In the rapidly evolving world of automotive engineering, the debate between classic and modern powerplants continues to ignite passionate discussions among enthusiasts, mechanics, and engineers alike.
While contemporary engines boast impressive technological advances with direct injection, variable valve timing, turbocharging, and sophisticated engine management systems, some legendary old-school engines refuse to bow down to their modern counterparts.
These mechanical marvels, born in an era when simplicity and raw engineering prowess ruled supreme, continue to demonstrate their superiority in specific areas that matter most to true automotive enthusiasts.
The automotive landscape has witnessed a fascinating paradox where some vintage engines, despite being decades old, continue to outperform their modern successors in reliability, tunability, and pure character.
These engines were designed with over-engineering in mind, featuring robust internal components, simpler architecture, and a focus on longevity rather than meeting stringent emissions regulations or fuel economy standards.
Their legacy lives on not just in classic car restoration projects, but also in modern engine swaps, racing applications, and performance builds where their proven capabilities shine brightest.
Conversely, certain engines from automotive history serve as stark reminders of engineering missteps, design flaws, and the consequences of rushing products to market without adequate testing.
These powerplants, while perhaps innovative in concept, failed to deliver on their promises and left owners frustrated with poor reliability, expensive maintenance, and subpar performance.
Understanding both sides of this spectrum provides valuable insight into what makes an engine truly great and helps us appreciate the engineering excellence that stands the test of time versus the failures that should remain buried in automotive history.
5 Old-School Engines That Beat Modern Ones
These legendary powerplants represent the pinnacle of mechanical engineering excellence, proving that superior design principles and robust construction methods can outperform modern engines despite lacking contemporary technology features.
The Toyota 2JZ-GTE engine continues to dominate tuning circles decades after production ended, with arguably the best two production engines from Japan, the RB26 and 2JZ are the subject of a fierce rivalry that originated more than three decades ago, while the 1JZ-GTE lives in the shadow of its bigger sibling, the 2JZ-GTE, but in some regards, it may prove to be better.
Both engines share identical, cast-iron block, and the 1JZ can rev, in standard, form to 8,000 RPM something the 2JZ can’t do. The Honda B16A established the foundation for high-revving naturally aspirated performance, with its late 1980s B-Series line legitimized Honda’s bonafides thanks to engines like the B16A3, demonstrating that mechanical precision and intelligent design create lasting performance advantages over complex modern alternatives that prioritize emissions compliance over pure engineering excellence.
1. Chevrolet Small Block 350 (1967-2003)
The Chevrolet Small Block 350 stands as perhaps the most iconic and successful V8 engine in automotive history, representing the pinnacle of American engineering simplicity and effectiveness.
Introduced in 1967, this 5.7-liter pushrod V8 became the backbone of American performance for over three decades, and its influence continues to reverberate through modern engine design and aftermarket culture.
What makes the Small Block 350 superior to many modern engines isn’t just its impressive power output or legendary reliability, but its fundamental design philosophy that prioritized strength, simplicity, and serviceability above all else.
The engine’s architecture is a masterclass in mechanical engineering fundamentals. The cast iron block features a deep-skirt design with four-bolt main caps on performance variants, creating an incredibly rigid foundation that can handle enormous amounts of power without structural failure.
The cylinder heads, whether the legendary L48, L82, or later aluminum variants, feature large, straight ports that flow exceptionally well even in stock form. This design allows for massive airflow potential that modern engines, constrained by emissions regulations and packaging requirements, often cannot match.
The overhead valve configuration with a centrally located camshaft provides excellent valve train geometry and reduces the overall height of the engine, making it ideal for a wide variety of applications.
One of the most compelling advantages of the Small Block 350 over modern engines is its incredible tunability and modification potential. Unlike contemporary engines that rely heavily on complex computer systems and proprietary software, the 350 can be modified with basic mechanical knowledge and traditional tools.
The aftermarket support for this engine is unparalleled, with virtually every component available in multiple performance levels from dozens of manufacturers.

Whether you need forged pistons, performance camshafts, high-flow cylinder heads, or complete rotating assemblies, the options are limitless and relatively affordable compared to modifying modern engines.
From a reliability standpoint, the Small Block 350 demonstrates the advantage of proven, time-tested design over cutting-edge technology. While modern engines achieve impressive power outputs, they often require premium fuel, synthetic oils, and strict maintenance schedules to maintain reliability.
The 350, with its simple pushrod valve train, can run on regular gasoline, conventional oil, and withstand abuse that would destroy a modern engine.
Many examples continue to run strong well beyond 200,000 miles with basic maintenance, something that cannot be said for many contemporary high-performance engines with their complex turbocharging systems and variable valve timing mechanisms.
The manufacturing quality of the Small Block 350, particularly in its golden era from the late 1960s through the 1970s, reflects an approach to engine building that prioritized durability over meeting strict emissions and fuel economy standards.
The castings are thick and robust, the machining tolerances are generous enough to accommodate wear without immediate failure, and the component materials were chosen for longevity rather than weight savings.
This results in an engine that improves with age, developing character and personality that modern engines, with their precise but fragile components, simply cannot replicate.
Performance-wise, the Small Block 350 offers a combination of low-end torque and high-rpm capability that modern engines struggle to match without forced induction.
The long-stroke design inherent in the 350’s architecture produces substantial torque output from idle through mid-range RPM, making it ideal for street driving and practical applications.
Yet with proper modifications, these engines can rev to 7,000 RPM and beyond, producing well over 500 horsepower naturally aspirated. Try achieving similar numbers from a modern naturally aspirated engine without spending significantly more money and dealing with far greater complexity.
2. Toyota 2JZ-GTE (1991-2002)
The Toyota 2JZ-GTE represents the absolute pinnacle of Japanese engineering excellence, combining bulletproof reliability with extraordinary performance potential in a package that continues to embarrass modern turbocharged engines.
This 3.0-liter twin-turbocharged inline-six engine, found in the legendary Toyota Supra and other high-performance Toyota models, has achieved mythical status in the automotive world for its ability to produce enormous power with minimal modifications while maintaining exceptional reliability.
What sets the 2JZ-GTE apart from contemporary engines isn’t just its impressive stock performance, but its incredible over-engineering that allows it to handle power levels that would destroy most modern engines.
Few production engines before or since are capable of the sort of outlandish horsepower the 2JZ-GTE’s good for with so few modifications. The engine’s internal architecture is a testament to Toyota’s commitment to building engines that could withstand far more stress than their factory applications would ever demand.
The closed-deck cast iron block features a deep-skirt design with cross-bolted main caps and incredibly thick cylinder walls that can accommodate significant bore increases without compromising structural integrity. The forged crankshaft and connecting rods were built to withstand power levels far exceeding the engine’s factory output, making it capable of handling 800-1000 horsepower with minimal internal modifications.
The cylinder head design of the 2JZ-GTE showcases Toyota’s advanced understanding of airflow dynamics and combustion chamber optimization. The dual overhead cam configuration with four valves per cylinder provides excellent breathing capabilities, while the relatively conservative cam timing allows for broad power delivery that works equally well for street driving and track use.
The factory sequential twin-turbo system is remarkably sophisticated for its era, using a complex vacuum and boost control system that eliminates turbo lag while providing smooth power delivery across the RPM range.
This system predates many of the electronic turbo management systems found in modern engines, yet delivers comparable performance with greater reliability and simpler maintenance requirements.

One of the most impressive aspects of the 2JZ-GTE compared to modern turbocharged engines is its ability to make substantial power increases with bolt-on modifications alone.
While contemporary engines often require expensive engine management systems, custom tuning, and internal modifications to achieve meaningful power gains, the 2JZ-GTE can produce 500+ horsepower with simple modifications like a larger single turbo, upgraded fuel system, and basic tuning.
The engine’s conservative factory tune and robust internal components provide enormous headroom for power increases that modern engines, already pushed to their limits from the factory, simply cannot match.
The reliability reputation of the 2JZ-GTE is legendary throughout the automotive community, with many examples continuing to run strong well beyond 300,000 miles despite extensive modifications and abuse. This longevity stems from Toyota’s meticulous attention to detail in material selection, manufacturing processes, and design tolerances.
The engine was designed during an era when Japanese manufacturers were competing to build the most durable and reliable engines possible, resulting in components that are significantly over-engineered for their intended application. Modern engines, while technologically advanced, are often designed to meet specific lifespan targets and cost constraints that prevent the same level of over-engineering.
From a tuning and modification perspective, the 2JZ-GTE offers advantages that modern engines cannot match. The engine’s architecture is well-understood by tuners worldwide, with decades of development resulting in proven modification paths and extensive aftermarket support.
Unlike modern engines that require expensive proprietary diagnostic tools and software for tuning, the 2JZ-GTE can be modified using widely available aftermarket engine management systems and traditional tuning methods.
The engine’s robust construction allows for aggressive tuning that would be impossible with modern engines featuring thin cylinder walls, fragile internal components, and strict emissions control requirements.
3. Ford 302 Windsor (1968-1995)
The Ford 302 Windsor V8 engine represents American automotive engineering at its most practical and effective, combining compact dimensions with robust construction and exceptional versatility.
This 5.0-liter pushrod V8 served as Ford’s workhorse engine for nearly three decades, powering everything from economy cars to high-performance Mustangs, and its design philosophy of simplicity and reliability continues to make it superior to many modern engines in specific applications.
The 302 Windsor’s success lies not in cutting-edge technology or maximum power output, but in its fundamental engineering excellence that prioritizes durability, serviceability, and broad powerband characteristics over complexity.
Unlike modern engines filled with sensors and complex electronics, the Windsor can be diagnosed and repaired with basic tools. It also has a strong bottom end and excellent aftermarket support, making it a favourite for hot rodders and classic restorers alike.
The engine’s architecture represents the refined evolution of the small block Ford design, featuring a lightweight yet strong cast iron block with adequate deck thickness for performance applications. The short-deck design allows for a more compact overall package while maintaining excellent rigidity, and the generous main bearing journals provide exceptional crankshaft support for high-performance applications.
What makes the 302 Windsor particularly superior to modern engines is its incredible ease of maintenance and repair. The simple pushrod valve train configuration eliminates the complexity of overhead cam systems, timing chains, and variable valve timing mechanisms that plague contemporary engines.
Valve adjustments, if needed, can be performed with basic tools in a matter of minutes, while timing chain replacement is a straightforward procedure that doesn’t require specialized equipment or extensive engine disassembly. This simplicity translates to lower maintenance costs, reduced downtime, and the ability to perform repairs in virtually any location with basic tools.

The performance characteristics of the 302 Windsor demonstrate the advantages of traditional American V8 design philosophy over modern approaches focused on peak horsepower numbers and fuel economy. The engine’s relatively long stroke and conservative cam timing produce excellent low-end torque that makes it ideal for real-world driving conditions.
Unlike modern engines that require high RPMs to produce meaningful power, the 302 Windsor delivers usable torque from just above idle, making it superior for applications requiring immediate throttle response and low-speed pulling power. This characteristic makes it particularly well-suited for street driving, where the majority of operation occurs below 4,000 RPM.
The manufacturing quality and material selection of the 302 Windsor reflect Ford’s commitment to building engines that could withstand decades of service with minimal maintenance. The cylinder heads, while not as sophisticated as modern designs, feature adequate port size and valve sizing for excellent airflow potential.
The intake manifold mounting system is robust and leak-resistant, unlike many modern engines that suffer from intake manifold gasket failures due to thermal cycling and material incompatibility. The accessory drive system is simple and reliable, using a basic serpentine belt system that can be serviced roadside if necessary.
From a modification standpoint, the 302 Windsor offers unparalleled flexibility and cost-effectiveness compared to modern engines. The extensive aftermarket support includes everything from mild performance upgrades to complete racing assemblies, with parts availability and pricing that make serious performance builds accessible to enthusiasts with modest budgets.
The engine’s robust block casting can accommodate significant bore increases, while the simple valve train allows for aggressive cam profiles that would be impossible with modern engines featuring complex valve timing systems.
Unlike contemporary engines that require expensive computer modifications for performance upgrades, the 302 Windsor can be transformed into a serious performance engine using traditional mechanical modifications and carburetion or simple fuel injection systems.
4. BMW M30 Engine (1968-1995)
The BMW M30 inline-six engine stands as one of the finest examples of European engineering excellence, representing a design philosophy that prioritized smoothness, durability, and driving pleasure over raw power numbers or fuel economy compliance.
This naturally aspirated 2.5 to 3.5-liter engine served as the heart of BMW’s most prestigious models for nearly three decades, including the legendary 5-Series, 6-Series, and 7-Series, as well as the iconic M1 supercar in turbocharged form.
What makes the M30 superior to many modern engines is its combination of sophisticated engineering, exceptional build quality, and character that contemporary engines, constrained by emissions regulations and cost-cutting measures, simply cannot replicate.
The M30’s architecture represents the pinnacle of traditional inline-six design, featuring a cast iron block with exceptional rigidity and thermal stability.
The engine’s long stroke configuration and conservative bore diameter create ideal combustion chamber characteristics for both efficiency and power production, while the deep-skirt block design provides excellent crankshaft support and overall structural integrity.
The cylinder head design showcases BMW’s advanced understanding of airflow dynamics, with carefully shaped intake ports and combustion chambers that promote excellent mixture motion and complete combustion.
This attention to detail results in an engine that produces smooth, linear power delivery across a wide RPM range, characteristics that modern turbocharged engines struggle to match despite their higher peak power outputs.
One of the most compelling advantages of the M30 over contemporary engines is its exceptional refinement and smoothness. The inherent balance of the inline-six configuration, combined with BMW’s meticulous attention to internal component balancing and vibration dampening, creates an engine that runs with silk-like smoothness from idle to redline.
Modern engines, particularly those with turbocharging and direct injection, often exhibit harsh combustion characteristics, vibration, and noise that the M30 simply doesn’t possess.
This refinement extends to the engine’s throttle response, which is immediate and linear thanks to the naturally aspirated design and relatively simple fuel injection system, unlike modern engines that suffer from turbo lag and complex throttle mapping.
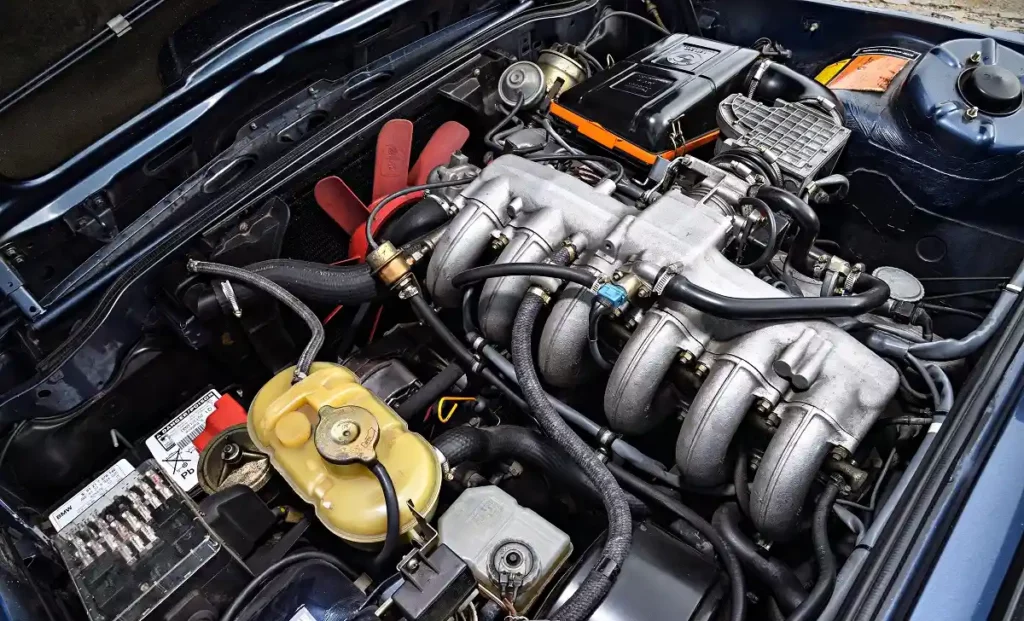
The build quality and materials used in the M30 reflect BMW’s commitment to creating engines that would maintain their performance characteristics for hundreds of thousands of miles. The engine features forged internals in many variants, with connecting rods and crankshafts that are significantly over-engineered for the engine’s power output.
The timing chain system is robust and long-lasting, unlike many modern engines that use timing belts requiring regular replacement or suffer from timing chain stretch issues. The engine’s simple yet effective lubrication system ensures adequate oil supply to all critical components, contributing to the exceptional longevity that M30 engines are known for throughout the BMW community.
From a maintenance perspective, the M30 demonstrates the advantages of traditional engineering over modern complexity. The engine’s straightforward design allows for easy access to all service items, with spark plugs, filters, and fluids readily accessible without requiring extensive disassembly.
The fuel injection system, while sophisticated for its era, uses proven Bosch components that are well-understood by technicians and readily serviceable with standard diagnostic equipment.
Unlike modern engines that require expensive proprietary scan tools and software updates, the M30 can be maintained and repaired using traditional methods and widely available parts, making ownership significantly more affordable over the long term.
The performance characteristics of the M30 showcase the benefits of naturally aspirated design over modern forced induction approaches. While peak power numbers may not match contemporary turbocharged engines, the M30 delivers power in a completely linear and predictable manner that makes it superior for spirited driving and track use.
The engine’s broad torque curve means that power is available across the entire usable RPM range, eliminating the need for constant gear changes to maintain performance.
This characteristic, combined with the engine’s exceptional throttle response and rev-happy nature, creates a driving experience that modern engines, with their electronic throttle control and complex boost management systems, cannot replicate.
Also Read: 5 Engine Swaps That Extend Life and 5 That End It
5. Nissan RB26DETT (1989-2002)
The Nissan RB26DETT represents the absolute pinnacle of Japanese high-performance engine development, combining advanced technology with bulletproof reliability in a package that continues to outperform many modern engines in both power potential and character.
This 2.6-liter twin-turbocharged inline-six engine powered the legendary Nissan Skyline GT-R through its most successful generations, earning a reputation as one of the most capable and tunable engines ever produced.
What sets the RB26DETT apart from contemporary engines is its sophisticated engineering that was decades ahead of its time, combined with the robust construction necessary to handle the extreme demands of high-performance driving and modification.
Arguably the best two production engines from Japan, the RB26 and 2JZ are the subject of a fierce rivalry that originated more than three decades ago, with the RB26DETT representing Nissan’s most advanced engineering capabilities during the height of the Japanese performance car era.
The engine’s architecture showcases several innovative technologies that wouldn’t become commonplace until decades later, including individual throttle bodies for each cylinder, sophisticated turbo management systems, and advanced engine management that could adapt to various driving conditions and fuel qualities.
These features, combined with the engine’s racing-derived internal components, create a powerplant that delivers both exceptional performance and remarkable versatility. The internal construction of the RB26DETT demonstrates Nissan’s commitment to building an engine that could withstand the extreme stresses of professional racing while maintaining reliability in street applications.
The cast iron block features a closed-deck design with exceptional wall thickness and a deep-skirt configuration that provides outstanding rigidity under high boost conditions.
The crankshaft is fully counterweighted and manufactured to incredibly tight tolerances, while the connecting rods are forged steel units that can handle enormous loads without failure. The pistons are designed with generous ring land thickness and robust skirt construction that allows for significant power increases without internal modifications.

One of the most impressive aspects of the RB26DETT compared to modern turbocharged engines is its sophisticated turbo system that eliminates many of the compromises associated with forced induction.
The twin-turbo configuration uses relatively small turbochargers that spool quickly and provide excellent throttle response, while the advanced boost control system prevents the harsh power delivery characteristics that plague many modern single-turbo engines.
The individual throttle bodies create exceptional throttle response and allow for precise air metering to each cylinder, resulting in smooth power delivery and exceptional drivability that modern engines with single throttle bodies cannot match.
The tunability and modification potential of the RB26DETT surpasses that of virtually any modern engine, thanks to its robust construction and well-understood architecture.
The engine can reliably produce 600+ horsepower with basic modifications like larger turbochargers, upgraded fuel system, and engine management tuning, while the strong internal components allow for even more extreme power levels with minimal internal modifications.
Unlike modern engines that are already pushed to their limits from the factory, the RB26DETT was conservatively tuned to meet various market requirements, leaving enormous headroom for performance enhancement that today’s engines simply don’t possess.
The racing heritage and development of the RB26DETT provides it with characteristics that modern engines, designed primarily for emissions compliance and fuel economy, cannot replicate.
The engine was developed with input from Nissan’s racing programs, resulting in features like oil squirters for piston cooling, a robust oiling system capable of handling high-G cornering forces, and thermal management systems designed for sustained high-performance operation.
These racing-derived features make the RB26DETT superior for track use and high-performance applications where modern engines, despite their advanced technology, often struggle with heat management and oiling under extreme conditions.
5 Old-School Engines That Don’t Belong Anymore
These problematic engines represent the worst aspects of older automotive engineering, featuring fundamental design flaws and material choices that create persistent reliability nightmares for owners unfortunate enough to encounter them.
The Chrysler 2.7L V6 stands as one of the most notorious failures in automotive history, with its problems being plentiful, but by far its most significant was sludge buildup due to water pump gaskets that leaked oil into the coolant supply. They were given the reputation of “sludge monsters,” and the engines had no redeeming qualities to overcome it.
The engine’s fundamental water pump design flaw meant that a poorly designed water pump allowed coolant to leak into the crankcase, turning the oil into a gel and blocking oil passages. This could lead to complete engine failure, while many car companies have made bad engines. The Chrysler 2.7 may have been one of the worst engines of all time, with some failing at 40,000 miles.
These engines demonstrate how poor engineering decisions create lasting negative impacts that no amount of maintenance or care can overcome, making them unsuitable for any contemporary application.
1. Chevrolet Vega 2300 (1971-1977)
The Chevrolet Vega 2300 engine stands as one of the most notorious failures in automotive history, representing everything that can go wrong when cost-cutting measures and rushed development take precedence over proper engineering practices.
This 2.3-liter inline-four engine was designed to power General Motors’ answer to the growing import car market, but instead became a cautionary tale about the dangers of unproven technology and inadequate testing.
The Vega engine’s failures were so comprehensive and well-documented that it serves as a perfect example of why certain old-school engines should never be considered superior to modern alternatives, no matter how much nostalgia or historical significance they might possess.
The fundamental design flaws of the Vega 2300 begin with its experimental aluminum block construction, which seemed innovative on paper but proved disastrous in real-world application. General Motors decided to use an aluminum block with iron cylinder liners, a technology that required precise manufacturing tolerances and expansion coefficients that GM’s production capabilities couldn’t consistently achieve.
The aluminum block would expand at different rates than the iron liners during thermal cycling, causing the liners to shift, crack, or even drop into the crankcase. This fundamental design flaw meant that even perfectly maintained Vega engines would eventually suffer catastrophic failure, usually well before 60,000 miles of normal driving.
The cooling system design of the Vega 2300 compounded the block problems by creating hotspots and inadequate coolant circulation that accelerated thermal stress and liner movement.
The engine’s cylinder head design featured inadequate coolant passages and poor thermal management, leading to frequent overheating issues that would damage the aluminum block material and exacerbate the liner problems.
Unlike modern engines that incorporate sophisticated cooling system designs with multiple thermostats, electric fans, and computer-controlled temperature management, the Vega relied on a primitive system that couldn’t cope with the thermal management requirements of the aluminum construction.

The lubrication system of the Vega 2300 represents another area where corner-cutting led to premature failure and poor reliability. The engine featured an inadequate oil pump, insufficient oil capacity, and poor oil circulation to critical wear areas, resulting in rapid wear of internal components even under normal operating conditions.
The camshaft, in particular, was prone to rapid wear due to inadequate lubrication and poor material selection, often requiring replacement before 50,000 miles.
Modern engines, even basic economy designs, feature sophisticated lubrication systems with high-capacity pumps, adequate oil capacity, and careful attention to oil flow patterns that ensure proper lubrication of all critical components.
From a performance perspective, the Vega 2300 failed to deliver competitive power, economy, or drivability compared to the import engines it was designed to compete against.
The engine produced minimal power due to restrictive intake and exhaust systems, conservative cam timing, and poor combustion chamber design, while simultaneously achieving poor fuel economy due to inefficient combustion and excessive internal friction.
The carburetion system was inadequately sized and poorly calibrated, resulting in hesitation, stalling, and poor throttle response that made the engine unpleasant to drive under all conditions.
Modern engines, even entry-level designs, produce significantly more power while achieving better fuel economy and superior drivability through advanced fuel injection, engine management, and combustion chamber design.
The reliability issues of the Vega 2300 extended far beyond the fundamental design flaws to include poor quality control, inadequate materials, and insufficient testing that resulted in multiple failure modes affecting virtually every engine component.
The timing chain system was prone to stretch and failure, the valve train suffered from rapid wear and inadequate adjustment procedures, and the ignition system was plagued by problems that caused poor running and difficult starting.
These issues, combined with the fundamental block problems, created an engine that was essentially unreliable from the day it left the factory, with most examples requiring major repairs or replacement well before they should have reached the end of their useful life.
Modern engines, regardless of their complexity, undergo extensive testing and validation that ensures reliable operation for well over 100,000 miles with proper maintenance.
2. Cadillac V8-6-4 (1981-1982)
The Cadillac V8-6-4 engine represents one of the most ambitious but ultimately disastrous attempts to combine fuel economy with luxury car performance, serving as a perfect example of how premature technology implementation can create an engine that’s inferior to both its predecessors and modern alternatives.
This 6.0-liter V8 engine featured an early form of cylinder deactivation technology that was supposed to seamlessly switch between eight, six, and four-cylinder operation depending on driving conditions, but instead created a complex, unreliable system that pleased no one and frustrated countless owners.
The V8-6-4’s failures demonstrate why certain technological approaches, while conceptually sound, require proper development time and supporting technology to be successful.
The cylinder deactivation system of the V8-6-4 was groundbreaking in concept but catastrophically flawed in execution, relying on primitive computer control systems and mechanical components that weren’t capable of managing the complex switching requirements reliably.
The system used solenoid-controlled rocker arm assemblies that would deactivate specific cylinders by preventing the intake and exhaust valves from opening, while simultaneously shutting off fuel delivery to those cylinders.
However, the crude engine management computer couldn’t accurately determine when to activate or deactivate cylinders, resulting in rough running, hesitation, and poor performance in all operating modes.
The mechanical components were prone to failure, with solenoids sticking, rocker arms jamming, and the entire system requiring frequent, expensive repairs that often exceeded the cost of a complete engine replacement.
The fundamental engine architecture of the V8-6-4, beyond the problematic cylinder deactivation system, suffered from typical early 1980s emissions-era compromises that prioritized compliance over performance or reliability.
The engine featured extremely low compression ratios, restrictive intake and exhaust systems, and primitive fuel injection that resulted in poor power output and throttle response even when functioning properly.
The combustion chamber design was optimized for emissions compliance rather than efficiency or power, creating an engine that produced minimal torque and required excessive throttle input for normal driving.
Unlike modern engines that achieve both excellent emissions compliance and strong performance through advanced combustion management and direct injection technology, the V8-6-4 represented the worst of both worlds.

The reliability issues of the V8-6-4 extended far beyond the cylinder deactivation system to include fundamental problems with the engine’s basic architecture and supporting systems. The early computer control system was primitive and unreliable, prone to failure from heat, vibration, and electrical interference that would cause the engine to run poorly or not at all.
The fuel injection system used early electronic components that weren’t robust enough for automotive applications, resulting in frequent failures of expensive components that were difficult to diagnose and repair. The ignition system relied on early electronic modules that were notoriously unreliable, often leaving drivers stranded with no warning signs of impending failure.
From a performance and drivability perspective, the V8-6-4 failed to deliver the smooth, powerful operation expected from a luxury car engine, instead providing jerky, unpredictable power delivery that made the car unpleasant to drive under all conditions.
The cylinder deactivation system created vibration and noise issues that were transmitted through the drivetrain and into the passenger compartment, destroying the refined driving experience that Cadillac customers expected.
The engine’s poor throttle response and unpredictable power delivery made it unsuitable for highway merging, passing, or any situation requiring immediate acceleration, effectively negating the performance advantages that a V8 engine should provide.
The complexity and cost of maintaining the V8-6-4 system made it economically unviable for most owners, with many choosing to disable the cylinder deactivation system entirely rather than continue paying for expensive repairs.
The specialized diagnostic equipment required to service the system was expensive and not widely available, making proper repairs difficult even for experienced technicians. The electronic components were expensive to replace and often failed repeatedly, creating ongoing maintenance costs that far exceeded the fuel savings the system was supposed to provide.
Modern cylinder deactivation systems, while using similar basic concepts, benefit from decades of development in engine management technology, materials science, and manufacturing processes that make them reliable and transparent to the driver, something the primitive V8-6-4 system could never achieve.
3. Oldsmobile Diesel V8 (1978-1985)
The Oldsmobile Diesel V8 engine represents one of the most spectacular failures in automotive history, demonstrating how a fundamental misunderstanding of diesel engine requirements can create a powerplant so problematic that it damaged an entire manufacturer’s reputation and set back diesel passenger car acceptance in America by decades.
This 5.7-liter V8 diesel engine was General Motors’ attempt to capitalize on the fuel crisis of the late 1970s by offering diesel efficiency in traditional American luxury cars, but instead became a cautionary tale about the dangers of converting gasoline engine designs to diesel operation without proper engineering changes.
The Oldsmobile diesel’s failures were so comprehensive that it serves as a perfect example of why certain old-school engines should be completely avoided in favor of modern alternatives.
The fundamental flaw of the Oldsmobile diesel lay in General Motors’ decision to convert an existing gasoline engine design to diesel operation rather than developing a purpose-built diesel engine from the ground up.
The basic engine block was derived from Oldsmobile’s gasoline V8, which lacked the structural strength necessary to handle the high compression ratios and combustion pressures inherent in diesel operation.
The cylinder heads were inadequately reinforced for diesel service, while the crankshaft, connecting rods, and pistons were not designed to withstand the massive forces generated by diesel combustion.
This fundamental design inadequacy meant that even perfectly maintained engines would eventually suffer catastrophic failures as the basic structure couldn’t cope with the stresses of diesel operation.
The fuel injection system of the Oldsmobile diesel was primitive even by the standards of its era, using a mechanical injection pump that was poorly matched to the engine’s requirements and notorious for inconsistent fuel delivery and premature failure.
The injection pump was expensive to rebuild and required specialized knowledge that most technicians didn’t possess, making proper service difficult and costly. The fuel injection timing was critical for proper operation, but the system provided no easy method for adjustment or verification, resulting in engines that ran poorly due to incorrect timing that was difficult to diagnose and correct.
Modern diesel engines use sophisticated high-pressure common rail injection systems with electronic control that provide precise fuel metering, multiple injection events per cycle, and comprehensive diagnostic capabilities that the primitive Oldsmobile system couldn’t approach.

The cylinder head design of the Oldsmobile diesel created numerous problems that made reliable operation virtually impossible under normal service conditions.
The heads were prone to cracking due to inadequate material thickness and poor thermal management, while the head gaskets couldn’t withstand the combination of high compression ratios and thermal cycling inherent in diesel operation.
The valve train was inadequately designed for the higher loads imposed by diesel combustion, resulting in rapid wear of valve guides, seats, and related components. The precombustion chamber design was inefficient and prone to carbon buildup that would affect performance and eventually require expensive cleaning or replacement procedures that most service facilities couldn’t perform properly.
From a performance perspective, the Oldsmobile diesel failed to deliver the fuel economy benefits that diesel operation should provide, while simultaneously offering poor power output and unacceptable noise and vibration levels.
The engine’s inefficient combustion system and poor fuel injection resulted in fuel economy that was only marginally better than comparable gasoline engines, while producing significantly less power and torque.
The engine was notoriously difficult to start in cold weather, often requiring extended cranking periods or auxiliary starting aids that negated much of the convenience advantage that passenger car engines should provide.
The noise and vibration levels were excessive even by diesel standards, creating an unpleasant driving experience that luxury car buyers found completely unacceptable.
The reliability issues of the Oldsmobile diesel were legendary throughout the automotive industry, with failure rates that were catastrophically high even by the standards of the 1970s and 1980s automotive quality.
The engines were prone to multiple failure modes, including head gasket failure, injection pump problems, timing chain issues, and complete internal destruction that often occurred without warning and well before the engine should have reached the end of its useful life.
The specialized parts and service requirements made repairs expensive and difficult, while the frequent failures meant that many owners faced repeated major repair bills that far exceeded the cost of comparable gasoline engines.
Modern diesel engines, while more complex, benefit from decades of development in materials science, combustion management, and fuel injection technology that make them reliable, efficient, and capable of hundreds of thousands of miles of service with proper maintenance.
4. AMC Pacer 258 I6 (1975-1980)
The AMC Pacer 258 inline-six engine, while not inherently flawed like some other engines on this list, represents the kind of outdated, inefficient powerplant that has no place in modern automotive applications and demonstrates why certain old-school engines should be retired in favor of contemporary alternatives.
This 4.2-liter inline-six engine was designed in the 1960s as a workhorse powerplant for American Motors Corporation’s various models, but by the time it found its way into the innovative Pacer, it had become a relic of earlier automotive thinking that prioritized simplicity over efficiency, performance, or refinement.
The 258’s inclusion in the futuristic Pacer highlighted the engine’s inadequacies and demonstrated how outdated powerplants can undermine even the most innovative vehicle designs.
The fundamental architecture of the AMC 258 inline-six reflects 1960s engineering priorities that are completely at odds with modern automotive requirements, featuring a long-stroke design that prioritizes low-end torque over efficiency or high-RPM performance.
The engine’s primitive combustion chamber design, with its large quench areas and poor mixture motion, results in incomplete combustion that wastes fuel and produces excessive emissions even by the relaxed standards of its era.
The intake and exhaust port design is similarly antiquated, with poor flow characteristics that restrict breathing and limit power output despite the engine’s relatively large displacement.
Modern engines, even basic designs, feature sophisticated combustion chamber geometry, variable valve timing, and optimized port designs that extract significantly more power from smaller displacements while achieving superior fuel economy and emissions compliance.
The fuel delivery system of the 258, whether equipped with a carburetor or the primitive throttle-body fuel injection used in later years, represents technology that was already obsolete when the Pacer was introduced.
The carburetor versions suffered from poor fuel metering, altitude sensitivity, and inconsistent performance that made the cars difficult to drive and maintain.
The later throttle-body injection system was a crude attempt to improve fuel economy and emissions compliance, but lacked the precision and adaptability of modern port fuel injection or direct injection systems that can adjust fuel delivery thousands of times per second based on dozens of sensor inputs.
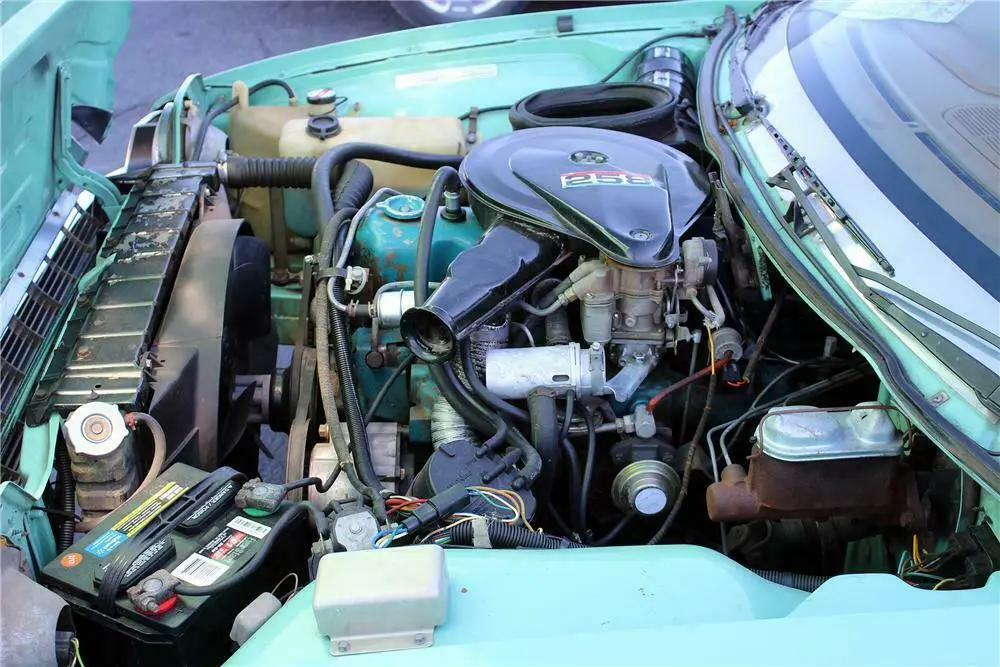
The performance characteristics of the 258 inline-six were inadequate even by the standards of its era, producing minimal power and torque despite its relatively large displacement and heavy weight. The engine’s long-stroke design and primitive valve train limited its rev capability, while the poor breathing characteristics meant that power output dropped off dramatically at higher RPM.
The engine’s response to throttle inputs was sluggish due to the primitive fuel delivery system and heavy rotating assembly, making acceleration feel labored and unresponsive.
Modern engines, even those with significantly smaller displacements, produce substantially more power and torque while weighing considerably less and providing superior throttle response through advanced engine management systems and lightweight internal components.
The fuel economy of the 258 was particularly disappointing, especially considering the relatively modest power output and the innovative aerodynamic design of the Pacer body.
The engine’s inefficient combustion, poor fuel metering, and heavy internal components resulted in fuel consumption that was excessive even by 1970s standards, negating much of the aerodynamic advantage that the Pacer’s design should have provided.
The engine’s inability to take advantage of the car’s low drag coefficient highlighted the importance of powertrain efficiency in achieving good fuel economy, something that modern engines accomplish through direct injection, variable valve timing, cylinder deactivation, and sophisticated combustion management systems.
From a refinement perspective, the 258 inline-six failed to provide the smooth, quiet operation that the Pacer’s innovative design deserved, instead producing excessive noise, vibration, and harshness that detracted from the driving experience.
The engine’s primitive balance shafts and crude mounting system allowed vibrations to be transmitted throughout the vehicle structure, while the inefficient exhaust system produced noise levels that were unacceptable for a car positioned as a technological showcase.
The cooling system was barely adequate for the engine’s heat rejection requirements, often struggling to maintain proper operating temperatures in hot weather or under load conditions.
Modern engines incorporate sophisticated noise and vibration dampening systems, efficient cooling designs, and precise manufacturing tolerances that result in remarkably smooth and quiet operation that the primitive 258 could never achieve.
5. Pontiac Iron Duke 2.5L (1977-1993)
The Pontiac Iron Duke 2.5-liter four-cylinder engine represents the absolute nadir of American automotive engineering during the malaise era, combining poor performance, questionable reliability, and unacceptable refinement in a package that exemplifies everything wrong with cost-cutting approaches to engine design.
This engine, which powered countless GM vehicles for over fifteen years, was designed as a cheap solution to corporate average fuel economy requirements and emissions regulations, but instead became a symbol of American automotive decline and a perfect example of why certain old-school engines should never be considered viable alternatives to modern powerplants.
The Iron Duke’s shortcomings were so comprehensive that it managed to make even the most innovative vehicle designs feel sluggish, crude, and undesirable.
The fundamental architecture of the Iron Duke reflects the worst aspects of 1970s automotive engineering, with a design philosophy that prioritized manufacturing cost over every other consideration including performance, refinement, durability, and fuel economy.
The engine featured an extremely primitive combustion chamber design with poor mixture motion and inefficient burning that resulted in both poor power output and disappointing fuel economy despite the modest displacement.
The intake and exhaust port designs were crude and restrictive, limiting the engine’s breathing capacity and ensuring that power output remained minimal across the entire RPM range.
The valve train used the most basic possible configuration with hydraulic lifters and a simple camshaft design that provided adequate reliability but no performance benefits whatsoever.
The construction quality and materials used in the Iron Duke represented the absolute minimum acceptable for a production engine, with cost-cutting evident in every aspect of the design from the thin cylinder walls to the basic bearing materials.
The engine block casting was adequate but unrefined, with minimal reinforcement and poor thermal management that led to hot spots and uneven thermal expansion. The crankshaft was a basic cast iron unit without counterweights, resulting in poor balance and excessive vibration that was transmitted throughout the vehicle.
The connecting rods were similarly basic, using the minimum material and machining necessary for adequate strength but providing no margin for performance or longevity. These cost-cutting measures resulted in an engine that felt crude and unrefined compared to contemporary engines from other manufacturers, let alone modern powerplants.

From a performance perspective, the Iron Duke was catastrophically inadequate for virtually any application, producing minimal power and torque that made even light vehicles feel sluggish and unresponsive.
The engine’s peak power output was achieved at such low RPM that there was virtually no power available for highway driving or passing situations, while the primitive fuel delivery system provided poor throttle response and inconsistent performance.
The engine’s inability to rev freely meant that drivers had to constantly downshift to maintain adequate performance, negating much of the fuel economy benefit that the small displacement should have provided.
Modern four-cylinder engines, even basic designs, produce significantly more power and torque while achieving better fuel economy through advanced combustion management, direct injection, and turbocharging technologies that the Iron Duke’s primitive design couldn’t accommodate.
The refinement characteristics of the Iron Duke were particularly problematic, with noise, vibration, and harshness levels that were excessive even by the relaxed standards of American automotive manufacturing in the 1970s and 1980s.
The engine’s poor internal balance created vibrations that were transmitted throughout the vehicle structure, while the primitive exhaust system and lack of adequate sound dampening resulted in intrusive noise levels that made highway driving unpleasant.
The engine’s rough idle and poor throttle response created a driving experience that felt agricultural rather than automotive, with hesitation, surging, and inconsistent power delivery that made smooth driving virtually impossible.
The cooling system was barely adequate for the engine’s modest heat rejection requirements, often struggling to maintain proper operating temperatures under load or in hot weather conditions.
The reliability and durability of the Iron Duke, while adequate for basic transportation needs, fell short of the standards expected from automotive powerplants and demonstrated the long-term consequences of excessive cost-cutting in engine design.
The engine was prone to various failure modes, including head gasket problems, timing chain stretch, and premature wear of internal components that required expensive repairs relative to the vehicle’s value.
The primitive fuel delivery system, whether carburetor or early throttle-body injection, was prone to problems that affected drivability and required frequent adjustment and maintenance.
The ignition system used basic components that were adequate but not robust, often requiring replacement of expensive modules and sensors that were difficult to diagnose without specialized equipment.
Modern engines, regardless of their complexity, undergo extensive testing and validation procedures that ensure reliable operation for well over 100,000 miles with proper maintenance, something that the Iron Duke’s rushed development and cost-constrained design couldn’t guarantee.
Also Read: 5 Toyota Hybrids With Long Lives and 5 That Constantly Glitch