Space exploration is currently constrained by a critical factor: the reliance on Earth-based resupply missions. These long-distance supply chains are expensive and unsustainable for extended missions, especially those targeting distant destinations like the Moon and Mars.
To overcome this limitation, space agencies are exploring innovative solutions, such as in situ resource utilization (ISRU) and 3D printing. ISRU aims to extract essential materials like oxygen, water, and metals directly from the local environment, reducing the need for Earth sourced supplies.
This approach could significantly extend the duration of missions and lower the cost of space exploration. For example, on Mars, astronauts could potentially extract water from the planet’s polar ice caps and oxygen from the atmosphere, providing a sustainable source of life support.
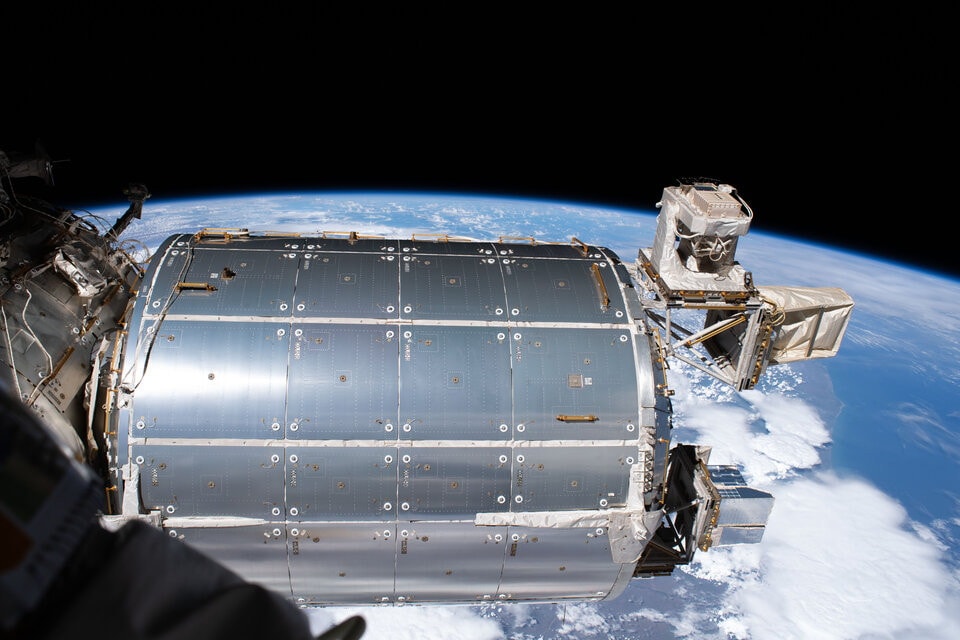
3D printing offers another promising solution. By producing spare parts, tools, and even structures on-demand, 3D printing could reduce the need for carrying large quantities of equipment from Earth. This would not only save space and weight on spacecraft but also enable astronauts to quickly repair or replace damaged components, ensuring mission continuity.
NASA has conducted pioneering 3D printing experiments aboard the International Space Station, demonstrating the feasibility of this technology in the space environment. Recently, the European Space Agency made a significant breakthrough by successfully printing a metal object in space. This achievement marks a major step forward in the development of 3D printing for space applications.
Metal printing could be particularly useful for producing structural components, tools, and other items that require high strength and durability. In-situ resource utilization and 3D printing hold the promise of revolutionizing space exploration by reducing our reliance on Earth-based supplies. By harnessing the resources of the local environment and manufacturing essential items on demand, we can enable longer, more sustainable missions to the Moon, Mars, and beyond.
A groundbreaking achievement in space technology has been marked by the successful operation of the Metal 3D Printer aboard the International Space Station. This monumental feat, achieved by the European Space Agency (ESA), demonstrates the potential of additive manufacturing in extraterrestrial environments. The printer, a massive piece of hardware developed by Airbus, was installed on the ISS earlier this year and has since produced the first-ever metal object printed in space.
This significant milestone represents a major step forward in space exploration, as it opens up new possibilities for on-demand manufacturing and repair in off-world environments. By harnessing the capabilities of 3D printing technology, astronauts and space explorers can now create essential tools, components, and even structures directly on site, reducing the need for costly resupply missions from Earth.
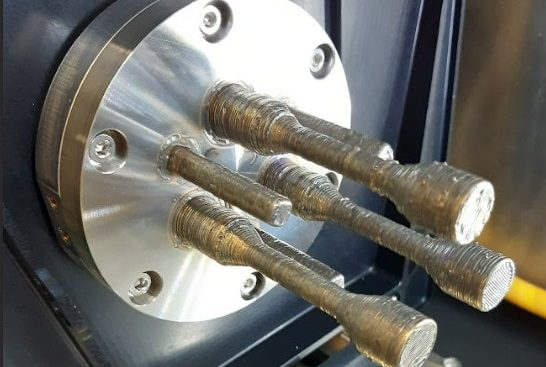
The Metal 3D Printer, a cutting edge piece of equipment capable of producing metal objects from stainless steel wire, operates under challenging conditions within the ISS.
The printer must withstand the extreme temperatures and microgravity environment of space, while also maintaining a controlled atmosphere to prevent oxidation and ensure the safety of the astronauts.
Despite these hurdles, the printer has successfully demonstrated its ability to produce high-quality metal parts, paving the way for future applications in space exploration. The potential benefits of this technology are vast, ranging from the creation of spare parts for spacecraft to the construction of habitats on other planets.