engine damage.
The oil control valves frequently fail completely, while the complex oil passages required for MIVEC operation become restricted easily, leading to system failure and expensive repairs.
The 4B12’s reliability problems are compounded by Mitsubishi’s declining dealer network and parts availability issues, making repairs difficult and expensive even when owners are willing to invest in fixing the numerous problems that develop.
The combination of poor initial quality, inadequate engineering, and limited service support makes this engine one of the worst choices available for buyers seeking reliable, long-term transportation in the budget car segment.
Also Read: 5 Hybrids With the Best Traction Off-Road and 5 Slipping Behind