Pickup trucks hold a unique place in automotive culture. They are symbols of strength, reliability, and functionality—vehicles engineered not just to get people from point A to point B, but to haul, tow, endure, and conquer.
From rural farms to industrial job sites, from off-road trails to suburban driveways, the pickup truck has transcended its utilitarian roots to become both a workhorse and a lifestyle statement.
Yet beneath all the chrome, horsepower, and clever marketing lies the true heart of a pickup: its frame. The frame is more than a foundation—it is the structural spine that determines everything from durability and safety to handling and longevity. In many ways, a truck’s reputation lives or dies by the integrity of its frame.
While manufacturers often highlight engine power, towing capacity, and interior tech, the strength and resilience of a truck’s frame are often overlooked in the spec sheet. But for those who depend on their vehicles for heavy-duty use, the quality of the frame is the defining factor.
It dictates how well a truck can handle weight, absorb stress, resist twisting over uneven terrain, and survive years—or decades—of punishing use. A well-designed frame translates to stability, safety, and confidence. Conversely, a flawed or under-engineered frame can turn a promising truck into a dangerous liability, prone to rust, cracks, flexing, and even catastrophic failure.
This article dives deep into that critical component, highlighting 5 pickup trucks known for their legendary frame strength, and contrasting them with 5 trucks whose frames suffered from serious structural failures.
We’re not just exploring frame design from a theoretical or engineering standpoint—we’re looking at real-world results: how these trucks have performed over time, what owners and mechanics have experienced, and how design choices made by automakers played out in the long run.
We’ll explore boxed frames vs. C-channel designs, the impact of materials and rustproofing, and how structural engineering can elevate—or destroy—a truck’s legacy.
On the positive side, some trucks have become nearly mythic in their frame resilience. These are vehicles that still operate decades later, sometimes with half a million miles on the odometer, and still maintain their structural integrity. They’ve carried heavy loads, traversed brutal terrain, and been put through torture tests few vehicles could survive.
Their frames haven’t just endured—they’ve become the foundation of entire enthusiast communities and restoration subcultures. These are the trucks that people keep running not just because of nostalgia, but because their bones are still strong.
In contrast, some pickups—despite stylish exteriors and capable engines—suffered fatal flaws beneath the surface. Structural issues such as premature rusting, poor welds, frame flexing, and weak cross members plagued certain models and years, leading to recalls, buybacks, and bitter reputational damage.
For every legend, there’s a cautionary tale—a reminder that strength on paper doesn’t always translate to strength on the road. Some trucks that looked impressive on the showroom floor quickly began to show their weaknesses under real stress, particularly in harsh climates or when pushed beyond basic use.
This is not an attack on any brand or an attempt to pick favorites; rather, it’s a candid exploration of structural engineering—what worked, what didn’t, and what lessons have been learned along the way.
The frame doesn’t always make headlines, but it should. It is the difference between a truck that gets passed down through generations and one that ends up in the scrap yard far too soon.
Frame strength determines whether your truck can survive 300,000 miles of towing and off-roading, or if it will buckle under rust and fatigue by year ten.
So, whether you’re an off-road enthusiast, a heavy hauler, a loyal brand devotee, or someone shopping for a used truck, this article will help you understand the structural soul of these machines.
We’ll walk you through the five most respected frames in pickup history—trucks that built a name on their bones—and follow that with five examples where engineering missed the mark, leaving otherwise capable vehicles hampered by one unforgivable flaw: a weak frame.
Also Read: Top 10 EV Features That Come in Useful in Daily Commute
5 Pickup Trucks With Legendary Frame Strength

1. 1995–2004 Toyota Tacoma (First Generation)
The first-generation Toyota Tacoma, introduced in 1995 and continuing through 2004, marked a significant step forward in the midsize truck market, especially in terms of frame strength and build quality.
Designed as a replacement for the long-running Toyota Pickup (also known as the Hilux in international markets), the Tacoma was engineered with a specific focus on the North American consumer while retaining the toughness that made its predecessor world-famous.
At its core was a highly durable frame structure that set it apart from competitors in the compact and midsize segments. Toyota used thicker-gauge steel in the frame rails and reinforced key stress points, giving the truck the capability to handle heavy payloads and abusive terrain without twisting or cracking—an issue that plagued many domestic small trucks of the era.
Unlike many pickups of its size, the Tacoma utilized a fully boxed front frame section, transitioning into a C-channel design in the rear. This hybrid approach balanced strength and weight, helping the Tacoma remain nimble off-road while ensuring rigidity where it mattered most—under the engine and front suspension.
Off-road enthusiasts gravitated toward the Tacoma for this reason, often modifying it for use in rock crawling, overlanding, and Baja-style desert racing.
The frame tolerated the additional weight of steel bumpers, winches, skid plates, and aftermarket suspension components without losing structural integrity. Stories of Tacomas surviving rollover accidents or hauling far beyond their rated capacity are not uncommon, lending to the truck’s legendary status.
In longevity terms, the first-gen Tacoma continues to impress. It’s not unusual to find these trucks with 250,000 or even 400,000 miles still running reliably with minimal frame-related issues—provided they were maintained properly and not exposed to excessive road salt without rust protection.
In dry climates especially, these trucks are almost indestructible. Even in cases where the body panels show signs of age and wear, the underlying frame remains solid, a testament to Toyota’s overengineering philosophy during this period. The reputation earned by this generation helped solidify Toyota’s foothold in the American truck market, carving out a loyal fanbase that persists to this day.
Moreover, the first-gen Tacoma influenced Toyota’s approach to future truck designs. Lessons learned from its performance in both urban and extreme environments were carried forward into the second and third generations, although later models would face different structural challenges.
Nevertheless, the 1995–2004 Tacoma represents a golden era of Toyota toughness—a truck whose frame was built not only to meet expectations but to exceed them over and over again, even decades after it rolled off the factory floor.
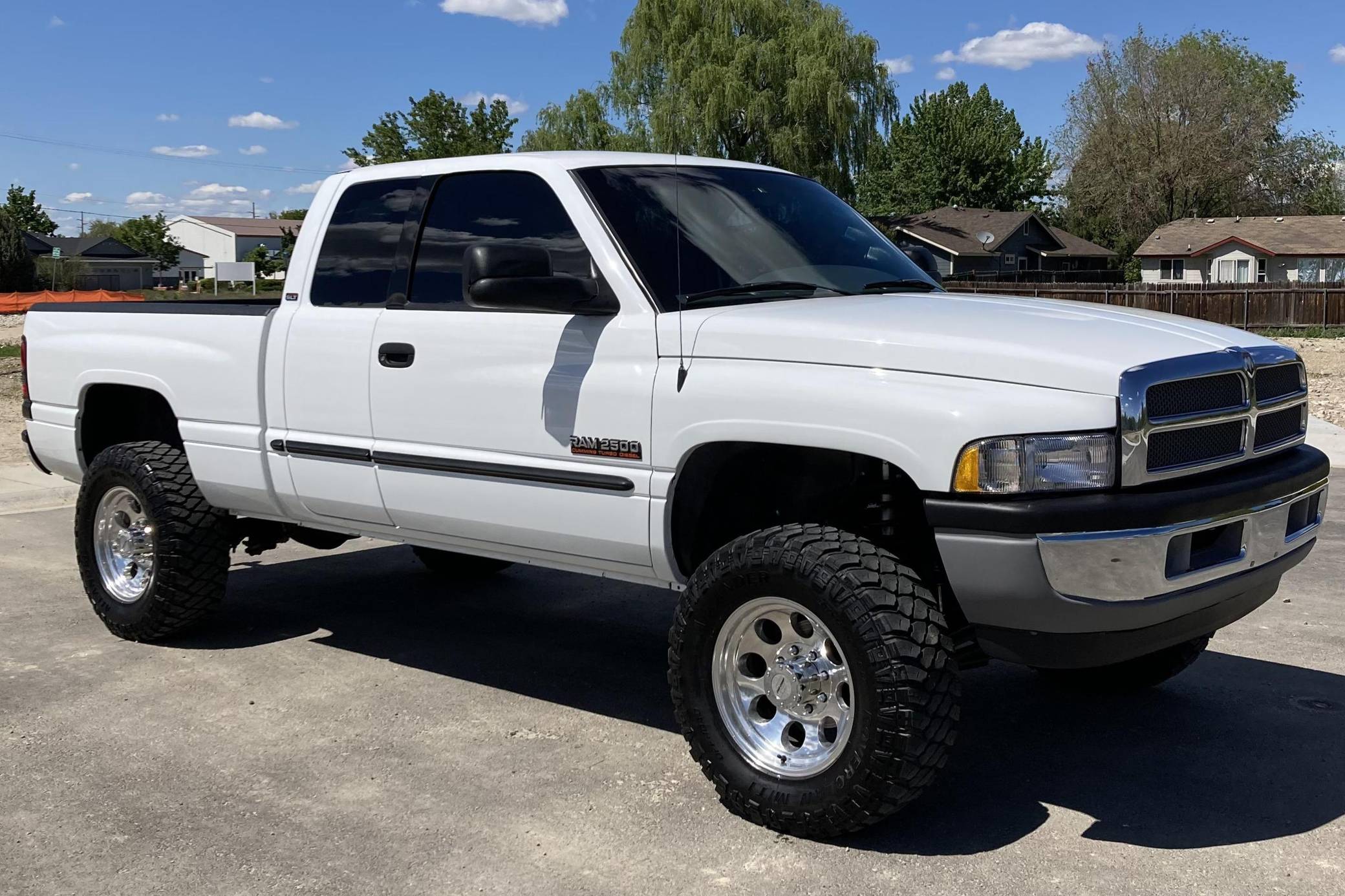
2. 1994–2002 Dodge Ram 2500/3500 (Second Generation)
The second-generation Dodge Ram 2500 and 3500 trucks, produced from 1994 to 2002, quickly gained a reputation for unrelenting strength, particularly due to their heavy-duty frame construction. At a time when most competitors were still refining the idea of trucks that could be both comfortable and rugged, Dodge went all in on brute power and brawn.
The ladder-style steel frame on these models was designed specifically for high-stress environments. Thicker than the competition’s and reinforced at multiple stress points, this frame could absorb years of towing, payload, and off-road abuse without significant degradation. It’s not surprising that many of these trucks are still on the road today, working just as hard as they did in the ’90s.
The true test of any heavy-duty frame is how well it performs under extreme torque, and this generation of Ram delivered with flying colors—largely due to the 5.9L Cummins turbo diesel engine available in the 2500 and 3500 models. With torque figures that far exceeded those of gasoline engines at the time, the Cummins motor required a frame that could withstand significant drivetrain stress.
Dodge responded by integrating thicker boxed frame sections, especially in the engine bay and undercarriage, supported by robust cross members. This design not only handled torque effectively but also resisted the bending and flexing that can occur during heavy towing or uneven terrain traversal, which could lead to structural fatigue in lesser trucks.
What made these trucks stand out further was their versatility in various industries. Farmers, construction foremen, and oil field workers all turned to the second-gen Ram for its unbeatable durability. Unlike some of its contemporaries, which would show signs of stress with cracked welds or bending frame rails, the Ram’s frame stayed true even after years of hard use.
Many owners outfitted these trucks with snowplows, flatbeds, and towing rigs, pushing them beyond factory specs. And still, the frame held strong—an iron backbone in a world where cutting corners had become increasingly common in vehicle design.
The longevity of the second-generation Ram’s frame is evidenced today by the thriving enthusiast community dedicated to restoring and maintaining these models. While the bodywork may rust and the interiors may wear, the frame often remains the strongest part of the truck.
Even salvage yards frequently find these frames intact long after the truck has been retired for other reasons. The legacy of the 1994–2002 Dodge Ram HD lies not just in its Cummins-powered glory but in the unshakeable steel that kept it grounded.

3. 2007–2014 Ford F-150 (Twelfth Generation)
When Ford introduced the twelfth generation of its wildly successful F-150 in 2007, it marked more than just a cosmetic upgrade—it was a structural overhaul focused on strength and utility. At the heart of this transformation was a fully boxed, high-strength steel frame that significantly enhanced the truck’s rigidity and durability.
This redesign was more than just an engineering milestone—it was a strategic move to reinforce the F-150’s position as America’s best-selling truck. The boxed frame allowed for better stress distribution during towing and hauling, reducing the likelihood of frame flex or metal fatigue over time.
Ford’s decision to transition away from the traditional open C-channel frame (used in previous models) paid off. The new frame provided 10% greater torsional rigidity compared to its predecessor, which translated to improved ride quality, safer handling, and better control under load.
For contractors and blue-collar workers, this meant a more stable platform for daily operations. For weekend warriors, it offered confidence when towing boats, trailers, or campers over long distances. Even under maximum tow capacities, the F-150 retained its composure—thanks to the strategically placed cross members and a stiffer spine that could take a beating without compromise.
Another key aspect that contributed to this frame’s success was its compatibility with Ford’s growing suite of technological and mechanical enhancements. The frame provided a stable foundation for innovations like the EcoBoost engine, integrated trailer brake controllers, and advanced stability systems.
Owners appreciated how the frame didn’t just offer brute strength but allowed the truck to feel planted, predictable, and safe—qualities that contributed to its top crash-test ratings and customer satisfaction scores during its production run.
Longevity-wise, the 2007–2014 F-150 remains a favorite in the used truck market. Many examples with over 200,000 miles still retain their structural rigidity with little to no frame issues reported, provided routine maintenance and rust prevention were observed.
Its combination of everyday usability and true workhorse capability cemented its status not only as a commercial tool but as a trusted family vehicle. In a competitive field filled with promises of toughness, this generation of F-150 delivered, quite literally, from the ground up.
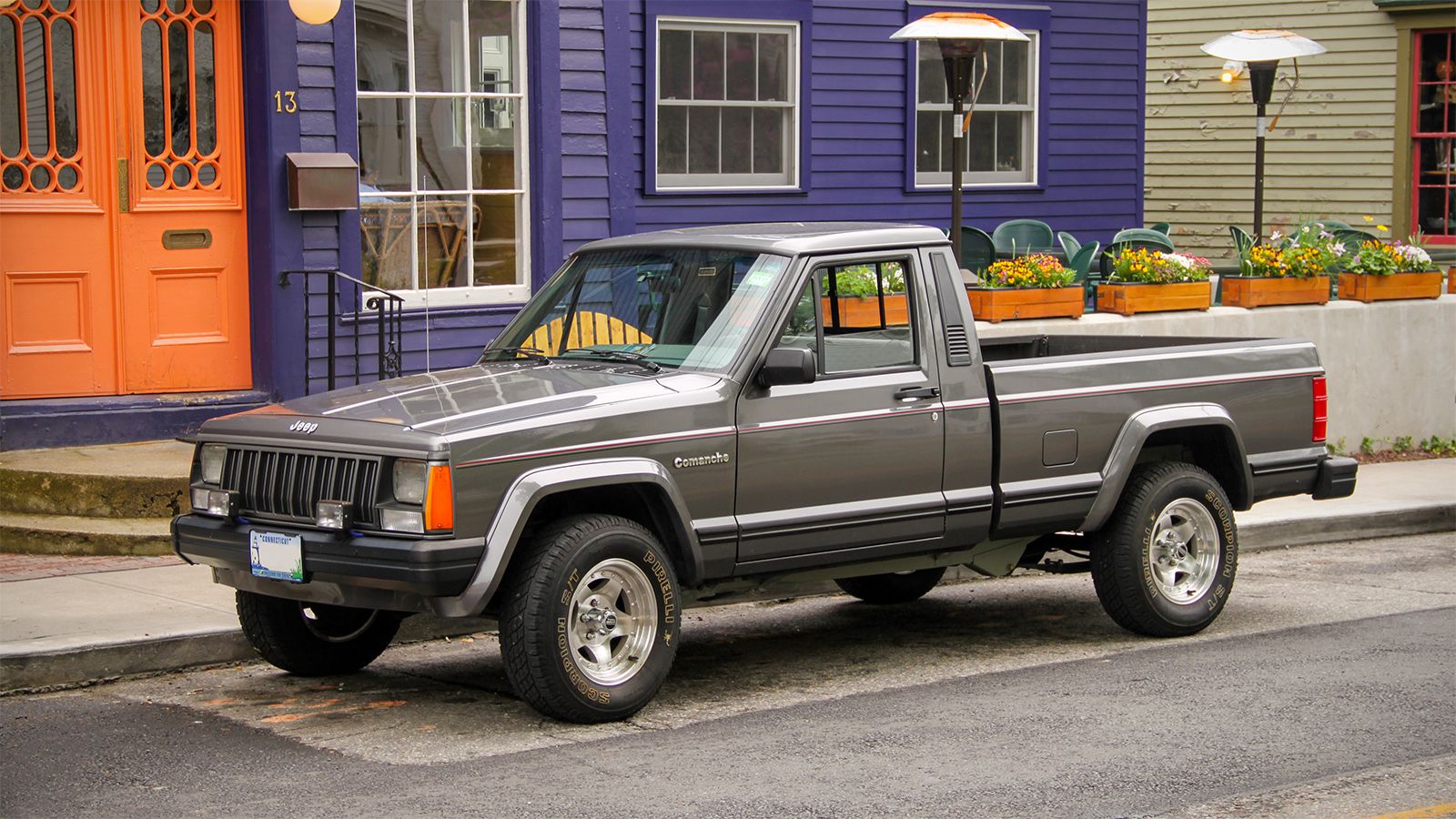
4. 1984–2001 Jeep Comanche (MJ)
The Jeep Comanche MJ, produced from 1984 to 1992 (with some carryover models into the early 2000s in niche markets), holds a unique place in pickup truck history—not only for its rarity but for its unconventional, yet remarkably resilient, frame structure.
Built on a modified version of the Jeep Cherokee’s unibody platform, the Comanche featured a hybrid frame that combined a unibody front with a traditional body-on-frame rear section.
This duality resulted in a structure that was lighter than full-frame trucks but surprisingly tough and capable. Jeep’s engineers managed to strike an impressive balance between comfort and strength—a feat few compact trucks of the era could replicate.
Off-road enthusiasts quickly took notice. The Comanche’s solid front axle and durable underpinnings made it a capable trail machine straight from the factory. But it was the way the frame absorbed abuse that truly defined its toughness. Trails that left other compact pickups creaking or showing signs of frame twist were easily navigated by the MJ.
Owners frequently reported rock crawling, fording streams, and navigating deep ruts without significant body-flex or frame fatigue. Its structure also allowed for extensive customization—many Comanches were lifted, fitted with heavy-duty bumpers, roll cages, and oversized tires, all without compromising structural integrity.
Despite being out of production for over 30 years, the Comanche continues to earn respect in off-road and enthusiast circles. Survivors of this truck are often praised for how “tight” the body still feels—no door misalignments, no frame creaks, and no rusted-through rails, especially in dry climates.
Part of this durability stems from the fact that Jeep, during the 1980s, overengineered the MJ to appeal to both personal and fleet buyers, particularly targeting military-style robustness. The result was a compact truck that punched well above its weight in terms of frame resilience.
Collectors and restorers now actively seek Comanches not only for their rarity but because of how well their frames hold up after decades of use.
In a world that increasingly moved toward crossover softness, the Comanche remains a relic of toughness—a compact pickup with the heart (and frame) of a true off-road legend. Whether hauling gear or conquering trails, the MJ’s frame was and still is up to the task.
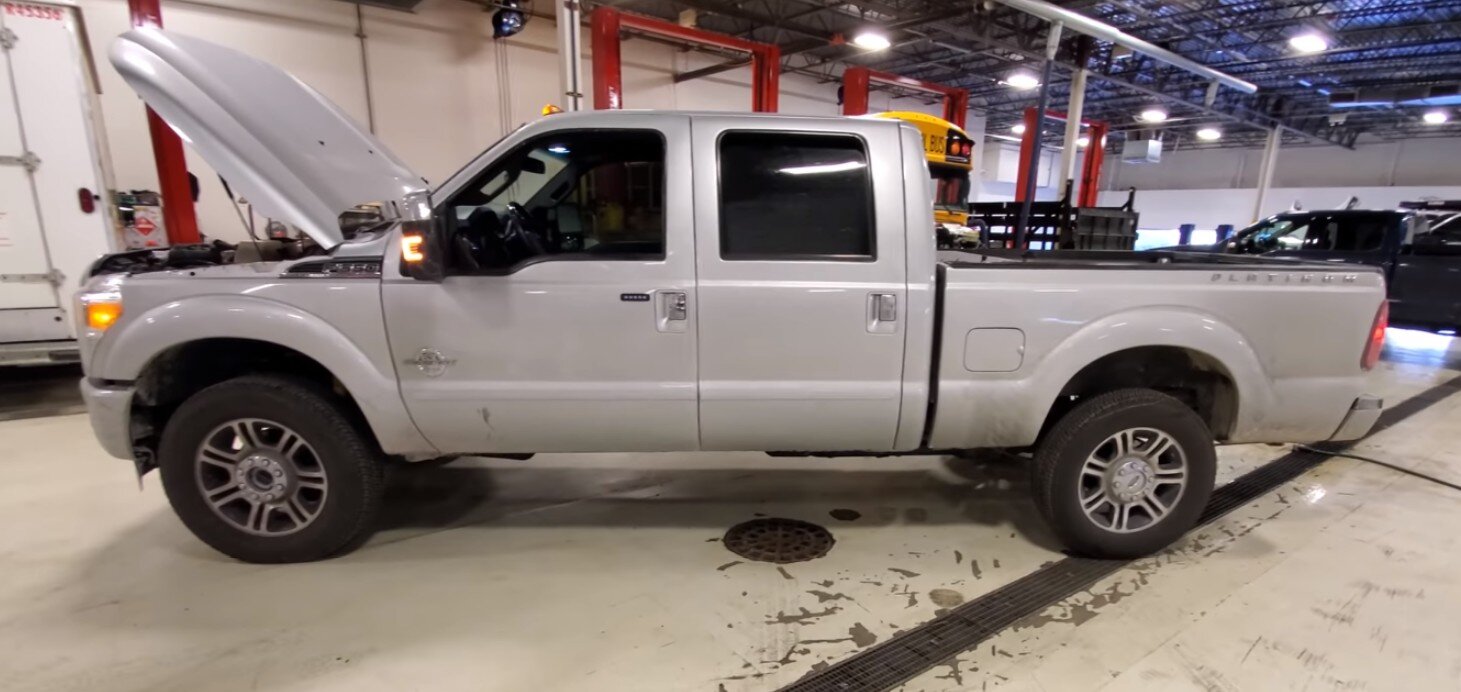
5. 1989–1997 Ford F-350 (OBS – Old Body Style)
The 1989–1997 Ford F-350, commonly referred to as the OBS (Old Body Style) Ford, is considered one of the last true heavy-duty pickups built with a no-nonsense, overbuilt philosophy.
Introduced before modern emissions standards and comfort-oriented redesigns began reshaping the pickup landscape, the OBS F-350 was a product of pure function.
Central to its enduring popularity was its ultra-robust frame, designed from the ground up to endure extreme use in agriculture, construction, towing, and even military contexts.
The fully boxed frame under the engine and cab area, paired with high-strength C-channel rails in the rear, created a structural platform that could handle payloads and tow capacities few trucks at the time could match—without compromising longevity or ride stability.
One of the defining characteristics of the OBS F-350’s frame is its sheer mass. The frame rails are thicker and heavier than what you’d find even on some later Super Duty models, with cross members and welds engineered for maximum strength under consistent pressure. It was designed not just for occasional towing but for daily, long-term heavy hauling.
When paired with the iconic 7.3L IDI and later the 7.3L Power Stroke diesel engines, the truck became a legend in the towing community.
These engines generated enough torque to test the mettle of any chassis, but the F-350’s frame absorbed the punishment year after year with no measurable decline in structural integrity. Unlike some trucks where the powertrain seemed to outlast the frame, here both worked in harmony for hundreds of thousands of miles.
In practical application, this meant the truck excelled not only on highways but in rougher environments. From logging operations in the Pacific Northwest to icy roads in the Midwest, the F-350’s frame proved resistant to flex, cracking, and corrosion (with proper maintenance).
It became a favorite for fifth-wheel hauling, gooseneck trailers, and flatbed conversions. Even those who engaged in off-road towing or operated in flood zones and fire country found that the frame withstood severe conditions with ease. It’s not unusual to hear stories of these trucks being used to pull out stuck equipment, transport livestock trailers, or carry loads that far exceeded published specifications.
Even decades after production ended, the OBS F-350 remains one of the most sought-after platforms for restoration and modification. Its frame is so trusted that many builders repurpose it for modern engine swaps, custom utility builds, or even RV conversions.
Unlike newer trucks which often emphasize lightweight materials and fuel economy, the OBS Ford was built during an era when trucks were expected to be near-indestructible.
The result is a frame that still rivals or surpasses modern trucks in strength, a testament to the “overbuilt is better” philosophy that Ford applied at the time. For those in the know, few trucks embody true steel-frame grit like the 1989–1997 F-350.
5 Pickup Trucks With Known Structural Failures

1. 2005–2010 Toyota Tacoma (Second Generation)
The second-generation Toyota Tacoma, produced from 2005 to 2010, carried high expectations after the massive success of its predecessor. While it introduced modernized styling, improved interior features, and more powerful engine options, it also came with a major Achilles’ heel—significant frame rust issues.
The frames used during this production run were outsourced and manufactured using a coating process that proved inadequate for long-term corrosion resistance, particularly in regions that used road salt during winter.
Over time, these frames were found to rot from the inside out, leading to alarming safety concerns and eventual recalls. For a truck with an otherwise strong reliability reputation, this was a glaring structural failure that tarnished its legacy.
The frame issues became so severe that Toyota was forced to launch an extensive recall and buyback program. Under pressure from consumers and watchdog agencies, Toyota offered full frame replacements or, in some cases, full vehicle buybacks when frames were deemed too far gone to safely repair. These weren’t isolated incidents.
Thousands of owners across the U.S. and Canada reported premature frame perforation, even in trucks that had been relatively well-maintained.
Mechanics frequently encountered Tacomas where the frame rails had split, suspension mounting points had rusted away, or structural integrity had been so compromised that normal driving became a risk. For a brand known for overengineering, this was a rare but significant misstep.
Many drivers were shocked by how quickly the corrosion set in. Trucks that were only five or six years old began failing state safety inspections due to frame decay. In some cases, owners reported driving over bumps and hearing sharp cracks, only to discover the frame had rusted so badly that components like the rear axle or spare tire carrier were barely attached.
Even vehicles that had never towed or been off-road showed signs of frame rot, indicating that the problem wasn’t usage-related but rather an issue with materials and protective coatings. This wasn’t just surface rust; it was deep, structural corrosion that undermined the core of the vehicle.
Though Toyota did take accountability with recalls, reimbursements, and frame replacement campaigns, the damage to the Tacoma’s reputation lingered. It was a bitter pill for fans of the brand, many of whom had purchased their trucks based on Toyota’s previous reputation for durability and resilience.
The second-generation Tacoma remains popular for its overall reliability and off-road capabilities, but the frame rust issue is a glaring structural flaw that reminds buyers that even legendary automakers can make critical mistakes in the design and supply chain processes.

2. 1997–2004 Ford F-150 (Tenth Generation)
The tenth-generation Ford F-150, introduced in 1997, represented a major shift in Ford’s approach to truck design. This generation moved toward a more rounded, aerodynamic body and emphasized passenger comfort over heavy-duty utility.
Unfortunately, with that shift came a series of frame and structural issues that plagued many of these models throughout their lifecycle.
The biggest problem was frame corrosion—particularly in northern U.S. states and Canada, where road salt and winter weather contributed to premature rusting of key structural components. The C-channel frame used in these models, while lighter and more cost-effective to produce, lacked the long-term durability and protection that earlier boxed or hybrid designs had offered.
In addition to rust, the design of the frame also contributed to poor rigidity under stress. Reports from mechanics and owners noted that under heavy towing or off-road usage, the frame was more prone to flexing than previous generations. This not only affected driving dynamics but also accelerated wear on other components like body mounts, suspension brackets, and crossmembers.
Cracks around shock mounts and leaf spring hangers became common in trucks that had seen significant use, especially in models with minimal undercoating protection. While this generation did appeal to a broader market of suburban and lifestyle buyers, those who used the trucks for traditional work purposes were often disappointed by their structural limitations.
The corrosion issues were not merely cosmetic. In some cases, critical parts such as fuel tank straps and spare tire carriers detached due to rusted frame components. Ford did issue recalls for specific frame rust issues, but they were limited in scope and didn’t fully address the widespread nature of the problem.
As the trucks aged, more and more owners began reporting unsafe conditions. Some frames would crumble around mounting points, rendering the truck unsafe for towing or even everyday driving. In worst-case scenarios, frames would snap entirely in the middle during heavy loads—an unforgivable failure for a vehicle marketed as a durable workhorse.
While the tenth-gen F-150 did well in sales and introduced many modern features, its frame design proved to be one of the weaker aspects of the vehicle. Over time, it became clear that the emphasis on weight savings and comfort came at the cost of long-term structural reliability.
For those in regions where road salt and moisture are prevalent, the structural integrity of these trucks often failed far earlier than expected. It serves as a cautionary tale about the consequences of shifting too far from the core principles of durability in favor of aesthetics or cost-cutting measures.

3. 2004–2008 Nissan Titan (First Generation)
Nissan’s first major entry into the full-size pickup market, the 2004–2008 Titan, was a bold move intended to take on domestic heavyweights like the F-150, Silverado, and Ram. While the Titan did succeed in offering a powerful V8 engine and respectable towing capabilities, it quickly earned a less flattering reputation for structural shortcomings, particularly with its frame design.
Despite its muscular appearance, the Titan’s frame was known to be under-engineered relative to its competitors, resulting in a variety of long-term durability issues. From weak welds to rust-prone steel, the Titan struggled to maintain its structural integrity over time, especially under the demands of real-world truck usage.
One of the most common complaints among Titan owners was premature frame corrosion, especially in trucks exposed to humid or salty environments. Unlike some competitors who used thicker-gauge steel or better rustproofing, the Titan’s frame was susceptible to oxidation that started around weld joints and cross members and spread rapidly.
Owners reported instances of frame rot that led to dangerous failures in suspension mounts or cab supports. The frame’s vulnerability was further exacerbated by poor drainage design, which allowed moisture to collect in critical areas, speeding up the corrosion process. For a truck expected to compete in the American market, where heavy-duty performance is paramount, this flaw was hard to overlook.
Compounding the rust issues was the frame’s limited resistance to torsional stress. While the Titan performed decently on paper in terms of tow ratings and payload capacity, real-world experiences often fell short. Owners towing near the truck’s capacity noted excessive frame flexing, which in turn affected ride quality and control.
Some even reported misaligned body panels and creaks developing around the cab—indications that the frame was flexing too much under load. Over time, repeated exposure to stress without proper reinforcement could lead to weld failures or mounting point deformations, reducing the truck’s functional lifespan.
The structural problems of the first-generation Titan severely hindered its acceptance in the full-size truck community. Although Nissan improved the frame and materials in later generations, the initial reputation damage was hard to overcome.
Mechanics frequently advised against using early Titans for heavy work applications due to concerns about long-term durability. For a truck aimed at taking a bite out of the Big Three’s dominance, its inability to match them in frame strength was a critical failure that held the Titan back from true market success.

4. 2000–2006 Chevrolet Silverado 1500 (GMT800 Platform)
The Chevrolet Silverado 1500 models built on the GMT800 platform between 2000 and 2006 represent a mixed bag in the pickup world. These trucks were lauded for their engine reliability—especially the 5.3L Vortec V8—and overall drivability.
However, they were also notorious for a series of structural and frame-related issues that many owners experienced after just a few years of ownership.
One of the most persistent problems involved frame rust and corrosion, which plagued these vehicles across rust-belt states. GM’s use of thinner frame steel and inconsistent undercoating practices led to premature frame decay, often starting at the rear where road grime and salt accumulated.
Beyond rust, the frame design of the GMT800 had other notable flaws. The cross members in the rear section of the frame were particularly vulnerable to corrosion and flex. Once rust set in, they would weaken, sometimes to the point of collapsing or disconnecting from the main rails.
These structural failures were not only costly to repair but potentially hazardous, especially if they occurred while towing or under load.
Suspension component mounts and shock towers were also known to rust through, causing severe handling issues and requiring expensive welding or full frame replacements in some cases. The factory rustproofing measures simply did not hold up over time, and this became one of the main criticisms of the platform.
Additionally, many owners and off-roaders noted excessive frame flex in uneven terrain or during heavy towing, leading to cracked welds and even fractured frame rails in severe cases. GM attempted to improve stiffness with reinforcements in later years, but earlier models were already widely reported as having weak torsional rigidity.
Trucks that were heavily used—whether for towing, hauling, or off-road recreation—often showed signs of structural fatigue earlier than expected. Some drivers also observed cab misalignment, squeaking body mounts, and bed separation, all pointing to an underperforming frame.
Despite the Silverado’s popularity and engine performance, its long-term durability was significantly undercut by these structural problems. The frame issues have affected resale values in rust-prone regions and led many fleet owners and rural users to move toward more robust options.
.While later iterations of the Silverado addressed many of these flaws, the damage done by the GMT800 platform’s frame vulnerabilities remains a black mark on an otherwise capable vehicle.

5. 2006–2008 Honda Ridgeline (First Generation)
When Honda launched the Ridgeline in 2006, it introduced a fresh perspective to the pickup market. With its unibody construction—borrowed from Honda’s SUV platforms—it offered car-like comfort, great handling, and innovative features like the in-bed trunk.
However, while these were appealing to casual users, the Ridgeline’s structural design drew criticism from traditional truck buyers for one key reason: it wasn’t built on a body-on-frame chassis. That choice, while technically innovative, ultimately led to the Ridgeline being seen as structurally compromised when it came to heavy-duty use. The unibody construction simply couldn’t match the strength, rigidity, or long-term durability of traditional truck frames.
Though suitable for light-duty use and daily commuting, the first-generation Ridgeline showed its structural limits quickly under more demanding tasks. Owners who attempted towing near the maximum rating—especially up hills or over long distances—often reported flexing in the rear subframe area, uneven load distribution, and issues with suspension alignment.
These were not the type of problems associated with traditional pickups. Furthermore, the Ridgeline’s non-traditional frame limited its off-road capability; frame flex during articulation sometimes led to compromised door seals and noises from the cabin, especially as the vehicle aged.
Another issue was the lack of modularity and repairability in the event of structural damage. With a body-on-frame truck, damage to the frame can sometimes be repaired or replaced independently of the body. In the Ridgeline’s case, the unibody structure meant that any significant frame damage was usually terminal.
Even minor collisions could result in repairs that exceeded the truck’s value, since the unibody required precision reconstruction. For fleet operators or commercial users, this lack of serviceability made the Ridgeline a less attractive option for rugged use.
While the Ridgeline has found a loyal customer base and continues to evolve in its second and third generations, the first generation remains a cautionary tale. Its innovative structure was ahead of its time in terms of design philosophy but failed to live up to the demands of traditional truck buyers.
For those needing a tough frame that can withstand years of hauling, trailering, and abuse, the original Ridgeline simply fell short—proving that not all strength is found in numbers on a spec sheet, but in the steel that lies beneath.
Also Read: 5 SUVs With the Best Headlight Throw and 5 With Dark Spots
As we step back and look at the legacy of these ten trucks—five built on frames that earned legend status, and five that struggled under the weight of their own structural compromises—it becomes abundantly clear that a truck’s greatness starts not with its horsepower or its badge, but with its bones.
The frame is more than a physical structure—it’s a silent indicator of how seriously a manufacturer takes durability, long-term reliability, and respect for the user’s needs. A strong frame often reflects a truck engineered with purpose and foresight, while a weak one hints at compromises, shortcuts, or miscalculations that eventually come back to haunt owners.
The trucks that stood the test of time—like the first-gen Toyota Tacoma or the second-gen Dodge Ram 2500/3500—weren’t just lucky or blessed with good engines. They were crafted with structural integrity in mind from the very beginning. Their frames were designed to take abuse, resist fatigue, and last longer than many owners ever expected.
These trucks became symbols of toughness not through marketing gimmicks, but through real-world results. They worked on farms, traversed mountains, towed trailers, hauled lumber, and kept coming back for more, year after year. Their durability is not just anecdotal—it’s measurable in their continued use decades later and the high resale value they continue to command.
On the other end of the spectrum, we have trucks that fell short—not always because of poor intentions, but because of missteps in material selection, engineering execution, or long-term testing. The second-gen Toyota Tacoma, for example, was built by a company known for reliability, yet it was undone by a critical oversight in frame coating.
The Ford F-150’s tenth generation attempted to modernize and lighten the platform but ended up sacrificing durability in key areas. These were not necessarily bad trucks across the board—but they suffered from one deeply consequential flaw that often proved fatal in the eyes of consumers: weak or rust-prone frames.
Understanding these examples doesn’t just help us judge past models—it informs the way we look at current and future pickups. As modern trucks become increasingly advanced, with aluminum bodies, hybrid powertrains, and computerized systems, the temptation grows for manufacturers to reduce weight and cut costs.
In this push for efficiency and innovation, the lessons of the past must not be forgotten. A frame that is too light, too poorly protected, or too thinly engineered can sabotage an otherwise excellent truck. Regardless of how many cameras, sensors, or towing modes a truck offers, none of it matters if the frame underneath can’t hold together when it counts.
This is why the conversation around frame strength is more relevant than ever. The truck market is evolving, but the core principles remain the same.
Whether you’re towing 12,000 pounds, navigating rocky trails, or just expecting your vehicle to last 20 years, frame integrity is non-negotiable. It’s the foundational promise that every truck makes to its owner: “You can count on me.” Trucks that fulfill that promise become legends. Those that don’t become costly lessons—and sometimes, liabilities.
Ultimately, when evaluating or investing in a pickup truck, it pays to look past the paint, the brand, and the brochure. Ask the hard questions about the frame: What’s it made of?
How was it treated? Has it held up in the real world? These are the questions that matter when your truck is fifteen years old and still carrying a full load down a gravel road at dawn. The trucks featured in this article—both the triumphs and the failures—serve as a framework (pun intended) for understanding how critical structural integrity truly is.
So, the next time you shop for a pickup, restore an old one, or debate which truck brand “builds them best,” remember this: a truck’s legacy isn’t just in its engine or its looks—it’s in its frame. That’s where the battle is won or lost. That’s what separates the legends from the letdowns.