When it comes to towing heavy loads, whether it’s a massive RV across the country, a boat to the lake every weekend, or construction equipment to job sites, your engine becomes the heart that either powers through challenges or leaves you stranded on the roadside.
The difference between a reliable towing engine and a problematic one isn’t just about convenience; it’s about thousands of dollars in repair bills, missed opportunities, and the peace of mind that comes with knowing your truck will start every morning and haul your load without hesitation.
Towing places extraordinary demands on an engine that normal driving simply cannot replicate. The constant high-load operation, elevated operating temperatures, increased stress on internal components, and extended periods of peak performance separate the champions from the pretenders in the automotive world.
Some engines thrive under these conditions, earning legendary reputations for reliability that span decades and hundreds of thousands of miles. Others, despite impressive marketing claims and impressive horsepower figures, crumble under the relentless pressure of heavy-duty work.
The engines featured in our “forever” category have earned their reputations through real-world performance, standing the test of time with owners who’ve put hundreds of thousands of miles on them while towing heavy loads.
These powerplants combine robust engineering, proven durability, and the ability to maintain performance even after years of hard work. Conversely, the engines in our “struggle” category represent cautionary tales powerplants that may perform well initially but develop chronic problems, require frequent repairs, or simply weren’t designed for the rigors of serious towing duty.
Understanding which engines fall into each category can save you thousands in repair costs and ensure your towing adventures remain adventures, not roadside emergencies.
5 Engines That Last Forever
These exceptionally robust powerplants feature conservative tuning parameters and precision-engineered cooling systems that deliver sustained towing performance through years of heavy-duty trailer hauling across demanding terrain conditions and extreme temperature variations without developing overheating or component failure issues.
Their thoughtful engineering includes oversized radiators, reinforced internal components, and generous torque reserves that resist the stress concentrations typically created by sustained high-load operation or mountain climbing with maximum trailer weights during commercial and recreational towing applications.
From construction equipment transport that demands constant power delivery to RV hauling scenarios where reliability matters for family safety, these remarkable engines continue providing dependable service without experiencing power degradation or cooling system failures.
Owners report decades of confident towing with these bulletproof powerplant solutions a durability-enhancing quality feature that proves its worth through maintained pulling power and extended component life throughout heavy-duty hauling applications and regular trailer transportation duties.
1. Cummins 6.7L Turbo Diesel I6 (Ram HD)
The Cummins 6.7L turbo diesel inline-six represents the gold standard of towing engines, a powerplant so legendary that it has single-handedly carried Ram’s heavy-duty truck reputation for over three decades.
This engine doesn’t just tow heavy loads it does so with a reliability that borders on the supernatural, earning devotion from owners that runs deeper than brand loyalty and approaches something closer to religious faith.
What makes the 6.7L Cummins so exceptional begins with its fundamental architecture. The inline-six configuration provides inherently better balance than V8 alternatives, reducing vibration and internal stress that can lead to premature wear.
The cast-iron block construction, while heavier than aluminum alternatives, provides thermal stability and durability that aluminum simply cannot match when subjected to the constant heat cycling of heavy towing.
The cylinder head, also cast iron, maintains consistent sealing even after hundreds of thousands of miles of thermal expansion and contraction.
The turbocharging system on the 6.7L Cummins represents sophisticated engineering designed for longevity rather than just peak performance. The variable geometry turbocharger adjusts its internal geometry to provide optimal boost across the entire RPM range, ensuring that the engine develops its peak torque of 1,000 lb-ft at just 1,600 RPM.
This low-end torque characteristic means the engine doesn’t have to work as hard to move heavy loads, reducing internal stress and extending component life. The turbocharger itself is built to withstand the constant high-temperature operation that comes with towing, using materials and bearing systems designed for commercial truck applications.
Fuel injection on the 6.7L Cummins utilizes a high-pressure common rail system that delivers precise fuel metering under all operating conditions. The system operates at pressures exceeding 29,000 PSI, atomizing fuel so thoroughly that combustion efficiency remains high even under the varying loads encountered during towing.
This precision fuel delivery not only maximizes power and efficiency but also minimizes the formation of carbon deposits that can plague other diesel engines over time.
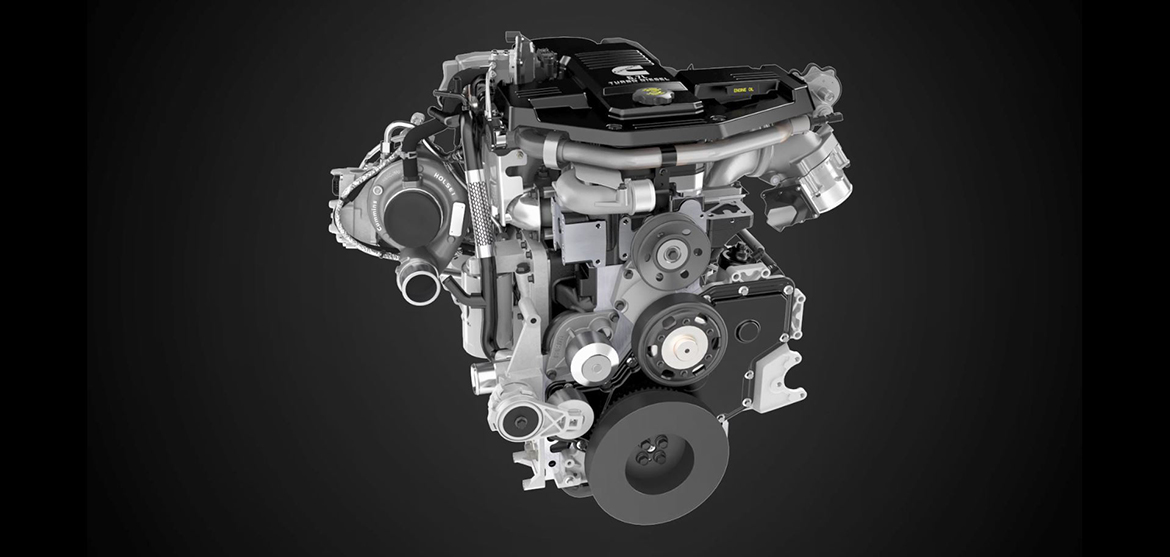
The cooling system represents another area where Cummins’ engineering excellence shines. The engine features a massive cooling capacity designed not just for normal operation but for sustained high-load work.
The cooling system includes features like coolant bypass valves that help maintain optimal operating temperatures during warm-up, and a robust radiator design that can dissipate the enormous heat loads generated during heavy towing in challenging conditions.
Maintenance intervals on the 6.7L Cummins reflect its commercial-grade engineering. Oil changes are required every 15,000 miles under normal conditions, but the engine’s robust construction means that even if maintenance is occasionally delayed, catastrophic failure is unlikely.
The engine uses a full-flow oil filtration system with a high-capacity filter that improves oil quality over time by removing contaminants and allowing additives to properly condition engine internals.
Real-world performance data supports the 6.7L Cummins’s reputation for longevity. Owner forums regularly feature examples of engines exceeding 300,000 miles with only routine maintenance, and commercial applications often see these engines surpass 500,000 miles before requiring major service.
The engine’s ability to maintain its power output and fuel efficiency even at high mileages is particularly impressive, with many owners reporting that their high-mileage Cummins engines still pull strong and return good fuel economy. The aftermarket support for the 6.7L Cummins further enhances its longevity.
Decades of production have created a robust ecosystem of performance and maintenance parts, meaning that even if components do eventually wear out, replacements are readily available and often improved over original specifications.
The engine’s simple, robust design also means that many maintenance tasks can be performed by knowledgeable owners, reducing long-term ownership costs.
Perhaps most importantly, the 6.7L Cummins was designed from the ground up for towing applications. Unlike engines adapted from passenger car duty, every component was engineered to handle sustained high-load operation.
This purpose-built approach means that when you’re pulling a 12,000-pound trailer up a mountain pass, the engine is operating well within its design parameters rather than being pushed to its limits.
2. GM 6.6L Duramax Turbo Diesel V8 (LBZ/LLY Generations)
The General Motors 6.6L Duramax diesel engine, particularly in its LBZ and LLY iterations, represents one of the most successful diesel engine programs in American automotive history.
Developed in partnership with Isuzu, this engine combines Japanese precision engineering with American heavy-duty requirements, creating a powerplant that has earned legendary status among serious towing enthusiasts and commercial operators alike.
The foundation of the Duramax’s exceptional reliability lies in its sophisticated aluminum block construction. While aluminum blocks were once considered less durable than cast iron, the Duramax’s block features thick walls and strategically placed reinforcement ribs that provide strength equivalent to iron while offering significant weight savings.
The aluminum construction also provides superior heat dissipation, crucial for maintaining optimal operating temperatures during extended towing sessions. The cylinder liners are cast iron, providing the wear resistance necessary for long-term durability while maintaining the thermal advantages of the aluminum block.
The Duramax’s fuel injection system represents cutting-edge technology that was years ahead of its competition when introduced. The high-pressure common rail system operates at pressures up to 26,000 PSI, delivering fuel with precision that was previously impossible in diesel engines.
Each cylinder has its fuel injector controlled by sophisticated electronics that can adjust injection timing, duration, and pressure multiple times per combustion cycle. This level of control allows the engine to optimize performance for varying loads and conditions, ensuring efficient combustion whether idling in traffic or climbing a steep grade with a heavy trailer.
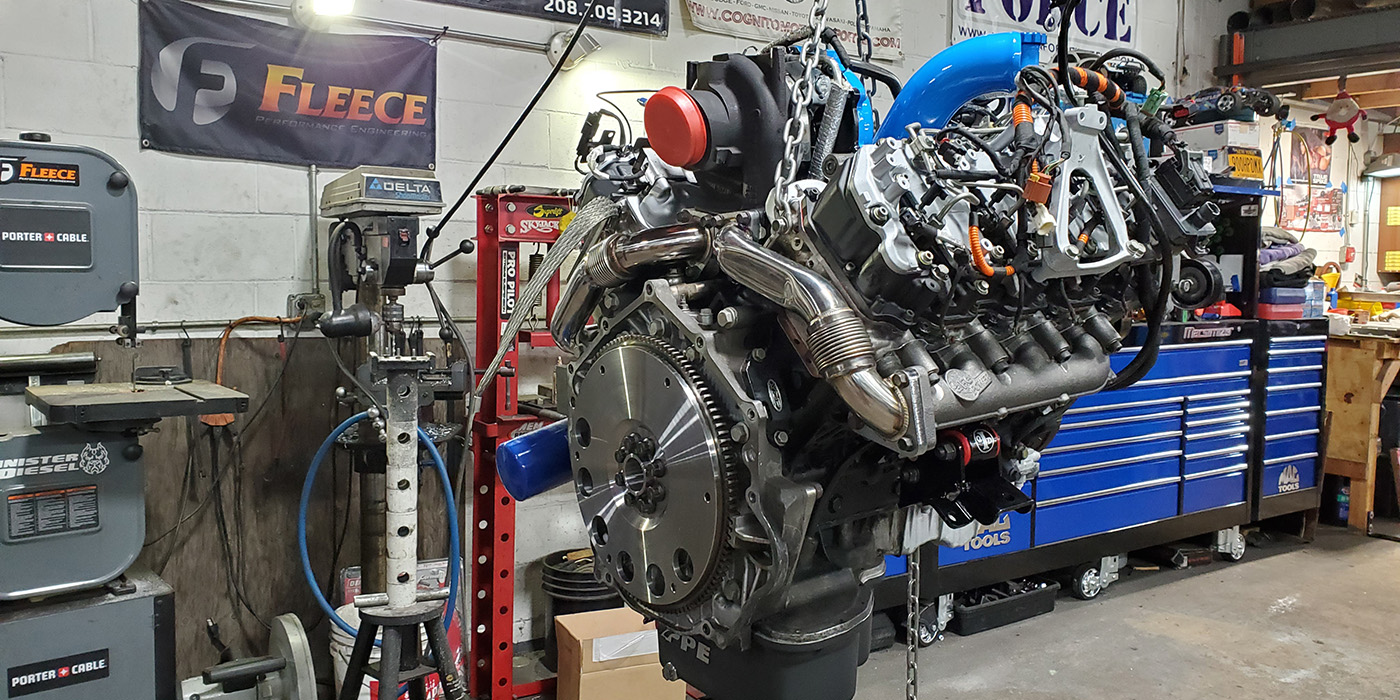
The turbocharging system on the Duramax utilizes a variable geometry turbocharger that can adjust its internal configuration to provide optimal boost across the entire operating range.
At low RPMs, the turbocharger’s vanes close to accelerate exhaust gases and spool the turbine quickly, providing immediate throttle response and strong low-end torque. As engine speed increases, the vanes open to allow higher flow rates while maintaining optimal boost pressure.
This sophisticated system eliminates the turbo lag that plagued earlier diesel engines while providing the high-altitude performance necessary for mountain towing. Cooling system design on the Duramax reflects the engineers’ understanding that thermal management is critical for diesel engine longevity.
The engine features a high-capacity cooling system with a massive radiator, robust water pump, and sophisticated thermostatic controls.
The cooling system is designed to maintain optimal operating temperatures even during extended periods of high-load operation, such as climbing mountain grades with heavy trailers. An engine oil cooler is integrated into the system, ensuring that lubrication remains effective even under extreme conditions.
The Duramax’s transmission integration deserves special mention, as the engine was designed to work seamlessly with the Allison 1000 series automatic transmission.
This pairing creates a powertrain combination that can handle enormous torque loads while providing smooth, reliable operation. The Allison transmission’s adaptive shift programming learns driving patterns and load conditions, optimizing shift points to keep the Duramax in its optimal powerband for any given situation.
Real-world durability of the LBZ and LLY Duramax engines is exceptional, with many examples exceeding 300,000 miles with only routine maintenance. The engines maintain their power output and fuel efficiency remarkably well over time, with owners regularly reporting that their high-mileage Duramax engines still provide strong performance and competitive fuel economy.
The engine’s ability to maintain tight tolerances even at high mileages speaks to the precision of its manufacturing and the quality of its materials. Maintenance requirements for the Duramax are reasonable considering its performance capabilities.
Oil changes are required every 10,000 miles under normal conditions, but the engine’s robust filtration system and high-quality oil specifications mean that the lubricant remains effective throughout the service interval. The fuel filtration system includes both primary and secondary filters, protecting the high-pressure injection system from contamination that could cause expensive failures.
The aftermarket support for the Duramax engine is extensive, with numerous companies offering performance upgrades, maintenance parts, and enhancement packages.
The engine’s sophisticated electronic controls mean that performance modifications can be made through programming changes rather than mechanical modifications, allowing owners to extract additional performance while maintaining reliability. Many commercial operators have found that mild performance modifications improve long-term durability by allowing the engine to work more efficiently.
Environmental compliance was a key consideration in the Duramax’s design, and the engine incorporates sophisticated emissions control systems that maintain performance while meeting strict standards.
The diesel particulate filter and selective catalytic reduction systems work seamlessly with the engine’s combustion optimization to reduce emissions without sacrificing the power and torque necessary for heavy towing applications.
3. Ford 7.3L Power Stroke Diesel V8 (International T444E)
The Ford 7.3L Power Stroke diesel engine stands as perhaps the most beloved diesel engine in American automotive history, a powerplant so revered that used trucks equipped with this engine often command premium prices decades after production ended.
Developed in partnership with International Harvester (later Navistar), this engine represents the perfect intersection of robust mechanical engineering and field-proven reliability, creating a legend that continues to influence diesel engine design today.
The 7.3L Power Stroke’s reputation for indestructibility begins with its fundamentally conservative engineering approach. At a time when other manufacturers were pushing the boundaries of technology and performance, Ford and International chose to prioritize reliability and longevity above all else.
The result is an engine that may not win any horsepower contests but will reliably start every morning and pull heavy loads for hundreds of thousands of miles with minimal maintenance.
The engine block construction exemplifies this conservative approach. Cast from high-grade iron with thick walls and robust main bearing caps, the 7.3L block can withstand enormous internal pressures and thermal cycling without distortion.
The cylinder heads, also cast iron, feature large coolant passages and robust valve seats that maintain their sealing properties even after extended high-temperature operation.
The head gasket design is particularly noteworthy, using a multi-layer steel construction that provides reliable sealing while accommodating the thermal expansion differences between the block and heads.
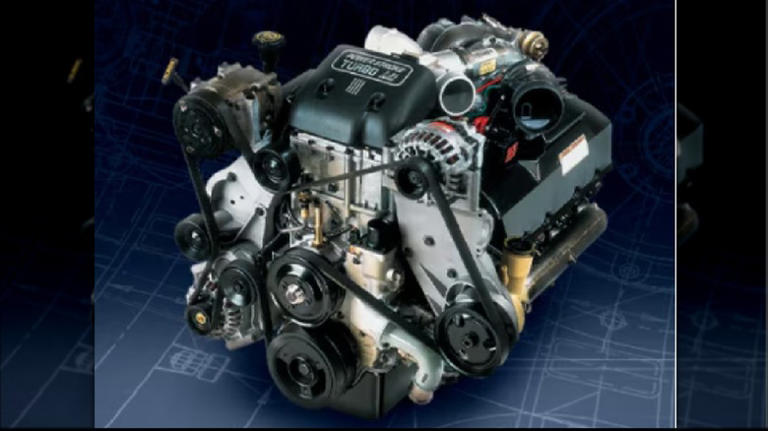
Fuel injection on the 7.3L Power Stroke utilizes a relatively simple but highly reliable system. The engine employs a Hydraulically-actuated Electronically-controlled Unit Injector (HEUI) system that uses engine oil pressure to actuate the fuel injectors. While this system doesn’t provide the precision of modern common rail systems, its simplicity means fewer failure points and easier maintenance.
Each injector is essentially a self-contained unit that can be individually replaced without affecting the others, a significant advantage for field maintenance and long-term serviceability. The turbocharging system on the 7.3L is deliberately conservative, using a single fixed-geometry turbocharger that prioritizes reliability over peak performance.
The turbocharger is sized to provide adequate boost across the operating range without creating excessive backpressure or requiring exotic materials to withstand extreme temperatures. This approach means the turbocharger typically outlasts the rest of the engine, with many examples running hundreds of thousands of miles on their original turbochargers.
Cooling system design reflects the engine’s commercial truck heritage. The massive cooling capacity includes a large radiator, robust water pump, and oversized coolant passages throughout the engine.
The system is designed to maintain optimal operating temperatures even during extended periods of high-load operation, such as pulling heavy trailers at highway speeds in desert conditions. An integrated oil cooler ensures that lubrication remains effective even under extreme thermal conditions.
The 7.3L’s electronic controls are refreshingly simple compared to modern engines, using basic sensors and straightforward programming to manage fuel delivery and timing.
This simplicity means that diagnosis and repair can often be accomplished with basic tools and knowledge, a significant advantage for owners who need to maintain their vehicles in remote locations or who prefer to perform their own maintenance.
Real-world durability statistics for the 7.3L Power Stroke are legendary. Engines with over 400,000 miles are common, and examples exceeding 500,000 miles while still providing reliable service are not unusual.
The engine’s ability to maintain its performance characteristics even at extreme mileages is particularly impressive, with many high-mileage examples still providing strong pulling power and acceptable fuel economy.
Maintenance requirements for the 7.3L are straightforward and forgiving. Oil changes are required every 5,000-7,500 miles, but the engine’s robust construction means that occasional extended intervals won’t cause catastrophic failure.
The fuel system requires regular filter changes, but the components are readily available and inexpensive. The engine’s mechanical simplicity means that most maintenance tasks can be performed with basic tools and moderate mechanical knowledge.
The aftermarket support for the 7.3L Power Stroke is extensive and mature, with decades of production creating a robust ecosystem of performance and maintenance parts. Upgrade options are available for virtually every engine component, allowing owners to improve performance while maintaining the engine’s fundamental reliability.
Many commercial operators have found that careful performance modifications can improve the engine’s longevity by reducing operating temperatures and improving combustion efficiency. The 7.3L’s reputation extends far beyond its mechanical excellence. The engine has achieved iconic status among truck enthusiasts, with many owners developing an almost emotional attachment to their engines.
This loyalty is based on years of reliable service, often under conditions that would challenge modern engines. The 7.3L’s ability to start reliably in extreme cold, operate effectively at high altitudes, and maintain performance even with minimal maintenance has created a generation of owners who simply won’t consider any other engine.
4. Toyota 5.7L iForce V8 (3UR-FE)
The Toyota 5.7L iForce V8 engine represents Japanese engineering excellence applied to American heavy-duty requirements, creating a gasoline engine that delivers exceptional reliability and longevity in towing applications.
While diesel engines often dominate discussions of towing capability, the 5.7L iForce proves that a well-engineered gasoline engine can provide both the performance and durability necessary for serious towing duty while offering advantages in maintenance simplicity and fuel availability.
The foundation of the 5.7L iForce’s exceptional reliability lies in Toyota’s legendary approach to engineering, which prioritizes long-term durability over short-term performance advantages.
The aluminum block construction features thick walls and robust main bearing caps designed to withstand the internal pressures generated by high-load operation. The cylinder heads, also aluminum, incorporate Toyota’s advanced port and chamber design that promotes efficient combustion while minimizing hot spots that could lead to pre-ignition or detonation under load.
The engine’s dual overhead cam design with four valves per cylinder provides excellent breathing characteristics that are crucial for maintaining power output during extended towing sessions.
The valve train incorporates Toyota’s proven hydraulic lash adjusters, which automatically maintain optimal valve clearances throughout the engine’s life, eliminating the need for periodic adjustments while ensuring consistent performance. The timing chain system uses a robust design with automatic tensioners that maintain proper chain tension even as components wear over time.

Variable valve timing technology on the 5.7L iForce represents sophisticated engineering that optimizes performance across the entire operating range. The system can advance or retard both intake and exhaust cam timing independently, allowing the engine to maximize torque at low RPMs for towing while maintaining high-RPM power for highway merging and passing.
This flexibility means the engine operates efficiently whether crawling up a steep grade with a heavy trailer or cruising unloaded on the highway. The fuel injection system utilizes Toyota’s advanced port fuel injection design, which provides precise fuel metering while maintaining the simplicity and reliability of port injection systems.
Each cylinder has its own electronically controlled injector that can adjust fuel delivery based on engine load, temperature, and operating conditions. The system includes sophisticated knock detection that allows the engine to operate on regular gasoline while automatically adjusting timing to prevent detonation under high-load conditions.
Cooling system design on the 5.7L iForce reflects Toyota’s understanding of thermal management requirements for towing applications. The engine features a high-capacity cooling system with a large radiator and robust water pump designed to maintain optimal operating temperatures even during extended periods of high-load operation.
The system includes features like coolant bypass valves and thermostatic controls that help maintain consistent operating temperatures across varying conditions. The 5.7L iForce’s integration with Toyota’s electronic transmission controls creates a powertrain combination optimized for towing performance.
The transmission programming includes specific towing modes that adjust shift points and torque converter lockup strategies to keep the engine in its optimal power band while minimizing heat generation. The system can also detect trailer loading and automatically adjust its operation to provide optimal performance and component protection.
Real-world durability of the 5.7L iForce engine is exceptional, with numerous examples exceeding 200,000 miles while maintaining their original power output and fuel efficiency.
The engine’s ability to maintain tight tolerances and consistent performance even at high mileages speaks to the precision of Toyota’s manufacturing processes and the quality of materials used throughout the engine. Many commercial operators have adopted the engine for fleet applications specifically because of its proven longevity and low maintenance requirements.
Maintenance requirements for the 5.7L iForce are straightforward and cost-effective. Oil changes are required every 10,000 miles under normal conditions, but the engine’s robust construction and effective filtration system mean that the lubricant remains effective throughout the service interval.
The spark plugs, using iridium electrodes, typically last 100,000 miles or more, significantly reducing maintenance costs compared to engines requiring more frequent plug changes. The 5.7L iForce’s environmental compliance systems are seamlessly integrated and don’t compromise performance or reliability.
The engine meets strict emissions standards without requiring complex aftertreatment systems like those found on diesel engines, simplifying maintenance and reducing the potential for emissions-related failures. The three-way catalytic converters are long-lived and rarely require replacement under normal operating conditions.
Cold weather performance of the 5.7L iForce is exceptional, with the engine starting reliably even in extreme conditions without requiring block heaters or other cold weather aids.
This reliability extends to high-altitude operation, where the engine’s sophisticated engine management system automatically compensates for reduced air density to maintain performance and prevent altitude-related issues that can plague other engines.
The aftermarket support for the 5.7L iForce continues to grow as the engine gains recognition for its performance and reliability. While not as extensive as some domestic engines, quality performance parts and maintenance components are readily available.
The engine’s sophisticated electronic controls allow for performance modifications through programming changes, enabling owners to extract additional performance while maintaining the engine’s legendary reliability.
Also Read: 5 Engine Swaps That Extend Life and 5 That End It
5. General Motors 6.0L Vortec V8 (LQ4/LQ9)
The General Motors 6.0L Vortec V8 engine, particularly in its LQ4 and LQ9 configurations, represents the pinnacle of pushrod V8 engineering, combining time-tested architecture with modern materials and manufacturing techniques to create an engine that excels in towing applications.
This powerplant has earned a reputation for bulletproof reliability while delivering the torque characteristics that make heavy towing effortless, all wrapped in a package that’s simple to maintain and modify.
The 6.0L Vortec’s success begins with General Motors’ decision to stick with proven pushrod architecture rather than following industry trends toward overhead cam designs.
The pushrod configuration provides several advantages for towing applications, including a lower center of gravity, more compact overall dimensions allowing for better cooling airflow, and fewer moving parts that could potentially fail under high-stress conditions.
The engine’s iron block construction provides thermal stability and durability that aluminum blocks struggle to match when subjected to the constant heat cycling of heavy towing operations.
The cylinder head design incorporates GM’s cathedral port technology, which optimizes airflow characteristics for the engine’s operating range. These ports provide excellent low-end torque production, crucial for towing applications where pulling power at low RPMs is more important than high-RPM horsepower.
The combustion chamber design promotes efficient burning of the air-fuel mixture while maintaining compression ratios that allow the engine to operate on regular gasoline, reducing operating costs for high-mileage applications.
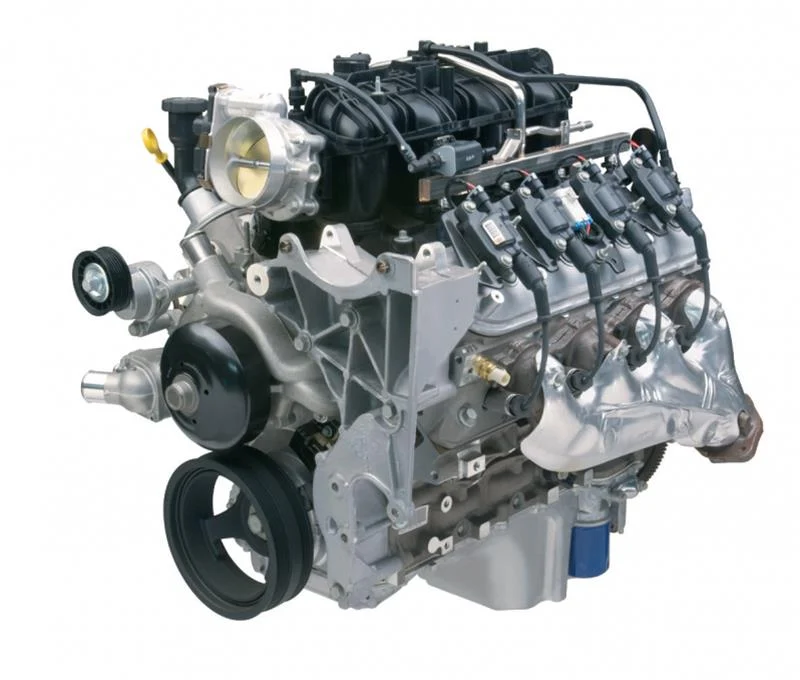
Fuel injection on the 6.0L Vortec utilizes a sequential port fuel injection system that provides precise fuel metering across all operating conditions. The system includes sophisticated closed-loop controls that continuously monitor exhaust gas composition and adjust fuel delivery to maintain optimal air-fuel ratios.
This precision control ensures efficient combustion whether the engine is idling in traffic or working hard pulling a heavy trailer up a mountain grade. The ignition system features individual coil-on-plug designs for each cylinder, eliminating the spark plug wires that were common failure points on earlier engines.
Each coil is controlled independently by the engine management system, allowing for precise timing control that can be adjusted for varying load conditions. The system features sophisticated knock detection, allowing the engine to operate on regular gasoline while automatically retarding the timing if detonation is detected.
Cooling system design on the 6.0L Vortec reflects GM’s extensive experience with heavy-duty applications. The engine features a high-capacity cooling system with a robust water pump design and large coolant passages throughout the block and heads.
The system includes features like reverse-flow cooling that ensure optimal temperature distribution across all cylinders, particularly important for maintaining consistent performance under varying load conditions.
The 6.0L Vortec’s integration with GM’s 4L80E and later 6L90E transmissions creates a powertrain combination that’s ideally suited for towing applications. The transmission programming includes specific algorithms for towing that optimize shift points and torque converter operation to maintain engine RPM in the optimal torque range while minimizing heat generation.
The system can detect trailer loading through various sensors and automatically adjust its operation accordingly. Real-world durability statistics for the 6.0L Vortec are impressive, with numerous examples exceeding 300,000 miles while still providing reliable service.
The engine’s simple architecture means fewer components that can fail, and the robust construction ensures that normal wear doesn’t compromise performance or reliability.
Many commercial operators have adopted these engines specifically because of their proven ability to provide consistent performance with minimal maintenance requirements.
Maintenance requirements for the 6.0L Vortec are straightforward and cost-effective. Oil changes are required every 7,500 miles under normal conditions, and the engine’s effective filtration system means that the lubricant remains protective throughout the service interval.
The pushrod valvetrain requires no periodic adjustments, and the hydraulic lifters automatically compensate for normal wear to maintain optimal valve operation throughout the engine’s life. The aftermarket support for the 6.0L Vortec is extensive, with the engine serving as the foundation for countless performance builds and commercial applications.
The simple architecture makes modifications straightforward, and the robust bottom end can handle significant power increases without requiring internal modifications. This extensive aftermarket support means that parts are readily available and competitively priced, reducing long-term ownership costs.
Performance characteristics of the 6.0L Vortec are ideally suited for towing applications, with peak torque available at relatively low RPMs where it’s most useful for pulling heavy loads. The engine’s torque curve is broad and flat, meaning that pulling power remains strong across a wide RPM range, reducing the need for frequent transmission shifts during varying load conditions.
This characteristic makes the engine particularly pleasant to drive when towing, as it provides strong acceleration and passing power without requiring high RPMs. The 6.0L Vortec’s reputation for reliability extends beyond mechanical durability to include consistent performance in varying conditions.
The engine starts reliably in extreme cold, maintains performance at high altitudes, and operates effectively in desert heat, making it suitable for towing applications that may encounter challenging environmental conditions. This broad operating capability, combined with proven mechanical reliability, has made the 6.0L Vortec a favorite among serious towing enthusiasts and commercial operators alike.
5 Engines That Struggle Hard
These inadequate powerplants suffer from persistent overheating issues due to insufficient cooling capacity, marginal power output, and lightweight construction that creates dangerous reliability problems during sustained towing operations and challenging terrain encounters with moderate trailer loads.
Their problematic engineering includes undersized cooling systems, aggressive tuning for fuel economy, and basic component designs that amplify the stress failures typically associated with towing demands beyond their intended capability during normal hauling scenarios.
From frequent overheating warnings that force roadside stops to transmission failures caused by excessive engine strain, these powerplants demand careful load management and constant monitoring.
Owners discover that while these engines may offer acceptable performance for daily driving and fuel economy benefits, their towing limitations create safety concerns and require avoiding challenging routes or reducing trailer weights significantly below advertised towing capacity ratings to prevent costly mechanical failures.
1. Ford 6.4L Power Stroke Diesel V8
The Ford 6.4L Power Stroke diesel engine stands as one of the most notorious examples of engineering ambition exceeding reliability capabilities in modern automotive history.
Produced from 2008 to 2010, this engine was Ford’s attempt to create a high-performance diesel that could compete with the best offerings from General Motors and Dodge, but the result was a powerplant plagued by so many fundamental design flaws that it nearly destroyed Ford’s diesel truck reputation and cost owners millions in repair bills.
The 6.4L Power Stroke’s problems begin with its basic architecture, which prioritized performance and emissions compliance over the long-term durability that commercial and serious recreational users demand.
The engine features an aluminum block with cast-iron cylinder liners, a combination that sounds sophisticated but creates thermal expansion problems that plague the engine throughout its life.
The aluminum block expands and contracts at different rates than the iron liners, creating stress points that can lead to liner movement, coolant leaks, and eventual catastrophic failure.
Perhaps the most infamous problem with the 6.4L Power Stroke is its diesel particulate filter (DPF) system, which was designed to meet strict emissions regulations but proved to be a nightmare for real-world operations.
The DPF system requires periodic regeneration cycles where the exhaust temperature is raised to extremely high levels to burn off accumulated soot particles. These regeneration cycles can occur every 300-400 miles under normal operation, but towing heavy loads or stop-and-go driving can trigger them even more frequently.
The regeneration process itself creates numerous problems. The system injects raw diesel fuel into the exhaust stream to raise temperatures, which dilutes the engine oil and can cause premature wear of internal components.
The high exhaust temperatures required for regeneration can damage downstream components and create fire hazards if the vehicle is parked near combustible materials. Most problematically, incomplete regeneration cycles can clog the DPF beyond recovery, requiring expensive replacement of the entire system.

Fuel system problems plague the 6.4L Power Stroke due to its high-pressure common rail injection system operating at pressures exceeding 29,000 PSI. While high pressure allows for precise fuel metering, it also creates stress on system components that many simply can’t handle long-term.
The high-pressure fuel pump is particularly problematic, with many units failing before 100,000 miles and often taking out other expensive fuel system components when they fail catastrophically.
The fuel injectors themselves are another major weakness, with many requiring replacement between 80,000 and 120,000 miles at costs that can exceed $4,000 for a complete set.
The injectors are prone to sticking, which can cause rough running, excessive smoke, and poor fuel economy. When injectors fail, they often dump excessive fuel into cylinders, which can wash oil from cylinder walls and cause severe engine damage.
Cooling system inadequacies represent another fundamental flaw in the 6.4L Power Stroke design. The engine generates enormous amounts of heat, particularly during DPF regeneration cycles, but the cooling system wasn’t adequately designed to handle these thermal loads.
The radiator, while large, often proves insufficient for sustained high-load operation, leading to overheating issues that can cause expensive engine damage.
The EGR (Exhaust Gas Recirculation) cooler is particularly problematic, frequently failing and allowing coolant to enter the combustion chambers, potentially causing catastrophic engine damage. Turbocharger problems are endemic to the 6.4L Power Stroke, largely due to the extreme operating conditions created by the emissions systems.
The engine uses a sequential twin-turbo setup designed to provide strong low-end torque while maintaining high-RPM power, but the complexity of this system creates multiple failure points.
The turbochargers are subjected to extreme temperatures during DPF regeneration cycles, and the variable geometry mechanisms are prone to sticking due to soot buildup. When turbochargers fail, they often send metal debris throughout the intake system, requiring extensive repairs.
EGR system failures represent another major category of problems for the 6.4L Power Stroke. The EGR system recirculates exhaust gases back into the intake to reduce combustion temperatures and lower NOx emissions, but this system introduces soot and contaminants into the intake system that can cause extensive damage.
The EGR valves frequently stick or fail, and the EGR coolers often develop leaks that allow coolant to enter the combustion chambers. Real-world reliability statistics for the 6.4L Power Stroke are sobering. Many engines require major repairs before reaching 100,000 miles, with complete engine replacements not uncommon before 150,000 miles.
The combination of emissions system failures, fuel system problems, and cooling system inadequacies often creates cascading failures that make repair costs exceed the value of the vehicle. Many owners find themselves facing repair estimates of $15,000 or more for engines that are only a few years old.
The maintenance requirements for the 6.4L Power Stroke are extensive and expensive, reflecting the complexity of its emissions systems. Oil changes must be performed more frequently than in other diesel engines due to fuel dilution from DPF regeneration cycles.
The fuel filters require frequent replacement, and the DPF system requires periodic professional cleaning that can cost several hundred dollars. Despite these extensive maintenance requirements, many engines still experience premature failures.
Towing with the 6.4L Power Stroke exacerbates all of its existing problems. The high loads and extended high-temperature operation associated with towing trigger more frequent DPF regeneration cycles, accelerate fuel system wear, and stress the already inadequate cooling system.
Many owners report that their engines developed problems shortly after beginning regular towing operations, suggesting that the engine simply wasn’t designed for the sustained high-load operation that towing requires.
The aftermarket response to the 6.4L Power Stroke’s problems has been to develop solutions that often involve removing or bypassing the emissions systems entirely. While these modifications can improve reliability, they’re illegal for on-road use and can void warranties.
The fact that the aftermarket’s primary focus has been on disabling rather than improving the engine’s systems speaks volumes about the fundamental flaws in the design.
2. Nissan 5.6L VK56 V8 with CVT Transmission
The combination of Nissan’s 5.6L VK56 V8 engine with Continuously Variable Transmission represents one of the most problematic powertrains ever offered in a vehicle marketed for towing applications.
While the engine itself shows promise in terms of power output and refinement, its pairing with Nissan’s CVT technology creates a combination that’s fundamentally unsuited for the sustained high-load operation that towing demands, leading to premature failures and expensive repairs that have left countless owners stranded and financially devastated.
The VK56 V8 engine, taken in isolation, represents competent engineering with aluminum block construction, dual overhead cams, and variable valve timing technology.
The engine produces respectable power and torque figures that, on paper, suggest adequate towing capability. However, the engine’s relatively lightweight construction and emphasis on fuel economy over durability become problematic when subjected to the sustained high-load operation that towing requires.
The aluminum block, while reducing weight, doesn’t provide the thermal stability of iron construction, leading to consistency problems as the engine heats up during extended towing sessions.
The real problems begin with Nissan’s decision to pair this engine with their Xtronic CVT transmission, a choice that defies conventional wisdom about what type of transmission is appropriate for towing applications.
Nissan CVT transmissions are not recommended for towing, and the engineering reasons behind this recommendation become clear when examining how CVT technology functions under high-load conditions.
CVT transmissions work by using a belt or chain running between two variable-diameter pulleys, allowing for infinite gear ratios within their operating range.
While this technology can provide smooth acceleration and optimal fuel economy under light loads, it’s fundamentally unsuited for the high torque loads and sustained operation associated with towing. The belt or chain system must handle all the engine’s torque, creating stress concentrations that traditional gear sets can distribute more effectively.
Heat generation represents the CVT’s most critical weakness in towing applications. The continuous slipping action required for CVT operation generates friction heat that must be dissipated to prevent component failure.
Under normal driving conditions, this heat generation is manageable, but towing heavy loads creates sustained high-torque conditions that generate heat faster than the transmission can dissipate it. This thermal overload leads to rapid degradation of the CVT belt or chain, transmission fluid breakdown, and eventual catastrophic failure.
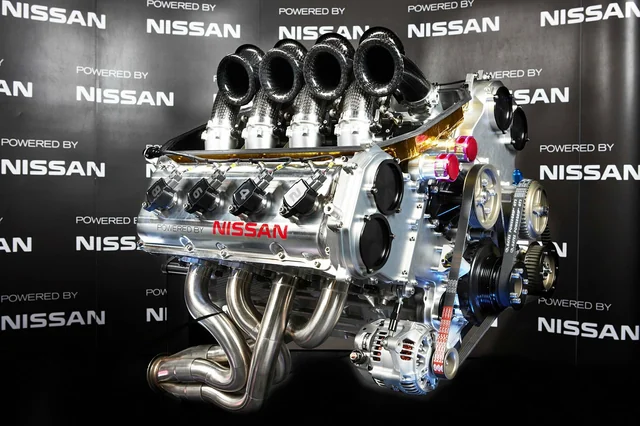
The CVT’s control systems exacerbate the problem by attempting to maintain optimal engine RPM for fuel economy rather than prioritizing component protection. When towing heavy loads, the CVT often tries to keep engine RPM low to maximize fuel efficiency, but this forces the transmission to operate at high slip ratios that generate excessive heat.
Unlike conventional automatics that can lock up their torque converters to eliminate slip, CVTs must maintain some degree of slip to function, making thermal management nearly impossible under sustained high-load conditions.
Real-world failure rates for Nissan CVT transmissions in towing applications are alarming. Many units fail before reaching 60,000 miles when subjected to regular towing, and some experience problems with loads as light as 3,000 pounds.
The failures are often catastrophic, leaving owners stranded and facing repair bills that can exceed $6,000 for transmission replacement. The frequency of these failures has led to multiple class-action lawsuits and forced Nissan to extend warranties on CVT transmissions multiple times.
The symptoms of impending CVT failure are often subtle initially but progress rapidly once problems begin. Owners report experiencing shuddering during acceleration, particularly when attempting to accelerate while towing.
The transmission may slip under load, causing the engine RPM to rise without corresponding acceleration. Strange noises, including whining or grinding sounds, often precede complete failure. Most troubling is that these symptoms can appear suddenly, giving owners little warning before catastrophic failure occurs.
Nissan’s attempts to address CVT reliability problems have been largely unsuccessful. Multiple software updates have been released to modify transmission behavior, but these updates often reduce towing capacity or create new problems. Hardware modifications, including improved cooling systems and stronger belts, have been implemented in newer models, but these changes haven’t eliminated the fundamental incompatibility between CVT technology and towing applications.
The resale value of vehicles equipped with the VK56/CVT combination has been significantly impacted by reliability concerns. Potential buyers are increasingly aware of the transmission problems, leading to reduced demand and lower resale values.
This depreciation represents an additional cost for owners who may already be facing expensive transmission repairs. The combination of high repair costs and poor resale values makes the total cost of ownership for these vehicles particularly high.
3. Ram 1500 EcoDiesel 3.0L V6 (VM Motori)
The Ram 1500 EcoDiesel 3.0L V6 engine represents one of the most disappointing engines in recent automotive history, a powerplant that promised to deliver European-style diesel efficiency in an American pickup truck but instead delivered a litany of problems that have cost owners millions in repairs and left Ram scrambling to maintain its reputation in the competitive truck market.
This Italian-designed engine, manufactured by VM Motori, was intended to provide the fuel economy advantages of diesel technology without the size and weight penalties of larger diesel engines, but the execution was so flawed that it became a cautionary tale about the challenges of adapting foreign engines to American conditions.
The 3.0L EcoDiesel’s problems begin with its fundamental design philosophy, which prioritized fuel economy and emissions compliance over the durability and reliability that American truck buyers expect. The engine features an aluminum block and heads, which reduces weight but creates thermal management challenges that the cooling system struggles to address.
The lightweight construction, while beneficial for fuel economy, simply doesn’t provide the robust foundation necessary for sustained high-load operation that towing requires.
Emissions control systems represent the EcoDiesel’s most significant weakness, with the engine featuring one of the most complex and problematic emissions packages ever installed in a light-duty truck.
The system includes a diesel particulate filter (DPF), selective catalytic reduction (SCR) with diesel exhaust fluid (DEF) injection, and an exhaust gas recirculation (EGR) system that work together to reduce emissions but create multiple failure points that frequently leave owners stranded with expensive repair bills.

The DPF system on the EcoDiesel is particularly problematic, requiring frequent regeneration cycles that can occur every 300-500 miles under normal driving conditions.
These regeneration cycles involve injecting raw fuel into the exhaust system to raise temperatures high enough to burn off accumulated soot, but the process often fails to complete properly, leading to DPF clogging and expensive repairs.
The regeneration process also dilutes the engine oil with fuel, reducing its lubricating properties and potentially causing premature engine wear. DEF system failures plague the EcoDiesel, with the injection system frequently malfunctioning and leaving owners unable to start their vehicles.
The DEF tank, lines, and injection components are prone to freezing in cold weather, crystallization in hot weather, and contamination from poor-quality DEF fluid. When the DEF system fails, the engine management system limits power output and eventually prevents starting, leaving owners stranded until expensive repairs can be completed.
The legal consequences of the EcoDiesel’s problems have been significant, with Ram facing multiple class-action lawsuits and regulatory investigations.
The engine’s emissions systems were found to be inadequate for meeting federal standards, leading to recalls and software updates that often reduced performance while failing to address underlying reliability issues. The legal settlements have cost Ram hundreds of millions of dollars while failing to restore consumer confidence in the engine.
4. Ford 6.7L Power Stroke Diesel V8 (Early Years 2011-2014)
The early years of Ford’s 6.7L Power Stroke diesel engine represent a painful lesson in the challenges of developing clean diesel technology under aggressive timelines and regulatory pressure.
Introduced in 2011 as Ford’s replacement for the disastrous 6.4L Power Stroke, the 6.7L was intended to restore Ford’s reputation in the diesel truck market, but the early versions were plagued by teething problems that left many owners questioning Ford’s commitment to diesel reliability and engineering excellence.
The 6.7L Power Stroke’s problems began with Ford’s decision to develop the engine entirely in-house rather than partnering with an established diesel manufacturer as they had done previously.
While this approach gave Ford complete control over the design and manufacturing process, it also meant they were essentially starting from scratch in developing a modern, clean diesel engine.
The compressed development timeline, driven by competitive pressure and regulatory requirements, meant that many design issues weren’t discovered until the engines were in customer hands.
Turbocharger problems plagued early 6.7L Power Stroke engines, with many units experiencing failures before 100,000 miles. The single variable geometry turbocharger, while simpler than the twin-turbo setup used in the 6.4L, proved to be inadequately robust for the demanding conditions of modern diesel operation.
The variable geometry mechanism was particularly problematic, frequently sticking due to soot buildup and thermal cycling. When the turbocharger failed, it often sent metal debris throughout the intake system, requiring extensive repairs.
The emissions control systems on early 6.7L engines were another major source of problems, though less severe than those experienced with the 6.4L. The diesel particulate filter (DPF) system required frequent regeneration cycles that could occur every 300-500 miles, and incomplete regeneration cycles could clog the DPF beyond recovery.
The selective catalytic reduction (SCR) system with diesel exhaust fluid (DEF) injection was prone to component failures, particularly in cold weather conditions where DEF could freeze and damage system components.
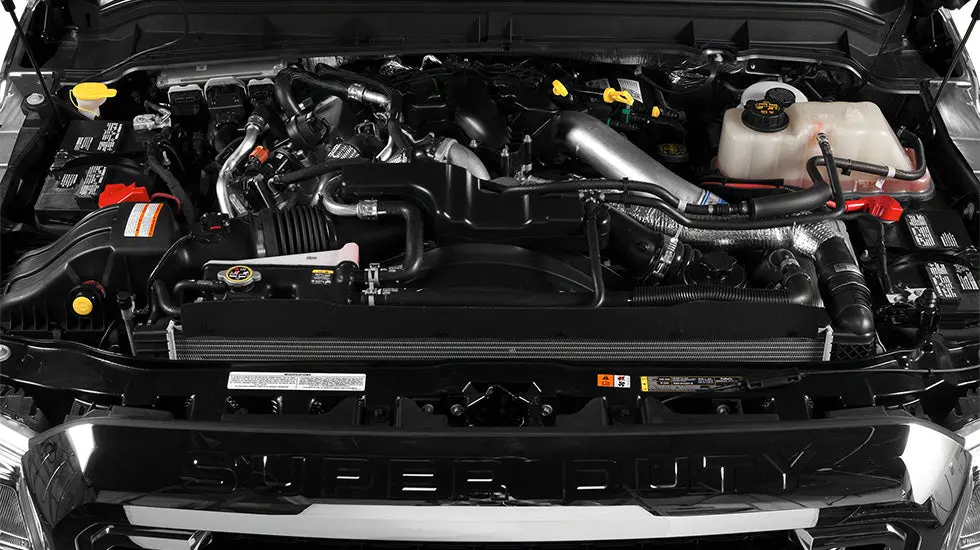
Fuel system issues affected many early 6.7L engines, with the high-pressure fuel pump being a particular weak point. The pump was prone to failure, often taking out other expensive fuel system components when it failed catastrophically.
The fuel injectors were also problematic, with many requiring replacement before 100,000 miles. The fuel system’s sensitivity to fuel quality meant that using lower-grade diesel fuel could accelerate component wear and increase failure rates.
EGR (Exhaust Gas Recirculation) system problems were common on early 6.7L engines, with the EGR valve frequently sticking and the EGR cooler prone to failure.
When the EGR cooler failed, it could allow coolant to enter the combustion chambers, potentially causing catastrophic engine damage. The EGR system also contributed to carbon buildup in the intake system, which could reduce performance and increase maintenance requirements.
Cooling system inadequacies became apparent when early 6.7L engines were subjected to sustained high-load operation, particularly during towing. The cooling system, while adequate for normal operation, struggled to maintain optimal operating temperatures during extended periods of high-load operation.
The radiator design was later improved, but early engines often experienced overheating problems that could cause expensive damage. Ford’s response to the early 6.7L’s problems was more aggressive than their handling of the 6.4L issues, with multiple recalls and service campaigns addressing known problems.
The company updated software calibrations, replaced problematic components under warranty, and made running changes to improve reliability. However, these improvements didn’t address all the fundamental issues, and many early engines continued to experience problems even after multiple service interventions.
5. Chrysler 2.7L V6 Engine
The Chrysler 2.7L V6 engine stands as one of the most problematic engines ever produced by an American manufacturer, a powerplant so fundamentally flawed that it has achieved legendary status among automotive technicians and used car buyers as an engine to avoid at all costs.
While not specifically designed for towing applications, this engine found its way into numerous vehicles that owners attempted to use for light towing, with universally disastrous results that highlight the importance of proper engine design and engineering execution.
The 2.7L V6’s problems begin with its basic architecture, which represents a series of cost-cutting decisions that prioritized manufacturing expenses over long-term reliability. The engine features an aluminum block with iron cylinder liners, a combination that creates thermal expansion issues that plague the engine throughout its service life.
The aluminum block expands and contracts at different rates than the iron liners, creating stress points that can lead to liner movement, coolant leaks, and eventual catastrophic failure.
Perhaps the most infamous problem with the 2.7L V6 is its inadequate cooling system design, which simply cannot handle the heat loads generated by normal operation, let alone the increased thermal stress of towing.
The engine features a single cooling system that must handle both the engine block and cylinder heads, but the coolant passages are too small and the water pump too weak to provide adequate flow. This inadequate cooling leads to hotspots within the engine that cause premature component failure.
The timing chain system on the 2.7L represents another fundamental design flaw that contributes to the engine’s poor reliability. The engine uses a timing chain rather than a belt, which should provide better durability, but the chain tensioning system is inadequate and prone to failure.
When the timing chain stretches or the tensioners fail, the engine can experience timing problems that lead to poor performance, increased emissions, and potential internal damage.

Oil sludge formation is perhaps the most notorious problem associated with the 2.7L V6, with many engines developing thick, tar-like sludge deposits that can completely block oil passages and cause catastrophic engine failure.
This sludge formation is caused by a combination of factors, including inadequate oil circulation, poor crankcase ventilation, and the tendency for the engine to run hot due to cooling system inadequacies. Once sludge formation begins, it accelerates rapidly and can destroy the engine in a matter of thousands of miles.
The oil pump design on the 2.7L is inadequate for the engine’s needs, providing insufficient oil pressure and flow to properly lubricate all components.
The pump is driven by the timing chain, and when chain stretch occurs, oil pump timing can be affected, further reducing oil pressure. The oil pump pickup tube is also prone to cracking, which can cause complete loss of oil pressure and immediate engine destruction.
The resale value of vehicles equipped with the 2.7L V6 has been severely impacted by the engine’s reputation for unreliability. Many potential buyers specifically avoid vehicles with this engine, leading to reduced demand and lower prices.
The combination of high repair costs and poor resale values makes the total cost of ownership for vehicles with the 2.7L V6 particularly high, often exceeding the cost of more reliable alternatives.
Also Read: 5 Toyota Hybrids With Long Lives and 5 That Constantly Glitch