Engine swaps represent one of the most transformative modifications an automotive enthusiast can undertake, fundamentally altering not just a vehicle’s performance characteristics but also its long-term reliability and lifespan.
The practice of transplanting powerplants between different vehicles has evolved from a niche pursuit of hot rodders and racers into a mainstream automotive modification, driven by advances in aftermarket support, improved documentation, and the growing availability of donor engines from salvage yards and specialty suppliers.
The relationship between engine swaps and vehicle longevity is complex and multifaceted. While some swaps can breathe new life into aging chassis by providing more reliable, fuel-efficient, or easily serviceable powerplants, others can create a cascade of mechanical failures that ultimately doom the host vehicle to premature retirement.
The key lies in understanding the compatibility between donor engine and recipient chassis, not just in terms of physical fitment, but in the broader context of stress loads, cooling requirements, electrical systems, and long-term maintenance considerations.
Modern engine swap culture has been significantly influenced by the reliability lessons learned from decades of automotive evolution.
Engines that have proven their durability over hundreds of thousands of miles in their original applications often make excellent swap candidates, while powerplants known for inherent weaknesses or complex maintenance requirements can transfer those problems to their new homes.
The most successful longevity-focused swaps typically involve well-understood, extensively documented engines with strong aftermarket support, predictable maintenance schedules, and proven track records across multiple vehicle platforms.
Conversely, swaps that prioritize peak performance over reliability, involve experimental combinations, or stress supporting systems beyond their design limits often result in shortened vehicle lifespans despite impressive initial performance gains.
5 Engine Swaps That Extend Vehicle Life
These exceptionally strategic replacements feature proven powerplant selections and precision-engineered compatibility that transform aging vehicles into reliable long-term transportation through years of enhanced performance across demanding driving conditions and extended service intervals.
Their thoughtful engineering includes simplified electronic integration, improved cooling capacity, and better fuel delivery systems that resist the reliability issues typically created by original equipment complexity or outdated technology during modern driving demands and maintenance cycles.
From replacing failure-prone turbocharged units with naturally aspirated alternatives to installing diesel powerplants for commercial longevity applications, these remarkable conversions continue providing dependable service without developing the chronic problems that plagued original configurations.
Owners report renewed vehicle confidence with these longevity-focused powerplant solutions a preservation-enhancing quality feature that proves its worth through eliminated chronic repair cycles and extended vehicle lifespan throughout continued daily transportation duties and commercial applications.
1. LS Engine Family into Classic Muscle Cars (Chevrolet Camaro, Corvette, Chevelle)
The General Motors LS engine family swap into classic American muscle cars represents perhaps the most successful longevity-focused engine transplant in modern automotive history.
Originally introduced in the 1997 Corvette as the LS1, this family of small-block V8 engines has evolved into one of the most reliable and well-supported powerplants ever produced, making it an ideal candidate for breathing new life into aging muscle car chassis from the 1960s and 1970s.
The fundamental engineering excellence of the LS architecture lies in its sophisticated yet robust design philosophy. Unlike the original small-block Chevrolet engines that came in these classic cars, LS engines feature aluminum construction in most variants, significantly reducing weight while maintaining structural integrity.
The deep-skirt block design with six-bolt main caps provides exceptional bottom-end strength, while the coil-near-plug ignition system eliminates the maintenance headaches associated with distributors and plug wires that plagued original muscle car engines.
From a longevity perspective, LS engines excel in several critical areas that directly translate to extended vehicle life. The advanced port fuel injection system provides precise fuel metering across all operating conditions, eliminating the rich-running tendencies and cylinder wash-down issues common with period-correct carburetors.
This precise fuel control, combined with sophisticated engine management, results in more complete combustion, reduced carbon buildup, and significantly lower emissions – factors that contribute to longer engine life and reduced maintenance intervals.
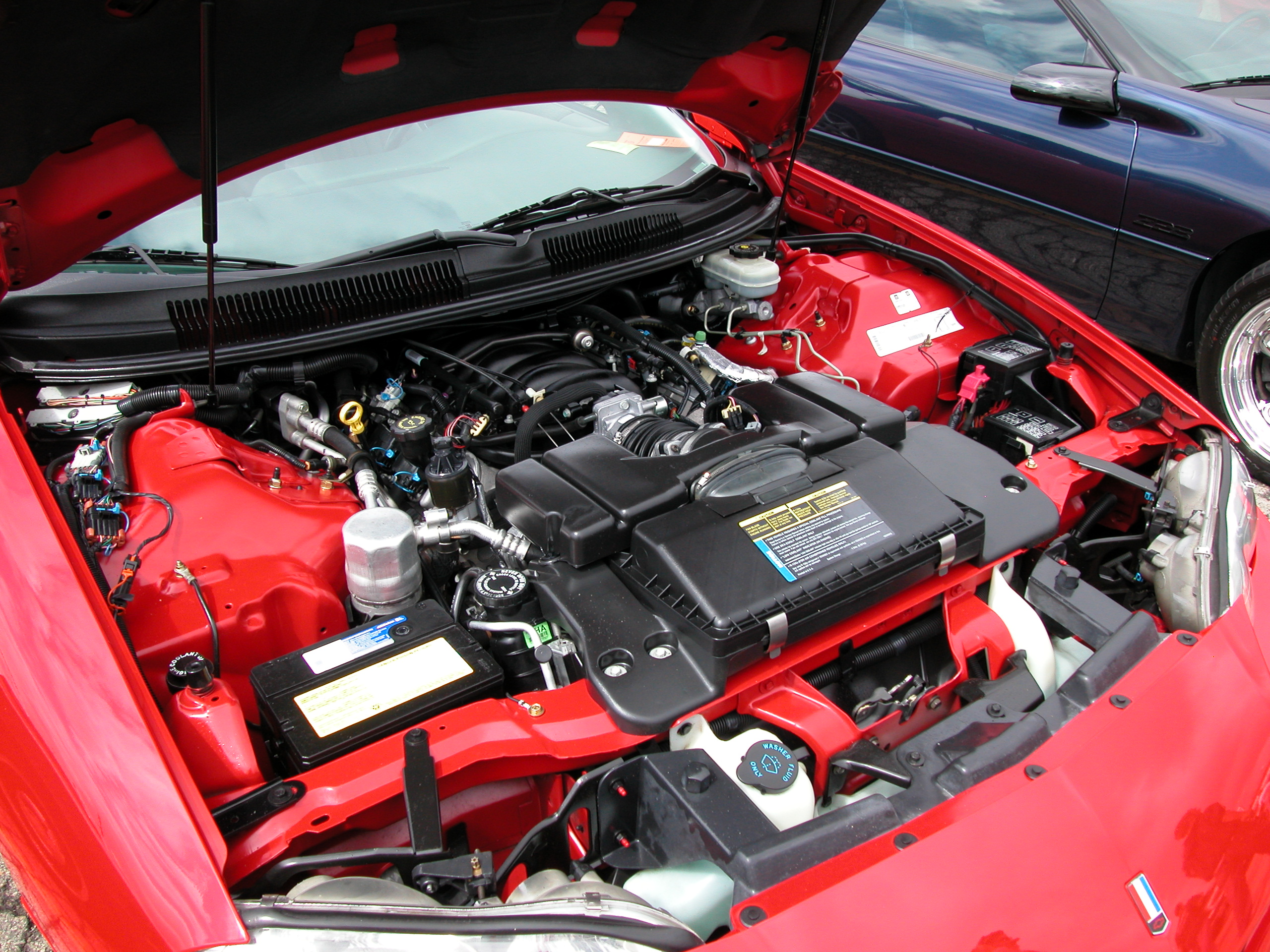
The cooling system integration represents another major advantage for long-term reliability. LS engines were designed from the ground up with modern cooling system requirements in mind, featuring optimized water jacket design, precisely controlled thermostat operation, and efficient coolant flow patterns.
When properly integrated into classic muscle car chassis with appropriately sized radiators and electric cooling fans, LS engines typically run cooler and more consistently than their original counterparts, preventing the overheating issues that frequently led to premature engine failure in classic muscle cars.
Maintenance simplicity is a crucial factor in the LS swap’s longevity benefits. The modular design allows for straightforward service procedures, with easily accessible oil filters, spark plugs, and other wear items.
The robust valvetrain, featuring self-adjusting hydraulic roller lifters and durable rocker arms, eliminates the periodic valve adjustments required by solid lifter engines, while the long-life engine oil specifications allow for extended service intervals without compromising protection.
The electrical integration aspects of LS swaps have been thoroughly refined through decades of installations, with comprehensive aftermarket support providing plug-and-play solutions for everything from engine management systems to gauge integration.
This maturity means that electrical gremlins, often the Achilles’ heel of engine swaps, are largely eliminated, contributing to long-term reliability and owner satisfaction.
Perhaps most importantly for longevity, the LS engine family has an unparalleled track record of high-mileage durability in its original applications.
Taxi fleets, police vehicles, and daily-driven trucks regularly accumulate 300,000+ miles on original LS engines with basic maintenance, providing real-world validation of the architecture’s long-term reliability.
This proven durability, combined with the reduced stress of installation in lighter classic car chassis, creates an ideal scenario for extended vehicle life.
2. Honda K-Series into Lightweight Sports Cars (Lotus Elise, Exige, Evora)
The Honda K-series engine swap into lightweight British sports cars, particularly the Lotus Elise and its variants, represents a masterclass in how thoughtful powertrain selection can dramatically extend vehicle longevity while maintaining the intended driving characteristics of the host chassis.
This particular combination has gained legendary status among enthusiasts not just for its performance benefits, but for its ability to transform notoriously maintenance-intensive British sports cars into reliable, daily-drivable machines.
Honda’s K-series engines, spanning from the K20 to the K24, embody decades of refined naturally aspirated four-cylinder technology. The VTEC variable valve timing system, while complex in theory, has proven remarkably durable in practice, with the mechanical cam switching mechanism operating reliably for hundreds of thousands of miles when properly maintained.
The all-aluminum construction keeps weight low – a critical consideration for lightweight sports cars while the closed-deck block design provides exceptional structural rigidity that can handle both stock applications and significant power modifications without compromising long-term durability.
The reliability advantages of K-series swaps become particularly apparent when compared to the original British powerplants found in cars like the Lotus Elise.
The Toyota-sourced engines used in later Elise variants, while generally reliable, still required more complex maintenance procedures and had higher parts costs than their Honda counterparts.
Earlier British engines suffered from well-documented issues, including oil pump failures, timing chain problems, and electrical system complications that could leave owners stranded and facing expensive repair bills.

From a longevity standpoint, the K-series swap addresses several fundamental weaknesses common to lightweight sports car ownership. The Honda engine’s exceptional fuel economy often achieving 35+ MPG even in spirited driving means less frequent fuel system cycling and reduced contamination from moisture and fuel degradation.
The sophisticated engine management system maintains optimal air-fuel ratios across all operating conditions, preventing the lean-running conditions that can cause premature engine wear in high-performance applications.
The mechanical simplicity of the K-series architecture contributes significantly to its longevity advantages. The chain-driven overhead cam system eliminates the belt replacement intervals and potential interference engine damage associated with timing belt failures.
The robust transmission integration, whether using Honda’s 6-speed manual or adapted alternatives, provides smooth, reliable power transfer with well-understood maintenance requirements and readily available replacement parts.
Cooling system optimization represents another crucial longevity factor in K-series swaps. The Honda engine’s efficient combustion characteristics generate less waste heat than many alternatives, while the compact packaging allows for optimal radiator placement and airflow management in the Lotus chassis.
This thermal efficiency prevents the overheating issues that can plague high-performance engines in lightweight cars, particularly during track use or aggressive driving conditions.
The electrical integration aspects of K-series swaps have been thoroughly developed by both professional tuners and dedicated enthusiasts, resulting in comprehensive wiring harness solutions that maintain full engine management functionality while integrating seamlessly with the host vehicle’s electrical systems.
This mature integration eliminates the electrical reliability concerns that often plague engine swaps, ensuring that the long-term ownership experience remains positive.
Perhaps most importantly for long-term vehicle preservation, the K-series swap maintains the fundamental character and balance that makes lightweight sports cars appealing while adding the reliability and serviceability that enables confident long-distance driving and regular use.
This transformation from weekend-only garage queen to dependable daily driver significantly extends effective vehicle life by encouraging regular operation and maintenance rather than storage-induced deterioration.
3. Toyota 2JZ-GTE into Nissan 240SX/Silvia Chassis
The Toyota 2JZ-GTE swap into Nissan 240SX and Silvia chassis represents one of the most respected engine transplants in the drifting and street performance communities, earning its reputation not just for impressive power potential but for remarkable long-term reliability under extreme conditions.
This combination brings together Toyota’s legendary bulletproof inline-six architecture with Nissan’s well-balanced rear-wheel-drive platform, creating a synergy that can provide decades of reliable service even under heavy performance use.
The 2JZ-GTE engine, originally powering the Toyota Supra Turbo from 1993-2002, was over-engineered from its inception with the intention of providing robust performance and longevity.
The iron block construction, while heavier than aluminum alternatives, provides exceptional thermal stability and wear resistance that becomes particularly valuable in high-stress applications.
The closed-deck design with seven main bearings creates a foundation capable of handling significantly more power than the stock 320 horsepower output, with many examples reliably producing 500-800 horsepower for years without internal modifications.
The longevity advantages of the 2JZ-GTE become immediately apparent when compared to the original SR20DET engines commonly found in 240SX variants.
While the Nissan turbo four-cylinder is a capable performer, it suffers from well-documented weaknesses, including oil pump drive failures, turbocharger oil starvation issues, and bottom-end durability limitations that become problematic as mileage accumulates or power levels increase.
The 2JZ-GTE’s robust oil system, featuring a gear-driven oil pump and sophisticated oil cooling provisions, virtually eliminates these failure modes while providing consistent lubrication even under extreme conditions.

The turbocharger system integration represents another significant longevity advantage. The 2JZ-GTE’s twin-turbo configuration, while complex, was designed for sustained high-output operation with sophisticated boost control, intercooling, and oil cooling systems.
The ceramic turbine wheels and advanced metallurgy used in the CT12A turbochargers provide exceptional durability compared to aftermarket alternatives, often lasting 200,000+ miles in stock configuration.
Even when upgraded to larger single-turbo configurations, the engine’s robust internals can handle the increased stress without compromising long-term reliability.
The transmission compatibility aspects of this swap contribute significantly to overall vehicle longevity. The 2JZ-GTE pairs naturally with Toyota’s robust R154 5-speed manual transmission or the even stronger V160 6-speed from later Supras.
Both transmissions have proven capable of handling significant power increases while maintaining smooth operation and predictable maintenance requirements. This drivetrain strength prevents the cascading failures often seen when powerful engines are paired with inadequate transmissions.
Cooling system optimization is crucial for 2JZ-GTE longevity, and the 240SX chassis provides an excellent platform for proper thermal management.
The inline-six configuration allows for efficient coolant flow and heat dissipation, while the front-engine, rear-drive layout provides ample space for properly sized radiators, intercoolers, and oil coolers.
When properly designed, these cooling systems can maintain optimal operating temperatures even during extended track sessions or aggressive street driving.
The electrical integration challenges of 2JZ-GTE swaps have been thoroughly addressed by the aftermarket, with standalone engine management systems like the HKS F-Con or AEM Infinity providing complete control over fuel, ignition, and boost parameters.
These systems eliminate the complexity of integrating Toyota’s factory ECU while providing the tuning flexibility necessary for optimizing performance and reliability in the new chassis environment.
From a maintenance perspective, the 2JZ-GTE benefits from Toyota’s reputation for engineering longevity into their powertrains. The robust valve train, featuring hydraulic lash adjusters and durable timing belt systems, requires only periodic timing belt service to maintain optimal operation.
The sophisticated engine management system provides diagnostic capabilities that allow for proactive maintenance and early detection of potential issues before they become catastrophic failures.
4. Ford Coyote 5.0L into Fox Body Mustangs
The Ford Coyote 5.0L engine swap into Fox Body Mustangs (1979-1993) represents a perfect marriage of modern engineering excellence with classic American muscle car aesthetics, creating a combination that significantly extends vehicle longevity while dramatically improving performance, fuel economy, and drivability.
This swap has become increasingly popular as Coyote engines become more readily available from salvage yards and Ford’s extensive aftermarket support continues to mature.
The Coyote engine, introduced in 2011 as Ford’s answer to the GM LS series, incorporates cutting-edge technology including dual overhead cams, Ti-VCT (Twin Independent Variable Camshaft Timing), and advanced port fuel injection.
This sophisticated architecture provides remarkable efficiency and power output while maintaining the durability characteristics necessary for long-term reliability.
The all-aluminum construction significantly reduces weight compared to the original iron-block engines found in Fox Body Mustangs, improving both performance and handling characteristics while reducing stress on aging suspension components. From a longevity perspective, the Coyote swap addresses numerous fundamental weaknesses inherent in original Fox Body powertrains.
The 302 Windsor and 351 Windsor engines that originally powered these cars, while charismatic, suffered from various reliability issues, including carburetor complexity, ignition system problems, and cooling system inadequacies that often led to overheating and subsequent engine damage.
The Coyote’s sophisticated engine management system eliminates these issues through precise fuel metering, advanced ignition control, and integrated cooling system management. The mechanical advantages of the Coyote architecture contribute significantly to extended vehicle life.
The chain-driven overhead cam system eliminates the timing chain stretch and guide wear issues common to pushrod engines, while the roller cam followers and sophisticated valve train geometry reduce friction and wear throughout the rpm range.

The forged steel crankshaft and powder metal connecting rods provide exceptional strength and durability, easily handling the stress of spirited driving while maintaining smooth operation through hundreds of thousands of miles.
Cooling system integration represents a critical success factor for Coyote swaps in Fox Body chassis. The modern engine’s efficient combustion characteristics and advanced thermal management systems, when properly integrated with appropriately sized radiators and electric cooling fans, provide superior temperature control compared to original powertrains.
This improved cooling prevents the overheating issues that frequently led to blown head gaskets and cracked cylinder heads in original Fox Body engines.
The transmission compatibility aspects of Coyote swaps have been thoroughly developed, with numerous companies offering adapter solutions for both manual and automatic applications.
The Tremec T56 Magnum 6-speed manual provides an ideal pairing, offering close-ratio gearing that takes full advantage of the Coyote’s broad power band while providing overdrive ratios for improved fuel economy and reduced highway cruising rpm.
For automatic applications, Ford’s 6R80 transmission integrates seamlessly and provides smooth, efficient power transfer with advanced torque converter lockup strategies.
Electrical integration has evolved significantly as the Coyote swap community has matured, with companies like Ford Racing, Holley, and others offering complete plug-and-play engine management solutions.
These systems maintain full functionality of the sophisticated Coyote engine management while providing the interface necessary for proper gauge operation and diagnostic capabilities. The elimination of electrical compatibility issues removes a major source of long-term reliability concerns.
The fuel system requirements for Coyote swaps, while more complex than carbureted applications, actually contribute to improved longevity through more precise fuel delivery and reduced fuel contamination issues.
Modern returnless fuel injection systems maintain optimal fuel pressure and temperature while preventing vapor lock and fuel percolation issues that could plague carbureted engines in hot weather or performance applications.
Also Read: 5 Performance Engines Built to Last and 5 That Burn Out Fast
5. Subaru EJ Series into Volkswagen Beetle/Type 1
The Subaru EJ series engine swap into classic Volkswagen Beetles represents one of the most transformative engine transplants available for vintage automobiles, converting notoriously underpowered and maintenance-intensive air-cooled cars into reliable, practical daily drivers with modern performance and efficiency.
This swap has gained tremendous popularity among VW enthusiasts who want to preserve the iconic Beetle aesthetic while enjoying contemporary reliability and drivability.
The EJ series engines, spanning from 1.8L to 2.5L displacement across naturally aspirated and turbocharged variants, bring decades of Subaru’s boxer engine refinement to the classic Beetle platform.
The horizontally opposed configuration proves ideally suited for rear-engine installation, maintaining the Beetle’s inherent balance characteristics while providing significantly more power and torque than any original VW air-cooled engine.
The all-aluminum construction keeps weight reasonable despite the increased displacement and complexity, preventing adverse effects on the Beetle’s delicate front-end balance.
From a longevity standpoint, the EJ swap addresses virtually every weakness associated with original VW air-cooled engines. The notorious cooling inadequacies of air-cooled VW engines, which frequently led to overheating, oil breakdown, and premature wear, are eliminated through the Subaru engine’s sophisticated liquid cooling system.
Proper radiator installation in the front luggage compartment, combined with thermostatically controlled electric fans, provides consistent temperature control regardless of ambient conditions or driving demands.
The lubrication system advantages of EJ engines cannot be overstated when compared to air-cooled VW powerplants. Original Beetle engines suffered from marginal oil capacity, poor oil circulation at idle, and inadequate filtration that led to accelerated wear and frequent rebuilds.
The EJ engine’s full-pressure lubrication system, with spin-on oil filtration and generous oil capacity, virtually eliminates these failure modes while extending service intervals and reducing maintenance costs.

Fuel system modernization represents another crucial longevity benefit. Original VW carburetors were notoriously temperamental, requiring frequent adjustment and often providing poor fuel economy and inconsistent performance.
The EJ engine’s sophisticated electronic fuel injection system delivers precise fuel metering across all operating conditions, improving fuel economy, reducing emissions, and eliminating the maintenance headaches associated with carburetor systems. This precision also prevents the rich-running conditions that could wash cylinder walls and accelerate engine wear.
The electrical system improvements inherent in EJ swaps contribute significantly to long-term reliability. Original VW electrical systems were minimalist and often problematic, with 6-volt systems that struggled to provide adequate charging and ignition performance.
The modern alternator and electronic ignition systems used with EJ engines provide reliable starting, consistent ignition timing, and sufficient electrical capacity for modern accessories and lighting systems.
Transmission integration has been thoroughly developed by the VW community, with numerous companies offering adapter solutions that mate EJ engines to either original VW transaxles or modern Subaru transmissions.
The increased torque output of EJ engines often necessitates upgrading to stronger VW Type 2 or Type 4 transaxles, but these combinations have proven reliable in thousands of installations. For ultimate durability, complete Subaru drivetrain swaps using modified Subaru transaxles provide seamless integration and bulletproof reliability.
The maintenance advantages of EJ swaps extend far beyond simple service intervals. Modern diagnostic capabilities allow for proactive maintenance and early detection of potential issues, while the widespread availability of Subaru parts ensures that maintenance and repairs can be performed affordably anywhere in the world.
This global parts availability transforms classic Beetles from garage-bound collectibles into practical transportation that can be confidently driven anywhere. Climate control benefits represent an often-overlooked longevity factor.
Original VW heating systems were marginal at best, often forcing owners to avoid driving in cold weather to prevent interior moisture buildup and subsequent rust formation. EJ swaps enable the installation of modern heating and defrosting systems that maintain proper interior climate control, preventing the moisture-related deterioration that affects many vintage vehicles.
5 Engine Swaps That End Vehicle Life
These catastrophic replacements create devastating reliability consequences due to incompatible powerplant selections, inadequate engineering preparation, and rushed installation procedures that introduce cascading system failures and electrical complications throughout the vehicle’s remaining operational lifespan.
Their problematic engineering includes mismatched computer systems, inadequate cooling modifications, and poor wiring integration that amplify the complexity issues typically associated with ambitious performance upgrades or inappropriate powerplant choices during conversion projects.
From electrical fires caused by incompatible wiring harnesses to transmission failures resulting from excessive torque applications, these swaps demand constant troubleshooting and expensive repairs that exceed vehicle value.
Owners discover that while these conversions may promise impressive performance gains and unique capabilities, their installation complications create persistent reliability nightmares and safety concerns that ultimately render vehicles unusable and require complete rebuilding or scrapping decisions.
1. High-Performance Rotary Engines into Traditional Sports Cars
The allure of rotary engine swaps, particularly the legendary Mazda 13B-REW twin-turbo from the RX-7, has captivated enthusiasts for decades with promises of incredible power-to-weight ratios and distinctive character.
However, the reality of rotary engine transplants into traditional piston-engine sports cars often results in dramatically shortened vehicle lifespans due to the unique maintenance requirements, inherent design limitations, and compatibility challenges that accompany these exotic powerplants.
The fundamental engineering philosophy behind rotary engines creates immediate longevity concerns when transplanted into vehicles originally designed for conventional piston engines.
The Wankel rotary design relies on apex seals, side seals, and corner seals to maintain compression and separate combustion chambers components that experience significantly higher wear rates than traditional piston rings and cylinder walls.
These seals operate in an environment of extreme temperature cycling and mechanical stress, typically requiring replacement every 60,000-100,000 miles even under ideal conditions. In swap applications, where cooling and lubrication systems may not be optimally integrated, seal life can be dramatically reduced.
The cooling system requirements of rotary engines present particularly challenging integration problems that often lead to long-term reliability issues. Rotary engines generate substantially more waste heat per unit of power output compared to piston engines, requiring cooling system capacity that far exceeds what most sports car chassis were designed to accommodate.
The eccentric nature of rotary combustion creates uneven heat distribution throughout the engine, necessitating sophisticated coolant routing and temperature management that is difficult to achieve in retrofit applications. Inadequate cooling leads to rapid seal deterioration, warped rotor housings, and catastrophic engine failure often within the first few thousand miles of operation.
Oil consumption represents another fundamental challenge that directly impacts vehicle longevity. Rotary engines consume oil by design, with the oil metering pump injecting lubricant directly into the combustion chambers to lubricate the apex seals.
This consumption rate, typically 1-2 quarts per 1000 miles, is far higher than any piston engine and requires religious attention to oil levels and quality. In swap applications, owners unfamiliar with this requirement often experience seal failure and engine destruction when oil levels drop below critical thresholds.
Additionally, the constant oil burning creates carbon buildup in the exhaust system, leading to premature catalytic converter failure and emissions system problems.
The fuel system demands of rotary engines, particularly turbocharged variants, create additional complexity that often overwhelms the host vehicle’s infrastructure. The 13B-REW requires sophisticated fuel delivery systems with multiple injectors, complex fuel rail configurations, and precise pressure regulation to maintain proper air-fuel ratios across the engine’s operating range.
Integrating these requirements into a chassis originally designed for simpler fuel systems often results in compromised fuel delivery, leading to lean conditions that can destroy the engine within minutes.
The high fuel consumption of rotary engines also stresses fuel system components beyond their design limits, leading to pump failures and fuel contamination issues.
Electrical integration challenges compound the reliability problems inherent in rotary swaps. The complex engine management systems required for modern rotary engines, with their multiple injectors, boost control systems, and emission controls, often prove incompatible with the host vehicle’s electrical architecture.
Attempting to integrate Mazda’s sophisticated engine management with foreign vehicle systems frequently results in electrical gremlins that can cause intermittent failures, poor performance, and premature component wear. These electrical issues are often intermittent and difficult to diagnose, leading to frustrating reliability problems that can strand owners without warning.
The vibration characteristics of rotary engines create unique stress patterns that can accelerate wear throughout the host vehicle. While rotary engines are inherently smooth in their primary balance, the eccentric motion of the rotors creates secondary vibrations and harmonic frequencies that differ significantly from those produced by piston engines.
When installed in a chassis designed for piston engines, these vibrations can cause premature wear of engine mounts, transmission components, and chassis structures, leading to expensive repairs and reduced vehicle life.
Maintenance complexity represents perhaps the most significant factor in shortened vehicle lifespan for rotary swaps. The specialized knowledge required for proper rotary engine maintenance is rare and expensive, with many general automotive technicians lacking the expertise to properly service these engines.
This often leads to deferred maintenance, improper service procedures, and costly mistakes that can destroy engines and related systems. The limited availability of qualified service providers means that minor issues often escalate into major failures, ultimately forcing vehicle retirement rather than repair.
2. Large Displacement V8s into Compact Cars
The temptation to install massive American V8 engines into compact cars has resulted in some of the most spectacular and short-lived vehicles in automotive modification history.
While the initial results can be impressive in terms of straight-line performance, these swaps typically create a cascade of reliability and structural issues that ultimately destroy the host vehicle through a combination of inadequate cooling, transmission failures, suspension component overload, and chassis fatigue that accumulates far faster than in the engine’s original application.
The fundamental mismatch between large displacement V8 engines and compact car architecture becomes immediately apparent in cooling system integration.
Compact cars were designed with minimal cooling requirements for their original four or six-cylinder engines, often featuring small radiators, single cooling fans, and limited airflow through cramped engine bays. Installing a 400+ cubic inch V8 in such an environment creates an immediate thermal management crisis.
The massive heat output of these engines quickly overwhelms undersized cooling systems, leading to chronic overheating that destroys head gaskets, warps cylinder heads, and causes rapid coolant loss.
Even with extensive cooling system modifications, the physical constraints of compact car engine bays often prevent adequate heat dissipation, resulting in shortened engine life and frequent cooling system failures.
Weight distribution problems created by V8 swaps fundamentally alter the handling characteristics and structural loading of compact cars in ways that accelerate overall vehicle deterioration.
A typical small block Chevrolet or Ford V8 weighs 150-200 pounds more than the original four-cylinder engine it replaces, while big block engines can add 300+ pounds to the front of the vehicle.
This weight addition moves the center of gravity forward and increases front axle loading beyond design specifications, causing premature wear of suspension components, steering systems, and tire wear patterns that can become dangerous.
The altered weight distribution also affects braking performance, often requiring extensive brake system upgrades that still may not adequately address the fundamental physics problems created by the swap.
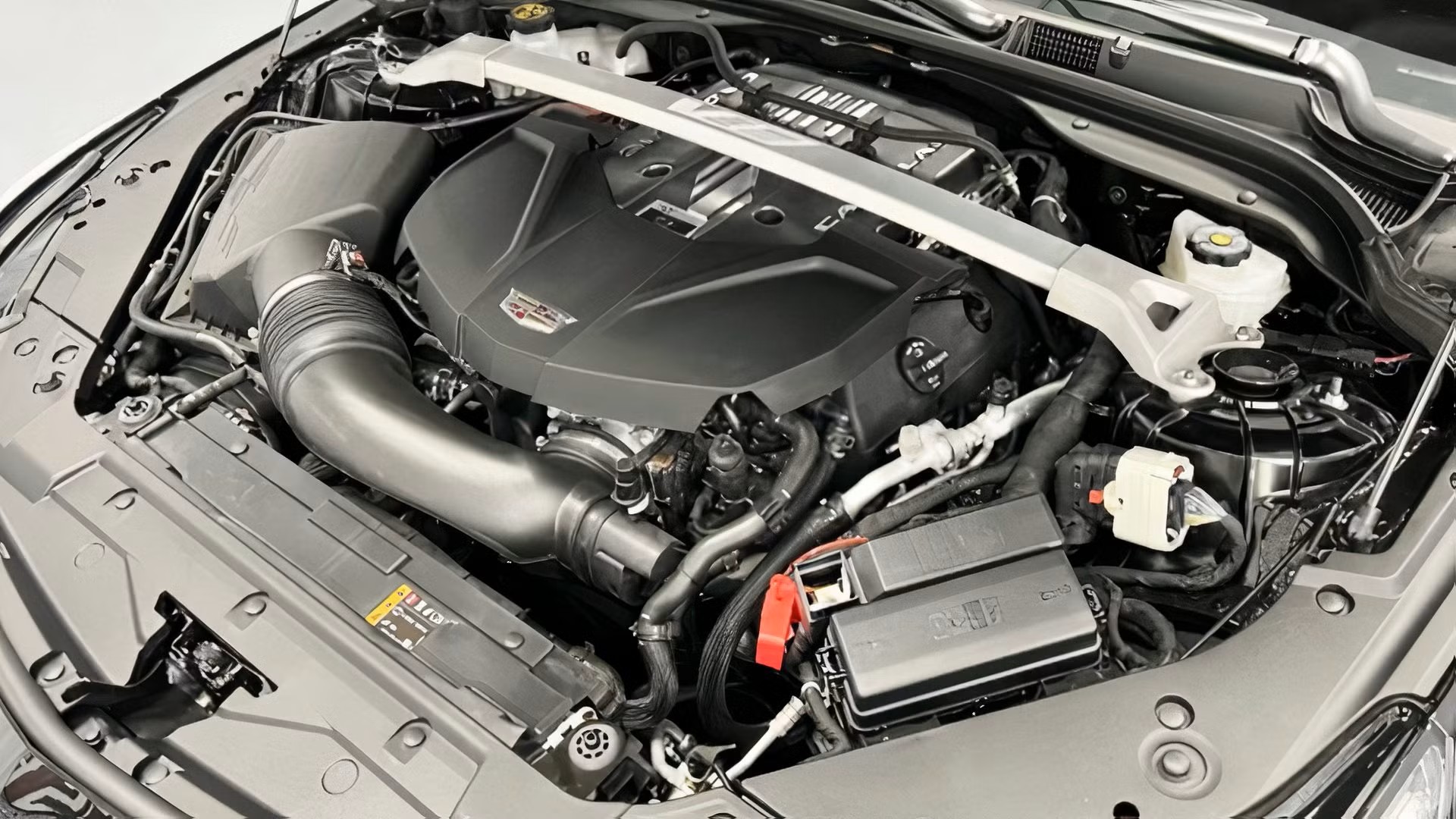
Transmission compatibility represents one of the most problematic aspects of V8 swaps into compact cars. The torque output of large displacement V8 engines typically exceeds the design limits of compact car transmissions by 200-400%, leading to rapid failure of clutches, synchronizers, and internal components.
While transmission upgrades are possible, they often require extensive modification of transmission tunnels, floor pans, and suspension mounting points that compromise structural integrity.
Even when robust transmissions are successfully integrated, the drivetrain shock loads generated by high-torque V8s can cause differential failures, axle shaft breakage, and universal joint destruction at an accelerated rate.
Fuel system inadequacies create ongoing reliability problems that often prove insurmountable in V8 swaps. Compact cars typically feature fuel systems designed for engines consuming 15-25 gallons per hour at maximum output, while large V8s can consume 50+ gallons per hour under full load.
The original fuel pumps, lines, and pressure regulators are inadequate for these demands, leading to fuel starvation under acceleration that can cause lean conditions and engine damage. Upgrading fuel systems requires extensive modification of fuel tanks, line routing, and vapor recovery systems that often prove unreliable and create fire hazards due to improper installation or inadequate engineering.
Electrical system overload represents another failure mode that accumulates over time in V8 swaps. Large V8 engines typically require high-output alternators, upgraded starter motors, and more robust ignition systems that can overwhelm the electrical capacity of compact car wiring harnesses and charging systems.
The increased current demands often cause voltage drops, connector overheating, and wire insulation failure that leads to electrical fires or complete system failures. Even when electrical systems are upgraded, the increased complexity and modification required often introduces reliability problems that can strand the vehicle without warning.
Chassis structural fatigue develops rapidly in compact cars subjected to the power and torque of large V8 engines. The unibody construction typical of compact cars was engineered for the relatively modest forces generated by small displacement engines, with specific stress calculations based on original powertrain specifications.
The dramatically increased forces from V8 engines cause stress concentrations at mounting points, frame rails, and suspension attachment areas that lead to cracking, distortion, and eventual structural failure. These problems are often not immediately apparent but accumulate over time, eventually resulting in catastrophic failures that render the vehicle unrepairable.
The increased maintenance demands and component wear rates associated with V8 swaps often overwhelm owners and lead to deferred maintenance that accelerates vehicle deterioration.
The complexity of integrating modern engine management systems, emissions controls, and safety systems creates maintenance requirements that exceed the capabilities of most owners and many service facilities.
When problems develop, the custom nature of the installation often makes diagnosis and repair extremely difficult and expensive, leading many owners to abandon the project rather than invest in proper repairs.
3. Highly Modified Turbo Four-Cylinders with Excessive Boost
The pursuit of maximum power output from small displacement turbocharged engines has led many enthusiasts down a path of modifications that ultimately destroys both the engine and the host vehicle through a combination of mechanical stress, thermal overload, and supporting system failures.
While modern turbocharged four-cylinder engines can be remarkably robust in stock configuration, the extreme modifications often employed to achieve 500+ horsepower from 2.0-liter engines create reliability problems that typically result in catastrophic failures and shortened vehicle lifespans.
The fundamental engineering principles governing internal combustion engine reliability become increasingly critical as power density increases beyond manufacturer specifications.
Turbocharged engines operating at elevated boost levels generate cylinder pressures that can exceed design limits by 100% or more, creating mechanical stresses throughout the engine that accelerate wear and increase the likelihood of catastrophic failure.
The connecting rods, pistons, and cylinder heads of production engines are engineered with specific safety factors based on stock boost levels and power outputs.
When these limits are exceeded through aggressive tuning, the safety margins are eliminated, making the engine vulnerable to destruction from minor fueling errors, detonation events, or mechanical malfunctions that would be benign in stock applications.
Cooling system inadequacies become critical failure points when turbocharged engines are pushed to extreme power levels. The combination of increased combustion heat generation and turbocharger heat rejection creates thermal loads that can overwhelm even extensively modified cooling systems.
Intercooler efficiency becomes crucial as intake air temperatures rise with increased boost pressure, but the physical constraints of most engine bays limit intercooler sizing and airflow. High intake air temperatures reduce knock resistance and increase the likelihood of detonation, which can destroy pistons and cylinder heads within seconds.
Even when cooling systems are extensively upgraded, the thermal cycling associated with high-boost operation accelerates fatigue in cooling system components, leading to frequent failures of radiators, hoses, and water pumps.

Turbocharger reliability becomes exponentially more problematic as boost levels increase beyond stock specifications. Production turbochargers are engineered for specific pressure ratios, mass flow rates, and thermal conditions that ensure reasonable service life under normal operating conditions.
Operating turbochargers at elevated boost levels increases exhaust gas temperatures, compressor discharge temperatures, and shaft speeds beyond design limits, leading to accelerated bearing wear, compressor wheel failure, and turbine housing cracking.
The oil starvation issues common to turbocharged engines become critical when turbochargers operate at extreme speeds and temperatures, often resulting in bearing seizure and complete turbocharger destruction that can damage the entire engine through oil contamination and debris ingestion.
Fuel system limitations create particularly dangerous failure modes in high-boost applications. The exponentially increasing fuel requirements of turbocharged engines operating at elevated boost levels quickly exceed the capacity of stock fuel injection systems. When fuel injectors reach their maximum duty cycle, lean conditions develop that can cause piston melting and cylinder head damage within minutes.
Even when fuel injectors are upgraded, fuel pump capacity, fuel line sizing, and fuel pressure regulation become limiting factors that can create dangerous lean conditions under full load. The complexity of properly sizing and tuning fuel systems for extreme boost applications often exceeds the capabilities of many tuners, leading to marginal fuel delivery that eventually results in engine destruction.
Engine management system limitations compound the reliability problems associated with high-boost modifications. Stock engine control units are programmed with conservative fuel and ignition maps designed to ensure reliability across a wide range of operating conditions and fuel qualities.
Achieving maximum power output at elevated boost levels requires aggressive tuning that eliminates safety margins and optimizes performance for specific conditions.
This optimization often makes the engine extremely sensitive to variations in fuel quality, ambient temperature, and atmospheric pressure, creating situations where the engine operates safely under ideal conditions but suffers catastrophic failure when conditions change.
The complexity of properly tuning high-boost applications requires extensive knowledge and experience that is often lacking in the modification community. Transmission and drivetrain component failures become increasingly common as turbo four-cylinder engines are modified for extreme power output.
The torque multiplication characteristics of turbocharged engines create shock loads throughout the drivetrain that can exceed the design limits of clutches, transmissions, and differential components. The sudden torque application characteristic of turbocharged engines is particularly destructive to manual transmissions, often causing synchronizer damage, gear tooth breakage, and input shaft failure.
Even when drivetrain components are upgraded, the increased stress and shock loading accelerates wear rates and reduces component life significantly. The supporting system modifications required for reliable high-boost operation often compromise other aspects of vehicle functionality and reliability.
Larger fuel injectors can cause poor idle quality and drivability problems, while aggressive camshaft profiles can reduce low-end torque and increase emissions. The extensive modifications required for cooling, fuel delivery, and engine management often compromise the vehicle’s ability to pass emissions testing, limiting its usefulness as transportation.
The complexity and interconnected nature of these modifications create troubleshooting nightmares when problems develop, often leading to cascading failures that render the vehicle inoperable.
4. Diesel Engines into Gasoline Vehicle Chassis
The conversion of gasoline-powered vehicles to diesel operation, while theoretically offering benefits in fuel economy and torque output, typically results in shortened vehicle lifespans due to the fundamental incompatibilities between diesel engine characteristics and chassis systems designed for gasoline engines.
The weight, vibration, and operating characteristics of diesel engines create stress patterns and mechanical loads that accelerate wear throughout the host vehicle while introducing reliability challenges that often prove insurmountable for most enthusiasts and even professional installers.
The substantial weight penalty associated with diesel engines immediately compromises the structural and dynamic characteristics of vehicles designed for lighter gasoline powerplants. Modern diesel engines typically weigh 200-400 pounds more than equivalent gasoline engines due to their heavy-duty construction requirements, with the additional weight concentrated at the front of the vehicle.
This weight increase moves the center of gravity forward, increases front axle loading beyond design specifications, and alters weight distribution in ways that accelerate tire wear, brake component wear, and suspension system fatigue. The increased unsprung weight at the front axle also degrades handling characteristics and steering responsiveness while increasing the loads transmitted to chassis components beyond their design limits.
Vibration characteristics of diesel engines create unique stress patterns that accelerate fatigue throughout the host vehicle structure. The compression ignition process inherent to diesel operation generates significantly higher combustion pressures and more abrupt pressure rises compared to gasoline engines, resulting in increased vibration amplitudes and different harmonic frequencies.
When these vibrations are transmitted through engine mounts and chassis structures designed for the smoother operation of gasoline engines, they create resonance conditions and stress concentrations that lead to premature failure of exhaust systems, body panels, interior components, and structural elements.
The diesel knock characteristic, while normal for compression ignition engines, transmits harsh vibrations through the chassis that can cause dashboard rattles, door panel loosening, and accelerated wear of rubber components throughout the vehicle.
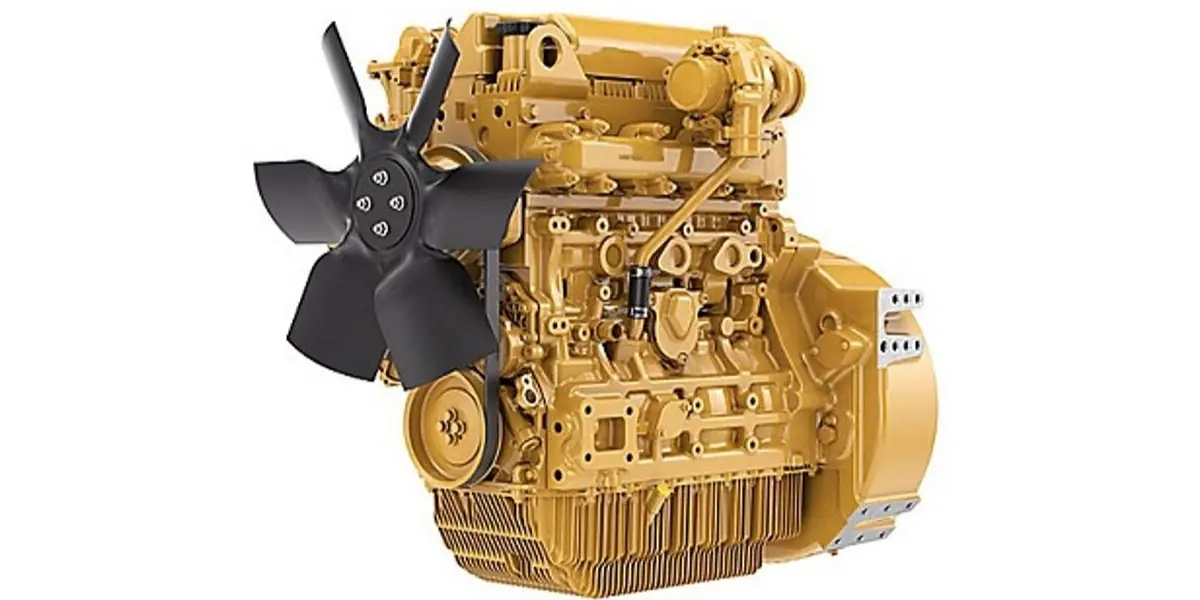
Cooling system integration presents particularly challenging obstacles for diesel conversions that often result in chronic overheating and related failures. Diesel engines generate substantially more waste heat per unit of power output compared to gasoline engines, while also operating at higher peak combustion temperatures that stress cooling system components.
The radiator capacity, water pump flow rates, and cooling fan specifications of gasoline vehicles are typically inadequate for diesel heat rejection requirements, leading to elevated operating temperatures that reduce component life and increase the likelihood of head gasket failures, cylinder head warping, and coolant system component deterioration.
Even when cooling systems are extensively upgraded, the space constraints of engine bays designed for gasoline engines often prevent adequate airflow and heat dissipation. Fuel system modifications required for diesel operation introduce complexity and reliability concerns that often prove problematic throughout the vehicle’s remaining lifespan.
Diesel fuel injection systems operate at pressures of 15,000-30,000 PSI compared to the 40-60 PSI typical of gasoline systems, requiring completely different fuel delivery infrastructure including high-pressure pumps, injection lines, and filtration systems.
The integration of these high-pressure systems into vehicles designed for low-pressure gasoline fuel delivery often results in inadequate fuel filtration, which can cause premature injection system wear and expensive component failures.
Additionally, diesel fuel’s different storage characteristics, including its tendency to gel in cold temperatures and support microbial growth, create fuel system maintenance requirements that are foreign to most gasoline vehicle owners.
Emissions system complications represent another source of long-term reliability problems in diesel conversions. Modern diesel engines require sophisticated emissions control systems including diesel particulate filters, selective catalytic reduction systems, and exhaust gas recirculation systems that are extremely difficult to integrate into vehicles not originally designed for these components.
The complexity and interdependence of these systems create numerous potential failure points, while the high exhaust temperatures and corrosive exhaust gases associated with diesel operation accelerate deterioration of exhaust system components. Attempting to circumvent emissions requirements through system deletion often results in poor drivability, increased emissions, and potential legal complications that can affect vehicle registration and insurance coverage.
Electrical system incompatibilities create ongoing reliability challenges that compound over time in diesel conversions. Diesel engines require high-current glow plug systems, robust starter motors capable of overcoming high compression ratios, and often complex engine management systems that can overwhelm the electrical capacity of vehicles designed for gasoline engines.
The higher current demands of diesel starting systems can cause voltage drops, connection overheating, and battery life reduction that creates reliability problems, particularly in cold weather when diesel starting requirements are most demanding.
Additionally, the electromagnetic interference generated by high-pressure diesel injection systems can cause problems with sensitive electronic systems in modern vehicles.
5. Experimental or Prototype Engines with Unproven Reliability
The allure of cutting-edge technology and unique powerplant combinations has led many enthusiasts to experiment with prototype engines, early production units, or exotic powerplants that lack the extensive real-world validation necessary for long-term reliability.
These experimental swaps, while intellectually fascinating and potentially offering impressive performance characteristics, typically result in dramatically shortened vehicle lifespans due to undeveloped maintenance procedures, limited parts availability, and inherent design flaws that only become apparent after extended operation.
The fundamental challenge with experimental engine swaps lies in the absence of extensive real-world testing and validation that production engines undergo before reaching the market. Production engines benefit from hundreds of thousands of miles of testing across various operating conditions, climate zones, and duty cycles before achieving market release.
This testing reveals potential failure modes, allows for design refinements, and establishes maintenance procedures that ensure reasonable longevity. Experimental engines lack this validation, making them vulnerable to unexpected failures that can occur without warning and often result in catastrophic damage that extends beyond the engine itself to related vehicle systems.
Parts availability represents a critical long-term reliability factor that often proves insurmountable for experimental engine swaps. Production engines benefit from extensive supply chains, aftermarket support, and standardized replacement parts that ensure maintenance and repair capabilities throughout the engine’s service life.
Experimental engines often rely on prototype parts, limited production runs, or custom-manufactured components that become unavailable as projects are discontinued or companies shift focus to other developments. When these engines require maintenance or repair, owners often face impossible parts sourcing challenges that force vehicle retirement rather than repair, regardless of the engine’s actual condition.

The technical support infrastructure necessary for proper maintenance and troubleshooting is typically nonexistent for experimental engines, creating situations where minor problems become major failures due to lack of diagnostic information or proper service procedures.
Production engines benefit from extensive service literature, diagnostic procedures, and trained technician networks that enable proper maintenance and rapid problem resolution.
Experimental engines often lack basic service information, forcing owners to develop maintenance procedures through trial and error a process that frequently results in improper service practices that accelerate wear and increase failure rates.
Engine management and control system development often lags behind mechanical engineering in experimental power plants, creating reliability problems that manifest as poor drivability, inconsistent performance, and potential damage from improper fuel or ignition control.
Production engines undergo extensive calibration development that optimizes performance, fuel economy, and reliability across all operating conditions. Experimental engines frequently rely on preliminary calibrations that may work adequately under ideal conditions but prove inadequate when faced with real-world variables such as altitude changes, temperature extremes, or fuel quality variations.
These calibration inadequacies can result in engine damage from detonation, overheating, or mechanical overstress that occurs when the engine management system fails to properly protect the engine under adverse conditions.
Quality control and manufacturing consistency issues plague many experimental engines, as the limited production volumes and developmental nature of these powerplants often preclude the rigorous quality assurance processes employed in production engine manufacturing.
Critical tolerances, material specifications, and assembly procedures may vary between individual engines, creating situations where some units operate reliably while others suffer premature failures due to manufacturing defects.
The lack of established quality control procedures means that potential problems may not be identified until after engine installation and break-in, often requiring expensive removal and reinstallation procedures to address manufacturing-related issues.
Integration challenges with host vehicle systems become particularly problematic with experimental engines, as the unique characteristics and requirements of these powerplants often conflict with standard automotive systems in unexpected ways.
Production engines are designed with consideration for integration requirements, including emissions compliance, noise and vibration characteristics, and compatibility with standard transmission and cooling system designs.
Experimental engines may lack these integration considerations, requiring extensive custom work to achieve proper system integration work that often introduces reliability compromises or compatibility issues that become apparent only after extended operation.
The financial implications of experimental engine failures often accelerate vehicle retirement beyond what would be economically justified for production engine problems. When experimental engines fail, the combination of unavailable parts, lack of service expertise, and custom integration requirements often creates repair costs that exceed the value of the host vehicle.
Unlike production engines, where failure analysis, warranty support, and established repair procedures can limit financial exposure, experimental engine failures typically result in total loss situations where the entire project must be abandoned. This economic reality means that experimental engine swaps often have extremely short service lives, regardless of their theoretical potential or initial performance characteristics.
The documentation and knowledge transfer problems associated with experimental engines create ongoing challenges that worsen over time as institutional knowledge is lost and original developers move on to other projects.
Production engines benefit from comprehensive service manuals, technical bulletins, and ongoing manufacturer support that preserves critical maintenance and repair information throughout the engine’s service life.
Experimental engines often rely on informal knowledge networks, personal relationships, and undocumented procedures that become unavailable as time passes and people change focus. This knowledge erosion makes long-term ownership increasingly difficult and expensive, often forcing vehicle retirement when critical information becomes unavailable rather than when the engine fails.
Also Read: 5 Budget Engines With Million-Mile Potential and 5 That Don’t Even Try