Brakes are one of the most critical safety components on any vehicle, and maintaining them properly is essential for safe driving. For pickup truck owners, brake-pad replacement is a common maintenance task that can either be a straightforward DIY project or a complex procedure requiring specialized tools and knowledge.
While some trucks boast simple, user-friendly brake systems that make replacing pads a relatively easy weekend job, others feature advanced electronic systems or proprietary components that complicate even basic brake service.
Understanding which trucks fall into each category can save owners time, money, and frustration — and help them decide whether they can tackle the job themselves or should seek professional assistance.
Pickup trucks are among the most popular vehicles in the world, especially in markets like North America where ruggedness, towing capacity, and off-road capability are prized. Along with their mechanical robustness, truck owners often prefer to handle maintenance themselves, both to save on labor costs and to have a hands-on understanding of their vehicle.
However, not all trucks are designed equally when it comes to serviceability. Brake-pad replacement, while seemingly straightforward, can vary widely in complexity depending on the truck’s design, age, and incorporated technology.
Traditionally, brake systems on trucks featured mechanical or hydraulic components that were largely standardized across makes and models.
Most used floating calipers with manual pistons that could be compressed with basic hand tools like a C-clamp or brake piston tool. These setups allowed owners with basic mechanical skills and standard toolkits to confidently replace brake pads.
However, in recent years, automakers have incorporated more advanced braking technologies such as electronic parking brakes (EPB), brake-by-wire systems, and integration with vehicle stability and safety modules. These innovations improve safety and performance but introduce new challenges for DIY brake maintenance.
The rise of electronic parking brakes alone has dramatically changed the brake replacement landscape. Unlike older trucks where the parking brake was a simple mechanical cable system, many modern pickups now use electric motors inside the calipers to engage and release the parking brake.
This change means that compressing the brake pistons to replace pads requires specialized electronic tools to retract the calipers without causing damage. Furthermore, these systems often need to be reset or recalibrated using manufacturer-specific diagnostic equipment after maintenance.
Other complications arise from integrated sensor systems that monitor brake pad wear, temperature, and overall brake health. These sensors communicate with the truck’s computer, alerting the driver to brake issues but also requiring resets after new pads are installed.
Additionally, some newer trucks employ torque-to-yield bolts or security fasteners on brake components, necessitating proprietary sockets or drivers. Combine these factors with increasingly compact brake caliper designs and the integration of brake systems with advanced driver-assist technologies, and the once-simple brake-pad replacement becomes a technically demanding job.
This article explores five trucks that are known for having the easiest brake-pad replacement DIY processes, focusing on models with traditional mechanical designs and wide aftermarket support. It also highlights five trucks where brake-pad replacement demands specialty tools, electronic diagnostics, or complex procedures that place the task beyond most DIY mechanics.
Whether you own one of these trucks or are considering purchasing one, understanding the brake maintenance requirements can help you prepare properly, avoid costly mistakes, and ensure your vehicle remains safe and reliable on the road.
Ultimately, the goal is to empower truck owners with the knowledge needed to make informed decisions about their brake maintenance. Whether you prefer rolling up your sleeves and getting your hands dirty or would rather entrust the job to professional technicians equipped with the right tools, knowing which trucks fall into each category saves valuable time and resources.
So, let’s dive into the world of pickup truck brake systems — from the simplest DIY jobs to the most demanding specialty tool requirements — and help you navigate brake-pad replacement with confidence.
ALSO READ: 5 Cars with Quickest Seat-Belt Latches and 5 That Snag
5 Trucks with the Easiest Brake-Pad DIY

1. Toyota Tacoma (Pre-2016 Models)
The Toyota Tacoma has long been celebrated not only for its reliability and off-road prowess but also for its ease of maintenance, especially in older models built before 2016. The brake system in these Tacomas follows a relatively simple mechanical design that is forgiving for DIY enthusiasts of all skill levels.
The front and rear brakes utilize a conventional floating caliper system, meaning the caliper slides on pins and does not require complex hardware or electronics to service the pads. This floating caliper setup allows for quick access to the brake pads without needing to dismantle other suspension or brake components extensively.
In practical terms, replacing brake pads on these Tacomas involves removing the wheel, loosening the caliper bolts, and sliding the caliper off the rotor. The pistons can be compressed back into the caliper bore with a simple C-clamp or a dedicated brake caliper tool.
Unlike modern trucks equipped with electronic parking brakes or integrated sensors, the Tacoma’s straightforward setup means you don’t have to worry about resetting any onboard computer systems or interfacing with the truck’s electronic modules after the job is done.
Furthermore, the physical accessibility of the brake components is a major advantage. The caliper bolts and hardware are typically not rusted or seized, a common issue in trucks that see heavy use in wet or snowy climates.
Toyota’s engineering emphasizes durable yet easy-to-service components, which means DIY mechanics can expect fewer surprises like stuck bolts or frozen clips during the replacement process. This accessibility translates to faster turnaround times and less frustration.
From an aftermarket perspective, Toyota’s huge popularity means that replacement brake pads, caliper hardware kits, and related components are widely available and affordable.
Many suppliers provide complete kits that include everything needed to do a proper brake job, including anti-squeal grease and new hardware clips, which can be installed without specialized knowledge. For those who enjoy learning about vehicle maintenance, the Toyota Tacoma is a perfect entry point that offers both reliability and ease of serviceability.
Lastly, the design philosophy behind the Tacoma emphasizes long-term durability with minimal fuss. Brake pads wear predictably, and the absence of complex systems means that troubleshooting brake noise, vibration, or uneven wear is much easier.
As a result, Tacoma owners often find themselves confident enough to perform routine brake pad replacements at home without hesitation, saving on labor costs and gaining a deeper connection with their vehicle.

2. Ford F-150 (2009-2014 Models)
The Ford F-150 has earned a reputation as the backbone of the American pickup truck segment, and its 2009-2014 generation models are particularly praised for their maintenance-friendly design.
When it comes to brake-pad replacement, these trucks strike a balance between durability and simplicity. The front disc brakes and rear disc or drum brakes utilize familiar caliper and mechanical parking brake setups that make the job approachable for DIYers.
One key aspect that makes brake pad replacement easier on these F-150s is the use of a floating caliper design on the front brakes. The floating caliper slides on pins and can be retracted using common tools like a C-clamp or a dedicated brake piston tool.
This means there’s no need for expensive or specialized tools to service the brake pads. Rear brakes on many of these models use drum brakes or simple mechanical disc brakes with parking brake cables that do not require electronic intervention, further simplifying the replacement process.
The layout of the brake components also plays a critical role. Ford engineers designed these trucks with practical maintenance in mind, resulting in brake calipers and rotors that are easy to access once the wheels are removed.
The caliper mounting bolts are usually straightforward to remove, and the hardware rarely becomes rusted to the point of needing penetrating oil or impact tools. This ease of access reduces the likelihood of needing professional-grade tools or services.
Additionally, the F-150’s huge popularity means that DIY tutorials, videos, and repair manuals are abundant, allowing novice mechanics to confidently tackle brake pad replacements.
Aftermarket support is extensive, with many brake pad kits designed for quick and clean installation. These kits often include anti-rattle clips, grease packets, and instructions that make the process seamless.
Owners of these trucks often report that the brake pad replacement process can be completed within a few hours, even on a first attempt. The combination of a simple caliper design, conventional parking brake setup, and the broad availability of parts and documentation makes the 2009-2014 Ford F-150 a top contender for easy brake-pad DIY.

3. Chevrolet Silverado 1500 (2007-2013 Models)
The Chevrolet Silverado 1500 from 2007 to 2013 is a popular full-size pickup known for its robust build and straightforward mechanical design, especially regarding the braking system.
The brake pad replacement process on these trucks is generally considered approachable for DIY mechanics due to the lack of electronic parking brakes and the use of traditional floating caliper designs.
The floating caliper system employed in these Silverados means the caliper slides on pins and can be compressed using basic hand tools. This eliminates the need for specialized caliper compression tools or electronic reset devices, which are common obstacles in newer trucks.
After removing the wheel and caliper bolts, the caliper can be carefully lifted off, exposing the worn pads. The pistons can be gently compressed back into place with a standard C-clamp or a brake piston tool, allowing room for the new pads.
Another important factor is the straightforward pad retention system. Chevy uses simple hardware clips to hold the brake pads in place, which are easy to remove and reinstall. This reduces the risk of losing parts during the job or needing to source rare replacement clips. Additionally, rotors on these models typically don’t need to be removed unless they are worn or warped, speeding up the overall replacement process.
Physical accessibility also plays a role; the caliper bolts are usually located in easily reachable spots, and the braking components don’t require removal of suspension parts or other complex assemblies to access. This makes the Silverado an ideal choice for weekend mechanics or those working with limited space and tools.
Lastly, the aftermarket ecosystem for Silverado brake components is mature and well-established. Brake pads, rotors, and hardware kits are plentiful and reasonably priced.
Many kits come with everything needed for a complete brake job, including detailed instructions and replacement clips, which reduces the risk of mistakes and improves the overall DIY experience. This combination of straightforward design and strong aftermarket support cements the Silverado’s reputation as a truck with easy brake-pad DIY.

4. Nissan Frontier (2005-2014 Models)
The Nissan Frontier, especially the models from 2005 to 2014, offers a brake system that aligns well with the needs of DIY mechanics. These trucks employ a conventional disc brake setup with floating calipers that make the brake-pad replacement process accessible and manageable, even for those with limited automotive experience.
The floating calipers on the Frontier allow the brake pads to be replaced without removing or adjusting the caliper in complex ways.
After removing the wheel and unbolting the caliper, the piston can be pushed back manually using a C-clamp or a brake piston tool. This simplicity avoids the pitfalls of electronic parking brakes or complicated brake hardware that require more specialized knowledge or equipment.
The design of the brake system favors accessibility, with the caliper bolts and pads positioned so they can be reached easily once the wheel is off. The hardware used to retain the brake pads is minimal and straightforward, making the disassembly and reassembly process smoother. This means fewer parts to juggle and a lower chance of errors during installation.
Nissan’s design philosophy for the Frontier also emphasizes durability, meaning the brake components are built to last and resist corrosion. This durability reduces the likelihood of seized bolts or stuck calipers, which are common challenges in brake jobs on older or heavily used vehicles.
Furthermore, Nissan benefits from a strong aftermarket community, making brake pads, hardware kits, and accessories widely available at reasonable prices. For truck owners who prefer to work on their vehicles themselves, the Frontier represents a practical, user-friendly option for brake pad DIY.

5. Dodge Ram 1500 (2002-2008 Models)
The Dodge Ram 1500 models manufactured between 2002 and 2008 are widely recognized for their straightforward mechanical setup, making brake-pad replacement a manageable task for DIY enthusiasts.
These trucks employ a floating caliper design without the complications of electronic parking brakes, allowing owners to carry out brake maintenance using basic hand tools and some patience.
The calipers on these Rams slide on guide pins and can be compressed using standard tools like a C-clamp or brake piston tool. This means there is no need to purchase specialized equipment or rely on dealer software to reset or recalibrate brake components after replacement. The hardware clips and pad retention systems are simple and designed for easy removal and installation.
Moreover, the caliper bolts and brake hardware are generally accessible once the wheel is removed, allowing the mechanic to work efficiently without removing additional suspension components or other parts. The relative ease of access speeds up the job and reduces frustration, especially for those working in tight or makeshift workspaces.
The Dodge Ram also benefits from robust aftermarket support. Replacement brake pads, rotors, and hardware kits are readily available, often in all-in-one packages that simplify the buying process.
These kits usually come with clear instructions and all necessary hardware, further supporting the DIY community. Additionally, Dodge’s engineering at this time focused on building rugged and reliable trucks that could be easily serviced by their owners.
This approach means fewer surprises and complications during maintenance tasks, contributing to a positive DIY experience. For those looking for a truck with a brake system that invites hands-on care, the 2002-2008 Ram 1500 offers an ideal balance of simplicity, availability, and durability.
5 Trucks Requiring Specialty Tools for Brake-Pad Replacement
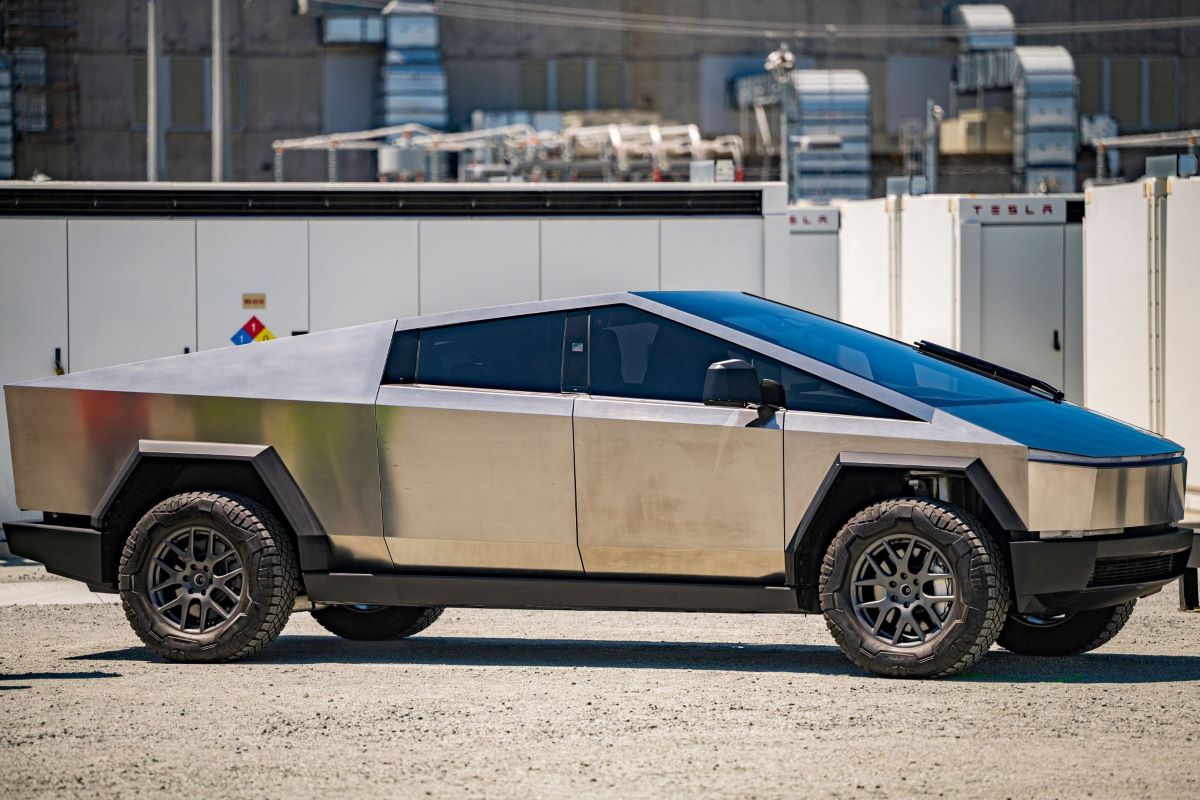
1. Tesla Cybertruck (All Models)
The Tesla Cybertruck, a revolutionary entrant into the pickup market, represents a fundamental shift not just in powertrain technology but also in vehicle maintenance.
Unlike conventional trucks with straightforward hydraulic brake systems, the Cybertruck incorporates an advanced regenerative braking system combined with electronically controlled brake actuators. This complexity requires specialized diagnostic and brake service tools that are far beyond typical mechanical tools used for brake-pad replacement.
One key challenge with the Cybertruck’s brake system is its integrated electronic parking brake (EPB). Unlike manual parking brakes or simple mechanical calipers, the EPB requires specific electronic tools to release the brake caliper pistons safely before removing the brake pads.
This prevents damage to the electronic servos and ensures that the brake system remains calibrated correctly after servicing. Tesla’s proprietary service software and calibrated diagnostic equipment are essential to interface with the vehicle’s onboard computer, reset warning lights, and perform the necessary brake system relearns.
Furthermore, the regenerative braking system changes how brake wear occurs. Since much of the braking force is generated electronically through motor resistance, the mechanical brake pads are used less frequently but require precise replacement to maintain system integrity and safety.
The unique brake system components are tightly integrated with the Cybertruck’s advanced suspension and chassis electronics, demanding that service personnel follow exact procedures verified by Tesla’s diagnostic software.
Physically, the Cybertruck’s brake hardware uses non-standard fasteners and mounting configurations designed to optimize performance and efficiency.
This requires specialized sockets, torque wrenches calibrated to Tesla’s specifications, and possibly even custom brake pad spreaders designed specifically for the Cybertruck’s calipers. Without these, DIYers risk damaging expensive components or triggering unintended system errors.
Finally, Tesla’s commitment to remote diagnostics and over-the-air software updates means that brake service procedures can evolve with software revisions.
This dynamic environment further complicates DIY brake-pad replacement because up-to-date Tesla service tools and software access are necessary to ensure compliance with the latest maintenance protocols. As such, the Tesla Cybertruck demands a professional or highly specialized DIYer equipped with both the right hardware tools and proprietary software.

2. Ford F-150
The newer Ford F-150 models equipped with electronic parking brakes (EPB) significantly complicate what was once a straightforward brake-pad replacement job. While older F-150s allowed easy caliper removal and piston retraction, these modern trucks integrate electronically actuated parking brake calipers that require specialized tools to service properly.
The EPB system uses electric motors inside the caliper to apply and release the parking brake. To replace brake pads, the caliper piston must be retracted electronically, which is not possible with a manual C-clamp or standard brake piston tool.
Instead, a dedicated EPB service tool or scan tool capable of activating the motor is required to safely retract the piston without causing damage to the caliper or the motor.
Moreover, disconnecting and reconnecting the EPB system necessitates careful handling to avoid triggering fault codes or warning lights on the dashboard. After replacement, the system must be reset and recalibrated using Ford’s proprietary diagnostic software to ensure the parking brake functions correctly and safely.
In addition to the electronic challenges, the physical hardware on these F-150 models often features security fasteners or torque-to-yield bolts that require specialized sockets or drivers.
This prevents unauthorized tampering but also complicates DIY repairs. The modern caliper design is more compact and tightly integrated with sensors that monitor pad wear and brake temperature, making physical disassembly more intricate.
Because these newer F-150s incorporate complex brake sensors and safety interlocks, simply swapping brake pads without proper diagnostic tools can lead to persistent brake warnings or degraded system performance.
The required tools typically include an OBD-II scanner with EPB functions, a brake piston retraction tool compatible with electric calipers, and possibly proprietary software access, which are generally beyond the reach of casual DIY mechanics.

3. Ram 1500
The Ram 1500 from 2019 onward introduced significant advances in both suspension and braking systems that complicate brake-pad replacement, especially for DIY enthusiasts. The combination of a 4-corner air suspension system and an electronic parking brake system requires specialized tools and procedures to perform maintenance safely and correctly.
The air suspension system actively adjusts ride height and suspension stiffness, which affects brake component alignment. Before any brake service can be done, the suspension must be placed in service mode using a diagnostic scan tool.
This prevents the suspension from attempting to compensate for the vehicle’s stationary position and allows safe wheel and brake component removal. Without placing the system into service mode, you risk damage to air springs, sensors, or control modules.
The electronic parking brake on the Ram 1500 uses electric motors inside the rear calipers, similar to other modern trucks. Compressing the rear brake caliper pistons requires specialized EPB retraction tools that electronically disengage the parking brake mechanism before brake-pad replacement. A traditional C-clamp will not suffice and could damage the caliper assembly.
Additionally, these trucks often have integrated brake pad wear sensors and brake temperature sensors that communicate with the truck’s onboard computer. After replacement, these sensors must be reset or recalibrated with a scan tool to avoid brake warning lights and ensure the system functions correctly.
Furthermore, the brake caliper bolts and hardware sometimes use proprietary fasteners requiring special sockets or drivers. The complexity of the braking system is compounded by the need to handle air suspension components carefully during disassembly to avoid system faults or damage.
All these factors make brake-pad replacement on a modern Ram 1500 a task that goes well beyond simple mechanical work. It requires access to OEM-level diagnostic tools and knowledge of the electronic brake and suspension systems, placing it out of reach for typical DIYers without investment in the right equipment.

4. Chevrolet Silverado 1500
The 2019 and newer Chevrolet Silverado 1500 models introduce electronic parking brakes and advanced braking technologies that increase the difficulty of performing brake-pad replacements without specialty tools. Unlike older Silverado models with traditional parking brakes, these trucks use electronic actuators integrated into the rear calipers.
To retract the caliper pistons for pad replacement, you cannot simply use manual compression tools. Instead, you need an electronic parking brake (EPB) service tool or a professional-grade OBD-II scanner that can command the electronic motors to release the brake pads. Attempting to use standard mechanical tools risks damaging the actuator motor and the caliper.
Additionally, the truck’s computer system closely monitors brake wear through sensors on each caliper. Once the pads are replaced, these sensors must be reset or recalibrated via the vehicle’s diagnostic port to prevent error codes and dashboard warnings. Without this reset, the vehicle may continue to show brake system faults or limit braking performance.
The physical hardware design also poses challenges. These newer Silverados often have tight caliper mounting bolts secured with torque-to-yield bolts or security fasteners. Removing and reinstalling these components requires specialized sockets, drivers, and torque wrenches calibrated to the manufacturer’s specifications.
Moreover, the electronic parking brake system is integrated with other safety features, including hill hold assist and trailer brake controls. This integration means that brake service must be performed carefully and according to the manufacturer’s protocols to maintain full system functionality and safety compliance.
As a result, the 2019-and-newer Chevrolet Silverado 1500 models push brake-pad replacement tasks into the realm of professional service centers or highly equipped DIYers who have invested in OEM tools and software.
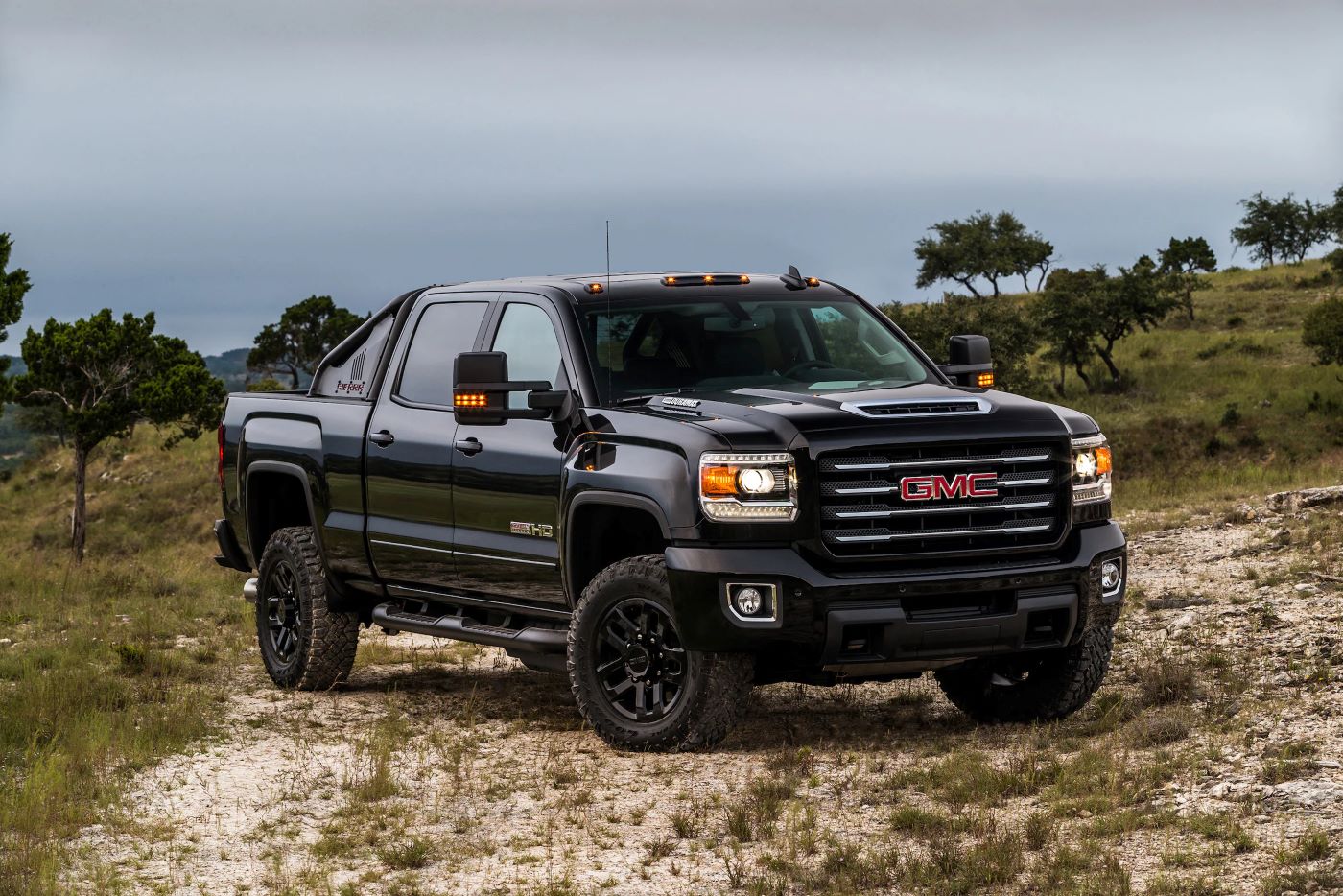
5. GMC Sierra 1500
The GMC Sierra 1500, particularly models from 2020 onward, features advanced brake assist systems that elevate the complexity of brake-pad replacement beyond simple mechanical work. These trucks include electronic parking brakes, integrated brake-by-wire systems, and sophisticated safety sensors requiring specialized tools and procedures for service.
The brake-by-wire technology replaces traditional hydraulic linkages with electronic controls that modulate brake force dynamically. This system demands electronic calibration tools to service, reset, and validate the brake system after pad replacement. Without these tools, the brake assist system may not function correctly, leading to degraded braking performance or safety warnings.
The electronic parking brake system in these models utilizes motors embedded within the rear calipers. Retracting the pistons and releasing the parking brake before pad replacement requires EPB service tools capable of communicating with the truck’s onboard computers. Manual tools simply cannot perform this function without risking damage.
Additionally, the Sierra’s braking system integrates with advanced driver assistance systems (ADAS) like automatic emergency braking, lane-keeping assist, and adaptive cruise control. This interconnectedness means that brake system service may affect other vehicle systems, necessitating specialized scan tools to verify and recalibrate all relevant modules post-maintenance.
The physical fasteners on these trucks often include tamper-resistant bolts requiring proprietary sockets. Torque specifications are precise, and using incorrect tools or methods can lead to component damage or compromised brake performance.
Consequently, the 2020-and-newer GMC Sierra 1500 models are best serviced by professional technicians or highly skilled DIYers with access to OEM diagnostic tools and the latest manufacturer service protocols. These trucks exemplify how modern brake systems have evolved into integrated, software-dependent systems that demand specialized tools and expertise.
ALSO READ: 5 Cars With The Most Free Scheduled Maintenance Miles And 5 With None
Brake-pad replacement is a fundamental aspect of truck maintenance that significantly affects vehicle safety and performance. However, as truck technology evolves, the complexity of this seemingly routine task varies dramatically depending on the make, model, and year of the vehicle.
From traditional hydraulic systems with easily accessible floating calipers to cutting-edge electronic parking brakes and brake-by-wire systems, the spectrum of brake system designs has expanded. Understanding which trucks offer the easiest DIY brake-pad replacement versus those requiring specialty tools is essential for truck owners aiming to maintain their vehicles effectively and economically.
The five trucks featured with the easiest brake-pad DIY procedures — such as the Toyota Tacoma, older Ford F-150s, Chevrolet Silverado 1500 models from the late 2000s, Nissan Frontier, and early Dodge Ram 1500s — represent vehicles with time-tested, user-friendly braking systems.
These trucks typically employ conventional floating calipers, manual parking brake systems, and mechanical hardware that can be serviced with basic tools available to most DIY mechanics. Their design emphasizes straightforward access to caliper bolts and brake pads, standard fasteners, and minimal integration with electronic modules.
The vast aftermarket support for these popular models also means replacement parts are affordable and readily available. For truck owners who enjoy working on their vehicles, these models offer the confidence that brake-pad replacement can be done quickly, safely, and without the need for specialized equipment.
On the other hand, modern trucks like the Tesla Cybertruck, recent Ford F-150s with electronic parking brakes, Ram 1500 models featuring 4-corner air suspension combined with electronic parking brakes, and newer Chevrolet Silverado and GMC Sierra models with advanced brake assist systems showcase the increasing complexity of brake maintenance.
The integration of electronic actuators, sensors, and computer-controlled brake functions means that servicing these brakes is far from simple. Specialty electronic tools, diagnostic software, and proprietary hardware are required to retract calipers, reset sensors, and recalibrate the system properly.
Attempting DIY brake-pad replacement without these tools risks damaging sensitive components, triggering warning lights, or impairing the truck’s safety systems. For owners of these advanced trucks, investing in the right equipment or entrusting the job to trained technicians is the safest and most cost-effective approach.
This divergence in brake maintenance complexity reflects the broader trends in automotive engineering, where safety and technology improvements are accompanied by more intricate servicing requirements.
For truck buyers, this underscores the importance of considering not just the vehicle’s performance and features but also its maintenance demands. Understanding the brake system design before purchasing a truck can influence ownership experience, maintenance costs, and the level of DIY involvement possible.
Moreover, for current truck owners, knowledge of your vehicle’s brake system complexity enables better preparation when it’s time for brake service. Knowing whether your truck allows a straightforward pad replacement or requires specialized electronic tools can help avoid unnecessary trips to the shop or costly mistakes.
It also encourages owners to seek out the appropriate resources, whether that means acquiring specialized tools, consulting manufacturer service manuals, or scheduling professional maintenance.
In conclusion, brake-pad replacement remains a critical, routine maintenance task that varies widely in difficulty across truck models. While some trucks embrace simplicity, offering accessible and affordable DIY brake servicing, others incorporate advanced technology that demands specialized knowledge and tools.
By understanding these differences, truck owners can make informed decisions, maintain optimal vehicle safety, and enjoy a smoother, more confident ownership experience. Whether you prefer hands-on maintenance or rely on professional services, this awareness equips you to navigate brake-pad replacement effectively in today’s evolving truck landscape.