Air conditioning (AC) systems have become an essential comfort feature in modern vehicles, especially trucks, which often face extreme environmental conditions and long hours on the road. For truck owners, a reliable AC system isn’t just a luxury — it’s a necessity.
Whether you’re towing heavy loads through the desert heat, navigating urban traffic on a blistering summer afternoon, or simply commuting in humid weather, having dependable air conditioning can significantly affect comfort, safety, and even the longevity of your vehicle.
Unfortunately, not all truck AC systems are created equal. Some models boast HVAC setups known for their durability and minimal maintenance requirements, while others struggle with recurring issues that leave owners frustrated, uncomfortable, and facing expensive repairs.
The complexity of a truck’s AC system is a major factor influencing its reliability. Modern HVAC systems involve multiple components: compressors, condensers, evaporators, refrigerant lines, sensors, electrical modules, and climate control interfaces. Each of these parts must function harmoniously to deliver cold, clean air efficiently.
In many trucks, especially older or less well-engineered models, weaknesses in any of these components can result in leaks, mechanical failures, electrical glitches, or diminished performance. The environment in which trucks operate—exposure to heat, dust, vibration, and heavy use—adds to the strain, accelerating wear and tear on these critical systems.
Some truck manufacturers have recognized these challenges and invested heavily in designing HVAC systems that prioritize reliability, durability, and ease of maintenance. These trucks often use higher-quality components, improved materials resistant to heat and corrosion, and simpler system designs that reduce the chance of failure.
Furthermore, the integration of smart climate controls and variable displacement compressors in recent models has improved efficiency and longevity, allowing these trucks to maintain comfortable cabin temperatures even under strenuous conditions without frequent breakdowns.
On the other side of the spectrum are trucks plagued by design flaws or subpar component choices that lead to chronic AC problems. Refrigerant leaks due to poor hose or seal quality, compressor failures from inadequate cooling or lubrication, and electrical control module malfunctions are some of the most common complaints.
In many cases, the positioning of HVAC components in tight engine bays or behind dashboards makes repairs labor-intensive and costly, discouraging routine maintenance and exacerbating the issues.
For owners, this results in repeated trips to repair shops, hefty bills, and the constant inconvenience of ineffective cooling, particularly during hot weather when an efficient AC system is most critical.
This article aims to shed light on both ends of this spectrum by highlighting five trucks that are known for their dependable, low-maintenance AC systems, alongside five models notorious for requiring constant AC repairs. Understanding these differences can help current and prospective truck owners make informed decisions based on their climate, usage patterns, and maintenance preferences.
Whether you are in the market for a new truck or evaluating the reliability of your current vehicle, knowing which trucks offer peace of mind with their AC performance—and which tend to be problematic—can save you time, money, and discomfort.
In the sections that follow, we will dive deep into the engineering, design, and real-world owner experiences that differentiate trucks with rock-solid AC systems from those that frequently falter. From Toyota’s rugged and straightforward Tundra to Nissan’s Titan and its troubling HVAC reputation, we’ll explore the nuances behind each truck’s AC reliability or lack thereof.
By highlighting the specific components, maintenance considerations, and common failure points, this comprehensive guide serves as both a technical resource and a practical advisory for anyone who values dependable climate control in their pickup truck.
ALSO READ: 10 Chevrolet and Ford Engines That Lasted Over a Million Miles Without a Rebuild
5 Trucks That Don’t Need AC Repairs

1. Toyota Tundra
The Toyota Tundra is renowned for its legendary durability and ruggedness, and its air conditioning system is no exception. One of the primary reasons why the Tundra’s AC rarely requires repairs lies in Toyota’s engineering philosophy, which emphasizes simplicity and robustness.
Unlike some competitors that integrate complex, electronically controlled HVAC systems with multiple sensors and modules, the Tundra opts for a more straightforward design.
This reduction in complexity significantly decreases the number of potential failure points in the system, making it less likely for leaks, electrical faults, or sensor malfunctions to occur. Moreover, Toyota uses high-grade components sourced from reputable suppliers, ensuring that parts like compressors, condensers, and evaporators maintain performance over extended periods.
Another factor contributing to the Tundra’s AC longevity is the design of its refrigerant circuit. Toyota engineers have optimized the flow and pressure management in the AC system to reduce stress on the compressor and minimize refrigerant leakage—two common causes of system failure in other trucks.
The robust construction of hoses, seals, and fittings also means that the system holds its charge better than many rivals, resulting in fewer top-ups and service visits. Truck owners from hot climates like Arizona, Nevada, and Texas often highlight the Tundra’s ability to maintain ice-cold airflow even after years of heavy-duty usage, towing, and off-roading.
Maintenance also plays a role in the Tundra’s enduring AC reliability. Routine tasks such as replacing the cabin air filter, checking refrigerant levels, and ensuring the condenser remains free of debris are easy to perform thanks to the system’s accessibility under the hood.
This design consideration means owners and technicians can spot potential issues early and address them before they escalate into costly repairs. The long service intervals combined with the truck’s well-thought-out HVAC architecture mean that major components like compressors rarely fail prematurely.
Finally, Toyota’s reputation for building long-lasting vehicles is reflected in the user experience with the Tundra’s AC system. Customer feedback consistently praises the quiet operation and rapid cooling ability of the HVAC setup, even during the hottest summer days.
The absence of complicated climate zones or overly sensitive electronics ensures the system performs reliably and predictably. For those seeking a no-nonsense truck with an air conditioning system that simply works, the Toyota Tundra stands out as one of the best in the market.

2. Ford F-150 (Recent Generations)
Ford’s F-150 has long been the best-selling vehicle in the United States, and with good reason. In recent generations, especially from 2018 onwards, the F-150’s AC system has undergone significant upgrades that have elevated its reliability to new heights.
The previous generation experienced issues with compressor failures and refrigerant leaks, often tied to subpar components and less efficient designs. However, Ford took these lessons seriously and revamped the entire HVAC system in the newer models.
One notable improvement is the use of a more robust compressor unit built with advanced materials that resist heat and pressure wear, key factors that often cause early failures.
Additionally, the introduction of smart climate control technology in recent F-150s has helped reduce unnecessary strain on the AC system. This technology modulates compressor engagement and fan speeds based on cabin temperature and outside conditions, preventing the system from working harder than needed.
By balancing the workload intelligently, the components experience less wear, extending their useful life. The F-150 also incorporates enhanced moisture management features such as improved driers and desiccants, which keep internal parts dry and free of corrosion—a common culprit behind compressor and evaporator failures.
Ease of maintenance further contributes to the F-150’s strong track record. Ford’s engineers designed the HVAC layout with technician accessibility in mind, allowing for straightforward servicing of filters, refrigerant ports, and key components.
This accessibility reduces service costs and downtime, encouraging owners to stay on top of preventative maintenance. In regions with harsh summers, many owners report consistent cold airflow even after heavy towing or off-road use, a testament to the durability of the system’s core components.
Lastly, the F-150’s overall build quality plays a role in the reliability of its AC system. The integration of high-quality seals and connectors ensures minimal refrigerant loss, while the wiring harnesses are protected from heat damage and corrosion.
These seemingly small details add up to a system that can endure long-term abuse without frequent failures. For those who rely on their truck year-round, including in sweltering climates, the F-150 offers one of the best AC systems available in a full-size pickup today.

3. Honda Ridgeline
Although the Honda Ridgeline diverges from the traditional body-on-frame truck design, it punches above its weight in AC reliability, making it a standout for drivers who prioritize comfort and low maintenance. This midsize pickup shares much of its underpinnings with the Honda Pilot SUV, a model well-known for its reliable and efficient climate control system.
By leveraging this proven architecture, the Ridgeline benefits from HVAC components that have been tested extensively in both passenger and utility vehicle environments. This cross-platform synergy ensures that key parts such as the compressor, condenser, and evaporator are not only durable but also designed to be easily serviceable.
A core reason for the Ridgeline’s dependable AC lies in its optimized airflow and cooling efficiency. The HVAC system is engineered to cool the cabin rapidly, distributing air evenly through multiple vents without the need to overwork the compressor.
This efficiency reduces component stress and extends the system’s lifespan. Furthermore, the Ridgeline employs advanced moisture seals and high-quality refrigerant hoses that prevent common issues such as leaks and corrosion.
These design choices make the system resilient against humidity and temperature extremes, whether driving in the sweltering heat of the southern United States or colder northern climates.
Honda’s commitment to quality control is evident in the rigorous testing each Ridgeline undergoes before leaving the factory. The climate control system is subjected to prolonged thermal cycling and durability trials to ensure it can handle years of continuous use without breakdowns.
Owners often report that the AC system remains impressively quiet and free of unusual odors, indicating excellent maintenance of the system’s internal cleanliness and air quality. This attention to detail is a major plus for anyone looking to avoid costly repairs.
Lastly, the Ridgeline’s HVAC system benefits from Honda’s extensive dealer network and user-friendly diagnostics. Should any minor issues arise, technicians can quickly identify and resolve them without lengthy troubleshooting, reducing downtime and repair bills. For a midsize truck that blends utility with comfort and reliability, the Ridgeline’s AC system stands out as an example of Honda’s engineering excellence.

4. Chevrolet Silverado 1500 (Post-2019 Models)
The Chevrolet Silverado 1500 has traditionally been one of the most popular full-size pickups, but earlier models often faced criticism for their HVAC systems, particularly for refrigerant leaks and compressor failures. Recognizing these issues, General Motors undertook a comprehensive redesign of the Silverado’s HVAC components starting with the 2019 model year.
This overhaul included the adoption of a variable-displacement compressor that adjusts cooling capacity based on real-time demand. This not only enhances fuel efficiency but also reduces mechanical wear by preventing the compressor from running at full capacity unnecessarily.
Moreover, GM improved the durability of the condenser and evaporator by using corrosion-resistant materials and better sealing techniques. These upgrades help prevent refrigerant leaks—a frequent cause of costly AC repairs in previous model years.
The system’s refrigerant lines were also redesigned with higher-grade hoses and fittings that withstand the vibrations and heat cycles typical in a full-size truck’s operating environment. Combined, these enhancements significantly boost the reliability and longevity of the Silverado’s AC system.
Owners of the post-2019 Silverado praise how quickly the cabin cools, even on the hottest days, thanks to improved airflow dynamics within the truck’s interior. Chevrolet’s engineers reworked the venting system to deliver more even air distribution, reducing hotspots and ensuring passenger comfort regardless of seating position. Additionally, the system operates quietly, with minimal compressor noise or vibrations—a marked improvement over earlier versions.
Serviceability was another key focus for GM in the redesign. Components like the compressor and condenser are now more accessible under the hood, simplifying routine inspections and maintenance. This design reduces labor time and costs when servicing is needed.
The positive feedback from owners, combined with fewer reported AC failures, underscores how Chevrolet’s investment in HVAC improvements has paid dividends, making the Silverado 1500 a dependable choice for drivers who want hassle-free cooling.

5. Ram 1500 (2019–Present)
The latest generation Ram 1500, introduced in 2019, represents a significant leap forward in both comfort and technology, and its air conditioning system exemplifies these improvements.
Ram engineers focused on durability by incorporating more rugged components capable of withstanding the vibrations and heat associated with truck usage. The compressor, for instance, was redesigned using reinforced internal parts and improved heat shielding to prevent premature failure caused by heat soak—a common issue in earlier models.
In addition to hardware upgrades, Ram optimized the AC system’s refrigerant flow and heat exchange efficiency. The condenser and evaporator are larger and better positioned for airflow, helping the system maintain optimal pressure and temperature levels.
This design innovation reduces compressor cycling frequency, which in turn lowers wear and extends component lifespan. Furthermore, Ram incorporated high-quality seals and advanced moisture traps to prevent refrigerant loss and internal corrosion, two main factors that cause frequent AC repairs in many trucks.
Owners report that the Ram 1500’s AC cools the cabin quickly and maintains a consistent temperature even during heavy towing or extended idling in hot conditions.
The system is also noted for being exceptionally quiet, with smooth compressor engagement and minimal vibration transmitted into the cabin. These qualities reflect Ram’s commitment to delivering a premium ownership experience without sacrificing reliability.
Maintenance considerations were also improved, with easy access to critical AC components enabling quicker diagnostics and repairs if necessary. Ram’s onboard diagnostics system assists technicians in pinpointing issues early, helping to prevent major failures before they happen.
Overall, the Ram 1500’s AC system has become one of the most dependable in the full-size truck segment, giving owners peace of mind when the temperatures climb.
5 Trucks That Constantly Do Need AC Repairs

1. Nissan Titan
The Nissan Titan, while often praised for its powerful engine and spacious interior, unfortunately struggles with chronic air conditioning issues that frustrate many owners. One of the core problems stems from its HVAC system’s design, which includes a complex arrangement of hoses and fittings prone to refrigerant leaks.
The Titan’s AC compressor, a critical component responsible for pressurizing and circulating refrigerant, has been known to fail prematurely in several model years, especially in early 2010s versions.
Owners often report symptoms like weak airflow, warm air blowing, or a noticeable drop in cooling efficiency after just a few years of use. These issues often result from refrigerant loss due to leaks at connection points and deteriorating seals, which are notoriously difficult and costly to repair.
A significant contributing factor to the Titan’s frequent AC failures is the system’s sensitivity to heat and vibration. The truck’s body-on-frame design and relatively stiff suspension mean the HVAC components are exposed to significant physical stress during daily use, particularly when towing or driving on rough terrain.
This stress can cause rubber seals and hoses to crack or loosen, allowing refrigerant to escape. Moreover, the Titan’s condenser is sometimes criticized for its placement, where debris and dirt buildup can obstruct airflow, reducing cooling capacity and placing additional strain on the compressor. This increased workload accelerates wear and often leads to early system breakdowns.
Nissan’s warranty and repair data also reflect the Titan’s reputation for AC unreliability. Numerous recalls and technical service bulletins have been issued over the years addressing refrigerant leaks and compressor failures.
Repair shops frequently report that many of these issues are related to design flaws rather than isolated defects, making AC problems almost inevitable on older Titan models.
The costs of repairs can be high, particularly if the evaporator core or compressor needs replacement, which often requires labor-intensive dashboard removal. These expenses add up quickly and make the Titan one of the more costly trucks to maintain when it comes to air conditioning.
Finally, owner experiences highlight the frustration that comes with the Titan’s AC system. Many describe the need for repeated repairs or refrigerant refills to keep the system functional, leading to dissatisfaction despite the truck’s other strengths.
In hot climates, this unreliability can be a serious drawback, diminishing driver comfort and safety. While Nissan has made improvements in newer models, the legacy of persistent AC issues continues to shadow the Titan’s otherwise solid reputation in the full-size truck market.

2. Chevrolet Colorado (Early Models)
The Chevrolet Colorado, especially first- and second-generation models from the mid-2000s through the early 2010s, is notorious for its troublesome air conditioning systems. One of the biggest issues lies in the system’s evaporator core, which is prone to premature failure and refrigerant leaks.
The evaporator, located deep inside the dashboard, can develop cracks or corrosion that are difficult and expensive to access and repair. Many Colorado owners report that after just a few years, the AC stops blowing cold air, often requiring a full HVAC teardown to replace the evaporator—a costly and labor-intensive procedure.
Adding to the Colorado’s AC woes is the subpar quality of some system components. Compressors and condensers used in earlier models have been criticized for their susceptibility to overheating and mechanical failure. The condenser’s position behind the grille exposes it to damage from road debris, which can lead to punctures or reduced airflow.
This, in turn, causes the compressor to work harder, increasing the likelihood of premature breakdown. Frequent compressor cycling is another problem that wears down system parts faster than usual, leading to a vicious cycle of repairs.
The Colorado’s HVAC system design also suffers from inadequate moisture management. Moisture buildup inside the system often leads to corrosion and electrical component failures, compounding problems with refrigerant leaks.
The cabin air filters in these trucks sometimes become clogged quickly, reducing airflow and forcing the system to work harder to cool the cabin. This combination of issues means that many Colorado owners find themselves making frequent trips to the mechanic for AC recharges, leak repairs, or component replacements.
Finally, owner forums and repair shops consistently report a high incidence of AC problems on earlier Colorado models. The cost and difficulty of repairs, especially those involving evaporator replacement, can be a major deterrent for buyers considering used Colorados.
Although newer generations have addressed many of these issues with better components and design improvements, the legacy of early model AC failures still influences buyer perception and resale values.
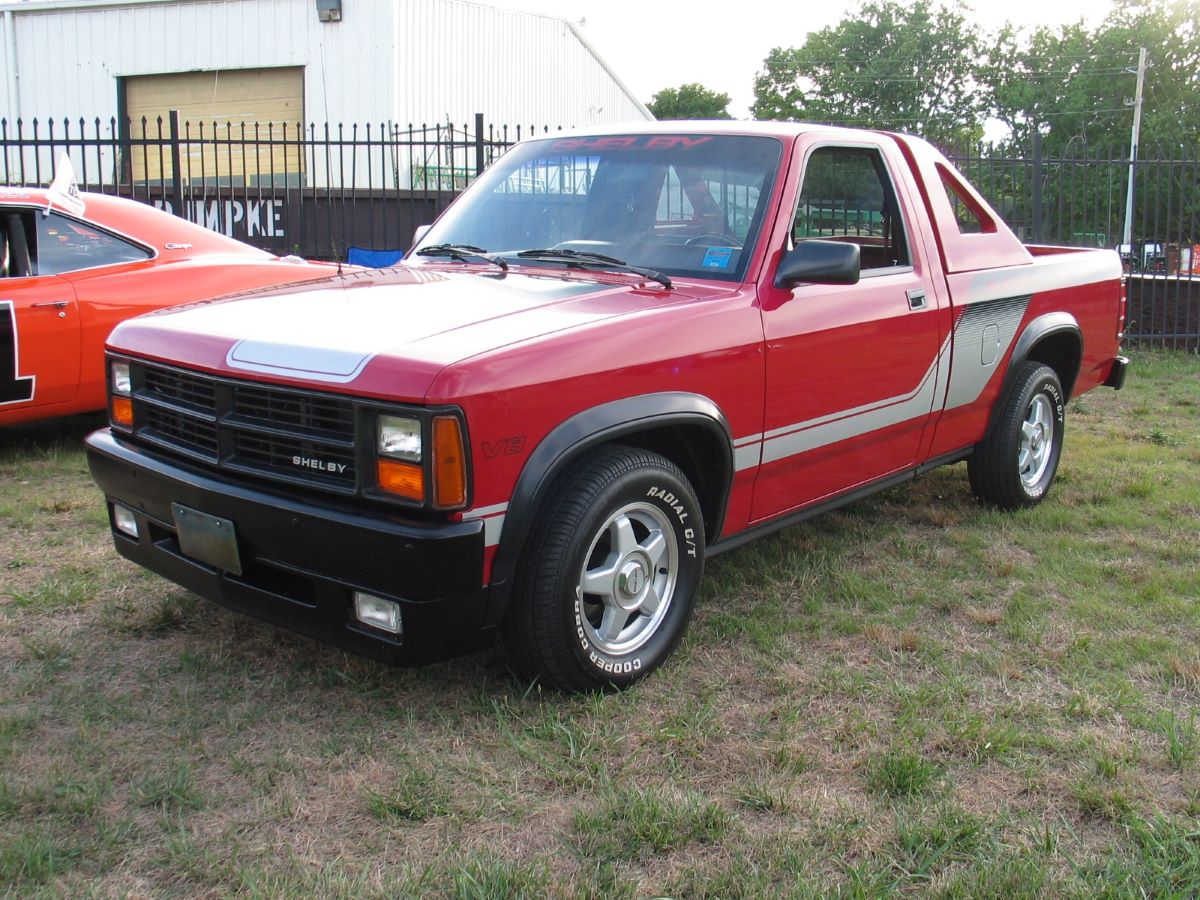
3. Dodge Dakota
The Dodge Dakota, especially models produced in the late 1990s through the early 2000s, has earned a reputation for having a fragile and failure-prone AC system. One of the main culprits is the AC compressor, which frequently seizes or leaks refrigerant due to substandard internal components and poor lubrication.
The Dakota’s compressor design did not adequately address heat dissipation or wear resistance, resulting in many trucks requiring compressor replacements well before the expected service life. This is especially true in hot climates, where the system is under constant strain and failure rates skyrocket.
The HVAC system’s plumbing layout in the Dakota also contributes to its air conditioning problems. Many hoses and fittings are routed through tight engine bay spaces where heat exposure and vibrations accelerate wear and cracking.
These leaks not only cause a loss of refrigerant but also introduce moisture and air into the system, which damages other components such as the evaporator and expansion valve. Furthermore, the evaporator’s placement within the dashboard makes it difficult to service, and replacement often involves extensive disassembly that adds to repair costs.
Electrical issues also plague the Dakota’s AC system, with frequent failures of switches, relays, and control modules. These components can malfunction due to moisture ingress or general wear, causing intermittent cooling or complete system shutdowns.
Diagnosing these electrical gremlins often requires specialized knowledge, meaning many Dakota owners face frustration and escalating repair bills. The combination of mechanical, plumbing, and electrical failures makes the Dakota one of the trucks with the most unreliable AC systems in its era.
Finally, the owner community for the Dakota frequently discusses the challenges of keeping the AC operational, with many opting for aftermarket repairs or system overhauls.
While the truck itself is lauded for its overall ruggedness and performance, the AC system often detracts from the driving experience, especially in summer months. This persistent issue has made the Dakota a cautionary example for buyers prioritizing HVAC reliability in a mid-size pickup.

4. GMC Canyon (Early Models)
The early-generation GMC Canyon shares many mechanical and HVAC system traits with its sibling, the Chevrolet Colorado, and unfortunately, it has inherited many of the same AC reliability problems. Owners of first-generation Canyons frequently report refrigerant leaks and compressor failures within the first 5 to 7 years of ownership.
The system’s evaporator core is particularly problematic, often developing leaks due to corrosion and manufacturing defects. Repairing this requires significant labor as the evaporator sits deep inside the dash, making it one of the most expensive HVAC fixes in the truck segment.
Another notable issue with the Canyon’s AC system involves the condenser and associated pressure switches. The condenser’s location makes it susceptible to damage from rocks and road debris, which can puncture the unit or block airflow. This results in higher operating pressures within the system, forcing the compressor to work overtime and eventually fail.
The pressure switches, which regulate compressor cycling, are also prone to malfunction due to heat exposure and vibration, leading to erratic AC performance or system shutdowns.
Additionally, the Canyon suffers from moisture buildup inside the HVAC system. This moisture can freeze or cause corrosion, damaging internal components like the expansion valve and blower motor.
The result is often poor airflow and weak cooling, symptoms that frequently prompt expensive diagnostics and repairs. The cabin air filter, which is essential for maintaining airflow and protecting the system, sometimes clogs quickly and contributes to these problems.
Mechanics who specialize in GMC Canyons report a steady stream of AC repairs related to these chronic issues. While newer models have improved component quality and design, the legacy of early-generation HVAC failures impacts owner satisfaction and repair costs. For buyers considering a used Canyon, awareness of these common AC problems is critical to avoid unexpected expenses and discomfort.

5. Ford Ranger (Early 2000s Models)
The early 2000s Ford Ranger, a popular compact pickup, is well-regarded for its reliability in many areas but is often singled out for frequent air conditioning troubles. One of the biggest problems is the AC compressor, which has a high failure rate due to bearing wear and internal seal degradation.
These failures often occur prematurely compared to other trucks in its class, resulting in expensive compressor replacements that require significant labor.
The Ranger’s HVAC system design also contributes to refrigerant leaks and performance issues. Hoses and O-rings are prone to drying out and cracking under engine heat, leading to loss of refrigerant and reduced cooling efficiency.
The placement of the evaporator makes leak detection and repairs difficult and time-consuming, adding to repair costs. Owners report recurring issues with the expansion valve as well, which can get clogged or stuck, causing inconsistent cooling or system shutdown.
Electrical problems further complicate the Ranger’s AC reliability. Faulty pressure switches and control relays are common, often causing the compressor clutch not to engage or disengage prematurely.
These intermittent electrical faults are notoriously difficult to diagnose, frequently resulting in multiple repair attempts. Moisture buildup and corrosion inside the HVAC system exacerbate these issues, often causing additional damage to sensors and wiring harnesses.
Owner feedback underscores the frustration with the Ranger’s AC system, especially during hot summer months when reliable cooling is essential. Many have resorted to aftermarket fixes or system upgrades to improve longevity. While the Ranger remains a solid performer in other respects, its frequent air conditioning failures continue to be a significant drawback for many users.
ALSO READ: 5 Pickups With the Best Factory Running Boards and 5 Needing Aftermarket
In summary, the reliability of a truck’s air conditioning system is a critical factor that significantly affects the overall ownership experience, especially in regions with extreme heat or prolonged usage.
As we’ve explored in this article, some trucks stand out for their durable, well-engineered HVAC systems that rarely require repairs, while others struggle with persistent AC problems that can lead to costly and inconvenient fixes. Recognizing these differences can empower truck owners to better manage maintenance, make informed buying decisions, and avoid the frustrations associated with unreliable climate control.
Trucks like the Toyota Tundra, Ford F-150 (recent generations), Honda Ridgeline, Chevrolet Silverado 1500 (post-2019 models), and Ram 1500 (2019–present) exemplify what thoughtful design, quality components, and efficient system management can achieve.
These vehicles benefit from simpler but robust AC system architectures, superior materials, and smarter climate control technologies that reduce wear and tear on critical components.
Owners of these trucks often report long intervals between AC maintenance and enjoy consistent cooling performance even under demanding conditions such as heavy towing, off-road use, or extreme summer temperatures. The ease of servicing these systems and proactive manufacturer support also contribute to their strong reputations for HVAC reliability.
Conversely, trucks such as the Nissan Titan, early Chevrolet Colorado, Dodge Dakota, early GMC Canyon, and early 2000s Ford Ranger highlight the challenges that arise from design shortcomings, inferior parts, or complicated system layouts.
These vehicles frequently experience refrigerant leaks, compressor failures, electrical glitches, and other issues that make maintaining effective air conditioning a constant battle.
The placement of key HVAC components in hard-to-reach locations, combined with sensitivity to heat and vibration, exacerbates these problems and drives up repair costs. Owners often find themselves spending more on repairs or resorting to aftermarket solutions to keep their AC systems functional, reducing overall satisfaction and comfort during hot weather.
This contrast underscores the importance of understanding not just the make and model of a truck but also the specific engineering choices behind its HVAC system. A truck’s AC reliability hinges on factors such as component quality, system design simplicity, moisture management, and ease of access for maintenance.
Additionally, advances in climate control technology, such as variable displacement compressors and intelligent temperature regulation, have contributed to improved durability in many newer trucks. Prospective buyers and current owners who prioritize dependable air conditioning should weigh these factors carefully when selecting or evaluating their vehicles.
Moreover, routine maintenance cannot be overstated in preserving the longevity of any truck’s AC system. Even the most well-designed systems require regular checks, timely refrigerant top-ups, filter changes, and component inspections to perform at their best.
Neglecting these tasks can accelerate system deterioration regardless of build quality, leading to preventable failures and discomfort. Therefore, combining thoughtful vehicle choice with proactive maintenance is the best strategy to ensure reliable, refreshing air conditioning year after year.
Ultimately, the trucks that don’t need frequent AC repairs provide peace of mind, enhanced comfort, and often lower total ownership costs, making them attractive options for anyone living or working in warm climates.
Meanwhile, trucks with known AC challenges demand greater attention, readiness for repairs, and potentially higher costs. Being informed about these differences helps truck owners set realistic expectations and plan accordingly.
Whether you seek a tough, dependable workhorse with a rock-solid AC system or are willing to accept more maintenance for other attributes, understanding your truck’s HVAC strengths and weaknesses is invaluable. By prioritizing models known for their AC durability or taking extra care with maintenance in less reliable trucks, you can enjoy the ride no matter how hot it gets outside.